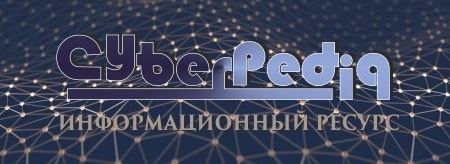
Типы оградительных сооружений в морском порту: По расположению оградительных сооружений в плане различают волноломы, обе оконечности...
Индивидуальные и групповые автопоилки: для животных. Схемы и конструкции...
Топ:
Техника безопасности при работе на пароконвектомате: К обслуживанию пароконвектомата допускаются лица, прошедшие технический минимум по эксплуатации оборудования...
Когда производится ограждение поезда, остановившегося на перегоне: Во всех случаях немедленно должно быть ограждено место препятствия для движения поездов на смежном пути двухпутного...
Интересное:
Подходы к решению темы фильма: Существует три основных типа исторического фильма, имеющих между собой много общего...
Аура как энергетическое поле: многослойную ауру человека можно представить себе подобным...
Средства для ингаляционного наркоза: Наркоз наступает в результате вдыхания (ингаляции) средств, которое осуществляют или с помощью маски...
Дисциплины:
![]() |
![]() |
5.00
из
|
Заказать работу |
|
|
Аннотация
В данном курсовом проекте освещены теоретические основы процесса гидрогенизации, выполнено проектирование установки гидроочистки вакуумного дистиллята смеси Арыскумской нефти производительностью 6,2 млн. т/г (в том числе, произведены технологический и механический расчеты основного аппарата). В ходе выполнения проекта, были изучены типичные технологическая и поточная схема процесса гидроочистки, составлены материальные балансы установок, применяющихся при проведении процесса.
Настоящий курсовой проект состоит из пояснительной записки.
Пояснительная записка включает 40 страницы, 2 рисунок и 12 таблицы.
Нормативные ссылки
В настоящем курсовом проекте использованы ссылки на следующие документы:
ГОСТ 5426-65 Нефтепереработка. Процессы Переработки.
ГОСТ 2111-2014 Топлива. Нефтяные скважины.
ГОСТ 1012-2013 Бензины авиационные.
ГОСТ 2084-77 Бензины автомобильные.
ГОСТ 11851-85 Нефть. Метод определения парафина.
ГОСТ 2177-99 Нефтепродукты. Метод определения фракционного состава.
ГОСТ 1233-2006 Процесс гидроочистки.
ГОСТ 1002-2008 Гидрокрекинг.
ГОСТ 1996-77 Бензины автомобильные.
ГОСТ 12р12-86 Гидрогенизационные процессы.
ГОСТ 1313-98 Исследование процесса гидроочистки
ГОСТ 1809-1989 Высокооктановые бензины.
ГОСТ 1006-1999 Гидрооблагораживание.
Определения
В настоящем курсовом проекте применяют следующие термины с соответствующими определениями:
Катализатор – химическое вещество, ускоряющее реакцию, но не расходующееся в процессе реакции.
Крекинг – процесс переработки нефти и входящих в её состав фракций, существенно увеличивающий выход светлых нефтепродуктов. Крекинг бывает термическим (под влиянием высокой температуры) и каталитическим (с использованием катализатора).
|
Гидроочистка – процесс химического превращения веществ под воздействием водорода при высоком давлении и температуре. Гидроочистка нефтяных фракций направлена на снижение содержания сернистых соединений в товарных нефтепродуктах. Побочно происходит насыщение непредельных углеводородов, снижение содержания смол, кислородсодержащих соединений, а также гидрокрекинг молекул углеводородов.
Гидрокрекинг – это один из видов крекинга, переработка высококипящих нефтяных фракций, мазута, вакуумного газойля или деасфальтизата для получения бензина, дизельного и реактивного топлива, смазочных масел, сырья для каталитического крекинга и другого.
