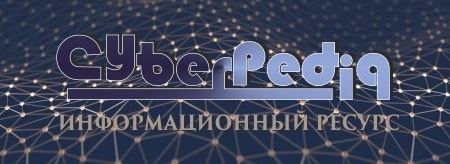
Типы сооружений для обработки осадков: Септиками называются сооружения, в которых одновременно происходят осветление сточной жидкости...
Адаптации растений и животных к жизни в горах: Большое значение для жизни организмов в горах имеют степень расчленения, крутизна и экспозиционные различия склонов...
Топ:
Теоретическая значимость работы: Описание теоретической значимости (ценности) результатов исследования должно присутствовать во введении...
Основы обеспечения единства измерений: Обеспечение единства измерений - деятельность метрологических служб, направленная на достижение...
Когда производится ограждение поезда, остановившегося на перегоне: Во всех случаях немедленно должно быть ограждено место препятствия для движения поездов на смежном пути двухпутного...
Интересное:
Как мы говорим и как мы слушаем: общение можно сравнить с огромным зонтиком, под которым скрыто все...
Средства для ингаляционного наркоза: Наркоз наступает в результате вдыхания (ингаляции) средств, которое осуществляют или с помощью маски...
Инженерная защита территорий, зданий и сооружений от опасных геологических процессов: Изучение оползневых явлений, оценка устойчивости склонов и проектирование противооползневых сооружений — актуальнейшие задачи, стоящие перед отечественными...
Дисциплины:
![]() |
![]() |
5.00
из
|
Заказать работу |
|
|
Практические работы
по дисциплине
«Технология производства заготовок и сортового проката»
Учебно-методическое пособие
Направления: 550500 – металлургия
Специальности: 110600 – обработка металлов давлением
Череповец
2003
Практические работы по дисциплине «Технология производства заготовок и сортового профиля»: Учебн.-метод. пособие. Череповец: ЧГУ, 2004. 36 с.
Рассмотрено на заседании кафедры машины и агрегаты металлургических заводов, протокол № от 2004г.
Одобрено редакционно-издательской комиссией Института металлургии и химии ЧГУ, протокол № от 2004г.
Р е ц е н з е н т ы: Э.А. Гарбер – д-р техн. наук, профессор (ЧГУ)
И.А.Шадрунова – к.т.н., доцент (ЧГУ)
Н а у ч н ы й р е д а к т о р: Э.А. Гарбер - д-р техн. наук, профессор
С о с т а в и т е л ь: М.А.Тимофеева – ассистент
Ó Череповецкий государственный
университет, 2004
Введение
Настоящее учебно-методическое пособие написано на основе курса лекций по «Технологии производства заготовок и сортового проката».
Занятие 1
Нагрев стали и сплавов
Теоретические сведения
Нагрев слитков и заготовок перед прокаткой имеет целью улучшение исходной структуры, уменьшение сопротивления деформации и повышение технологической пластичности металла.
Основные требования к качеству нагрева металла сводятся к тому, чтобы нагрев был произведен до максимально допустимой температуры без перегрева или пережога, должен быть обеспечен равномерный прогрев с минимально допустимым перепадом по сечению и длине слитка или заготовки. Перепад температуры по сечению слитка допустим до 100 ˚С на 500 мм толщины от оси к поверхности. Для слитков массой 2-5 т перепад температуры по сечению рекомендуется 1-3 ˚С на 1 см толщины слитка. Для легированных сталей в зависимости от химического состава перепад температуры по сечению слитка не должен превышать 30-50 ˚С.
|
Температурный режим нагрева металла зависит от ряда факторов, главным из которых является химический состав стали. Верхний предел, или допустимая температура нагрева, лимитируется протеканием собирательной рекристаллизации, явлениями перегрева и пережога и другими факторами; Нижний предел температуры нагрева определяют, исходя из допустимой температуры конца обработки давлением и ее влияния на сопротивление деформации и усилие прокатки; учитывается также выделение и коагуляция фаз упрочнения (карбидов, интерметаллидов и т.д.), структура и механические свойства металла.
