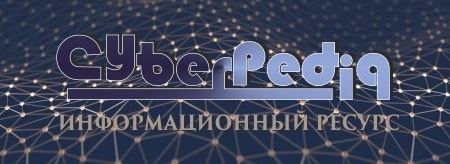
Архитектура электронного правительства: Единая архитектура – это методологический подход при создании системы управления государства, который строится...
Механическое удерживание земляных масс: Механическое удерживание земляных масс на склоне обеспечивают контрфорсными сооружениями различных конструкций...
Топ:
Марксистская теория происхождения государства: По мнению Маркса и Энгельса, в основе развития общества, происходящих в нем изменений лежит...
Характеристика АТП и сварочно-жестяницкого участка: Транспорт в настоящее время является одной из важнейших отраслей народного хозяйства...
Генеалогическое древо Султанов Османской империи: Османские правители, вначале, будучи еще бейлербеями Анатолии, женились на дочерях византийских императоров...
Интересное:
Искусственное повышение поверхности территории: Варианты искусственного повышения поверхности территории необходимо выбирать на основе анализа следующих характеристик защищаемой территории...
Финансовый рынок и его значение в управлении денежными потоками на современном этапе: любому предприятию для расширения производства и увеличения прибыли нужны...
Национальное богатство страны и его составляющие: для оценки элементов национального богатства используются...
Дисциплины:
![]() |
![]() |
5.00
из
|
Заказать работу |
|
|
КЛАССИФИКАЦИЯ, МАРКИРОВКА И ПРИМЕНЕНИЕ КОНСТРУКЦИОННЫХ ЧЕРНЫХ И ЦВЕТНЫХ СПЛАВОВ
Специалисту в его работе крайне необходимы знания в области применения материалов, поскольку на практике достаточно часто приходится решать вопросы их подбора для конкретных условий эксплуатации.
Число металлических сплавов, применяемых в технике, очень велико. При этом оно постоянно возрастает в связи с растущими требованиями промышленности. Всех их необходимо отличать друг от друга, а, следовательно, каким-то образом обозначать, при этом указывать свойства и назначение сплавов, подчеркивать качество. Однако классифицировать металлы и сплавы по одному признаку не представляется возможным, так как их состав, свойства, назначение и способы производства слишком разнообразны. Поэтому существуют несколько признаков, по которым проводят классификацию сплавов: по химическому составу, назначению, способу получения, свойствам и качеству.
Стали
Сталью называется сплав железа с углеродом, в котором углерода содержится не более 2%.
Сталь является основной продукцией черной металлургии. В Российской Федерации приняты стандарты на стали, которые устанавливают маркировку, химический состав, способы производства и раскисления, механические свойства и правила приемки.
Основным классификационным признаком, определяющим марку стали, является ее химический состав. По химическому составу стали делятся на углеродистые и легированные. В углеродистых сталях помимо железа и углерода, содержатся еще постоянные примеси. Эти примеси являются как элементами, специально вводимыми в состав шихты, так и элементами естественного происхождения, которые в процессе плавки невозможно полностью удалить из металла. Так, марганец, кремний вводятся в состав шихты как технологические добавки, необходимые для раскисления металла, т.е. удаления из него кислорода. Сера, фосфор, кислород, водород, азот являются элементами естественного происхождения, которые попадают в металл из руды и атмосферы. В состав стали также попадают примеси случайного происхождения, которые находятся в руде или шихте, например, хром, никель, медь и др. Содержание в стали всех примесей также зависит от способа выплавки.
|
Марганец и кремний повышают прочностные характеристики сталей. Марганец к тому же устраняет вредное воздействие серы на свойства стали, переводя серу в тугоплавкое соединение MnS. Сера и фосфор являются вредными примесями, оказывающими негативное воздействие на сталь, попадая в неё из руды. Сера придает стали красноломкость, свойство давать трещины при горячей обработке давлением в области высоких температур (850 – 1150°С). Фосфор сообщает стали хладноломкость, т.е. способность охрупчиваться при пониженных температурах, что делает невозможным применение изделий из такой стали в районах с холодным климатом. Вредными примесями в стали являются кислород и водород. Кислород образует окислы, которые снижают прочностные свойства стали, а водород может образовывать трещинки-надрывы, называемые флокенами.
По способу производства различают стали конверторные, мартеновские, стали, выплавляемые в электрических печах, и стали особых методов выплавки, таких как электрошлаковый переплав (ЭШП), вакуумно-индукционная плавка (ВИП), вакуумно-диффузионная плавка (ВДП), электронно-лучевой переплав (ЭЛП), плазменно-дуговая плавка (ПДП). Применение особых методов выплавки позволяет получить более чистый и, следовательно, более качественный металл.