Вакуумные дистилляты (газойли) – являются сырьем для процессов каталитического крекинга, гидрокрекинга, получения электродного кокса. Для повышения выхода и улучшения качества продуктов, полученных указанными процессами, и с целью уменьшения загрязнения окружающей среды оксидами серы все большая доля вырабатываемых вакуумных газойлей подвергается гидроочистке. Эффективность процесса гидроочистки вакуумного газойля во многом определяется качеством исходного сырья и требованиями к качеству продуктов для последующих процессов.
Обозначения и сокращения
ρc–плотность сырья, керосино-газойлевой фракции;
ρ420– плотность нефти или нефтепродуктов при 200С
ВОК-высокооктановые компоненты;
ВСГ-водородсодержащий газ;
ИВ-индекс вязкости;
КР, КРб – каталитический риформинг, риформинг «на бензин»;
ОЧ-октановое число;
ЭЛОУ-электрообессоливающая и электрообезвоживающая установка.
Содержание
Аннотация | |
Нормативные ссылки | |
Определения | |
Обозначения и сокращения | |
1 Введение | |
2 Аналитический обзор по теме | |
3 Физико-химические характеристики данной нефти | |
4 Описание поточной схемы переработки нефти | |
5 Материальный баланс переработки нефти по потенциальным содержанием фракций | |
6 Описание технологической схемы проектируемой установки | |
7 Материальный баланс проектируемой установки | |
8 Технологические расчеты основных аппаратов установки | |
9 Общие выводы | |
10 Приложение | |
11 Список использованных источников |
|
Введение
Актуальность работы. В последние 5-10 лет актуальность процессов гидроочистки в связи с необходимостью улучшения качества и увеличения выпуска нефтепродуктов значительно возросла. Это определяется двумя главными тенденциями современной нефтепереработки: увеличением глубины их переработки и ужесточением экологических норм. Первая тенденция из-за вовлечения в переработку и, следовательно, в гидроочистку все более тяжелого нефтяного сырья с большим содержанием серы, азота, металлов, смол и асфальтенов приводит к ужесточению технологического режима и требует создания более устойчивых катализаторов. При сгорании сернистых топлив образуются оксиды серы SO и SO2, которые в зоне пониженных температур вместе с конденсирующимися парами воды образуют сернистую и серную кислоты и оказывают сильное корродирующее действие на металл двигателя. Борьбу с сернистой коррозией ведут способами: во-первых, применением присадок к топливам и маслам, нейтрализующих агрессивное действие продуктов сгорания серы; во-вторых, очисткой топлив от сернистых соединений; в-третьих, для поршневых двигателей, применением устойчивых против коррозии металлов для гильз цилиндров и поршневых колец [1].
Вторая тенденция превращает процессы гидроочистки из вспомогательных в основные, определяющие качество и потребительские свойства моторных и энергетических топлив. Здесь требуется более тонкая очистка от серы и азота, частичное гидрирование ароматических соединений, легкий гидрокрекинг нормальных парафинов, переработка вторичных дистиллятов, содержащих непредельные соединения и т.п. Совместное действие этих двух тенденций выдвигает процессы гидроочистки в ряд важнейших каталитических процессов, занимающих к тому же одно из первых мест в мире по суммарной мощности перерабатываемого сырья и мощности единичных агрегатов.
Научная новизна. Внедрение любого промышленного химико-технологического процесса можно разделить на три этапа:
|
1. Разработку и исследование в лаборатории;
2. Создание укрупненных опытных установок и проектирование промышленной установки;
3. Осуществление процесса в промышленных условиях.
Задачи изучения процесса на каждом из этих этапов различны. При разработке и исследовании в лаборатории нужно подобрать наилучшие условия осуществления процесса, после чего можно оценить его технико-экономическую эффективность и исследовать физико-химические закономерности. На втором этапе необходимо обеспечить создание наиболее эффективной промышленной установки при наименьшем числе переходных стадий — опытных установок. Промышленная эксплуатация требует периодического или непрерывного изменения характеристик процесса для оптимизации по выбранному критерию (выход продукта, прибыль, себестоимость и т. п.). Эти задачи до последних лет решались исследователем или инженером на основе собственных знаний, опыта и интуиции.
