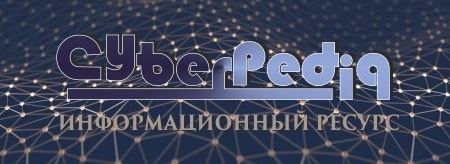
Своеобразие русской архитектуры: Основной материал – дерево – быстрота постройки, но недолговечность и необходимость деления...
Биохимия спиртового брожения: Основу технологии получения пива составляет спиртовое брожение, - при котором сахар превращается...
Топ:
Определение места расположения распределительного центра: Фирма реализует продукцию на рынках сбыта и имеет постоянных поставщиков в разных регионах. Увеличение объема продаж...
Проблема типологии научных революций: Глобальные научные революции и типы научной рациональности...
Выпускная квалификационная работа: Основная часть ВКР, как правило, состоит из двух-трех глав, каждая из которых, в свою очередь...
Интересное:
Финансовый рынок и его значение в управлении денежными потоками на современном этапе: любому предприятию для расширения производства и увеличения прибыли нужны...
Лечение прогрессирующих форм рака: Одним из наиболее важных достижений экспериментальной химиотерапии опухолей, начатой в 60-х и реализованной в 70-х годах, является...
Искусственное повышение поверхности территории: Варианты искусственного повышения поверхности территории необходимо выбирать на основе анализа следующих характеристик защищаемой территории...
Дисциплины:
![]() |
![]() |
5.00
из
|
Заказать работу |
|
|
Вопросы для проверки.
Что влияет на точность механической обработки?
Перечислите пути повышения точности при механической обработке заготовок.
Занятие № 7. Виды операций и этапы технологического процесса
Технологический процесс — это совокупность выстроенных в определенном порядке операций Он направлен на превращение сырья и заготовок в конечные изделия. Для этого с ними совершают определенные действия, обычно выполняемые механизмами. Технологический процесс не существует сам по себе, а является важнейшей частью более общего производственного процесса, включающего в себя в общем случае также процессы контрактации, закупки и логистики, продажи, управления финансами, административного управления и контроля качества
Технологи на предприятии занимают весьма важное положение. Они являются своего рода посредниками между конструкторами, создающими идею изделия и выпускающими его чертежи, и производством, которому предстоит воплощать эти идеи и чертежи в металл, дерево, пластмассу и другие материалы. При разработке техпроцесса технологи работают в тесном контакте не только с конструкторами и производством, но и с логистикой, закупками, финансами и службой контроля качества. Именно техпроцесс и является той точкой, в которой сходятся требования всех этих подразделений и находится баланс между ними.
Описание технологического процесса должно содержаться в таких документах, как:
Маршрутная карта — описание высокого уровня, в нем перечислены маршруты перемещения детали или заготовки от одного рабочего места к другому или между цехами.
Операционная карта – описание среднего уровня, более подробное, в нем перечислены все операционные переходы, операции установки-съемки, используемые инструменты.
|
Технологическая карта — документ самого низкого уровня, содержит самое подробное описание процессов обработки материалов, заготовок, узлов и сборок, параметры этих процессов, рабочие чертежи и используемая оснастка.
Технологическая карта даже для простого на первый взгляд изделия может представлять собой довольно толстый том.
По критерию степени детализации различают следующие виды технологических процессов:
Маршрутный техпроцесс исполняется в виде маршрутной карты, содержащей информацию верхнего уровня: перечень операций, их последовательность, класс или группа используемого оборудования, технологическая оснастка и общая норма времени.
Пооперационный техпроцесс содержит детализированную последовательность обработки вплоть до уровня переходов, режимов и их параметров. Исполняется в виде операционной карты.
Этапы ТП
В ходе конструкторско-технологической подготовки производства различают такие этапы написания технологического процесса, как:
Сбор, обработка и изучение исходных данных.
Определение основных технологических решений.
Подготовка технико-экономического обоснования (или обоснования целесообразности).
