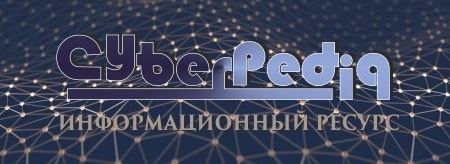
Организация стока поверхностных вод: Наибольшее количество влаги на земном шаре испаряется с поверхности морей и океанов (88‰)...
Историки об Елизавете Петровне: Елизавета попала между двумя встречными культурными течениями, воспитывалась среди новых европейских веяний и преданий...
Топ:
Характеристика АТП и сварочно-жестяницкого участка: Транспорт в настоящее время является одной из важнейших отраслей народного хозяйства...
Характеристика АТП и сварочно-жестяницкого участка: Транспорт в настоящее время является одной из важнейших отраслей народного...
Эволюция кровеносной системы позвоночных животных: Биологическая эволюция – необратимый процесс исторического развития живой природы...
Интересное:
Как мы говорим и как мы слушаем: общение можно сравнить с огромным зонтиком, под которым скрыто все...
Подходы к решению темы фильма: Существует три основных типа исторического фильма, имеющих между собой много общего...
Принципы управления денежными потоками: одним из методов контроля за состоянием денежной наличности является...
Дисциплины:
![]() |
![]() |
5.00
из
|
Заказать работу |
Ремонт надрессорных балок
10.1. Надрессорные балки перед ремонтом и дефектацией очищают от грязи, отслоившейся ржавчины и разрушившегося лакокрасочного покрытия, обмывают в моечной машине, осматривают на возможность обнаружения трещин, отколов и износов. Опорную поверхность подпятника балки очищают до металла.
10.2. При осмотре и дефектации надрессорной балки определяют целостность верхних, нижних поясов, вертикальных стенок и колонки при ее наличии, опорной части подпятника, как указано в Приложении Г.
Трещины во внутренней колонке и ребрах усиления подпятника надрессорной балки независимо от их длины ремонту не подлежат. Внутреннюю поверхность балки осматривают с подсветкой через технологические окна верхнего и нижнего поясов.
10.3. При капитальном или деповском ремонтах под вагон подкатывают тележки с надрессорными балками, с установленными износостойкими элементами.
Оставшийся срок службы надрессорных балок должен быть не менее чем до следующего капитального или деповского ремонта вагона соответственно.
10.4. Ремонт подпятника надрессорной балки.
10.4.1. При поступлении надрессорной балки с установленными ранее в подпятнике износостойкими элементами (или накладкой чертеж 100.00.027-0, или прокладкой чертеж М1698.01.005, или чашей чертеж 578.00.012-1), накладку или прокладку, или чашу снять.
Подпятник и снятые износостойкие элементы осмотреть.
После определения объема ремонта все дефекты подпятника надрессорной балки должны быть отремонтированы.
10.4.2. При плановых видах ремонта разрешается заварка трещин в подпятнике надрессорной балки, согласно рисунку 15, в соответствии с требованиями "Инструкции по сварке и наплавке при ремонте грузовых вагонов".
Заварку трещин на опорной поверхности подпятникового места, не переходящих через наружный бурт и расположен от центра не ближе 80 мм, при условии, что суммарная длина не более 250 мм, как указано в приложении Г.
Подпятник с глубиной, имеющий износы плоской опорной поверхности или износы на наружном и внутреннем буртах наплавить согласно "Инструкции по сварке и наплавке при ремонте грузовых вагонов" с обеспечением твердости 240...300 НВ с последующей механической обработкой и обеспечением конусности внутренней поверхности наружного бурта 1:12,5 и до размеров, приведенных таблице 8.1 и установкой или износостойкой накладки, или прокладки, или чаши.
Для установки чаши, подпятник надрессорной балки тележки модели 18-578, растачивается на глубину мм с обеспечением конусности 1:12,5.
Диаметр подпятника, определять от верхней горизонтальной поверхности наружного бурта на глубине 10 мм с учетом конусности 1:12,5 ("И" рисунок 13).
Глубину подпятника определять от верхней горизонтальной поверхности наружного бурта.
Контроль диаметра подпятника надрессорной балки производить в соответствии с "Методикой выполнения измерений деталей и узлов тележек моделей 18-578 и 18-9771 при проведении плановых видов ремонта" РД 32 ЦВ 081-2018.
10.4.3. Оставшаяся толщина опорной поверхности подпятника надрессорных балок тележек моделей 18-578 и 18-9771 до проведения наплавочных (ремонтных) работ должна быть не менее 30 мм.
