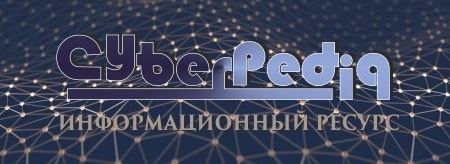
Индивидуальные очистные сооружения: К классу индивидуальных очистных сооружений относят сооружения, пропускная способность которых...
Особенности сооружения опор в сложных условиях: Сооружение ВЛ в районах с суровыми климатическими и тяжелыми геологическими условиями...
Топ:
Оснащения врачебно-сестринской бригады.
Техника безопасности при работе на пароконвектомате: К обслуживанию пароконвектомата допускаются лица, прошедшие технический минимум по эксплуатации оборудования...
Интересное:
Финансовый рынок и его значение в управлении денежными потоками на современном этапе: любому предприятию для расширения производства и увеличения прибыли нужны...
Инженерная защита территорий, зданий и сооружений от опасных геологических процессов: Изучение оползневых явлений, оценка устойчивости склонов и проектирование противооползневых сооружений — актуальнейшие задачи, стоящие перед отечественными...
Уполаживание и террасирование склонов: Если глубина оврага более 5 м необходимо устройство берм. Варианты использования оврагов для градостроительных целей...
Дисциплины:
![]() |
![]() |
5.00
из
|
Заказать работу |
|
|
Введение
Сварка - технологический процесс получения неразъёмного соединения посредством установления межатомных и межмолекулярных связей между свариваемыми частями изделия при их нагреве (местном или общем), или пластическом деформировании.
В 1802 году впервые в мире профессор физики Санкт-Петербургской медико-хирургической академии В.В. Петров (1761-1834 гг.) открыл электрическую дугу и описал явления, происходящие в ней, а также указал на возможность её практического применения.
В 1881 году русский изобретатель Н.Н. Бенардос (1842-1905 гг.) применил электрическую дугу для соединения и разъединения стали. Дуга Н.Н. Бенардоса горела между угольным электродом и свариваемым металлом. Присадочным прутком для образования шва служила стальная проволока. В качестве источника электрической энергии использовались аккумуляторные батареи. Сварка, предложенная Н.Н. Бенардосом, применялась в России в мастерских Риго-Орловской железной дороги при ремонте подвижного состава. Н.Н. Бенардосом были открыты и другие виды сварки: контактная точечная сварка, дуговая сварка несколькими электродами в защитном газе, а также механизированная подача электрода в дугу.
В 1888 году русский инженер Н.Г. Славянов (1854-1897 гг.) предложил дуговую сварку плавящимся металлическим электродом. Он разработал научные основы дуговой сварки, применил флюс для защиты металла сварочной ванны от воздействия воздуха, предложил наплавку и сварку чугуна. Н.Г. Славянов изготовил сварочный генератор своей конструкции и организовал первый в мире электросварочный цех в Пермских пушечных мастерских, где работал с 1883 по 1897 г.
Н.Н. Бенардос и Н.Г. Славянов положили начало автоматизации сварочных процессов. Однако в условиях царской России их изобретения не нашли большого применения. Только после Великой Октябрьской социалистической революции сварка получает распространение в нашей стране. Уже в начале 20-х гг. под руководством профессора В.П. Вологдина на Дальнем Востоке производили ремонт судов дуговой сваркой, а также изготовление сварных котлом, а несколько позже - сварку судов и ответственных конструкций.
|
Развитие и промышленное применение сварки требовало разработки и изготовления надёжных источников питания, обеспечивающих устойчивой горение дуги. Такое оборудование - сварочный генератор СМ-1 и сварочный трансформатор с нормальным магнитным рассеянием СТ-2 - было изготовлено впервые в 1924 году Ленинградским заводом «Электрик». В том же году советский учёный В.П. Никитин разработал принципиально новую схему сварочного трансформатора типа СТН. Выпуск таких трансформаторов заводом «Электрик» начал с 1927 г.
В 1928 году учёный Д.А. Дульчевский изобрёл автоматическую сварку под флюсом.
Новый этап в развитии сварки относится к концу 30-ых годов, когда коллективом института электросварки АН УССР под руководством академика Е.О. Патона был разработан промышленный способ автоматической сварки под флюсом. Внедрение его в производство началось с 1940 г. Сварка под флюсом сыграла огромную роль в годы войны при производстве танков, самоходных орудий и авиабомб. Позднее был разработан способ полуавтоматической сварки под флюсом.