Таким образом, для каждой группы марок стали устанавливается свой оптимальный интервал температур нагрева и обработки. В этом интервале данная сталь должна обладать наилучшим сочетанием технологических параметров, структуры и свойства металла.
Н.Ю.Тайц и М.Л.Зарощинский рекомендуют рассчитывать температуру нагрева углеродистой стали по эмпирической формуле
, (1.1)
где Тн – температура нагрева стали, °C;
Тсол – температура по линии солидуса, °C (рис.1.1).
При повышении содержания углерода в стали максимальная температура нагрева понижается:
до 1350°С при 0,1%С;
1250÷1270°С при 0,2%С;
1200÷1220°С при 0,4%С;
1180÷1200°С при 0,6%С.
В производственной практике температуру поверхности и середины слитка или заготовки определяют используя метод Л.М. Мариенбаха.
1. Определяют коэффициент теплопередачи α по формуле Шака с поправкой Хейлингенштедта, ккал/(м2·ч·град)*:
,
где t газ – температура газа в нагревательной печи, °C.
|
2. Используя физические параметры стали, определяют следующие отношения
где S – расчетная толщина (сторона или диаметр) нагреваемого тела, м;
λ – коэффициент теплопроводности, Вт/(м·град);
τ – время нагрева металла, ч;
а – коэффициент температуропроводности, м2/ч.
,
где ср – удельная массовая теплоемкость, Дж/(кг·град);
и
,
ρ – плотность стали, кг/м3.
Рис.1.1. Диаграмма состояния углеродистой стали
3. По найденым отношениям и
с помощью диаграмм (рис. 1.2 –1.5) находят значения отношений:
и
,
где t0 – начальная температура тела, °C;
tп – температура поверхности тела, °C;
t с – температура середины тела, °C.
4. Из этих отношений определяют tп и t с.
Продолжительность нагрева слитков, заготовок зависит от внешнего и внутреннего теплообменов, массы, размеров слитка или заготовки, допустимым перепадом температуры по сечению и определяется по опытным данным, аналитическим методом или по эмпирическим формулам.
Для определения времени нагрева слитков или заготовок при холодном всаде Ю.М. Чижиков рекомендует следующую зависимость
, (1.2)
где τ - время нагрева, ч;
k - коэффициент, учитывающий влияние химического состава стали и условий нагрева (табл.1);
S - сторона или диаметр слитка или заготовки, см.
Продолжительность нагрева слитков в колодцах при горячем всаде по Ю.М. Чижикову определяется по формуле
(1.3)
где t - температура металла при посадке, ˚С.
Таблица 1
Рис. 1.2 График температур Шака для поверхности пластин
Рис.1.3 График температур Шака для середины пластин
Рис.1. 4 График температур Шака для поверхности цилиндра
Рис.1. 5 График температур Шака для оси цилиндра
k - коэффициент, учитывающий температуропроводность стали (для углеродистой и легированной k = 12,5, для высоколегированных k = 20 – 25);
d – поперечное сечение заготовки, м.
Для определения времени нагрева заготовок из малоуглеродистых сталей в методических печах при температуре уходящих газов 800 - 850 °C можно использовать формулу Н. Ю. Тайца:
, (1.5)
где τ – время нагрева заготовок, мин;
S – толщина заготовки, см.
Для расчетов продолжительности нагрева по зонам печи предложены следующие формулы:
|
, (1.6)
где τ j – время нагрева в j-ой зоне печи, ч;
R – радиус сечения цилиндра равновеликого по площади сечения с нагреваемым телом прямоугольного или квадратного сечения, м;
Δ ij – изменение теплосодержания в разные периоды нагрева (по зонам печи), Дж/кг;
.
k 1 – поправочный коэффициент времени нагрева, учитывающий форму тела (для пластины k 1 =1, для цилиндра – 2, для шара – 3);
- средняя поверхностная плотность тепловых потоков в j-ой зоне печи, Вт/м2.
