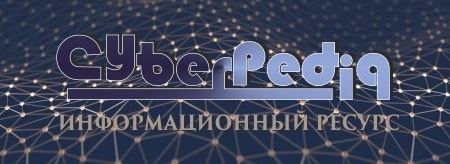
Типы сооружений для обработки осадков: Септиками называются сооружения, в которых одновременно происходят осветление сточной жидкости...
Наброски и зарисовки растений, плодов, цветов: Освоить конструктивное построение структуры дерева через зарисовки отдельных деревьев, группы деревьев...
Топ:
Эволюция кровеносной системы позвоночных животных: Биологическая эволюция – необратимый процесс исторического развития живой природы...
Оценка эффективности инструментов коммуникационной политики: Внешние коммуникации - обмен информацией между организацией и её внешней средой...
Интересное:
Отражение на счетах бухгалтерского учета процесса приобретения: Процесс заготовления представляет систему экономических событий, включающих приобретение организацией у поставщиков сырья...
Подходы к решению темы фильма: Существует три основных типа исторического фильма, имеющих между собой много общего...
Финансовый рынок и его значение в управлении денежными потоками на современном этапе: любому предприятию для расширения производства и увеличения прибыли нужны...
Дисциплины:
![]() |
![]() |
5.00
из
|
Заказать работу |
|
|
Анализ представлен в табл.1.
Таблица 1 – Технологичные и нетехнологичные элементы детали
Технологичные элементы | Нетехнологичные элементы | ||
Элемент | Пояснение | Элемент | Пояснение |
![]() | Не требует контроля глубины отверстия, т.к. оно сквозное. | ![]() | Требуют контроля глубины сверления, т.к. отверстия несквозные. |
![]() | Отверстия диаметром 4,2 располагаются на одной размерной линии. |
![]() | Требует проектирование специального инструмента. |
![]() | Тонкие стенки, не позволяют использовать высокопроизво-дительные методы обработки. Требует контроля глубины. |
Анализ технологических условий
Анализ технических условий представлен в табл. 2.
Таблица 2 – Анализ технических условий
Конструкторский параметр | Способ обеспечения | Контроль |
![]() | Метод пробных проходов и промеров | Микрометр МГ Н25 ГОСТ 6507-90 |
![]() | Метод пробных проходов | Профилометр 130 ГОСТ 19300-86 |
Отклонение от круглости | Метод пробных проходов и промеров | Кругломер-250-2 ГОСТ 17353-89 |
Торцевое биение
![]() | Обработку производить за одну установку | ![]() |
Анализ технологического процесса
Составили улучшенный план обработки, воспользовавшись заводским технологическим процессом (Рис. 2.1).
Рис. 2.1 Анализ технологического процесса
1. Смена заготовки.
Заготовка не приближена к конфигурации детали, следовательно, высокий расход материала.
2. Повышение точности обработки.
Операции 030 и 070 Токарные: принцип единства баз снижает погреш-ности взаимного расположения обработанных поверхностей.
3. Сокращение рабочих площадей.
|
Токарные, фрезерная и сверлильная операции выполнены на одном станке.
4. Повышение точности обработки.
Операции 080 и 090 Фрезерные: принцип единства баз снижает погрешности взаимного расположения обработанных поверхностей.
Вывод: Выбор метода получения заготовки – это важный этап в проектировании технологического процесса. От выбора заготовки, т. е. установления метода ее получения, формы, величины припусков, напусков и др., зависит масса заготовки и объем последующей механической обработки детали. Увеличение припусков на обработку ведет к возрастанию расхода металла и трудности обработки, повышает затраты на режущий инструмент, ремонт станков, электроэнергию и т. п. Поэтому был выбран метод получения заготовки – прямое лазерное спекание.
Аналитический обзор
Постепенно технологии 3D печати входят в нашу жизнь, открывая новые возможности в самых разных областях деятельности. 3D печать позволяет создать трехмерную модель какого-то изделия на компьютере и за считанное время, получить полноценный физический объект, соответствующий заданным параметрам. Преимущества использования современных 3D принтеров очевидны: снижение себестоимости изготовления продукции и сокращение сроков ее появления на рынке, моделирование элементов любой формы и сложности, быстрота и высокая точность изготовления, возможность использования разных материалов. В ближайшие годы снижение стоимости 3D принтеров должно открыть новые перспективы для реализации трехмерной печати [5].