Документирование техпроцесса
Довольно широкое распространение получило понятие технологическая операция. Она определяет законченную часть технологического процесса, который выполняется на одном рабочем месте.
Виды операций
Выделяют довольно большое количество различных видов операций, которые могут проводится для получения той или иной заготовки, а также конечного изделия. Наименование операций может отличаться в зависимости от особенностей налаженного производства. Выделяют следующие виды технологических операций:
1. Маршрутные.
2. Операционные.
3. Маршрутно-операционные.
Встречается довольно большое количество технической документации, в которой указывается основная информация. При этом некоторым операциям присваиваются определенные номера.
|
Основные элементы
Выделяют самые различные элементы технологической операции. Основными можно назвать следующие:
1. Установка. Эта часть технологической операции, выполняемая при неизменном закреплении, проводится в самом начале. Ей уделяется также довольно много внимания, так как допущенные ошибки могут стать причиной смещения заготовки при ее обработке.
2. Позиция. Законченная часть технологической операции, характеризуемая постоянством, должна проводится при фиксировании положения заготовки. Стоит учитывать, что на данном этапе может проводиться и сборка технологической оснастки, которая отвечает за непосредственную фиксацию заготовки.
3. Технологический переход. Технологический процесс перехода могут осуществляться в рамках одной операции без изменения ранее установленных режимов работы. Он осуществляется в случае, когда обработка заготовки не может быть завершена по причине недостаточной функциональности оборудования. Количество переходов во многом зависит от того, насколько сложна заготовка. Нумерация переходов проводится с учетом последовательности механической обработки заготовки.
4. Рабочий ход. Именно этот элемент технологической операции считается наиболее важным, так как он обеспечивает механическое удаление материала с поверхности для придания требуемой формы и размеров. Как правило, совершается перемещение инструмента относительно поверхности заготовки с заданными параметрами при определенном углублении режущей кромки в обрабатываемый материал. Также при рабочем ходе обеспечивается обработка поверхности для получения определенной шероховатости. Рабочий ход может быть продольным или поперечным, при этом определяется глубина и скорость резания, а также многие другие параметры. Как правило, он более продолжительный и точный, рассчитан на оказание серьезного механического воздействия на рабочий орган.
5. Вспомогательный ход. Он также является неотъемлемой частью технологического процесса. Вспомогательный ход представлен однократным перемещением инструмента относительно заготовки, однако при этом не происходит изменение формы, размеров и других параметров заготовки. Применяется вспомогательный ход в большинстве случаев для смещения основных органов относительно заготовки. Примером можно назвать подвод инструмента в зону резания, а также фиксирующего элемента.
|
6. Наладка. Перед непосредственным производством проводится наладка оборудования, а также применяемой оснастки. Наладка предусматривает установку всех приспособлений, выверку размера инструмента и их положения. Наладочному процессу уделяется довольно много внимания, так как неправильная фиксация инструмента может привести к весьма серьезным последствиям. Сложнее всего провести наладку станков с ЧПУ, так как они должны обеспечивать высокую точность обработки. Кроме этого, часто финишным этапом проводимой наладки становится контрольная обработка заготовки, в ходе которой определяется точность и другие моменты.
7. Подналадка. Еще одним вспомогательным процессом можно назвать подналадку, которую выделяют крайне редко. Она предусматривает регулировку технологического оборудования или применяемой технологической оснастки. В некоторых случаях только после того, как было налажено производство можно определить неправильное позиционирование инструмента и технологической оснастки.
8. Технологическое оборудование. Также встречаются различные средства обеспечения проводимой процедуры. В эту категорию относят материалы и заготовки, а также требуемую оснастку. Встречается в продаже просто огромное количество различной оснастки, которая существенно упрощает поставленную задачу по обработке заготовки самой различной формы и размеров.
9. Технологическая оснастка. Это определение применяется для определения технологического оснащения, без которого провести обработку заготовки практически невозможно. Она может быть самой различной, подбирается в зависимости от того, какая процедура проводится.
