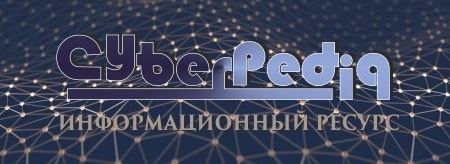
Автоматическое растормаживание колес: Тормозные устройства колес предназначены для уменьшения длины пробега и улучшения маневрирования ВС при...
Адаптации растений и животных к жизни в горах: Большое значение для жизни организмов в горах имеют степень расчленения, крутизна и экспозиционные различия склонов...
Топ:
Выпускная квалификационная работа: Основная часть ВКР, как правило, состоит из двух-трех глав, каждая из которых, в свою очередь...
Теоретическая значимость работы: Описание теоретической значимости (ценности) результатов исследования должно присутствовать во введении...
Процедура выполнения команд. Рабочий цикл процессора: Функционирование процессора в основном состоит из повторяющихся рабочих циклов, каждый из которых соответствует...
Интересное:
Как мы говорим и как мы слушаем: общение можно сравнить с огромным зонтиком, под которым скрыто все...
Мероприятия для защиты от морозного пучения грунтов: Инженерная защита от морозного (криогенного) пучения грунтов необходима для легких малоэтажных зданий и других сооружений...
Инженерная защита территорий, зданий и сооружений от опасных геологических процессов: Изучение оползневых явлений, оценка устойчивости склонов и проектирование противооползневых сооружений — актуальнейшие задачи, стоящие перед отечественными...
Дисциплины:
![]() |
![]() |
5.00
из
|
Заказать работу |
|
|
Анализ при разработке технологии изготовления конструкции
Выбор материала конструкции. Характеристика свариваемости материала.
Существует большое количество конструкционных титановых сплавов различного назначения. В качестве легирующих элементов используется: алюминий – представитель α-стабилизирующих элементов; железо, хром, марганец, молибден, ванадий, ниобий – β-стабилизирующие элементы. Используется также цирконий и олово, относящиеся к типу нейтральных упрочнителей.
В связи с определенным характером действия на титан различных легирующих элементов промышленные сплавы по типу структуры могут быть подразделены на три группы: титановые на основе α-структуры, сплавы на основе β-структуры и двухфазные α+β-титановые сплавы.
Промышленные титановые сплавы с (α+β) -структурой подразделяют на три группы: псевдо α -сплавы с небольшим количеством β-фазы со свойствами, близкими к α -сплавам, типичные (α+β) -сплавы и псевдо β-сплавы. Псевдо β-сплавы представляют собой сплавы на основе β-структуры. В отожжённом состоянии их физико-механические свойства и технологические характеристики типичны для β-сплавов, однако β-фаза у этих сплавов термически нестабильна.
Среднепрочные титановые сплавы с пределом прочности 75-80 кгс/мм2 (ОТ4, АТ3) являются универсальным конструкционным материалом для сварных конструкций. [1]
ОТ4 являются универсальным конструкционным материалом для сварных конструкций. Следовательно, целесообразно будет использовать ОТ4 для изготовления конструкции (сосуда высокого давления). Все данные и характеристики сплава представлены в таблицах 2,3.
Марка: ОТ4
|
Fe | C | Si | Mn | N | Ti | Al | Zr | O | H |
до 0,3 | до 0,1 | до 0,15 | 0,8 - 2 | до 0,05 | 91,638 - 95,7 | 3,5 - 5 | до 0,3 | до 0,15 | до 0,012 |
Химический состав в % сплава ОТ4
Таблица 1
Свойства и полезная информация:
Твердость материала: HB 10 -1 = 207 - 285 Мпа
Свариваемость материала: Хорошая.
Физические свойства сплава ОТ4
Таблица 2
T (Град) | E 10- 5 (МПа) |
20 | 1.15 |
Механическая резка
Листовой прокат, из которого вырезаются заготовки имеет небольшую толщину – 6 мм. Применение термической резки может привести к короблению вырезанных деталей, а также к возможности структурных изменений в металле в связи с активностью титана при нагреве более 450 градусов. Поэтому для изготовления поясов обечайки используется механическая резка. Заготовки можно вырезать с помощью гильотинных или дисковых ножниц.
Гильотинные ножницы позволяют осуществлять резку деталей с прямолинейными кромками из листов толщиной до 20-25 мм, в некоторых случаях - до 40 мм. У таких ножниц ограниченная ширина ножа (до 3200 мм). Погрешность размера обычно составляет ±(2,0 – 3,0) мм при резке по разметке и ±(1,5 – 2,5) мм при резке по упору.
