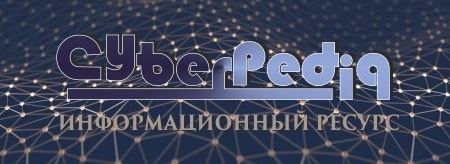
Общие условия выбора системы дренажа: Система дренажа выбирается в зависимости от характера защищаемого...
Организация стока поверхностных вод: Наибольшее количество влаги на земном шаре испаряется с поверхности морей и океанов (88‰)...
Топ:
Устройство и оснащение процедурного кабинета: Решающая роль в обеспечении правильного лечения пациентов отводится процедурной медсестре...
Техника безопасности при работе на пароконвектомате: К обслуживанию пароконвектомата допускаются лица, прошедшие технический минимум по эксплуатации оборудования...
Интересное:
Распространение рака на другие отдаленные от желудка органы: Характерных симптомов рака желудка не существует. Выраженные симптомы появляются, когда опухоль...
Национальное богатство страны и его составляющие: для оценки элементов национального богатства используются...
Средства для ингаляционного наркоза: Наркоз наступает в результате вдыхания (ингаляции) средств, которое осуществляют или с помощью маски...
Дисциплины:
![]() |
![]() |
5.00
из
|
Заказать работу |
|
|
ЛЕКЦИЯ №2
Тема: «Технология ремонта двигателей внутреннего сгорания»
Вопросы:
Причины изнашивания деталей двигателя.
Восстановление блока цилиндров двигателя.
Износ деталей цилиндро-поршневой группы.
Восстановление цилиндров и гильз.
Причины изнашивания деталей двигателя.
Среди агрегатов тракторов и автомобилей наиболее быстро изнашиваемый и наименее надежный и долговечный агрегат — двигатель.
В процессе эксплуатации тракторов и автомобилей за двигателями ведется постоянный контроль, тщательное обслуживание, словом, уделяется им максимум внимания, и все же первыми из всех агрегатов они выходят из строя. Это объясняется тем, что детали двигателя подвержены активному химическому и механическому воздействию и нагружены значительными усилиями.
В большинстве случаев сроком службы двигателей определяется межремонтный срок работы тракторов и автомобилей. В свою очередь, срок службы двигателей обусловливается долговечностью его ответственных В большинстве случаев сроком службы двигателей определяется межремонтный срок работы тракторов и автомобилей. В свою очередь, срок службы двигателей обусловливается долговечностью его ответственных деталей.
В двигателях наиболее быстро изнашиваются поршневые кольца, поршни, цилиндры, клапаны, коленчатый вал, шатунные и коренные подшипники коленчатого вала.
Обычно срок службы автотракторных двигателей определяется износом поршневых колец, канавок поршней, цилиндров, подшипников и шеек коленчатого вала, а также неплотностью прилегания клапанов к гнездам. Появление этих неисправностей приводит к необходимости разборки двигателя с последующим сложным ремонтом.
|
Неисправности и дефекты остальных узлов и деталей, несомненно, влияют также на техническое состояние двигателя в целом, но их ремонт не вызывает необходимости полной разборки двигателя, и эти дефекты могут быть устранены путем замены неисправных узлов и деталей новыми или отремонтированными.
На износ поршневых колец, канавок поршня, цилиндров, шеек коленчатого вала, клапанов и других деталей оказывают влияние многие факторы. Некоторые из них, например температура, при благоприятных обстоятельствах оказывают умеренное влияние и, наоборот, при неблагоприятных обстоятельствах ускоряют изнашивание деталей в несколько раз.
Срок службы детали в первую очередь зависит от качества материала, из которого она изготовлена, ее термической и механической обработки точности сборки машины и от других конструктивных и производственных факторов.
Практика показывает, что при одних и тех же конструктивных данных и одинаковых производственных условиях изготовления решающее влияние на срок службы деталей оказывают условия эксплуатации, в частности режимы работы машин. Так, при работе двигателей важнейшие факторы, влияющие на изнашивание деталей, — это абразивная среда, число пусков и остановок, температурный и нагрузочный режимы, вибрация и деформация деталей.