10.4.4. При механической обработке подпятника в месте сопряжения наружного бурта с плоской опорной поверхностью подпятника должна быть обеспечена галтель радиусом 3 - 4 мм. Отсутствие радиуса галтели не допускается.
10.4.5. Разрешается производить ремонт отверстия "Л" показанного на рисунке 13 и таблицах 8.1 и 10.2 подпятника под шкворень с восстановлением внутреннего бурта "К" приведенного на рисунке 13 и таблицах 8.1 и 10.2 и постановкой втулки, изготовленной из стали марки Ст 3 ГОСТ 380, с приваркой ее по наружному диаметру сплошным швом. Внутренний бурт подпятника восстанавливается наплавкой с последующей механической обработкой до размеров, указанных в таблицах 8.1 и 10.2.
Верхняя кромка внутреннего бурта или втулки должна располагаться от плоской опорной поверхности на высоте 10+/-1 мм у подпятника, расточенного на глубину мм.
10.4.6. За базовую поверхность надрессорной балки при установке на станок принимать опорные поверхности, которыми надрессорная балка опирается на пружины рессорных комплектов.
10.4.7. Чашу чертеж 578.00.012-1, имеющую трещины или деформации, не позволяющие свободно устанавливать ее в восстановленный подпятник, а также имеющую сверхнормативные износы, при всех видах ремонта заменить на новую.
Чаши, имеющие механические повреждения, трещины, деформации, недопустимые износы ремонту и восстановлению не подлежат.
При капитальном ремонте чашу заменить на новую.
При деповском ремонте допускается постановка чаши с максимальным внутренним диаметром не более 304 мм определенным на глубине 10 мм с учетом конусности 1:12,5. При этом толщина стенок чаши в месте измерения диаметра должна быть не менее 3,5 мм.
Установка чаши в подпятниковое место надрессорной балки производится с наплавкой ограничителей.
10.5. Ремонт наклонных плоскостей надрессорной балки.
10.5.1. При плановых видах ремонта удалить ранее приваренные планки на наклонных плоскостях.
Изношенные наклонные плоскости восстановить износостойкой наплавкой с обеспечением твердости 240 - 300 НВ, согласно "Инструкции по сварке и наплавке при ремонте грузовых вагонов" с последующей механической обработкой до размеров, указанных в таблице 8.1.
10.5.2. Оставшаяся толщина изношенных наклонных поверхностей надрессорной балки, в том числе после удаления планок, должна быть не менее 7 мм.
10.5.3. При капитальном ремонте изношенные наклонные плоскости восстановить износостойкой наплавкой с обеспечением твердости 240...300 НВ согласно "Инструкции по сварке и наплавке при ремонте грузовых вагонов" с последующей механической обработкой до размеров, указанных в таблице 8.1.
При выпуске из деповского ремонта допускается не восстанавливать наклонные плоскости, если они имеют размер нижней опорной поверхности "З" (рисунок 13, таблица 10.2) надрессорной балки не менее 166 мм и угол 45° причем величина суммарного просвета между поверхностью надрессорной балки и нижней кромки шаблоном должна быть не более 6 мм. Просвет сверху не допускается.
10.5.4. При всех видах ремонта дефектацию надрессорной балки провести в соответствии с требованиями приложения Г.
10.5.5. При деповском ремонте расстояние между ограничительными буртами для фрикционного клина "е" согласно рисунку 15 и таблицы 10.2 при размере более 140 мм восстанавливают наплавкой, согласно "Инструкции по сварке и наплавке при ремонте грузовых вагонов" с последующей механической обработкой до размеров, указанных в таблице 8.1.
При капитальном ремонте расстояние между ограничительными буртами "е" (рисунок 15 и таблица 8.1) восстанавливаются до размеров, указанных в таблице 8.1.
10.5.6. При комплектовании тележек новыми или отремонтированными надрессорными балками на них устанавливаются износостойкие элементы завода-изготовителя или по проекту М1698.00.000.
10.6. Ремонт скользунов надрессорной балки.
10.6.1. Технические требования к скользунам, показанным на рисунке 4, приведены в таблице 10.1.
10.6.2. При плановых видах ремонта восстановление или ремонт деталей скользуна сваркой и наплавкой не допускается. Ремонт производить только заменой негодных деталей скользуна на новые.
10.6.3. При деповском ремонте разрешается установка деталей скользуна с износами, указанными в таблице 10.1 и соответствующие требованиям, определяющим предельное состояние.
При капитальном ремонте детали скользуна с износами или повреждениями заменяются новыми, соответствующими требованиям, указанным в таблице 10.1.