Дисковые ножницы позволяют осуществлять вырезку листовых деталей толщиной до 20…25 мм. Дисковые ножницы позволяют вырезать заготовки любой формы, поворачивая лист относительно инструмента. Это осуществляется за счёт того, что режущие кромки ножниц образованы пересечением конических поверхностей. Погрешность размера составляет ±(2,0 – 3,0) мм. Для получения листовой заготовки заданной ширины с параллельными кромками дисковые ножницы располагают попарно на заданном расстоянии друг от друга. Длина реза за одну настройку достигает 15 м.
При резке на ножницах металл у кромки реза подвергается значительной пластической деформации. Эта кромка в дальнейшем при изготовлении корпуса цистерны попадает в зону сварки и полностью переплавляется, дополнительной обработки не требуется.
Для вырезки заготовок обечаек рациональнее использовать дисковые ножницы. Так как при изменении величины конструкции не будет необходимости смены оборудования. Заготовки для штамповки также удобнее вырезать дисковыми ножницами, т. к. они имеют криволинейную конфигурацию реза. При резке заготовок обечаек дисковые ножницы можно выставить на необходимое расстояние друг от друга и получить необходимую ширину заготовок. На рисунке 3 представлена схема резки металла на разных ножницах.
|
Рисунок 3. Схема резки метала на ножницах различных типов: а) гильотинные ножницы; б) специальные ножницы; в) дисковые ножницы; г) попарные дисковые ножницы на заданном расстоянии друг от друга.
Защитная среда
Сварка и прихватка изделий из титана и его сплавов должна иметь надежную защиту места сварки и остывающих участков шва и околошовной зоны, надежную защиту обратной стороны сварного соединения от воздействия газов окружающей среды, охлаждение сварного соединения в процессе сварки. При сварке сосудов рекомендуется применять насадку (рис.8) для защиты наружной стороны стыка обечайки.
Рисунок 8. Защита наружной стороны шва насадкой при сварке сосудов: 1 – свариваемая обечайка; 2- присадочная проволока; 3 - горелка; 4 - козырек; 5 - сетка
В качестве защитного газа необходимо использовать высший сорт аргона (99,9*%) ГОСТ 10157-73. Этот выбор принят так как титан является активным металлом и сварка в активных газах категорически запрещена, необходимо использовать инертные газы таки как аргон и гелий. В виду экономичности и практическом отсутствии разницы качества сварки в этих атмосферах, принято использовать высший сорт аргона. Необходимо наполнить камеру для изготовления днищевой части, а также при использовании технологии изготовления сосуда со сваркой встык без разделки кромки (обечайка + днище) изготовить приспособление для продувки всей конструкции так как необходимо защищать обратную сторону шва от кислорода (Рис.9).
Рисунок 9.Установка для защиты внутренней стороны шва.
При варианте с расточкой кромок отпадает необходимость в защите внутренней стороны шва.
Расчет прочности
Необходимо отметить, что в нашей конструкции есть экстремальные участки. В процессе выбора технологии изготовления, обнаружено два опасных участка на промежутке которых, толщина металла составляет 3 мм.
|
Для проверки способности сосуда выдержать давления 6 атм (6*10^5 Па) необходимо произвести расчет толщины стенки для сосуда диаметром 380мм и рабочим давлением 6 МПа. Расчет (ГОСТ 14249-2003 СОСУДЫ И АППАРАТЫ нормы и методы расчета на прочность). Гладкие цилиндрические обечайки. Обечайки, нагруженные внутренним избыточным давлением. Толщину стенки следует рассчитывать по формуле:
;
где, толщина стенки;
рабочие давление; D – диаметр обечайки;
допускаемое напряжение;
коэффициент прочности шва (принимаем за 1).
Расчет показывает, что данное опасное сечение имеет запас в 1.2 мм по толщине металла.
Оборудование
Следует определить необходимое оборудование для изготовления сосуда из титанового сплава. Стоит заметить, что технология изготовления сосуда предусматривает собой только поточное производство, в единичном случае вся изготавливается вручную. Для определения всех необходимых единиц оборудования необходимо составить список операций.
Операции изготовления сосуда производятся в следующей последовательности:
- разметка;
- резка;
- вальцовка обечаек;
- штамповка днищ;
- сборка и сварка днищ с фланцами;
- сборка и сварка днищ и обечаек.
Разметка
Разметка производится по схеме, показанной на рис.10.