В целом можно сказать, что технологическая операция является сложной процедурой, которая состоит из довольно большого количества различных частей
Классификаторы
Классификация технологических операций позволяет стандартизировать проводимые процедуры. При этом применяется различная система стандартизации, а также кодировки. Структура кода проводимой операции может существенно отличаться, все зависит от конкретного случая.
|
В последнее время применяется классификатор 1 85 151, который является общесоюзным. Он применяется для решения следующих наиболее распространенных задач:
1. Упорядочивания текстовой части создаваемой технологической документации, которая требуется при проводимой обработке.
2. Есть возможность перейти на технологическую документацию бестекстового типа. Применяемая информация может подвергаться машинной обработке, так как она представлена сочетанием кодов, которые стандартизированы.
3. Проводится объединение однородных операций для организации специализированных производственных операций.
4. Применяемый классификатор технологических операций машиностроения позволяет провести расчет трудовых и материальных расчетов. Они требуются для того, чтобы определить основные моменты, касающиеся производственной деятельности.
5. Анализ трудоемкости технологического процесса. За счет этого можно исключить вероятность ликвидации операций, которые могут стать причиной снижения стоимости детали.
6. Проводится оперативно-календарные и другие планировки производства.
7. Обеспечиваются условия для механизации учета основной информации.
8. Создание наиболее благоприятных условий для автоматизации системы обработки.
Встречаются также различные временные характеристики, для этого применяется справочник. Стоит учитывать тот момент, что классификация проводится по ступенчатой системе. При этом для каждой ступени применяется собственный номер, который позволяет быстро определить основные показатели.
Классификационная таблица выглядит следующим образом:
1. Операции общего назначения получили весьма широкое распространение. Без их применения практически не обходится ни одна из проводимых операций. Примером можно назвать перемещение заготовки или детали, их предварительное закрепление перед непосредственной обработкой. Существует много различных операций общего назначения, все они характеризуются своими определенными особенностями.
2. Технический контроль также является важной частью проводимой процедуры. Он позволяет контролировать основные показатели на различных этапах налаженного производства. Контроль качества и размеров должен проводится для того, чтобы исключить вероятность допущения дефектов при производстве. Для технического контроля могут применяться самые различные устройства и механизмы, а также инструменты. Довольно распространенным примером можно назвать штангенциркуль. Практически во всех случаях применяется технологическая операция, связанная с контролем основных параметров получаемого изделия. Линейные размеры, диаметр, шероховатость и другие параметры считаются наиболее важными, они указываются в технологической карте, по которой проводится выпуск изделия.
|
3. Перемещение является одной из наиболее распространенных операций. Оно предусматривает смещение рабочих и многих других органов относительно заготовки, а также базовой поверхности. Процедура перемещения весьма распространена.
4. Испытание. Также в отдельную группу отводится процедура, которая предусматривает испытание оборудования. Подобная процедура характеризуется достаточно большим количеством различных особенностей. Испытания несколько отличаются от процедуры, связанной с контролем размеров и других моментов. Испытания позволяют определить свойства, которые проявляются только при совершении определенного воздействия. Подобным образом проводится определение твердости и других параметров материалов. Провести испытание можно исключительно при применении специального оборудования и механизмов.
5. Обработка давлением и резанием. В последнее время чаще всего изменение формы и размеров проводится при применении оборудования, которое совершает механическое снятие с поверхности определенного количества материалов. Чаще всего устанавливается токарное и фрезеровальное, а также сверлильное оборудование. В этом случае обработка совершается за счет оказания воздействия режущей кромки на поверхность. Резание осуществляется за счет трения, поэтому велика вероятность нагрева поверхности. Довольно широкое распространение получила процедура, связанная с обработкой давлением. Подобная технологическая операция характеризуется своими особенностями, к примеру, используемые заготовки могут иметь только определенную толщину. Сегодня встречается просто огромное количество оборудования, которое может оказывать воздействие давлением на заготовку. Устанавливается оно в том случае, когда нужно обеспечить высокую производительность. Проведенные исследования указывают на то, что при обработке давлением затраты существенно снижаются.