Дорожные и климатические условия и резкое различие режимов полевых и транспортных работ обусловливают частое изменение скоростей и длительное применение пониженных передач с высокой степенью использования большого крутящего момента, что приводит к резкому изменению температурного и нагрузочного режимов работы двигателя.
В результате проведенных испытаний тракторов установлено, что темп изнашивания многих деталей не находится в прямей зависимости от наработки машин, а обусловливается в большей степени конкретными условиями работы. В частности, разброс интенсивности изнашивания одноименных деталей в масштабе страны характеризуется коэффициентом вариации 0,625.
|
Скорость изнашивания деталей непрерывно меняется в зависимости от того, с какой активностью действуют в данный отрезок времени на изнашивание такие факторы, как пылезасоренность воздуха, число запусков и их длительность, температура окружающего воздуха, неравномерность нагрузочного и температурного режимов и т. п.
ЛЕКЦИЯ №3
ТЕМА: «РЕМОНТ УЗЛОВ СИСТЕМЫ СМАЗКИ И ОХЛАЖДЕНИЯ»
Вопросы:
1. Ремонт масляного насоса.
2. Ремонт масляных фильтров.
3. Ремонт узлов системы охлаждения.
4. Ремонт основных узлов, агрегатов и приборов электрооборудования.
1. Ремонт масляного насоса.
Надежность двигателя во многом зависит от исправности узлов системы смазки и качества применяемых масел.
Характерные неисправности системы смазки:
- износ деталей масляного насоса и фильтров,
- нарушение регулировок клапанов,
- потеря герметичности узлов,
- загрязнение системы.
Ремонт масляного насо са. Техническое состояние масляного насоса характеризуется его производительностью при номинальной частоте вращений ведущего валика и рабочем давлении, а также давлением открытия предохранительного клапана.
Определение износов. Перед проверкой и ремонтом масляного насоса его промывают и осматривают снаружи. При осмотре определяют износ валиков, втулок и обнаруживают другие повреждения. Затем насос испытывают на стенде на производительность и давление открытия предохранительного клапана.
Вязкость масла при этом должна быть такой же, как и при испытании насоса после ремонта, и соответствовать вязкости картерного масла у прогретого двигателя.
По результатам испытаний судят о необходимости ремонта насоса.
В случае необходимости разбирают насос, моют его детали и выявляют дефекты и износ.
У корпуса масляного насоса изнашиваются поверхности в местах сопряжения с торцами шестерен и стенки гнезд в местах сопряжения с вершинами зубьев шестерен, места посадки втулки ведущего валика и пальца ведомой шестерни. Кроме того, изнашивается гнездо предохранительного клапана, повреждается резьба, образуются трещины.
При износе корпуса резко снижается производительность насоса.
Износ деталей предохранительного клапана приводит к нарушению его герметичности и снижению давления открытия.
|
У ведущей и ведомой шестерен насоса изнашиваются торцы и зубья по высоте и толщине. При износе шестерен по торцам и зубьев по высоте уменьшается производительность масляного насоса. На производительность масляного насоса износ зубьев толщине не оказывает существенного влияния. Износ наружной поверхности втулок насоса приводит ослаблению их посадки в корпусе, крышке и ведомой шестерне, а износ внутренней поверхности — к увеличению зазора между втулками, ведущим валиком и пальцем ведомой стерни.
Несвоевременное устранение этой неисправности может быть причиной аварийного износа гнезд корпуса и выхода насоса из строя. Палец ведомой шестерни изнашивается в местах сопряжения корпусом и втулкой ведомой шестерни.
Ведущий валик масляного насоса изнашивается в местах сопряжения со втулками. При несвоевременном устранении этого износа резко увеличивается зазор и быстро изнашиваются корпус и шестерни. У валика изнашиваются также шлицы или шпоночные канавки.
На поверхностях предохранительных клапанов во время эксплуатации появляются риски, задиры, местные износы, вследствие чего нарушается герметичность клапана. Отложение на клапане смолистых веществ приводит к его залеганию.
На клапанах шарикового типа появляются кольцевые выбоины риски. Витки пружины клапанов при длительной работе стираются, что приводит к потере ими упругости, а иногда и к поломке.