Суммарное время нагрева τ, ч:
, (1.7)
где n – количество зон в печи.
Удельная продолжительность нагрева z, мин/см:
. (1.8)
Расположение заготовок | α | Расположение заготовок | α |
![]() | 1 1 2 1,4 1,3 | ![]() | 1,4 1 4 2,2 2 1,8 |
Рис.1.6 Влияние расположения заготовок в печи на время нагрева
Задачи
Задача 1. Заготовку круглого сечения диаметром S = 200 мм из мягкой углеродистой стали нагревают в печи при температуре газа t газ = 1250 ˚С, начальная температура металла t0= 0 ˚С. Определить разность температур Δt между поверхностью и центром заготовки, если металл нагревают в течение τ = 30 мин. Физические параметры стали: коэффициент теплопролводности λ = 51,17 Вт/(м·град); плотность стали ρ = 7850 кг/м2; удельная массовая теплоемкость ср = 0,57 кДж/(кг·град)*.
Задача 2. Определить продолжительность нагрева слитков размерами 680х680х2000 мм из стали 20 плотностью ρ = 7800 кг/м3 до температуры поверхности 1280 ˚С. Начальная температура слитка 20 ˚С.
Условия нагрева в рекуперативных колодцах следующие:
1. Нагрев двухступенчатый: первый период – при постоянной тепловой мощности; второй период – при постоянной температуре печи.
2. Средние тепловые потоки и изменения теплосодержания металла: = 93,02 кВт/м2;
= 37,82 кВт/м2; Δ i 1 = 582,12 кДж/кг; Δ i 2 = 292,32 кДж/кг;
Задача 3. В нагревательных колодцах нагревают слиток стали 12ХН3А массой 5200 кг, размеры слитка 640х640х1750 мм, плотность литой структуры стали ρ = 7300 кг/м3, начальная температура слитка 25 ˚С. Определить предельную температуру нагрева слитка, полную продолжительность нагрева слитка и по периодам (трехступенчатый нагрев). Средние тепловые потоки и изменения теплосодержания металла: = 36,19 кВт/м2;
= 48,72 кВт/м2;
= 26,91 кВт/м2; Δ i 1 = 352,0 кДж/кг; Δ i 2 = 223,0 кДж/кг; Δ i 3 = 261,4 кДж/кг.
|
Задача 4. Определить продолжительность нагрева слитка углеродистой стали с содержанием 0,3% С при горячем посаде в ячейки рекуперативных колодцев. Размеры слитка мм. Начальная температура поверхности слитка t п = 850 ˚С, конечная температура поверхности слитка t п2 = 1250 ˚С при перепаде Δt = 50 ˚С, температура воздуха t в = 20 ˚С. Физические параметры стали: коэффициент теплопролводности λ = 41,7 Вт/(м·град); плотность стали ρ = 7708 кг/м2; удельная массовая теплоемкость ср = 695 Дж/(кг·град).
Условия нагрева в рекуперативных колодцах следующие:
1. Нагрев двухступенчатый: первый период – при постоянной тепловой мощности; второй период – при постоянной температуре печи.
2. Тепловые потоки: охлаждения q 0 = 86.65 кВт/м2; первого периода q 1 = 63,8 кВт/м2; второго периода q 2 = 12,6 кВт/м2.
3. Начальная температура середины слитка =1200 ˚С; средняя температура в начале посадки t н = 1025 ˚С; температура поверхности слитка в первом периоде t п1 = 1115 ˚С.
Решение.
1. Расчетный радиус слитка:
м.
2. Продолжительность первого периода нагрева слитка:
а) определяем следующие отношения:
;
;
б) из рис. 1.7 по полученным данным определяем:
,
тогда
;
ч.
3. Температуру оси слитка t ос по данным и
определяем из рис.1.8:
;
откуда
°C.