В конце 40-ых годов получила промышленное применение сварка в защитном газе. Коллективами Центрального научно-исследовательского института технологий машиностроения и Института электросварки имени Е.О. Патонова разработана и в 1952 году внедрена полуавтоматическая сварка в углекислом газе.
Огромным достижением сварочной техники явилась разработка коллективом ИЭС в 1949 году электрошлаковой сварки, позволяющей сваривать металлы практически любой толщины.
|
Авторы сварки в углекислом газе плавящимся электродом и электрошлаковой сварки К.М. Новожилив, Г.З. Волошкевич, К.В. Любавский и др. удостоены Ленинской премии.
В последующие годы в стране стали применяться: сварка ультразвуком, электронно-лучевая, плазменная, диффузионная, холодная сварка, сварка трением и др. Большой вклад в развитие сварки внесли учёные нашей страны: В.П. Вологдин, В.П. Никитин, Д.А. Дульчевский, Е.О. Патонов, а также коллективы Института электросварки имени Е.О. Патонова, Центрального научно-исследовательского института технологии машиностроения, Всесоюзного научно-исследовательского и конструктивного института автогенного машиностроения, Института металлургии имени А.А. Байкова, ленинградского завода «Электрик» и др.
Наименование конструкции
Тяга представляет собой сварную металлоконструкцию, детали изготовлены из листового проката 09Г2С.
Габаритные размеры изделия - 2060 х 278 х 435 мм.
Вес - 337 кг.
Рама состоит из следующих деталей:
деталь «Щека» поз. 1 - 2 шт.;
деталь «Валик» поз. 2 - 1 шт.;
деталь «Накладка» поз. 3 - 2 шт.;
деталь «Ребро» поз. 4 - 1 шт.;
деталь «Ребро» поз. 5 - 1 шт.;
деталь «Ребро» поз. 6 - 2 шт.;
Рис. 1 - Петля
2.
Характеристика металла конструкции. Расчет Сэкв
Конструкция изготавливается из стали 09Г2С, которая обладает хорошей свариваемостью.
Химический состав и механические свойства стали 09Г2С представлены в таблицах 2.1 и 2.2.
Таблица 2.1 - Химический состав стали 09Г2С, %
Марка стали | ГОСТ | С | Si | Mn | Cr | Ni | Cu | S | P |
Не более | Не более | ||||||||
09Г2С | 19282-73 | 0,12 | 0,5-0,8 | 1,3-1,7 | 0,30 | 0,30 | 0,30 | 0,040 | 0,035 |
Таблица 2.2 - Механические свойства стали 09Г2С
Марка стали | ГОСТ | ![]() ![]() | ||
не менее | не менее | не менее | ||
09Г2С | 19282-73 | 305 | 460 | 21 |
Температура ковки, 0С: начала 1250, конца 850.
Свариваемость - сваривается без ограничений. Способы сварки - РДС, АДС под флюсом и газовой защитой, ЭШС.
Легирующие элементы Mn, Si, Cr, Cu, Ni - растворяются в феррите, упрочняют его и измельчают перлит. Благодаря этому прочностные характеристики такой стали повышаются и предел прочности доходит до 55 кг/мм². Наличие в стали Мn повышает ее ударную вязкость и хладноломкость, обеспечивает хорошую свариваемость. Введение в состав стали Мn позволяет получать сварные соединения более высокой прочности, при знакопеременных и ударных нагрузках. Сталь 09Г2С относится к спокойной, так как она получается раскислением Si и Мn и содержит более 0,8% Si. Данная сталь менее склонна к старению и отличается меньшей реакцией на сварочный нагрев.
|
Влияние углерода и других легирующих элементов на свариваемость определяется по эквиваленту углерода. Величина эквивалентного содержания углерода зависит от химического состава стали и ее толщины.
Эквивалент углерода определяется по формуле:
, (2.1)
где C, Mn, Cr, Ni, Mo - элементы, содержащиеся в стали 09Г2С,
, 18, 13 - эмпирические коэффициенты.
Определим полный эквивалент углерода с учетом толщины по формуле (2.2):
, (2.2)
где - полный эквивалент углерода с учетом толщины;
- эквивалент углерода;
S - толщина металла;
; 0,005 - эмпирические коэффициенты.
Так как С’э< 0,45%, то сталь Ст. 09Г2С сваривается хорошо всеми способами сварки в широких диапазонах режимов и не требует дополнительных технологических приемов.
