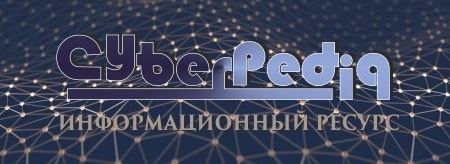
Кормораздатчик мобильный электрифицированный: схема и процесс работы устройства...
Общие условия выбора системы дренажа: Система дренажа выбирается в зависимости от характера защищаемого...
Топ:
Характеристика АТП и сварочно-жестяницкого участка: Транспорт в настоящее время является одной из важнейших отраслей народного хозяйства...
Марксистская теория происхождения государства: По мнению Маркса и Энгельса, в основе развития общества, происходящих в нем изменений лежит...
Теоретическая значимость работы: Описание теоретической значимости (ценности) результатов исследования должно присутствовать во введении...
Интересное:
Финансовый рынок и его значение в управлении денежными потоками на современном этапе: любому предприятию для расширения производства и увеличения прибыли нужны...
Подходы к решению темы фильма: Существует три основных типа исторического фильма, имеющих между собой много общего...
Инженерная защита территорий, зданий и сооружений от опасных геологических процессов: Изучение оползневых явлений, оценка устойчивости склонов и проектирование противооползневых сооружений — актуальнейшие задачи, стоящие перед отечественными...
Дисциплины:
![]() |
![]() |
5.00
из
|
Заказать работу |
|
|
Предварительный расчет валов, подбор муфты
Расчет выполняем на кручение по пониженным допускаемым напряжениям, с учетом действия на вал изгибающего момента.
Ведущий вал:
Диаметр выходного конца при допускаемом напряжении [τк]=20 МПа вычисляется мо формуле:
, (33)
где Mк1– крутящий момент на ведущем валу, Mк1=50,39 Н·м, (ПЗ, табл. 1);
[τк]– допускаемое напряжение на кручение, [τк]=20 МПа, [1, с. 160].
d в1 = =23,7 мм.
Принимаем dв1=32 мм из стандартного ряда [1, с.162].
Так как вал редуктора соединен муфтой с валом электродвигателя, то необходимо согласовать диаметры вала двигателя dдв и вала dв1. У подобранного электродвигателя диаметр вала dдв=38 мм, [1,с391. табл.П2]. Выбираем муфту упругую втулочно-пальцевую МУВП по ГОСТ 21424-75, с допускаемым моментом [T]=125Н·М, d=28 мм, длина полумуфты на вал редуктора
ℓм =60мм,[1,с.277] расточкой полумуфты под вал двигателя dдв=38 мм и
dв1=32 мм, [1, с277].
Принимаем диаметр вала под подшипники dп1=40 мм, диаметр буртика dб1=45 мм. Шестерню выполняем за одно целое с валом.
Рисунок 2 - Конструкция ведущего вала
Ведомый вал:
Принимаем материал вала сталь 45, термическая обработка улучшение, твердость HB 16…170
Учитывая влияние изгиба вала от натяжения цепи, принимаем [τк2]=16 МПа.
Диаметр выходного конца вала:
, (34)
где Мк2=156,2 Н·м – крутящий момент на ведомом валу, (ПЗ, табл.1).
dв2 = = 36,7мм.
Принимаем ближайшее значение из стандартного ряда: dв2=38 мм. Принимаем под подшипниками диаметр вала dп2=45 мм. Принимаем диаметр вала под зубчатым колесом dk2=50 мм, диаметр буртика dб2=55 мм.
|
Рисунок 3 - Конструкция ведомого вала
[1,с161 162, 296
297].
Методические указания
Допускаемое напряжение на кручение принимать с учетом действия напряжений изгиба и условий работы вала в интервале
[τк]=15 25 МПа.
Диаметры ступеней принимать из стандартного ряда, [1, с 161 162], разница диаметров ступеней 4
6 мм.
Диаметры цапф вала под подшипники качения выбирать из стандартного вала [1, с.393].
Разница диаметров полумуфт для соединения валов двигателя и редуктора не более 10 мм.