4. Средняя температура слитка первого периода нагрева
°C.
5. Средняя температура слитка второго периода нагрева
°C.
Рис. 1.7 Относительная температура поверхности цилиндра при постоянном тепловом потоке и при наличии температурного градиента в начальный момент.
Рис.1.8 Относительная температура по оси цилиндра при постоянном тепловом потоке и при наличии температурного градиента в начальный момент
6. Согласно табл. 2 теплосодержание в первом периоде нагрева
i1 = 745,8 кДж/кг; во втором периоде i2 = 860,19 кДж/кг.
Таблица 1.2
Теплосодержание чистого железа и углеродистых сталей, кДж/кг
Температура, °C | Содержание углерода в стали, % | ||||
0,30 | 0,610 | 0,795 | 1,235 | 1,575 | |
900 1000 1100 1200 1250 | 627 698 767 840 875 | 618 686 756 832 864 | 610 678 750 778 855 | 603 660 728 795 833 | 612 669 720 783 816 |
Тогда изменение теплосодержания во второй период нагрева
кДж/кг.
7. Средний тепловой поток во втором периоде нагрева:
кВт/м2.
8. Продолжительность нагрева за второй период
ч.
9. Общая продолжительность нагрева
ч.
|
Занятие 2
Теоретические сведения
В этой системе калибров чередуются плоский прямоугольный ящичный калибр и ящичный квадрат. Перед задачей раската в ящичный квадрат выполняется кантовка полосы на 90°.
Геометрия ящичных калибров
В зависимости от ширины исходной полосы b 0 выбирается ширина калибра по дну ручья:
для чистовых калибров
; (2.1)
для промежуточных калибров (без закругления углов)
; (2.2)
для промежуточных калибров (с закруглением углов)
. (2.3)
При происходит удержание и боковое обжатие (защемления) заготовки стенками калибра при входе ее в валки, улучшаются условия захвата и устойчивость раската в калибре.
Высота калибра определяется в соответствии с толщиной исходной полосы h 0 и принятым обжатием Δh:
. (2.4)
Выпуск боковых стенок калибра tgφ можно определить по следующим формулам, %:
для обычных калибров
; (2.5)
для калибров с небольшой глубиной вреза ручья
. (2.6)
Выбрав величину выпуска боковых стенок калибра в соответствии с назначением калибра, определяют ширину калибра:
; (2.7)
. (2.7а)
Величина практически находится в пределах 0,5-2,5.
По найденным размерам выполняют построение калибра (рис.2.1). В зависимости от диаметра валков и назначения калибра принимают величину зазора t (табл.2.1). Глубину вреза ручьев можно рассчитать по формулам:
; (2.8)
при
; (2.8a) при
; (2.8б)
Ширину вреза ручьев можно рассчитать по формуле:
. (2.9)
Радиус закруглений:
; (2.10)
. (2.11)
В некоторых случаях дно ящичного калибра выполняют с выпуклостью s. Это способствует улучшению устойчивости раската на рольганге, предотвращает переполнение при прокатке в следующем калибре после кантовки на 90°. Величину выпуклости s принимают 0,5÷5,0 мм в зависимости от размеров прокатываемого профиля.
Степень заполнения металлом ящичных калибров рекомендуется принимать .
В зависимости от степени заполнения можно определить площадь сечения раската в ящичном калибре:
. (2.12)
За счет выполнения выпуклости дна калибра площадь сечения раската уменьшается на величину
.
При приближенных расчетах площадь сечения раската с учетом закруглений углов принимают равной
. (2.12а)
Расчет режима обжатий
Обжатие за проход Δhmax можно определить по одной из формул:
, (2.13)
где DK – катающий диаметр, мм;
αmax – угол захвата металла валками, град (табл.2.2).