Технологии 3D-печати
1. Экструзионная 3D-печать
Процесс печати методом послойного наплавления подразумевает создание слоев за счет экструзии быстро застывающего материала в виде микрокапель или тонких струй. Экструдер (машина для размягчения (пластикации) материалов и придания им формы путем продавливания через профилирующий инструмент (т. н. экструзионную головку), сечение которого соответствует конфигурации изделия нагревает) материал до температуры плавления с последующим выдавливанием расплавленной массы через сопло. Сам экструдер приводится в движение пошаговыми двигателями или сервомоторами, обеспечивающими позиционирование печатной головки в трех плоскостях. Перемещение экструдера контролируется производственным программным обеспечением, привязанным к микроконтроллеру. [1]
|
Рис. 3.1. Схема устройства 3D-принтера экструзивного типа:
1 – корпус, 2 – закрепленные на нем направляющие,
3 – печатающая головка, 4 – шаговые двигатели, 5 – рабочий стол;
6 – управляющая электроника
Используемые материалы: термопластичные полимеры (такие как полилактид (ПЛА), акрилонитрилбутадиенстирол (АБС-пластик) и др.)
2. Ламинирование
Изготовление объектов методом ламинирования (LOM) – технология быстрого прототипирования, разработанная компанией Helisys Inc. Метод подразумевает последовательное склеивание листового материала (бумаги, пластика, металлической фольги) с формированием контура каждого слоя с помощью лазерной резки. Объекты, производимые этим методом, обычно подлежат дополнительной механической обработке после печати. Толщина наносимого слоя напрямую зависит от толщины используемого листового материала. [1]
Рис. 3.2 Схема процесса ламинирования
3. Струйная трехмерная печать
Как и другие технологии аддитивного производства, струйная
трехмерная печать подразумевает послойное построение физических
объектов на основе цифровой трехмерной модели. В качестве расход-
ных материалов используются различные порошки, гипс, пластики, металлические порошки, песчаные смеси, наносимые последователь-ными тонкими слоями. Контуры модели вычерчиваются печатной го-ловкой, наносящей связующий материал. Таким образом частицы каждого нового слоя склеиваются между собой и с предыдущими слоями до образования готовой трехмерной модели. [1]
Рис. 3.3 Схема процесса струйной трехмерной печати
4. Электронно-лучевая плавка (проволочная)
Концепция EBF основана на постройке «практически готовых форм» (Near-net-shape в англоязычной терминологии). Это означает, что изделия создаются на основе трехмерных цифровых моделей с настолько высокой точностью, что механическая обработка и доводка изделий практически не требуются.
|
Технология использует электронные излучатели высокой мощности в вакуумной камере для плавки металла. Электронный пучок
передвигается по рабочей поверхности, повторяя контуры цифровой
модели, в то время как металлическая проволока постепенно подается
в точку фокусирования пучка. Расплавленный материал немедленно
застывает, формируя прочные слои заданной модели. Процесс повторяется до построения цельной модели, требующей лишь минимальной обработки внешней поверхности. [1]
Рис. 3.4 Схема процесса электронно-лучевой плавки
Используемые материалы: практически любые металлические сплавы.
5. Прямое лазерное спекание металлов [1]
Процесс печати включает использование трехмерных моделей в формате STL в качестве чертежей для построения физических моделей. Трехмерная модель подлежит цифровой обработке для виртуального разделения на тонкие слои с толщиной, соответствующей толщине слоев, наносимых печатным устройством. Готовый «построечный» файл используется как набор чертежей во время печати. В качестве нагревательного элемента для спекания металлического порошка используются оптоволоконные лазеры относительно высокой мощности – порядка 200 Вт. Некоторые устройства используют более мощные лазеры с повышенной скоростью сканирования (т.е. передвижения лазерного луча) для более высокой производительности. Как вариант возможно повышение производительности за счет использования нескольких лазеров.
Порошковый материал подается в рабочую камеру в количествах, необходимых для нанесения одного слоя. Специальный валик выравнивает поданный материал в ровный слой и удаляет излишний материал из камеры, после чего лазерная головка спекает частицы свежего порошка между собой и с предыдущим слоем согласно контурам, определенным цифровой моделью. После завершения вычерчивания слоя процесс повторяется: валик подает свежий материал и лазер начинает спекать следующий слой. [1]
Рис. 3.5 Схема процесса прямого лазерного спекания
|
Используемые материалы: практически любые металлические сплавы.
6. Электронно-лучевая плавка металлов
Этот метод производства деталей произвольных форм позволяет
создавать металлические модели высокой плотности из металлического порошка. Готовые изделия практически не отличаются от литых деталей по механическим свойствам. Устройство считывает данные с
файла, содержащего трехмерную цифровую модель, и наносит после-довательные слои порошкового материала. Контуры слоев модели вычерчиваются электронным пучком, плавящим порошок в местах соприкосновения. Плавка проводится в вакуумных рабочих камерах,
что позволяет работать с материалами, чувствительными к оксидации,
например с чистым титаном. [1]
Рис. 3.6 Схема процесса электронно-лучевой плавки
Используемые материалы: титановые сплавы.