Упругий элемент скользуна осмотреть, при наличии трещин, разрывов и других механических повреждений, заменить новым.
Перед установкой упругого элемента в корпус скользуна ВМ 003.000 упругий элемент необходимо выдержать не менее 12 часов при температуре не ниже +50 С.
Демпфер скользуна 578.00.020-0 до регулировки скользунов должен быть выдержан в течение не менее 8 часов при температуре не менее 180 С.
Таблица 10.1
Наименование параметра | Технические требования или размеры, мм | Указания по использованию | |
при КР | при ДР | ||
1 | 2 | 3 | 4 |
Скользун ВМ 003.000 | |||
Установочная высота скользуна (расстояние между опорной пластиной скользуна на кузове вагона и надрессорной балкой в месте установки скользуна), мм | Не менее 127 | отрегулировать пластинами на опоре кузова вагона | |
Трещины и изломы элемента упругого | не допускается | не допускается | бракуется, ремонту не подлежит |
Износ опорной поверхности колпака скользуна упорного, мм | не допускается | не более 2 | бракуется, ремонту не подлежит |
Толщина опорной поверхности колпака скользуна упорного, мм | не менее 17 | не менее 15 | бракуется, ремонту не подлежит |
Упруго-катковый скользун 578.00.020-0 СБ | |||
Размер "А" от ролика до опорной поверхности колпака, мм: | |||
в свободном состоянии; | не менее 28 | отрегулировать прокладками | |
под тарой (брутто) | 8+/-2 | не менее 6 | |
Высота демпфера, мм | 116+/-1 | не менее 114 | бракуется, ремонту не подлежит |
Трещины и изломы демпфера | не допускается | дефект, нарушающий целостность | бракуется, ремонту не подлежит |
Диаметр ролика, мм | 65-0,74 | не менее 62 | бракуется, ремонту не подлежит |
Износ опорной поверхности колпака скользуна, мм | не допускается | не более 2 | деталь из ВЧ бракуется, ремонту не подлежит |
Толщина опорной поверхности колпака скользуна, мм | 12+/-1 | не менее 10 | бракуется, ремонту не подлежит |
10.6.4. При деповском ремонте контактную пластину скользуна на кузове вагона, приведенной на рисунке 16, при максимальном износе 1 мм заменить на новую.
10.7. При деповском ремонте шкворни, имеющие износы по диаметру более 3 мм, восстановить наплавкой в соответствии "Инструкцией по сварке и наплавке при ремонте грузовых вагонов" с последующей механической обработкой. Верхнюю часть шкворня обрабатывают согласно рисунку 14.
Тележки должны иметь шкворни длиной 440+/-3 мм.
Отверстия подпятника надрессорной балки под шкворень должны соответствовать размерам, приведенным в таблицах 8.1. и 10.2.
10.8. При капитальном ремонте шкворни, имеющие механические повреждения, изгибы или износы, заменить на новые.
При деповском ремонте шкворни, имеющие изгибы не более 5 мм разрешается править в нагретом состоянии до размеров, приведенных на рисунке 14.
10.9. Разрешается наплавлять разработанные отверстия в кронштейне державки "мертвой точки".
10.10. При сборке тележки проверить размеры надрессорной балки, показанные на рисунке 13, которые должны соответствовать размерам, указанным в таблице 10.2.