Расчет цепной передачи
Выбираем приводную роликовую однорядную цепь по ГОСТ 13568 - 75, так как она наиболее приемлема для применения в приводах общего назначения, где необходимо понизить частоту вращения приводного вала.
Определяем число зубьев ведущей и ведомой звездочек и фактическое передаточного число
Число зубьев ведущей звездочки:
, (52)
где Uц – передаточное число цепной передачи, Uц = 3,23, (ПЗ, п.1).
Z 3=31-2·3,23=24,54.
Принимаем Z 3 =25
Число зубьев ведомой звездочки:
Z 4=Z3·Uц , (53)
Z4=25·3,23=80,75.
Принимаем Z4=81
Фактическое передаточное число:
Uцф = .
Uцф= =3,24
Определяем процентное расхождение
∆U = ·100%, (54)
∆U= =0,31 %, допускается до 3%.
Определяем расчетные коэффициенты нагрузки
, (55)
где КД -динамический коэффициент при спокойной нагрузке (передача к ленточному конвейеру, Кд=1, [1,с.149];
|
Кα- коэффициент, учитывающий влияние межосевого расстояния, при α=(30÷50)·t, Кα=1, [1,с.150];
Кн- коэффициент, учитывающий влияние наклона цепи, при α =0° КН=1;
Кр- коэффициент, учитывающий способ регулирования натяжения цепи, при периодическом Кр=1,25;
Ксм- коэффициент, учитывающий способ смазки цепи, при периодической ручной Ксм=1;
Кп- коэффициент, учитывающий периодичность работы передачи, при работе в одну смену Кп=1,[1, с.150].
Кэ=1·1·1,25·1·1=1,25.
Определяем шаг цепи
Для определения шага цепи необходимо знать допускаемое давление [Р] в шарнирах цепи. Так как в таблице допускаемое давление [P] задано в зависимости от шага t и частоты вращения ведущей звездочка [Р] задаем ориентировочно.
Ведущая звездочка имеет частоту вращения n2=307 об/мин.,(ПЗ, п.1).
Принимаем [Р]=22 МПа.
, (56)
где М2- вращающий момент на валу ведущей звездочки, М2=156,2 Н·м;
Кэ– коэффициент, учитывающий условия эксплуатации и монтажа
цепной передачи, Кэ=1,25;
Z3=25 – число зубьев ведущей звездочки;
m - число рядов цепи, m=1.
t =2, 8· =16, 54 мм.
Подбираем цепь ПР-19,05-31,8 по ГОСТ 13568-75, имеющую шаг t=19,05 мм;
разрушающую нагрузку Q=31,8 кН; масса одного метра цепи q=1,9 кг/м;
проекция опорной поверхности шарнира Аоп=105,8 мм2, [1,с.147]
Определяем окружную скорость цепи
, (57)
где Z3– число зубьев ведущей звездочки, Z3=25;
t– шаг цепи, t=19,05 мм;
n3– частота вращения ведущей звездочки, n3=307 об/мин.
υ= =2,44 м/с.
Определяем окружную силу, передаваемую цепью
, (58)
где М2-вращающий момент на валу звездочки, М2=156,2 Н·м;
ω2 – угловая скорость вала ведущей звездочки, ω2=32,12 1/с;
|
υ – окружная скорость цепи, υ=2,44 м/с.
Fтц = =2054 Н.
Определяем силы давления в шарнирах и проверяем цепь на износостойкость
, (59)
где FТЦ – окружная сила, FТЦ=2054 Н;
Кэ – коэффициент, учитывающий условия эксплуатации и монтажа
цепной передачи, Кэ=1,25;
АОП – проекция опорной поверхности шарнира, АОП=106 мм2.
P= =24МПа
Уточняем допускаемое давление:
[P]=22·[1+0,01(Z3-17)], [1,с.150]
[P]=22·[1+0,01(25-17)] 24 МПа;
Условие Р< [Р] выполнено.
Определяем число звеньев цепи
, (60)
где =[30÷50]·t – межосевое расстояние;
t – шаг цепи, t=19,05 мм.