Все сказанное справедливо для любого химико-технологического процесса, но наиболее существенно для крупнотоннажных производств нефтеперерабатывающей и нефтехимической промышленности — одной из наиболее важных отраслей народного хозяйства. Применение научных методов разработки, внедрения и осуществления этих процессов позволяет получить надежные данные, сократить срок разработки и исследования, уменьшить число стадий (опытных установок) при реализации лабораторного процесса, наиболее эффективно проектировать промышленные установки, вести промышленный процесс в оптимальных условиях т.е. на каждом этапе достигать существенной экономии времени и средств. Поэтому — умение пользоваться современными методами исследования и моделирования необходимо как научному работнику, разрабатывающему процесс, так и инженеру, проектирующему или эксплуатирующему его.
Проблема очистки топлив от серы технически решена. Разработано несколько технологических процессов, обеспечивающих в той или иной степени удаление серы из топлив. К таким процессам относятся: очистка топлив серной кислотой, селективными растворителями, адсорбентами, гидроочистка и др [2].
|
Цель работы. Наиболее эффективные результаты обессеривания получаются при легком гидрировании сернистых продуктов, т.е. при гидроочистке. Под гидроочисткой понимается процесс присоединения водорода к органическим веществам без изменения их углеводородного скелета.
Основными целями данного курсового проекта являются:
• Обобщить и систематизировать теоритический материал по установке гидроочистки.
• Изучить принципиальную схему установки, принцип работы.
• Изучить основные параметры процесса.
• Сделать расчеты материального баланса и механические расчеты реактора гидроочистки.
Расчет материального баланса нефтеперерабатывающего завода в целом и отдельных его установок в частности для различных нефтей и при разной производительности позволяет оценить целесообразность применения того или иного сырья для получения целевых продуктов, а также рассчитать экономическую эффективность данного производства.
Аналитический обзор по теме
2.1 Гидроочистка вакуумных дистиллятов. Вакуумные дистилляты являются сырьем для процессов каталитического крекинга и гидрокрекинга. Качество вакуумных газойлей определяется глубиной отбора и четкостью ректификации мазута. Вакуумные газойли 350—500°С практически не содержат металлорганических соединений и асфальтенов, а их коксуемость не превышает обычно 0,2 %. С повышением tKK до 540 - 560 °С коксуемость возрастает в 4-10 раз, содержание металлов - в 3-4 раза, серы - на 20-45 %. Влияние содержащихся в сырье металлов, азотистых соединений и серы проявляется в снижении активности работы катализатора за счет отложения кокса и необратимого отравления металлами.
Гидроочистка вакуумного газойля 350 -500°С не представляет значительных трудностей и проводится в условиях и на оборудовании, аналогичных для гидроочистки дизельных топлив. При давлении 4-5 МПа, температуре 360-410 °С и объемной скорости сырья 1-1.5 ч-1достигается 89-94%- ная глубина обессеривания; содержание азота снижается на 20—30%, металлов - на 75 - 85 %, а коксуемость — на 65 - 70 %. Универсальным способом облагораживания сырья каталитического крекинга является процесс гидроочистки. Применение гидроочистки вакуумных дистиллятов позволяет повысить качество и выход светлых продуктов, в основном, бензина, а также существенно уменьшить образование кокса и содержание SO в дымовых газах регенератора, что имеет большое экологическое значение. Наибольший эффект достигается при гидрировании сырья с высоким содержанием серы, азота, ароматических углеводородов, коксообразующих компонентов и металлоорганических соединений: например, при гидроочистке высокосернистых газойлей. В результате гидроочистки сырья с высоким содержанием азот- и металлоорганических соединений стабильность работы катализатора крекинга значительно возрастает. В обычных условиях гидроочистки вакуумных дистиллятов западносибирской нефти (давление до 5 МПа, температура 350-400 °С, объемная скорость подачи сырья 1,0-2,2 час-1) среднее уменьшение вредных компонентов составляет в % масс.: серы – 60-80, азота – 15-25, кокса (по Конрадсону) – 40-50, тяжелых металлов – 60-70, ароматических углеводородов – 10- 20.
