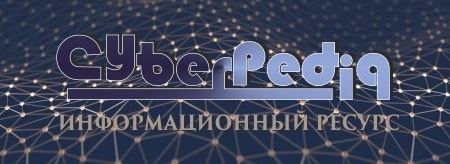
Поперечные профили набережных и береговой полосы: На городских территориях берегоукрепление проектируют с учетом технических и экономических требований, но особое значение придают эстетическим...
Историки об Елизавете Петровне: Елизавета попала между двумя встречными культурными течениями, воспитывалась среди новых европейских веяний и преданий...
Топ:
Характеристика АТП и сварочно-жестяницкого участка: Транспорт в настоящее время является одной из важнейших отраслей народного хозяйства...
Марксистская теория происхождения государства: По мнению Маркса и Энгельса, в основе развития общества, происходящих в нем изменений лежит...
Комплексной системы оценки состояния охраны труда на производственном объекте (КСОТ-П): Цели и задачи Комплексной системы оценки состояния охраны труда и определению факторов рисков по охране труда...
Интересное:
Инженерная защита территорий, зданий и сооружений от опасных геологических процессов: Изучение оползневых явлений, оценка устойчивости склонов и проектирование противооползневых сооружений — актуальнейшие задачи, стоящие перед отечественными...
Аура как энергетическое поле: многослойную ауру человека можно представить себе подобным...
Уполаживание и террасирование склонов: Если глубина оврага более 5 м необходимо устройство берм. Варианты использования оврагов для градостроительных целей...
Дисциплины:
![]() |
![]() |
5.00
из
|
Заказать работу |
![]() | ||||||||||||||
![]() | ||||||||||||||
![]() | ||||||||||||||
![]() | ||||||||||||||
![]() | ||||||||||||||
| ||||||||||||||
![]() | ||||||||||||||
| ||||||||||||||
![]() | ||||||||||||||
| ||||||||||||||
![]() | ||||||||||||||
| ||||||||||||||
![]() | ||||||||||||||
| ||||||||||||||
Расчёт моментов промежуточного вала
1 - е с е ч е н и е
Mx = 0 Н x мм
My = 0 Н x мм
M = = = 0 H x мм
2 - е с е ч е н и е
Mx = = = -228165,712 H x мм
My = = = -72025,499 H x мм
M = = = 239264,006 H x мм
3 - е с е ч е н и е
Mx = = = -154499,533 H x мм
My1 = = = -33243,2 H x мм
My2 = =
= = -556,163 H x мм
M1 = = = 158035,49 H x мм
M2 = = = 154500,534 H x мм
4 - е с е ч е н и е
Mx = 0 Н x мм
My = 0 Н x мм
M = = = 0 H x мм
Эпюры моментов промежуточного вала
![]() | ![]() | ||||
![]() | |||||
Расчёт моментов ведомого вала
1 - е с е ч е н и е
Mx = 0 Н x мм
My = 0 Н x мм
M = = = 0 H x мм
2 - е с е ч е н и е
Mx = 0 Н x мм
My = = = 825509,16 H x мм
M = = = 825509,16 H x мм
3 - е с е ч е н и е
Mx = = = 211925,982 H x мм
My = = = 383222,397 H x мм
M = = = 437917,832 H x мм
4 - е с е ч е н и е
Mx = 0 Н x мм
My = 0 Н x мм
M = = = 0 H x мм
Эпюры моментов ведомого вала
![]() | ![]() | ||||
![]() | |||||
Выбор и проверка долговечности подшипников
Ведущий вал
Выбираем шарикоподшипник радиальный однорядный (по ГОСТ 8338-75) 207 легкой серии со следующими параметрами:
d = 35 мм - диаметр вала (внутренний посадочный диаметр подшипника);
D = 72 мм - внешний диаметр подшипника;
C = 25,5 кН - динамическая грузоподъёмность;
Co = 13,7 кН - статическая грузоподъёмность.
Радиальные нагрузки на опоры:
Pr1 = 1254,016 H;
Pr2 = 496,098 H.
Будем проводить расчёт долговечности подшипника по наиболее нагруженной опоре 1.