Устранение износов. Износ поверхности корпуса, сопрягаемой с крышкой, устраняют шлифовкой или припиливанием с последующим шабрением.
Неплоскостность торцовой поверхности измеряют при помощи иглы и щупа.
Утопание нагнетательных шестерен относительно торцовой верхности корпуса измеряют при помощи линейки и щупа.
Наибольшую трудность представляет восстановление изношенных колодцев корпуса насоса. Колодцы восстанавливают меднением, мелированием, наплавкой меди или латуни, эпоксидными смолами, также расточкой гнезд с последующей запрессовкой вкладышей. Расточка гнезд с последующей постановкой вкладышей наиболее простой способ восстановления корпуса.
.Изношенные отверстия под втулку валика и палец шестерни развертывают и в них запрессовывают втулку увеличенного размера.
|
Посадочное место шариковых клапанов восстанавливают зенкованием до выведения следов износа с последующей осадкой шарика по гнезду.
Изношенные клапаны плунжерного типа восстанавливают притиркой.
Трещины, обнаруженные в корпусе, заваривают сваркой или запаивают твердыми припоями.
Крышку масляного насоса с изношенной торцовой поверхностью шлифуют или припиливают и затем шабрят. Отверстие под втулку развертывают и в него запрессовывают втулку увеличенного размера.
Втулки с изношенной наружной поверхностью восстанавливают осадкой в корпусе или крышке. При износе внутренней поверхности втулки обычно выбраковывают.
Изношенные пальцы и валики восстанавливают наплавкой с последующими проточкой и шлифованием шеек, а также фрезерованием шлицев.
У маслоприемника насоса может быть оборвана и повреждена сетка, а также нарушена плотность соединения его с корпусом масляного насоса.
Порванные места сетки запаивают. При этом общая площадь запайки не должна превышать 10%.
У привода масляного насоса изнашиваются втулки кронштейнов, валики и соединительные муфты. Изношенные детали восстанавливают обычными способами.
Обкатка и испытание. Отремонтированный масляный насос обкатывают, испытывают и регулируют на специальных стендах.
В процессе обкатки насоса не должно быть постороннего шума, перегрева деталей, просачивания масла в местах соединений и через предохранительный клапан. После обкатки регулируют предохранительный клапан.
По окончании ремонта масляного, насоса проверяют его на производительность при нормальной частоте вращения и определенном противодавлении в соответствии с техническими условиями.
Масляные насосы большинства автомобильных двигателей испытывают только на развиваемое давление.
Ремонт масляных фильтров.
Качество очистки масла от продуктов износа и других примесей зависит от состояния масляных фильтров.
Основные неисправности. Масляные фильтры после разборки промывают и дефектуют.
У фильтров двигателей с центробежной очисткой масла могут быть следующие неисправности: износы шеек ротора и втулок, а также износ и забивание отверстий форсунок (сопл) и защитных сеток на заборных трубках ротора центрифуги (в этом случае ухудшается герметичность ротора и снижается частота вращения его, вплоть до остановки); износ клапанов, резьб, появление трещин па корпусе фильтра, деформация колпаков, повреждение прокладок, что приводит к нарушению регулировок клапанов фильтра и подтеканию масла.
Восстановление деталей. При износе оси ротора центрифуги и втулок ось шлифуют до выведения следов износа. В в корпус ротора запрессовывают втулки ремонтных размеров.
|
При тугом вращении или заедании корпуса ротора допускается пришабривание втулок.
После запрессовки втулок их обрабатывают одновременно специальной комбинированной разверткой. В случае образования трещин и при обломах корпус и крышку ротора центрифуги выбраковывают.
Сопловые отверстия прочищают медной проволокой и проверяют на пропускную способность при помощи прибора для тарировки жиклеров карбюратора.
Трещины в корпусе фильтра заваривают биметаллическим электродом. Повреждения гнезд клапанов и пружин устраняют так же, как и повреждения предохранительного клапана масляного насоса.
Погнутые стальные колпаки фильтров выправляют, а трещины на горловине запаивают твердыми припоями.
Контроль. После сборки центрифуги на стенде регулируют перепускной клапан, определяют герметичность ротора и частоту его вращения.
