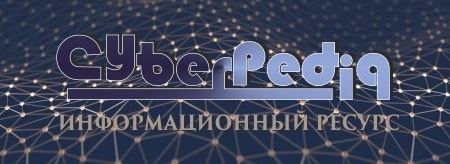
История создания датчика движения: Первый прибор для обнаружения движения был изобретен немецким физиком Генрихом Герцем...
Наброски и зарисовки растений, плодов, цветов: Освоить конструктивное построение структуры дерева через зарисовки отдельных деревьев, группы деревьев...
Топ:
Оценка эффективности инструментов коммуникационной политики: Внешние коммуникации - обмен информацией между организацией и её внешней средой...
Эволюция кровеносной системы позвоночных животных: Биологическая эволюция – необратимый процесс исторического развития живой природы...
Методика измерений сопротивления растеканию тока анодного заземления: Анодный заземлитель (анод) – проводник, погруженный в электролитическую среду (грунт, раствор электролита) и подключенный к положительному...
Интересное:
Распространение рака на другие отдаленные от желудка органы: Характерных симптомов рака желудка не существует. Выраженные симптомы появляются, когда опухоль...
Отражение на счетах бухгалтерского учета процесса приобретения: Процесс заготовления представляет систему экономических событий, включающих приобретение организацией у поставщиков сырья...
Мероприятия для защиты от морозного пучения грунтов: Инженерная защита от морозного (криогенного) пучения грунтов необходима для легких малоэтажных зданий и других сооружений...
Дисциплины:
![]() |
![]() |
5.00
из
|
Заказать работу |
|
|
Анализ чертежа детали и технологического процесса обработки
Служебное назначение детали
Деталь «Крышка» это часть гидроцилиндра. Гидроцилиндр – это самый простой образец двигателя. Выходное (подвижное) звено, которым может быть шток, плунжер или же сам корпус цилиндра, осуществляет возвратно-поступательное движение. «Крышка» монтируется в гидроцилиндр с помощью наружной резьбы М33-1,5е6, и с помощью торца упирается деталь упирается в торец гидроцилиндра, и сваривается в месте стыков. Также в деталь монтируется подшипник, после этого гидроцилиндр монтируется в узел.
Технологичность детали
Качественная оценка технологичности детали.
- Конструкция детали состоит из стандартных конструктивных элементов. В основном это цилиндрические поверхности.
- Конструкция детали обеспечивает свободный вход и выход инструмента и удобство выполнения обработки.
- Деталь изготавливается из стандартных и унифицированных заготовок. Конфигурация поверхностей не вызывает значительных трудностей при обработке и получении заготовки.
- Размеры и поверхности детали имеют оптимальные степень точности и шероховатости.
- Физико-химические и механические свойства материала, жесткость детали l/d=1,17, ее форма и размеры соответствуют требованиям технологии изготовления.
- Показатели базовых поверхностей детали обеспечивают точность установки, обработки и контроля.
- конструкция не обеспечивает возможность обработки за два установа детали
-
Изм. |
Лист |
№ докум. |
Подпись |
Дата |
Лист |
5 |
- Деталь изготавливается в основном по 12 классу точности. Для достижения этого класса точности достаточно чистового точения резцами и чистового фрезерование фрезой
|
- упрощение конструкции ПР, РИ, СИ
- нет наличие простых и удобных баз
- не возможность сквозного прохода инструмента.
Количественная оценка.
Коэффициент точности обработки [17]
, (1)
где Аср – средний квалитет обработки
, (2)
где ni – количество поверхностей с одинаковыми значениями квалитетов;
ITA – соответствующий квалитет;
n – количество всех поверхностей;
Коэффициент качества обработки
, (3)
где Бср - среднее числовое значение параметра шероховатости
, (4)
где ni - количество поверхностей с одинаковой шероховатостью;
Ra – параметр шероховатости, мкм;
n – количество всех поверхностей;
Коэффициент унификаций
, (5)
где Qэ – число конструктивных элементов
Qу.э – число унифицированных элементов
Изм. |
Лист |
№ докум. |
Подпись |
Дата |
Лист |
6 |
Произведя качественную и количественную оценки можно сделать вывод, что деталь является технологичной по основным параметрам.