Эквивалентная нагрузка вычисляется по формуле:
Рэ = (Х x V x Pr1 + Y x Pa) x Кб x Кт,
где - Pr1 = 1254,016 H - радиальная нагрузка; Pa = Fa = 280,175 H - осевая нагрузка; V = 1 (вращается внутреннее кольцо подшипника); коэффициент безопасности Кб = 1,1 (см. табл. 9.19[1]); температурный коэффициент Кт = 1 (см. табл. 9.20[1]).
Отношение 0,02; этой величине (по табл. 9.18[1]) соответствует e = 0,204.
Отношение 0,223 > e;£ e; тогда по табл. 9.18[1]: X = 0,56; Y = 2,157.
Тогда: Pэ = (0,56 x 1 x 1254,016 + 2,157 x 280,175) x 1,1 x 1 = 1437,295 H.
Расчётная долговечность, млн. об. (формула 9.1[1]):
L = = = 5584,481 млн. об.
Расчётная долговечность, ч.:
Lh = 64635,197 ч,
что больше 38263,68 ч, здесь n1 = 1440 об/мин - частота вращения вала.
Промежуточный вал
Выбираем шарикоподшипник радиальный однорядный (по ГОСТ 8338-75) 208 легкой серии со следующими параметрами:
d = 40 мм - диаметр вала (внутренний посадочный диаметр подшипника);
D = 80 мм - внешний диаметр подшипника;
C = 32 кН - динамическая грузоподъёмность;
Co = 17,8 кН - статическая грузоподъёмность.
Радиальные нагрузки на опоры:
Pr1 = 4125,241 H;
Pr2 = 2809,101 H.
Будем проводить расчёт долговечности подшипника по наиболее нагруженной опоре 1.
Эквивалентная нагрузка вычисляется по формуле:
Рэ = (Х x V x Pr1 + Y x Pa) x Кб x Кт,
где - Pr1 = 4125,241 H - радиальная нагрузка; Pa = Fa = 280,175 H - осевая нагрузка; V = 1 (вращается внутреннее кольцо подшипника); коэффициент безопасности Кб = 1,1 (см. табл. 9.19[1]); температурный коэффициент Кт = 1 (см. табл. 9.20[1]).
Отношение 0,016; этой величине (по табл. 9.18[1]) соответствует e = 0,194.
Отношение 0,068 £ e; тогда по табл. 9.18[1]: X = 1; Y = 0.
Тогда: Pэ = (1 x 1 x 4125,241 + 0 x 280,175) x 1,1 x 1 = 4537,765 H.
Расчётная долговечность, млн. об. (формула 9.1[1]):
L = = = 350,69 млн. об.
Расчётная долговечность, ч.:
Lh = 40294,56 ч,
что больше 38263,68 ч, здесь n2 = 288 об/мин - частота вращения вала.
Ведомый вал
Выбираем шарикоподшипник радиальный однорядный (по ГОСТ 8338-75) 212 легкой серии со следующими параметрами:
d = 60 мм - диаметр вала (внутренний посадочный диаметр подшипника);
D = 110 мм - внешний диаметр подшипника;
C = 52 кН - динамическая грузоподъёмность;
Co = 31 кН - статическая грузоподъёмность.
Радиальные нагрузки на опоры:
Pr1 = 10669,772 H;
Pr2 = 6635,119 H.
Будем проводить расчёт долговечности подшипника по наиболее нагруженной опоре 1.
Эквивалентная нагрузка вычисляется по формуле:
Рэ = (Х x V x Pr1 + Y x Pa) x Кб x Кт,
где - Pr1 = 10669,772 H - радиальная нагрузка; Pa = Fa = 0 H - осевая нагрузка; V = 1 (вращается внутреннее кольцо подшипника); коэффициент безопасности Кб = 1,1 (см. табл. 9.19[1]); температурный коэффициент Кт = 1 (см. табл. 9.20[1]).
Отношение 0; этой величине (по табл. 9.18[1]) соответствует e = 0.
Отношение 0 £ e; тогда по табл. 9.18[1]: X = 1; Y = 0.
Тогда: Pэ = (1 x 1 x 10669,772 + 0 x 0) x 1,1 x 1 = 11736,749 H.
Расчётная долговечность, млн. об. (формула 9.1[1]):
L = = = 86,969 млн. об.
Расчётная долговечность, ч.:
Lh = 40131,713 ч,
что больше 38263,68 ч, здесь n3 = 72 об/мин - частота вращения вала.