После окончательной сборки центрифуги проверяют ее на стенде на герметичность и пропускную способность совместно с масляным насосом нормальной производительности при номинальной частоте вращения и противодавлении.
Ремонт масляных радиаторов. В масляном радиаторе чаще всего забиваются внутренние полости трубок и засоряются маслосборники отложениями, в связи с чем уменьшается пропускная способность радиатора, повышается температура масла. При высокой температуре масла уменьшаются его вязкость и маслянистость, что приводит к повышенному износу деталей, а также старению масла.
Перед ремонтом масляный радиатор вываривают в 5—10-процентном растворе каустической соды в течение 2—3 ч, а затем промывают горячей водой. Отложения в трубках масляного радиатора можно также удалить четыреххлористым углеродом или другим раствором моющего средства. Течь трубок или маслосборников радиатора устраняют пайкой поврежденных мест латунным припоем. Смятую и оборванную ленту трубки выпрямляют и припаивают по всей длине латунным припоем. После ремонта радиатор проверяют на герметичность.
ЛЕКЦИЯ №4
Тема: «Ремонт силовой передачи, механизмов управления и ходовой части тракторов»
Вопросы:
1. Ремонт осей и валов.
2. Ремонт шестерен и звездочек.
3. Ремонт подшипников качени я.
Ремонт осей и валов
Значительное количество тракторов, автомобилей, комбайнов сельскохозяйственных машин различных типов и марок приводит необходимости унификации технологии ремонта отдельных деталей и сопряжений.
Технология восстановления некоторых талей силовой передачи, ходовой части и механизмов управления тракторов и автомобилей.
Ремонт валов и осей. В тракторах и автомобилях применяют различные по конструкции, материалу и термической обработке валы и оси.
Для получения большей износостойкости валы, оси, полуоси другие детали подвергаются термической или термохимической работке.
Некоторые детали цементуют на глубину 1,0—1,5 мм, закаливают в еле и отпускают до получения твердости поверхностей НRС 40—62.
Детали, изготовленные из углеродистой стали с содержанием лерода 0,4% и более, закаливают с нагревом ТВЧ и отпускают.
Валы автомобилей, изготовленные из стали 40Х, цианируют глубину 0,2—0,3 мм до получения твердости НRС 48—53.
Основные дефекты валов: износ шпоночных (деформация и износ шпонок, канавок) и шлицевых соединений (износ боковой поверхности шлицев), посадочных мест, повреждение центровых отверстий и резьбы, а также изгиб.
Устранение дефектов. Изношенные валы восставливают разнообразными способами. Применение того или другого способа обусловливается наличием оборудования, технико-экономискими соображениями и ожидаемыми результатами при восстановлении деталей.
Небольшой износ шпоночных канавок устраняют вручную или станках (фрезерных, строгальных, долбежных или токарных), используя различные приспособления. После этого при сборке применяют шпонки увеличенных размеров. При значительном износе канавок их заваривают электродуговой сваркой, а в другом месте делают новые.
Если шпонка служит одновременно и для фиксации сопрягаемой детали в определенном положении, менять положение паза на валу нельзя.
Изношенные по ширине шлицы наплавляют электродуговой плавкой, вибродуговой наплавкой, наплавкой под слоем флюса; в среде защитных газов. При электродуговой наплавке шлицы плавляют электродами ЦН-250, ОЗН-300, ОЗН-350 и др.
При восстановлении валов диаметром 45—50 мм со шлицами шириной до 5—6 мм часто заваривают канавку шлица. У валов больших размеров наплавляют неизношенную сторону шлица. После наплавки деталь медленно охлаждают в песке или термостате, чтобы не допустить коробления. Валики накладывают поочередно с диаметрально противоположных сторон. Валик начинают наплавлять, в точке а (рис. 1), отступив от конца на 10—15 мм, и заканчивают в точке б. Наложение валиков в 3—4 слоя предупреждает образование закалочной зоны на границе с расплавленным металлом.
После наплавки шлицы обрабатывают на станках. Деталь на станке закрепляют по меткам, нанесенным на ее торцовой поверхности перед наплавкой. Это необходимо для того, чтобы снимать только наплавленный металл.