Следует отметить, что бессемеровская сталь по сравнению с мартеновской содержит повешенное количество растворенных азота и фосфора и при одинаковом содержании углерода имеет более высокую прочность и твердость и пониженную пластичность. Свойства стали, полученной томасовским способом, приближаются к свойствам мартеновской стали.
|
По назначению стали разделяются на конструкционные, инструментальные и стали специального назначения. Конструкционными называют такие стали, которые применяются для изготовления деталей машин, конструкций и сооружений. Конструкционная сталь должна обладать высокой прочностью, пластичностью и вязкостью в сочетании с хорошими технологическими свойствами: обрабатываемостью, штампуемостью, свариваемостью, т.е. сталь должна легко обрабатываться резанием, давлением и хорошо свариваться. Углеродистые конструкционные стали вплавляются мартеновским и конверторным способами.
По качеству стали делятся на стали обыкновенного качества, качественные и высококачественные. Чем меньше вредных примесей в стали, тем выше её качество.
По способу раскисления стали делятся на три группы: спокойные, полуспокойные, кипящие.
Спокойные стали обозначаются строчными буквами «сп». Их получают полным раскислением металла, т.е. кислород из стали удаляют марганцем, кремнием и алюминием, сначала в печи, а затем в ковше. Полуспокойные стали обозначаются строчными буквами «пс». Их получают раскислением металла марганцем и кремнием или марганцем и алюминием. Кипящие стали маркируются строчными буквами «кп». Их получают раскислением металла только марганцем. Чем полнее раскислен металл, тем выше у него прочностные свойства.
Все металлы и сплавы получили условные обозначения, т. е. марки, состоящие из букв и цифр.
Легированные стали
Легированной называют сталь, в которой наряду с обычными примесями и технологическими добавками содержатся специально вводимые легирующие элементы. Такими элементами могут быть марганец, кремний, хром, ванадий, кобальт, вольфрам, молибден и титан, которые вводят в сталь с целью повышения механических, технологических, физико-химических свойств сталей. Часто легирующие элементы определяют название легированной стали. Например, хромистая, никелевая, ванадиевая, хромоникелевая, хромомарганцевая и др. Изделия из легированной стали более прочные и обладают большей долговечностью, чем изделия из углеродистой стали. По назначению легированные стали делятся на три группы: конструкционные стали, инструментальные стали и стали специального назначения с особыми физическими и химическими свойствами.
|
В основу обозначения марок легированных сталей положена буквенно-цифровая система. Легирующие элементы обозначаются прописными русскими буквами (табл. 2)
Обозначение легирующих элементов в сталях Таблица2
Название | Химический символ | Маркиров. обознач. | Название | Химический символ | Маркиров. обознач. |
Марганец | Mn | Г | Кобальт | Co | К |
Кремний | Si | С | Алюминий | Al | Ю |
Хром | Cr | Х | Медь | Cu | Д |
Никель | Ni | Н | Бор | B | Р |
Вольфрам | W | В | Ниобий | Nb | Б |
Ванадий | V | Ф | Цирконий | Zr | Ц |
Титан | Ti | Т | Фосфор | P | П |
Молибден | Mo | М | Азот | N | А (внутри марки) |
Для конструкционных сталей цифры с левой стороны букв обозначают среднее содержание углерода в сотых долях процента. Например, в стали 45ХВ содержится 0,45% углерода. Если содержание легирующего элемента в стали около 1%, то после буквы цифры не ставятся. Например, ХГ. Если впереди марки нет цифры, то это значит, что углерода в стали содержится около 1%. Например, Х12. Если содержание легирующего элемента в стали больше 1%, то после буквы указывается его среднее значение в целых процентах. Например, в стали Х18Н10Т содержится 18% хрома, 10% никеля и 1% титана.
В качестве основных легирующих элементов в конструкционных сталях используются хром Cr, никель Ni, кремний С. Такие легирующие элементы, как молибден Mo, вольфрам W, ванадий V и титан Т обычно используются в сталях в сочетании с хромом Cr и никелем Ni с целью дополнительного повышения их физико-механических свойств. Их количество в конструкционных сталях, как правило, не превышает 1%. Общее количество легирующих элементов в конструкционных сталях обычно не превышает 7 – 8%.
Поставляются конструкционные легированные стали по ГОСТ 4543-71. По содержанию углерода они делятся на две группы: малоуглеродистые цементируемые стали, содержащие до 0,2% углерода и подвергающиеся в последующем дополнительному насыщению углеродом при химико-термической обработке, и среднеуглеродистые улучшаемые стали, содержащие 0,25 – 0,5% углерода и подвергающиеся в последующем термическому упрочнению путем закалки и высокого отпуска (улучшению). Легированные стали выплавляются с малым содержанием вредных примесей (сера и фосфор менее 0,035%) и являются качественными. Вместе с тем производятся также высококачественные стали. В этом случае, как и в углеродистой стали, в конце марки ставится буква «А», обозначающая высококачественную сталь, т.е. сталь, в которой содержится значительно меньше серы и фосфора (не более 0,025%), например, 30ХГСА. Для пояснения расшифруем некоторые марки. Например, сталь 12Х2Н4А – хромоникелевая конструкционная высококачественная сталь с содержанием 0,12% углерода, 2% хрома, 4% никеля. Сталь марки ХВ5 – хромовольфрамовая конструкционная качественная сталь с содержанием 1% углерода, 1% хрома, 5% вольфрама.