Уточненный расчёт валов
Расчёт ведущего вала
Крутящий момент на валу Tкр. = 38261,758 Hxмм.
Для данного вала выбран материал: сталь 45. Для этого материала:
- предел прочности sb = 780 МПа;
- предел выносливости стали при симметричном цикле изгиба
s-1 = 0,43 x sb = 0,43 x 780 = 335,4 МПа;
- предел выносливости стали при симметричном цикле кручения
t-1 = 0,58 x s-1 = 0,58 x 335,4 = 194,532 МПа.
1 - е с е ч е н и е.
Диаметры вала в данном сечении D = 38 мм и d = 35 мм, радиус скругления r = 1,4 мм. Концентрация напряжений обусловлена галтелью (см. табл. 8.2[1]). Проверку будем проводить по 2-му сечению, где наибольший изгибающий момент.
Коэффициент запаса прочности по нормальным напряжениям:
Ss =
- амплитуда цикла нормальных напряжений:
sv = 13,704 МПа,
здесь
Wнетто = 4209,243 мм3- среднее напряжение цикла нормальных напряжений:
sm = 0,291 МПа, Fa = -280,175 МПа - продольная сила,
- ys = 0,2 - см. стр. 164[1];
- b = 0.97 - коэффициент, учитывающий шероховатость поверхности, см. стр. 162[1];
- ks = 1,75
- es = 0,88 - находим по таблице 8.8[1];
Тогда:
Ss = 11,913.
Коэффициент запаса прочности по касательным напряжениям:
St =
- амплитуда и среднее напряжение отнулевого цикла:
tv = tm = 0,5 x 2,272 МПа,
здесь
Wк нетто = 8418,487 мм3
- yt = 0.1 - см. стр. 166[1];
- b = 0.97 - коэффициент, учитывающий шероховатость поверхности, см. стр. 162[1].
- kt = 1,27
- et = 0,77 - находим по таблице 8.8[1];
Тогда:
St = 47,558.
Результирующий коэффициент запаса прочности:
S = = = 11,556
Расчётное значение получилось больше минимально допустимого [S] = 2,5. Сечение проходит по прочности.
2 - е с е ч е н и е.
Диаметры вала в данном сечении D = 38 мм и d = 35 мм, радиус скругления r = 1,4 мм. Концентрация напряжений обусловлена галтелью (см. табл. 8.2[1]). Проверку будем проводить по 3-му сечению, где наибольший изгибающий момент.
Коэффициент запаса прочности по нормальным напряжениям:
Ss =
- амплитуда цикла нормальных напряжений:
sv = 13,704 МПа,
здесь
Wнетто = 4209,243 мм3- среднее напряжение цикла нормальных напряжений:
sm = 0,291 МПа, Fa = -280,175 МПа - продольная сила,
- ys = 0,2 - см. стр. 164[1];
- b = 0.97 - коэффициент, учитывающий шероховатость поверхности, см. стр. 162[1];
- ks = 1,75
- es = 0,88 - находим по таблице 8.8[1];
Тогда:
Ss = 11,913.
Коэффициент запаса прочности по касательным напряжениям:
St =
- амплитуда и среднее напряжение отнулевого цикла:
tv = tm = 0,5 x 2,272 МПа,
здесь
Wк нетто = 8418,487 мм3
- yt = 0.1 - см. стр. 166[1];
- b = 0.97 - коэффициент, учитывающий шероховатость поверхности, см. стр. 162[1].
- kt = 1,27
- et = 0,77 - находим по таблице 8.8[1];
Тогда:
St = 47,558.
Результирующий коэффициент запаса прочности:
S = = = 11,556
Расчётное значение получилось больше минимально допустимого [S] = 2,5. Сечение проходит по прочности.
Расчёт промежуточного вала
Крутящий момент на валу Tкр. = 183715,044 Hxмм.
Для данного вала выбран материал: сталь 45. Для этого материала:
- предел прочности sb = 780 МПа;
- предел выносливости стали при симметричном цикле изгиба
s-1 = 0,43 x sb = 0,43 x 780 = 335,4 МПа;
- предел выносливости стали при симметричном цикле кручения
t-1 = 0,58 x s-1 = 0,58 x 335,4 = 194,532 МПа.
