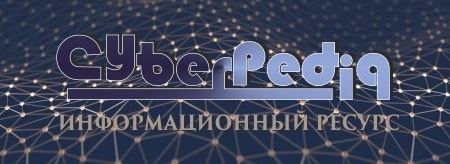
Кормораздатчик мобильный электрифицированный: схема и процесс работы устройства...
Наброски и зарисовки растений, плодов, цветов: Освоить конструктивное построение структуры дерева через зарисовки отдельных деревьев, группы деревьев...
Топ:
Выпускная квалификационная работа: Основная часть ВКР, как правило, состоит из двух-трех глав, каждая из которых, в свою очередь...
Организация стока поверхностных вод: Наибольшее количество влаги на земном шаре испаряется с поверхности морей и океанов...
Интересное:
Искусственное повышение поверхности территории: Варианты искусственного повышения поверхности территории необходимо выбирать на основе анализа следующих характеристик защищаемой территории...
Отражение на счетах бухгалтерского учета процесса приобретения: Процесс заготовления представляет систему экономических событий, включающих приобретение организацией у поставщиков сырья...
Аура как энергетическое поле: многослойную ауру человека можно представить себе подобным...
Дисциплины:
![]() |
![]() |
5.00
из
|
Заказать работу |
|
|
ВВЕДЕНИЕ
В процессе слесарной учебной практики, я узнал множество новой информации, связанной с слесарным делом. Познакомился с большим количеством оборудования, приспособлений, инструментов, а также научился применять их на практике. Узнал, какие бывают слесарные операции, как они правильно выполняются и что при их выполнении применяется (оборудование, приспособления, инструменты), а именно такие операции, как: разметка, рубка, правка и рихтовка, гибка, резка, опиливание металла, а также сверление, зенкерование, зенкование, развертывание, нарезание резьбы, клепка, шабрение и др. Познакомился с такими станками как: сверлильный, сверлильно-фрезерный, заточный. Узнал из каких основных частей они состоят, принцип их работы, а также охрану труда и технику безопасности при работе на них. На этих станках я научился выполнять такие операции как: сверление, фрезерование, зенкованиеметаллических деталей, а также заточку различного инструмента для выполнения работы. Научился работать с мерительным (ШЦ-1) и разметочным (ШЦ-2) инструментами, а так же узнал, какие существуют шкалы твердости. Еще я научился организовывать свое рабочее место (слесарный верстак), узнал, как правильно располагать инструменты и приспособления на своем рабочем месте, познакомился с режимом труда, санитарно-гигиеническими условиями труда, противопожарными мероприятиями, безопасными условиями труда. Так как моей основной темой отчета по практике является доводочные работы (полирование металла), то далее пойдет речь именно об этой теме.
ДОВОДОЧНЫЕ РАБОТЫ.
Доводка - это окончательная стадия притирки поверхностей по заданным размерам с получением точной формы обрабатываемых поверхностей. При обработке поверхностей доводкой получают размеры с точностью до 0,1 мкм и зеркальную поверхность. Эта операция является сложной и требует от работающего настойчивости и терпения.
|
Доводку выполняют на поверхностях, предварительно обработанных шлифованием. Припуск на доводку составляет 1-2 мкм.
Для предварительной и окончательной доводки применяют такие же абразивные порошки и пасты, как и для притирки. Чтобы получить зеркальную поверхность, используют тонкую пасту ГОИ, крокус, а также окись хрома или алюминиевую пудру, разведенные в бензине. Кроме того, зеркальную поверхность можно получить с помощью притира с остатками абразивного порошка от предыдущей доводки с применением смазочного материала.
Доводка и притирка состоят из аналогичных, последовательно выполняемых рабочих приемов, повторяемых до полной обработки поверхностей детали. При доводке необходимо:
- правильно распределять прилагаемое усилие, иначе могут получиться поверхности неправильной формы;
- не делать сильного нажима на деталь, выполняя движение с малой скоростью, что обеспечивает получение обрабатываемой поверхности малой шероховатости. При сильном нажиме на деталь от большого трения под действием тепла может возникнуть коробление тонких деталей и изменение размеров;
- при работе с абразивными порошками по притиру делать не более 12-15 движений, а при работе пастами - не более восьми- десяти движений, после чего притирочный материал заменять новым; в процессе доводки необходимо соблюдать последовательность применения грубых, средних и тонких порошков;
- периодически осуществлять контроль за качеством обрабатываемых поверхностей в зависимости от конфигурации изделия, проверяя:
1. прямолинейность поверхностей лекальной линейкой (Рисунок 1);
Рисунок 1 Доводка внутреннего ребра угольника
а - угольник; б - прием работы
2. параллельность плоскостей микрометром или индикатором;
|
3. величину углов угольником, угломером, шаблонами и угловыми плитками;
4. заданный профиль детали шаблоном;
5. линейные размеры штангенциркулем, микрометром и плоскопараллельными плитками;
6. перпендикулярность рабочие поверхностей лекальным угольником;
7. шероховатость зеркальной поверхности - на глаз.