Подводя итог, можно сделать вывод, что в целом конструкция технологична, как с точки зрения сборки, так с точки зрения сварки. Следует отметить простоту форм заготовок, рациональное расположение сварных швов, возможность выполнения заготовительных и сборочно-сварочных операций по типовым технологиям. При изготовлении конструкции возможно применение высокопроизводительных способов сварки и прогрессивных приемов изготовления.
Выбор сварочных материалов
Принцип выбора сварочных материалов характеризуется следующими основными условиями:
а) обеспечение требуемой эксплуатационной прочности сварного соединения или наплавленного металла;
б) обеспечение необходимой сплошности сварного шва или наплавленного металла;
в) отсутствие холодных и горячих трещин;
г) получение комплекса специальных свойств наплавленного металла или метала шва.
Стальная проволока 08Г2Сдолжна изготавливаться по ГОСТ 2246-70.
В соответствии с данным стандартом устанавливают диаметр сварочной проволоки, ее химический состав, правила приемки и методы испытания, требования к упаковке, маркировке, транспортированию и хранению.
|
В сертификате, сопровождающем партию проволоки, должны быть указаны следующие данные: товарный знак предприятия-изготовителя, условное обозначение проволоки согласно стандарту, номер плавки и партии, состояние поверхности проволоки (омедненная или неомедненная), химический состав в процентном содержании каждого элемента, результаты испытания на растяжение, масса проволоки в килограммах (нетто).
Проволока для автоматической и полуавтоматической сварки должна быть чистой от грязи, масла, ржавчины, без трещин, клейм и расслоений, не должна иметь резких перегибов и жучков. Бухта должна состоять из одного отрезка проволоки и легко разматываться.
На поверхности сварочной проволоки допускаются риски, царапины и отдельные вмятины, глубиной не более ¼ от предельного отклонения по диаметру.
Наличие бирки, прикрепленной к бухте сварочной проволоки, на которой указаны наименование и товарный знак предприятия-изготовителя, условное обозначение проволоки согласно стандарту и номер партии, а также сертификата на проволоку является гарантией того, что она пригодна для сварочных работ.
Таблица 3.1 - Химический состав сварочной проволоки Св-08Г2С, %.
Марка проволоки | С | Mn | Si | Cr | Ni | S | P |
Св-08Г2С | 0,05-0,11 | 1.80-2.10 | 0,70-0,95 | ≤0,20 | ≤0,25 | не более 0,025 | не более 0,030 |
При сварке проволокой св-08Г2С стали 09Г2С, получаем необходимые механические свойства металла шва.
Для защиты зоны сварки при полуавтоматической сварки используем углекислый газ (СО2). Углекислый газ бесцветен, не ядовит, тяжелее воздуха. При давлении 760 мм рт. ст и при температуре 0ºС плотность углекислого газа равна 1,97686 г./л, что в 1,5 раза больше плотности воздуха.
Углекислый газ поставляется согласно ГОСТ 8050-85. Для сварки используется сварочная углекислота или пищевая с дополнительной осушкой. В соответствии с ГОСТ содержание двуокиси углерода в углекислом газе должно быть не менее 99,5%; содержание водяных паров - не более 0,184 мг/м³, содержание минеральных масел должно быть не более 0.1 мг/кг. Кислород для сварки поставляется в соответствии с ГОСТ 5383-78, согласно которому содержание кислорода в объеме должно быть не менее 99,5%, а содержание водяных паров - не более 0,07 г/м³.
Таблица 3.2 - Химический состав углекислоты.
Состав | Сорт | |
Сварочная, 1 сорт | Сварочная, 2 сорт | |
СО2, (не меньше), % СО, (не более), % Водяных паров при 760 мм.рт. ст. и 20 °С (не более), г/м³ | 99,5 0 0,178 | 99,0 0 0,515 |
В углекислом газе не должны содержаться минеральные масла, глицерин, сероводород, соляная, серная и азотная кислоты, спирты; эфиры, органические кислоты и аммиак.
|
В качестве защитного газа целесообразно применение смеси углекислого газа с кислородом (СО2+О2).
Смесь СО2+О2 оказывает более интенсивное окисляющее действие на жидкий металл, чем чистый углекислый газ. Благодаря этому повышается жидко текучесть металла, что улучшает формирование шва и снижает привариваемость капель металла к поверхности изделия. Кроме того, кислород дешевле углекислого газа, что делает смесь экономически выгодной.