Шлицевые соединения восстанавливают постановкой дополнительной втулки. Для этого стачивают внутренние шлицы детали и растачивают на токарном станке так, чтобы диаметр отверстий был больше на 0,5—1,5 мм высоты шлицев вала. Затем вытачивают втулку по размерам сопрягаемой детали, нагревают и осаживают ее по валу.
Протачивают втулку на токарном станке до получения наружного диаметра, равного диаметру расточки в отверстии восстанавливаемой детали с учетом натяга; снимают фаски и приваривают в нескольких местах электросваркой (рис. 2). При обработке на станке в качестве оправки используют шлицевой вал.
Изношенные посадочные места под подшипники качения, шестерни, сальники и другие детали восстанавливают наплавкой, осталиванием, электронатиранием, хромированием, никелированием, металлизацией, с применением полимеров и электромеханической обработки и в редких случаях кузнечной осадкой или раздачей.
Иногда целесообразно восстанавливать валы напрессовкой втулок, колец, бандажей, т. е. способом использования дополнительных деталей. Предварительно валы протачивают и затем напрессовывают втулку, кольцо и т. п.
Размер проточки под дополнительную деталь должен обеспечить толщину ее стенки после обработки в пределах не менее 3—6 мм. Если эти детали воспринимают осевые нагрузки, то, кроме напрессовки с натягом, необходимо их закреплять штифтами толщиной 6—8 мм или приваривать электросваркой.
Высокую чистоту обработки и прочный поверхностный слой можно получить после накатки детали шариковыми или роликовыми накатками.
Изогнутые или скрученные валы правят в холодном или горячем состоянии.
При ремонте коробок передач обязательно надо проверять параллельность и перекосы осей валов, иначе эти дефекты вызывают износы шестерен.
Ремонт шестерен и звездочек
Ремонт шестерен и звездочек. Шестерни машин работают в условиях значительных нагрузок, перекосов в зацеплении, при большом количестве абразивных частиц и т. п. Абразивные частицы попадают в зазоры между зубьями из-за недостаточно надежного уплотнения выступающих концов валов и рычагов. В сопряжения также непрерывно попадают частицы продуктов износа трущихся деталей.
При перекосах зубчатые передачи работают в еще более тяжелых условиях. Перекосы в зацеплений возникают из-за многих причин. Одной из них служит несимметричное расположение венца шестерни по длине ступицы. Шестерни работают в весьма неблагоприятных условиях при одновременных перекосе и непараллельности валов. В этом случае напряжения увеличиваются значительно больше, чем только при перекосах или только при непараллельности.
Основные неисправности шестерен: износ зубьев по толщине, выкрашивание, скалывание и поломка зубьев, износ торцовой поверхности обода, ступицы и зубьев, износ кольцевой канавки под вилку переключения, шлицев и посадочных отверстий, трещины в ступице. Интенсивность шума повышается после 950—1000 ч работы зубчатой передачи вследствие выкрашивания зубьев.
Устранение неисправностей. При износе зубьев шестерни восстанавливают заменой венцов, давления и др.
Кроме того, у шестерен восстанавливают сопрягаемые поверхности. Венцы у шестерен заменяют в том случае, если имеется сменный венец, фиксируемый заклепками, или у блоков шестерен (например, блок шестерен коробки передач автомобиля ГАЗ-53), когда из-за поломки зубьев одного венца нецелесообразно выбраковывать дорогостоящие детали.
При замене венца срубают заклепки, спрессовывают изношенный и напрессовывают новый венец, обеспечивая совпадение канавок ступицы и венца, а также торцовых поверхностей.
Головки заклепок должны быть плотно прижаты к торцовым поверхностям венца и ступицы. Торцовое биение венцов со ступицами в сборе допускается не более 0,25 мм.
В отдельных случаях наплавляют изношенные зубья газовой или электродуговой сваркой. При наплавке цементованных шестерен пользуются присадочным металлом с более высоким содержанием углерода.