, (2.13a)
где μ – коэффициент трения металла о валки, определяемый по формуле Экелунга:
Таблица 2.1
Зазоры t между валками для различных калибров
Тип стана | Тип калибра | Зазор между валками, мм |
Проволочный и мелкосортный | Обжимные | ![]() |
Черновые | ![]() | |
чистовые | ![]() | |
Среднесортные | Обжимные | ![]() |
Черновые | ![]() | |
Чистовые и предчистовые | ![]() | |
Крупносортные | Обжимные | ![]() |
Черновые | ![]() | |
Непрерывные заготовочные | Черновые | ![]() |
Предчистовые и чистовые | ![]() | |
Блюминги | Калибры при сведенных валках | ![]() |
* - В числителе – для текстолитовых подшипников, в знаменателе – для подшипников качения и жидкостного трения. |
Рис. 2.1 Построение ящичного калибра
Таблица 2.2
Расчетные уравнения для определения допустимого угла захвата
Скорость прокатки, м/с | Угол захвата металла валками αmax, град | |
Стальные валки | Чугунные валки | |
0-2 2-4 4-6 6-8 более 8 | ![]() ![]() ![]() ![]() ![]() | ![]() ![]() ![]() ![]() ![]() |
(для стальных валков);
(для чугунных валков).
, (2.13б)
где RK – катающий радиус, мм.
Если известны число проходов n, площади поперечного сечения заготовки F0 и конечного профиля Fn, то средняя вытяжка λср
, (2.14)
где λобщ – общая вытяжка при прокатке за n проходов.
Зная частные вытяжки (средняя вытяжка) и сторону готового профиля а n можно найти размеры переходных квадратов в четных клетях
. (2.15)
Уширение полосы Δb в ящичных калибрах можно определить по формуле Э. Зибеля:
, (2.16)
где Н – высота задаваемой полосы в калибр, мм;
h – высота профиля на выходе из калибра, мм.
Размеры промежуточных прямоугольных полос между квадратными калибрами
; (2.17)
. (2.18)
Задачи
Задача 1. Рассчитать режимы обжатий и калибровку валков I и II клетей для прокатки заготовки квадратного сечения мм, исходя из средних величин вытяжек в каждой паре калибров на непрерывном заготовочном шестиклетевом стане. Средняя температура металла при прокатке t = 1060°С. Средние вытяжки от квадрата к квадрату: во втором проходе λ2 =1,35; в предчистовом квадрате λ4 = 1,3.
Решение.
1. Исходя из заданных вытяжек определяем стороны квадратов (2.15):
мм;
мм.
Задаемся средней вытяжкой λср =1,32от заготовки к квадрату со стороной а2, тогда сторона исходной квадратной заготовки А равна
мм.
2. Определяем коэффициент трения
.
3. Задаемся (предварительно) обжатием за проход Δh1 = 84 мм.
Тогда высота прямоугольного сечения в I калибре
мм.
5. Уширение определяем по формуле Э. Зибеля:
.
Катающий диаметр ориентировочно можно найти из равенства (2.13):
мм.
Тогда
мм,
принимаем мм.
6. Ширина раската
мм;
7. Проверяем возможность получения квадрата а2 =210 ммво II клети. Прямоугольный раскат кантуется при подаче в квадратный калибр. Тогда обжатие
мм.
При таком обжатии катающий диаметр из равенства (2.13):
мм.
Тогда уширение
мм,
принимаем мм.
Ширина раската во втором калибре
мм.
Таким образом, расчетными размерами раската окончательно являются: мм для I клети и
мм для II клети.
8. Определяем геометрические параметры калибра I и II клетей.
Ширина калибра по дну ручья (2.3):
мм;
мм.
Отношения ;
.
Высота калибра (2.4):
мм;
мм.
Зазор между валками согласно табл.2.1:
мм;
мм.
Глубину вреза ручьев можно рассчитать по формуле (2.8):
мм;
мм.
Выпуск боковых стенок калибра tgφ можно определяем по формуле (2.5):
%;
%.
Ширина вреза ручьев (2.9):
мм;
мм.
