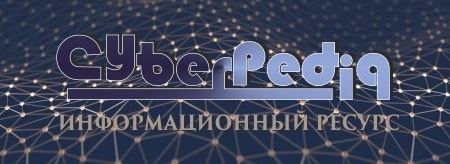
Особенности сооружения опор в сложных условиях: Сооружение ВЛ в районах с суровыми климатическими и тяжелыми геологическими условиями...
Общие условия выбора системы дренажа: Система дренажа выбирается в зависимости от характера защищаемого...
Топ:
Генеалогическое древо Султанов Османской империи: Османские правители, вначале, будучи еще бейлербеями Анатолии, женились на дочерях византийских императоров...
Оценка эффективности инструментов коммуникационной политики: Внешние коммуникации - обмен информацией между организацией и её внешней средой...
Интересное:
Мероприятия для защиты от морозного пучения грунтов: Инженерная защита от морозного (криогенного) пучения грунтов необходима для легких малоэтажных зданий и других сооружений...
Национальное богатство страны и его составляющие: для оценки элементов национального богатства используются...
Финансовый рынок и его значение в управлении денежными потоками на современном этапе: любому предприятию для расширения производства и увеличения прибыли нужны...
Дисциплины:
![]() |
![]() |
5.00
из
|
Заказать работу |
|
|
Введение Примерное
В настоящее время обеспечение ресурсосберегающего производства первичного алюминия возможно только на мощных электролизерах с предварительно обожженными анодами.
Разработка технологии и способов конструирования электролизеров с высокой амперной нагрузкой выполняется с применением методов математического моделирования магнитных полей на основе современных представлений тепло- и массопереноса в криолит-глиноземных расплавах.
Рационально ресурсосбережение достигается при высоких скоростях растворения глинозема и его смесей в кислых электролитах, высоком уровне контроля технологических параметров, уменьшения влияния магнитного поля на металл и рециклинге катодной футеровки и использовании высокоуправляемых систем автоматизированного питания глиноземом для работы электролизеров с максимальными технико-экономическими показателями.
В курсовом проекте содержатся расчеты: материального баланса, конструкции и количества электролизеров, электрические и тепловые расчеты, являющиеся основой оптимальной работы всего цеха.
Описательная часть Вопросы вставлять свои
Теоретические основы электролиза алюминия
Сущность электролитического метода получения алюминия заключается в следующем.
Требования к сырью для производства алюминия
В электролитическом производстве алюминия применяют следующие основные виды сырья и материалов:
Конструкция электролизера с обожженными анодами
Электролизер большой мощности – технологический агрегат для получения алюминия-сырца электролизом криолитоглиноземного расплава разработан специалистами ООО «РУСАЛ ИТЦ», для оснащения новых электролизных серий компании «РУСАЛ».
|
Устройство катодное
Катодное устройство предназначено для создания условий, необходимых для протекания процесса электролиза и отвода тока.
Устройство анодное
Анодное устройство предназначено для подвода тока в зону непосредственного протекания процесса электролиза и подачи сырья, а также для улавливания, выделяющихся при электролизе газов с последующей их эвакуацией в общую систему газоудаления.
1.3.3 Ошиновка катодная
Ошиновка катодная предназначена для отвода тока от электролизера и передаче его к следующему, а также для снижения негативного влияния магнитного поля на процесс.
Расчетная часть
Материальный баланс
В процессе электролиза криолитоглинозёмного расплава расходуется глинозём, фтористые соли и угольный анод. При этом образуется расплавленный алюминий и газообразные окислы углерода.
На основании опыта эксплуатации алюминиевых электролизёров ОА задаёмся параметрами для расчета электролизера:
- сила тока I = кА
- анодная плотность тока dа = А/см2
- выход по току h = %
Расход сырья N кг на получение 1 кг Al принимаем по практическим данным:
- глинозем, NГ = кг
- фтористый алюминий, NФа = кг
- фтористый кальций, NCа = кг
- анодные блоки, NМ = кг
Производство из двух серий. Для упрощения расчеты ведут на один час работы электролизера.
Производительность электролизера РА1, кг, рассчитывается по формуле:
РА1= j*I* τ *h (2.1)
где j - электрохимический эквивалент алюминия, 0,335 кг/(кА*час);
I - сила тока, кА;
τ - время, час;
h - выход по току, доли единицы.
