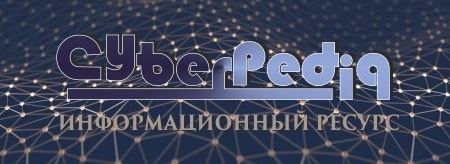
Механическое удерживание земляных масс: Механическое удерживание земляных масс на склоне обеспечивают контрфорсными сооружениями различных конструкций...
Эмиссия газов от очистных сооружений канализации: В последние годы внимание мирового сообщества сосредоточено на экологических проблемах...
Топ:
Техника безопасности при работе на пароконвектомате: К обслуживанию пароконвектомата допускаются лица, прошедшие технический минимум по эксплуатации оборудования...
Отражение на счетах бухгалтерского учета процесса приобретения: Процесс заготовления представляет систему экономических событий, включающих приобретение организацией у поставщиков сырья...
Определение места расположения распределительного центра: Фирма реализует продукцию на рынках сбыта и имеет постоянных поставщиков в разных регионах. Увеличение объема продаж...
Интересное:
Средства для ингаляционного наркоза: Наркоз наступает в результате вдыхания (ингаляции) средств, которое осуществляют или с помощью маски...
Лечение прогрессирующих форм рака: Одним из наиболее важных достижений экспериментальной химиотерапии опухолей, начатой в 60-х и реализованной в 70-х годах, является...
Мероприятия для защиты от морозного пучения грунтов: Инженерная защита от морозного (криогенного) пучения грунтов необходима для легких малоэтажных зданий и других сооружений...
Дисциплины:
![]() |
![]() |
5.00
из
|
Заказать работу |
|
|
Сбор, транспортирование и подготовка газа и конденсата на газовых месторождениях существенно отличается от сбора, транспортирования и подготовки нефти, газа и воды на нефтяных месторождениях. Основное отличие, прежде всего, сводится к тому, что на нефтяных месторождениях мы имеем дело с добычей и транспортированием вязких нефтяных эмульсий по трубопроводам, а на газовых месторождениях – с добычей и транспортированием маловязких «чистых» газов и газоконденсатных смесей.
Газ на газовом месторождении собирается для подачи на головную компрессорную станцию, которая транспортирует его по магистральному газопроводу к потребителям с возможно меньшими гидравлическими потерями, капитальными и эксплуатационными расходами.
Элементы газосборной сети являются общими для разных месторождений и состоят обычно из фонтанных елок, газоотводящих линий (манифольдов, шлейфов), отключающих задвижек газосборных коллекторов, конденсатопроводов, промысловых газосборных пунктов (ПГСП) (рис. 10.1, а, б, в, г).
Форма газосборных коллекторов зависит, прежде всего, от конфигурации площади месторождения (вытянутая, круглая), от размещения скважин на ней, от числа и характеристики продуктивных горизонтов и принятой схемы осушки, очистки и учета газа по скважинам. Название газосборной системы определяется обычно формой газосборного коллектора. Если газосборный коллектор представляет собой одну линию, схема сбора называется линейной (рис.10.1, а). Когда газосборные коллекторы сходятся в виде лучей к центральному сборному пункту, схема называется лучевой системой (рис. 10.1, б). При кольцевой системе газосборный коллектор огибает площадь газоносного месторождения (рис. 10.1, в). Групповая система сбора применяется при наличии на промысле групповых пунктов сепарации газа (рис. 10.1, г).
|
Система сбора выбирается исходя из необходимости обеспечения бесперебойной подачи газа потребителям, маневренности, удобства обслуживания газосборной сети и минимальных расходов на ее сооружение и эксплуатацию.
Кольцевая система сбора газа более маневренная, так как при аварии на каком-нибудь участке этой системы перекрытием отключающих задвижек можно обеспечить бесперебойную работу всей газосборной сети. Другие системы сбора этому условию не удовлетворяют.
Однако с точки зрения удобства обслуживания скважин, сепараторов и применения средств автоматики групповая система сбора более предпочтительна. При этом применяют шлейфы высокого давления и сравнительно малого диаметра (100-150 мм). При малом числе скважин на месторождении групповая система сбора газа превращается в бесколлекторную.
