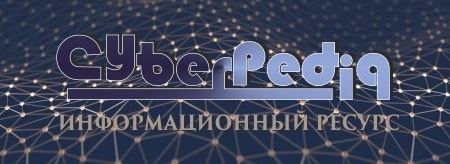
Автоматическое растормаживание колес: Тормозные устройства колес предназначены для уменьшения длины пробега и улучшения маневрирования ВС при...
Типы оградительных сооружений в морском порту: По расположению оградительных сооружений в плане различают волноломы, обе оконечности...
Топ:
Устройство и оснащение процедурного кабинета: Решающая роль в обеспечении правильного лечения пациентов отводится процедурной медсестре...
Комплексной системы оценки состояния охраны труда на производственном объекте (КСОТ-П): Цели и задачи Комплексной системы оценки состояния охраны труда и определению факторов рисков по охране труда...
Марксистская теория происхождения государства: По мнению Маркса и Энгельса, в основе развития общества, происходящих в нем изменений лежит...
Интересное:
Национальное богатство страны и его составляющие: для оценки элементов национального богатства используются...
Подходы к решению темы фильма: Существует три основных типа исторического фильма, имеющих между собой много общего...
Искусственное повышение поверхности территории: Варианты искусственного повышения поверхности территории необходимо выбирать на основе анализа следующих характеристик защищаемой территории...
Дисциплины:
![]() |
![]() |
5.00
из
|
Заказать работу |
|
|
Введение
Процессы прессования с прямым и обратным истечением металла (рис.1) известны достаточно давно. Уже с начала XIX века выявлены основные отличия и достоинства каждого из способов прессования.
Так, в области прессования сплошных профилей, наиболее предпочтительным оказалось обратное прессование, как обеспечивающее минимальное усилие прессования. При прессовании труб, наиболее эффективным оказалось прямое прессование. При повышенном, относительно обратного прессования, усилии прессования, оно обеспечивает меньший разностен пресс-изделий, а также имеет более простую конструкцию оборудования.
Значительное различие в усилии прессования при прямом и обратном способе принято объяснять наличием значительных сил трения при прямом прессовании, а также различием в объеме зоны металла, перешедшего в пластическое состояние – очага деформации.
Существующие теоретические способы расчета усилия прессования основаны на предположении, что очаг деформации ограничивается сектором сферы с центральным углом α (см. рис.1). При прямом прессовании принято считать, что угол α = 60º. При обратном прессовании угол α значительно больше, за счет чего объем очага деформации значительно уменьшается.
При заданном таким способом объеме очага деформации усилие на деформацию определяется следующим образом:
, (1)
где – объем очага деформации;
– интенсивность касательных напряжений сдвига;
– интенсивность скорости деформации;
– скорость прессования.
Следовательно, большое влияние на точность расчета усилия деформации при прессовании имеет точность определения границ очага деформации.
|
Таким образом, рассмотрим в данной лабораторной работе метод практического определения формы очага деформации при прямом и обратном прессовании сплошных профилей.
Для этих целей воспользуемся методом координатных сеток, позволяющих определить распределение степени деформации по сечению заготовки, и с достаточной точностью определить границы очага деформации.
Данный метод заключается в нанесении на продольный разъем цилиндрической заготовки координатной сетки, которая во время деформации искажается в соответствии с течением металла в очаге деформации. Анализ полученной после деформации сетки позволяет определить характер течения металла и форму очага деформации.
Так, для проведения эксперимента, воспользуемся цилиндрическим разъемным образцом длиной 70 - 100 мм и диаметром 50 мм с нанесенной на диаметральный разъем координатной сеткой с шагом 5 мм (см. рис. 6, 7 а).
Для успешного отслеживания изменения местоположения каждой конкретной точки (узла нанесенной сетки), а также для удобства ввода данных о координатах точки в ЭВМ для дальнейших расчетов, на каждой исследуемой сетке введена однозначная система нумерация узлов. Соответственно, при работе с деформированной сеткой, система нумерации точек должна повторять нумерацию исходного образца.
Для работы с сетками, как имеющими определенное количество строк и столбцов (сетки, вписанные в прямоугольный разъем детали) введена система нумерации, представленная на рис. 2. Точка с координатами (i,j) расположена на пересечении i-ой горизонтальной линии и j-ой вертикальной линии (i-я строка, j-й столбец).
Для значительного упрощения определения координат узлов сетки (как исходной, так и деформированной), работа по определению координат узлов проводится на ЭВМ путем обработки фотографии координатной сетки в цифровом виде (растрового изображения), см. рис. 3,7.