При сварке в чистом углекислом газе потери металла на разбрызгивание может достигать 10 ÷ 12%. Это снижает эффективность этого способа сварки, ухудшает формирование сварочного шва, вызывает дополнительные трудовые затраты на очистку поверхности изделия и сопла сварочной горелки от брызг.
Для повышения стабильности дуги, уменьшения разбрызгивания снижения себестоимости защитного газа рекомендуется применение смеси углекислого газа (70..80)% и кислорода (20..30)%.
Расчет режимов сварки
При выборе параметров применяем методику расчета режимов механизированной сварки, соединений различных типов. Режимы сварки выбираем в зависимости от свариваемости металла, толщины, типа шва, выбранного способа сварки и сварочных материалов.
Рассчитаем параметры режимов для полуавтоматической сварки в среде СО2.
Принимаем диаметр сварочной проволоки dэ = 1,6 мм. Сварочный ток определится из допустимой плотности тока j = 110..130 А/мм²
, (5.1)
Механизированные способы сварки позволяют применять значительно большие плотности тока по сравнению с ручной сваркой. Это объясняется меньшей длиной вылета электрода.
Напряжение на дуге определим по формуле:
(5.2)
Определим скорость подачи электродной проволоки:
, (5.3)
где ρ=7.85 г./мм² - плотность стали,
αН - коэффициент наплавки, равный
(5.4)
Тогда скорость подачи проволоки равна:
= 206 м/ч
Таблица 5.1 - Режим полуавтоматической сварки швов стали 09Г2С
Сила сварочного тока, А | 240 |
Напряжение на дуге, В | 25 |
Скорость подачи проволоки, м/ч | 206 |
Диаметр электродной проволоки, мм | 1,6 |
Расход газа, л/мин | 18-20 |
Подготовка металла под сварку
Изделия из металлопроката должны быть отрихтованы, очищены от загрязнений, ржавчины, окалины, заусенцев, наплывов любым способом, не снижающим прочность. Изделия из металлопроката без обработки плоскостей листа не должны иметь раковин, трещин, вкатанной окалины. На поверхности допускаются без зачистки отдельные забоины, риски, царапины, отпечатки. Если глубина их залегания не выводит толщину листов за предельные отклонения. Местные поверхностные дефекты на необрабатываемых плоскостях должны быть удалены пологой вырубкой или зачисткой наждачным кругом на глубину не большую минусового допуска на прокат, и по ширине быть не менее пятикратной глубины.
7. Общие требования к основным и вспомогательным материалам
Материалы основные и вспомогательные должны соответствовать требованиям чертежей, 0СТ24.940.0 1 - 75 и ТУ. Соответствие материалов должно подтверждаться сертификатами. Основные элементы должны изготавливаться из стали 09Г2С не ниже 10 категории по ГОСТ 5520-79, допускается использование стали марки 1 6ГС не ниже 10 категории по ГОСТ 5520-79, стали марки 16 Г2С по ГОСТ 19282-73 с полистным испытанием на ударную вязкость.
Предельные отклонения свободных поверхностей, не ограниченных допусками на чертеже не должна превышать допусков по 7-му классу точности ОСТ 1010 для размеров до 500 мм и ГОСТ 2689 - 54 для размеров свыше 500 мм.
Разметку производить с помощью рулеток соответствующей точности 2-го класса по ГОСТ 7502-69, и линеек измерительных металлических по ГОСТ 427-56. При разметке учитывают припуски на мехобработку.
Детали, полученные газовой резкой должны соответствовать чертежам и требованиям настоящих ТУ. Размеры должны находится в пределах допусков, установленных рабочими чертежами. Параметры шероховатостей поверхностей должны соответствовать параметрам установленным в чертежах. Кромки, не отвечающие по шероховатости поверхности допускается исправлять плавной зачисткой.
Сборка элементов конструкции производится в соответствии с требованиями 0СТ24.04.01 - 75. Сопрягаемые детали должны быть промаркированы. Зазоры в стыках под сварку устанавливаются в зависимости от способа сварки и должны соответствовать требованиям стандартов и чертежей. Смещение кромок под сварку, форма и размеры должны соответствовать требованиям ГОСТ 5264-80, ГОСТ 8713-70, ГОСТ 11533-75 и чертежей.
Допускается замена указанного чертежами способа сварки другим способом, обеспечивающим равнопрочность сварного соединения и не нарушающего, заданные чертежом, внешнюю формы и размеры шва. Сварка должна производится квалифицированными сварщиками, имеющими право сварки ответственных конструкций. Место сварки должно быть защищено от сильного ветра, атмосферных осадков, сквозняков, в открытых помещениях сварка производится при плюсовой температуре.