|
В инструментальных сталях вначале, как правило, ставиться одна цифра, показывающая содержание углерода в десятых долях процента, например, 7ХФ, 3Х2В8Ф. Если углерода не более 1%, то вначале цифра не ставиться, например, ХГ и ХВГ. Исключение из этого правила составляют две марки инструментальной стали: 11ХФ и 13Х.
Стали специального назначения с особыми свойствами (жаростойкие, жаропрочные, коррозионно-стойкие нержавеющие) маркируются точно также как конструкционные легированные стали, например, 08Х13, 12Х17, 12Х18Н10Т и 40Х10С2М. Только суммарная доля легирующих элементов в этих сталях в большинстве случаев значительно превышает 10%
Указанная система маркировки охватывает большинство легированных сталей. Исключение составляют некоторые группы сталей, которые дополнительно обозначаются буквой: Р – быстрорежущие, Е – магнитные, Ш – шарикоподшипниковые, Э – электросталь.
C тали для отливок
В тяжелом и транспортном машиностроении эту группу сталей применяют в виде фасонных отливок для станин станков, картеров агрегатов, зубчатых колес и многого другого.
Стали для отливок дополнительно маркируются буквой «Л» в конце марки, что означает литая сталь. Перед ней ставятся цифры, указывающие среднее содержание в стали углерода в сотых долях процента. Литыми сталями могут быть углеродистые конструкционные, легированные конструкционные стали и стали специального назначения с особыми свойствами. Литые углеродистые конструкционные маркируются 15Л и 20Л. Литые легированные конструкционные стали обозначаются 40ХЛ и 35ХМЛ. Литая сталь специального назначения с особыми свойствами маркируется 10Х18Н9Л.
Литая сталь по сравнению с деформированной при одинаковом значении пределов текучести и прочности имеет меньшую вязкость и пластичность.
Для фасонного литья применяют углеродистые стали 15Л, 20Л, 40Л, 50Л, 70Л. Сталь 20Л используется для литья станин прокатных станов, траверс, зубчатых колес. Сталь 30Л – для литья маховиков, цилиндров, станин, станков. 40Л и 45Л – для литья тормозных дисков, опорных катков и др. Высокоуглеродистые стали 50Л, 55Л применяются для износостойких отливок, не испытывающих ударных нагрузок.
|
Автоматные стали
Отличительной особенностью автоматных сталей является хорошая обрабатываемость резанием. Это достигается повышением в автоматных сталях содержания серы до 0,15 – 0,35% и фосфора до 0,1 – 0,15 %. Эти химические элементы снижают прочность и повышают пластичность сталей. Это дает возможность изготавливать в условиях массового производства на автоматических линиях простые в отношении конструкции изделия: винты, болты, гайки и многое другое.
Стали этой группы маркируются буквой «А», что означает автоматная сталь. После буквы ставиться цифра, которая указывает среднее содержание углерода в сотых долях процента. Например, А12, А40Г.
Для улучшения обработки резанием сталь нередко легируют свинцом в количестве от 0,15 до 0,3 %. Также добавляют селен и кальций в количестве до 0,007%. Свинец в марке обозначается буквой «С», селен – буквой «Е», а кальций – буквой «Ц». Они ставятся после буквы «А». Например, АС40, АЦ20.
Химический состав и механические свойства автоматных сталей
(ГОСТ 1414-94)
Марка стали | Химический состав, % | Механические свойства | |||||
С | Si | Mn | P | S | σв, Мпа | δ, % | |
А12 | 0,08-0,16 | 0,15-0,35 | 0,60-0,90 | 0,08-0,15 | 0,08-0,15 | 420-800 | 7-22 |
А20 | 0,15-0,25 | 0,15-0,35 | 0,60-0,90 | 0,06 | 0,08-0,15 | 460-820 | 7-20 |
А30 | 0,25-0,35 | 0,15-0,35 | 0,70-1,00 | 0,06 | 0,08-0,15 | 520-850 | 6-15 |
А40Г | 0,35-0,45 | 0,15-0,35 | 1,20-1,55 | 0,05 | 0,18-0,30 | - | - |
Сталь А12 применяется для изготовления винтов, болтов, гаек и различных мелких деталей сложной конфигурации на быстроходных автоматах. Стали А20, А30, А40Г используются для изготовления деталей, работающих при повышенных нагрузках.