|
Процессы переработки нефтяных фракций в присутствии водорода называются гидрогенизационными [3]. Они протекают на поверхности гидрирующих катализаторов в присутствии водорода при высоких значениях температуры (250-420 °С) и давления (от 2,5-3,0 вплоть до 32 МПа). Такие процессы используются для регулирования углеводородного и фракционного состава перерабатываемых нефтяных фракций, очистки их от серо-, азот- и кислородсодержащих соединений, металлов и других нежелательных примесей, улучшения эксплуатационных (потребительских) характеристик нефтяных топлив, масел и сырья нефтехимии. Гидрокрекинг позволяет получать широкий ассортимент нефтепродуктов практически из любого нефтяного сырья путем подбора соответствующих катализаторов и рабочих условий, поэтому он является наиболее универсальным, эффективным и гибким процессом нефтепереработки. Разделение гидрогенизационных процессов на гидрокрекинг и гидроочистку довольно условно по принципу свойств применяемых катализаторов, количества используемого водорода и технологических параметров процесса (давление, температура и др.).
Например, принята следующая терминология: «гидроочистка» (Hydro-treating), «гидрооблагораживание» (Hydrorefining) и «гидрокрекинг» (Hydrocracking). Гидроочистка включает процессы, в которых не происходит существенного изменения в молекулярной структуре сырья (например, сероочистка при давлении 3-5 МПа). Гидрооблагораживание включает процессы, в которых до 10 % сырья подвергается изменению молекулярной структуры (сероочистка - деароматизация - деазотизация при давлении 6-12 МПа). Гидрокрекинг - это процессы (высокого давления - более 10 МПа и среднего давления - менее 10 МПа), в которых более 50 % сырья подвергается деструкции с уменьшением размера молекул. В 80-х годах XX в. процессы гидрооблагораживания с конверсией менее 50 % получили название мягкого или легкого гидрокрекинга, к которому стали относить промежуточные процессы с гидродеструкцией сырья от 10 до 50 % при давлениях как менее, так и более 10 МПа. Мощности установок (млн т/год) гидрокрекинга в мире равны примерно 230, а гидроочистки и гидрооблагораживания - 1380, из них в Северной Америке - соответственно 90 и 420; в Западной Европе - 50 и 320; в России и СНГ - 3 и 100.
История развития промышленных гидрогенизационных процессов начиналась с гидрогенизации продуктов ожижения угля. Еще до Второй мировой войны Германия достигла больших успехов в производстве синтетического бензина (синтина) при гидрогенизационной переработке углей (на основе применения синтеза Фишера-Тропша), а в годы Второй мировой войны Германия производила более 600 тыс. т/год синтетических жидких топлив, что покрывало большую часть потребления страны. В настоящее время мировое производство искусственного жидкого топлива на основе угля составляет около 4,5 млн т/год. После широкого промышленного внедрения каталитического риформинга, производящего в качестве побочного продукта избыточный дешевый водород, наступает период массового распространения различных процессов гидроочистки сырьевых нефтяных фракций (кстати, необходимой и для процессов риформинга) и товарной продукции НПЗ (бензиновые, керосиновые, дизельные и масляные фракции).