Хорошие результаты для повышения износостойкости и прочности наплавляемых зубьев шестерен получают в случае применения сормайта в качестве присадочного материала. Сормайт рекомендуется использовать для наплавки зубьев при торцовых износах, выкрашивании цементованного слоя или сколов. Справка сормайт 1 (сплав 3,1% углерода, 28% хрома, 3% никеля, 1,5% марганца, 3,5% кремния)
Наплавленные зубья фрезеруют, шлифуют или обрабатывают (электроэрозионным способом. Перед наплавкой шестерню отжигают, нагревая до температуры 850—900° С.
Разработана и успешно применяется специальная установка для механизированной наплавки зубьев под слоем флюса.
Шестерни, изношенные по толщине и имеющие на венце достаточный запас металла, можно восстанавливать методом горячей осадки. В этом случае изготовляют штампы для шестерен каждого вида.
Способом осадки могут быть восстановлены как блочные, так и одинарные цилиндрические шестерни без поломанных зубьев, сколов, трешин на ободе и ступице.
Сущность осадки сводится к следующему. Восстанавливаемую деталь нагревают и помещают в штамп (рис. 3). Кроме штампов, необходимо иметь гидравлические прессы (40—50-тонные) или горяче-штамповочные кривошипные прессы и термические печи.
Для того чтобы диаметр посадочного отверстия не менялся, используют оправку, имеющую форму и размеры такие же, как и у сопрягаемого вала. Шестерни, изготовленные из стали 18ХГТ, рекомендуется восстанавливать осадкой при нагреве до температуры 900—1160° С, а шестерни из стали 40Х — при нагреве до температуры 900—1000° С.
Шестерни из цементованных сталей нагревают в карбюризаторе, а шестерни из среднеуглеродистой стали — в соляных ваннах. При осадке перемещают металл с торцовых поверхностей обода к изношенным зубьям и посадочному отверстию.
Размеры штампа должны обеспечить получение припусков по толщине зуба 1,4—1,5 мм, по наружному диаметру 0,5—0,8 мм и по диаметру внутреннего отверстия 1,2—1,4 мм для последующей обработки.
Перед механической обработкой на токарных и зуборезных станках шестерню подвергают нормализации нагревая до температуры 830—850° С и охлаждая на воздухе.
После механической обработки проводят термообработку шестерни. Восстановленные этим способом шестерни должны отвечать тем же требованиям, что и новые детали.
Односторонне изношенные шестерни можно использовать для дальнейшей работы, если их перевернуть неработавшей стороной. Отдельные шестерни при этом требуют незначительной переделки. Например, шестерню с несимметричной ступицей подрезают с одной стороны (рис. 4 а), делая ступицу симметричной. Для правильного положения шестерни на вал при сборке надевают кольца с шириной, равной ширине отрезанной части, т. е. х. Остальные размеры соответствуют размерам сопрягаемого вала и других деталей.
Односторонне изношенные подвижные шестерни с кольцевыми проточками для вилок переключения передач не только переворачивают на 180° для работы иеизношенной стороной, но и резцом с пластиной из твердого сплава типа Т5К10 отрезают часть ступицы (рис. 4, б) и к противоположной стороне приваривают новую кольцевую муфту.
Конструкция отдельных шестерен позволяет использовать их для работы в качестве других деталей.
Например, при поломке зубьев венца третьей передачи шестерню трактора класса 60 кН с венцом четвертой передачи используют для шестерни реверса. Для этого резцом с пластиной из твердого сплава отрезают венец третьей передачи. Венец четвертой передачи соответствует по количеству зубьеа шестерне реверса (рис. 4, в).
Симметричное расположение шестерен дает возможность переворачивать их при одностороннем износе для работы неизношенной стороной зуба и позволяет значительно продлить технический ресурс деталей при нормальном зацеплении. После переворачивания венца торцы зубьев закругляют.
Изношенные пазы подвижных шестерен под вилку включения восстанавливают проточкой до выведения следов износа. Вилку переключения передач в этом случае наплавляют, а затем обрабатывают до размера проточенного паза. При износе шлицев шестерен рекомендуется запрессовывать в них шлицевые втулки (см. рис.2).