Строительные стали
Низколегированные конструкционные стали широко применяются в строительстве и машиностроении для изготовления горячекатаного проката различных профилей, предназначенных для сварных конструкций и содержат легирующих элементов до 5%. По сравнению с углеродистыми сталями эти стали обладают повышенной прочностью, износостойкостью, пластичностью при низких температурах, коррозионной стойкостью и хорошей свариваемостью. В соответствии с ГОСТ 277-88 в зависимости от механических свойств (не принимая во внимание химический состав) эти стали подразделяются на классы: стали обычной прочности, повышенной прочности и высокой прочности.
Классы строительных сталей
Класс прочности | Предел текучести σ0,2, МПа | Марка стали по ГОСТ и ТУ |
Обычная прочность | ||
С235 | 235 | Ст3кп, Ст18кп |
С245 | 245 | Ст3пс, Ст18пс |
С255 | 255 | Ст3Гпс, Ст18пс |
С275 | 275 | Ст3пс |
С285 | 285 | Ст3сп, Ст3Гсп |
Повышенная прочность | ||
С345 | 345 | 09Г2С, 12Г2С, 14Г2 |
С345Т | 345 | 15ХСНД, Ст3псТ |
С345К | 345 | 10ХНДП |
С375, С375Д | 375 | 12Г2С, 12Г2СД |
С390, С390Т | 390 | 14Г2АФ, 10Г2С1 |
С390К | 390 | 15Г2АФД |
Высокая прочность | ||
С440 | 440 | 16Г2АФ |
С590 | 590 | 12Г2СМФ |
С590К | 590 | 12Н2МФАЮ |
Стали для подшипников
Конструктивные элементы подшипников (кольца, ролики и шарики) работают в условиях высоких контактных деформаций, которые требуют от стали высокой твердости, износостойкости и сопротивляемости контактной усталости (фреттингстойкости). В качестве шарикоподшипниковой стали часто применяют углеродистые (с содержанием углерода в количестве 1%) хромистые стали, а для массивных подшипников добавляют большее (до 1%) количество марганца и кремния, получая таким образом хромомарганцевую сталь.
Стали для подшипников поставляются по ГОСТ 801-78.
Особенностью маркировкисталей для подшипников является обозначение их буквой «Ш» в начале марки. Далее ставится буква «Х», обозначающая основной легирующий элемент – хром, следующая за буквой цифра показывает содержание хрома в десятых долях процента.
Состав и назначение шарикоподшипниковой стали.
Марка стали | Химический состав в % | Назначение | ||||
C | Mn | Si | Cr | шарики | ролики | |
Диаметр, мм | ||||||
ШХ6 | 1,05-1,15 | 0,2-0,4 | 0,17-0,37 | 0,4-0,7 | до 13,5 | до 10 |
ШХ9 | 1,0-1,1 | 0,2-0,4 | 0,17-0,37 | 0,9-1,2 | 13,5-22,5 | 10-15 |
ШХ15 | 0,95-1,05 | 0,2-0,4 | 0,17-0,37 | 1,3-1,65 | более22,5 | 15-30 |
ШХ15СГ | 0,95-1,05 | 0,9-1,2 | 0,4-0,65 | 1,3-1,65 | - | более 30 |
Быстрорежущие стали
Быстрорежущие стали применяется для изготовления режущей части многих обрабатывающих инструментов. Она в отличие от других инструментальных сталей обладает высокой теплостойкостью, т.е. способностью сохранять свою структуру, высокую твердость, прочность и износостойкость при повышенных температурах (620°С), возникающих в процессе обработки в области режущей кромки инструмента. Теплостойкость быстрорежущей стали придает вольфрам, являющийся основным легирующим элементом.
Маркируется быстрорежущая сталь буквой «Р». Цифра, стоящая за буквой «Р», показывает среднее содержание вольфрама в целых процентах. Далее ставятся буквы и цифры, указывающие среднее содержание других легирующих элементов, например, ванадия «Ф», кобальта «К». Все быстрорежущие стали содержат около 1% углерода.
Классическим примером быстрорежущей стали является чисто вольфрамовая сталь Р9 и Р18. Однако вольфрам имеет достаточно высокую стоимость. Поэтому его в стали частично заменяют более дешевым аналогом – молибденом. Например, Р6М5. Для повышения износостойкости дополнительно легируют ванадием или кобальтом, например Р6М5К5.
Поставляются быстрорежущие стали по ГОСТ 19265-73.