Принимаем =50·t мм, тогда
(61)
Определяем суммарное число зубьев звездочек:
, (62)
где Z3– число зубьев ведущей звездочки,Z3=25;
Z4 – число зубьев ведомой звездочки, Z4=81;
ZΣ=25+81=106
. (63)
∆=
=8,92
Определяем число звеньев в цепи:
, (64) Lt=2·50+0,5·106+
=154,59.
Округляем до четного числа Lt=154.
Уточняем межосевое расстояние
, (65)
где t– шаг цепи, t=19,05 мм;
Lt – число звеньев цепи, Lt=154;
ZΣ– суммарное число зубьев звездочек, ZΣ=106;
Δ=8,92.
ац=0,25·19,05[154-0,5·106 + ]=946 мм.
Для свободного провисания цепи предусматриваем возможность уменьшения межосевого расстояния на 0,4%, т.е. на 946·0,004 4мм.
|
Определяем размеры звездочек
Определяем диаметр делительной окружности:
, (66)
где t– шаг цепи, t=19,05 мм;
Z3 –число зубьев ведущей звездочки, Z3=25.
dдз= =152 мм.
dд4= =491 мм.
Определяем силы, действующие на цепь
Окружная сила FТЦ – определена выше, FТЦ=2054 Н.
Определяем центробежную силу:
, (67)
где q– масса одного метра цепи, q=1,9 кг/м;
υ– окружная скорость цепи, υ=2,44 м/с.
Fv=1, 9· 2,442=11Н.
Определяем силу от провисания цепи:
, (68)
где Кf – коэффициент, учитывающий расположение цепи, при горизонтально расположенной цепи, Кf=1,5 [1, с. 151];
=946 мм – межосевое расстояние,
=946 мм.
Ff = 9,81·1,5·0,949=26Н.
Определяем расчетную нагрузку на валы:
, (69)
F в =2054+2·26 2100Н.
Определяем коэффициент запаса прочности цепи
, (70)
где Q – разрушающая нагрузка,Q=31,8 кН;
FТЦ – окружная сила, FТЦ=2054 кН;
КД- динамический коэффициент, КД=1;
Fv – центробежная сила,Fv=11 H;
Ff– сила от провисания цепи, Ff=26 H.
S= =15,2.
[S] – нормативный коэффициент запаса, [S] 8,9, [1,с.151, табл.7.19],
условие S>[S] выполнено.
Определяем конструктивные размеры ведущей звездочки
Диаметр ступицы звездочки:
, (71)
где dв2– диаметр выходного конца ведомого вала, dв2=38 мм, (ПЗ, п.3).
d ст =1,6·38=60 мм.
Длина ступицы звездочки:
(72)
lC Т = (1,2÷1,6) · 38=45÷60мм
Принимаем lCТ=55 мм
Толщина диска звездочки:
|
С=0,93·ВВН, (73)
где ВВН=12,7 мм – расстояние между пластинками внутреннего звена, ВВН=12,7 мм, [1, ст.147, табл. 7.15].
С=0,93·12,7=12 мм
Таблица 5
Наименование параметра и единицы измерения | Обозначение параметров и числовое значение |
Число зубьев звездочек: ведущей ведомой Фактическое передаточное число Расчетный коэффициент нагрузки Шаг цепи, мм Разрушающая нагрузка, кН Масса одного метра цепи, кг/м Проекция опорной поверхности шарнира, мм2 Окружная скорость цепи, м/с Окружная сила, Н Сила давления в шарнирах, МПа Допускаемое давление в шарнирах цепи, МПа Суммарное число зубьев звездочек Δ Число звеньев цепи Межосевое расстояние, мм Диаметр делительной окружности ведущей звездочки, мм Сила от провисания цепи, Н Расчетная нагрузка на валы, Н Коэффициент запаса прочности Центробежная сила, Н Диаметр ступицы звездочки, мм Длина ступицы звездочки, мм Толщина диска звездочки, мм | Z3=25 Z4=81 UЦ=3,24 Кэ=1,25 t=19,05 Q=31,8 q=1,9 АОП=106 υ=2,44 FТЦ=2054 Р=24 [P]=24 ZΣ=106 Δ=8,92 Lt=154 aЦ=946 dд3=152 Ff=26 Fв=2100 S=15,2 FV=11 dCТ=60 lСТ=55 12 |
[1,с240 243, 298].