В дальнейшем после резки: заготовки, предназначенные для обечаек, транспортируются на операции гибки и сварки продольного шва; Заготовки, предназначенные для последующей штамповки днищ, вырезаются дисковыми ножницами. На рис. 10 показана схема разметки листов, указаны размеры стандартных листов по ГОСТ 22178 (600×2000) и размеры вырезаемых заготовок все размеры в масштабе 1:10.
Разметку контуров деталей производят разметочно-маркировочной машиной пневмо-керном по программе установленной оператором.
Рисунок 10. Схема разметки листов: 1-для заготовок обечаек; 2-3- для заготовок днищ.
Машина работает в автономном режиме и имеет следующие характеристики [4]:
- наибольшие размер обрабатываемых листов, мм
длина 10000;
ширина до 6000;
- наибольшая скорость перемещения пневмо-керна, м/мин 8-10;
- точность перемещения машины, мм ±1,0.
Резка
Резка производится на дисковых ножницах (рис.11.) марки Н4422 по схеме раскроя, которые имеют следующие технические характеристики:
|
Дисковые ножницы Н4422:
- наибольшая толщина разрезаемого листа, мм 16;
- скорость резки, м/мин 2-6;
- мощность электродвигателей, кВт 12;
- габаритные размеры, мм 7590´1530´2780;
- масса, т 15,4.
Рисунок 11. Схема резки дисковыми ножницами:1 – дисковые ножи; 2 – разрезаемый лист.
Вальцовка
Обечайки получают гибкой листов на листогибочных вальцах. При холодной гибке пластическую деформацию приходиться ограничивать. При изготовлении обечаек рациональнее использовать четырехвалковые гибочные вальцы, т.к. несвальцованным остается небольшой участок. Схема процесса гибки показана на рис. 12.
Рисунок 12. Схема процесса гибки в вальцах.
Для получения необходимого радиуса вальцовку производить на листогибочном станке И2416.
Четырех валковые машины считаются наиболее универсальными, точными и простыми в эксплуатации. Мгновенное и идеальное центрирование листа на этапе загрузки стало возможным благодаря использованию одного из боковых валков как ориентира для отсчета. Это позволяет выполнение операции одним оператором. Лист остается «зажатым» сразу после центрирования и до конца цикла вальцевания. Это позволяет избежать случайного проскальзывания детали с гарантией максимальной точности гиба и безопасности для оператора. Операция подгиба не приводит к опусканию листа ниже уровня ввода, как это происходит в вальцовочных машинах с тремя валками. Это позволяет использование столов подачи и центрирования. Вальцевание детали начинается сразу после первого подгиба. Таким образом, не нужно оставлять свободное пространство по двум сторонам машины, а только на стороне, соответствующей выбранной стороне подачи [2].
Формирование второго края (второй подгиб) происходит после вальцевания, ввиду чего возможно изготовление обечайки за один проход. Гибка конусов на машине с четырьмя валками облегчается, т.к. боковые валки наклоняются для обспечения угла конусности и центральный нижний валок также наклоняется таким образом, что лист будет зажат и хорошо протягиваться. В таблице 3 указаны основные технические характеристики гибочной машины И2416.
Технические характеристики листогибочной машины И2416.
Наибольшие размеры сечения листа при гибке, мм | Минимальный радиус гибки | Мощность привода, кВт | Габариты, мм |
2000х6 | 125 | 6,3 | 3250х850х1300 |
Таблица 3
3.4 Штамповка днища
В серийном и массовом производствах для получения элементов с поверхностью сложного очертания широко используют холодную штамповку из листового материала, толщиной преимущественно до 10 мм. Высокая производительность холодной штамповки, точность размеров и формы получаемых заготовок, их малая масса и низкая себестоимость обеспечивают создание весьма технологичных штампосварных изделий.
|
Для получения необходимого радиуса, штамповку производить на гидравлическом прессе К04.К3533.
Пресс К04.К3533 предназначен для изготовления из листового материала средних и крупных деталей, требующих вырубки, гибки, формовки, неглубокой вытяжки и других операций холодной штамповки.
Технические характеристики:
Номинальное усилие, МН -2,0
Недоход ползуна, мм-12
Ход ползуна, мм -320
Число непрерывных ходов,-18
Число одиночных включений, мин-1, не более- 12
Закрытая высота, мм -450
Регулировка закрытой высоты, мм- 200
Размер от пола до верхней плоскости подштамповой плиты, мм - 810
Размеры стола, мм слева направо -2700
спереди назад -1350
Размеры ползуна, мм слева направо -2700
спереди назад -1100
Размеры окон в стойках, мм ширина - 900
высота - 610
Высота пресса над уровнем пола, мм - 5670
Масса, кг – 49985
Рисунок 13. Схема процесса штамповки днища: 1- пуансон; 2- заготовка днища.