Изм. |
Лист |
№ докум. |
Подпись |
Дата |
Лист |
По исходным данным заготовкой штампока наибольший диаметр которой 41, а наибольшая длинна 48.
Рассмотрим характеристики материала применяемого для изготовления детали приведены в таблице 2.3. Хим. состав в таблице 2.3.1. Механические свойства в таблице 2.3.2
Изм. |
Лист |
№ докум. |
Подпись |
Дата |
Лист |
7 |
Характеристика материала. Сталь 30ХГСА
Таблица 2.3
Марка | Сталь 30ХГСА |
Заменитель: | Сталь 40ХФА, ст.35ХМ, ст.40ХН, ст.35ХГСА ГОСТ 4543-71 |
Классификация | Сталь конструкционная легированная |
Применение | различные улучшаемые детали: валы, оси, зубчатые колеса, фланцы, корпуса обшивки, лопатки компрессорных машин, работающие при температуре до 200°С, рычаги, толкатели, ответственные сварные конструкции, работающие при знакопеременных нагрузках, крепежные детали, работающие при низких температурах |
Дополнение: | Сталь хромокремнемарганцовая |
Таблица 2.3.1
|
Химический состав в % материала 30ХГСА ГОСТ 4543 - 71
C | Si | Mn | Ni | S | P | Cr | Cu |
0.28 - 0.34 | 0.9 - 1.2 | 0.8 - 1.1 | до 0.3 | до 0.025 | до 0.025 | 0.8 - 1.1 | до 0.3 |
Среднее содержание углерода обеспечивает вязкость сердцевины, что позволяет получить высокую твердость поверхности и обеспечить достаточную прочность всей детали.
Добавки марганца повышают твердость и износостойкость стали.
Кремний увеличивает прочность, при сохранении вязкости, а также повышает упругость материала.
Добавки хрома при незначительном снижении пластичности, повышают прочность и коррозионную стойкость стали.
Изм. |
Лист |
№ докум. |
Подпись |
Дата |
Лист |
8 |
Расчёт элементов привода
Расчёт зубчатой передачи
Проектный расчёт цилиндрической зубчатой передачи на выносливость зубьев при изгибе:
Рассчитаем самую нагруженную зубчатую передачу с передаточным отношением i=0,25. Данная передача является прямозубой и состоит из шестерни 1 с числом зубьев z1 и колеса 2 с числом зубьев z2.
Соответственно при расчете параметрам шестерни приписываем индекс - 1, а параметрам колеса -2.
Материал колеса и шестерни: Сталь 25ХГМ, термообработка колеса и шестерни – нитроцементация с закалкой; твёрдость поверхности зубьев -
HRCЭ 58…60, твёрдость сердцевины зубьев - HRCЭ 32…45.
Модуль передачи должен удовлетворять условию [2]:
Изм. |
Лист |
№ докум. |
Подпись |
Дата |
Лист |
21 |
где km - вспомогательный коэффициент; для прямозубых передач km=13;
M1F - исходный расчетный крутящий момент на шестерне, M1F=560 Н·м;
KF - коэффициент нагрузки для шестерни; KF=1,4;
z1 - число зубьев шестерни; z1=18;
YF1- коэффициент, учитывающий форму зуба; YF1=4,1;
ψbm- отношение ширины колеса b к модулю m;
Рекомендуется ширину венца принимать равной 6-10 модулям: ψbm=8.
Допустимое напряжение при изгибе:
|
σFP=0,4·σFlimb·kFL, (4.2)
где σFlimb =1000 - предел выносливости материала зубьев, МПа.
kFL -коэффициент режима нагружения и долговечности.
, (4.3)
где mF - показатель кривой усталости;
NF0 - базовое число циклов перемены напряжений при изгибе;
NFE - эквивалентное число циклов перемены напряжений.
Для зубчатых колёс, подвергаемых нитроцементации, принимают mF=9 и NF0=107.
NFE=60×n×t×µН=60×1000×104Ħ0,125=7,5×107, (4.4)
где n - частота вращения, мин-1;
t =104 - расчетный срок службы передачи, ч;
µН=0,125 - для лёгкого режима нагружения.
