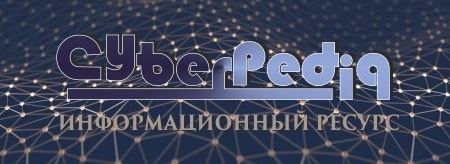
Автоматическое растормаживание колес: Тормозные устройства колес предназначены для уменьшения длины пробега и улучшения маневрирования ВС при...
Археология об основании Рима: Новые раскопки проясняют и такой острый дискуссионный вопрос, как дата самого возникновения Рима...
Топ:
Эволюция кровеносной системы позвоночных животных: Биологическая эволюция – необратимый процесс исторического развития живой природы...
Особенности труда и отдыха в условиях низких температур: К работам при низких температурах на открытом воздухе и в не отапливаемых помещениях допускаются лица не моложе 18 лет, прошедшие...
Интересное:
Аура как энергетическое поле: многослойную ауру человека можно представить себе подобным...
Инженерная защита территорий, зданий и сооружений от опасных геологических процессов: Изучение оползневых явлений, оценка устойчивости склонов и проектирование противооползневых сооружений — актуальнейшие задачи, стоящие перед отечественными...
Средства для ингаляционного наркоза: Наркоз наступает в результате вдыхания (ингаляции) средств, которое осуществляют или с помощью маски...
Дисциплины:
![]() |
![]() |
5.00
из
|
Заказать работу |
|
|
ПРОИЗВОДСТВО СТАЛИ
Сталь, как и чугун, является сплавом железа с углеродом, но с меньшим содержанием углерода, кремния, марганца, серы и фосфора. Исходными материалами для получения стали служат передельный чугун (жидкий или твердый) и стальной лом (скрап). В ходе выплавки стали решаются три основные задачи, определяющие качество стали:
1. Снижение содержания C, Si, Mn;
2. Снижение содержания S и P (рафинирование стали);
3. Снижение содержания кислорода (раскисление стали).
Снижения содержания C, Si, Mn добиваются за счет их окисления – выжигания. Окисление углерода и примесей обеспечивается за счет кислорода воздуха, технически чистого кислорода и кислорода оксидов (руда, окалина). Продукты окисления углерода монооксид углерода CO и диоксид углерода CO2 уходят в атмосферу печи и далее в дымовые газы. Примеси Si, Mn, P, S образуют соединения, которые не растворяются или плохо растворяются в стали и за счет этого переходят в шлак непосредственно или после взаимодействия с флюсом.
C+O2→CO
Si+O2→SiO2
Mn+O2→MnO
P+O2→P2O5
При выплавке стали окисляется и железо:
Fe+O2→FeO
FeO растворяется в стали в количестве около 1% при температуре 1500 ∘C и в количестве около 2% при температуре 1700 ∘C. В окислительный период плавки присутствие FeO в стали играет положительную роль, т.к. FeO отдает свой кислород на окисление C, Si, Mn, P, ускоряя процесс их выжигания:
C+FeO→Fe+CO
Si+FeO→Fe+SiO2
Mn+FeO→MnO
P+FeO→Fe+P2O5
Чем больше оксида железа присутствует в сталеплавильной ванне, тем активнее протекает процесс выплавки стали. Поэтому в окислительный период плавки в сталеплавильную печь вводят железную руду и окалину, содержащие оксиды железа.
Интенсивность окислительных процессов сильно зависит от температуры и протекают они в следующей последовательности: до 1300 ∘C Si, Mn, P, Fe; в интервале 1300−1400 ∘C Si, C, Mn, P, Fe и при температуре выше 1470 ∘C C, Si, Mn, P, Fe.
|
В начальный период плавки, когда температура стали относительно не велика, активнее идут реакции окисления Si, Mn, P, сопровождающиеся выделением тепла. Окисление углерода активно идет только при высокой температуре.
Удаление P и S (рафинирование стали). Фосфор и сера в стали являются вредными примесями. Фосфор придает стали хладноломкость – понижение прочности при низких температурах, а сера придает красноломкость – понижение прочности при высоких температурах. Уменьшение содержания фосфора и серы является важной задачей сталеплавильного процесса. Необходимым условием для удаления фосфора и серы является наличие в шлаке свободного оксида кальция CaO, способного связать фосфор и серу в нерастворимые в стали химические соединения. Для того, чтобы иметь в шлаке СаОСаО плавку необходимо вести в оснОвной печи, т.е. печи, футерованной оснОвными огнеупорными материалами на базе CaO и MgO.
В кислой печи удаление фосфора и серы невозможно.