6. Термическая обработка. Часто для изменения основных свойств металла он подвергается воздействию высокой температуры, которая становится причиной перестроения кристаллической решетки. Этой технологической операции уделяется довольно много внимания, так как закалка и отпуск существенно повышают основные характеристики изделия. Закалка позволяет повысить твердость поверхностного слоя. Слишком мягкий материал быстро изнашивается, на поверхности могут появляться различные дефекты. Отпуск позволяет исключить вероятность появления внутренних напряжений, которые становятся причиной появления различных дефектов при эксплуатации на момент оказания переменной нагрузки. Термическая обработка предусматривает применение специального оборудования, к примеру, печей. Они нагревают заготовку или изделие до высокой температуры, после чего происходит резкое охлаждение при применении воды или масла. При этом в последнее время используется масло, так как оно исключает вероятность появления серьезных дефектов на поверхности, к примеру, окалины.
7. Получение покрытий металлического и неметаллического типа. Выделяют технологические операции, которые связаны с изменением основных качеств поверхностного слоя. Особые технологии позволяют проводить нанесение специальных веществ в поверхностный слой. Примером можно назвать цементацию и некоторые другие процедуры. В последнее время часто встречается процедура, которая связана с покрытием металлических изделий полимерными порошками. Они существенно повышают степень защиты металла от воздействия повышенной влажности.
8. Получение органических поверхностей. Некоторые лакокрасочные материалы позволяют существенно продлить эксплуатационный срок и увеличить основные эксплуатационные характеристики изделия. Именно поэтому довольно много внимания уделяется технологической операции, связанной с их непосредственным нанесением.
9. Пайка. Для соединение отдельных элементов и восстановления поврежденной поверхности металлических и других изделий часто проводится пайка. Эта операция, которую не следует путать со сваркой, также предусматривает воздействие высокой температуры, которая становится причиной изменения основных свойств материала. Сегодня процедура пайки получила весьма широкое распространение, так как встречается оборудование, которое может применяться и в быту. Распространенным примером можно назвать пайку проводов и других металлических изделий, за счет которой и происходит их соединение. Также есть другие изделия, которые могут получить дефект и их устраняют именно при применении подобной технологии.
10. Электромонтаж. Подобная работа относится к особой категории технологических операций. Воздействие высокого тока становится причиной нагрева металла, за счет чего повышается его плавкость и степень обрабатываемости. Провести подобную технологическую операцию можно исключительно при применении специального оборудования.
11. Сборка. Часто встречается ситуация, когда конечное изделие получается при соединении отдельных элементов. Для выполнения подобной работы отведена целая операция. В последнее время сборка часто проводится на конвейере, за счет чего снижается стоимость конечного изделия и упрощается поставленная задача. Часто сборочная технологическая операция связана с применением болтов и других подобных крепежных изделий.
В заключение отметим, что существует довольно большое количество различных технологических операций, которые могут проводится для получения заготовок и деталей требуемой формы. В большинстве всего они заносятся в соответствующие технологические карты и отмечаются соответствующим символом. Встречается много различной технической документации, которая применяется при выпуске различной продукции.