Методические указания
При выборе коэффициента нагрузки необходимо учитывать, что цепная передача открытая, расположена горизонтально, нагрузка спокойная, работа односменная, (ПЗ, задание).
При определении числа звеньев цепи принять четное число, для удобства соединения звеньев.
Расчёт зубчатых колес редуктора
Так как в задании нет особых требований в отношении габаритов передачи, выбираем материалы со средними механическими характеристиками: для шестерни сталь 45, термическая обработка – улучшение, твёрдость НВ 230; для колеса – сталь 45, термическая обработка – улучшение, но твердость на 30 единиц ниже - НВ 200. Разница твердости объясняется необходимостью равномерного износа зубьев зубчатых колес.
Определим допускаемое контактное напряжение:
, (11)
где σHlimb – предел контактной выносливости при базовом числе циклов,
σHlimb=2 HB+70, [1, с. 34, табл. 3.2];
KHL – коэффициент долговечности, KHL=1, [1, с. 33];
[SH] – коэффициент безопасности, [SH] =1.1, [1, с. 33].
Для шестерни
, (12)
482 МПа.
Для колеса
, (13)
=428 МПа.
Для непрямозубых колёс расчётное допускаемое контактное напряжение определяется по формуле
, (14)
[σH]=0,45·([482 +428]) = 410 МПа.
Требуемое условие выполнено.
(Для прямозубых передач [σH]= [σH2])
Определяем межосевое расстояние.
Межосевое расстояние из условия контактной выносливости определяется по формуле
, (15)
где Ka– коэффициент для косозубой передачи, Ka=43, [1, с. 32], (Для прямозубых Ka=49,5);
U1 – передаточное число редуктора, U1=3,15, (ПЗ, задание);
М2– вращающий момент на ведомом валу, М2=156,2 Н·м, (ПЗ, табл.1);
КНВ – коэффициент, учитывающий неравномерность распределения
нагрузки, КНВ=1, [1, с.32];
[σH] – допускаемое контактное напряжение, [σH]=410MПа;
ψba – коэффициент ширины венца, ψba=0,4, (ПЗ, задание).
аω= 43·(3,15+1)·
=110 мм.
В первом ряду значений межосевых расстояний по ГОСТ 2185-66 выбираем ближайшее и принимаем аω=125 мм, [1, с. 36].
Определяем модуль передачи
Нормальный модуль зацепления принимают по следующей рекомендации:
мм.
Принимаем по ГОСТ 9563-60, =2 мм, [1, с. 36]. (В силовых передачах
≥1,5 мм.)
Определяем угол наклона зубьев и суммарное число зубьев
Принимаем предварительно угол наклона зубьев β=9º, (ПЗ, задание) и определяем суммарное число зубьев
, (16)
где – межосевое расстояние,
=125 мм;
– нормальный модуль зацепления,
=2 мм.
Z∑ = =123,39.
Принимаем Z∑=123.
Определяем числа зубьев шестерни и колеса.
Число зубьев шестерни равно:
, (17)
где U1 – передаточное число редуктора, U1=3,15;
Z∑= 123 – суммарное число зубьев, Z∑= 123.
=
=29,64.
Принимаем =30.
Определяем число зубьев колеса:
Z2= Z∑ -Z1, (18)
Z2=123-30=93.
Уточняем передаточное число
(19)
где Z1 – число зубьев шестерни, Z1=30;
Z2 – число зубьев колеса, Z2=93.
U1ф= 3,1.
Уточняем угол наклона зубьев:
, (20)
где mn– модуль передачи, mn=2 мм;
аω – межосевое расстояние, аω=125 мм.
cos β = =0,984.
Принимаем β=10º26'.
Определяем диаметры колес и их ширину.