Удаление серы (десульфурация). Сера присутствует в стали в виде сульфидов железа – FeS и сульфидов марганца – MnS. Сульфид железа хорошо растворяется в стали, сульфид марганца – плохо. Марганец обладает более высокой химической активностью по отношению к сере, чем железо, поэтому при невысоких температурах уже возможна реакция:
FeS+Mn→Fe+MnS
Сульфид марганца имеет невысокую плотность и переходит в шлак. Главные же реакции удаления серы идут за счет CaO в оснОвном шлаке и на границе металл – шлак:
[FeS] – в стали (FeS) – в шлаке
(FeS)+(CaO)→(CaS)+(FeO)
[FeS]+(CaO)→(CaS)+(FeO)
(MnS)+(CaO)→(CaS)+(MnO)
[MnS]+(CaO)→(CaS)+(Mn)
Для наиболее полного удаления серы необходимо периодически удалять (скачивать) шлак и вводить СаОСаО – свежеобожженную известь. Удалению серы способствует повышение температуры шлака. Такие условия создают электродуговые печи.
|
Удаление фосфора (дефосфорация). Процесс удаления фосфора из стали лучше всего протекает в окислительный период плавки при пониженных и умеренных температурах. Фосфорный ангидрид Р2О5 Может ошлаковыватся за счет монооксида железа FeO:
P2O5+FeO→P2O5·(FeO)3
Удалению фосфора способствует введение в печь железной руды, ведущее к образованию шлака богатого оксидами железа. Однако, соединение P2O5·(FeO)3 является непрочным и при высоких температурах оно разлагается:
P2O5·(FeO)3→3FeO+P2O5
При этом P2O5 восстанавливается углеродом и фосфор снова растворяется в стали:
P2O5+C→P+CO
Чем выше температура плавки, тем энергичнее восстанавливается фосфор.
Для того, чтобы предотвратить этот процесс необходимо удалять фосфорный шлак и поддерживать в шлаке высокое содержание CaO. CaO при умеренных температурах взаимодействует с (FeO)3·P2O5 c образованием более прочного соединения:
(FeO)3·P2O5+CaO→(CaO)4·P2O5+FeO
В кислых печах (футеровка динасовая – SiO2 нет условий для удаления фосфора. В шлаке преобладает кремнезем SiO2 и при введении извести она будет связана в соединение CaO·SiO2 и не сможет участвовать в реакциях, способствующих удалению фосфора и серы. В кислых печах можно выплавлять сталь только из исходных материалов, в которых содержание фосфора и серы ниже допустимого в стали, так что удаление фосфора и серы не является необходимым.
Раскисление стали. Повышенное содержание кислорода в стали виде FeO оказывает благоприятное влияние на ускорение процесса окисления примесей, ускорение плавки. Но в готовой стали кислород является вредной примесью, ухудшающей механические свойства, особенно при повышенных температурах. Поэтому завершающим этапом выплавки стали является ее раскисление – восстановление FeO, растворенного в стали.
Для раскисления стали используют раскислители – химические элементы, обладающие более высокой химической активностью по отношению к кислороду, чем железо.
Используются два способа раскисления:
Осаждающее раскисление проводят введением в жидкую сталь растворимых раскислителей (ферромарганец, ферросилиций, алюминий и др.). Раскисление проводится в печи или в ковше.
FeO+Mn→Fe+MnO
FeO+Si→Fe+SiO2
FeO+Al→Fe+Al2O3
После раскисления содержание FeO снижается примерно до 0,1%, что соответствует 0,02 – 0,03% кислорода в стали.
|
Образующиеся при осаждающем раскислении оксиды Si, Mn, Al обладают меньшей плотностью чем сталь и всплывают в шлак. Однако, этот процесс может не завершиться полностью и сталь загрязняется неметаллическими включениями, что снижает ее качество.
Диффузионное раскисление стали проводят за счет раскисления шлака. Нарушение равновесной концентрации FeO между сталью и шлаком ведет к переходу FeO в шлак. При этом продукты раскисления образуются в шлаке и не загрязняют сталь, а восстановленное железо переходит в сталь. Наиболее благоприятные условия для диффузионного раскисления создает высокая температура шлака в электродуговых печах. Благоприятные условия для хорошего раскисления стали создают кислые печи. В кислых печах шлак содержит около 60% SiO2. Кремнезем связывает оксид железа в соединение FeO·SiO2. Это приводит к тому, что в стали после длительной выдержки под слоем кислого шлака содержание FeO резко уменьшается и для ее окончательного раскисления достаточно небольшого количества ферромарганца.
В кислых печах можно осуществлять кремневосстановительный процесс плавки, при котором сталь раскисляется кремнием, восстановленным из кремнезема:
SiO2+C→Si+CO
исноваповторениеFeO+Si→Fe+SiO2 и снова повторение.
Содержание кислорода в стали понижается.
За счет хорошего раскисления сталь, выплавленная в кислых печах, отличается Повышенной плотностью, однородностью, повышенной вязкостью, низким содержанием неметаллических включений. Однако, необходимость использования чистых по фосфору и сере (не более 0,025%) исходных материалов удорожает процесс и ограничивает его использование область выплавки высококачественных высоколегированных сталей (шарикоподшипниковых и др.).