Контроль качества
4.1 Виды контроля качества
Применяют следующие виды контроля качества сварных соединений:
- внешний осмотр и измерение;
- ультразвуковой контроль;
- радиографический контроль;
- механические испытания;
- металлографические исследования;
- радиоскопия;
- испытания на стойкость против межкристаллической коррозии;
- гидравлические испытания;
- пневматические испытания;
- другие методы (магнитография, цветная дефектоскопия, акустическая эмиссия).
4.2 Внешний осмотр и измерение.
Визуальному и измерительному контролю подлежат все сварные соединения сосудов и их элементов с целью выявления в них следующих дефектов:
- трещин всех видов и направлений;
- свищей и пористости наружной поверхности шва;
- подрезов;
- наплывов, прожогов, незаплавленных кратеров;
- смещения и совместного увода кромок свариваемых элементов свыше норм, предусмотренных настоящими Правилами;
- непрямолинейность соединяемых элементов;
- несоответствие формы и размеров швов требованиям технической документации.
Перед визуальным осмотром поверхность сварного шва и прилегающие к нему участки основного металла шириной не менее 20мм в обе стороны от шва должны быть зачищены от шлака и других загрязнений, при электрошлаковой сварке это расстояние должно быть не менее 100 мм.
Осмотр и измерения сварных соединений должны производиться с наружной и внутренней сторон по всей протяженности швов. В случае невозможности осмотра и измерения сварного соединения с двух сторон его контроль должен производиться в порядке, предусмотренном автором проекта.
4.3 Радиографический и ультразвуковой контроль.
Ультразвуковая дефектоскопия и радиографический контроль производятся с целью выявления в сварных соединениях внутренних дефектов (трещин, непроваров, пор, шлаковых включений и др.).
Метод контроля (ультразвуковая дефектоскопия, радиографический контроль, оба метода в сочетании) выбирается исходя из возможности обеспечения более полного и точного выявления недопустимых дефектов с учетом особенностей физических свойств металла.
4.4 Гидравлические испытания.
Гидравлическому испытанию подлежат все сосуды после их изготовления.
Сосуды, изготовление которых заканчивается на месте установки, транспортируемые на место монтажа частями, подвергаются гидравлическому испытанию на месте монтажа.
Сосуды, имеющие защитное покрытие или изоляцию, подвергаются гидравлическому испытанию до наложения покрытия или изоляции.
Сосуды, имеющие наружный кожух, подвергаются гидравлическому испытанию до установки кожуха.
Допускается эмалированные сосуды подвергать гидравлическому испытанию рабочим давлением после эмалирования.
Гидравлическое испытание сосудов должно проводиться пробным давлением.
Для гидравлического испытания сосудов должна применяться вода с температурой не ниже 5 °С и не выше 40 °С, если в технических условиях не указано конкретное значение температуры.
Разность температур стенки сосуда и окружающего воздуха во время испытаний не должна вызывать конденсации влаги на поверхности стенок сосуда.
По согласованию с разработчиком проекта сосуда вместо воды может быть использована другая жидкость.
Давление в испытываемом сосуде следует повышать плавно.
Давление при испытании должно контролироваться двумя манометрами. Оба манометра выбираются одного типа, предела измерения, одинаковых классов точности, цены деления.
После выдержки под пробным давлением давление снижается до расчетного, при котором производят осмотр наружной поверхности сосуда, всех его разъемных и сварных соединений.
Обстукивание стенок корпуса, сварных и разъемных соединений сосуда во время испытаний не допускается.
Сосуд считается выдержавшим гидравлическое испытание, если не обнаружено:
- течи, трещин, слезок, потения в сварных соединениях и на основном металле;
- течи в разъемных соединениях;
- видимых остаточных деформаций, падения давления по манометру.
Сосуд и его элементы, в которых при испытании выявлены дефекты, после их устранения подвергаются повторным гидравлическим испытаниям пробным давлением.
Гидравлическое испытание допускается заменять пневматическим при условии контроля этого испытания методом акустической эмиссии или другим, согласованным с Госгортехнадзором России методом. Все данные по контролю качества взяты из РД 34.15.132-96.
Выбор режимов сварки
1. Пост сварки прямолинейного шва с подкладкой
2. Пост сварки круглых швов
3. Пост прихватки
4. Пост сварки в контролируемой атмосфере(выбран).