ПОЛИРОВАНИЕ МЕТАЛЛА
Полирование — это слесарная операция, при которой детали обрабатывают мелкозернистыми и мягкими материалами: различными сортами пасты ГОИ, сукном, байкой, фетром. Полировать можно вручную и механическим способом.
Полируют вручную при помощи полировочных паст так же, как и шлифуют. Разница только в том, что на напильнике или деревянном бруске крепят и периодически смазывают пастой суконную или войлочную полоску.
При полировании пастами необходимо менять положение детали, повертывая ее на 90° при каждом последующем проходе и замене отработанной пасты.
Плоские детали удобнее полировать на стеклянных плитах. Стеклянную плиту, протертую керосином и вытертую насухо, покрывают тонким слоем пасты и перемещают по ней деталь вперед и назад 5 — 7 раз. Затем плиту снова протирают и покрывают пастой и продолжают полировать до тех пор, пока поверхность детали не станет гладкой и блестящей. Отполированную деталь протирают тряпкой, смоченной в керосине, и вытирают насухо чистой тряпкой.
Для механического полирования применяют полировальные станки. На шпинделе таких станков установлен полировальный круг (Рисунки 6,7)
из плотно сложенных слоев сукна, фетра, байки или войлока. Можно использовать и деревянные круги с наклеенными на них толстыми лентами из указанных материалов. Наносят пасту ГОИ на круг и сообщают ему 2000 — 2500 оборотов в минуту. Деталь периодически поворачивают разными сторонами и прижимают к кругу — полируют. Круг время от времени покрывают новым слоем пасты. Окончив полировать, деталь протирают начисто.
Рисунок. 6 Полирование на станке
Рисунок 7 Полирование на станке
ЗАКЛЮЧЕНИЕ
В ходе слесарной учебной практики, я научился выполнять множество слесарных операций, в числе которых, есть доводочные работы, о которые шла речь в данном отчете. Научился правильно использовать мерительные и разметочные инструменты, работать на слесарных станках, использовать слесарные инструмент, организовывать свое рабочее место (слесарные верстак) и правилам Охраны труда. Так же нас научили выявлять и предотвращать появление всевозможных дефектов на инструментах, приспособлениях и деталях, и научили способам их устранения.
|
ВВЕДЕНИЕ
В процессе слесарной учебной практики, я узнал множество новой информации, связанной с слесарным делом. Познакомился с большим количеством оборудования, приспособлений, инструментов, а также научился применять их на практике. Узнал, какие бывают слесарные операции, как они правильно выполняются и что при их выполнении применяется (оборудование, приспособления, инструменты), а именно такие операции, как: разметка, рубка, правка и рихтовка, гибка, резка, опиливание металла, а также сверление, зенкерование, зенкование, развертывание, нарезание резьбы, клепка, шабрение и др. Познакомился с такими станками как: сверлильный, сверлильно-фрезерный, заточный. Узнал из каких основных частей они состоят, принцип их работы, а также охрану труда и технику безопасности при работе на них. На этих станках я научился выполнять такие операции как: сверление, фрезерование, зенкованиеметаллических деталей, а также заточку различного инструмента для выполнения работы. Научился работать с мерительным (ШЦ-1) и разметочным (ШЦ-2) инструментами, а так же узнал, какие существуют шкалы твердости. Еще я научился организовывать свое рабочее место (слесарный верстак), узнал, как правильно располагать инструменты и приспособления на своем рабочем месте, познакомился с режимом труда, санитарно-гигиеническими условиями труда, противопожарными мероприятиями, безопасными условиями труда. Так как моей основной темой отчета по практике является доводочные работы (полирование металла), то далее пойдет речь именно об этой теме.
ДОВОДОЧНЫЕ РАБОТЫ.
Доводка - это окончательная стадия притирки поверхностей по заданным размерам с получением точной формы обрабатываемых поверхностей. При обработке поверхностей доводкой получают размеры с точностью до 0,1 мкм и зеркальную поверхность. Эта операция является сложной и требует от работающего настойчивости и терпения.
|
Доводку выполняют на поверхностях, предварительно обработанных шлифованием. Припуск на доводку составляет 1-2 мкм.
Для предварительной и окончательной доводки применяют такие же абразивные порошки и пасты, как и для притирки. Чтобы получить зеркальную поверхность, используют тонкую пасту ГОИ, крокус, а также окись хрома или алюминиевую пудру, разведенные в бензине. Кроме того, зеркальную поверхность можно получить с помощью притира с остатками абразивного порошка от предыдущей доводки с применением смазочного материала.