Другой особенностью плавки в кислых печах является то, что слой кремнистого шлака почти непроницаем для кислорода воздуха и окисление углерода идет за счет кислорода оксида железа. Процесс идет медленно и лишний углерод в шихте приводит к увеличению продолжительности плавки. Это снижает его экономичность.
Разливка стали
Заключительной стадией любого процесса выплавки стали является выпуск стали из печи в ковш и разливка ее в слитки.
|
Сталеразливочный ковш имеет форму усеченного конуса, несколько уширенного кверху. Корпус ковша стальной, футерован внутри огнеупорным кирпичом. Емкость ковша определяется емкостью печи и может превышать 400 тонн. Высота таких ковшей около 6м, а малый диаметр около 5,5 м. В дне ковша находится разливочный стакан с пробкой – стопором с ручным или механизированным управлением.
После выпуска сталь выдерживают в ковше 5 – 15 минут в зависимости от ее температуры, марки стали и количества металла. Ковш под разливку нагревают до 700 ∘C, температура в начале разливки 1480–1540 ∘C, в конце 1390–1450 ∘C. Во время выдержки в ковше из металла удаляется часть продуктов растворения и газы, выравнивается состав металла.
Для получения из жидкой стали слитков используют разливку стали в изложницы и непрерывную разливку. Небольшой процент (около 5%) выплавленной стали используется для получения фасонных стальных отливок. В этом случае сталь из ковша заливается в специальные литейные формы.
Изложницы – металлические (чаще всего чугунные) формы для получения стальных слитков. Изложницы отливаются из жаростойкого чугуна и представляют собой толстостенную форму, открытую сверху и снизу (иногда они имеют дно). Форма поперечного сечения изложницы определяется назначением слитка, маркой стали и др. Высота изложниц больше их среднего поперечного размера в 2,5 – 3 раза. Внутренние стенки изложниц выполняются с небольшой конусностью, что облегчает извлечение (раздевание) слитка. Для удобства перемещения изложницы имеют цапфы или скобы.
Для слитков, подвергаемых затем прокатке, применяются изложницы квадратного или прямоугольного сечения. Для слитков, предназначенных для ковки и штамповки – многоугольные (восьмигранные). Для прокатки труб слитки получают в изложницах круглого сечения. Для прокатки листа удобны слитки прямоугольного сечения.
Слитки для прокатки имеют массу от 200 кг до 20 и более тонн, для ковки до 300 тонн. Из мелких слитков в 250-300 кг получают проволоку.
Перед заливкой стенки изложниц очищают и покрывают смазкой из каменноугольной смолы и графита для увеличения срока службы и предохранения от припекания стали. Стойкость изложниц от 100 (для крупных слитков) до 300 (для мелких) заливок.
Способы разливки стали в изложницы. Существуют два способа разливки стали в изложницы – разливка сверху и разливка снизу (сифонная).
Разливка стали сверху заключается в заполнении изложницы жидким металлом непосредственно из ковша или через воронку. Изложницы при этом устанавливают на толстые чугунные плиты – поддоны и по периметру обмазывают огнеупорным материалом.
|
При разливке сверху можно предельно снизить температуру заливки, что хорошо сказывается на качестве слитка. Разливка сверху сопровождается сильным разбрызгиванием, затвердевшие на стенках брызги ухудшают качество поверхности слитка и поэтому перед горячей обработкой слитки нужно подвергать обдирке. При заливке сверху создаются также неблагоприятные условия для удаления газов.
Разливка снизу (сифонная).
Изложницы устанавливают не на металлические поддоны, а на специальные керамические пустотелые плиты (сифонный припас), собранные в чугунном поддоне. Эти плиты имеют внутренние каналы, объединяющие их в единую литниковую систему. Сталь из ковша заливается в центральный стояк, выложенный шамотными трубками, и поступает одновременно в целый ряд изложниц (до 40).
Отсутствие брызг при заполнении изложницы снизу, позволяет получать более чистую поверхность слитка, но размывание металлом огнеупоров сифонного припаса приводит к образованию неметаллических включений. Имеет место также потеря металла в литниковой системе, более трудоемка подготовка изложниц к заливке, сифонный припас используется однократно.
Однако, дополнительные затраты на сифонную разливку полностью окупаются уменьшением стоимости зачистки поверхности слитков.
Практически применяют оба способа. Выбор способа зависит от множества конкретных причин.
Непрерывная разливка стали
Это наиболее совершенный способ разливки стали. Сущность способа непрерывной разливки состоит в следующем.
Жидкая сталь через промежуточное разливочное устройство 1 поступает в медный водоохлаждаемый кристаллизатор 2.