Так как NFE> NF0, то принимаем kFL=1.
σFP=0,4·1000·1=400 МПа,
Изм. |
Лист |
№ докум. |
Подпись |
Дата |
Лист |
22 |
Принимаем m=5 мм.
Определим основные геометрические параметры передачи:
Делительные диаметры найдём по формуле:
di = mzi, (4.5)
d1 =5*18=90 мм;
d2 =5*72=360 мм.
Межосевое расстояние передачи аW:
аW= (4.6)
Диаметры вершин и диаметры впадин зубьев:
dai=di+2×m, (4.7)
dfi=di-2,5×m, (4.8)
Подставив значения в формулы 4.7 и 4.8, получим:
Диаметры вершин зубьев:
da1=90+2×5=100 мм;
da2=360+2×5=370 мм;
Диаметры впадин зубьев:
df1=90-2,5×5=57,5 мм;
df2=360-2,5×5=347,5 мм;
Ширина венца:
bi= m ·ψbm; (4.9)
Рекомендуется ширину венца принимать равной 6-10 модулям (меньше для подвижных колёс).
Принимаем
b1= 5 *8=40 мм
b2= 5*10=50 мм.
Проектный расчёт передачи на контактную выносливость
Изм. |
Лист |
№ докум. |
Подпись |
Дата |
Лист |
23 |
Начальный диаметр шестерни должен удовлетворять условию [2]:
|
(4.10)
где kd - вспомогательный коэффициент, kd=770 для прямозубых передач;
kH - коэффициент нагрузки; kH=1,4;
u - передаточное число (u ≥ 1);
ψbd - отношение рабочей ширины венца передачи к начальному диаметру шестерни, ψbd=0,38;
Допускаемое контактное напряжение для прямозубых передач:
, (4.11)
где σHlimb - базовый предел контактной выносливости поверхностей зубьев,
σHlimb=1350 МПа;
SH-коэффициент безопасности, SH=1,2;
МПа;
мм;
Условие выполняется, так как dw1=104>90 мм.
Проверочный расчет на выносливость зубьев при изгибе:
Удельная расчетная окружная сила (Н) [2]:
(4.12) где Ft - расчётная окружная сила, Н;
b - ширина венца по основанию зуба, мм;
kFV - коэффициент, учитывающий динамическую нагрузку в зацеплении, которая возникает вследствие колебаний масс колёс и ударов в зацеплении;
kFb - коэффициент, учитывающий неравномерность распределения нагрузки по ширине венца, которая возникает вследствие погрешностей изготовления колёс, упругих деформаций валов, зазорах в подшипниках;
kFa - коэффициент, учитывающий при расчёте прямозубых передач распределение нагрузки между зубьями.
Коэффициенты: kFV=1; kFb=1,25; kFa=1.
Изм. |
Лист |
№ докум. |
Подпись |
Дата |
Лист |
24 |
, (4.13)
где YF - коэффициент формы зуба, YF=4,1;
Ye - коэффициент, учитывающий перекрытие зубьев: Ye=1;
Yb - коэффициент, учитывающий наклон зуба, Yb=1.
Подставив значения в формулу 4.13, получим:
Допускаемое напряжение при расчёте зубьев на выносливость при изгибе:
, (4.14)
где sFlimb - длительный предел выносливости зубьев при изгибе;
kFg - коэффициент, учитывающий влияние шлифования переходной
поверхности зубьев, kFg=0,7;
kFa - коэффициент, учитывающий влияние упрочнения переходной
поверхности зубьев в результате механической обработки kFa=1,3;
kFc - коэффициент, учитывающий особенности работы зубьев при
передаче реверсивной нагрузки, kFc=1,0;
kxF - коэффициент, учитывающий размеры зубчатого колеса, kxF=1,0;
kFL - коэффициент режима нагружения и долговечности, kFL=1,0;
YS - коэффициент, отражающий чувствительность материала к
концентрации напряжений;
YR - коэффициент, учитывающий параметры шероховатости
переходной поверхности зуба, YR=1,2;
SF - коэффициент безопасности;
Коэффициент YS находим по формуле
YS=1,1×m-0,09=1,1×5-0,09=0,95; (4.15)
Коэффициент безопасности находим по формуле:
, (4.16)
|
где S’F - коэффициент безопасности, учитывающий нестабильность
свойств материала зубчатого колеса и ответственность зубчатой
передачи, S’F =1,55;
S’’F - коэффициент, учитывающий способ получения заготовки, S’’F=1.
