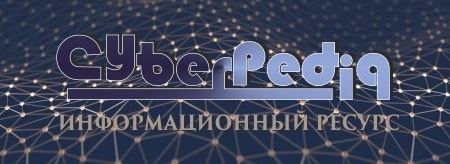
Археология об основании Рима: Новые раскопки проясняют и такой острый дискуссионный вопрос, как дата самого возникновения Рима...
Общие условия выбора системы дренажа: Система дренажа выбирается в зависимости от характера защищаемого...
Топ:
История развития методов оптимизации: теорема Куна-Таккера, метод Лагранжа, роль выпуклости в оптимизации...
Когда производится ограждение поезда, остановившегося на перегоне: Во всех случаях немедленно должно быть ограждено место препятствия для движения поездов на смежном пути двухпутного...
Марксистская теория происхождения государства: По мнению Маркса и Энгельса, в основе развития общества, происходящих в нем изменений лежит...
Интересное:
Что нужно делать при лейкемии: Прежде всего, необходимо выяснить, не страдаете ли вы каким-либо душевным недугом...
Принципы управления денежными потоками: одним из методов контроля за состоянием денежной наличности является...
Национальное богатство страны и его составляющие: для оценки элементов национального богатства используются...
Дисциплины:
![]() |
![]() |
5.00
из
|
Заказать работу |
|
|
6.1 При передаче металла на вакууматор, перед началом обработки металла, в позиции отдачи порошковой проволоки, производится замер содержания водорода в металле.
6.2 Во время обработки металла на вакууматоре без использования кислорода, фурма находится в верхнем рабочем положении (позиция ожидания), через сопло фурмы подается защитный газ – азот. Расход защитного газа 160 м3/ч.
6.3 После постановки сталеразливочного ковша с металлом в позицию вакуумирования, вакуум-камера опускается до уровня касания патрубками шлака, производится замер температуры стали. Возможно проведение одновременного замера температуры и окисленности металла.
6.4 Для создания необходимого вакуума при дегазации и обезуглероживании стали, предусмотрена трехступенчатая система, которая состоит из четырех пароэжекторных и четырех водокольцевых насосов (один в резерве). Пароэжекторные насосы № 3А и № 3Б и водокольцевые насосы работают параллельно. Конденсация рабочего пара происходит в двух смешивающих конденсаторах.
6.5 Отходящие газы, образующиеся в вакуумной системе, и насыщенные CO по газоходам направляются на установку дожигания CO. Режим работы горелок настраивается автоматизированной базовой системой управления в зависимости от состава отработанных газов. Технические данные установки дожигания CO представлены в приложении Б.
6.6 На всасывающий патрубок подается транспортирующий газ – аргон (азот) с расходом 1200 л/мин. Опусканием и подъемом вакуум-камеры патрубки ошлаковываются на высоту 600 - 650 мм.
6.7 После ошлакования патрубки устанавливаются в положение касания шлака в ковше. Затем патрубки погружаются в металл в ручном режиме на глубину 450 мм. При достижении остаточного давления менее 80 мбар, вакуум-камера в ручном режиме дополнительно опускается на 150 - 200 мм.
|
6.8 При достижении остаточного давления в камере менее 3 мбар расход транспортирующего газа устанавливается от 900 до 2500 л/мин в зависимости от температуры металла и получения необходимого содержания водорода.
6.9 После окончания вакуумирования производится разгерметизация системы, патрубки вакуум-камеры выводятся из металла. Производится измерение температуры и, при необходимости (определяется условиями заказа), измеряется содержание кислорода и водорода в стали.
6.10 При поднятии вакуум-камеры после вакуумирования производится автоматическое включение подачи во всасывающий патрубок азота вместо аргона.
6.11 После окончания доводки стали по температуре и химическому составу отбираются пробы металла и шлака, сталеразливочный ковш выдается из позиции обработки в позицию крана.
Передача металла на МНЛЗ без данных химического состава и без окончательного измерения температуры запрещается.
6.12 Удаление гарнисажа с патрубков вакуум-камеры, при необходимости, осуществляется с помощью устройства для удаления настылей.
6.13 При перерыве в вакуумировании от 1 до 12 ч температура футеровки камеры поддерживается газовой горелкой в автоматическом режиме на уровне 1100 °С – 1250 °С.
6.14 При длительных перерывах в работе вакууматора и снижении температуры его футеровки до 800 °С, разогрев последней производится согласно ТИ 102 - СТ.К - 82- 2013.
6.15 Футеровка нижней части вакуум-камеры, сушка и разогрев вакууматора производятся в соответствии с требованиями ТИ 102 - СТ.К - 82- 2013.
Обезуглероживание стали
6.16.1 На вакууматоре возможно производить операции естественного и форсированного обезуглероживания для получения стали с особо низким содержанием углерода (менее 0,010 %).