Гидрокрекинг (ГК) позволяет получать светлые нефтепродукты (бензиновые, керосиновые, дизельные фракции и сжиженные газы С3-С4) практически из любого нефтяного сырья подбором соответствующих катализаторов и технологического режима процесса. Иногда термин «гидроконверсия» (Hydroconversion) используется как синоним термина гидрокрекинг (Hydrocracking). Первая установка ГК пущена в 1959 г. в США. Большинство процессов ГК предусматривает переработку дистиллятного сырья: тяжелых атмосферных и вакуумных газойлей, газойлей каталитического крекинга и коксования, а также и деасфальтизаторов. Получаемые продукты - это предельные (насыщенные) углеводородные газы, высокооктановая бензиновая фракция, низкозастывающие фракции дизельного и реактивного топлив. Гидрокрекинг сырья, содержащего значительные количества соединений на основе серы, азота, кислорода и других элементов, обычно проводят в две ступени. На первой ступени осуществляется неглубокий мягкий гидрокрекинг в режиме гидроочистки от нежелательных примесей, обычно являющихся катализаторными ядами или снижающих их активность [4]. Катализаторы этой ступени идентичны катализаторам обычной гидроочистки и содержат оксиды и сульфиды никеля, кобальта, молибдена и вольфрама на разных носителях - активном оксиде алюминия, алюмосиликате или специальных цеолитах. На второй ступени подготовленное, очищенное сырье, содержащее не более 0,01 % серы и не более 0,0001 % азота, подвергается основному жесткому гидрокрекингу на катализаторах на основе палладия или платины на носителе - цеолитах типа Y. Гидрокрекинг тяжелых газойлевых фракций применяется для получения бензина, реактивного и дизельного топлива, а также для повышения качества масел, котельного топлива и сырья пиролиза и каталитического крекинга. Гидрокрекинг малосернистых вакуумных дистиллятов в бензин осуществляют в одну ступень на сульфидных катализаторах, стойких к отравлению гетероорганическими соединениями, при температуре 340-420 °С и давлении 10-20 МПа с выходом бензина 30-40 % и вплоть до 80-90 об. %. Если сырье содержит более 1,5 % серы и 0,003-0,015 % азота, то применяется двухступенчатый процесс с гидроочисткой сырья на первой ступени. Гидрокрекинг во второй ступени протекает при температуре 290-380 °С и давлении 7-10 МПа. Выход бензина достигает 70-120 об. % на сырье, получаемый легкий бензин до 190 °С используют как высокооктановый компонент товарных бензинов, тяжелый бензин можно направлять на риформинг. Гидрокрекинг тяжелых газойлей в средние фракции (реактивное и дизельное топливо) также проводят в одну или две ступени.
В ходе бензина получить до 85 % реактивного или дизельного топлива. Например, отечественный одноступенчатый процесс гидрокрекинга вакуумного газойля на цеолитсодержащем катализаторе типа ГК-8 может давать до 52 % реактивного топлива или до 70 % зимнего дизельного топлива с содержанием ароматических углеводородов 5-7 %. Гидрокрекинг вакуумных дистиллятов сернистых нефтей проводят в две ступени. Включением гидрокрекинга в технологическую схему НПЗ достигается высокая гибкость в производстве его товарной продукции.
На одной и той же установке гидрокрекинга возможны разные варианты получения бензина, реактивного или дизельного топлива изменением технологического режима гидрокрекинга и блока ректификационного фракционирования продуктов реакции. Например, бензиновый вариант производит бензиновую фракцию с выходом до 51 % на сырье и фракцию дизельного топлива 180-350 °С с выходом 25 % от сырья. Бензиновую фракцию разделяют на легкий бензин С5-С6 с ОЧм = 82 и тяжелый бензин Су-Сю с ОЧм = 66 при содержании в них серы до 0,01 %. Фракцию С-С можно направить на каталитический риформинг для повышения ее октанового числа. Дизельная фракция имеет цетановое число 50-55, не более 0,01 % серы и температуру застывания не выше минус 10 °С (компонент летнего дизельного топлива). В отличие от каталитического крекинга газы С3-С4 и жидкие фракции гидрокрекинга содержат только насыщенные стабильные углеводороды и практически не содержат гетероорганических соединений, они менее ароматизированы, чем газойли каталитического крекинга. При реактивно-то-пливном варианте можно получать до 41 % фракции 120-240 °С, отвечающей стандартным требованиям на реактивное топливо. При дизельно-топливном варианте можно производить 47 или 67 % фракции дизельного топлива с цетановым числом около 50.