Первоначально, при работе программы, координаты узлов определяются в системе координат растрового изображения. После чего, значения координат пересчитываются в реальную систему координат, заданную мерным угольником с размерами внутренних граней 52 мм, помещенного при фотографировании в плоскость разъема образца (см. рис. 3, 7).
|
Так как, рассматриваемая ниже, методика определения деформированного состояния производит расчет для элемента сетки (четырехгранника, заключенного между 4-мя точками), то точкой приложения рассчитанных параметров, будем считать центр масс данного элемента. Номером элемента будем считать номер левого верхнего узла элемента (рис. 2 а).
Для расчета тензора деформации, определяется средняя величина деформации по элементу. Для чего, определялся усредненный тензор преобразования для элемента из начального положения в деформированное.
Так, рассмотрим определение тензора преобразования для двух векторов, соответствующих первым двум смежным точкам элемента – (i,j) и (i,j+1). При этом начало рассматриваемой системы координат сместим в центр масс элемента (рис.4).
Уравнение для определения тензора преобразования запишется в следующем виде:
; (2)
где: – матрица тензора преобразования.
Решив это уравнение относительно T, получим выражение для определения тензора преобразования для первых двух точек элемента:
. (3)
Аналогично для трех других пар точек элемента получим следующие выражения:
; (4)
; (5)
. (6)
Для определения усредненного тензора преобразования, усредним воздействие полученных четырех тензоров на единичные вектора исходного базиса:
. (7)
Для определения тензора деформации рассмотрим результат воздействия усредненной матрицы преобразования на единичные векторы базиса i и j (рис.5).
Как видно из рис.5, компоненты тензора деформации можно рассчитать следующим образом:
; (8)
; (9)
. (10)
Из условия не сжимаемости определим компонент тензора :
|
. (11)
Таким образом, мы получим девиатор тензора деформации вида:
. (12)
Для расчета величины степени деформации элементов воспользуемся формулой:
. (13)
При этом, форма очага при деформации определяется как линия уровня со степенью деформации на поле значений степени деформации, рассчитанной по формуле (13).
Под понимается такое значение степени деформации, превышение которого говорит о переходе данной точки металла в пластическое состояние.
Для оценки величины усилия, необходимого для деформации в процесса прессования, воспользуемся следующей формулой:
, (14)
где – максимальная интенсивность касательных напряжений сдвига;
– скорость деформации;
–скорость прессования;
– объем очага деформации.
Величина скорости деформации определяется по формуле [9]:
, (15)
где – коэффициент вытяжки при прессовании;
– диаметр контейнера;
– диаметр пресс-изделия;
– полуугол наклона мертвой зоны к оси прессования.
Таким образом, подставив в формулу (14) выражение (15) и определив из геометрических соображений значение величины , получим для определения усилия прессования следующие формулы.
Определение усилия деформации при прямом прессовании:
, (16)
где – сопротивление деформации металла;
– средняя длина очага деформации.
Значение средней длины очага деформации определяется как среднее расстояние от плоскости матрицы до границы очага деформации.
При определении объема очага деформации при прямом прессовании принято допущение о том, что очаг деформации ограничивается плоскостью матрицы и мертвыми зонами определяющимися полууглом .
Определение усилия деформации при обратном прессовании:
. (17)
|
При определении объема очага деформации при обратном прессовании принято допущение о том, что очаг деформации ограничивается плоскостью матрицы и занимает объем контейнера на длину . То есть, предполагаем, что объем мертвых зон приблизительно компенсируется объемом очага деформации проникающим в пресс-изделие.
При расчете усилия прессования по формулам (16), (17), примем значение полуугла равным 60º.
Для реализации описанного выше алгоритма на языке визуального программирования Borland C++ Builder v.6.0 написана программа Grid Analyser, предназначенная для работы с осесимметричными координатными сетками, нанесенными на осевой разъем цилиндрических образцов.
Общий вид рабочего окна программы приведен на рис.10.
Цели работы
Ознакомление со способом анализа деформированного состояния методом координатных сеток;
Определение параметров деформированного состояния при прямом и обратном прессовании свинца;
Определение зависимости размеров пластической зоны при прямом и обратном прессовании от коэффициента вытяжки.