Рис. 10.1 Схемы сбора газа на газовом промысле:
а – линейная; б – лучевая; в – кольцевая: г – групповой метод сбора и переработки газа с линейными коллекторами; 1 – скважины; 2 – шлейфы; 3 – линейный газосборный коллектор; 4 – контур газоносности; 5 – кольцевой газосборный коллектор;
ГСП – групповой сборный пункт; МГ – магистральныйгазопровод
Для многопластовых месторождений с различными пластовыми давлениями часто применяют раздельный сбор газа по разным газосборным сетям. Разные газосборные сети строят также в том случае, если газ одного из продуктивных горизонтов содержит большое количество конденсата, сероводорода или углекислого газа.
При составлении схемы подготовки газа к транспорту учитывают также наличие поблизости месторождения действующих УКПГ, дожимных компрессорных станций (ДКС), газоперерабатывающих заводов и установок и степень загрузки их мощностей, характеристику выпускаемого промышленностью оборудования, возможность обеспечения объектов водой, теплом, химическими реагентами и так далее.
|
Проектирование систем сбора продукции скважин включает в себя в первую очередь определение производительности и диаметра указанных газопроводов, гидравлический расчет и мероприятия по предупреждению гидратообразования и коррозии.
Один из основных вопросов систем сбора газа – это выбор шлейфов – трубопроводов, предназначенных для подачи газа от устья скважин до установок комплексной подготовки газа. Шлейфовые газопроводы характеризуются диаметром, пропускной способностью, температурным режимом, перепадом давления в них и так далее.
Наибольшее применение на газовых и газоконденсатных месторождениях получила централизованная система сбора. Газ и газовый конденсат от группы скважин по индивидуальным газопроводам – шлейфам поступают на УКПГ и затем после подготовки на каждой УКПГ – в газосборный коллектор и на головные сооружения (ГС). Следует отметить, что на первых стадиях разработки газовых месторождений широко применяли индивидуальные схемы сбора газа, когда на каждую скважину устанавливали свой комплекс оборудования для подготовки газа. Эта схема сбора газа отличалась высокой степенью надежности, так как выход из строя одной индивидуальной установки не прекращает работы всей системы. Однако из-за ряда крупных недостатков: большой металлоемкости и рассредоточенности объектов, повышенной численности обслуживающего персонала, сложной системы водо- и теплоснабжения – эта система в настоящее время не применяется.
На современных газовых месторождениях система сбора и подготовки газа включает следующие сооружения: установку предварительной подготовки газа (УППГ), УКПГ и ГС. Это общая схема, так как в зависимости от характера месторождения (чисто газовое или газоконденсатное) и других факторов процессы подготовки газа могут в основном сосредотачиваться на УППГ, УКПГ или на УКПГ и ГС. Например, если месторождение чисто газовое, то вся подготовка газа сосредотачивается на УКПГ, а на УППГ выполняют только замер объемов продукции, поступившей от каждой газовой скважины. На газоконденсатных месторождениях на УППГ выполняют не только замер объема продукции каждой скважины, но и частичное отделение влаги и конденсата.
Требования к качеству товарного газа
|
Вследствие того, что природный газ транспортируют на большие расстояния от мест добычи до потребителя по магистральным газопроводам, пересекающим различные климатические зоны, особое значение приобретает вопрос качественной его обработки и осушки до точки росы, исключающей конденсацию воды из газа.
Наличие в газе влаги, жидких углеводородов, агрессивных и механических примесей снижает пропускную способность газопроводов, повышает расход ингибиторов, усиливает коррозию, увеличивает потребную мощность компрессорных агрегатов, способствует забиванию линий контрольно – измерительных и регулирующих приборов.
Все это снижает надежность работы технологических систем, увеличивает вероятность аварийных ситуаций на компрессорных станциях и газопроводах.
Кроме того, пыль и механические примеси способствуют истиранию металла и, осаждаясь на поверхностях теплообменных аппаратов, ухудшают их тепловые характеристики.