Вопросы
Занятие № 7. Пути повышения точности при механической обработке заготовок
Повышение точности и производительности обработки на металлорежущих станках является комплексной проблемой, решение которой связано с улучшением качества изготовления металлорежущего оборудования, приспособления и инструментов, поддержанием их точностных характеристик при эксплуатации, а также автоматизацией, комплексной механизацией и роботизацией производства. Повышение качества оборудования на стадиях проектирования и изготовления достигается за счет совершенствования методов расчета конструкций, применения современных материалов, прогрессивной технологии обработки и сборки деталей и узлов. В результате этих мероприятий обеспечиваются надлежащие показатели жесткости станков и их рабочих органов, виброустойчивости и точности взаимного расположения исполнительных поверхностей. В процессе эксплуатации оборудования эти показатели поддерживаются в заданных пределах, научно обоснованной системой профилактики, технического обслуживания и ремонта. Автоматизация погрузочно-разгрузочных работ, контрольно-измерительных и транспортных операций на станках, внедрение автоматизированных и роботизированных линий коренным образом повышает производительность и точность обработки. Однако, вышеуказанные методы повышения точности не могут исключить влияния на размер обрабатываемых деталей таких факторов, как износ режущего инструмента, температурные, упругие и контактные деформации технологической системы станка. В связи с этим широкое применение на станках находят управление точностью обработки путем применения приборов активного контроля, управления упругими перемещениями технологической системы станок-деталь и системы автоматической подналадки. Кратко рассмотрим возможности и область применения каждого из этих способов управления. При управлении точностью с помощью приборов активного контроля, размер обрабатываемой детали непрерывно контролируется измерительным прибором. При достижении размеров обработки определенной, заранее установленной величины прибор активного контроля автоматически изменяет режимы резания, а когда размер достигает заданной номинальной величины — подается команда на остановку станка. Приборы активного контроля получили широкое применение в шлифовальных и хонинговальных станках, где происходит интенсивный износ режущего инструмента и требуется повышенная точность обработки. Однако, при применении приборов активного контроля измерение размеров происходит непосредственно в зоне резания, где на точность показания прибора оказывают влияния тепловыделения при резании, вибрации, стружка и смазочно-охлаждающая жидкость. Управление упругими перемещениями (адаптивная система управления станками) позволяет в процессе обработки изменять режимы резания в зависимости от заранее выбранного критерия точности. При адаптивной системе управления упругие перемещения технологической системы станка сохраняются постоянными, вследствие размерной поднастройки или же автоматического изменения скорости резания, величины подачи а также геометрии режущего инструмента. Адаптивная система управления позволяет достигать не только повышения размерной точности, но и высокой производительности, так как обработка ведется на оптимальных режимах резания. Этот способ управления точностью применяются на токарных и фрезерных станках, и требует окончательной шлифовки, так как из-за непостоянства режимов резания, шероховатости поверхности деталей получаются неодинаковые. Применение систем автоматической подналадки значительно повышает точность обработки, так как контролирование размеров деталей производится вне зоны резания на специальных измерительных устройствах, где точность измерения не зависит от тех факторов, которые влияют при активном контроле. Системы автоматической подналадки, по результатам измерения деталей, периодически корректируют положение режущего инструмента относительно обрабатываемой детали. При этом систематические составляющие погрешностей обработки, связанные с размерным износом инструмента, влиянием температурных деформаций, компенсируются. Недостатком системы автоматической подналадки является то, что процесс измерения отстает от процесса обработки, так как перемещение обработанной детали в позицию измерения требует определенного времени. Системы автоматической подналадки применяются на токарных, фрезерных, расточных и других станках. Определение оптимальных параметров системы автоматической подналадки является одним из основных этапов конструирования и эта задача, исходя из конкретных технологических процессов решается либо аналитически, либо моделированием на ЭВМ. Аналитический метод основан на анализе и установлении математической модели процесса по результатам обработки на станках без применения автоподналадчиков. При моделировании на ЭВМ исходный процесс задаётся в виде последовательности размеров обработанных деталей с помощью случайных чисел. Варьированием методов и параметров подналадки и сравнением находят оптимальные параметры для данного технологического процесса. В отличие от одношпиндельных станков, обработки на многошпиндельных токарных автоматах (МТА) является многопозиционной и многоинструментальной, т. е. обработка деталей ведется одновременно во всех позициях, за исключением загрузочной. Детали, закрепленные на шпинделях МТА, за полный оборот шпиндельного барабана последовательно проходят обработку во всех рабочих позициях. Обработка на каждом из шпинделей МТА протекает при неповторяющихся условиях, вызванных следующим индивидуальными особенностями: - шпиндели МТА, как сборочные единицы, отличаются точностью изготовления деталей и сборки; - степень смазки и регулировки подшипников шпинделей колеблются в переделах определенного допуска, следовательно, колеблются их износ и температурные деформации; - шпиндели отличаются упругой и контактной жесткостью; - расположения шпинделей по окружности барабана имеют погрешности, отличающиеся по модулю и направлению; - прутки в разных шпинделях могут отличаться по длине, отклонению диаметра и зажаты с различной силой. Вышеперечисленные особенности шпинделей являются причиной значительного расширения полей рассеивания размеров деталей, обработанных на МТА. Кроме того, на точность деталей, обработанных на разных шпинделей МТА, сказываются погрешности изготовления суппорта и его привода, непостоянство сил трения и жесткости всей технологической системы, динамической нагрузки, возникающей при повороте барабана и направления осей жесткости технологической системы. Для токарных станков, особенно, многошпиндельных токарных автоматов, которые работают на значительном диапазоне режимов резания и параметров заготовок приведенные выше методы расчета оптимальных параметров не приемлемы. Для таких станков параметры подналадки должны быть более универсальными, легко переналаживаемыми.