Таблица 10.2
Обозначение размера | Размеры надрессорной балки по рабочим чертежам, мм | Размеры надрессорной балки, мм | |||||
при ДР (без восстановления) | при КР | ||||||
тележка модели 18-578 | тележка модели 18-9771 | тележка модели 18-578 | тележка модели 18-9771 | ||||
тележка модели 18-578 | тележка модели 18-9771 | ||||||
е | 134+4 | не более 140,0 | 134+4 | ||||
З | 175+/-1 | не менее 166,0 | 175+/-1 | ||||
Л | 54+/-2 | не более 60,0 | 54+/-2 | ||||
К | 77-0,74 | 77-3 | не менее 72,0 | 77-0,74 | 77-3 | ||
И (с прокладкой) |
| не более 306 |
| ||||
И (с чашей) | 315+1,0+0,2 | - | 315+2,0 | - | 315+1,0+0,2 | - | |
Разность размеров А1 и А2 должна быть не более 5 мм |
Рисунок 13 - Размеры надрессорных балок грузовых тележек моделей
18-578 и 18-9771
* Размер для справок;
Допускается смятие концов не более 90 на длине 50 мм;
Материал:
Рисунок 14 - Шкворень
(1) - продольные трещины стенки наклонной плоскости, не переходящие на ограничительные бурты;
(2) - износ упорных ребер, ограничивающих пружины;
(3) - трещины на опорной поверхностях подпятникового места, не переходящих через наружный бурт и расположенных от центра не ближе 80 мм, при условии, что их суммарная длина не превышает 250 мм;
(4) - отколовшиеся части наружного бурта подпятникового места;
(5) - трещины на верхнем поясе, идущие от технологического отверстия, суммарной длиной не более 250 мм и не переходящие через наружный бурт подпятникового места;
(6) - износ внутренней поверхности ограничительных буртов при оставшейся толщине бурта не менее 10 мм;
(7) - трещины в углах между ограничительными буртами и наклонной плоскостью, не переходящие на верхний пояс балки;
(8) - износ наружной поверхности внутреннего бурта;
(9) - износ внутренней поверхности наружного бурта при оставшейся толщине наружного бурта не менее 15 мм;
(10) - износ отверстий в кронштейне державки "мертвой точки";
(11) - отколовшиеся части внутреннего бурта подпятникового места;
(12) - износ опорной поверхности подпятникового места балок при оставшейся толщине металла в месте износа не менее 30 мм
(13) - износ отверстия под шкворень;
(14) - износа наклонных плоскостей, в том числе вваркой пластин-вставок при оставшейся толщине стенки менее 7,0 мм;
Примечание: трещины, расположенные к продольной оси балки под углом более 30° относятся к поперечным, под углом менее 30° - к продольным.
Рисунок 15 - Дефекты надрессорных балок, ремонт которых разрешен сваркой и наплавкой
1 - скользун, 2 - опорная пластина, 3 - винт, 4 - шайба стопорная,5 - гайка, 6 - проволока, 7 - прокладка регулировочная, 8 - контргайка, 9 - ролик, 10 - демпфер скользуна тележки
Рисунок 16 - Узел соединения скользуна тележки вагона и ответной части
на шкворневой балке вагона
11. Ремонт узла "клин - фрикционная планка"
11.1. Узел гасителя колебаний тележек моделей 18-9771 и 18-578 состоит из составной фрикционной планки чертеж 100.00.008-2, фрикционного клина чертеж 578.30.002-1 с полиуретановой накладкой марки АПИ-4 ТУ 2252-008-00203476 чертеж 578.30.003-1, показанного на рисунке 17 и наклонной поверхности надрессорной балки.
11.2. При плановых видах ремонта во фрикционный узел тележки модели 18-578, при переоборудовании по проекту М1826.00.000, устанавливается клин фрикционный по чертежу М1698.00.003 из чугуна СЧ35 ГОСТ 1412, показанного на рисунке 18.
11.2.1. При деповском ремонте на все типы грузовых вагонов, кроме цистерн, разрешается устанавливать чугунные клинья СЧ35 с суммарным износом наклонной и вертикальной плоскостей клина до 3 мм, но не более 2 мм одной из сторон и не имеющих других дефектов (трещин, отколов), а фрикционные клинья чертеж 578.30.002-1 с полиуретановой накладкой чертеж 578.30.003-1 (если тележку не переоборудовали по проекту М1826.00.000) с износом вертикальной плоскости до 2 мм и не имеющих других дефектов (трещин, отколов).
Полнота клина с полимерной накладкой (размер "А", показанный на рисунке 17) при деповском ремонте должна составлять не менее 232 мм, а при капитальном ремонте не менее 237,5 мм.
Не допускается постановка износостойкой полиуретановой накладки, имеющей трещины, отколы, расслоения, прижоги и другие повреждения.
11.3. При капитальном ремонте в тележки устанавливаются новые фрикционные клинья.
Трещины в ребрах жесткости клина при всех видах ремонта не допускаются.
Рисунок 17 - Фрикционный клин чертеж 578.30.002-1 с полиуретановой
накладкой чертеж 578.30.003-1
Рисунок 18 - Фрикционный клин чертеж М 1698.00.003 ПКБ ЦВ
11.4. При капитальном ремонте составные фрикционные планки заменить новыми по чертежам М1698.02.001 и М1698.02.004, показанными на рисунке 19.
а) планка подвижная толщиной 6 мм | б) планка неподвижная толщиной 10 мм |
Рисунок 19. - Фрикционные планки
11.5. При деповском ремонте фрикционные планки с трещинами, отколами и износами, превышающими нормативные значения, заменяются новыми.
Допускается на все типы грузовых вагонов, кроме цистерн, устанавливать неподвижные фрикционные планки по проекту М1698.00.000 толщиной 10 мм с износом 1,5 мм поверхности, взаимодействующей с подвижной планкой толщиной 6 мм и подвижные фрикционные планки с суммарным износом по толщине до 2 мм, но не более 1,5 мм с одной стороны.