6200000
18235294,1
759803,922
Расход
Газ до 28 *С
0,3
18600
54705,8823
2279,41177
Фр н.к -85
2,4
148800
437647,058
18235,2941
Фр 85-180*С
3,5
217000
638235,294
26593,1373
Фр 180-230*С
7,8
483600
1422352,94
59264,7059
Фр 230-350*С
7,15
443300
1303823,53
54325,9804
Фр 350-500*С
24,9
1543800
4540588,23
189191,177
Остаток
53,95
3344900
9837941,17
409914,216
Итого
100
6200000
18235294,1
759803,922
Установка работает 340 дней в году
Материальный баланс установки гидроочистки вакуумного дистиллята (фр. 350-500С) | ||||||
Приход | % мас.на сырье | % мас.на нефть | т/год | т/сут | кг/ч | |
1. Фр. 350-500 С | 100 | 24 | 1543800 | 4540588,23 | 189191,177 | |
Итого | 100 | 24 | 1543800 | 4540588,23 | 189191,177 | |
2. Водород (100%-ный) | 1,5 | 0,36 | 21600 | 63529,41177 | 2647058,823 | |
Всего | 101,5 | 24,36 | 1461600 | 4298823,53 | 179117647 | |
Расход |
|
|
|
|
| |
1. Гидроочищенный вак дис | 94,8 | 22,752 | 1365120 | 4015058,824 | 167294117,6 | |
2. Бензин-отгон | 1,4 | 0,336 | 20160 | 59294,11765 | 2470588,235 | |
3. Сероводород | 2,3 | 0,552 | 33120 | 97411,76471 | 4058823,529 | |
4. Газ | 2 | 0,48 | 28800 | 84705,88236 | 3529411,764 | |
5. Потери | 1 | 0,24 | 14400 | 42352,94118 | 1764705,882 | |
Всего | 101,5 | 18,28 | 1581600 | 4628823,53 | 196117,647 | |
|
|
|
|
|
|
Таблица 10-Материальный баланс
Механический расчет
Исходные данные: Определение средней молекулярной массы
-производительность установки по сырью - 759803,922кг/ч;
-объемная скорость подачи сырья - 5 ч-1;
-давление в реакторе - 7 МПа;
-кратность циркуляции водородсодержащего газа - 500 нм3/м3;
-плотность керосиновой фракции - 782 кг/м3
-температура в реакторе 320-380
Определение средней молекулярной массы:
Найдём среднюю температуру в реакторе, 0С по формуле (9):
(9)
где - температура начала отбора фракции, 0С;
- температура конца отбора фракции, 0С
По формуле Войнова находим молекулярную массу керосиновой фракций, г/моль (10):
(10)
где t - средняя температура кипения фракции, 0С.Размеры реактора
г/моль
Размеры реактора
Определяем объем сырья, м3/ч (11)
(11)
где - количество керосиновой фракции РТ, кг/ч;
- плотность керосиновой фракции
Объем катализатора в реакторе определяем по формуле, м3 (12)
(12)
где - объем сырья при 20 0С, м3/ч;
- объемная скорость подачи жидкого сырья, ч-1.
Секундный объем смеси паров сырья и ЦВСГ при температуре и давлении на входе в реактор находим по формуле, м3 (13)
(13)
где - объем паров сырья при температуре (t) и давлении (P) в реакторе, м3/ч;
- объем циркулирующего и свежего ВСГ при тех же условиях, м3/ч.
Для этого сначала определяем объём паров сырья на входе в реактор по формуле, м2/с (14)
(14)
где - расход сырья поступающего в реактор, кг/ч; Z - коэффициент сжимаемости;
- средняя температура в реакторе, 0С;
- средняя молекулярная масса сырья; P - давление в реакторе, МПа.
Суммарный объем ВСГ на входе в реактор определяют по формуле м2/с (15)
(15)
где - плотность сырья;
- кратность циркуляции ВСГ; Z - коэффициент сжимаемости, для газа значительно разбавленного водородом можно принять равным 1.
Определив суммарный объем смеси, находят сечение (F) (16) и диаметр (d) реактора (17):
(16)
(17)
где - суммарный объем смеси;
- линейная скорость движения сырья (0,3-0,5 м/с);
- математическая константа.
Зная сечение аппарата и объем катализатора, определяют высоту слоя катализатора (18)
(18)
где - объем катализатора в реакторе;
- сечение реактора.
Реактор заполняют катализатором на 2/3 высоты цилиндрической части аппарата. Следовательно, высота цилиндрической части реактора (19):
(19)
где - определяют высоту слоя катализатора.