2 - е с е ч е н и е.
Диаметр вала в данном сечении D = 42 мм. Концентрация напряжений обусловлена наличием шпоночной канавки. Ширина шпоночной канавки b = 12 мм, глубина шпоночной канавки t1 = 5 мм.
Коэффициент запаса прочности по нормальным напряжениям:
Ss =
- амплитуда цикла нормальных напряжений:
sv = 38,004 МПа,
здесь
Wнетто = 6295,715 мм3,
где b=12 мм - ширина шпоночного паза; t1=5 мм - глубина шпоночного паза;
- среднее напряжение цикла нормальных напряжений:
sm = 0,202 МПа, Fa = 280,175 МПа - продольная сила,
- ys = 0,2 - см. стр. 164[1];
- b = 0.97 - коэффициент, учитывающий шероховатость поверхности, см. стр. 162[1];
- ks = 1,8 - находим по таблице 8.5[1];
- es = 0,85 - находим по таблице 8.8[1];
Тогда:
Ss = 4,041.
Коэффициент запаса прочности по касательным напряжениям:
St = где:
- амплитуда и среднее напряжение отнулевого цикла:
tv = tm = 6,77 МПа,
здесь
Wк нетто = 13569,288 мм3,
где b=12 мм - ширина шпоночного паза; t1=5 мм - глубина шпоночного паза;
- yt = 0.1 - см. стр. 166[1];
- b = 0.97 - коэффициент, учитывающий шероховатость поверхности, см. стр. 162[1].
- kt = 1,7 - находим по таблице 8.5[1];
- et = 0,73 - находим по таблице 8.8[1];
Тогда:
St = 11,49.
Результирующий коэффициент запаса прочности:
S = = = 3,812
Расчётное значение получилось больше минимально допустимого [S] = 2,5. Сечение проходит по прочности.
3 - е с е ч е н и е.
Диаметр вала в данном сечении D = 42 мм. Концентрация напряжений обусловлена посадкой ведомого элемента передачи с гарантированным натягом (см. табл. 8.7[1]).
Коэффициент запаса прочности по нормальным напряжениям:
Ss =
- амплитуда цикла нормальных напряжений:
sv = 21,727 МПа,
здесь
Wнетто = 7273,572 мм3
- среднее напряжение цикла нормальных напряжений:
sm = 0,202 МПа, Fa = 280,175 МПа - продольная сила,
- ys = 0,2 - см. стр. 164[1];
- b = 0.97 - коэффициент, учитывающий шероховатость поверхности, см. стр. 162[1];
- s = 3,65 - находим по таблице 8.7[1];
Тогда:
Ss = 4,1.
Коэффициент запаса прочности по касательным напряжениям:
St = где:
- амплитуда и среднее напряжение отнулевого цикла:
tv = tm = 6,314 МПа,
здесь
Wк нетто = 14547,145 мм3
- yt = 0.1 - см. стр. 166[1];
- b = 0.97 - коэффициент, учитывающий шероховатость поверхности, см. стр. 162[1].
- = 2,59 - находим по таблице 8.7[1];
Тогда:
St = 11,122.
Результирующий коэффициент запаса прочности:
S = = = 3,847
Расчётное значение получилось больше минимально допустимого [S] = 2,5. Сечение проходит по прочности.
1 - е с е ч е н и е.
Диаметры вала в данном сечении D = 42 мм и d = 40 мм, радиус скругления r = 1,6 мм. Концентрация напряжений обусловлена галтелью (см. табл. 8.2[1]). Проверку будем проводить по 2-му сечению, где наибольший изгибающий момент.
Коэффициент запаса прочности по нормальным напряжениям:
Ss =
- амплитуда цикла нормальных напряжений:
sv = 38,08 МПа,
здесь
Wнетто = 6283,185 мм3- среднее напряжение цикла нормальных напряжений:
sm = 0,223 МПа, Fa = 280,175 МПа - продольная сила,
- ys = 0,2 - см. стр. 164[1];
- b = 0.97 - коэффициент, учитывающий шероховатость поверхности, см. стр. 162[1];
- ks = 1,75
- es = 0,88 - находим по таблице 8.8[1];
Тогда:
Ss = 4,294.
