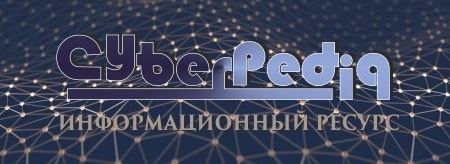
История создания датчика движения: Первый прибор для обнаружения движения был изобретен немецким физиком Генрихом Герцем...
Особенности сооружения опор в сложных условиях: Сооружение ВЛ в районах с суровыми климатическими и тяжелыми геологическими условиями...
Топ:
Характеристика АТП и сварочно-жестяницкого участка: Транспорт в настоящее время является одной из важнейших отраслей народного хозяйства...
Генеалогическое древо Султанов Османской империи: Османские правители, вначале, будучи еще бейлербеями Анатолии, женились на дочерях византийских императоров...
Интересное:
Аура как энергетическое поле: многослойную ауру человека можно представить себе подобным...
Уполаживание и террасирование склонов: Если глубина оврага более 5 м необходимо устройство берм. Варианты использования оврагов для градостроительных целей...
Инженерная защита территорий, зданий и сооружений от опасных геологических процессов: Изучение оползневых явлений, оценка устойчивости склонов и проектирование противооползневых сооружений — актуальнейшие задачи, стоящие перед отечественными...
Дисциплины:
![]() |
![]() |
5.00
из
|
Заказать работу |
|
|
Служебное назначение и конструкция детали
![]() |
Рисунок 1 – Чертеж детали |
Деталь «Втулка» является частью трубопровода и служит для прочного и герметичного соединения между собой деталей трубопровода. Соединительными элементами втулки является фланец с отверстиями для болтов и шпилек, равномерно расположенными по окружности, а также резьбовое отверстие М48х2. Втулка состоит из внутренних и наружных цилиндрических поверхностей. Поверхности с точными размерами выполнены по 8 и 7 квалитетам и предназначены для центрирования присоединяемых деталей. В конструкции втулки нет плоских и фасонных поверхностей.
Анализ технологичности детали
Технологичностью конструкции изделия по ГОСТ 14.205 - 83 называется совокупность свойств конструкции изделия, определяющих ее приспособленность к достижению определенных затрат при производстве, эксплуатации и ремонте для заданных показателей качества, объема выпуска и условий выполнения работ. Иными словами, технологичность – это совокупность свойств изделия, обеспечивающих его простое, качественное, экономичное изготовление и эксплуатацию.
Согласно ГОСТ 14.205 – 83 основными количественным показателям технологичности являются материалоемкость и трудоемкость изготовления изделия. До выбора заготовки и разработки технологического процесса изготовления детали определить эти показатели не представляется возможным. Потому первоначально технологичность конструкции определяется качественно экспертным путем.
Конструкция детали на рис. 1 является типовой для деталей данного класса. Поэтому технологический процесс также будет типовым, состоящим из токарной, сверлильной и шлифовальной операций. На токарной операции деталь следует обрабатывать за два установа. В этой связи необходимо проверить, чтобы линейные размеры на чертеже были проставлены от баз – торцевых поверхностей детали, как на рис. 2.
|
![]() |
Рисунок 2 – Чертеж детали с линейными размерами, проставленными от баз |
Такие поверхности называются настроечными базами. Использование этих баз обеспечивает заданную точность при обработке заготовки по методу автоматического получения размеров и упрощает промежуточный и окончательный контроль изделия. При необходимости в чертеж детали следует внести изменения.
Цилиндрические поверхности детали с высокими требованиями к точности и шероховатости обрабатываются шлифованием, чистовым или тонким точением. Задачу точности расположения поверхностей следует решать за счет точности станка и технологической оснастки. Так допуски отклонений от соосности и параллельности следует обеспечить базированием детали по внутренней поверхности Ø 30Н7. Поэтому данную поверхность необходимо обработать раньше, чем поверхности, базой для которых она является. Затем деталь устанавливается на эту поверхность с использованием самоцентрирующего устройства, например, цанговой оправки.