Если при транспортировании газа падает давление, то повышается равновесная влагоемкость, тем самым делая газ менее насыщенным. При постоянной температуре не произойдет выделения капельной влаги из такого газа.
Если при танспортировании газа понижается его температура, то при постоянном давлении уменьшается равновесная влагоемкость такого газа: газ станет перенасыщенным. В этом случае часть капельной влаги конденсируется и выпадает в трубе.
Показатели качества товарного газа основаны на следующих требованиях:
а) газ при транспортировке не должен вызывать коррозию трубопровода, арматуры, приборов и так далее;
б) качество газа должно обеспечить его транспортировку в однофазном состоянии, то есть не должно произойти образования и выпадения в газопроводе углеводородной жидкости, водяного конденсата и газовых гидратов;
в) товарный газ не должен вызывать осложнений у потребителя при его использовании.
Для того чтобы газ отвечал указанным требованиям, необходимо определять точку росы по воде, содержание углеводорода, содержание в газе сернистых соединений, механических примесей и кислорода.
Важный показатель качества товарного газа – содержание в нем кислорода. Значение этого показателя – не более 1 %. При большем содержании кислорода газ становится взрывоопасным. Кроме того, кислород способствует усилению коррозии в системе.
|
Отраслевой стандарт не устанавливает конкретное содержание отдельных углеводородов в товарном газе. Это связано с разнообразием составов сырьевого газа.
В стандартвведен новый показатель, ограничивающий содержание меркаптановой серы в товарном газе не более 36 мг/м3.
В газе могут содержаться также сероокись углерода (СОS), сероуглерод (СS2) и др. В стандарте содержание этих компонентов не указаны. Следовало бы установить общее количество всех сернистых соединений в газе.
Несомненно, обеспечение надежности транспортировки, хранения и использования продукции газовой промышленности должно отвечать определенным требованиям, изложенным в соответствующих стандартах и технических условиях.
Однако на практике бывают ситуации, когда экономически нецелесообразно производство продукции, отвечающей всем требованиям регламентирующих документов.
Например, на заключительном этапе разработки газоконденсатных месторождений для получения товарного газа, отвечающего требованиям отраслевого стандарта, необходимо вводить установки искусственного холода (УИХ). Затраты на строительство и эксплуатацию УИХ значительно превышают прибыль от выхода дополнительной продукции УКПГ. Для поддержания высокой эффективности работы газотранспортных систем предложен комплексный подход к определению показателей качества газа. Суть предложения сводится к тому, чтобы не внедрять ОСТ на каждом месторождении, связанном с одним магистральным трубопроводом, а на основном месторождении установить более высокие показатели качества газа, чем по стандарту. За основное можно принимать наиболее крупное месторождение из рассматриваемой группы с тем, чтобы на нем было экономически выгодно применять сложную технологию, позволяющую на всех этапах разработки осуществлять осушку газа по влаге и извлечению тяжелых углеводородов.
Базовыми могут служить месторождения, в газе которых содержится сероводород, так как на газоперерабатывающих заводах после сероочистки необходимо проводить осушку на гликолевых установках или охлаждать весь объем газа с использованием искусственного холода.
Практически без больших дополнительных затрат на базовых месторождениях или на газоперерабатывающих заводах можно готовить газ с точкой росы по влаге и углеводородам ниже, чем регламентировано стандартом. Это позволит подавать в магистральный газопровод газ, добываемый на небольших месторождениях, находящийся вдоль трассы, без организации сложных систем промысловой подготовки газа, осуществляя только отделение жидкой фазы.
|
Применение такой системы промысловой подготовки газа дает возможность сконцентрировать сложное промысловое оборудование на одном базовом месторождении, мелкие месторождения обустраивать по упрощенным схемам.
Основные требования к технологическим процессам промысловой и заводской обработки природных и нефтяных газов – это обеспечение показателей качества товарного газа и другой продукции газовой промышленности.
Следует отметить, что в настоящее время единых международных норм по допустимым содержаниям сероводорода, углекислоты, сероорганических соединений, азота, воды, механических примесей и так далее не существует.