Кристаллизатор имеет высоту 800-1200мм, сечение его может быть различным, например: 150 на 300, 600 на 1200, 350 на 2200мм для получения прямоугольных слитков (слябов) или от 150 на 150 до 400 на 400мм для получения квадратных слитков (блюмов).
В кристаллизатор перед заливкой вводится временное дно – затравка с пазом в форме ласточкина хвоста (углубление).
Вследствие интенсивного охлаждения жидкий металл затвердевает у стенок кристаллизатора и затравки. Затравка при помощи тянущих валиков 3 движется вниз, вытягивая за собой затвердевающий слиток. Слиток выходит из кристаллизатора с еще жидкой сердцевиной и затвердевает полностью после вторичного охлаждения водяными струями 4.
Скорость движения слитка 0,5 – 2,5 м/мин. Ограничивается выходом наружу жидкой сердцевины при резке. Резка газокислородная или гидравлическими ножницами. Во время резки режущее устройство движется вместе со слитком. С целью уменьшения высоты установки для непрерывной разливки стали слиток изгибают под углом 90° и он от движения по вертикали переходит к движению по горизонтали (установка радиальной разливки).
Способ непрерывной разливки позволяет избежать использования дорогостоящего и громоздкого оборудования – изложниц, разливочных устройств, обжимных прокатных станов и др. Позволяет сократить производственный цикл, повысить производительность труда, увеличить выход годного металла (отходы 2 – 3% вместо 15 – 25% при разливке в изложницы).
Классификация сталей
Стали подразделяются (классифицируются) по нескольким признакам:
1. по химическому составу
2. по назначению (применению)
3. по качеству
4. по микроструктуре
Химический состав стали является основным классификационным признаком, им определяется марка стали.
По химическому составу сталь делят на углеродистую (нелегированную) и легированную.
Углеродистой сталью называют сплав железа с углеродом, содержащий углерода от 0,02 до 2.14% и примеси марганца до 0,9%, кремния до 0,5%, серы до 0,06%, фосфора до 0,07%.Главной составляющей, определяющей свойства стали, является углерод.
В зависимости от количества углерода углеродистую сталь подразделяют на:
· низкоуглеродистую – углерода до 0,25%
· среднеуглеродистую - углерода от 0,25 до 0,6%
· высокоуглеродистую – углерода от 0,6% до 2,0%
Такое деление необходимо для выбора технологического процесса обработки углеродистых сталей.
По назначению (применению) различают следующие углеродистые стали:
1. конструкционные:
o а) строительные – низкоуглеродистые
o б) машиностроительные – среднеуглеродистые и высокоуглеродистые
2. инструментальные;
3. специального назначения.
По качеству стали подразделяют на:
· сталь обыкновенного качества
· сталь качественную
· сталь высококачественную
· сталь особовысококачественную.
Углеродистые стали
Конструкционная углеродистая сталь. Конструкционной углеродистой сталью называют сталь, содержащую углерода до 0,6% (в некоторых случаях до 0,85%).
По качеству углеродистая конструкционная сталь делится на сталь обыкновенного качества и сталь качественную.
Сталь углеродистая конструкционная обыкновенного качества (ГОСТ 380 – 2005). Применяется для изготовления изделий не ответственного назначения: строительных конструкций, крепежных деталей, листового и профильного проката, заклепок, труб, арматуры, проволоки и др.
По степени раскисленности она может быть кипящей, полуспокойной и спокойной. Это находит отражение в маркировке этих сталей в виде букв «кп», «пс» и «сп».
Маркировка этих сталей буквенно-цифровая: от Ст0 до Ст6, где буквы означают «сталь», а цифры порядковый номер. Содержание углерода в этих сталях находится в пределах, повышаясь с увеличением порядкового номера.
Сталь углеродистая конструкционная качественная (ГОСТ 1050-88). Качественную сталь применяют для изделий, требующих материала с большей пластичностью и сопротивлением удару, деталей, работающих при повышенных давлениях, для зубчатых колес, труб, винтов, болтов, для сварных изделий, для деталей, подлежащих цементации и др
Качественная конструкционная углеродистая сталь отличается по свойствам от стали обыкновенного качества большей прочностью, пластичностью и сопротивлением ударным нагрузкам.
Маркировка этих сталей цифровая от 05 до 60, например, «Сталь 45». Двузначное число указывает на содержание углерода в сотых долях процента.
Сталь углеродистая инструментальная. По ГОСТ 1435 – 20005 «Сталь инструментальная нелегированная».
Углеродистой (нелегированной) инструментальной сталью называется сталь с содержанием углерода от 0,7 до 1,4%. Эту сталь применяют после термообработки (закалка и отпуск).
Инструментальная углеродистая сталь подразделяется на качественную и высококачественную.
Маркировка этих сталей буквенно-цифровая:
Марки качественной стали: от У7 до У13.