PAl = 0,335 * = кг
Расчёт прихода сырья в электролизёр
Приход материалов в электролизёр рассчитывают по расходу сырья N на 1кг алюминия и производительности электролизёра в час PAl. Тогда приход сырья составит:
|
- глинозема RГ, кг
RГ =PAl *NГ (2.2)
RГ = = кг
- фтористых солей (А1F3,СаF2)RФ, кг
RФ =PAl* (NФа+ NCa) (2.3)
RФ = = кг
- обожженные аноды Rоа, кг
Rоа = PAl*Nоа (2.4)
Rоа = = кг
Расчёт потерь сырья
Теоретический расход глинозема составляет 1,89 кг на 1 кг алюминия. Перерасход глинозема объясняется наличием в его составе примесей и механическими потерями. Тогда потери глинозема G, кг, составят:
G = PAl* (Nг - 1,89) (2.13)
G =
Потери углерода Rуг, кг, находят по разности прихода обожженных анодов Rоа и расхода углерода, связанного в окислы:
Rуг = Rоа - (mcco2 + mcco) (2.14)
Rуг =
Приход фторсолей в электролизёр принимаем равным расходу. Данные расчета материального баланса приведены в таблице .
Таблица - Материальный баланс электролизера на силу тока кА
Приход | кг | % | Расход | кг | % |
Глинозем |
|
| Алюминий | ||
СО2 | |||||
СО | |||||
Фтористые соли |
|
| Потери: | ||
Глинозем | |||||
Фтористые соли | |||||
Анодные блоки | Анодные блоки | ||||
Итого | 100 | Итого | 100 | ||
*С учетом образования анодных газов и угольной пены |
Конструктивный расчет
В задачу конструктивного расчета входит определение основных размеров электролизера. Алюминиевый электролизер состоит из трех основных частей:
- анодное устройство;
- катодное устройство;
- ошиновка.
Электрический расчет
Электрическим балансом называют представление напряжения U в виде суммы составляющих ее величин. В практике электролиза различают три вида напряжений: среднее, рабочее и греющее.
Электрический баланс электролизера определяется по следующему уравнению, В:
Uср = Ua + Uп + Uэл + ΔUaэ + Uо + Uоо + Ер, (2.32)
где Ua – падение напряжения в анодном устройстве, В;
Uп – падение напряжения в подине, В;
Uэл – падение напряжения в электролите, В;
ΔUаэ – доля падения напряжения при анодных эффектах, В;
|
Uo – падение напряжения в ошиновке электролизера, В;
Uoo – падение напряжения в общесерийной ошиновке, В;
Ер – напряжение разложения глинозема (или ЭДС поляризации), В.
Падение напряжения в аноде
В данном электролизере применяются трехниппельные анодные блоки типа Б по ТУ 1913-001-00200992-95.
![]() | |||||
![]() ![]() | |||||
![]() |
Рисунок 2 – Трехниппельный анодный блок. Тип Б
Падение напряжения в обожженном аноде складывается из падения напряжения в угольной части UУГ, в контактах ниппель-анод UНА, кронштейн-ниппель UКН, штанга-кронштейн UШК, и в штанге, кронштейне и ниппеле.
Падение напряжения в угольной части анода ΔUуг, В, рассчитывают по уравнению:
Uуг= (2.34)
где ρa – удельное электросопротивление анода, Ом * см;
l – среднее расстояние от подошвы анода до дна ниппельного гнезда, 46 см;
Sa – площадь сечения одного блока, 10 150 см2;
nH – число ниппелей, 3
Удельное электросопротивление угольного анода ρа, Ом * см:
ρа = 0,007 * (1 – 0,00025 * tанода) (2.35)
ρа = 0,007 * (1 – 0,00025 * 640) = 58,8 * 10-4 Ом * см
Uуг = = 0,080 В
Падение напряжения в алюминиевой штанге Uшт, В:
Uшт= , (2.36)
где ρшт – удельное сопротивление штанги, 3,54 * 10-6 Ом*см;
l – длина штанги 255,5 см;
I – сила тока, А;
Sшт – площадь сечения штанги, 14*15,6 = 218,4 см2;
Nб - число анодных блоков.
Uшт = = 0,0374 В
При проектировании нового электролизера очень важно знать величину падения напряжения во всех анодах. Для упрощения расчета можно воспользоваться практическими данными, которые неоднократно подтверждались, приведенными в таблице 15.