10.3. Условия образования гидратов
Содержание в газе паров воды в капельном состоянии приводит к неприятным последствиям при сборе и транспортировании этого газа. При контакте газа, имеющего высокое давление, с водным конденсатом образуются гидраты, которые, отлагаясь на стенках газопровода, уменьшают его пропускную способность, а в некоторых случаях приводят к полному прекращению подачи газа.
Гидраты природных газов образуются только при наличии в этих газах паров воды.
Пары воды могут насыщать газ до определенного давления, равного давлению насыщенного водяного пара при данной температуре. Это предельное содержание водяных паров при данной температуре называется точкой росы. Если содержание водяных паров превышает этот предел, то начинается их конденсация, то есть переход в жидкое состояние.
Принято различать абсолютную и относительную влажность газа. Под абсолютной влажностью понимают массовое количество водяных паров, содержащихся в 1 м3 газа при нормальных условиях. Массовое количество водяного пара в газе выражается в г/м3 или в кг на 1000 м3 газа. Под относительной влажностью понимается отношение фактически содержащегося в газе водяного пара к максимально возможному при данных температуре и давлении.
Газовые гидраты представляют собой кристаллические соединения, образуемые ассоциированными молекулами углеводородов и воды. Они внешне напоминают снег или лед.
По структуре газовые гидраты – это клатраты, которые образуются при внедрении молекул газа в пустоты кристаллических структур, составленных из молекул воды.
Различают два типа кристаллической решетки гидратов: структура 1 построена из 46 молекул воды и имеет 8 полостей; структура 2 построена из 136 молекул воды, имеет 16 малых и 8 больших полостей.
Метан, этан, двуокись углерода образуют гидраты первой структуры. При этом идеальная формула гидрата будет 8М×46 Н2О (М – молекула гидратообразователя).
Метан образует гидрат, имеющий формулу СН4×6Н2О. Массовое содержание метана в составе гидрата составляет 12,9 %. Для связывания 1 кг метана в гидрат, соответствующий указанной формуле, требуется 6,75 кг воды. При добыче и обработке газов образуются смешанные типы гидратов. Установлено, что пропан и изобутан наиболее склонны к гидратообразованию.
Для образования гидратов необходимы наличие капельной воды и определенный термодинамический режим в системе. Наличие воды в жидкой фазе хотя и является обязательным условием, но недостаточно для образования гидратов. Образование гидратов происходит при определенных температурах и давлениях и зависит от состава газа. Для предупреждения гидратообразования необходимо снизить давление газа или повысить его температуру.
При снижении давления влагоемкость газа повышается, и он становится недонасыщенным при заданной температуре. Поэтому не происходит конденсации водяных паров и выпадения капельной влаги.
Ликвидация гидратов снижением давления связана с выбросом газа в атмосферу или снижением пропускной способности газопровода. Поэтому применение этого способа ограничено. Его нельзя использовать при температурах ниже 0 °С, так как вода, образовавшаяся в результате разложения гидратов, может замерзать и образовывать ледяные пробки.
Разложение гидратов подогревом системы применяют для обеспечения работы дроссельных устройств, теплообменников и коротких участков газопроводов.
Наиболее распространенный способ ликвидации гидратных пробок – это подача в систему соответствующих ингибиторов. Пары ингибитора насыщают газовую фазу и снижают парциальное давление паров воды над гидратом, что приводит к его разрушению.
10.4. Ингибиторы гидратообразования и их свойства
Для предотвращения гидратообразования широко применяют ингибирование газа специальными реагентами подачей их в поток. В качестве ингибиторов можно использовать водные растворы метанола, гликолей, гликолевых эфиров, некоторых солей.
Водные растворы ди- и триэтиленгликолей в качестве ингибитора предпочтительно применять до температур – 10 °С. При низких температурах разделение гликолевого раствора и углеводородного конденсата происходит очень трудно.
Водные растворы этиленгликоля (ЭГа) можно использовать при температуре – 35 °С. При более низких температурах он становится трудно перекачиваемым, часть раствора постепенно накапливается в трубопроводах, что увеличивает потери давления на установке.