Марки высококачественной стали: от У7А до У13А.
Буква «У» обозначает «сталь углеродистая (нелегированная), т.е. свидетельствует о принадлежности этой стали к определенной группе. Цифры указывают на среднее содержание углерода в десятых долях процента. Индекс «А» в конце марки указывает на то, что эта сталь высококачественная. Высококачественная сталь отличается более узкими пределами содержания входящих в состав элементов и низким содержанием вредных примесей – серы и фосфора, большим содержанием легирующих элементов – хрома и никеля.
Содержание серы в качественной инструментальной стали 0,03%, в высококачественной – 0,02%; фосфора 0,035% и 0,030%.
Твердость высококачественной стали не выше твердости качественной, однако, высококачественная сталь прочнее, содержит меньше неметаллических включений, лучше противостоит действию ударных нагрузок, дает при закалке меньше брака.
Углеродистые инструментальные стали используются для изготовления режущего, измерительного и штампового инструмента. После термической обработки инструменты обладают высокой прочностью и твердостью (до HRC 60-65), а также высокой износостойкостью, что важно для сохранения формы и размеров инструмента.
К недостаткам углеродистой инструментальной стали относятся невозможность сочетания прочности и твердости с пластичностью и потеря твердости и режущей способности при нагревании до 200 ∘ и потеря прочности при высокой температуре.
Поэтому инструментальные углеродистые стали применяют обычно для изготовления измерительного инструмента (штангенциркули, калибры, нутромеры и т.п.) и для режущего инструмента, работающего при низких скоростях резания (напильников, зубил, метчиков, шаберов, для хвостовиков сверл и разверток и т.п.).
Углеродистые стали специального назначения. Примерами углеродистых сталей специального назначения могут служить следующие стали:
1. сталь для глубокой вытяжки с содержанием углерода не более 0,2%, обладающая хорошей пластичностью,
2. электротехническая сталь с содержанием углерода не более 0,05% (легирована кремнием до 4%).
3. стали с повышенной обрабатываемостью резанием (старое название – автоматные стали) с повышенным содержанием серы до 0,30% и фосфора до 0,15%. Марки А12, А20, А30 и др.
Эти стали удобно использовать для изготовления изделий не ответственного назначения на станках-автоматах, так как они образуют короткую ломкую стружку, что важно при работе скоростных автоматов. Стойкость режущего инструмента при обработке автоматных сталей в 2 – 3 раза выше, чем при обработке обыкновенных и качественных конструкционных сталей.
Легированные стали
Легированной сталью называется сталь, в состав которой, наряду со всеми элементами, входящими в углеродистую сталь, входят еще специально введенные добавки – легирующие элементы (хром, вольфрам, никель, кобальт и др.).
Влияние легирующих элементов на свойства стали определяется не только природой и количеством легирующих элементов, но и их взаимодействие с железом, углеродом и между собой.
По отношению к углероду легирующие элементы делят на две группы:
А. образующие с углеродом химические соединения – карбиды (хром, марганец, титан, ванадий, вольфрам, молибден и др.)
Б. не образующие карбидов (никель, алюминий, кремний и др.).
Все стали, легированные карбидообразующими элементами, обладают высокой твердостью, повышенным сопротивлением износу.
Легирующие элементы оказывают влияние на аллотропические превращения железа. Такие элементы, как хром, вольфрам, молибден, титан и др. повышают температуру превращения гамма-железа в альфа-железо (критическую точку А3), т.е. сужают область твердых растворов гамма-железа. Никель, марганец, медь, цинк и др. понижают температуру превращения гамма-железа в альфа-железо (критическую точку А3), т.е. расширяют область твердых растворов гамма-железа, что может иметь важное значение для термической обработки сталей.
Легирующие элементы оказывают влияние на превращения, протекающие в стали в твердом состоянии (перлитные, мартенситные), а также на превращения при отпуске. Большинство легирующих элементов понижают точку начала мартенситного превращения, что также имеет практически важное значение, так как при закалке легированных сталей можно применять более медленно охлаждающие средства. В некоторых высококачественных сталях структуру мартенсита можно получить даже после охлаждения на воздухе.
Легированную сталь подразделяют по количеству входящих легирующих элементов на:
1. низколегированную с добавками не более 2,5%
2. среднелегированную с добавками от 2,5% до 10%
3. высоколегированную с добавками более 10%
Маркировка легированных сталей буквенно-цифвовая. Приняты следующие буквенные обозначения основных легирующих элементов: марганец – Г, кремний – С, хром – Х, ванадий – Ф, титан – Т, молибден – М, медь – Д, алюминий – Ю, ниобий – Б, бор – Р, азот – А, редкоземельные металлы – Ч.
Легированные стали применяют как конструкционные, инструментальные и как стали с особыми свойствами.