Подставив значения в формулу 4.16, получим:
.
Подставив значения в формулу 4.14, получим:
МПа.
Изм. |
Лист |
№ докум. |
Подпись |
Дата |
Лист |
25 |
Расчёт передачи на контактную выносливость зубьев:
Удельную окружную силу находим по формуле [2]:
(4.17)
где Ft - расчётная окружная сила, Н;
b - ширина венца по основанию зуба, мм;
kНV - коэффициент, учитывающий динамическую нагрузку в зацеплении,
kНV=1;
kНb - коэффициент, учитывающий неравномерность распределения
нагрузки по ширине венца, kНb=1,25;
kНa - коэффициент, учитывающий распределение нагрузки между
зубьями.
KHa=1+0,0025(0,17N)4v+0,02(N-6)1,35, (4.18)
где N=7 – степень точности зубчатой передачи;
v – окружная скорость в зацеплении, м/с
м/с;
KHa=1+0,0025(0,17Ħ7)4Ħ4,71+0,02(7-6)1,35=1,04.
Подставив значения в формулу 4.1.16, получим:
Н.
Расчётное контактное напряжение находим по формуле:
, (4.19)
где zH - коэффициент, учитывающий форму сопряжённых поверхностей
зубьев в полюсе зацепления, zH=1,76;
zM - коэффициент, учитывающий механические свойства материала
сопряжённых зубчатых колёс, для колёс из стали zM=274;
Изм. |
Лист |
№ докум. |
Подпись |
Дата |
Лист |
26 |
Коэффициент ze определяем в зависимости от коэффициентов торцевого и осевого
перекрытия.
, (4.20)
Так как передача прямозубая, то =0.
Принимаем ze=0,88.
Подставив значения в формулу 4.19, получим:
МПа;
Допускаемое контактное напряжение для прямозубых передач:
, (4.21)
где zR - коэффициент, учитывающий параметр шероховатости
поверхностей зубьев, zR=1;
zv - коэффициент, учитывающий окружную скорость v, zv=1;
kL - коэффициент, учитывающий влияние смазочного материала, kL=1;
kxH - коэффициент, учитывающий размеры зубчатого колеса, kxH=1;
kHL - коэффициент режима нагружения и долговечности;
SH - коэффициент безопасности;
sHlimb- предел выносливости зубьев на контактную выносливость;
Коэффициент режима нагружения и долговечности kHL определяется по формуле:
, (4.22)
где mH - показатель кривой усталости;
NH0 - базовое число циклов перемены напряжений при изгибе NF0=120*106;
NHE - эквивалентное число циклов перемены напряжений.
NHE=60×n×t=60×1000×104×0,125=75×106, (4.23)
где n - частота вращения, мин-1;
t =104 - расчетный срок службы передачи, ч.
µН=0,125 - для лёгкого режима нагружения.
Так как NHE< NH0, то принимаем по графику kHL=1,2.
Так как NHE< NH0, то принимаем по графику kHL=1,2.
Подставив значения в формулу 4.21, получим:
МПа.
В нашем случае sHP=1350 МПа >sH=754 МПа, что удовлетворяет условию.