Делительный диаметр шестерни:
, (21)
где mn – модуль передачи, mn=2 мм;
Z1– число зубьев шестерни, Z1=30;
– косинус угла наклона зубьев,
=0,984.
d1= 60,98 мм
Делительный диаметр колеса:
, (22)
где Z2– число зубьев колеса, Z2= 93.
d2= =189,02 мм
Проверяем межосевое расстояние:
aw = мм
Определим диаметры вершин зубьев:
, (23)
da1=60,98 +2·2=64,98 мм;
da2=189,02 +2·2=193,02 мм.
Определим диаметры впадин зубьев:
df1 = d1 -2,5 mn.
df1 =60,98-2,5·2=55,98 мм;
df2=189,02-2,5·2=184,02 мм.
Определяем ширину колеса:
, (24)
где – коэффициент ширины венца,
=0,4;
аω– межосевое расстояние, аω=125 мм.
b2=0,4·125=50 мм.
Определяем ширину шестерни:
, (25)
b1=50+5=55 мм.
Определяем коэффициент ширины шестерни по диаметру:
, (26)
ψ ba = .
Определяем окружные скорости и значения степени точности изготовления шестерни и колеса.
υ= , (27)
где n1– частота вращения шестерни,
n1=967 об/мин, (ПЗ, п.1);
d1 – делительный диаметр шестерни, d1=60,98 мм.
υ = =3,09 м/с.
При такой скорости для косозубых колес принимаем 8-ю степень точности, [1, с. 32].
Определяем коэффициент нагрузки, проверяем зубья на контактное напряжение
, (28)
где KHB – коэффициент, учитывающий неравномерность
распределения нагрузки по ширине венца, KHB=1,[1, табл. 3.5];
KHα- коэффициент, учитывающий неравномерность
распределения нагрузки между зубьями, KHα=1,12, [1, табл. 3.5];
KHV – динамический коэффициент, KHV=1,1, [1, табл. 3.6].
Кн=1·1,12·1,1=1,23.
Проверяем зубья на контактные напряжения:
(29)
где aω – межосевое расстояние, aω=125 мм;
M2 – передаваемый момент, M2=156,2 Н·м, (ПЗ, п.1);
b2 -ширина колеса, b2=50 мм;
U1 – передаточное число редуктора, U1=3,1;
270-коэффициент для непрямозубых колес (для прямозубых зубчатых передач 310)
σH= =352,81МПа<
=410 МПа.
<
.
Определяем силы, действующие в зацеплении.
Определяем окружную силу:
Ft= , (30)
где M1– вращающий момент на валу шестерни, M1= 52,2 H·м;
d1– делительный диаметр шестерни, d1=60,98 мм.
Ft= = 1712 Н
Определяем радиальную силу:
, (31)
где
- угол зацепления в нормальном сечении,
= 20°, [1, с. 29];
- угол наклона зубьев,
= 10° 26´.
Fr= =633 Н
Определяем осевую силу:
, (32)
Fa=1712·tg10º26´=295 Н.
(Для прямозубых и шевронных передач Fa=0)
Полученные данные приведем в таблице.
Таблица 2
Наименование параметров и единица измерения | Обозначение параметров и числовое значение |
Материал, вид термической обработки, твердость: шестерни колеса Допускаемое контактное напряжение, МПа: шестерни колеса Расчетное допускаемое контактное напряжение, МПа Межосевое расстояние, мм Нормальный модуль зацепления, мм Суммарное число зубьев Число зубьев: шестерни колеса Угол наклона зубьев Передаточное число редуктора Делительный диаметр, мм: шестерни колеса Диаметр вершин зубьев, мм шестерни колеса Диаметр впадин зубьев, мм шестерни колеса |
Продолжение таблицы 2
Наименование параметров и единица измерения | Обозначение параметров и числовое значение |
Ширина, мм шестерни колеса Коэффициент ширины шестерни по диаметру Окружная скорость, м/c Степень точности изготовления Коэффициент нагрузки Окружная сила, Н Радиальная сила, Н Осевая сила, Н | b1=55 b2=50 ψba=1,23 υ=3,09 8 KH=1,123 Ft=1712 Fr=633 Fa=295 |
Методические указания
Разница твердости зубьев шестерен и колеса для прямозубых передач 25 30 HB, для косозубых передач и шевронных 30
50 HB.
Фактическое передаточное число должно отличаться от заданного не более чем на 3%.