Коэффициент запаса прочности по касательным напряжениям:
St =
- амплитуда и среднее напряжение отнулевого цикла:
tv = tm = 0,5 x 7,31 МПа,
здесь
Wк нетто = 12566,371 мм3
- yt = 0.1 - см. стр. 166[1];
- b = 0.97 - коэффициент, учитывающий шероховатость поверхности, см. стр. 162[1].
- kt = 1,27
- et = 0,77 - находим по таблице 8.8[1];
Тогда:
St = 14,781.
Результирующий коэффициент запаса прочности:
S = = = 4,124
Расчётное значение получилось больше минимально допустимого [S] = 2,5. Сечение проходит по прочности.
3 - е с е ч е н и е.
Диаметры вала в данном сечении D = 42 мм и d = 40 мм, радиус скругления r = 1,6 мм. Концентрация напряжений обусловлена галтелью (см. табл. 8.2[1]). Проверку будем проводить по 4-му сечению, где наибольший изгибающий момент.
Коэффициент запаса прочности по нормальным напряжениям:
Ss =
- амплитуда цикла нормальных напряжений:
sv = 25,152 МПа,
здесь
Wнетто = 6283,185 мм3- среднее напряжение цикла нормальных напряжений:
sm = 0,223 МПа, Fa = 280,175 МПа - продольная сила,
- ys = 0,2 - см. стр. 164[1];
- b = 0.97 - коэффициент, учитывающий шероховатость поверхности, см. стр. 162[1];
- ks = 1,75
- es = 0,88 - находим по таблице 8.8[1];
Тогда:
Ss = 6,499.
Коэффициент запаса прочности по касательным напряжениям:
St =
- амплитуда и среднее напряжение отнулевого цикла:
tv = tm = 0,5 x 7,31 МПа,
здесь
Wк нетто = 12566,371 мм3
- yt = 0.1 - см. стр. 166[1];
- b = 0.97 - коэффициент, учитывающий шероховатость поверхности, см. стр. 162[1].
- kt = 1,27
- et = 0,77 - находим по таблице 8.8[1];
Тогда:
St = 14,781.
Результирующий коэффициент запаса прочности:
S = = = 5,949
Расчётное значение получилось больше минимально допустимого [S] = 2,5. Сечение проходит по прочности.
Расчёт ведомого вала
Крутящий момент на валу Tкр. = 705662,865 Hxмм.
Для данного вала выбран материал: сталь 45. Для этого материала:
- предел прочности sb = 780 МПа;
- предел выносливости стали при симметричном цикле изгиба
s-1 = 0,43 x sb = 0,43 x 780 = 335,4 МПа;
- предел выносливости стали при симметричном цикле кручения
t-1 = 0,58 x s-1 = 0,58 x 335,4 = 194,532 МПа.
2 - е с е ч е н и е.
Диаметр вала в данном сечении D = 60 мм. Концентрация напряжений обусловлена посадкой подшипника с гарантированным натягом (см. табл. 8.7[1]).
Коэффициент запаса прочности по нормальным напряжениям:
Ss =
- амплитуда цикла нормальных напряжений:
sv = 38,929 МПа,
здесь
Wнетто = 21205,75 мм3
- среднее напряжение цикла нормальных напряжений:
sm = 0 МПа, Fa = 0 МПа - продольная сила,
- ys = 0,2 - см. стр. 164[1];
- b = 0.97 - коэффициент, учитывающий шероховатость поверхности, см. стр. 162[1];
- s = 3,102 - находим по таблице 8.7[1];
Тогда:
Ss = 2,694.
Коэффициент запаса прочности по касательным напряжениям:
St = где:
- амплитуда и среднее напряжение отнулевого цикла:
tv = tm = 8,319 МПа,
здесь
Wк нетто = 42411,501 мм3
- yt = 0.1 - см. стр. 166[1];
- b = 0.97 - коэффициент, учитывающий шероховатость поверхности, см. стр. 162[1].
- = 2,202 - находим по таблице 8.7[1];
Тогда:
St = 9,866.
Результирующий коэффициент запаса прочности:
S = = = 2,599
Расчётное значение получилось больше минимально допустимого [S] = 2,5. Сечение проходит по прочности.
3 - е с е ч е н и е.
Диаметр вала в данном сечении D = 65 мм. Концентрация напряжений обусловлена наличием двух шпоночных канавок. Ширина шпоночной канавки b = 18 мм, глубина шпоночной канавки t1 = 7 мм.