Для остальных передач:
Передача i2
диаметры делительные: d1=m·Z1=2·35=70 мм;
d2=m·Z2=2·55=110 мм;
da1=d1+2m=70+2·2=74 мм;
da2=d2+2m=110+2·2=114 мм;
df1=d1-2m(ha+с)=70-2·2· (1+0,25)=65 мм;
df2=d2-2m(ha+с)=110-2·2· (1+0,25)=105 мм;
Ширина венца колеса:
b2=ψba*aW=0,25·90=12,5 мм, принимаем 22 мм
Ширина венца шестерни:
b1=b2+(5…10)=22+8=30 мм;
;
0.25+2*2=64) колеса
Передача i4:
диаметры делительные: d1=m·Z1=2·45=90 мм;
d2=m·Z2=2·45=90 мм;
Изм. |
Лист |
№ докум. |
Подпись |
Дата |
Лист |
27 |
da2=d2+2m=90+2·2=94 мм;
df1=d1-2m(ha+с)=90-2·2· (1+0,25)=85 мм;
df2=d2-2m(ha+с)=90-2·2· (1+0,25)=85 мм;
Ширина венца колеса:
b2=ψba·aW=0,25·90=22,5 мм, принимаем 22 мм
Ширина венца шестерни:
b1=b2+(5…10)=22+8=30 мм;
Передача i3, (i5)
диаметры делительные: d1=m·Z1=2·40=80 мм;
d2=m·Z2=2·50=100 мм;
da1=d1+2m=80+2·2=84 мм;
da2=d2+2m=10+2·2=104 мм;
df1=d1-2m(ha+с)=80-2·2· (1+0,25)=75 мм;
df2=d2-2m(ha+с)=100-2·2·(1+0,25)=95 мм;
Ширина венца колеса:
b2=ψba*aW=0,25·90=22,5 мм, принимаем 22 мм
Ширина венца шестерни:
b1=b2+(5…10)=22+8=30 мм;
Передача i8
диаметры делительные: d1=m·Z1=5·55=275 мм;
d2=m·Z2=5·35=175 мм;
da1=d1+2m=275+2·5=285 мм;
da2=d2+2m=175+2·5=185 мм;
df1=d1-2m(ha+с)=275-2·5· (1+0,25)=262,5 мм;
df2=d2-2m(ha+с)=175-2·5· (1+0,25)=162,5 мм;
Ширина венца колеса:
b2=ψba*aW=0,25·225=56,25 мм, принимаем 58 мм
Ширина венца шестерни:
b1=b2+(5…10)=58+8=64 мм;
;
0.25+2*2=64) колеса
Изм. |
Лист |
№ докум. |
Подпись |
Дата |
Лист |
28 |
В зависимости от сечения ремня могут применяться следующие ременные передачи: плоскоременная, клиноременная, поликлиновая.
а) б) в)
Рисунок 4.1 – Виды ременной передачи: а – плоскоременная,
б – клиноременная, в – поликлиновая
При применении поликлиновой ременной передачи уменьшается консольная нагрузка на вал, смягчаются динамические нагрузки и снижаются габариты передачи по сравнению с клиноременной передачей, поэтому принимаем поликлиновую передачу.
Задаемся расчетным диаметром ведущего и ведомого шкивов d1=112 мм, d2=140 мм, так как передаточное отношение и=0,8 в соответствии с требованиями ГОСТ 20889.
Сечение ремня выбираем в зависимости от мощности, передаваемой ведущим шкивом, и его частоты вращения:
кВт, (4.24)
где Рном=7,5 кВт – номинальная мощность потребляемая приводом;
Ср=1,0 – коэффициент динамичности нагрузки и режима работы.
Принимаем сечение B.
Определяем линейную скорость ремня:
м/с (4.25)
Определяем рекомендуемое межцентровое расстояние для обыкновенной открытой передачи по формуле:
0,7(d1+d2) < а < 2(d1+d2) (4.26)
0,7(112+140) < а < 2(112+140)
Принимаем межцентровое расстояние а=300 мм
Расчетная длина ремня:
(4.27)
Значение округляем до ближайшего большего стандартного по ГОСТ1284.1 l=1000 мм.
Определим угол обхвата:
Число клиньев поликлинового ремня:
Изм. |
Лист |
№ докум. |
Подпись |
Дата |
Лист |
29 |
где [PП] - допускаемая мощность передаваемая ремнями, кВт
[PП]=[P0]×Сa×Сl×СK =7,5×1,0×0,82×0,85=5,2 кВт, (4.29)
где [P0]=7,5 - допускаемая приведенная мощность, передаваемая
поликлиновым ремнем;
СP=1,0 - коэффициент динамичности нагрузки и длительности работы;
Сa=1,0 - коэффициент угла обхвата;
Сl=0,82 - коэффициент, зависящий от длины ремня
СK=0,85 - коэффициент, учитывающий число ремней в комплекте
,
принимаем K=2
Сила предварительного натяжения поликлинового ремня:
, (4.30)
H
Сила давления на вал:
Н
где a1=180о - угол обхвата ремнем ведущего шкива.