Таким образом, можно сказать, что существуют следующие пути повышения точности при механической обработке заготовок
1. Применение прогрессивных технологий и методов обработки поверхностей деталей.
Разработка технологий для комплексной (сопряженной) обработки высокоточных деталей.
2. Использование на станках систем автоматического управления точностью обработки.
Использование систем автоматического управления режимами обработки на металлорежущих станках позволяет в несколько раз снизить погрешности, вызванные упругими деформациями технологической системы от силы резания.
На станках с ЧПУ погрешности обработки от упругих деформаций технологической системы можно снизить также путем целенаправленного искажения траектории перемещения режущего инструмента относительно заготовки.
3. Применение более точного технологического оснащения на операциях механической обработки. Повышение точности технологического оснащения достигается: Применением виброустойчивой быстродействующей оснастки с повышенной жесткостью для обработки без переустановки заготовки; Оснащением станков системами температурной стабилизации отдельных узлов, устройствами для автоматической подналадки станка; Применением систем для оценки состояния режущего инструмента и систем автоматизированного контроля качества обрабатываемой поверхности; Использованием в приводах станков беззазорных сопряжений и механизмов, имеющих высокий коэффициент полезного действия; Применением виброизолирующих опор и направляющих из композиционных материалов, обладающих повышенной износостойкостью; Широким внедрением систем диагностики состояния станочного оборудования. 4. Повышение технологической дисциплины на операциях механической обработки, заключающейся в строгом регламентировании: Обоснованности допусков на параметры точности поверхностей или осей деталей; Системы мероприятий по обеспечению и контролю точности обработки на технологических операциях изготовления ответственных деталей; Выбора технологического оснащения и режимов обработки; Процедуры калибровки и поверки систем контроля процесса обработки; Системы мероприятий по подготовке инструмента к работе; Периодичности и содержания мероприятий по оценке состояния станков. В заключение следует отметить, что для каждого конкретного технологического процесса (или технологической операции) целесообразно выявлять свои наиболее эффективные пути повышения точности обработки. Это возможно лишь в том случае, когда технолог учитывает особенности функционирования, эксплуатации и наладки имеющегося в цехе технологического оборудования. |
Вопросы для проверки.
|
|
Автоматическое растормаживание колес: Тормозные устройства колес предназначены для уменьшения длины пробега и улучшения маневрирования ВС при...
Двойное оплодотворение у цветковых растений: Оплодотворение - это процесс слияния мужской и женской половых клеток с образованием зиготы...
Типы сооружений для обработки осадков: Септиками называются сооружения, в которых одновременно происходят осветление сточной жидкости...
Организация стока поверхностных вод: Наибольшее количество влаги на земном шаре испаряется с поверхности морей и океанов (88‰)...
© cyberpedia.su 2017-2024 - Не является автором материалов. Исключительное право сохранено за автором текста.
Если вы не хотите, чтобы данный материал был у нас на сайте, перейдите по ссылке: Нарушение авторских прав. Мы поможем в написании вашей работы!