При температурах ниже – 40 °С в качестве ингибитора для предупреждения гидратообразования рекомендуется применять метанол.
Иногда возможно также применение комбинированных ингибиторов, состоящих из нескольких веществ. К ним можно отнести смеси гликоля с метанолом и бутиллактоном (БЛО), метилпирролидоном и так далее.
Для борьбы с гидратообразованием используют этилкарбитол, являющийся побочным продуктом производства эфиров гликолей. Этилкарбитол в основном состоит из моноэтилового эфира диэтиленгликоля и этиленгликоля (около 95 %), в состав раствора входят также ДЭГ (1 %), этилцеллозоли, пропиленгликоль и вода. Этилкарбитол – прозрачная, бесцветная жидкость с температурой замерзания – 60 °С и кипения 202 °С. Плотность при 20 °С составляет 0,99 кг/л и вязкость – 4,5 МПа×с.
При проектировании систем добычи, сбора и обработки газов необходимо принять во внимание следующее:
а) ввиду большой вязкости и плотности, гликоли склонны к скоплению в отдельных неровных участках шлейфовых газопроводов, образуя так называемые «застойные зоны», что приводит к уменьшению свободного сечения газопроводов и, следовательно, к увеличению их гидравлических потерь; при использовании водных растворов метанола вероятность образования «застойных зон» мала, поэтому в скважины и шлейфы чаще всего подают водные растворы метанола;
б) метанол более летуч, ввиду чего его потери в газовой фазе на два порядка больше, чем потери гликолей;
в) из-за низкой температуры застывания метанола и его растворов хранение их в условиях Крайнего Севера требует меньше эксплуатационных затрат, чем хранение ДЭГа и его растворов; кроме того, метанол в 7 – 8 раз дешевле, чем гликоли.
На практике для борьбы с гидратообразованием в стволах скважин и шлейфах газопроводов используют водные растворы метанола. Растворы гликолей применяют для обеспечения безгидратной работы установок низкотемпературной сепарации (НТС).
Метанол представляет собой бесцветную прозрачную жидкость плотностью 0,81 и молекулярной массы 32,04. С водой смешивается в любых отношениях. Упругость паров метанола при температуре 20 °С составляет 11864 Па. Температура кипения при атмосферном давлении равна 64,7 °С, а температура замерзания – 97,1 °С.
МЕТОДЫ ПОДГОТОВКИ ПРИРОДНОГО ГАЗА
11.1. Основные процессы подготовки
Физические методы переработки продукции месторождений основаны на процессах следующих трех групп.
1. Газогидромеханические процессы, скорость протекания которых определяется законами газогидродинамики (сепарация, центрифугирование, фильтрация и тому подобное).
2. Тепловые процессы, скорость протекания которых определяется законами теплопередачи (охлаждение, нагревание и конденсация).
3. Массообменные (диффузионные) процессы, скорость которых определяется законами массопередачи.
Промысловая подготовка газа – это разделение многокомпонентных газообразных или жидких смесей с использованием сепарации, фильтрации, абсорбции, адсорбции, ректификации и экстракции.
Сепарационные процессы – отделение жидких или твердых частиц газа, наиболее распространены при подготовке в заводских условиях.
Технологические схемы практически всех промысловых установок и дожимных компрессорных станций (ДКС) включают в себя те или иные сепарационные процессы, которые служат для разделения жидких и газовых фаз, образовавшихся при изменении температуры и давления смеси, а также для отделения механических примесей из газов и жидкостей.
Установки подготовки газа к транспорту, включающие в себя только сепарационные процессы, на практике принято называть установками низкотемпературной сепарации (НТС).
При больших объемах транспортируемого газа его осушка является наиболее эффективным и экономичным способом предупреждения образования кристаллогидратов в магистральном газопроводе. В результате осушки газа точка росы паров воды должна быть снижена ниже минимальной температуры при транспортировке газа. Газ осушают на специальных установках жидкими или твердыми веществами.