а общая высота реактора (20):
(20)
где - высота верхнего и нижнего днища, то есть (21)
(21)
где - диаметр реактора.
Общие выводы
По ходу выполнения курсового проекта были изучены теоретические основы процесса гидроочистки, выполнено проектирование установки вакуумного дистиллята смеси Арыскумской нефти производительностью 6,2 млн. т/г (в том числе, произведены технологический и механический расчеты основного аппарата). В ходе выполнения проекта, были изучены типичные технологическая и поточная схема процесса гидроочистки, составлены материальные балансы установок, применяющихся при проведении процесса.
При выполнении данной курсовой работы был рассмотрен процесс гидрогенизации(гидрокрекинга). Внимание было уделено изучению физико-химических основ процесса, а также сырью и продуктам процесса.
Приложение А
Поточная схема Арыскумской нефти.
Приложения Б
Технологическая схема Гидроочистки вакуумного дистиллята
Аннотация
В данном курсовом проекте освещены теоретические основы процесса гидрогенизации, выполнено проектирование установки гидроочистки вакуумного дистиллята смеси Арыскумской нефти производительностью 6,2 млн. т/г (в том числе, произведены технологический и механический расчеты основного аппарата). В ходе выполнения проекта, были изучены типичные технологическая и поточная схема процесса гидроочистки, составлены материальные балансы установок, применяющихся при проведении процесса.
Настоящий курсовой проект состоит из пояснительной записки.
Пояснительная записка включает 40 страницы, 2 рисунок и 12 таблицы.
Нормативные ссылки
В настоящем курсовом проекте использованы ссылки на следующие документы:
ГОСТ 5426-65 Нефтепереработка. Процессы Переработки.
ГОСТ 2111-2014 Топлива. Нефтяные скважины.
ГОСТ 1012-2013 Бензины авиационные.
ГОСТ 2084-77 Бензины автомобильные.
ГОСТ 11851-85 Нефть. Метод определения парафина.
ГОСТ 2177-99 Нефтепродукты. Метод определения фракционного состава.
ГОСТ 1233-2006 Процесс гидроочистки.
ГОСТ 1002-2008 Гидрокрекинг.
ГОСТ 1996-77 Бензины автомобильные.
ГОСТ 12р12-86 Гидрогенизационные процессы.
ГОСТ 1313-98 Исследование процесса гидроочистки
ГОСТ 1809-1989 Высокооктановые бензины.
ГОСТ 1006-1999 Гидрооблагораживание.
Определения
В настоящем курсовом проекте применяют следующие термины с соответствующими определениями:
Катализатор – химическое вещество, ускоряющее реакцию, но не расходующееся в процессе реакции.
Крекинг – процесс переработки нефти и входящих в её состав фракций, существенно увеличивающий выход светлых нефтепродуктов. Крекинг бывает термическим (под влиянием высокой температуры) и каталитическим (с использованием катализатора).
Гидроочистка – процесс химического превращения веществ под воздействием водорода при высоком давлении и температуре. Гидроочистка нефтяных фракций направлена на снижение содержания сернистых соединений в товарных нефтепродуктах. Побочно происходит насыщение непредельных углеводородов, снижение содержания смол, кислородсодержащих соединений, а также гидрокрекинг молекул углеводородов.
Гидрокрекинг – это один из видов крекинга, переработка высококипящих нефтяных фракций, мазута, вакуумного газойля или деасфальтизата для получения бензина, дизельного и реактивного топлива, смазочных масел, сырья для каталитического крекинга и другого.
Вакуумные дистилляты (газойли) – являются сырьем для процессов каталитического крекинга, гидрокрекинга, получения электродного кокса. Для повышения выхода и улучшения качества продуктов, полученных указанными процессами, и с целью уменьшения загрязнения окружающей среды оксидами серы все большая доля вырабатываемых вакуумных газойлей подвергается гидроочистке. Эффективность процесса гидроочистки вакуумного газойля во многом определяется качеством исходного сырья и требованиями к качеству продуктов для последующих процессов.