Радиусы закруглений (2.10) и (2.11):
мм;
мм.
мм;
мм.
Задача 2. Требуется рассчитать режимы обжатий и калибровку валков промежуточных клетей для прокатки заготовок квадратного сечения 150х150 мм, 190х190 мм, 240х240 мм в первой группе клетей НЗС 900/700/500, которая включает шесть клетей с минимальным диаметром валков 680 мм. Расчетная температура металла в процессе прокатки t = 1100°С. Скорость выхода полосы из последней клети υ6 = 1,85 м/с.
Задача 3. Определить размеры исходной заготовки для квадратного профиля 240х240 мм получаемого из ящичного калибра 4-ой клети НЗС 900/700/500, если коэффициенты вытяжки имеют следующие значения: λ1= 1,25; λ2= 1,30; λ3= 1,17; λ4= 1,21; минимальный диаметр валков 680 мм.
Задача 4. Определить обжатия по проходам и размеры калибров непрерывного заготовочного стана 720 для получения квадрата 150х150 мм из заготовки сечением 295х295 мм. Диаметры валков по буртам: D1 = 770 мм; D2 = 750 мм; D3 = 725 мм; D4 = 700 мм; D5 = 710 мм; D6 = 715 мм. Скорости вращения валков: n1 = 14,5 об/мин; n2 = 19,4 об/мин; n3 = 23,15 об/мин; n4 = 31,6 об/мин; n5 = 35,8 об/мин; n6 = 45,1 об/мин. Температура прокатываемого металла: t1 = 1100°C; t2 = 1080°C; t3 = 1060°C; t4 = 1040°C; t5 = 1020°C; t6 = 1000°C. Расчет вести против хода прокатки.
Занятие 3
Теоретические сведения
Ромбические калибры
Рис.3.1 Построение ромбического калибра
Размеры Нк и Вк ромбического калибра определяют в процессе расчета калибровки с учетом заданной величины коэффициента вытяжки в калибре, правильного заполнения калибра, а также с учетом получения размеров сечения, удовлетворяющим условиям прокатки в следующем калибре.
Откладывая на вертикальной и горизонтальной осях размеры НК и ВК (рис.3.1), выполняют построение скелета в виде геометрически правильного ромба со стороной ср и тупым углом при вершине β. Очевидны соотношения: ;
На практике используются ромбические калибры, характеризующиеся величиной .
При зазоре t (см. табл. 3) ширина вреза ручья будет равна
. (3.1)
Радиус закругления вершины калибра
. (3.2)
Закругления бурта обычно выполняют радиусом
. (3.3)
Иногда ромбический калибр выполняют «с развалом» для предупреждения переполнения калибра металлом, тогда радиус закругления значительно увеличивают:
. (3.3а)
Высота полосы, выходящей из калибра, определяется с учетом закругления вершин:
. (3.4)
Глубина вреза ручья:
. (3.5)
Для предотвращения образования в зазорах калибра заусенцев на профиле в виде «лампасов» рекомендуется принимать степень заполнения калибра
.
При этом образуется притупление m1 ромбической полосы у разъема калибра, величина которого зависит от степени заполнения и высоты калибра:
. (3.6)
С учетом степени заполнения ромбического калибра и закруглений на профиле площадь сечения раската на выходе из калибра будет равна
. (3.7)
Используя размеры прокатанной ромбической полосы, площадь ее поперечного сечения можно определить по формуле
; (3.7а)
или приближенно
. (3.7б)
Квадратные калибры
Построение квадратного калибра выполняется аналогично построению ромбического калибра (рис.3.2) с учетом β = 90° и НК = ВК.
Радиус закругления вершины калибра
, (3.8)
где с – сторона квадрата, мм.
Рис.3.2 Построение квадратного калибра
Чистовой квадратный калибр и предчистовой ромбический калибр выполняют без закругления вершин.