Пост № 1 и № 2 использует автоматическую аргона-дуговую сварку титана для сварки толщины порядка 6 мм в один проход. Режимы сварки такой толщины в один проход в таблице 5 [4].
Режим для поста №1 и №2
Таблица 5
Металл, мм | Число проходов | Iсв, А | Uд, В | Vсв, м/ч | Расход газа горелка л/мин | Расход газа насадка л/мин |
6 | 1 | 180-210 | 10-12 | 10-15 | 14-16 | 16-20 |
Пост №3 и №4 использует ручную аргона-дуговую сварку титана для сварки толщины порядка 6 мм. Режимы сварки такой толщины в таблице 6 [4].
Режим для поста №3 и №4
Таблица 6
Металл, мм | Число проходов | Iсв, А | Uд, В | Расход аргона л/мин | Vсв для одного прохода м/ч |
6 | 4-3 | 130-160 | 11-15 | 12-16 | 12-15 |
Следовательно, из данных режимов мы можем рассчитать время, затраченное на сварку и количество аргона на изготовление одного сосуда.
ВЫВОД
Количество сосудов, изготовленных в месяц, при использовании смены равной 8 часов, равняется 72 штуки. Данное значение полностью совпадает с заданным условием. Данная технология может увеличить производительность при параллельном выполнении операций
Таких как: штамповка и вальцевание; прихватка и приварка фланца и сварки прямолинейного шва. Для разработки оптимального режима сварки рекомендуется пользоваться современным ПО, данная работа сделана по списку литературы, что был выдан преподавателем и не предусматривает использование современных подходов к построению технологии изготовления конструкций, что в действительности сильно влияет на производительность.
Стоит так же заметить, что в данной работе не рассмотрены все актуальные на сегодняшний день технологии, так как информация касаемо титана и его сплавов весьма ограничена. Этот факт не позволил с точностью оценить все технические моменты изготовления титанового тонкостенного сосуда.
Список литературы
[1] Г.А.Николаев и др., Сварка в машиностроении (справочник) т.3, Москва: "машиностроение", 1979. [2] Г.А.Николаев и др., Сварка в машиностроении (справочник) т.4, Москва: "Машиностроение", 1979. [3] Б. И.А., Производство сварных конструкций часть 1, Караганда: "КАРАГАНДИНСКИЙ ГОСУДАРСТВЕННЫЙ ТЕХНИЧЕСКИЙ УНИВЕРСИТЕТ", 2008. [4] В. Никифоров, Технология металлов и конструкционные материалы, Ленинград, 1986. 5. ГОСТ 22178 Листы из титана и титановых сплавов. Технические условия. 6. ГОСТ 7566-81 Металлопродукция. Приемка, маркировка, упаковка, транспортирование и хранение. 7. ГОСТ 24297 Верификация закупленной продукции. Организация проведения и методы контроля. 8. СП 105-34-96 ПРОИЗВОДСТВО СВАРОЧНЫХ РАБОТ И КОНТРОЛЬ КАЧЕСТВА СВАРНЫХ СОЕДИНЕНИЙ ГОСТ 7502-98 Рулетки измерительные металлические. Технические условия 9. ГОСТ 14771-76 ДУГОВАЯ СВАРКА В ЗАЩИТНОМ ГАЗЕ. СОЕДИНЕНИЯ СВАРНЫЕ. 10. ГОСТ 27265-87 Проволока сварочная из титана и титановых сплавов. Технические условия. 11. ГОСТ 10157-73 Аргон газообразный и жидкий. 12. ГОСТ14249-2003 Сосуды и аппараты. Нормы и методы расчета на прочность. 13. РД 34.15.132-96 Сварка и контроль качества сварных соединений металлоконструкций зданий при сооружении промышленных объектов. |
Анализ при разработке технологии изготовления конструкции
|
|
Кормораздатчик мобильный электрифицированный: схема и процесс работы устройства...
Папиллярные узоры пальцев рук - маркер спортивных способностей: дерматоглифические признаки формируются на 3-5 месяце беременности, не изменяются в течение жизни...
Биохимия спиртового брожения: Основу технологии получения пива составляет спиртовое брожение, - при котором сахар превращается...
Состав сооружений: решетки и песколовки: Решетки – это первое устройство в схеме очистных сооружений. Они представляют...
© cyberpedia.su 2017-2024 - Не является автором материалов. Исключительное право сохранено за автором текста.
Если вы не хотите, чтобы данный материал был у нас на сайте, перейдите по ссылке: Нарушение авторских прав. Мы поможем в написании вашей работы!