Эскиз поковки
Эскиз поковки выполняется основными линиями на чертеже детали в тонких линиях, с увеличением размеров отливки за счет припусков на обрабатываемых поверхностях и штамповочных уклонов. Штриховка производится по контуру поковки (рис. 7). Из контура поковки на эскизе следует исключить отверстия малого диаметра, канавки, проточки, ступени между цилиндрическими поверхностями с небольшим перепадом диаметров и другие мелкие элементы, получить которые штамповкой трудно или невозможно. На эскизе поковки должны быть проставлены размеры и номера обрабатываемых поверхностей. Часть номеров для поверхностей мелких элементов пропускается. На рисунке 7 в первой позиции для линейных размеров через косую черту обозначены номера поверхностей, между которыми проставлен этот размер. Для диаметральных размеров обозначен номер поверхности для этого размера. На эскизе специальными знаками должна быть указана плоскость разъема штампов и обозначен верх и низ от этой плоскости.
|
![]() |
Рисунок 7 – Эскиз поковки а – при вертикальном положении, б – при горизонтальном положении |
Определение припусков
Припуск – это слой материала, который удаляется с поверхности заготовки для получения заданных размеров изделия. Для каждой поверхности поковки припуск состоит из основного и дополнительного [1].
Основные припуски определяются по табл. 3, стр. 58 [1]. Эти припуски зависят от исходного индекса поковки, размеров детали и шероховатости поверхности. Припуски назначаются на одну сторону от номинального размера детали. В табл. 3 [1] все размеры детали делятся на два типа. К первому типу относятся размеры по признаку «Толщина». Ко второму типу отнесены размеры с признаком «Длина, ширина, диаметр, глубина и высота». Для каждого признака имеется своя строка с интервалами размеров детали. Чтобы определить к какому признаку относится тот или иной размер, необходимо воспользоваться эскизом поковки (рис. 7). Если линейный или диаметральный размер пересекает плоскость разъема штампов, то этот размер относится к первому типу. Поверхности с таким размером штампуются в двух половинах штампа и припуск на них определяется по строке «Толщина». Если размер находится сверху или снизу от плоскости разъема штампов, то этот размер относится ко второму типу. Поверхности с таким размером штампуются в одной половине штампа и припуск на них определяется по строке «Длина, ширина, диаметр, глубина и высота».
Таблица 6 – Основные припуски для поковки при вертикальном положении | |||||
Номер поверхности | Тип размера | Шероховатость,
| Припуск на сторону
| ||
Толщина, мм | Длина, диаметр, мм | ||||
1/13 | 55 | - | 3,2/3,2 | 1,6/1,6 | |
1/3 | - | 20 | 3,2/3,2 | 1,6/1,5 | |
1/5 | - | 25 | 3,2/3,2 | 1,6/1,5 | |
13/9 | - | 23 | 3,2/3,2 | 1,6/1,5 | |
13/11 | - | 25 | 3,2/3,2 | 1,6/1,5 | |
2 | - | Ø30 | 1,25 | 1,6 | |
4 | - | Ø 50 | 1,6 | 1,6 | |
10 | - | Ø 100 | 3,2 | 1,6 | |
14 | - | Ø 60 | 1,6 | 1,6 | |
16 | - | Ø 46* | 3,2 | 1,6 | |
Дробью указаны поверхности между которыми приставлен линейный размер, а также шероховатость и припуск для этих поверхностей; * – внутренний диаметр резьбы.
|
На рис. 7 при вертикальном положении поковки линию разъема штампов пересекает только один линейный размер 55, проставленный между поверхностями 1 и 13. Поэтому припуски на эти поверхности следует назначать по строке «Толщина». Все остальные размеры находятся по разные стороны от плоскости разъема и припуски на поверхности с этими размерами следует назначать по строке «Длина, ширина, диаметр, глубина и высота» (табл. 6).
При горизонтальном положении поковки на рис. 7 диаметральные размеры пересекают линию разъему штампов. Поэтому припуски на эти поверхности следует назначать по строке «Толщина». Линейные размеры находятся по разные стороны от плоскости разъема и припуски на поверхности с этими размерами следует назначать по строке «Длина, ширина, диаметр, глубина и высота» (табл. 7).