Измерение производятся от неизношенной поверхности фрикционной планки в соответствии с требованиями, изложенными в "Методике выполнения измерений деталей и узлов тележек моделей 18-578 и 18-9771 при проведении плановых видов ремонта" РД 32 ЦВ 081-2018.
11.6. Неподвижные фрикционные планки в вертикальной плоскости должны быть непараллельны, расстояние между планками к низу должно увеличиваться на 4 - 10 мм.
Фрикционные планки, приклепанные к площадкам, должны плотно прилегать к ним, при этом допускается:
между сопрягаемыми поверхностями (в промежутках между заклепками и планки) местные не плотности не более 1 мм;
в зоне головок заклепок местный зазор на 1/3 окружности головки заклепки, при проверке которого щуп 1 мм не должен доходить до стержня заклепки;
западание головки заклепки относительно плоскости планки не более 2 мм.
Заклепки не должны выступать за рабочую поверхность планки. При наличии выступа его следует зачистить заподлицо с поверхностью планки.
Непараллельность фрикционных планок в горизонтальной плоскости не более 3 мм.
11.7. Перед началом клепальных работ поверхность боковой рамы, прилегающая к поверхности фрикционной планки, допускается зачистить шлифовальной машинкой, для обеспечения плотного прилегания фрикционной планки к привалочной поверхности.
11.8. При установке и креплении неподвижной планки чертеж 100.00.008-2, отверстия в боковой раме под заклепки должны быть диаметром 21+0,84 мм. Планки крепятся заклепками диаметром 20 мм по ГОСТ 10299. Усилие горячей клепки должно быть не менее 245 (25) кН (тс). Температура нагрева заклепки должна быть в пределах 1050 - 1100°С. Нагрев рекомендуется производить в угольных, газовых или электрических печах.
11.9. Неподвижные фрикционные планки толщиной 10 мм с одной и более ослабленными заклепками переклепываются путем замены ослабших заклепок.
Запрещается ослабшие заклепки фрикционных планок заваривать, подтягивать и подчеканивать, они должны быть заменены новыми.
Запрещается выпускать из ремонта боковые рамы с приваренными электросваркой фрикционными планками.
Требования к пружинам рессорного комплекта
12.1. При ремонте тележек моделей 18-578 и 18-9771, все пружины рессорного комплекта тележки проходят осмотр и измерения с целью выявления дефектов и подбора комплектов пружин.
Пружины снимают с тележки независимо от технического состояния, очищают и осматривают.
Пружины, имеющие дефекты:
изломы, отколы, трещины витков;
протертости, коррозированные повреждения более 10% площади сечения витков;
смещение опорных витков;
высоту, меньше указанной на рисунке 20, к установке в рессорный комплект при всех видах ремонта - не допускаются.
Каждая пружина рессорного комплекта тележки должна иметь клеймо завода-изготовителя или бирку завода-изготовителя с полной маркировкой пружины. Применение пружин, не имеющих маркировки завода-изготовителя не допускается.
Вновь устанавливаемые пружины по чертежам 578.30.006-1, 578.30.007-1, 9771-06.06.00.001 и 9771-06.06.00.002 должны соответствовать ГОСТ 1452.
Характеристики пружин рессорного подвешивания приведены в таблице 12.1.
Таблица 12.1.
Пружина | Диаметр прутка, мм | Наружный диаметр витка, мм | Внутренний диаметр витка, мм | Число витков | Высота пружины в свободном состоянии, мм | Масса, кг | |
полное | рабочее | ||||||
Наружная | 28 | 200 | 144+/-2,5 | 5,4 | 3,9 | 12,8 | |
Внутренняя | 19 | 134+/-2 | 96 | 7,5 | 6 | 6,8 |
Рисунок 20 - Дефекты пружин, при которых они подлежат браковке
12.2. Разница высот наружной и внутренней пружин (пружина в сборе) в свободном состоянии не должна превышать 2 мм.
Запрещается постановка пружин в одном рессорном комплекте (на одной боковой раме) с разницей по высоте более 4 мм.
12.3. Под фрикционные клинья устанавливаются пружины из рессорного комплекта наибольшей высоты.
12.4. На боковой поверхности опорного витка пружин должна быть нанесена следующая маркировка:
условный номер предприятия-изготовителя;
год и месяц изготовления (приемки);
марка стали.