Порядок выполнения работы
Фотографирование исходной координатной сетки на разъеме цилиндрического образца, предназначенного под прессование;
Прямое или обратное прессование заготовки с заданной вытяжкой;
Фотографирование деформированной координатной сетки;
Обработка полученных фотографий координатных сеток;
Определение зависимости средней относительной длины очага деформации от коэффициента вытяжки при прямом и обратном прессовании
Оформление отчета
В отчете необходимо отразить следующие пункты:
- цель работы;
- описать методику обработки координатных сеток;
- по описанной методике рассчитать степень деформации одного из элементов координатной сетки (координаты узлов рассматриваемого элемента взять из таблицы вывода координат расчетной программы) и сравнить с результатом, полученным в программе;
- построить график зависимости средней относительной длины очага деформации от коэффициента вытяжки при прямом и обратном прессовании;
- рассчитать среднюю величину коэффициента трения по Зибелю на контактной поверхности инструмента и заготовки;
- заполнить табл. 1;
- сделать выводы по работе.
Таблица 1
Сводная таблица результатов
№ образ-ца | Коэффи-циент вытяжки ![]() | Средняя длина очага деформации ![]() | Относительная длина очага деформации ![]() | Усилие прессо-вания F, кН | Усилие дефор-маци Р, кН | Коэффи-циент трения ψ | ||
Прямое прессование | ||||||||
1 |
| |||||||
2 |
| |||||||
… |
| |||||||
n |
| |||||||
Обратное прессование | ||||||||
1 |
| |||||||
2 |
| |||||||
… |
| |||||||
m |
| |||||||
В выводах по работе необходимо охарактеризовать форму очага деформации в контейнере, а также сопоставить ее с классическими представлениями [1-3]. Дать объяснение графикам полученных зависимостей с точки зрения теории ОМД. На основе полученных данных дать сравнительную характеристику прямого и обратного прессования.
Требования к безопасности
К выполнению работы допускаются студенты, прошедшие инструктаж в рамках утвержденных инструкций по технике безопасности при работе со свинцом и на технологическом оборудовании кафедры ОМД.
Во время проведения работы категорически запрещается включать приводы технологического оборудования при отсутствии и без разрешения преподавателя.
10. Контрольные вопросы
- Какие ограничения имеет метод координатных сеток?
- Какие допущения приняты в программе при определении объема очага деформации?
- Каким образом осуществляется расчет средней величины коэффициента трения по Зибелю на контактной поверхности инструмента и заготовки?
- Каким образом определяется средняя по очагу деформации величина сопротивления деформации?
- Какие отличия имеют процессы прямого и обратного прессования?
- Какова роль сил трения в процессах прямого и обратного прессования?
- Что представляет собой процесс прессования с активным действием сил трения?
Библиографический список
1. Жолобов В.В. Прессование металлов. 2-е изд. перераб. и доп. /В.В.Жолобов, Г.И. Зверев. – М.: Металлургия, 1971. – 450 с.
2. Перлин И.Л. Теория прессования металлов /И.Л. Перлин, Л.Х.Райтбарг: 2-е изд. – М.: Металлургия, 1975. – 448 с.
3. Грабарник Л.М. Прессование цветных металлов / Л.М. Грабарник, А.А. Нагайцев. – М.: Металлургия, 1983. – 240 с.
4. Зиновьев А.В. Технология обработки давлением цветных металлов и сплавов /А.В. Зиновьев, А.И. Колпашников, П.И. Полухин, Ю.П.Глебов, Д.И. Пирязев, В.С. Горохов, А.М. Галкин // Учебник для вузов. – М.: Металлургия, 1992. – 512 с.
5. Щерба В.Н. Технология прессования металлов /В.Н. Щерба, Л.ХРайтбарг. – М.: Металлургия, 1995. –336 с.
6. Щерба В.Н. Прессование алюминиевых сплавов / В.Н. Щерба. – М.: Интермет Инжиниринг, 2001. – 768 с.
7. Колмогоров В.Л. Решение технологических задач ОМД на микро-ЭВМ /В.Л. Колмогоров, С.И. Паршаков, С.П. Буркин, Ю.Н.Логинов, Б.Н.Березовский, А.В. Коновалов, Б.М. Антошечкин // Учебное пособие для вузов. Под ред. В.А. Колмогорова и С.П. Паршакова. – М.: Металлургия, 1993. – 320 с.
8. Колмогоров В.Л. Механика обработки металлов давлением /В.Л.Колмогоров // Учебник для вузов. 2-е изд., перераб. и доп. – Екатеринбург: УГТУ-УПИ, 2001. – 836 с.
9. Логинов Ю.Н. Технология прессования и листовой прокатки специальных сплавов в решении задач /Ю.Н. Логинов, С.П. Буркин // Учеб. Пособие по курсу “Технология пластической обработки специальных сплавов”. Екатеринбург: УГТУ-УПИ, 2004. – 117 с.