Естественное обезуглероживание – снижение углерода с 0,04 % и менее до 0,0050 % (50 ppm) и менее посредством вакуумирования нераскисленного металла без вдувания в камеру кислорода при давлении в камере 200 мбар и менее.
|
Форсированное обезуглероживание – снижение углерода с 0,06 % и менее до 0,015 % и менее посредством вакуумирования нераскисленного металла и вдувания кислорода в камеру при давлении в камере 200 мбар и менее.
6.16.2 Для выполнения операции обезуглероживания стали на вакууматоре необходимо соблюдение следующих условий:
- содержание углерода в стали на выпуске из конвертера должно быть не более 0,03 % для естественного обезуглероживания и не более 0,05 % для форсированного обезуглероживания;
- предварительная доводка химического состава стали по содержанию марганца производится на нижний предел во время выпуска металла из конвертера путем присадки в ковш ферромарганца или марганца металлического;
- раскисление металла алюминием и кремнием на сливе не производится;
- ввод шлакообразующих материалов после выпуска металла из конвертера для образования рафинировочного шлака и теплоизоляции;
- продолжительность продувки металла аргоном в сталеразливочном ковше после выпуска из конвертера должна составлять не менее 3 мин.
6.16.3 Длительность естественного или форсированного обезуглероживания при начальном давлении в камере не более 200 мбар определяется конечным содержанием углерода в металле, необходимым для выполнения заказа.
6.16.4 В начале форсированного обезуглероживания, с помощью фурмы верхнего дутья, производится продувка кислородом продолжительностью не менее 3 мин при давлении в камере не более 200 мбар.
6.16.5 После окончания операции обезуглероживания производится предварительное раскисление металла посредством ввода алюминия (таблетированный, дробь и т. п.). При этом вакуумирование металла продолжается.
6.16.6 Корректировка химического состава металла производится только после окончания операции обезуглероживания, после предварительного раскисления металла.
6.16.7 После окончания всех технологических операций производится разгерметизация системы путем открытия клапана разгерметизации, патрубки выводятся из металла, производится измерение температуры. Возможен одновременный замер температуры и окисленности металла.
6.16.8 По окончании операции обезуглероживания производится доводка металла по химическому составу вводом алюминиевой и порошковых проволок. Производится продувка металла аргоном в течение не менее 5 мин без оголения зеркала металла.
|
6.16.9 При получении температуры металла меньше, чем необходимо для разливки на МНЛЗ, сталеразливочный ковш подается на установку «печь-ковш».
КОНТРОЛЬ ТЕХНОЛОГИИ
7.1 При обработке металла на вакууматоре осуществляется автоматизированный учет основных технологических параметров и хронометраж процесса с накоплением контролируемой информации в памяти компьютера с последующим формированием отчетной документации. Данные основных технологических параметров передаются в объединенный паспорт плавки. По запросу, выдается отдельный отчетный документ о пооперационном контроле процесса.
7.2 В отчете о плавке фиксируются следующие параметры:
- время прибытия и передачи ковша;
- продолжительность операций обработки, продувки аргоном (азотом), вакуумирования;
- температура металла, окисленность металла, содержание водорода в металле до и после обработки, а также по ходу обработки;
- химический состав стали и время выдачи результатов химического анализа;
- наименование и количество присаживаемых материалов;
- расход аргона и азота;
- данные о стойкости футеровки вакуум–камеры, патрубков вакууматора;
- информация об обслуживающем персонале, номер плавки, номер сталеразливочного ковша и марка стали.
7.3 Контроль за основными технологическими операциями, а также за параметрами системы энергообеспечения осуществляется сменным мастером участка, сталеварами установки вакууматора.
МЕТРОЛОГИЧЕСКОЕ ОБЕСПЕЧЕНИЕ
8.1 Контроль параметров процесса обработки стали на установке вакуумирования № 1 осуществляется средствами измерения, разработанными и установленными австрийской фирмой «VAI».
8.2 Контроль параметров процесса обработки стали на установке вакуумирования № 2 осуществляется средствами измерения, разработанными и установленными фирмой «СМС».