Абсорбция – избирательное поглощение газов или паров жидкими поглотителями-абсорбентами. В этом процессе происходит переход вещества или группы веществ из газовой или паровой фазы в жидкую. Абсорбция – избирательный и обратимый процесс. Переход вещества из жидкой фазы в паровую или газовую называется десорбцией. Обычно оба процесса объединяются в один производственный цикл.
При десорбции, которую проводят после абсорбции, целевой компонент выделяется из жидкого поглотителя. Очевидно, что условия проведения абсорбции и десорбции прямо противоположны. В первом случае происходит растворение газа в жидкости, этому способствуют повышение давления и понижение температуры. Абсорбент, поглотивший в процессе абсорбции целевые компоненты, называется насыщенным или отработанным. Абсорбент, освобожденный в процессе десорбции от целевых компонентов, называется регенерированным и после охлаждения насосом может быть снова возвращен на абсорбцию. Таким образом, получается замкнутая абсорбционно-десорбционная система.
Примером абсорбционного процесса может служить гликолевая осушка природного газа. В процессе абсорбции гликоль (ДЭГ, ТЭГ) поглощает пары воды из природного газа. Регенерированный раствор снова возвращается в абсорбер.
По технологической схеме установки осушки газа (рис. 11.1) влажный газ поступает в нижнюю скрубберную секцию абсорбера 1, где отделяется от капельной жидкости и далее поступает в контактор. В контакторе газ, двигаясь снизу вверх навстречу абсорбенту, осушается, а затем проходит в верхнюю секцию, где отделяется от капель абсорбента высокой концентрации, уносимого с верхней тарелки контактора. Осушенный газ из абсорбера поступает в магистральный газопровод.
Рис. 11.1. Технологическая схема установки осушки газа гликолями:
I – газ сырой; II – газ сухой; III – газ регенерированный;IV – охладитель; V – насыщенный ДЭГ; VI– конденсат; VII – пар. 1 – абсорбер;2 – регулятор уровня; 3 – выветриватель; 4 – фильтр; 5 – десорбер; 6– холодильник; 7 – эжектор; 8 – насос; 9, 10 – теплообменники
Насыщенный раствор абсорбента из контактора сначала проходит теплообменник 9, выветриватель 3, фильтр 4, затем паровой подогреватель (ребойлер), установленный в нижней части десорбера 5, где нагревается до установленной температуры. После нагревания в ребойлере раствор поступает в выпарную колонну (десорбер) 5.
Водяной пар, отделяющийся из раствора, поступает в холодильник 6, где основная часть его конденсируется, а затем в сборник конденсата 8. Часть воды из этого сборника направляется обратно в верхнюю часть колонны, чтобы понизить температуру. В результате подымающиеся пары абсорбента конденсируются и сливаются вниз, что сокращает потерю абсорбента.
Раствор абсорбента, регенерированный до заданной концентрации, сначала проходит через теплообменник 9, где охлаждается насыщенным раствором, затем дополнительно охлаждается водой в теплообменнике 10 и поступает в контактор для орошения.
В качестве абсорбента для осушки природного газа широко применяют гликоли, причем преимущественно диэтиленгликоль и триэтиленгликоль. Если требуется осушка природного газа, в котором содержатся углеводородный конденсат с значительным количеством ароматических углеводородов, то при выборе абсорбента предпочтение отдается этиленгликолю. В этих условиях этиленгликоль может оказаться экономически эффективнее диэтиленгликоля и триэтиленгликоля, так как он менее растворим в углеводородном конденсате, содержащем ароматические углеводороды.
Широкое применение гликолей для осушки природного газа обусловлено их высокой гигроскопичностью, стойкостью к нагреву и химическому разложению, низким давлением пара и доступностью при сравнительно невысокой стоимости.
Этиленгликоль или, как принято называть, гликоль (СН2–ОН==СН2–ОН)– простейший двухатомный спирт. Бесцветная густоватая жидкость сладкого вкуса, без запаха. Молекулярная масса его 62,07, плотность = 1,115 г/см3, температура кипения при атмосферном давлении 197,5 °С, удельная теплоемкость 0,55 ккал/кг.