Конструкционные легированные стали (30ХГС, 30ХГСА, 30ХМА, 38ХМЮА, 18ХГТ, 40Х, 40ХГ и др.) маркируют следующим образом: на первом месте стоит число, указывающая процентное содержание углерода. Далее стоят буквы, обозначающие легирующие элементы, с последующими числами процентного содержания легирующих элементов. Если эти числа отсутствуют, то содержание легирующего элемента соответствует примерно 1,0 – 1,5%. Буква «А» в конце маркировки указывает, что данная сталь является высококачественной.
Наиболее широко применяют в конструкционных сталях такие легирующие элементы, как хром, марганец, кремний. В состав стали они вводятся в количестве от 0,8 до 2%, придавая стали высокую прочность, высокую твердость, упругость. Все они недорогие.
В зависимости от названия легирующих элементов стали бывают хромистые (15Х, 40Х), марганцовистые (10Г2,50Г2), кремнистые (55С2, 60С2), хромомарганцовистые (18ХГ), хромомарганцовокремнистые (30ХГС, (30ХГСА), хромоникелевые (20ХН, 12Х2Н4А) и др.
Инструментальные легированные стали (Х, 9Х, 9ХС, ХВГ, Х12, Х12М, 5ХНМ и др.) маркируют так: на первом месте стоят цифры, указывающие содержание углерода в десятых долях процента, а если цифр нет, то это указывает на содержание углерода примерно в 1%. Далее следуют буквы и цифры, указывающие содержание легирующих элементов в целых процентах. Буква А в конце маркировки, указывающая на высококачественность стали, здесь не ставится, так как все эти стали являются высококачественными.
Для выплавки легированной инструментальной стали используют дорогие, дефицитные легирующие элементы (вольфрам, ванадий, кобальт, титан), которые обеспечивают стали теплостойкость, высокую твердость и хорошие режущие свойства.
Легированные стали особого назначения – это стали с особыми физическими и химическими свойствами: магнитные, немагнитные, коррозионно-стойкие (нержавеющие), жаростойкие, жаропрочные, кислотостойкие и др.
Магнитные стали подразделяют на магнитотвердые и магнитомягкие. Магнитотвердые стали применяют для изготовления постоянных магнитов. Основными легирующими элементами являются хром и кобальт. Марки таких сталей: ЕХ, ЕХ3,Е7В5, ЕХ5К5, ЕХ9К15М.
Для постоянных магнитов, кроме этого, широко применяют железоникелевые и железоникелекремнисые сплавы.
Из магнитомягких сталей и сплавов, обладающих высокой магнитной проницаемостью, делают сердечники трансформаторов и т. д.
Немагнитные стали заменяют цветные металлы и сплавы. Такие стали широко применяются в приборостроении. Основной легирующий элемент – никель.
Коррозионно-стойкие (нержавеющие) стали бывают хромистые и хромоникелевые. Они широко используются в химическом машиностроении, турбостроении, медицине. Примеры маркировки: 30Х13, 40Х13, 12Х18Н9, 12Х18Н10Т.
Жаропрочные и жаростойкие (окалиностойкие) стали применяют для изготовления деталей, работающих при высоких температурах (детали газовых и паровых турбин, детали реактивных двигателей). Примеры маркировки: 4Х18Н25, 4Х14Н14В2М.
Рассмотренные системы маркировки охватывают большинство применяемых легированных сталей, но существуют стали, в маркировке которых с помощью особой буквы указывают на принадлежность стали к определенной группе. Например, Р для быстрорежущих сталей: Р18, Р9, Р6М5, Ш для шарикоподшипниковых сталей: ШХ15 и др.
ПРОИЗВОДСТВО СТАЛИ
Сталь, как и чугун, является сплавом железа с углеродом, но с меньшим содержанием углерода, кремния, марганца, серы и фосфора. Исходными материалами для получения стали служат передельный чугун (жидкий или твердый) и стальной лом (скрап). В ходе выплавки стали решаются три основные задачи, определяющие качество стали:
1. Снижение содержания C, Si, Mn;
2. Снижение содержания S и P (рафинирование стали);
3. Снижение содержания кислорода (раскисление стали).
Снижения содержания C, Si, Mn добиваются за счет их окисления – выжигания. Окисление углерода и примесей обеспечивается за счет кислорода воздуха, технически чистого кислорода и кислорода оксидов (руда, окалина). Продукты окисления углерода монооксид углерода CO и диоксид углерода CO2 уходят в атмосферу печи и далее в дымовые газы. Примеси Si, Mn, P, S образуют соединения, которые не растворяются или плохо растворяются в стали и за счет этого переходят в шлак непосредственно или после взаимодействия с флюсом.