Заводом-изготовителем в случае нечеткой маркировки пружины, в соответствии с п. 4.18.2 ГОСТ 1452, маркировка наносится на бирку формы установленной указанным ГОСТ.
Маркировка и бирка должны сохраняться в течение всего срока службы пружины.
12.5. Знаки маркировки наносятся при изготовлении пружин глубиной не более 2 мм штамповкой или другим способом с учетом сохранности знаков в течение всего срока службы пружины.
Не допускается применение пружин, не имеющих маркировки.
Окрашивание тележек
18.1. Окрашивание тележек производить по поверхностям, очищенным от отслоившейся ржавчины, разрушившейся старой краски, шлаков, окалины, жировых и других видов загрязнения.
18.2. Лакокрасочные материалы, применяемые для окраски тележек (эмали, краски) должны соответствовать стандартам и техническим условиям.
18.3. Поверхности деталей тележки, подготавливаемые к окраске должны быть сухими.
18.4. При капитальном ремонте тележки окрашиваются полностью, а при деповском - только в местах с поврежденной окраской.
18.5. Грунтовками для тележек могут быть:
эмали ПФ-115, ПФ-133;
масляные краски ГС-1, ГС-2 ГОСТ 6586.
Эти же материалы и их заменители применимы и для окраски тележек.
18.6. Колесные пары и корпуса букс окрашивать в соответствии с требованиями "Руководящего документа по ремонту и техническому обслуживанию колесных пар с буксовыми узлами грузовых вагонов магистральных железных дорог колеи 1520 (1524) мм" РД ВНИИЖТ 27.05.01-2017.
На ободах колес колесных пар наличие краски не допускается.
18.7. Надписи на деталях тележки наносить масляными красками только при помощи трафаретов с закраской мест разрыва букв и цифр. Все надписи на тележках наносятся краской белого цвета - на верхних поверхностях боковых рам по центру и на верхней поверхности с обоих концов надрессорной балки после деповского ремонта первая и три последних цифры номера вагона, а после капитального ремонта и строительства - год проведения капитального ремонта и строительства, номер вагоноремонтного предприятия или завода-изготовителя, первая и три последних цифры номера вагона, как показано на рисунках 22, 23, 24 и 25.
18.8. На тележках, признанных годными после ремонта с установкой износостойких элементов ставятся буквы "РМ", высотой 70 мм, которые наносятся белой краской в прямоугольник (100 х 100 мм) на верхнем поясе консольной части надрессорной балки и боковых рам тележки рядом с клеймами о производстве плановых видов ремонта, как показано на рисунках 24 и 25.
93 - год проведения капитального ремонта или год постройки вагона;
12 - номер вагоноремонтного предприятия или завода-изготовителя вагона;
6 - первая цифра номера вагона;
546 - три последние цифры номера вагона.
Рисунок 22 - Трафарет, наносимый при капитальном ремонте вагона
4 - первая цифра номера вагона;
563 - три последние цифры номера вагона.
Рисунок 23 - Трафарет, наносимый при деповском ремонте вагона
Рисунок 24 - Места нанесения трафаретов масляной краской на
надрессорной балке тележки при плановых видах ремонта
Рисунок 25 - Места нанесения трафаретов масляной краской на боковой раме тележки при плановых видах ремонта
19. Контроль тележек при выпуске из плановых видов ремонта
19.1. Контроль отремонтированных тележек модели 18-578 и 18-9771 надо производить по окончании планового вида ремонта и после подкатки под вагон с обязательной записью в "Журнале приемки отремонтированных тележек грузовых вагонов формы ВУ-32"
19.2. При выпуске всех грузовых вагонов из плановых видов ремонта отремонтированные тележки должны быть укомплектованы надрессорными балками и боковыми рамами, обеспечивающими эксплуатацию вагона до следующего планового ремонта или его исключения из инвентаря по сроку службы.
19.3. После сборки и подкатки под вагон тележки модели 18-578 и 18-9771 завышение хотя бы одного фрикционного клина относительно нижней опорной поверхности надрессорной балки не допускается, а занижение не более 12 мм при деповском ремонте. При капитальном ремонте фрикционные клинья одного рессорного подвешивания должны быть занижены относительно нижней опорной поверхности надрессорной балки на 4 - 12 мм. Размер определяется как средняя величина измерений уровней правого и левого клиньев рессорного комплекта относительно опорной плоскости надрессорной балки.
Полное прилегание краев ребер карманов надрессорной балки к упорным поверхностям клиньев допускается только к одному из двух смежных клиньев с каждой стороны тележки.