Химический состав быстрорежущих сталей, % (ГОСТ 9373-60)
Сталь | C | Cr | W | V | Co | Mo |
Р18 | 0,7-0,8 | 3,8-4,4 | 17,5-19,0 | 1,0-1,4 | - | 0,3 |
Р9 | 0,85-0,95 | 3,8-4,4 | 8,5-10, | 2,0-2,6 | - | 0,3 |
Р9Ф5 | 1,4-1,5 | 3,8-4,4 | 9,0-10,5 | 4,3-5,1 | - | 0,4 |
Р14Ф4 | 1,2-1,3 | 4,0-4,6 | 13,0-15,5 | 3,4-4,1 | - | 0,4 |
Р18Ф2 | 0,85-0,95 | 3,8-4,4 | 17,5-19,0 | 1,8-2,4 | - | 0,5 |
Р9К5 | 0,9-1,0 | 3,8-4,4 | 9,0-10,5 | 2,0-2,6 | 5,0-6,0 | 0,3 |
Р9К10 | 0,9-1,0 | 3,8-4,4 | 9,0-10,5 | 2,0-2,6 | 9,5-10,5 | 0,3 |
Р10К5Ф5 | 1,45-1,55 | 4,0-4,6 | 10,0-11,5 | 4,3-5,1 | 5,0-6,0 | 0,3 |
Р18К5Ф2 | 0,85-0,95 | 3,8-4,4 | 17,6-19,0 | 1,8-2,4 | 5,0-6,0 | 0,5 |
Магнитные стали
Магнитные стали широко применяются в электротехнике для изготовления постоянных магнитов, сердечников трансформаторов, электроизмерительных приборов, электромагнитов и др. Эти стали по резко различающимися магнитным характеристикам делятся на две группы: магнитотвердые и магнитомягкие. Эти определения не относятся к характеристике механических свойств (например, твердости) материала. Существуют механически мягкие, но магнитотвердые стали и, наоборот.
У магнитомягких сталей маленькая коэрцитивная сила и узкая петля гистерезиса, они обладают очень высокой магнитной проницаемостью, легко намагничиваются и перемагничиваются. Из них делают сердечники трансформаторов, электроизмерительных приборов, электромагнитов и др.
Все магнитомягкие стали делятся на три группы:
· сталь электротехническая тонколистовая и сортовая нелегированная, по-другому эта сталь называется техническое железо;
· сталь электротехническая кремнистая;
· прецизионные магнитомягкие сплавы.
Для сталей первых двух групп разработана чисто цифровая система обозначения. Нелегированные стали обозначаются пятизначным числом:
· 10895, 20895, 10880, 20880, 10864, 20864,
· 11895, 21895, 11880, 21880, 11864, 21864
Первая цифра в марке обозначает способ изготовления стали:
1 – горячекатаная, 2 – холоднотянутая. Вторая цифра «0» или «1» обозначает, что сталь не легирована и имеет нормированный или ненормированный коэффициент старения (упрочнения); третья, четвертая и пятая цифры в марке указывают на магнитные характеристики сталей.
Сталь кремнистая электротехническая имеет четырехзначное цифровое обозначение марки. Первая цифра, обозначающая способ изготовления стали, может варьироваться от 1 до 3:
1 – горячекатаная, 2 – холоднотянутая, 3 – текстурованная.
Вторая цифра, показывающая содержание кремния в целых процентах, может варьироваться от 0 до 5. Две последние цифры указывают на магнитные характеристики сталей:
· 1211 (Si 2%), 1312 (Si 3%), 1413 (Si 4%), 1514 (Si 5%) – горячекатаная сталь;
· 2111 (Si 1%), 2212 (Si 2%), 2312 (Si 3%), 2412 (Si 4%) – холоднотянутая сталь;
· 3411 (Si 4%), 3412 (Si 4%), 3413 (Si 4%), 3415 (Si 4%) – текстурованная сталь.
Из этой группы сталей наиболее высокие магнитные свойства имеет текстурованная сталь с крупнозернистой структурой, зерна которой расположены преимущественно вдоль листа.
Третья группа сплавов с добавками железа и кобальта содержит большое количество никеля (45 – 78%). Эти сплавы называют пермаллоями и применяют в радиотехнике, вычислительной технике, т.е. там, где используются слабые токи.
Магнитотвердые стали и сплавы применяют для изготовления постоянных магнитов. Такие стали обозначается буквой «Е», которая ставиться в начале марки. Далее идет стандартное обозначение, например, ЕХ3, ЕВ6, ЕХ5К5. Они содержат большое количество хрома, вольфрама, молибдена и кобальта, которые улучшают магнитные свойства. Если в качестве электротехнических сталей используются безуглеродистые сплавы, т.е. сплавы, содержащие ничтожное количество углерода (не выше 0,04%), то в качестве магнитотвердых сталей (для постоянных магнитов) используются сплавы с содержанием углерода около 1%.
Химический состав магнитных сталей (ГОСТ 6862-71).