C+O2→CO
Si+O2→SiO2
Mn+O2→MnO
P+O2→P2O5
При выплавке стали окисляется и железо:
Fe+O2→FeO
FeO растворяется в стали в количестве около 1% при температуре 1500 ∘C и в количестве около 2% при температуре 1700 ∘C. В окислительный период плавки присутствие FeO в стали играет положительную роль, т.к. FeO отдает свой кислород на окисление C, Si, Mn, P, ускоряя процесс их выжигания:
C+FeO→Fe+CO
Si+FeO→Fe+SiO2
Mn+FeO→MnO
P+FeO→Fe+P2O5
Чем больше оксида железа присутствует в сталеплавильной ванне, тем активнее протекает процесс выплавки стали. Поэтому в окислительный период плавки в сталеплавильную печь вводят железную руду и окалину, содержащие оксиды железа.
Интенсивность окислительных процессов сильно зависит от температуры и протекают они в следующей последовательности: до 1300 ∘C Si, Mn, P, Fe; в интервале 1300−1400 ∘C Si, C, Mn, P, Fe и при температуре выше 1470 ∘C C, Si, Mn, P, Fe.
В начальный период плавки, когда температура стали относительно не велика, активнее идут реакции окисления Si, Mn, P, сопровождающиеся выделением тепла. Окисление углерода активно идет только при высокой температуре.
Удаление P и S (рафинирование стали). Фосфор и сера в стали являются вредными примесями. Фосфор придает стали хладноломкость – понижение прочности при низких температурах, а сера придает красноломкость – понижение прочности при высоких температурах. Уменьшение содержания фосфора и серы является важной задачей сталеплавильного процесса. Необходимым условием для удаления фосфора и серы является наличие в шлаке свободного оксида кальция CaO, способного связать фосфор и серу в нерастворимые в стали химические соединения. Для того, чтобы иметь в шлаке СаОСаО плавку необходимо вести в оснОвной печи, т.е. печи, футерованной оснОвными огнеупорными материалами на базе CaO и MgO.
В кислой печи удаление фосфора и серы невозможно.
Удаление серы (десульфурация). Сера присутствует в стали в виде сульфидов железа – FeS и сульфидов марганца – MnS. Сульфид железа хорошо растворяется в стали, сульфид марганца – плохо. Марганец обладает более высокой химической активностью по отношению к сере, чем железо, поэтому при невысоких температурах уже возможна реакция:
FeS+Mn→Fe+MnS
Сульфид марганца имеет невысокую плотность и переходит в шлак. Главные же реакции удаления серы идут за счет CaO в оснОвном шлаке и на границе металл – шлак:
[FeS] – в стали (FeS) – в шлаке
(FeS)+(CaO)→(CaS)+(FeO)
[FeS]+(CaO)→(CaS)+(FeO)
(MnS)+(CaO)→(CaS)+(MnO)
[MnS]+(CaO)→(CaS)+(Mn)
Для наиболее полного удаления серы необходимо периодически удалять (скачивать) шлак и вводить СаОСаО – свежеобожженную известь. Удалению серы способствует повышение температуры шлака. Такие условия создают электродуговые печи.
Удаление фосфора (дефосфорация). Процесс удаления фосфора из стали лучше всего протекает в окислительный период плавки при пониженных и умеренных температурах. Фосфорный ангидрид Р2О5 Может ошлаковыватся за счет монооксида железа FeO:
P2O5+FeO→P2O5·(FeO)3
Удалению фосфора способствует введение в печь железной руды, ведущее к образованию шлака богатого оксидами железа. Однако, соединение P2O5·(FeO)3 является непрочным и при высоких температурах оно разлагается:
P2O5·(FeO)3→3FeO+P2O5
При этом P2O5 восстанавливается углеродом и фосфор снова растворяется в стали:
P2O5+C→P+CO
Чем выше температура плавки, тем энергичнее восстанавливается фосфор.
Для того, чтобы предотвратить этот процесс необходимо удалять фосфорный шлак и поддерживать в шлаке высокое содержание CaO. CaO при умеренных температурах взаимодействует с (FeO)3·P2O5 c образованием более прочного соединения:
(FeO)3·P2O5+CaO→(CaO)4·P2O5+FeO
В кислых печах (футеровка динасовая – SiO2 нет условий для удаления фосфора. В шлаке преобладает кремнезем SiO2 и при введении извести она будет связана в соединение CaO·SiO2 и не сможет участвовать в реакциях, способствующих удалению фосфора и серы. В кислых печах можно выплавлять сталь только из исходных материалов, в которых содержание фосфора и серы ниже допустимого в стали, так что удаление фосфора и серы не является необходимым.
Раскисление стали. Повышенное содержание кислорода в стали виде FeO оказывает благоприятное влияние на ускорение процесса окисления примесей, ускорение плавки. Но в готовой стали кислород является вредной примесью, ухудшающей механические свойства, особенно при повышенных температурах. Поэтому завершающим этапом выплавки стали является ее раскисление – восстановление FeO, растворенного в стали.