19.4. Тележка должна быть укомплектована боковыми рамами, с разницей баз не более 2 мм, которая определяется инструментально при сборке и фиксируется в журнале лицами, проводившими сборку.
19.5. Выходному контролю подвергаются все тележки.
19.5.1. При этом проверяют:
прилегание неподвижной фрикционной планки к привалочной поверхности боковой рамы. Местные зазоры допускаются не более 1 мм;
прилегание планки подвижной к неподвижной. Местные зазоры допускаются не более 1 мм;
прилегание скобы сменной на опорную поверхность буксы. Местные зазоры допускаются не более 1 мм;
суммарный зазор между направляющими боковой рамы тележки и корпусом одной буксы:
при деповском ремонте - вдоль тележки от 5 до 14 мм, а поперек от 5 до 13 мм;
при капитальном ремонте - вдоль тележки от 5 до 12 мм, а поперек от 5 до 11 мм.
19.6. При капитальном ремонте на тележки (в соответствии с моделью тележки) устанавливаются новые:
составные фрикционные планки (подвижные и неподвижные);
фрикционные клинья;
износостойкие скобы;
чаши или прокладки.
19.7. При деповском ремонте тележек допускается (кроме тележек, подкатываемых под цистерны):
установка неподвижной фрикционной планки с максимальным износом 1,5 мм поверхности, взаимодействующей с подвижной планкой;
установка подвижной фрикционной планки с максимальным суммарным износом по толщине (с двух сторон) до 2 мм, но не более 1,5 мм с одной стороны;
установка чугунного клина с суммарным износом (наклонная и вертикальная плоскости) до 3 мм, но не более 2 мм одной из сторон;
установка износостойкой скобы на опорную поверхность буксового проема боковой рамы с максимальным неравномерным износом относительно неизношенной ее части до 1,5 мм;
установка колпака скользуна упорного ВМ 003.000 с износом опорной поверхности не более 2 мм.
19.8. Перед подкаткой тележек под вагон производится обязательная регулировка скользунов тележки в свободном состоянии.
Измерение высот между опорной пластиной на кузове и монтажной площадкой корпуса скользуна на надрессорной балки тележки проводить при порожнем кузове вагона с демонтированными крышками скользунов и упругими элементами.
После подкатки тележек под вагон установочную высоту, указанную в таблице 10.1, регулировать методом подбора толщины регулировочной пластины и установки ее между опорой кузова вагона и опорной пластиной, как показано на рисунке 16. По завершению подбора пластин:
поднять домкратами кузов вагона и установить в корпуса скользунов тележки упругие элементы и колпаки;
опустить кузов вагона на укомплектованные скользунами тележки.
После того, как кузов будет опущен, упругому элементу потребуется некоторое время, чтобы сжаться и дать установочной высоте стабилизироваться.
Регулировка производится на прямом участке пути (превышение одного рельса над другим не более 2 мм, отклонение любого рельса от прямолинейности не более 4 мм, ширина колеи 1520+/-2 мм).
После регулировки скользунов фиксируется установочная высота скользунов, эта информация заносится в журнал ВУ-32 в графу "зазоры скользунов".
19.9. Детали тормозной рычажной передачи тележки должны соответствовать требованиям "Общего руководства по ремонту тормозного оборудования вагонов" 732-ЦВ-ЦЛ.
19.10. При оснащении вагоноремонтных предприятий автоматизированными стендами приемка тележек грузовых вагонов при плановых видах ремонта производится исходя из технических возможностей стендов с обязательной регистрацией параметров (размеров) в специальных журналах.