7. Селективное лазерное плавление
Селективное (выборочное) лазерное плавление (SLM) – метод аддитивного производства, использующий лазеры высокой мощности для создания трехмерных физических объектов за счет плавки металлических порошков.
Процесс печати начинается с разделения цифровой трехмерной модели на слои толщиной от 20 до 100 микрон. Готовый файл в стандартном формате STL используется в качестве чертежей для построения физической модели.
Производственный цикл состоит из нанесения тонкого слоя порошка на рабочую поверхность, как правило металлический стол, способный передвигаться в вертикальном направлении. Процесс печати протекает в рабочей камере, заполняемой инертными газами (например, аргоном). Отсутствие кислорода позволяет избегать оксидации расходного материала, что делает возможной печать такими материалами, как титан. Каждый слой модели сплавляется, повторяя контуры слоев цифровой модели. Плавка проводится с помощью лазерного луча, направляемого по осям X и Y двумя зеркалами с высокой скоростью отклонения. Мощность лазерного излучателя достаточно высока для плавки частиц порошка в гомогенный материал. [1]
Рис. 3.7 Схема процесса селективного лазерного плавления
Используемые материалы: титановые сплавы, кобальтхромовые сплавы, нержавеющая сталь, алюминий.
8. Селективное тепловое спекание
Селективное (выборочное) тепловое спекание (SHS) – метод ад-дитивного производства. Технология основана на плавке слоев тер-мопластического или металлического порошка с помощью тепловогоизлучателя.
По окончании формирования слоя рабочая платформа передвигается вниз на дистанцию, соответствующую толщине одного слоя, после чего новый слой порошка наносится с помощью автоматизированного ролика, а затем проводится спекание нового слоя по контурам, заданным цифровой трехмерной моделью. [1]
|
Рис. 3.8 Схема процесса селективного теплового спекания
Лучше всего технология SHS подходит для производства недорогих функциональных прототипов.
Используемые материалы: порошковые термопластичные полимеры.
9. Селективное лазерное спекание
Селективное (выборочное) лазерное спекание (SLS) – метод аддитивного производства, используемый для создания функциональных прототипов и мелких партий готовых изделий. Технология основана на последовательном спекании слоев порошкового материала с помощью лазеров высокой мощности. Метод SLS зачастую ошибочно принимают за схожий процесс, называемый выборочной лазерной плавкой (SLM). Разница заключается в том, что SLS обеспечивает лишь частичную плавку, необходимую для спекания материала, в то время как выборочная лазерная плавка подразумевает полную плавку, необходимую для построения монолитных моделей.
Технология SLS подразумевает использование одного или нескольких лазеров (как правило, углекислотных) для спекания частиц порошкообразного материала до образования трехмерного физического объекта. [1]
Рис. 3.9 Схема процесса селективного лазерного спекания
Используемые материалы: термопластичные полимеры, металлические порошки, керамические порошки.
Вывод: Рассмотрев несколько видов технологии 3D печати, был выбран метод прямого лазерного спекания. Этот метод можно считать фактически безотходным, что немаловажно при использовании дорогих материалов.
Неспеченный порошок не удаляется во время печати, а остается в рабочей камере. Кроме того, неизрасходованный материал может быть собран из рабочей камеры по завершении печати и использован заново. Высокая точность исполнения минимизирует необходимость механической обработки напечатанных изделий.
Этот метод подходит для материла Латунь ЛС 59-1 и для среднесерийного производства.
Проектное решение
Для получения заготовки был выбран метод прямого лазерного спекания.
Технология практически не имеет ограничений по геометрической сложности построения, а высокая точность исполнения минимизирует необходимость механической обработки напечатанных изделий.
Технология прямого лазерного спекания обладает несколькими достоинствами по сравнению с традиционными методами производства. Наиболее очевидным ее достоинством является возможность быстрого производства геометрически сложных деталей без необходимости механической обработки («субтрактивных» методов – фрезеровки, сверления и пр.). Производство практически безотходно, что выгодно отличает прямое лазерное спекание от субтрактивных технологий. Технология позволяет создавать несколько моделей одновременно с ограничением лишь по размеру рабочей камеры. Построение моделей занимает примерно несколько часов, что несоизмеримо выгоднее, чем литейный процесс, который может занимать до нескольких месяцев с учетом полного производственного цикла [1].
Выбор оборудования
Существует ряд установок систем лазерного сплавления металлических порошков для изготовления деталей.
Было выбрано оборудование EOS М 100, так как для изготовления малогабаритной детали не нужна большая установка.
Рис. 4.1 Установка EOS М100
Размеры и модульная концепция установки EOS M 100 делают ее идеальной для начала внедрения аддитивных технологии.