8.3 Данные по метрологическому обеспечению процесса внепечной обработки стали на вакууматоре приведены в приложении Д.
|
ТРЕБОВАНИЯ БЕЗОПАСНОСТИ
9.1 Все операции технологического процесса внепечной обработки стали должны соответствовать требованиям:
ПБ 03-517-02 «Общие правила промышленной безопасности для организаций, осуществляющих деятельность в области промышленной безопасности опасных производственных объектов» (утверждены Постановлением Госгортехнадзора России от 18.10.2002 № 61-А);
ПБ 11-401-01 «Правила безопасности в газовом хозяйстве металлургических и коксохимических предприятий и производств» (утверждены Постановлением Госгортехнадзора России от 20.02.2001 № 9);
ПБ 11-493-02 «Общие правила безопасности для металлургических и коксохимических предприятий и производств» (утверждены Постановлением Госгортехнадзора России от 21.06.2002 № 35);
ПБ 11-552-03 «Правила безопасности в сталеплавильном производстве» (утверждены Постановлением Госгортехнадзора России от 24.04.2003 № 25);
ОТИ 0.1-2010 «Для всех работников комбината»;
ОТИ 006-17-2013 «Инструкция по охране труда для сталеваров и подручных сталевара участка внепечной обработки стали конвертерного цеха № 1»;
ОТИ 102-62-2011 «Для стропальщиков».
9.2 Нормативные показатели неблагоприятных факторов производственной среды и трудового процесса, оказывающих вредное влияние на человека, должны соответствовать нормам, указанным в следующих документах:
ГН 2.2.5.1313-03 «Предельно допустимые концентрации (ПДК) вредных веществ в воздухе рабочей зоны», Постановление главного государственного санитарного врача Российской Федерации от 30.04.2003 № 76;
СанПиН 2.2.4.548-96 «Гигиенические требования к микроклимату производственных помещений», утверждённые Постановлением Госкомсанэпиднадзора России от 01.10.96 № 21;
СН 2.2.4/2.1.8.562-96 «Шум на рабочих местах, в помещениях жилых, общественных зданий и на территории жилой застройки», утверждённые Постановлением Госкомсанэпиднадзора России от 31.10.96 № 36.
9.3 Все посты управления установки вакуумирования, а также рабочие места сталеваров и их подручных должны быть оборудованы взаимосвязанной громкоговорящей связью, средствами звуковой и световой сигнализации, предупреждающей о нарушении установленных режимов работы и возникновении аварийных ситуаций. Посты управления должны быть оборудованы телефонными коммутаторами, связывающими установку вакуумирования с диспетчером цеха и участками, от которых зависит бесперебойная работа установки вакуумирования.
ТРЕБОВАНИЯ ОХРАНЫ ОКРУЖАЮЩЕЙ СРЕДЫ
10.1 При выполнении технологических операций необходимо соблюдать «Кардинальные экологические требования предприятий группы ООО «ЕвразХолдинг», утвержденные Приказом Президента ООО «ЕвразХолдинг» от 04.06.2012 № 57.
10.2 Нормативы воздействия на окружающую среду технологического процесса и оборудования представлены в приложении Е.
|
10.3 При выполнении технологических операций необходимо соблюдать нормативы выбросов загрязняющих веществ от технологического оборудования в атмосферу согласно «Проекту нормативов предельно допустимых (ПДВ) и временно согласованных (ВСВ) выбросов», утвержденному приказом Росприроднадзора от 20.06.2012 № 774.
10.4 Инструментальные замеры по соблюдению нормативов выброса загрязняющих веществ в атмосферу, оборотной воды производятся аккредитованными лабораториями Экоаналитического центра управления охраны природной среды (УОПС).
10.5 Технологический персонал производит контроль за исправной работой аспирационных установок в соответствии с «Правилами эксплуатации установок очистки газов» (Москва, Министерство химического и нефтяного машиностроения, 1984) и ПТИ 006-СТ-16-2009. Эксплуатация технологического оборудования без аспирационных установок запрещена.
10.6 В период аварийных ситуаций, в том числе случаев, указанных в ПЛА, следует руководствоваться СТП 102-177 М с обязательным учетом принятых мер в журнале.
В период неблагоприятных метеорологических условий (НМУ) следует руководствоваться СТП 102-240 М с обязательным учетом принятых мер в специальном журнале, который хранится в диспетчерской цеха.
10.7 Использование воды должно соответствовать «Индивидуальным текущим нормам водопотребления и водоотведения ОАО «НТМК» (разработаны НТП «Индеко», 2011). Для технологических нужд используется вода чистого оборотного цикла МНЛЗ, грязного оборотного цикла вакууматоров, химически очищенная вода.
10.8 Для охлаждения холодильников горячих газов, гидравлики, вакуумных насосов, горелок, вакуум – камеры используется вода чистого оборотного цикла, которая на вводе по химическому составу должна иметь следующие показатели, приведенные в таблице 3.
Таблица 3
Наименование показателя | Единица измерения | Значение |
Значение кислотности | pH | 7,5-8,5 |
Общая жесткость, не более | мг - экв/л | 5,0 |
Жесткость карбоната, не более | мг - экв/л | 1,5 |
Взвешенные вещества, не более | мг/л | 20,0 |
Температура | °С | 30 |
10.9 Вода грязного оборотного цикла используется для охлаждения конденсата вакууматора и для работы водокольцевых насосов. По химическому составу вода должна иметь предельные показатели, указанные в таблице 4.