Для заметок
Введение
Процессы прессования с прямым и обратным истечением металла (рис.1) известны достаточно давно. Уже с начала XIX века выявлены основные отличия и достоинства каждого из способов прессования.
Так, в области прессования сплошных профилей, наиболее предпочтительным оказалось обратное прессование, как обеспечивающее минимальное усилие прессования. При прессовании труб, наиболее эффективным оказалось прямое прессование. При повышенном, относительно обратного прессования, усилии прессования, оно обеспечивает меньший разностен пресс-изделий, а также имеет более простую конструкцию оборудования.
Значительное различие в усилии прессования при прямом и обратном способе принято объяснять наличием значительных сил трения при прямом прессовании, а также различием в объеме зоны металла, перешедшего в пластическое состояние – очага деформации.
Существующие теоретические способы расчета усилия прессования основаны на предположении, что очаг деформации ограничивается сектором сферы с центральным углом α (см. рис.1). При прямом прессовании принято считать, что угол α = 60º. При обратном прессовании угол α значительно больше, за счет чего объем очага деформации значительно уменьшается.
При заданном таким способом объеме очага деформации усилие на деформацию определяется следующим образом:
, (1)
где – объем очага деформации;
– интенсивность касательных напряжений сдвига;
– интенсивность скорости деформации;
– скорость прессования.
Следовательно, большое влияние на точность расчета усилия деформации при прессовании имеет точность определения границ очага деформации.
Таким образом, рассмотрим в данной лабораторной работе метод практического определения формы очага деформации при прямом и обратном прессовании сплошных профилей.
Для этих целей воспользуемся методом координатных сеток, позволяющих определить распределение степени деформации по сечению заготовки, и с достаточной точностью определить границы очага деформации.
Данный метод заключается в нанесении на продольный разъем цилиндрической заготовки координатной сетки, которая во время деформации искажается в соответствии с течением металла в очаге деформации. Анализ полученной после деформации сетки позволяет определить характер течения металла и форму очага деформации.
Так, для проведения эксперимента, воспользуемся цилиндрическим разъемным образцом длиной 70 - 100 мм и диаметром 50 мм с нанесенной на диаметральный разъем координатной сеткой с шагом 5 мм (см. рис. 6, 7 а).
Для успешного отслеживания изменения местоположения каждой конкретной точки (узла нанесенной сетки), а также для удобства ввода данных о координатах точки в ЭВМ для дальнейших расчетов, на каждой исследуемой сетке введена однозначная система нумерация узлов. Соответственно, при работе с деформированной сеткой, система нумерации точек должна повторять нумерацию исходного образца.
Для работы с сетками, как имеющими определенное количество строк и столбцов (сетки, вписанные в прямоугольный разъем детали) введена система нумерации, представленная на рис. 2. Точка с координатами (i,j) расположена на пересечении i-ой горизонтальной линии и j-ой вертикальной линии (i-я строка, j-й столбец).
Для значительного упрощения определения координат узлов сетки (как исходной, так и деформированной), работа по определению координат узлов проводится на ЭВМ путем обработки фотографии координатной сетки в цифровом виде (растрового изображения), см. рис. 3,7.
Первоначально, при работе программы, координаты узлов определяются в системе координат растрового изображения. После чего, значения координат пересчитываются в реальную систему координат, заданную мерным угольником с размерами внутренних граней 52 мм, помещенного при фотографировании в плоскость разъема образца (см. рис. 3, 7).
Так как, рассматриваемая ниже, методика определения деформированного состояния производит расчет для элемента сетки (четырехгранника, заключенного между 4-мя точками), то точкой приложения рассчитанных параметров, будем считать центр масс данного элемента. Номером элемента будем считать номер левого верхнего узла элемента (рис. 2 а).
Для расчета тензора деформации, определяется средняя величина деформации по элементу. Для чего, определялся усредненный тензор преобразования для элемента из начального положения в деформированное.
Так, рассмотрим определение тензора преобразования для двух векторов, соответствующих первым двум смежным точкам элемента – (i,j) и (i,j+1). При этом начало рассматриваемой системы координат сместим в центр масс элемента (рис.4).
Уравнение для определения тензора преобразования запишется в следующем виде:
; (2)
где: – матрица тензора преобразования.
Решив это уравнение относительно T, получим выражение для определения тензора преобразования для первых двух точек элемента:
. (3)
Аналогично для трех других пар точек элемента получим следующие выражения:
; (4)
; (5)
. (6)
Для определения усредненного тензора преобразования, усредним воздействие полученных четырех тензоров на единичные вектора исходного базиса:
. (7)
Для определения тензора деформации рассмотрим результат воздействия усредненной матрицы преобразования на единичные векторы базиса i и j (рис.5).