Установка комплектуется волоконным лазером мощностью 200Вт. Эти лазеры обладают стабильными характеристиками и излучением. Благодаря меньшему размеру пятна лазера можно получать детали со сложной геометрией с превосходной разрешающей способностью.
Модульная структура установки и лотки для материала позволяют запускать и завершать процесс построения за минуты. Также упрощается процедура замены материала и обслуживания установки.
Периферийное оборудование предназначено для промышленного применения и сокращает до минимума контакт с материалом. [6]
Технические данные:
Размеры (Д x Ш x В):
Подготовка данных:
Латунный порошок
Рис. 4.2 Латунный порошок
Порошок латунный изготавливается согласно ТУ 48-21-701-80 «Порошок латунный. Технические условия». Химический состав такого сплава, как латунь, регулируется ГОСТ 15527-2004 «Сплавы медно-цинковые (латуни), обрабатываемые давлением. Марки». Латунь является наиболее распространенным сплавом, в котором присутствует и является основой такой цветной металл, как медь. Благодаря своей отличной устойчивостью к коррозии, а также другим агрессивным воздействиям внешней среды она является одним из наиболее часто применяемых сплавов. Изготавливается такой порошок латунный, как правило, методом распыления. Размер порошковых частиц обычно составляет от 40 до 400 мкм, что также определяет универсальность использования данного вещества.
Химический состав
Согласно государственному стандарту изготовления латунных сплавов основой в данном порошковом веществе является медь. Кроме меди в нем присутствуют другие элементы, которые находятся в нем в меньшем количестве. Это свинец, железо, сурьма, висмут, фосфор и цинк, алюминий, мышьяк, марганец, никель, кремний, олово, бор, свинец. Сумма и наличие тех или иных прочих элементов может различаться в зависимости от марки порошка, как и расчетная насыпная плотность. [8]
Технологический расчет
Заготовка
Исходя из анализа ТП, составили план обработки. В качестве заготовки назначили прямое лазерное спекание.
Рис. 5.1 – Заготовка
План обработки
Таблица 3 – Технологический процесс
№ Операции, Наименование | Операционный эскиз | Оборудование |
00 Заготовительная | ![]() | EOS М100 |
05 Токарная | ![]() | TRENS SBL-300 |
06 Токарная | ![]() | TRENS SBL-300 |
Схема обработки
Алгоритм построения схемы формирования линейных размеров (рис.5.1):
1. Вычертили контур исходной заготовки
2. На эскизе заготовки отметили поверхность, являющейся технологической базой на первой операции механической обработки
3. От отмеченной базой поверхности проставили размеры заготовки
4. Отметили на схеме припуск (напуск) со стороны обработки согласно операционному эскизу.
Припуск – слой металла, при удалении которого конфигурация поверхности не изменяется. Припуски назначают для компенсации погрешностей точности и качества, возникающих при изготовлении заготовки.
Напуск – слой металла, при удалении которого конфигурация поверхности изменяется. Напуски назначают для упрощения выполнения операций заготовительного производства с целью получения качественной заготовки.
5. Перенесли размеры с операционного эскиза односторонней стрелкой (односторонняя стрелка указывает на обработанную поверхность, точка – измерительная база).
6. Повторили п.1,4,5 для всего технологического процесса.
7. Обозначили номера припусков zij, перенесли конструкторские размеры с чертежа детали, пронумеровали слева – направо полученные поверхности.
Рис. 5.2 – Схема обработки
Граф линейных размеров
Граф - совокупность множества точек (вершин) и соединяющих линий, которые называют ребрами, конец каждой предыдущей дуги совпадает с началом следующей.
Вершины (поверхности) обозначают кружечками, внутри которых указы-вают их номер. Ребра производного дерева изображают прямыми линиями со стрелками на конце, показывающие в какую вершину они входят. Ребра исходного дерева изображают в виде дуг, если они являются конструкторскими размерами в виде гладких дуг, если размеры припуска - в виде волнистых дуг.
На рис. 5.2 представлен граф линейных размеров.
Рис.5.2 – Граф линейных размеров
|
|
Архитектура электронного правительства: Единая архитектура – это методологический подход при создании системы управления государства, который строится...
Своеобразие русской архитектуры: Основной материал – дерево – быстрота постройки, но недолговечность и необходимость деления...
Состав сооружений: решетки и песколовки: Решетки – это первое устройство в схеме очистных сооружений. Они представляют...
История развития хранилищ для нефти: Первые склады нефти появились в XVII веке. Они представляли собой землянные ямы-амбара глубиной 4…5 м...
© cyberpedia.su 2017-2024 - Не является автором материалов. Исключительное право сохранено за автором текста.
Если вы не хотите, чтобы данный материал был у нас на сайте, перейдите по ссылке: Нарушение авторских прав. Мы поможем в написании вашей работы!