Таблица 15 - Падение напряжения в трехниппельном аноде по практическим данным
Размеры в вольтах
Наименование участка анода | Величина |
в кронштейне Uкр | 0,0016 |
в ниппеле Uн | 0,0027 |
в контакте ниппель-анод Uна | 0,22 |
в контактах ниппель-кронштейн и штанга-кронштейн Uнкшк | 0,006 |
Таким образом, падение напряжения в обожженном аноде составляет:
Ua = Uуг + Uшт + Uкр + Uн + Uна + Uнкшк (2.37)
Ua = 0,080 + 0,0374 + 0,0016 + 0,0027 + 0,22 + 0,006 = 0,348 В
Падение напряжения в подине
|
Падение напряжения в подине Uп, В, определяем по уравнению М. А. Коробова и А. М. Цыплакова:
Uп= , (2.38)
где lпр – приведенная длина пути тока по блоку, см;
ρбл – удельное сопротивление прошивных блоков, принимаем 3,72*10-3 Ом*см;
Вш – половина ширины шахты ванны, 188 см;
а – ширина настыли, расстояние от продольной стороны анода до боковой футеровки, см;
Sст – площадь сечения стержня, см2;
da – анодная плотность тока, А/см2.
Приведенную длину пути тока по блюмсу lпр, см, определяем по уравнению:
lпр = 2,5 + 0,92 * hб – 1,1 * hст + (2.39)
где hб – высота блока, 40 см;
hст – высота стержня, 14,5 см.
Вст– ширина блюмса с учётом заделки 26,5 см
lпр = 2,5 + 0,92 * 40 – 1,1 * 14,5 + = 28,33 см
Ширина подового блока с учетом набивного шва Bбл, см:
Вбл = bб + с (2.40)
Вбл = 55 + 4 = 59 см
Площадь сечения катодного стержня Sст, см2, с учетом заделки равна:
Sст = hст * Вст (2.41)
Sст = 14,5 * 26,5 = 384 см2
Тогда падение напряжения в подине Uп, В, составит:
Uп = = 155,60 мВ
Тепловой баланс
Нормальная работа электролизёра возможна только при соблюдении теплового равновесия, т. е. когда приход и расход тепла в единицу времени при установившемся режиме электролиза становятся равными:
Qпр = Qрасх (2.44)
Приход тепла
Приход тепла от прохождения электрического тока Qэл, кДж, определяется по уравнению:
Qэл = 3600 * I * Uгр* , (2.45)
где 3600 – тепловой эквивалент одного кВт * ч, кДж;
I – сила тока, кА;
Uгр – греющее напряжение, В;
– время, часы.
Qэл =
Приход тепла от сгорания угольного анода Qан, кДж, определяется следующей зависимостью:
Qан = Р1СО2 * ΔНТСО2 + Р1СО * НТСО, (2.46)
где Р1СО2 и Р1СО – число киломолей оксидов углерода; определяется по материальному балансу исходя из формул;
ΔНТСО2 и ΔНТСО – тепловые эффекты реакций образования СО2 и СО из углерода и кислорода при 25 °С (298 К):
ΔН298СО2 = 393769 кДж/кмоль
ΔН298СО = 110532 кДж/кмоль
Р1CO2 = (2.47)
P1CO2 =
Р1CO = (2.48)
Р1CO =
Qан =
Расход тепла
На разложение глинозёма расходуется тепла Qг, кДж:
Qг = R1Г * ΔНТГ, (2.49)
где R1Г – расход глинозёма, кмоль;
ΔНТГ – тепловой эффект образования оксида алюминия при 25 °С (298 К), равный 1676000 кДж/кмоль.
R1Г = (2.50)
R1Г =
Qг =
Потери тепла с выливаемым из ванны алюминием рассчитываются исходя из условия, что количество вылитого алюминия соответствует количеству наработанного за то же время. При температуре выливаемого алюминия:
|
- 960 °С энтальпия алюминия ΔНТ1Al составляет 43 982 кДж/кмоль,
- 25 °С энтальпия алюминия ΔHT2Al равна 6 716 кДж/кмоль.
Тогда потери тепла QAl, кДж, с выливаемым алюминием составят:
QAl = P1Al * (ΔНТ1Al - ΔНТ2Al), (2.51)
где P1Al – количество наработанного алюминия, кмоль, определяемого по формуле:
P1Al = (2.52)
P1Al = = кмоль
QAl = = кДж
Унос тепла с газами рассчитываем на основные компоненты анодных газов - оксид и диоксид углерода. Тогда унос тепла с газами Qгаз, кДж, будет равен:
Qгаз = P1CO * (ΔНТ1CO - ΔНТ2CO) + P1CO2 * (ΔНТ1CO2 - ΔНТ2CO2) (2.53)
где P1CO и P1CO2 – количество СО и CO2, кмоль;
ΔНТ1CO – энтальпия СО при температуре 550 °С, равна 24 860 кДж/кмоль;
ΔНТ2CO – энтальпия СО при температуре 25 °С, равна 8 816 кДж/кмоль;
НТ1CO2 – энтальпия СО2 при температуре 550 °С, равна 40 488 кДж/кмоль;
НТ2CO2 – энтальпия СО2 при температуре 25 °С соответственно, 16446 кДж/кмоль.