Как видно из рис.5, компоненты тензора деформации можно рассчитать следующим образом:
; (8)
; (9)
. (10)
Из условия не сжимаемости определим компонент тензора :
. (11)
Таким образом, мы получим девиатор тензора деформации вида:
. (12)
Для расчета величины степени деформации элементов воспользуемся формулой:
. (13)
При этом, форма очага при деформации определяется как линия уровня со степенью деформации на поле значений степени деформации, рассчитанной по формуле (13).
Под понимается такое значение степени деформации, превышение которого говорит о переходе данной точки металла в пластическое состояние.
Для оценки величины усилия, необходимого для деформации в процесса прессования, воспользуемся следующей формулой:
, (14)
где – максимальная интенсивность касательных напряжений сдвига;
– скорость деформации;
–скорость прессования;
– объем очага деформации.
Величина скорости деформации определяется по формуле [9]:
, (15)
где – коэффициент вытяжки при прессовании;
– диаметр контейнера;
– диаметр пресс-изделия;
– полуугол наклона мертвой зоны к оси прессования.
Таким образом, подставив в формулу (14) выражение (15) и определив из геометрических соображений значение величины , получим для определения усилия прессования следующие формулы.
Определение усилия деформации при прямом прессовании:
, (16)
где – сопротивление деформации металла;
– средняя длина очага деформации.
Значение средней длины очага деформации определяется как среднее расстояние от плоскости матрицы до границы очага деформации.
При определении объема очага деформации при прямом прессовании принято допущение о том, что очаг деформации ограничивается плоскостью матрицы и мертвыми зонами определяющимися полууглом .
Определение усилия деформации при обратном прессовании:
. (17)
При определении объема очага деформации при обратном прессовании принято допущение о том, что очаг деформации ограничивается плоскостью матрицы и занимает объем контейнера на длину . То есть, предполагаем, что объем мертвых зон приблизительно компенсируется объемом очага деформации проникающим в пресс-изделие.
При расчете усилия прессования по формулам (16), (17), примем значение полуугла равным 60º.
Для реализации описанного выше алгоритма на языке визуального программирования Borland C++ Builder v.6.0 написана программа Grid Analyser, предназначенная для работы с осесимметричными координатными сетками, нанесенными на осевой разъем цилиндрических образцов.
Общий вид рабочего окна программы приведен на рис.10.
Цели работы
Ознакомление со способом анализа деформированного состояния методом координатных сеток;
Определение параметров деформированного состояния при прямом и обратном прессовании свинца;
Определение зависимости размеров пластической зоны при прямом и обратном прессовании от коэффициента вытяжки.
Порядок выполнения работы
Фотографирование исходной координатной сетки на разъеме цилиндрического образца, предназначенного под прессование;
Прямое или обратное прессование заготовки с заданной вытяжкой;
Фотографирование деформированной координатной сетки;
Обработка полученных фотографий координатных сеток;
Определение зависимости средней относительной длины очага деформации от коэффициента вытяжки при прямом и обратном прессовании
Используемое оборудование и инструмент
Цифровой фотоаппарат Minolta DiMAGE X с расширением светочувствительной матрицы 2 мегапиксела;
Мерный уголок длиной внутренних сторон 52 мм и наружных 70 мм;
Экспериментальная оснастка, представляющая собой разъемный контейнер диаметром 50 мм со стяжными болтами, полый плунжер, сплошной плунжер и набор матриц;
Лабораторный вертикальный испытательный пресс усилием 500 кН;
Мерительный инструмент: штангенциркуль;
Персональный компьютер с программным обеспечением для анализа координатных сеток.
|
|
История создания датчика движения: Первый прибор для обнаружения движения был изобретен немецким физиком Генрихом Герцем...
История развития хранилищ для нефти: Первые склады нефти появились в XVII веке. Они представляли собой землянные ямы-амбара глубиной 4…5 м...
Архитектура электронного правительства: Единая архитектура – это методологический подход при создании системы управления государства, который строится...
Кормораздатчик мобильный электрифицированный: схема и процесс работы устройства...
© cyberpedia.su 2017-2024 - Не является автором материалов. Исключительное право сохранено за автором текста.
Если вы не хотите, чтобы данный материал был у нас на сайте, перейдите по ссылке: Нарушение авторских прав. Мы поможем в написании вашей работы!