Форма, размеры и смещения кромок соединений под сварку должны отвечать требованиям ГОСТ 5264 - 69, гост 8713 - 70 и соответствовать чертежу. Отклонения размеров сварных швов:
Список литературы
сталь сварка дефект оборудование
1. Сварка в машиностроении: Справочник в 4-х томах/ Под ред. Н, А, Ольшанского, - М.: Машиностроение, 1978 г.
. Л.Ц. Прох, Б.М. Шпаков Справочник по сварочному оборудованию, Киев, техника, 1983 г.
. Справочник сварщика: издание 4-е/ Под ред. В.В. Степанова, - М.: Машиностроение 1983 г.
Введение
Сварка - технологический процесс получения неразъёмного соединения посредством установления межатомных и межмолекулярных связей между свариваемыми частями изделия при их нагреве (местном или общем), или пластическом деформировании.
В 1802 году впервые в мире профессор физики Санкт-Петербургской медико-хирургической академии В.В. Петров (1761-1834 гг.) открыл электрическую дугу и описал явления, происходящие в ней, а также указал на возможность её практического применения.
В 1881 году русский изобретатель Н.Н. Бенардос (1842-1905 гг.) применил электрическую дугу для соединения и разъединения стали. Дуга Н.Н. Бенардоса горела между угольным электродом и свариваемым металлом. Присадочным прутком для образования шва служила стальная проволока. В качестве источника электрической энергии использовались аккумуляторные батареи. Сварка, предложенная Н.Н. Бенардосом, применялась в России в мастерских Риго-Орловской железной дороги при ремонте подвижного состава. Н.Н. Бенардосом были открыты и другие виды сварки: контактная точечная сварка, дуговая сварка несколькими электродами в защитном газе, а также механизированная подача электрода в дугу.
В 1888 году русский инженер Н.Г. Славянов (1854-1897 гг.) предложил дуговую сварку плавящимся металлическим электродом. Он разработал научные основы дуговой сварки, применил флюс для защиты металла сварочной ванны от воздействия воздуха, предложил наплавку и сварку чугуна. Н.Г. Славянов изготовил сварочный генератор своей конструкции и организовал первый в мире электросварочный цех в Пермских пушечных мастерских, где работал с 1883 по 1897 г.
Н.Н. Бенардос и Н.Г. Славянов положили начало автоматизации сварочных процессов. Однако в условиях царской России их изобретения не нашли большого применения. Только после Великой Октябрьской социалистической революции сварка получает распространение в нашей стране. Уже в начале 20-х гг. под руководством профессора В.П. Вологдина на Дальнем Востоке производили ремонт судов дуговой сваркой, а также изготовление сварных котлом, а несколько позже - сварку судов и ответственных конструкций.
Развитие и промышленное применение сварки требовало разработки и изготовления надёжных источников питания, обеспечивающих устойчивой горение дуги. Такое оборудование - сварочный генератор СМ-1 и сварочный трансформатор с нормальным магнитным рассеянием СТ-2 - было изготовлено впервые в 1924 году Ленинградским заводом «Электрик». В том же году советский учёный В.П. Никитин разработал принципиально новую схему сварочного трансформатора типа СТН. Выпуск таких трансформаторов заводом «Электрик» начал с 1927 г.
В 1928 году учёный Д.А. Дульчевский изобрёл автоматическую сварку под флюсом.
Новый этап в развитии сварки относится к концу 30-ых годов, когда коллективом института электросварки АН УССР под руководством академика Е.О. Патона был разработан промышленный способ автоматической сварки под флюсом. Внедрение его в производство началось с 1940 г. Сварка под флюсом сыграла огромную роль в годы войны при производстве танков, самоходных орудий и авиабомб. Позднее был разработан способ полуавтоматической сварки под флюсом.
В конце 40-ых годов получила промышленное применение сварка в защитном газе. Коллективами Центрального научно-исследовательского института технологий машиностроения и Института электросварки имени Е.О. Патонова разработана и в 1952 году внедрена полуавтоматическая сварка в углекислом газе.
Огромным достижением сварочной техники явилась разработка коллективом ИЭС в 1949 году электрошлаковой сварки, позволяющей сваривать металлы практически любой толщины.
Авторы сварки в углекислом газе плавящимся электродом и электрошлаковой сварки К.М. Новожилив, Г.З. Волошкевич, К.В. Любавский и др. удостоены Ленинской премии.