Qгаз = = кДж
Потери тепла за счет теплопроводности для плоской однослойной стенки определяется на основании закона Фурье и рассчитывается по уравнению:
Qтеп = λ * (t1 - t2) / δ (2.54)
где λ – коэффициент теплопроводности, кДж/(м*ч*град);
δ – толщина стенки, м;
(t1 - t2) – разница температур внутренней и наружной стенок, ºС.
Потери тепла конвекцией с наружных стенок электролизера определяют по формуле Ньютона – Рихмана:
Qк = αк * (tс – tв)·F, (2.55)
где αк – коэффициент теплоотдачи конвекцией от стенок к воздуху, кДж/(м2*ч*град);
tс, tв – температура стенки и воздуха соответственно, ºС;
F – площадь поперечного сечения стенки, м2.
Коэффициент теплоотдачи находят по следующей формуле:
αк = А * Δt1/3 (2.56)
где Δt – разность температур стенки и среды, °С;
А – коэффициент, зависящий от свойств среды и определяющей температуры, под которой понимают:
tm = 0,5 * (tс + tв) (2.57)
Потери тепла лучеиспусканием в общем виде представлены уравнением:
Qл = ε * С0 * F * [(Тс/100)* 4 – (Тв/100) * 4] * φ, (2.58)
где ε – степень черноты тела, доли единицы;
С0 – коэффициент лучеиспускания абсолютно черного тела (С0 = 20,75 кДж/(м2*ч*К));
φ – угловой коэффициент взаимного облучения данной поверхности соседними поверхностями, доли единицы;
F – площадь поверхности, м2;
Тс и Тв – температура стенки и среды соответственно, К.
Для расчета тепловых потерь с конструктивных элементов электролизера пользуются данными замеров температуры стенок и воздуха, произведенных на действующих электролизерах.
При установившемся тепловом потоке
Qтеп = Qк + Qл= αк * (tс – tв) * F (2.59)
Площадь поверхности анода:
S = 369 342-36*3*153 = 385 866 см2 = 38,59 м2
где 348 823 см2 – площадь анода;
36 – количество анодных блоков;
3 – количество ниппелей в аноде;
153 см2 – площадь ниппеля.
Площадь глиноземной засыпки на поверхности электролита:
Fглин.засып.= Lшах* Вшах – Sан (2.60)
Fглин.засып = 14,96 * 3,75 – 36,93 = 19,17 м2
Открытая поверхность электролита:
4 *·(3,14·* 2,52) + 300 = 378 см2 = 0,0378 м2
5 см – диаметр отверстия под пробойником АПГ
4 – количество пробойников
300 см2 – средняя открытая площадь электролита, связанная с технологической обработкой электролизера.
Фланцевый лист:
Fфл. лист = Нлиста·* Вкож + Нлиста·* Lкож (2.61)
Fфл. лист= 0,25 * 4,49+0,25·* 13,09 = 4,395 м2
Число катодных блюмсов равно удвоенному числу подовых катодных секций.
Площадь блюмсов: Катодных блоков 24, а не 30
Fбл = (2·* Нбл·* Lбл + 2·* Нбл·* Вбл)·* Nшт (2.62)
Fбл = (2 * 30 * 23 + 2 * 30 * 11,5) * 22 = 45540 см2 = 4,554 м2
Площадь катодного кожуха:
Fкож = Lкож·* Bкож = 3,89 * 14,31 = 55,67 м2 (2.63)
Потери тепла в окружающую среду определяются на основании законов теплоотдачи конвекцией, излучением и теплопроводностью. Теоретические расчеты показывают, что в первом приближении потери тепла конструктивными элементами электролизера, с поверхности электролита и корки можно принять как разность между приходом и расходом тепла по рассчитанным статьям:
Qп = (Qэл + Qан) – (Qг + QAl + Qгаз) (2.64)
Qп = (5 207 553+ 947 688) – (3 294 010 + 144 331 + 71 330) = 2 645 570 кДж
Таблица 17 – Тепловой баланс электролизера на силу тока кА
Приход тепла | кДж | % | Расход тепла | кДж | % |
От прохождения электроэнергии |
|
| На разложение глинозема | ||
С вылитым металлом | |||||
От сгорания угольного анода |
|
| С отходящими газами | ||
Конструктивными элементами и с поверхности электролизера | |||||
ИТОГО | 100 | ИТОГО | 100 |
Расчет цеха
Переменный ток напряжением 220 кВ от энергосистемы поступает на понизительные подстанции завода, где напряжение понижается до 10 кВ. Далее через распределительные системы шин переменный ток подаётся на кремниево – преобразовательные подстанции (КПП), где преобразуется в постоянный, а напряжение понижается до 1 500 В.