Ремонт подшипников качения
Ремонт подшипников качения. При работе подшипников качения из-за износа увеличиваются их осевые и радиальные зазоры, вследствие чего возникает шум, недопустимо нагреваются узлы и повышается износ других деталей.
На технический ресурс подшипников большое влияние оказывают непараллельность и перекос осей валов.
Основные неисправности подшипников качения: ослабление посадки в корпусах и на шейках валов, износ поверхностей качения (беговых дорожек), поломки, выкрашивание и трещины в кольцах, телах качения и сепараторах, их износ и поломки, а также перегрев, приводящий к появлению цветов побежалости.
Подшипники качения выбраковывают при появлении цветов побежалости, сколах металла или трещинах, выкрашивании или шелушении поверхностей качения, появлении раковин коррозийного характера.
Ремонтируют подшипники специализированные ремонтные предприятия. При ремонте выполняют следующие операции: разбирают подшипники, проверяют и сортируют детали, шлифуют поверхности колец, устраняют износ наружной и внутренней поверхностей хромированием или осталива-нием, шлифуют беговые дорожки, комплектуют подшипники шариками или роликами увеличенных размеров, подгоняют сепараторы и склепывают их.
Ремонт резьбовых соединений зависит от характера дефекта.
Основные дефекты резьбовых соединений: износ и срыв резьбы, ее выкрашивание, появление забоин и заусенцев.
Под резьбовые пробки резьбу нарезают только при помощи двух метчиков. Резьбовые пробки изготавливают из мягкой стали. Перед ввертыванием пробок их обмазывают масляной краской или клеем БФ-2. Ввертывают пробки в новые отверстия до отказа. В месте соприкосновения пробки с телом детали просверливают отверстия, в которые запрессовывают стальные стопорные штифты, обеспечивающие неподвижность этого соединения.
При восстановлении резьбы в нескольких отверстиях их рассверливают по кондуктору, чтобы обеспечить правильное взаимное расположение соединяемых деталей.
ВОССТАНОВЛЕНИЕ ДЕТАЛЕЙ ХОДОВОЙ ЧАСТИ ГУСЕНИЧНЫХ ТРАКТОРОВ
Ремонт муфт поворота, фрикционных муфт, тормозных колодок и лент.
Ремонт дисков сводится к замене накладок.
Основные дефекты дисков: износ рабочих поверхностей и фрикционных накладок, коробление, задиры и трещины на дисках, ослабление заклепочных соединений.
Устранение дефектов. Износ и задиры рабочих поверхностей нажимных и ведущих дисков устраняют шлифованием на плоскошлифовальных станках или протачиванием на токарных станках с последующей зачисткой наждачным полотном. Трещины на ведущих дисках устраняют газовой сваркой с последующей проточкой на токарных станках или шлифованием.
Изношенные фрикционные накладки ведомых дисков, тормозных колодок и лент заменяют новыми. Их приклепывают или приклеивают. Изношенные приклепанные накладки удаляют, срубая заклепки зубилом и выбивая их специальным бородком. Приклеенные накладки удаляют протачиванием на токарных станках, нагревом в печах до температуры 300—350° С или кипячением в специальных растворах.
Накладки переклепывают на специальных станках или при помощи простейших приспособлений полыми (допускается использование медных и латунных трубок) заклепками.
Крепление накладок заклепками имеет существенные недостатки.
Во-первых, используется только 30—50% материала накладки и ее рабочая поверхность уменьшается на 7—15%.
Во-вторых, появляются задиры и интенсивно изнашиваются сопрягаемые поверхности от трения выступающих заклепок.
В-третьих, расходуется большое количество цветного металла на заклепки и процесс крепления малопроизводителен. Поэтому широко применяют приклеивание фрикционных накладок клеем БФ, ВС-10Т и др.
Фрикционные накладки к дискам муфт сцепления, тормозным колодкам автомобилей рекомендуется приклеивать клеем ВС-10Т, который выдерживает нагрев до температуры 300° С.
Наименьшая допустимая толщина дисков в сборе с накладками муфт сцепления тракторов составляет 6 мм, нормальная—9,5—10 мм. Накладки должны плотно прилегать к дискам. При использовании накладок в виде секторов, т. е. таких, как у муфт сцепления тракторов класса 60 кН, разница по толщине для одного комплекта секторов не должна превышать 0,1 мм.'