Таблица 7 – Основные припуски для поковки при горизонтальном положении | ||||
Номер поверхности | Тип размера | Шероховатость,
| Припуск на сторону
| |
Толщина, мм | Длина, мм | |||
1/13 | - | 55 | 3,2/3,2 | 1,6/1,6 |
1/3 | - | 20 | 3,2/3,2 | 1,6/1,5 |
13/9 | - | 23 | 3,2/3,2 | 1,6/1,5 |
4 | Ø 50 | - | 1,6 | 1,7 |
10 | Ø 100 | - | 3,2 | 1,8 |
14 | Ø 60 | - | 1,6 | 1,7 |
Дополнительные припуски назначают для учета смещения по поверхности разъема штампов, а также изогнутости, отклонения от плоскостности и прямолинейности (коробления). Припуск для учета смещения по поверхности разъема штампов назначают в зависимости от массы и класса точности поковки (табл. 4, стр. 59 [1]. Припуск для учета изогнутости, отклонения от плоскостности и прямолинейности (коробления) назначают в зависимости от наибольшего размера поковки (детали) и класса точности поковки (табл. 5, стр. 59 [1]). Точных рекомендаций по назначению этих припусков в стандарте нет.
Только отмечается, что они зависят от формы поковки и технологии ее изготовления. Это требует анализа влияния этих факторов на назначение дополнительных припусков в каждом конкретном случае. В тоже время смещение по поверхности разъема штампов и коробление поковки могут одновременно влиять на форму и расположение поверхностей. Поэтому с целью упрощения задачи целесообразно назначать дополнительный припуск на каждую поверхность как сумму припусков от смещения и коробления, т.е.
|
В данном случае масса поковки 1,69 кг, наибольший размер поковки (детали) 100 мм, класс точности поковки Т4. Поверхность разъема – плоская. Для этих параметров будем иметь следующее значение для дополнительного припуска
Общий припуск равен суммеосновного и дополнительного припусков
Расчет размеров поковки
Линейные размеры. Этими размерами определяется расстояние между двумя поверхностями. Расчет линейных размеров заготовки производится по формуле
где размер детали,
припуски на первой и второй поверхности. Знаки припусков в этой формуле определяются типом поверхности (рис. 9).
![]() |
Рисунок 9 – Тип поверхности а – наружная, б – внутренняя, в – ступенчатая, г – глухая |
Выбор знаков припусков представлен в таблице 8
Таблица 8 – Знаки припусков
Припуск | Тип поверхности | |||
Наружная | Внутренняя | Ступенчатая | Глухая* | |
![]() | + | – | + | + |
![]() | + | – | – | – |
* используется для расчета размеров глубины глухих отверстий и пазов. |
Пример 1. Линейный размер между поверхностями 1 и 13. Исходный индекс здесь и далее 11. (рис. 7). Тип поверхности – наружная (рис. 9, а). Основной припуск на сторону для каждой поверхности
(табл. 7). Дополнительный припуск на сторону для каждой поверхности
Общий припуск
Размер поковки
.
Пример 2. Линейный размер между поверхностями 13 и 9.
(рис. 7). Тип поверхности – ступенчатая (рис. 9, в). Основной припуск на сторону для поверхности 13 Основной припуск на сторону для поверхности 9
(табл. 6). Дополнительный припуск на каждую сторону
Общий припуск для поверхности 13
Общий припуск для поверхности 9
Размер поковки
Пример 3. Линейный размер между поверхностями 13 и 11.
(рис. 7). Тип поверхности – глухая (рис. 9, г). Отверстие резьбовое. Внутренний диаметр резьбы 46 мм. Глубина намеченного отверстия
больше размера на чертеже. Поэтому припуск назначается на поверхность с размером на чертеже. Основной припуск на сторону для поверхности 13
Основной припуск на сторону для поверхности 11
(табл. 6). Дополнительный припуск на каждую сторону
Общий припуск для поверхности 13
Общий припуск для поверхности 11
Размер поковки
Пример 4. Линейный размер между поверхностями 1 и 5. (рис. 7).
Тип поверхности – глухая (рис. 9, г). Глубина намеченного отверстия
меньше размера на чертеже. Поэтому припуск назначается на глубину намеченного отверстия. Основной припуск на сторону для поверхности 1
Основной припуск на сторону для поверхности 5
(табл. 6). Дополнительный припуск на каждую сторону
Общий припуск для поверхности 1
|
Общий припуск для поверхности 5
Размер поковки
Диаметральные размеры заготовки определяются по формуле
Припуск со знаком «плюс» принимается для наружной поверхности, а припуск со знаком «минус» для внутренней поверхности.
Пример 5. Поверхность 10. Основной припуск на сторону для поверхности 10
(табл. 6). Дополнительный припуск на сторону
Общий припуск
Размер поковки
Пример 6. Поверхность 16. Отверстие резьбовое. Внутренний диаметр резьбы Основной припуск на сторону для поверхности 16
(табл. 6). Дополнительный припуск на сторону
Общий припуск
Размер поковки
Результаты расчета
Результаты расчета для поковки при вертикальном и горизонтальном положениях представлены в табл. 9 и в табл. 10.