Таблица 4
Наименование | Единица измерения | Значение |
Значение кислотности | pH | 11,3 |
Общая жесткость | мг - экв/л | 5,8 |
Жесткость карбоната, не более | мг - экв/л | 4,2 |
Взвешенные вещества | мг /л | 90 |
Сульфаты, не более | мг/л | 860 |
Хлориды, не более | мг/л | 380 |
Температура | ºС | 32 |
10.10 В ходе технологического процесса образуются отходы. При обращении с отходами производства и потребления необходимо руководствоваться приказом Управляющего директора ЕВРАЗ НТМК от 28.09.2012 № 752 «Об утверждении Регламента по обращению с отходами производства и потребления в ОАО «ЕВРАЗ НТМК».
10.10.1 Отходы черных металлов (скрап из сталеразливочных ковшей, аварийный скрап) передаются в цех переработки металлолома.
10.10.2 Шлак из сталеразливочных ковшей сливается или кантуется в шлаковые чаши и отправляется на шлакоразделку конвертерного цеха № 1.
10.10.3 Отходы от чистки узлов установок (остатки металла, заусеницы, скрап, окалина, остатки шлака) и мусор от уборки производственных помещений вывозятся на площадку мусора шлакового отвала.
10.10.4 Отработанные масла сливаются в емкость, частично регенерируются и используются в цехе, частично передаются на мазутный участок паросилового цеха СЦ ТОиР.
10.10.5 Пыль от аспирационных установок отделения внепечной обработки стали вывозится на шлаковый отвал.
10.10.6 Отработанные рукава фильтров аспирационных установок сжигаются в конвертерах или других термических печах цеха.
10.10.7 Все сырье и вспомогательные материалы, используемые в технологическом процессе, поступающие от сторонних организаций, должны иметь действующие санитарно-эпидемиологические заключения.
Отходы тары и упаковки из-под сырья и материалов, изготовленные из полипропилена, бумаги, а также пластиковые емкости вывозятся на площадку производственных мусоров. Металлические емкости после их очистки вывозятся в цех переработки металлолома (ЦПМ).
Приложение А
(справочное)
Перечень ссылочных документов
Обозначение НД | Обозначение пункта, приложения |
ГОСТ 166-89 | Приложение Д |
ГОСТ 295-98 | Приложение В |
ГОСТ 849-2008 | Приложение В |
ГОСТ 859-2001 | Приложение В |
ГОСТ 1415-93 | Приложение В |
ГОСТ 4755-91 | Приложение В |
ГОСТ 4756-91 | Приложение В |
ГОСТ 4757-91 | Приложение В |
ГОСТ 4759-91 | Приложение В |
ГОСТ 4761-91 | Приложение В |
ГОСТ 4762-71 | Приложение В |
ГОСТ 9293-74 | 2.2.2 |
ГОСТ 10157-79 | 2.2.1 |
ГОСТ 11069-2001 | Приложение В |
ГОСТ 11861-91 | Приложение В |
ГОСТ 14848-69 | Приложение В |
ГОСТ 16773-2003 | Приложение В |
ГОСТ 27130-94 | Приложение В |
СТП 102-177 М-2011 | 10.6 |
СТП 102-240 М-2008 | 10.6 |
ТУ 1529-003-59119133-2007 | Приложение В |
МУ 102-142-51-2003 | 4.2 |
Примечание – Пользователям настоящей технологической инструкции целесообразно проверить действие ссылочных документов. Если ссылочный документ заменен (изменен), то при пользовании настоящей технологической инструкцией следует руководствоваться замененным (измененным) документом. Если ссылочный документ отменен без замены, то положение, в котором дана ссылка на него, применяется в части, не затрагивающей эту ссылку. |
Приложение Б
(справочное)
Технические характеристики оборудования
установок вакуумирования
|
|
История развития пистолетов-пулеметов: Предпосылкой для возникновения пистолетов-пулеметов послужила давняя тенденция тяготения винтовок...
Особенности сооружения опор в сложных условиях: Сооружение ВЛ в районах с суровыми климатическими и тяжелыми геологическими условиями...
Опора деревянной одностоечной и способы укрепление угловых опор: Опоры ВЛ - конструкции, предназначенные для поддерживания проводов на необходимой высоте над землей, водой...
Биохимия спиртового брожения: Основу технологии получения пива составляет спиртовое брожение, - при котором сахар превращается...
© cyberpedia.su 2017-2024 - Не является автором материалов. Исключительное право сохранено за автором текста.
Если вы не хотите, чтобы данный материал был у нас на сайте, перейдите по ссылке: Нарушение авторских прав. Мы поможем в написании вашей работы!