Марка стали | Химический состав, % | ||
C | Cr | Co, W, Mo | |
ЕХ | 0,95-1,10 | 1,3-1,6 | - |
ЕХ3 | 0,90-1,10 | 2,8-3,6 | - |
Е7В3 | 0,68-0,78 | 0,3-0,5 | 5,2-6,2 W |
ЕХ9К15М2 | 0,90-1,05 | 8,0-10,0 | 13,5-16,5 Co 1,2-1,7 Mo |
Чугуны
Чугуном называется сплав железа с углеродом, в котором содержание углерода превышает 2%. Углерод в чугуне может находиться в двух состояниях: в химически связанном состоянии в виде цементита Fe 3 C и в свободном состоянии в виде графита. В зависимости от состояния углерода чугуны, соответственно, подразделяются на две группы: белые, в которых весь углерод находится в химически связанном состоянии и графитсодержащие (графитные), в которых основная масса углерода находится в виде графита. Графитные чугуны делятся на серые, высокопрочные и ковкие. Они отличаются друг от друга только формой выделения графита. В серых чугунах графит выделяется в виде пластинок; в высокопрочных – в виде шаров; в ковких – в виде хлопьев. От формы графитных включений зависит уровень механических свойств чугунов.
Серые чугуны маркируют буквами СЧ и двухзначным числом, которое показывает предел прочности при растяжении. Например, марка СЧ20 показывает, что чугун имеет σв =200 МПа. Серые чугуны имеют самую низкую прочность среди всех графитных чугунов, так как пластинчатая форма графита по существу является своеобразной трещиной внутри металла, ослабляющей его механические свойства. Но при этом серый чугун обладает высокими литейными свойствами, хорошо обрабатывается резанием, менее хрупок, чем белый чугун, ему присущи хорошие антифрикционные свойства. Благодаря этим характеристикам и своей относительно низкой себестоимости он нашел широкое применение в машиностроении для производства отливок и поэтому называется литейным.
Механические свойства серого чугуна (ГОСТ 1412-85)
Марка чугуна | Предел прочности σв, МПа | Твердость НВ, МПа | |
СЧ10 | 100 | 1900 | |
СЧ15 | 150 | 2100 | |
СЧ18 | 180 | 2200 | |
СЧ20 | 200 | 2300 |
Высокопрочные чугуны маркируют буквами ВЧ и двухзначным числом, которое показывает предел прочности при растяжении.
Благодаря высоким механическим свойствам высокопрочный чугун применяют вместо стали или ковкого чугуна для изготовления деталей большого сечения и особо нагруженных изделий, например, коленчатых и распределительных валов, различных кулачковых валиков и др.
Механические свойства высокопрочного чугуна (ГОСТ 7293-85)
Марка чугуна | Предел прочности σв,, МПа | Предел текучести σт,, МПа | Относительное удлинение δ, % | Твердость НВ, МПа | |
ВЧ35 | 350 | 220 | 22 | 1550 | |
ВЧ40 | 400 | 250 | 15 | 1700 | |
ВЧ45 | 450 | 310 | 10 | 1800 | |
ВЧ60 | 600 | 370 | 5,0 | 2350 | |
ВЧ100 | 1000 | 700 | 10,0 | 3100 |
Ковкий чугун маркируют буквами КЧи двумя числами: первое число показывает предел прочности при растяжении, второе – относительное удлинение. Например, марка КЧ 55-4 означает, что чугун имеет предел прочности σв= 540 – 550 МПа и относительное удлинение δ = 4%.
Механические свойства ковкого чугуна (ГОСТ 1215-79)
Марка чугуна | Предел прочности σв, МПа | Относительное удлинение δ, % | Твердость НВ (не более) |
Ферритный | |||
КЧ 30-6 | 300 | 6 | 1630 |
КЧ 33-8 | 330 | 8 | 1630 |
КЧ 35-10 | 350 | 10 | 1630 |
КЧ 37-12 | 370 | 12 | 1630 |
Ферритно – перлитный | |||
КЧ 45-7 | 450 | 7 | 2070 |
КЧ 50-5 | 500 | 5 | 2300 |
КЧ 60-3 | 600 | 3 | 2600 |
КЧ 70-2 | 700 | 2 | 2850 |
КЧ 80-1,5 | 785 | 1,5 | 3200 |
Ковкий чугун применяют при изготовлении тонкостенных деталей небольшого сечения, работающих в условиях ударных и вибрационных нагрузок.
Твердые сплавы
Порошковыми твердыми сплавами называют материалы, изготовленные из металлических порошков или их смесей с неметаллическими порошками по технологиям получения керамики. Твердые сплавы делят на металлокерамические и безвольфрамовые. Металлокерамическими называются композиционные материалы, получаемые, главным образом, спеканием тугоплавких компонентов (карбидов вольфрама, титана, тантала) на кобальтовой связке Исходные компоненты формуют прессованием в пресс-формах и далее спекают при температурах, обеспечивающих схватывание в монолитное металлокерамическое изделие без полного расплавления композиции. По сравнению с исходными компонентами металлокерамические сплавы обладают лучшими свойствами (высокой твердостью, теплостойкостью и износостойкостью). Их выпускают в виде пластинок различной формы, которыми оснащают режущие инструменты. Необходимые геометрические параметры режущей части пластинок получают в процессе прессования и в дальнейшем механически не обрабатывают.