Таблица 9 – Результаты расчета для поковки при вертикальном положении
| |||||||||||
Номер поверхности | Тип размера | Шероховатость Ra, мкм | Припуски на сторону, мм | Допуск, мм | Отклонения, мм | Размер, мм | |||||
Толщина, мм | Длина, диаметр, мм | ||||||||||
Основной | Дополнительный | Общий | Верхнее | Нижнее | |||||||
1/13 | 55 | - | 3,2/3,2 | 1,6/1,6 | 0,6 | 2,2/2,2 | 2 | +1,3 | – 0,7 | ![]() | |
1/3 | - | 20 | 3,2/3,2 | 1,6/1,5 | 0,6 | 2,2/2,1 | 1,6 | +1,1 | – 0,5 | ![]() | |
1/5 | - | 24* | 3,2/3,2 | 1,6/1,5 | 0,6 | 2,2/2,1 | 1,6 | +1,1 | – 0,5 | ![]() | |
13/9 | - | 23 | 3,2/3,2 | 1,6/1,5 | 0,6 | 2,2/2,1 | 1,6 | +1,1 | – 0,5 | ![]() | |
13/11 | - | 25 | 3,2/3,2 | 1,6/1,5 | 0,6 | 2,2/2,1 | 1,6 | +1,1 | – 0,5 | ![]() | |
2 | - | Ø30** | 1,25 | 1,6 | 0,6 | 2,2 | 1,6 | +1,1 | – 0,5 | ![]() | |
4 | - | Ø 50 | 1,6 | 1,6 | 0,6 | 2,2 | 2 | +1,3 | – 0,7 | ![]() | |
10 | - | Ø 100 | 3,2 | 1,6 | 0,6 | 2,2 | 2,2 | +1,4 | – 0,8 | ![]() | |
14 | - | Ø 60 | 1,6 | 1,6 | 0,6 | 2,2 | 2 | +1,3 | – 0,7 | ![]() | |
16 | - | Ø 46** | 3,2 | 1,6 | 0,6 | 2,2 | 2 | +1,3 | – 0,7 | ![]() | |
* – глубина намеченного отверстия, ** – диаметр отверстия |
Таблица 10 – Результаты расчета для поковки при горизонтальном положении
| |||||||||||
Номер поверхности | Тип размера | Шероховатость Ra, мкм | Припуски на сторону, мм | Допуск, мм | Отклонения, мм | Размер, мм | |||||
Толщина, мм | Длина, диаметр, мм | ||||||||||
Основной | Дополнительный | Общий | Верхнее | Нижнее | |||||||
1/13 | - | 55 | 3,2/3,2 | 1,6/1,6 | 0,6 | 2,2/2,2 | 2 | +1,3 | – 0,7 | ![]() | |
1/3 | - | 20 | 3,2/3,2 | 1,6/1,5 | 0,6 | 2,2/2,1 | 1,6 | +1,1 | – 0,5 | ![]() | |
13/9 | - | 23 | 3,2/3,2 | 1,6/1,5 | 0,6 | 2,2/2,1 | 1,6 | +1,1 | – 0,5 | ![]() | |
4 | Ø 50 | - | 1,6 | 1,7 | 0,6 | 2,3 | 2 | +1,3 | – 0,7 | ![]() | |
10 | Ø 100 | - | 3,2 | 1,8 | 0,6 | 2,4 | 2,5 | +1,6 | – 0,9 | ![]() | |
14 | Ø 60 | - | 1,6 | 1,7 | 0,6 | 2,3 | 2 | +1,3 | – 0,7 | ![]() |
Чертеж поковки
Чертеж поковки при вертикальном и горизонтальном положениях представлен на рис. 10. Отверстие в перемычке не пробивается, т.к. оно будет меньше 30 мм.
![]() |
Рисунок 7 – Чертеж поковки а – при вертикальном положении, б – при горизонтальном положении |
Библиографический список
1. 7505-89. Поковки стальные штампованные. Допуски, припуски и кузнечные напуски. – М.: Государственный комитет СССР по управлению качеством продукции и стандартами, 1990. – 52 с.
Приложение А
Правила нумерации поверхностей
Нумерация поверхностей для цилиндрической детали выполняется по следующим правилам.