После приклепывания или приклеивания поверхности накладок должны быть перпендикулярны оси ступицы. Непараллельность поверхностей дисков с накладками в сборе допускается не более 0,3 мм, а биение диска при проверке в центрах — не более 0,8 мм на крайних точках. Головки заклепок должны утопать от плоскости на глубину 1—1,5 мм. Допускаемое без ремонта утопание головок заклепок составляет 0,25 мм.
Если тормозные барабаны проточены, то под фрикционную накладку помещают подкладку (или применяют утолщенную фрикционную накладку).
Изношенные фрикционные накладки тормозных лент заменяют новыми.
Восстановление ведущих и ведомых барабанов муфт управления.
В зависимости от характера дефекта барабаны восстанавливают одним из рассмотренных ниже способов.
Основные возможные дефекты: износ зубьев и шлицев, поверхностей, соприкасающихся с тормозной лентой, износ и срыв резьбы в отверстиях под болты крепления.
Зубья барабанов по высоте изнашиваются из-за нарушения соосности, неправильной регулировки подшипников вала заднего моста и др.
Способы восстановления. При износе зубьев по высоте их протачивают не более чем на 0,5 мм. При боковых износах зубья прострагивают.
У внутренних (ведущих) барабанов тракторов класса 60 кН замеряют шаговый размер 11 зубьев. Если он меньше 103,5 мм, переставляют ведущие диски с полуосью в сборе на другую сторону трактора. При этом зачищают неровные поверхности зубьев. При шаговом размере меньше 102,3 мм и износе обеих поверхностей зубьев, а также при появлении трещин барабаны выбраковывают.
Отверстия под болты крепления наружных барабанов к фланцам рассверливают при износе или срыве резьбы и нарезают в них резьбу ремонтного размера. Чтобы предотвратить смещение отверстий, их рассверливают одновременно во фланце и в барабане. При повторных ремонтах отверстия сверлят на новом месте, сместив на половину дуги между прежними, и нарезают резьбу нормального размера.
У наружных (ведомых) барабанов замеряют шаговый размер зубьев с охватом 13 впадин. Если он более 126,5 мм, барабан с ведомыми дисками в сборе переставляют на другую сторону трактора для работы малоизношенной стороной. При шаговом размере более 127,8 мм или появлении трещин барабан выбраковывают.
В случае износа поверхностей под тормозную ленту наружные барабаны протачивают до выведения следов износа. При большем износе этой поверхности барабан протачивают и напрессовывают кольца или наплавляют на установках под слоем флюса, затем подвергают механической обработке.
Кольца изготовляют из полосовой или листовой стали марок 40 или 45.
Кольца напрессовывают, предварительно нагрев их до температуры 300—400° С, а затем протачивают до номинального размера. Радиальное биение наружной поверхности ведомого барабана допускается не более 0,1 мм, а торцовое биение ведущих барабанов — 0,2 мм на крайних точках.
На поверхности ведомого барабана тормозной ленты допускаются неровности высотой до 0,3—0,5 мм. Допустимый без ремонта зазор в шлицевом соединении ведущих барабанов составляет 1,5 мм.
ЛЕКЦИЯ №2
Тема: «Технология ремонта двигателей внутреннего сгорания»
Вопросы:
|
|
Типы сооружений для обработки осадков: Септиками называются сооружения, в которых одновременно происходят осветление сточной жидкости...
Общие условия выбора системы дренажа: Система дренажа выбирается в зависимости от характера защищаемого...
Автоматическое растормаживание колес: Тормозные устройства колес предназначены для уменьшения длины пробега и улучшения маневрирования ВС при...
Наброски и зарисовки растений, плодов, цветов: Освоить конструктивное построение структуры дерева через зарисовки отдельных деревьев, группы деревьев...
© cyberpedia.su 2017-2024 - Не является автором материалов. Исключительное право сохранено за автором текста.
Если вы не хотите, чтобы данный материал был у нас на сайте, перейдите по ссылке: Нарушение авторских прав. Мы поможем в написании вашей работы!