Коэффициент запаса прочности по нормальным напряжениям:
Ss =
- амплитуда цикла нормальных напряжений:
sv = 21,424 МПа,
здесь
Wнетто = 20440,262 мм3,
где b=18 мм - ширина шпоночного паза; t1=7 мм - глубина шпоночного паза;
- среднее напряжение цикла нормальных напряжений:
sm = 0 МПа, Fa = 0 МПа - продольная сила,
- ys = 0,2 - см. стр. 164[1];
- b = 0.97 - коэффициент, учитывающий шероховатость поверхности, см. стр. 162[1];
- ks = 1,8 - находим по таблице 8.5[1];
- es = 0,82 - находим по таблице 8.8[1];
Тогда:
Ss = 6,918.
Коэффициент запаса прочности по касательным напряжениям:
St = где:
- амплитуда и среднее напряжение отнулевого цикла:
tv = tm = 7,443 МПа,
здесь
Wк нетто = 47401,508 мм3,
где b=18 мм - ширина шпоночного паза; t1=7 мм - глубина шпоночного паза;
- yt = 0.1 - см. стр. 166[1];
- b = 0.97 - коэффициент, учитывающий шероховатость поверхности, см. стр. 162[1].
- kt = 1,7 - находим по таблице 8.5[1];
- et = 0,7 - находим по таблице 8.8[1];
Тогда:
St = 10,038.
Результирующий коэффициент запаса прочности:
S = = = 5,696
Расчётное значение получилось больше минимально допустимого [S] = 2,5. Сечение проходит по прочности.
2 - е с е ч е н и е.
Диаметры вала в данном сечении D = 65 мм и d = 60 мм, радиус скругления r = 2,4 мм. Концентрация напряжений обусловлена галтелью (см. табл. 8.2[1]). Проверку будем проводить по 3-му сечению, где наибольший изгибающий момент.
Коэффициент запаса прочности по нормальным напряжениям:
Ss =
- амплитуда цикла нормальных напряжений:
sv = 38,929 МПа,
здесь
Wнетто = 21205,75 мм3- среднее напряжение цикла нормальных напряжений:
sm = 0 МПа, Fa = 0 МПа - продольная сила,
- ys = 0,2 - см. стр. 164[1];
- b = 0.97 - коэффициент, учитывающий шероховатость поверхности, см. стр. 162[1];
- ks = 1,75
- es = 0,82 - находим по таблице 8.8[1];
Тогда:
Ss = 3,916.
Коэффициент запаса прочности по касательным напряжениям:
St =
- амплитуда и среднее напряжение отнулевого цикла:
tv = tm = 0,5 x 8,319 МПа,
здесь
Wк нетто = 42411,501 мм3
- yt = 0.1 - см. стр. 166[1];
- b = 0.97 - коэффициент, учитывающий шероховатость поверхности, см. стр. 162[1].
- kt = 1,27
- et = 0,7 - находим по таблице 8.8[1];
Тогда:
St = 11,868.
Результирующий коэффициент запаса прочности:
S = = = 3,719
Расчётное значение получилось больше минимально допустимого [S] = 2,5. Сечение проходит по прочности.
3 - е с е ч е н и е.
Диаметры вала в данном сечении D = 65 мм и d = 60 мм, радиус скругления r = 2,4 мм. Концентрация напряжений обусловлена галтелью (см. табл. 8.2[1]). Проверку будем проводить по 4-му сечению, где наибольший изгибающий момент.
Коэффициент запаса прочности по нормальным напряжениям:
Ss =
- амплитуда цикла нормальных напряжений:
sv = 20,651 МПа,
здесь
Wнетто = 21205,75 мм3- среднее напряжение цикла нормальных напряжений:
sm = 0 МПа, Fa = 0 МПа - продольная сила,
- ys = 0,2 - см. стр. 164[1];
- b = 0.97 - коэффициент, учитывающий шероховатость поверхности, см. стр. 162[1];
- ks = 1,75
- es = 0,82 - находим по таблице 8.8[1];
Тогда:
Ss = 7,382.