Для раскисления стали используют раскислители – химические элементы, обладающие более высокой химической активностью по отношению к кислороду, чем железо.
Используются два способа раскисления:
Осаждающее раскисление проводят введением в жидкую сталь растворимых раскислителей (ферромарганец, ферросилиций, алюминий и др.). Раскисление проводится в печи или в ковше.
FeO+Mn→Fe+MnO
FeO+Si→Fe+SiO2
FeO+Al→Fe+Al2O3
После раскисления содержание FeO снижается примерно до 0,1%, что соответствует 0,02 – 0,03% кислорода в стали.
Образующиеся при осаждающем раскислении оксиды Si, Mn, Al обладают меньшей плотностью чем сталь и всплывают в шлак. Однако, этот процесс может не завершиться полностью и сталь загрязняется неметаллическими включениями, что снижает ее качество.
Диффузионное раскисление стали проводят за счет раскисления шлака. Нарушение равновесной концентрации FeO между сталью и шлаком ведет к переходу FeO в шлак. При этом продукты раскисления образуются в шлаке и не загрязняют сталь, а восстановленное железо переходит в сталь. Наиболее благоприятные условия для диффузионного раскисления создает высокая температура шлака в электродуговых печах. Благоприятные условия для хорошего раскисления стали создают кислые печи. В кислых печах шлак содержит около 60% SiO2. Кремнезем связывает оксид железа в соединение FeO·SiO2. Это приводит к тому, что в стали после длительной выдержки под слоем кислого шлака содержание FeO резко уменьшается и для ее окончательного раскисления достаточно небольшого количества ферромарганца.
В кислых печах можно осуществлять кремневосстановительный процесс плавки, при котором сталь раскисляется кремнием, восстановленным из кремнезема:
SiO2+C→Si+CO
исноваповторениеFeO+Si→Fe+SiO2 и снова повторение.
Содержание кислорода в стали понижается.
За счет хорошего раскисления сталь, выплавленная в кислых печах, отличается Повышенной плотностью, однородностью, повышенной вязкостью, низким содержанием неметаллических включений. Однако, необходимость использования чистых по фосфору и сере (не более 0,025%) исходных материалов удорожает процесс и ограничивает его использование область выплавки высококачественных высоколегированных сталей (шарикоподшипниковых и др.).
Другой особенностью плавки в кислых печах является то, что слой кремнистого шлака почти непроницаем для кислорода воздуха и окисление углерода идет за счет кислорода оксида железа. Процесс идет медленно и лишний углерод в шихте приводит к увеличению продолжительности плавки. Это снижает его экономичность.
СОВРЕМЕННЫЕ СПОСОБЫ ПРОИЗВОДСТВА СТАЛИ
В настоящее время используются три основных способа выплавки стали: выплавка стали в мартеновских печах, выплавка стали в кислородных конверторах и выплавка стали в электропечах. Однако, значимость этих способов сильно отличается. Так доля мартеновского способа, которая в недавнем прошлом составляла около 70%, уменьшилась почти в 10 раз, уступив ведущее место кислородным конверторам примерно с 70% выплавки и второе место электропечам с долей около 20%.
Мартеновский способ оставался основным на протяжении более 100 лет. Мартеновская печь, построенная в 1865 году французскими металлургами отцом и сыном Мартенами, и названная по их имени была выдающимся изобретением. Мартеновская печь решила проблему переработки стального лома и выплавки стали из твердого чугуна. Имя Мартенов осталось и в названии структуры закаленной стали – мартенсит.
В чем был секрет изобретения? Мартены создали пламенную печь регенеративного типа, в которой плавка велась за счет тепла газового пламени, а газ и воздух, вдуваемые в печь, подогревались теплом отходящих дымовых газов в двух попеременно работающих регенераторах. Это позволило резко увеличить температуру в рабочем пространстве печи и расширить ее технологические возможности.
Мы не будем здесь останавливаться на рассмотрении конструкции мартеновской печи и технологии выплавки стали в ней. Прочитать об этом уходящем способе можно в любом учебнике по нашему курсу.
|
|
Историки об Елизавете Петровне: Елизавета попала между двумя встречными культурными течениями, воспитывалась среди новых европейских веяний и преданий...
Типы сооружений для обработки осадков: Септиками называются сооружения, в которых одновременно происходят осветление сточной жидкости...
Археология об основании Рима: Новые раскопки проясняют и такой острый дискуссионный вопрос, как дата самого возникновения Рима...
Организация стока поверхностных вод: Наибольшее количество влаги на земном шаре испаряется с поверхности морей и океанов (88‰)...
© cyberpedia.su 2017-2024 - Не является автором материалов. Исключительное право сохранено за автором текста.
Если вы не хотите, чтобы данный материал был у нас на сайте, перейдите по ссылке: Нарушение авторских прав. Мы поможем в написании вашей работы!