Металлокерамические сплавы по ГОСТу 3882-74 делятся на 3 группы: вольфрамокобальтовые (или вольфрамовые), обозначаемые буквами ВК, титановольфрамокобальтовые (или титановые), обозначаемые буквами ТК, и титанотанталовольфрамокобальтовые (или титанотанталовые), обозначаемые буквами ТТК.
Маркируются металлокерамические сплавы следующим образом: группа ВК – вольфрамокобальтовые сплавы, цифра после буквы указывает содержание в сплаве кобальта. Например, сплав ВК2 содержит 2% кобальта и 98% карбидов вольфрама WC. Иногда после цифры справа ставят буквы М, ОМ или В. Буква «М» означает, что сплав имеет мелкозернистую структуру (размер зерен 1,3 – 1,5 мкм), «ОМ» – особомелкозернистая структура (размер зерен до 1 мкм), и буква «В» – крупнозернистую структуру (размер зерен 3 – 5 мкм). Нормальный размер зерен твердых сплавов составляет 2 – 3 мкм.
Группа ТК – титановольфрамокобальтовые сплавы. Цифры после буквы «Т» указывают содержание карбидов титана, цифра после буквы «К» – содержание кобальта, остальное составляют карбиды вольфрама. Например, сплав Т5К10 содержит 5% титана Ti, 10% кобальта Со и 85% карбидов вольфрама WC.
Группа ТТК – титанотанталовольфрамокобальтовые сплавы. Цифра после букв «ТТ» показывает суммарное содержание карбидов титана и тантала, а после буквы «К» – количество кобальта. Например, ТТ7К12 содержит 7% карбидов титана и тантала (TiC + TaC), 12% кобальта Co и 8% карбидов вольфрама WC.
Химический состав (%) и твердость металлокерамических твердых сплавов (ГОСТ 3882-74)
Сплав | Карбид вольфрама | Карбид титана | Карбид тантала | Кобальт | Твердость HRA |
ВК3 | 97 | - | - | 3 | 89,5 |
ВК3М | 97 | - | - | 3 | 91,0 |
ВК6 | 94 | - | - | 6 | 88,5 |
ВК6М | 94 | - | - | 6 | 90,0 |
ВК6В | 94 | - | - | 6 | 87,5 |
ВК15 | 85 | - | - | 15 | 86,0 |
ВК25 | 75 | - | - | 25 | 83,0 |
Т30К4 | 66 | 30 | - | 4 | 92,0 |
Т15К6 | 79 | 15 | - | 6 | 90,0 |
Т14К8 | 78 | 14 | - | 8 | 89,5 |
Т6К10 | 85 | 6 | - | 9 | 88,5 |
ТТ7К12 | 81 | 4 | 3 | 12 | 87,0 |
ТТ10К8 | 82 | 3 | 7 | 8 | 89,0 |
Черновую токарную обработку твердого металла (HRC > 42) проводят резцами с режущей частью из твердых сплавов Т15К6, Т5К10 и ВК6, ВК8. Для точения заготовки по твердой корке (или при прерывистом точении) рекомендуется применять резцы с твердыми сплавами ВК6 и ВК8, так как они лучше выдерживают неравномерные, ударные нагрузки и обеспечивают наибольшую стойкость резцов. Однако при устойчивом черновом точении (без ударов) предпочтительнее применять резцы с твердыми сплавами Т15К6 и Т5К10. Чистовую токарную обработку, которая характеризуется высокими скоростями резания и температурами в зоне обработки, проводят резцами с твердым сплавом ВК6М с мелкозернистой структурой или твердым сплавом ВК6ОМ с особомелкозернистой структурой. Они сохраняют повышенную твердость и износостойкость при нагреве до температур 400 – 900°С.
Безвольфрамовые металлокерамические твердые сплавы были созданы вследствие необходимости замены дорогостоящего вольфрама. В них вместо карбидов вольфрама используют карбиды, нитриды, карбонитриды титана, окислы тугоплавких металлов на никелевой и молибденовой связке.
Наибольшее распространение получили твердые сплавы на никельмолибденовой связке с составом твердой фазы карбидов титана TiC или карбидов и нитридов титана TiC + TiN, так называемых монитикаров, – ТН20, ТНМ25, КТНМ-20А, МНТ-А2, МНТ-А3, МНТ-Б2 и другие имеющие твердость 88 – 91 HR А.
В ГОСТ 26530 включено только два безвольфрамовых металлокерамических твердых сплава ТН20 и КТН16. Цифра после букв «ТН», обозначающих титаноникелевую группу сплавов, показывает суммарное содержание никеля (15%) и молебдена (5%), остальное карбиды титана TiC. Стандарт предусматривает использование сплава ТН20 для чистового и получистового точения при непрерывном резании углеродистых, низколегированных конструкционных сталей.