Значения межосевого расстояния и нормального модуля рекомендуется выбирать из первого ряда. Угол наклона зубьев рассчитать с точностью до одной минуты, а для этого cosβ рассчитать до пятого знака после запятой.
Диаметры шестерни и колеса рассчитать с точностью до сотых долей мм. Ширину зубчатых колес округлить до целого числа. Окружная скорость для прямозубой передачи должна быть не более 5м/с. Контактные напряжения, возникающие в зацеплении должны быть в пределе до 5% -перегрузка и до 20% недогрузка.
Предварительный расчет валов, подбор муфты
Расчет выполняем на кручение по пониженным допускаемым напряжениям, с учетом действия на вал изгибающего момента.
Ведущий вал:
Диаметр выходного конца при допускаемом напряжении [τк]=20 МПа вычисляется мо формуле:
, (33)
где Mк1– крутящий момент на ведущем валу, Mк1=50,39 Н·м, (ПЗ, табл. 1);
[τк]– допускаемое напряжение на кручение, [τк]=20 МПа, [1, с. 160].
d в1 = =23,7 мм.
Принимаем dв1=32 мм из стандартного ряда [1, с.162].
Так как вал редуктора соединен муфтой с валом электродвигателя, то необходимо согласовать диаметры вала двигателя dдв и вала dв1. У подобранного электродвигателя диаметр вала dдв=38 мм, [1,с391. табл.П2]. Выбираем муфту упругую втулочно-пальцевую МУВП по ГОСТ 21424-75, с допускаемым моментом [T]=125Н·М, d=28 мм, длина полумуфты на вал редуктора
ℓм =60мм,[1,с.277] расточкой полумуфты под вал двигателя dдв=38 мм и
dв1=32 мм, [1, с277].
Принимаем диаметр вала под подшипники dп1=40 мм, диаметр буртика dб1=45 мм. Шестерню выполняем за одно целое с валом.
Рисунок 2 - Конструкция ведущего вала
Ведомый вал:
Принимаем материал вала сталь 45, термическая обработка улучшение, твердость HB 16…170
Учитывая влияние изгиба вала от натяжения цепи, принимаем [τк2]=16 МПа.
Диаметр выходного конца вала:
, (34)
где Мк2=156,2 Н·м – крутящий момент на ведомом валу, (ПЗ, табл.1).
dв2 = = 36,7мм.
Принимаем ближайшее значение из стандартного ряда: dв2=38 мм. Принимаем под подшипниками диаметр вала dп2=45 мм. Принимаем диаметр вала под зубчатым колесом dk2=50 мм, диаметр буртика dб2=55 мм.
Рисунок 3 - Конструкция ведомого вала
[1,с161 162, 296
297].
Методические указания
Допускаемое напряжение на кручение принимать с учетом действия напряжений изгиба и условий работы вала в интервале
[τк]=15 25 МПа.
Диаметры ступеней принимать из стандартного ряда, [1, с 161 162], разница диаметров ступеней 4
6 мм.
Диаметры цапф вала под подшипники качения выбирать из стандартного вала [1, с.393].
Разница диаметров полумуфт для соединения валов двигателя и редуктора не более 10 мм.
|
|
Опора деревянной одностоечной и способы укрепление угловых опор: Опоры ВЛ - конструкции, предназначенные для поддерживания проводов на необходимой высоте над землей, водой...
Автоматическое растормаживание колес: Тормозные устройства колес предназначены для уменьшения длины пробега и улучшения маневрирования ВС при...
Эмиссия газов от очистных сооружений канализации: В последние годы внимание мирового сообщества сосредоточено на экологических проблемах...
Адаптации растений и животных к жизни в горах: Большое значение для жизни организмов в горах имеют степень расчленения, крутизна и экспозиционные различия склонов...
© cyberpedia.su 2017-2024 - Не является автором материалов. Исключительное право сохранено за автором текста.
Если вы не хотите, чтобы данный материал был у нас на сайте, перейдите по ссылке: Нарушение авторских прав. Мы поможем в написании вашей работы!