В последующие годы в стране стали применяться: сварка ультразвуком, электронно-лучевая, плазменная, диффузионная, холодная сварка, сварка трением и др. Большой вклад в развитие сварки внесли учёные нашей страны: В.П. Вологдин, В.П. Никитин, Д.А. Дульчевский, Е.О. Патонов, а также коллективы Института электросварки имени Е.О. Патонова, Центрального научно-исследовательского института технологии машиностроения, Всесоюзного научно-исследовательского и конструктивного института автогенного машиностроения, Института металлургии имени А.А. Байкова, ленинградского завода «Электрик» и др.
Наименование конструкции
Тяга представляет собой сварную металлоконструкцию, детали изготовлены из листового проката 09Г2С.
Габаритные размеры изделия - 2060 х 278 х 435 мм.
Вес - 337 кг.
Рама состоит из следующих деталей:
деталь «Щека» поз. 1 - 2 шт.;
деталь «Валик» поз. 2 - 1 шт.;
деталь «Накладка» поз. 3 - 2 шт.;
деталь «Ребро» поз. 4 - 1 шт.;
деталь «Ребро» поз. 5 - 1 шт.;
деталь «Ребро» поз. 6 - 2 шт.;
Рис. 1 - Петля
2.
Характеристика металла конструкции. Расчет Сэкв
Конструкция изготавливается из стали 09Г2С, которая обладает хорошей свариваемостью.
Химический состав и механические свойства стали 09Г2С представлены в таблицах 2.1 и 2.2.
Таблица 2.1 - Химический состав стали 09Г2С, %
Марка стали | ГОСТ | С | Si | Mn | Cr | Ni | Cu | S | P |
Не более | Не более | ||||||||
09Г2С | 19282-73 | 0,12 | 0,5-0,8 | 1,3-1,7 | 0,30 | 0,30 | 0,30 | 0,040 | 0,035 |
Таблица 2.2 - Механические свойства стали 09Г2С
Марка стали | ГОСТ | ![]() ![]() | ||
не менее | не менее | не менее | ||
09Г2С | 19282-73 | 305 | 460 | 21 |
Температура ковки, 0С: начала 1250, конца 850.
Свариваемость - сваривается без ограничений. Способы сварки - РДС, АДС под флюсом и газовой защитой, ЭШС.
Легирующие элементы Mn, Si, Cr, Cu, Ni - растворяются в феррите, упрочняют его и измельчают перлит. Благодаря этому прочностные характеристики такой стали повышаются и предел прочности доходит до 55 кг/мм². Наличие в стали Мn повышает ее ударную вязкость и хладноломкость, обеспечивает хорошую свариваемость. Введение в состав стали Мn позволяет получать сварные соединения более высокой прочности, при знакопеременных и ударных нагрузках. Сталь 09Г2С относится к спокойной, так как она получается раскислением Si и Мn и содержит более 0,8% Si. Данная сталь менее склонна к старению и отличается меньшей реакцией на сварочный нагрев.
Влияние углерода и других легирующих элементов на свариваемость определяется по эквиваленту углерода. Величина эквивалентного содержания углерода зависит от химического состава стали и ее толщины.
Эквивалент углерода определяется по формуле:
, (2.1)
где C, Mn, Cr, Ni, Mo - элементы, содержащиеся в стали 09Г2С,
, 18, 13 - эмпирические коэффициенты.
Определим полный эквивалент углерода с учетом толщины по формуле (2.2):
, (2.2)
где - полный эквивалент углерода с учетом толщины;
- эквивалент углерода;
S - толщина металла;
; 0,005 - эмпирические коэффициенты.
Так как С’э< 0,45%, то сталь Ст. 09Г2С сваривается хорошо всеми способами сварки в широких диапазонах режимов и не требует дополнительных технологических приемов.
Подводя итог, можно сделать вывод, что в целом конструкция технологична, как с точки зрения сборки, так с точки зрения сварки. Следует отметить простоту форм заготовок, рациональное расположение сварных швов, возможность выполнения заготовительных и сборочно-сварочных операций по типовым технологиям. При изготовлении конструкции возможно применение высокопроизводительных способов сварки и прогрессивных приемов изготовления.
Выбор сварочных материалов
Принцип выбора сварочных материалов характеризуется следующими основными условиями:
а) обеспечение требуемой эксплуатационной прочности сварного соединения или наплавленного металла;
б) обеспечение необходимой сплошности сварного шва или наплавленного металла;
в) отсутствие холодных и горячих трещин;
г) получение комплекса специальных свойств наплавленного металла или метала шва.