Большое количество металлокерамического твердого сплава выпускают в виде многогранных неперетачиваемых пластин. Это позволяет экономить твердый сплав, так как переточка твердого сплава обычно вызывает микротрещины и приводит к преждевременному выходу из строя инструмента. С целью повышения эксплуатационных свойств твердосплавных пластин на них наносят однослойные и многослойные (до 4 слоев) покрытия толщиной 2 – 12 мкм. Наиболее широко применяются покрытия на основе карбидов титана TiC, нитридов титана TiN, карбонитридов титана Ti С N и оксидов алюминия Al 2 O 3.
Режущая керамика
Высокая стоимость компонентов металлокерамических твердых сплавов предопределила создание материалов с режущими свойствами не хуже, чем у них, но значительно дешевле. По сравнению с твердыми сплавами режущая керамика (минералокерамика) имеет большую твердость (до 95 HRA) и повышенную теплостойкость (до 1500°С) и пониженную склонность к схватыванию с обрабатываемыми материалами. Они могут работать в условиях высоких скоростях резания (до 600 м/мин) при тонком, чистовом и получистовом точении. Однако режущую керамику вследствие ее низкой ударной вязкости нельзя применять при прерывистом точении и в условиях циклического изменения тепловой нагрузки.
Оксидную керамику создают на основе оксидов алюминия Al 2 O 3 с добавлением до 0,6% оксида магния MgO или оксида хрома Cr2 O 3. Оксидная керамика ВО – 13, ВО – 100 (ЦМ – 332), ВШ – 75 с мелкозернистой структурой (размер зерна составляет 0,5 мкм) обладает высокой прочностью (σв = 550 МПа, HRC > 92) и износостойкостью.
Оксидно-карбидная керамика по своим качествам занимает промежуточное место между оксидной керамикой и твердыми сплавами. Изготовляют оксидно-карбидную керамику из смеси оксидной керамики и 20 – 40% карбидов вольфрама WC, молибдена Mo2C или системы карбидов молибдена и титана Mo2C + TiC. Оксидно-карбидная керамика В – 3, ВОК – 60, ВОК – 63, ВОК – 71, ВОК – 95 имеет высокую прочность (σв = 860 МПа), твердость (HR А = 93 – 95) и теплостойкость (до 1400°С).
Нитридная керамика, по другому силинит-Р изготавливается на основе нитридов кремния SiN4 с добавлением оксидов алюминия Al 2 O 3 и нитридов титана TiN. Она характеризуется невысокой стоимостью и высокой стабильностью свойств и стойкостью при больших температурах. Ее прочность составляет σв = 700 МПа, твердость равна 94 – 96 HR А.
Латуни
Латунями называется группа сплавов меди с цинком. Латуни широко применяются в приборостроении, в химическом машиностроении. Латуни обозначаются буквой «Л» и цифрами после буквы, которые указывают средний процент меди в сплаве. Нормировано 8 марок простых латуней Л96, Л90, Л85, Л80, Л70, Л68, Л63 и Л60. Латуни более сложного состава, имеющие несколько компонентов, в обозначении после буквы «Л» имеют другую букву, а цифры, размещенные после буквы, указывают процент добавки в последовательности написания этих цифр. Например, ЛС-59-1 означает: свинцовая латунь, содержащая от 57 до 60% меди и от 0,8 до 1,9 свинца; ЛМцА-57-3-1 – латунь марганцевистоалюминиевая, содержащая 57% меди, 3% марганца и 1% алюминия. Эти латуни называются сложными или специальными. Все добавляемые в латуни обозначаются начальными прописными буквами от названия химического элемента:
О – олово С – свинец А – алюминий
Ж – железо Н – никель К – кремний
Мц – марганец Мш – мышьяк Ц – цинк
Химический состав (%) и назначение специальных латуней ГОСТ15527-70 (2004)
Латунь | Марка латуни | Cu | Другие легирующие элементы | Zn | Примерное назначение |
Алюминиевая | ЛА77-2 | 76-79 | 1,75-2,5 Al | остальное | Трубы конденсаторные |
Никелевая | ЛН65-5 | 64-67 | 5-6,5 Ni | Трубы манометрические, проволока, л |
|
|
Эмиссия газов от очистных сооружений канализации: В последние годы внимание мирового сообщества сосредоточено на экологических проблемах...
Индивидуальные очистные сооружения: К классу индивидуальных очистных сооружений относят сооружения, пропускная способность которых...
Наброски и зарисовки растений, плодов, цветов: Освоить конструктивное построение структуры дерева через зарисовки отдельных деревьев, группы деревьев...
Биохимия спиртового брожения: Основу технологии получения пива составляет спиртовое брожение, - при котором сахар превращается...
© cyberpedia.su 2017-2024 - Не является автором материалов. Исключительное право сохранено за автором текста.
Если вы не хотите, чтобы данный материал был у нас на сайте, перейдите по ссылке: Нарушение авторских прав. Мы поможем в написании вашей работы!