КПП сооружаются вблизи электролизных корпусов, чтобы избежать больших потерь постоянного тока в ошиновке на участке от подстанции до электролизёра, а также больших затрат на устройство шинопроводов. Серия электролиза алюминия состоит из 2 корпусов и питается постоянным током от одной КПП.
Расчет цеха
Цех состоит из 2 серий. В цехе установлено электролизеров, Nуст:
Nуст = Ny * n (2.69)
Nуст = 312 * 2 = 624
из них рабочих
Nц = Nc * n (2.70)
Nц
Годовая производительность цеха Рц, т, рассчитывается по формуле:
Рц = j * I * η * 8 760 * N * 10-3, (2.71)
где j – электрохимический эквивалент алюминия, кг/(кА*ч);
I – сила тока, кА;
η - выход по току, д. е.;
8 760 – часов в год;
N – число работающих ванн в корпусе.
Рц =
Удельный расход электроэнергии W, кВт*ч/т:
W = (2.72)
W = = кВт*ч/т
Выход по энергии ηэ, г/кВт*ч:
ηэ = (2.73)
ηэ = = г/кВт*ч
На основании рассчитанных параметров и показателей производственная программа цеха приведена в таблице 18
Таблица 18 - План производства алюминия электролизного цеха из 2 серий
Показатели, ед. изм. | Формула | Количество |
Установлено электролизеров, шт. | Ny | |
Ванны подлежащие капитальному ремонту, шт. | a= ![]() | |
Длительность простоя одной ванны в капитальном ремонте, дней | t | |
Длительность планового ремонта, дней | T | |
Число электролизеров в резерве, штук. | n | |
Число рабочих электролизеров, штук. | Nц | |
Сила тока, А | I | |
Выход по току, % | η | |
Производительность электролизера, т/сутки | m=PAl*24 | |
Среднее напряжение на ванне, В | Uср | |
Удельный расход электроэнергии, кВт*ч/т | W | |
Производительность цеха, т/год | Рц |
Заключение
Согласно заданию на курсовой проект «Расчет двух серий электролизёров на силу тока кА» в проекте была использована современная технология электролиза глинозема в электролизерах с катодами шпангоутного типа и с обожженными анодами.
Проведенные технические расчеты показали следующие результаты:
- производительность одного электролизера 2,307 т/сутки;
- производительность цеха в год 523 876 тонн алюминия;
-
В проекте представлены
Приведены мероприятия по , способствующие
Введение Примерное
В настоящее время обеспечение ресурсосберегающего производства первичного алюминия возможно только на мощных электролизерах с предварительно обожженными анодами.
Разработка технологии и способов конструирования электролизеров с высокой амперной нагрузкой выполняется с применением методов математического моделирования магнитных полей на основе современных представлений тепло- и массопереноса в криолит-глиноземных расплавах.
Рационально ресурсосбережение достигается при высоких скоростях растворения глинозема и его смесей в кислых электролитах, высоком уровне контроля технологических параметров, уменьшения влияния магнитного поля на металл и рециклинге катодной футеровки и использовании высокоуправляемых систем автоматизированного питания глиноземом для работы электролизеров с максимальными технико-экономическими показателями.
В курсовом проекте содержатся расчеты: материального баланса, конструкции и количества электролизеров, электрические и тепловые расчеты, являющиеся основой оптимальной работы всего цеха.
Описательная часть Вопросы вставлять свои
Теоретические основы электролиза алюминия
Сущность электролитического метода получения алюминия заключается в следующем.
Требования к сырью для производства алюминия
В электролитическом производстве алюминия применяют следующие основные виды сырья и материалов:
|
|
Общие условия выбора системы дренажа: Система дренажа выбирается в зависимости от характера защищаемого...
Эмиссия газов от очистных сооружений канализации: В последние годы внимание мирового сообщества сосредоточено на экологических проблемах...
Кормораздатчик мобильный электрифицированный: схема и процесс работы устройства...
Механическое удерживание земляных масс: Механическое удерживание земляных масс на склоне обеспечивают контрфорсными сооружениями различных конструкций...
© cyberpedia.su 2017-2024 - Не является автором материалов. Исключительное право сохранено за автором текста.
Если вы не хотите, чтобы данный материал был у нас на сайте, перейдите по ссылке: Нарушение авторских прав. Мы поможем в написании вашей работы!