Коэффициент запаса прочности по касательным напряжениям:
St =
- амплитуда и среднее напряжение отнулевого цикла:
tv = tm = 0,5 x 8,319 МПа,
здесь
Wк нетто = 42411,501 мм3
- yt = 0.1 - см. стр. 166[1];
- b = 0.97 - коэффициент, учитывающий шероховатость поверхности, см. стр. 162[1].
- kt = 1,27
- et = 0,7 - находим по таблице 8.8[1];
Тогда:
St = 11,868.
Результирующий коэффициент запаса прочности:
S = = = 6,268
Расчётное значение получилось больше минимально допустимого [S] = 2,5. Сечение проходит по прочности.
Выбор сорта масла
Смазывание элементов передач редуктора производится окунанием нижних элементов в масло, заливаемое внутрь корпуса до уровня, обеспечивающего погружение элемента передачи примерно на 10-20 мм. Объём масляной ванны V определяется из расчёта 0,25 дм3 масла на 1 кВт передаваемой мощности:
V = 0,25 x 5,828 = 1,457 дм3.
По таблице 10.8[1] устанавливаем вязкость масла. При контактных напряжениях sH = 604,474 МПа и скорости v = 1,086 м/с рекомендуемая вязкость масла должна быть примерно равна 60 x 10-6 м/с2. По таблице 10.10[1] принимаем масло индустриальное И-50А (по ГОСТ 20799-75*).
Выбираем для подшипников качения пластичную смазку УТ-1 по ГОСТ 1957-73 (см. табл. 9.14[1]). Камеры подшипиков заполняются данной смазкой и периодически пополняются ей.
Заключение
При выполнении курсового проекта по “Деталям машин” были закреплены знания, полученные за прошедший период обучения в таких дисциплинах как: теоретическая механика, сопротивление материалов, материаловедение.
Целью данного проекта является проектирование привода цепного конвейера, который состоит как из простых стандартных деталей, так и из деталей, форма и размеры которых определяются на основе конструкторских, технологических, экономических и других нормативов.
В ходе решения поставленной передо мной задачей, была освоена методика выбора элементов привода, получены навыки проектирования, позволяющие обеспечить необходимый технический уровень, надежность и долгий срок службы механизма.
Опыт и навыки, полученные в ходе выполнения курсового проекта, будут востребованы при выполнении, как курсовых проектов, так и дипломного проекта.
Можно отметить, что спроектированный редуктор обладает хорошими свойствами по всем показателям.
По результатам расчета на контактную выносливость действующие напряжения в зацеплении меньше допускаемых напряжений.
По результатам расчета по напряжениям изгиба действующие напряжения изгиба меньше допускаемых напряжений.
Расчет вала показал, что запас прочности больше допускаемого.
Необходимая динамическая грузоподъемность подшипников качения меньше паспортной.
При расчете был выбран электродвигатель, который удовлетворяет заданные требования.
Список использованной литературы
1. Чернавский С.А., Боков К.Н., Чернин И.М., Ицкевич Г.М., Козинцов В.П. 'Курсовое проектирование деталей машин': Учебное пособие для учащихся. М.:Машиностроение, 1988 г., 416с.
2. Дунаев П.Ф., Леликов О.П. 'Конструирование узлов и деталей машин', М.: Издательский центр 'Академия', 2003 г., 496 c.
3. Шейнблит А.Е. 'Курсовое проектирование деталей машин': Учебное пособие, изд. 2-е перераб. и доп. - Калининград: 'Янтарный сказ', 2004 г., 454 c.: ил., черт. - Б.ц.
Автоматическое растормаживание колес: Тормозные устройства колес предназначены для уменьшения длины пробега и улучшения маневрирования ВС при...
Адаптации растений и животных к жизни в горах: Большое значение для жизни организмов в горах имеют степень расчленения, крутизна и экспозиционные различия склонов...
История создания датчика движения: Первый прибор для обнаружения движения был изобретен немецким физиком Генрихом Герцем...
Наброски и зарисовки растений, плодов, цветов: Освоить конструктивное построение структуры дерева через зарисовки отдельных деревьев, группы деревьев...
© cyberpedia.su 2017-2024 - Не является автором материалов. Исключительное право сохранено за автором текста.
Если вы не хотите, чтобы данный материал был у нас на сайте, перейдите по ссылке: Нарушение авторских прав. Мы поможем в написании вашей работы!