Расчёт вал ов
Изм. |
Лист |
№ докум. |
Подпись |
Дата |
Лист |
30 |
(4.31)
где Т-момент на соответствующем валу;
[tк]-допускаемое напряжение на кручение, [tк]=20...25;
мм
Диаметр выходного конца электродвигателя d=38 мм.
Конструктивно принимаем d=38 мм.
мм
Под посадку подшипников, обеспечивающих необходимую надёжность при работе ведомого вала, конструктивно принимаем d2=d3=35 мм.
Принимаем конструктивно d3=35 мм
Принимаем конструктивно d5=55 мм
Прочностной расчёт вала
Наиболее опасным сечением вала V является шлицевой участок, на валу присутствует наибольший изгибающий момент. Концентраторами напряжений являются шлицы.
Рисунок 4.1 Схема приложения нагрузки.
Определим окружную силу в зацеплении [4]:
Н,
где d1=m×z1=5×18=90 мм – делительный диаметр колеса;
Т2=560 Н×м – крутящий момент на колесе.
Радиальная сила:
Изм. |
Лист |
№ докум. |
Подпись |
Дата |
Лист |
31 |
где a=0° - угол зацепления.
По чертежу определяем места расположения сил и расстояние до точек их приложения, переносим их на рисунок.
l1=160 мм; l2=64 мм; l3=86 мм;
SМА=Ft1×l1-RB×(l1+l2)+FШК(l1+l2+l3)=0,
SМB=-RA(l1+l2)-Ft×l2+FШКl3=0,
Откуда:
H
H
Проверка:
SFz=-Fшк+RB-Ft-RA=-2072+3441,4-803,5-565,9=0
Строим эпюры изгибающих и крутящих моментов (рисунок 4.2)
Рисунок 4.2 Эпюры изгибающего и крутящего моментов.
Изм. |
Лист |
№ докум. |
Подпись |
Дата |
Лист |
32 |
Для опасного сечения определяем коэффициент запаса прочности по усталости S и сравниваем его с допускаемым значением [4]:
(4.32)
где Sσ и St - коэффициенты запаса по нормальным и касательным
напряжениям, определяемые по зависимостям [4]:
, (4.33)
где σ-1 =410 МПа и t-1=240 МПа – пределы выносливости материала
соответственно при изгибе и кручении;
σa и ta – амплитуды напряжений цикла, МПа;
σт и tт – средние напряжения цикла, МПа;
yσ=0,2; yt=0,1 – коэффициенты характеризующие чувствительность
материала к асимметрии цикла напряжений;
КσD и КtD – коэффициенты, учитывающие влияние всех факторов на
сопротивление усталости соответственно при изгибе и кручении
, (4.34)
где Кσ и Кt - эффективные коэффициенты концентрации напряжений;
Кd – коэффициент влияния абсолютных размеров поперечного
сечения;
КF=1 – коэффициент влияния шероховатости поверхности;
КV=2,8 – коэффициент влияния упрочнения
Для концентратора напряжений определим коэффициенты К:
- шлицевый участок вала
Кσ=1,7;
Кt=2,65;
Кd=0,81
Изм. |
Лист |
№ докум. |
Подпись |
Дата |
Лист |
33 |
где М=178,8 Н×мм – результирующий изгибающий момент;
МК=54,2 Н×мм – крутящий момент;
W – осевой момент сопротивления сечения вала, мм3;
WК – полярный момент сопротивление сечения вала, мм3
мм3,
мм3
МПа;
МПа
Запас прочности больше допустимого. Условие прочности выполняется
Расчёт подшипниковых узлов
Для рассчитываемого вала мы приняли шариковый радиально-упорный подшипник серии 36211 ГОСТ 831-75 (D=55 мм, B=21 мм, Сr=58,4 кН).