Стальная проволока 08Г2Сдолжна изготавливаться по ГОСТ 2246-70.
В соответствии с данным стандартом устанавливают диаметр сварочной проволоки, ее химический состав, правила приемки и методы испытания, требования к упаковке, маркировке, транспортированию и хранению.
В сертификате, сопровождающем партию проволоки, должны быть указаны следующие данные: товарный знак предприятия-изготовителя, условное обозначение проволоки согласно стандарту, номер плавки и партии, состояние поверхности проволоки (омедненная или неомедненная), химический состав в процентном содержании каждого элемента, результаты испытания на растяжение, масса проволоки в килограммах (нетто).
Проволока для автоматической и полуавтоматической сварки должна быть чистой от грязи, масла, ржавчины, без трещин, клейм и расслоений, не должна иметь резких перегибов и жучков. Бухта должна состоять из одного отрезка проволоки и легко разматываться.
На поверхности сварочной проволоки допускаются риски, царапины и отдельные вмятины, глубиной не более ¼ от предельного отклонения по диаметру.
Наличие бирки, прикрепленной к бухте сварочной проволоки, на которой указаны наименование и товарный знак предприятия-изготовителя, условное обозначение проволоки согласно стандарту и номер партии, а также сертификата на проволоку является гарантией того, что она пригодна для сварочных работ.
Таблица 3.1 - Химический состав сварочной проволоки Св-08Г2С, %.
Марка проволоки | С | Mn | Si | Cr | Ni | S | P |
Св-08Г2С | 0,05-0,11 | 1.80-2.10 | 0,70-0,95 | ≤0,20 | ≤0,25 | не более 0,025 | не более 0,030 |
При сварке проволокой св-08Г2С стали 09Г2С, получаем необходимые механические свойства металла шва.
Для защиты зоны сварки при полуавтоматической сварки используем углекислый газ (СО2). Углекислый газ бесцветен, не ядовит, тяжелее воздуха. При давлении 760 мм рт. ст и при температуре 0ºС плотность углекислого газа равна 1,97686 г./л, что в 1,5 раза больше плотности воздуха.
Углекислый газ поставляется согласно ГОСТ 8050-85. Для сварки используется сварочная углекислота или пищевая с дополнительной осушкой. В соответствии с ГОСТ содержание двуокиси углерода в углекислом газе должно быть не менее 99,5%; содержание водяных паров - не более 0,184 мг/м³, содержание минеральных масел должно быть не более 0.1 мг/кг. Кислород для сварки поставляется в соответствии с ГОСТ 5383-78, согласно которому содержание кислорода в объеме должно быть не менее 99,5%, а содержание водяных паров - не более 0,07 г/м³.
Таблица 3.2 - Химический состав углекислоты.
Состав | Сорт | |
Сварочная, 1 сорт | Сварочная, 2 сорт | |
СО2, (не меньше), % СО, (не более), % Водяных паров при 760 мм.рт. ст. и 20 °С (не более), г/м³ | 99,5 0 0,178 | 99,0 0 0,515 |
В углекислом газе не должны содержаться минеральные масла, глицерин, сероводород, соляная, серная и азотная кислоты, спирты; эфиры, органические кислоты и аммиак.
В качестве защитного газа целесообразно применение смеси углекислого газа с кислородом (СО2+О2).
Смесь СО2+О2 оказывает более интенсивное окисляющее действие на жидкий металл, чем чистый углекислый газ. Благодаря этому повышается жидко текучесть металла, что улучшает формирование шва и снижает привариваемость капель металла к поверхности изделия. Кроме того, кислород дешевле углекислого газа, что делает смесь экономически выгодной.
При сварке в чистом углекислом газе потери металла на разбрызгивание может достигать 10 ÷ 12%. Это снижает эффективность этого способа сварки, ухудшает формирование сварочного шва, вызывает дополнительные трудовые затраты на очистку поверхности изделия и сопла сварочной горелки от брызг.
Для повышения стабильности дуги, уменьшения разбрызгивания снижения себестоимости защитного газа рекомендуется применение смеси углекислого газа (70..80)% и кислорода (20..30)%.
Выбор сварочного оборудования
Для полуавтоматической сварки и постановки прихваток в среде защитных газов используем полуавтомат ПДГ-508, технические характеристики которого приведены в таблице 4.1.