АКТ
КАРТЫ
Дефектации и ремонта
| Листов 4 | Лист 1 | |||||||||||||||||||
Рама боковая | Тележка тип 2 по ГОСТ 9246 | ||||||||||||||||||||
Наименование изделия | |||||||||||||||||||||
Составная часть узла вагона | Обозначение изделия | ||||||||||||||||||||
1 - внутренний угол буксового проема; 2 - направляющая плоскость для букс внутренней челюсти буксового проема; 3 - вертикальная стенка наклонного пояса; 4 - наклонный пояс; 5 - стойка рессорного проема; 6 - нижний угол рессорного проема; 7 - ребро усиления рессорного проема; 8 - направляющий буртик для фрикционного клина; 9 - нижний пояс; 10 - поддомкратная подушка; 11 - направляющая плоскость для букс наружной челюсти буксового проема; 12 - наружный угол буксового проема; 13 - опорная поверхность буксового проема; 14 - вертикальная стенка над буксовым проемом; 15 - кромка технологического отверстия над буксовым проемом; 16 - кромка технологического окна; 17 - привалочные поверхности для крепления фрикционных планок; 18 - верхний пояс; 19 - верхний угол рессорного проема; 20 - прилив для валика подвески тормозного башмака; 21 - кронштейн подвески тормозного башмака триангеля, 22 - отверстие в приливе для валика подвески тормозного башмака
| |||||||||||||||||||||
| Лист 2 | ||||||||||||||||||||
Обозначение | Возможный дефект | Метод установления дефекта | Средство измерения | Заключение и рекомендуемые методы ремонта | Требования после ремонта | ||||||||||||||||
Внутренний и наружный угол буксового проема поз. 1 и 12 (наружная поверхность) | трещина | визуальный осмотр, измерение, мпк | линейка металлическая, дефектоскоп | брак | ремонту не подлежит | ||||||||||||||||
зарубы от износостойкой пластины | визуальный осмотр, измерение | штангенциркуль | глубина более 1 мм | брак | ремонту не подлежит | ||||||||||||||||
следы режущего инструмента | визуальный осмотр | - | независимо от размеров | брак | ремонту не подлежит | ||||||||||||||||
следы сварочно-наплавочных работ | визуальный осмотр | - | независимо от размеров | брак | ремонту не подлежит | ||||||||||||||||
Опорная поверхность поз. 13 | трещина | визуальный осмотр, измерение | линейка металлическая | брак | ремонту не подлежит | ||||||||||||||||
канавкообразный износ | измерение | линейка металлическая, штангенциркуль, параллель | ширина 20 мм и менее, глубина 2 мм и менее | ремонт механической обработкой на станке | визуальный осмотр, измерение | ||||||||||||||||
глубина более 2 мм | брак | ремонту не подлежит | |||||||||||||||||||
ширина более 20 мм | брак | ремонту не подлежит | |||||||||||||||||||
несоответствие остаточной высоты | измерение | штангенциркуль | высота менее 0,5 мм | брак | ремонту не подлежит | ||||||||||||||||
высота более 11,0 мм для тележек модели 18-578 | ремонт механической обработкой на станке | визуальный осмотр, измерение | |||||||||||||||||||
высота более 6 мм для тележек модели 18-9771 | |||||||||||||||||||||
| Лист 3 | ||||||||||||||||||||
Обозначение | Возможный дефект | Метод установления дефекта | Средство измерения | Заключение и рекомендуемые методы ремонта | Требования после ремонта | ||||||||||||||||
следы сварочно-наплавочных работ | визуальный осмотр | - | независимо от размеров | брак | ремонту не подлежит | ||||||||||||||||
Направляющие плоскости для букс (упорные поверхности) поз. 2 и 11 | несоответствие ширины направляющих для букс (буксовых челюстей) | измерение | штангенциркуль, шаблон | по ширине направляющих менее 155 мм при ДР и менее 159 мм при КР | ремонт наплавкой с мех обработкой | визуальный осмотр, измерение | |||||||||||||||
при ширине направляющих 155 - 161 мм при ДР и 159 - 161 мм при КР | не бракуется | визуальный осмотр, измерение | |||||||||||||||||||
несоответствие ширины буксового проема | измерение | шаблон | ширина буксового проема более 340 мм при ДР и более 336 мм при КР | ремонт наплавкой | визуальный осмотр, измерение | ||||||||||||||||
ширина буксового проема 344 мм и более | брак | ремонту не подлежит | |||||||||||||||||||
Вертикальная стенка над буксовым проемом поз. 14 | трещина | визуальный осмотр, измерение | линейка металлическая | брак | ремонту не подлежит | ||||||||||||||||
Кромка технологического отверстия над буксовым проемом поз. 15 | трещина | визуальный осмотр, измерение | линейка металлическая | брак | ремонту не подлежит | ||||||||||||||||
((__lxGc__=window.__lxGc__||{'s':{},'b':0})['s']['_228268']=__lxGc__['s']['_228268']||{'b':{}})['b']['_697691']={'i':__lxGc__.b++};
![]() Индивидуальные очистные сооружения: К классу индивидуальных очистных сооружений относят сооружения, пропускная способность которых... ![]() Типы сооружений для обработки осадков: Септиками называются сооружения, в которых одновременно происходят осветление сточной жидкости... ![]() История развития хранилищ для нефти: Первые склады нефти появились в XVII веке. Они представляли собой землянные ямы-амбара глубиной 4…5 м... ![]() Состав сооружений: решетки и песколовки: Решетки – это первое устройство в схеме очистных сооружений. Они представляют... © cyberpedia.su 2017-2024 - Не является автором материалов. Исключительное право сохранено за автором текста. |