Пригодность подшипников определяется сопоставлением расчётной динамической грузоподъёмности с базовой, или базовой долговечности с требуемой по условиям:
Crp ≤ Cr или L10h ≥ Lh. (4.35)
Требуемая долговечность подшипника Lh = 8,4· 103 по табл. 9.4 [2].
Расчётная динамическая грузоподъёмность определяется по формуле:
Изм. |
Лист |
№ докум. |
Подпись |
Дата |
Лист |
34 |
где: RE – эквивалентная динамическая нагрузка, Н;
ω - угловая скорость вала, с-1;
m – показатель степени, m = 3.
RE = V· Rr ·Kб ·Kт (4.37)
где: V – коэффициент вращения, V = 1 (при вращении внутреннего кольца
подшипника);
Rr – суммарная реакция подшипника, Rr=3487 Н;
Kб – коэффициент безопасности, =1,15;
Kт – температурный коэффициент, = 1.
RE = 1· 3487 ·1,15 ·1 = 4010 Н
кН
32 кН > 22,0 – условие Crp ≤ Cr выполняется.
Произведём расчёт подшипника на долговечность:
(4.38)
Расчёт подшипника на долговечность выполняется.
Смазка шпиндельной бабки.
Смазка шестерен шпиндельной бабки производится разбрызгиванием из масляной ванны. Смазка опор шпинделя производится маслом, поступающим из резервуара, расположенного в верхней части корпуса, по трубкам, самотеком.
Подача масла в резервуар производится шестеренчатым насосом, смонтированным на передней стенке корпуса, на одной оси с выходным валиком цепи подач.
Заливка масла в корпус шпиндельной бабки производится через отверстие в крышке, закрытое пробкой; спуск отработанного масла – через пробку 9. Контроль уровня масла в шпиндельной бабке осуществляется по маслоуказателю 3.
Маслоуказатель 2 контролирует работу насоса.
Смазка коробки подач.
Смазка механизма коробки подач осуществляется из резервуара, расположенного в верхней части корпуса, прикрытого крышкой. Для заливки масло необходимо снять крышку 26, залить в резервуар масло по маслоуказателю 10 и поставить крышку на место.
Подача масла в резервуар производится шестеренчатым насосом, расположенным на правой стенке коробки подач.
Смазка фартука.
Смазка червячной передачи осуществляется при помощи масляной ванны. Заливка масла в корпус фартука производится через пробку 21, расположенную на каретке станка, слив отработанного масла – через пробку 7. Контроль уровня масла осуществляется по маслоуказателю 8. Смазка паразитной шестерни, передающей движение на винт поперечной подачи суппорта, осуществляется шприц-масленкой 4. Смазка мелкозубчатых муфт продольной и поперечной подачи, а также опоры реечной шестерни осуществляется маслом из резервуара, расположенного в верхней части фартука, через подводящие трубки.
Смазка суппорта и задней бабки производится вручную. Места смазок указаны на схеме смазки.
В качестве смазочного материала для смазки станка должно применяться масло индустриальное И-20А ГОСТ 20799-75.
Таблица 7.1 – Карта смазки
№ пп | Узел | Место смазки | № по схеме | Род смазки | Срок смазки |
1 | 2 | 3 | 4 | 5 | 6 |
1 | Коробка скорос |
|
|
Автоматическое растормаживание колес: Тормозные устройства колес предназначены для уменьшения длины пробега и улучшения маневрирования ВС при...
Археология об основании Рима: Новые раскопки проясняют и такой острый дискуссионный вопрос, как дата самого возникновения Рима...
Биохимия спиртового брожения: Основу технологии получения пива составляет спиртовое брожение, - при котором сахар превращается...
Поперечные профили набережных и береговой полосы: На городских территориях берегоукрепление проектируют с учетом технических и экономических требований, но особое значение придают эстетическим...
© cyberpedia.su 2017-2024 - Не является автором материалов. Исключительное право сохранено за автором текста.
Если вы не хотите, чтобы данный материал был у нас на сайте, перейдите по ссылке: Нарушение авторских прав. Мы поможем в написании вашей работы!