Таблица 4.1 - Технические характеристики полуавтомата ПДГ-508
Диаметр электродной проволоки, мм | 1,6-2,0 |
Номинальный сварочный ток, А | 500 |
Скорость подачи проволоки, м/ч | 100-960 |
Масса аппарата, кг | 56 |
При полуавтоматической сварке механизирована только подача проволоки, а перемещение дуги вдоль свариваемого стыка осуществляется вручную.
Высокие эксплуатационные характеристики сварочного полуавтомата ПДГ-508 достигаются за счет применения тонкой проволоки, подаваемой к электрической дуге по гибкому направляющему каналу, который позволяет разместить относительно тяжелый механизм для подачи проволоки на значительное расстояние от зоны сварки, где расположен только рабочий орган - сварочная горелка.
Полуавтомат имеет плавно-ступенчатое регулирование скорости подачи электродной проволоки. В состав полуавтомата входят две сварочные горелки, комплект газовой аппаратуры, токоведущие кабеля и шланги. Подающее устройство оформлено в виде небольшого блока, внутри которого расположены электродвигатель с редуктором, кассета и газовый клапан.
При дуговой сварке в среде СО2 сварочная дуга имеет возрастающую вольтамперную характеристику. Для стабильности процесса и устойчивости работ, требуется источник с жесткой внешней характеристикой, одним из которых является выпрямитель ВДУ-506, он имеет следующие преимущества по сравнению с преобразователями и генераторами: широкие пределы регулирования сварочного тока, высокие динамические свойства и технико-экономические показатели, высокий К.П.Д.
Таблица 4.2 - Технические данные выпрямителя ВДУ-506.
Напряжение питающей сети, В | 380; 220 |
Номинальный сварочный ток, А | 500 |
Пределы регулирования сварочного тока, А для жестких характеристик для падающих характеристик | 60-500 50-500 |
Пределы регулирования рабочего напряжения, В для жестких характеристик для падающих характеристик | 18-50 22-46 |
Напряжение холостого хода, В, не более | 85 |
Продолжительность цикла сварки, мин | 10 |
Габаритные размеры, мм | 820х620х1100 |
Масса, кг | 300 |
Расчет режимов сварки
При выборе параметров применяем методику расчета режимов механизированной сварки, соединений различных типов. Режимы сварки выбираем в зависимости от свариваемости металла, толщины, типа шва, выбранного способа сварки и сварочных материалов.
Рассчитаем параметры режимов для полуавтоматической сварки в среде СО2.
Принимаем диаметр сварочной проволоки dэ = 1,6 мм. Сварочный ток определится из допустимой плотности тока j = 110..130 А/мм²
, (5.1)
Механизированные способы сварки позволяют применять значительно большие плотности тока по сравнению с ручной сваркой. Это объясняется меньшей длиной вылета электрода.
Напряжение на дуге определим по формуле:
(5.2)
Определим скорость подачи электродной проволоки:
, (5.3)
где ρ=7.85 г./мм² - плотность стали,
αН - коэффициент наплавки, равный
(5.4)
Тогда скорость подачи проволоки равна:
= 206 м/ч
Таблица 5.1 - Режим полуавтоматической сварки швов стали 09Г2С
Сила сварочного тока, А | 240 |
Напряжение на дуге, В | 25 |
Скорость подачи проволоки, м/ч | 206 |
Диаметр электродной проволоки, мм | 1,6 |
Расход газа, л/мин | 18-20 |
Подготовка металла под сварку
Изделия из металлопроката должны быть отрихтованы, очищены от загрязнений, ржавчины, окалины, заусенцев, наплывов любым способом, не снижающим прочность. Изделия из металлопроката без обработки плоскостей листа не должны иметь раковин, трещин, вкатанной окалины. На поверхности допускаются без зачистки отдельны
|
|
История развития хранилищ для нефти: Первые склады нефти появились в XVII веке. Они представляли собой землянные ямы-амбара глубиной 4…5 м...
История создания датчика движения: Первый прибор для обнаружения движения был изобретен немецким физиком Генрихом Герцем...
Наброски и зарисовки растений, плодов, цветов: Освоить конструктивное построение структуры дерева через зарисовки отдельных деревьев, группы деревьев...
Таксономические единицы (категории) растений: Каждая система классификации состоит из определённых соподчиненных друг другу...
© cyberpedia.su 2017-2024 - Не является автором материалов. Исключительное право сохранено за автором текста.
Если вы не хотите, чтобы данный материал был у нас на сайте, перейдите по ссылке: Нарушение авторских прав. Мы поможем в написании вашей работы!