Доводка и притирка состоят из аналогичных, последовательно выполняемых рабочих приемов, повторяемых до полной обработки поверхностей детали. При доводке необходимо:
- правильно распределять прилагаемое усилие, иначе могут получиться поверхности неправильной формы;
- не делать сильного нажима на деталь, выполняя движение с малой скоростью, что обеспечивает получение обрабатываемой поверхности малой шероховатости. При сильном нажиме на деталь от большого трения под действием тепла может возникнуть коробление тонких деталей и изменение размеров;
- при работе с абразивными порошками по притиру делать не более 12-15 движений, а при работе пастами - не более восьми- десяти движений, после чего притирочный материал заменять новым; в процессе доводки необходимо соблюдать последовательность применения грубых, средних и тонких порошков;
- периодически осуществлять контроль за качеством обрабатываемых поверхностей в зависимости от конфигурации изделия, проверяя:
1. прямолинейность поверхностей лекальной линейкой (Рисунок 1);
Рисунок 1 Доводка внутреннего ребра угольника
а - угольник; б - прием работы
2. параллельность плоскостей микрометром или индикатором;
3. величину углов угольником, угломером, шаблонами и угловыми плитками;
4. заданный профиль детали шаблоном;
5. линейные размеры штангенциркулем, микрометром и плоскопараллельными плитками;
6. перпендикулярность рабочие поверхностей лекальным угольником;
7. шероховатость зеркальной поверхности - на глаз.
ИНСТРУМЕНТЫ ИСПОЛЬЗУЕМЫ ПРИ ДОВОДКЕ.
Напильники (Рисунок 2)
Рисунок 2 Работа напильником
При работе с напильниками стоит соблюдать следующие правила:
1) обрабатываемое изделие закреплять в тисках в горизонтальной плоскости так, чтобы оно выступало над уровнем губок тисков на 8-10 мм. Более высокое положение, особенно тонких деталей, вызывает неустойчивость и вибрации;
2) толстые слои металла (припуск) снимать зубилом. Это не только сэкономит время, но и сохранит напильники;
3) пользоваться одной стороной напильника, а вторую использовать лишь после затупления первой;
|
4) не касаться опиливаемой поверхности рукой, так как жир и пот от руки создают скользкую поверхность, которую трудно опиливать;
5) пользоваться напильниками только по их назначению: нельзя мягкие металлы (свинец, олово, и т. д.), а также грубые заготовки опиливать личными напильниками;
6) при опиливании небольших поверхностей в работе должна участвовать вся длина напильника.
Надфили ( Рисунок 3)
Рисунок 3 Работа надфилями
Для мелких работ применяют надфили, которые также различают по форме поперечных сечений, а также рифлевки, представляющие собой надфили изогнутой формы, которые применяют для обработки углублений, поднутренных и других труднодоступных участков деталей
Наждачная бумага(Рисунок 4,5)
Рисунок 4. Работа наждачной бумагой
Рисунок 5. Работа наждачной бумагой
ПОЛИРОВАНИЕ МЕТАЛЛА
Полирование — это слесарная операция, при которой детали обрабатывают мелкозернистыми и мягкими материалами: различными сортами пасты ГОИ, сукном, байкой, фетром. Полировать можно вручную и механическим способом.
Полируют вручную при помощи полировочных паст так же, как и шлифуют. Разница только в том, что на напильнике или деревянном бруске крепят и периодически смазывают пастой суконную или войлочную полоску.
При полировании пастами необходимо менять положение детали, повертывая ее на 90° при каждом последующем проходе и замене отработанной пасты.
Плоские детали удобнее полировать на стеклянных плитах. Стеклянную плиту, протертую керосином и вытертую насухо, покрывают тонким слоем пасты и перемещают по ней деталь вперед и назад 5 — 7 раз. Затем плиту снова протирают и покрывают пастой и продолжают полировать до тех пор, пока поверхность детали не станет гладкой и блестящей. Отполированную деталь протирают тряпкой, смоченной в керосине, и вытирают насухо чистой тряпкой.
Для механического полирования применяют полировальные станки. На шпинделе таких станков установлен полировальный круг (Рисунки 6,7)
из плотно сложенных слоев сукна, фетра, байки или войлока. Можно использовать и деревянные круги с наклеенными на них толстыми лентами из указанных материалов. Наносят пасту ГОИ на круг и сообщают ему 2000 — 2500 оборотов в минуту. Деталь периодически поворачивают разными сторонами и прижимают к кругу — полируют. Круг время от времени покрывают новым слоем пасты. Окончив полировать, деталь протирают начисто.
Рисунок. 6 Полирование на станке
Рисунок 7 Полирование на станке
|
|
Кормораздатчик мобильный электрифицированный: схема и процесс работы устройства...
Состав сооружений: решетки и песколовки: Решетки – это первое устройство в схеме очистных сооружений. Они представляют...
Поперечные профили набережных и береговой полосы: На городских территориях берегоукрепление проектируют с учетом технических и экономических требований, но особое значение придают эстетическим...
Эмиссия газов от очистных сооружений канализации: В последние годы внимание мирового сообщества сосредоточено на экологических проблемах...
© cyberpedia.su 2017-2024 - Не является автором материалов. Исключительное право сохранено за автором текста.
Если вы не хотите, чтобы данный материал был у нас на сайте, перейдите по ссылке: Нарушение авторских прав. Мы поможем в написании вашей работы!