Обозначения и сокращения
ρc–плотность сырья, керосино-газойлевой фракции;
ρ420– плотность нефти или нефтепродуктов при 200С
ВОК-высокооктановые компоненты;
ВСГ-водородсодержащий газ;
ИВ-индекс вязкости;
КР, КРб – каталитический риформинг, риформинг «на бензин»;
ОЧ-октановое число;
ЭЛОУ-электрообессоливающая и электрообезвоживающая установка.
Содержание
Аннотация | |
Нормативные ссылки | |
Определения | |
Обозначения и сокращения | |
1 Введение | |
2 Аналитический обзор по теме | |
3 Физико-химические характеристики данной нефти | |
4 Описание поточной схемы переработки нефти | |
5 Материальный баланс переработки нефти по потенциальным содержанием фракций | |
6 Описание технологической схемы проектируемой установки | |
7 Материальный баланс проектируемой установки | |
8 Технологические расчеты основных аппаратов установки | |
9 Общие выводы | |
10 Приложение | |
11 Список использованных источников |
Введение
Актуальность работы. В последние 5-10 лет актуальность процессов гидроочистки в связи с необходимостью улучшения качества и увеличения выпуска нефтепродуктов значительно возросла. Это определяется двумя главными тенденциями современной нефтепереработки: увеличением глубины их переработки и ужесточением экологических норм. Первая тенденция из-за вовлечения в переработку и, следовательно, в гидроочистку все более тяжелого нефтяного сырья с большим содержанием серы, азота, металлов, смол и асфальтенов приводит к ужесточению технологического режима и требует создания более устойчивых катализаторов. При сгорании сернистых топлив образуются оксиды серы SO и SO2, которые в зоне пониженных температур вместе с конденсирующимися парами воды образуют сернистую и серную кислоты и оказывают сильное корродирующее действие на металл двигателя. Борьбу с сернистой коррозией ведут способами: во-первых, применением присадок к топливам и маслам, нейтрализующих агрессивное действие продуктов сгорания серы; во-вторых, очисткой топлив от сернистых соединений; в-третьих, для поршневых двигателей, применением устойчивых против коррозии металлов для гильз цилиндров и поршневых колец [1].
Вторая тенденция превращает процессы гидроочистки из вспомогательных в основные, определяющие качество и потребительские свойства моторных и энергетических топлив. Здесь требуется более тонкая очистка от серы и азота, частичное гидрирование ароматических соединений, легкий гидрокрекинг нормальных парафинов, переработка вторичных дистиллятов, содержащих непредельные соединения и т.п. Совместное действие этих двух тенденций выдвигает процессы гидроочистки в ряд важнейших каталитических процессов, занимающих к тому же одно из первых мест в мире по суммарной мощности перерабатываемого сырья и мощности единичных агрегатов.
Научная новизна. Внедрение любого промышленного химико-технологического процесса можно разделить на три этапа:
1. Разработку и исследование в лаборатории;
2. Создание укрупненных опытных установок и проектирование промышленной установки;
3. Осуществление процесса в промышленных условиях.
Задачи изучения процесса на каждом из этих этапов различны. При разработке и исследовании в лаборатории нужно подобрать наилучшие условия осуществления процесса, после чего можно оценить его технико-экономическую эффективность и исследовать физико-химические закономерности. На втором этапе
|
|
Семя – орган полового размножения и расселения растений: наружи у семян имеется плотный покров – кожура...
Опора деревянной одностоечной и способы укрепление угловых опор: Опоры ВЛ - конструкции, предназначенные для поддерживания проводов на необходимой высоте над землей, водой...
История развития пистолетов-пулеметов: Предпосылкой для возникновения пистолетов-пулеметов послужила давняя тенденция тяготения винтовок...
Общие условия выбора системы дренажа: Система дренажа выбирается в зависимости от характера защищаемого...
© cyberpedia.su 2017-2024 - Не является автором материалов. Исключительное право сохранено за автором текста.
Если вы не хотите, чтобы данный материал был у нас на сайте, перейдите по ссылке: Нарушение авторских прав. Мы поможем в написании вашей работы!