Закругления бурта выполняют радиусом
, (3.9)
а при построении квадратного калибра «с развалом» радиус увеличивают:
. (3.9а)
Высота профиля, выходящего из квадратного калибра, будет несколько меньше высоты калибра из-за закруглений вершин:
. (3.10)
Степень заполнения чистового квадратного калибра должна быть близка к 1, для остальных промежуточных квадратных калибров δ1 = (0,85 ÷ 0,9).
Площадь сечения квадратного профиля с учетом степени заполнения и закруглений углов:
. (3.11)
Площадь сечения квадратного профиля с закруглениями углов:
; (3.11а)
При приближенных расчетах принимают
. (3.11б)
Определение коэффициента вытяжки и уширения
При прокатке ромбической заготовки в квадратном калибре коэффициент вытяжки определяется по формулам:
при DK ≤ 500 мм
; (3.12)
при DK ≥ 500 мм
, (3.12а)
где ∆hКВ – абсолютное обжатие в квадратном калибре, мм;
DK – катающий диаметр валков в квадратном калибре, мм.
, (3.13)
где Dmin – минимальный диаметр валка по буртам, мм.
В чистовом квадратном калибре коэффициент вытяжки рекомендуется принимать
, (3.14)
в предчистовом ромбе
. (3.15)
Уширение ромбической полосы в квадратном калибре если с < 30 мм:
, (3.16)
если с ≥ 30 мм:
. (3.16а)
Уширение квадратной полосы в ромбическом калибре определяется по приближенной формуле:
, (3.17)
где ∆hР – абсолютное обжатие в ромбическом калибре, мм;
DK – катающий диаметр валков в ромбическом калибре, мм.
. (3.18)
Задачи
Задача 1. Выполнить расчет ромбического калибра 5-ой клети непрерывного шестиклетевого заготовочного стана, если задается квадрат со стороной с4 = 156 мм, а на выходе получают квадрат со стороной с6 = 120 мм.
Задача 2. Выполнить расчет калибровки валков второй непрерывной группы клетей НЗС 900/700/500 для получения квадратов со сторонами с14 = 80 мм, с12 = 100 мм, с10 = 120 мм, если в клеть 9 задается заготовка сечением 150х150 мм. Минимальный диаметр валков по буртам 530 мм, скорость выхода полосы из последней клети υ14 = 7,2 м/с. Расчет вести против хода прокатки.
Задача 3. Определить размеры предчистового ромбического калибра для прокатки квадратного чистового профиля со стороной 50 мм. Номинальный диаметр валков 250 мм. Общая вытяжка за два прохода λобщ = 1,52; λР = 1,1 λКВ.
Задача 4. Выполнить расчет калибровки валков 10, 11, 12 клетей мелкосортного стана 250, если в 11 клеть задается квадрат со стороной с10 = 14,5 мм, а на выходе получают квадрат со стороной с12 = 11,5 мм. Система калибровки квадрат – ромб – квадрат.
Решение
1. Общий коэффициент вытяжки в паре клетей 11-12 равен
.
Принимаем вытяжку в предчистовом ромбическом калибре равную вытяжке в чистовом квадратном калибре:
.
2. Площадь поперечного сечения квадратной полосы из 12 клети без учета закруглений углов:
Семя – орган полового размножения и расселения растений: наружи у семян имеется плотный покров – кожура...
Историки об Елизавете Петровне: Елизавета попала между двумя встречными культурными течениями, воспитывалась среди новых европейских веяний и преданий...
Двойное оплодотворение у цветковых растений: Оплодотворение - это процесс слияния мужской и женской половых клеток с образованием зиготы...
Биохимия спиртового брожения: Основу технологии получения пива составляет спиртовое брожение, - при котором сахар превращается...
© cyberpedia.su 2017-2024 - Не является автором материалов. Исключительное право сохранено за автором текста.
Если вы не хотите, чтобы данный материал был у нас на сайте, перейдите по ссылке: Нарушение авторских прав. Мы поможем в написании вашей работы!