1. С чертежа детали удалить все размеры и надписи.
2. Поверхности обозначаются выносными линиями, которые заканчиваются с одной стороны стрелкой, а с другой стороны полкой.
3. Поверхности, оси отверстий перпендикулярные оси детали, «глухие» отверстия и лыски, расположение которых определяется линейными размерами (рис. 2), последовательно обозначаются нечетными номерами с увеличением номера снизу-вверх про вертикали с левого торца, по горизонтали слева направо вдоль оси детали, сверху вниз по вертикали с правого торца.
4. Цилиндрические поверхности, фаски, канавки, сквозные лыски и оси сквозных отверстий параллельные оси детали последовательно обозначаются четными номерами с увеличением номера сверху вниз по вертикали с левого торца, по горизонтали слева направо вдоль оси детали, снизу-вверх по вертикали с правого торца.
5. Для удобства обозначения четными и нечетными номерами рекомендуется группировать их с разных сторон от оси детали. При горизонтальном расположении детали четные внизу, а нечетные вверху. При вертикальном расположении детали четные слева, а нечетные справа.
6. Четными номерами обозначаются радиусы и фаски, которые получаются отдельной обработкой. (поз. А, Г и Д, рис. 1). Фаски обозначаются четными номерами. Из двух нечетных поверхностей, между которыми находится фаска, обозначается только одна нечетная поверхность.
7. Не обозначаются радиусы и фаски в узких канавках (поз. Б, рис. 1, поз. Е, рис. 2). Форма этих поверхностей получается за счет формы инструмента.
8. Не обозначаются фаски и радиусы перехода цилиндрических поверхностей к цилиндрическим и торцевым поверхностям. Форма этих поверхностей получается за счет формы инструмента (поз. В, рис. 1, поз. К и Ж, рис. 3).
9. Не обозначаются фаски и радиусы в канавках для выхода резьбы и шлифовального круга. Форма этих поверхностей получается за счет формы инструмента (поз. З и И, рис. 3, поз. Л и М, рис. 4).
10. Линии перехода фасками и канавками от одной цилиндрической поверхности к другой с разными или одинаковыми диаметрами обозначать как указано в примерах (рис. 1, поз. 3 и 6; поз. 5 и 10; рис. 2, поз. 13 и 10; поз. 15 и 14; поз. 17 и 16; рис. 3, поз. 5 и 10; поз. 9; поз. 13 и 20; поз. 15, 17; рис. 4, поз. 7 и 10; поз. 5 и 12).
11. Нумерация поверхностей отверстий с общей осью, параллельной оси детали, показана позициями 5 и 10 на рис. 5.
12. На чертеже с обозначением поверхностей не должно быть выносных линий с буквами А, Б и. т. д. Они были нужны только для указания правил обозначения соответствующих поверхностей.
Примеры обозначения поверхностей представлены на рис.1 – 4.
Рисунок – 1 |
Рисунок – 5 |
Рисунок – 2 |
Рисунок – 3 |
Рисунок – 4 |
Приложение Б
Бланк для определения исходного индекса
Служебное назначение и конструкция детали
![]() |
Рисунок 1 – Чертеж детали |
Деталь «Втулка» является частью трубопровода и служит для прочного и герметичного соединения между собой деталей трубопровода. Соединительными элементами втулки является фланец с отверстиями для болтов и шпилек, равномерно расположенными по окружности, а также резьбовое отверстие М48х2. Втулка состоит из внутренних и наружных цилиндрических поверхностей. Поверхности с точными размерами выполнены по 8 и 7 квалитетам и предназначены для центрирования присоединяемых деталей. В конструкции втулки нет плоских и фасонных поверхностей.
|
|
Историки об Елизавете Петровне: Елизавета попала между двумя встречными культурными течениями, воспитывалась среди новых европейских веяний и преданий...
Своеобразие русской архитектуры: Основной материал – дерево – быстрота постройки, но недолговечность и необходимость деления...
Поперечные профили набережных и береговой полосы: На городских территориях берегоукрепление проектируют с учетом технических и экономических требований, но особое значение придают эстетическим...
Кормораздатчик мобильный электрифицированный: схема и процесс работы устройства...
© cyberpedia.su 2017-2024 - Не является автором материалов. Исключительное право сохранено за автором текста.
Если вы не хотите, чтобы данный материал был у нас на сайте, перейдите по ссылке: Нарушение авторских прав. Мы поможем в написании вашей работы!