Этиленгликоль смешивается с водой в любых отношениях. Водные его растворы имеют низкую температуру замерзания и широко применяются в качестве незамерзающей жидкости для охлаждения двигателей автомашин в зимнее время.
Диэтиленгликоль (СН2ОН–СН2–О–CH2–СН2ОН) представляет собой неполный эфир этиленгликоля. Бесцветная жидкость. Молекулярная масса его 106,12, плотность = 1,117 г/см3, температура кипения при атмосферном давлении 244,5 °С.
Диэтиленгликоль также смешивается с водой в любых отношениях и гигроскопичнее этиленгликоля.
Из гликолей наиболее эффективным абсорбентом является триэтиленгликоль (CH2OH-CH2-O-CH2-CH2-O-CH2-CH2OH). Молекулярная масса его 150,17, плотность = 1,1254 г/см3, температура кипения при атмосферном давлении 287,4 °С. Упругость паров его несколько меньше, чем у диэтиленгликоля.
Для триэтиленгликоля существенным недостатком является то, что его концентрированные растворы способны поглощать в небольшом количестве тяжелые углеводороды. Поэтому при осушке газов со значительным содержанием тяжелых углеводородов применяют растворы пониженной концентрации.
Адсорбция – это поглощение вещества поверхностью твердого поглотителя, называемого адсорбентом. Поглощающая способность поверхности объясняется особым состоянием молекул на границе раздела. Внутри фазы каждая молекула испытывает практически одинаковую по всем направлениям силу притяжения других молекул. Молекулы же, расположенные на границе раздела фаз, испытывают неодинаковые силы притяжения молекул, находящихся в разных фазах. Если результирующая сила притяжения направлена внутрь данной фазы, то особое состояние ее поверхности проявляется в способности поверхностного слоя притягивать, поглощать молекулы из другой фазы, находящейся в контакте с этим слоем.
Адсорбция, сопровождающаяся образованием химической связи между молекулами адсорбируемого вещества (адсорбата) и молекулами адсорбента, называется хемосорбцией (химической адсорбцией). Адсорбция, не сопровождающаяся образованием химического соединения, называется физической адсорбцией. Последняя обуславливается силами взаимного притяжения молекул. Эти силы называют вандерваальсовыми, а физическую адсорбцию – вандерваальсовой. При физической адсорбции связь адсорбата с адсорбентом менее прочна, чем при хемосорбции. Изменение внешних условий процесса (давления и температуры) ведет к нарушению связи между молекулами адсорбата и адсорбента, и начинается процесс десорбции – удаление молекул адсорбата с поверхности адсорбента.
В качестве адсорбентов (поглотителей) применяются твердые вещества, имеющие большую удельную поверхность, отнесенную обычно к единице массы вещества. Удельная поверхность адсорбента колеблется от сотен до десятков сотен квадратных метров на грамм в зависимости от вида и сорта адсорбента. В технике широко применяют адсорбенты с удельной поверхностью 600 – 800 м2/г.
Одна из важнейших характеристик адсорбента – его адсорбционная емкость, то есть количество вещества, которое может быть поглощено единицей массы или объема адсорбента при данных условиях адсорбции. Адсорбционная емкость выражается в процентах, в г/г, в г/100г и т.п. Ее иногда называют активностью адсорбента. Один и тот же адсорбент по отношению к различным веществам обладает разной активностью. Адсорбционная (поглотительная) активность зависит также от внешних условий адсорбции (давления, температуры и концентрации адсорбата в потоке).
Количество вещества, поглощаемое адсорбентом, определяется состоянием равновесия. Количественно процесс адсорбации в условиях равновесия принято представлять графически изотермой адсорбции, выражающей связь количества вещества, адсорбированного единицей массы или объема адсорбента, с концентрацией адсорбата в газовой или жидкой фазе при постоянной температуре процесса.
Промышленные адсорбенты должны удовлетворять следующим требованиям: иметь большую адсорбционную емкость, высокую механическую прочность, низкую стоимость; обладать высокой селективностью, способностью к регенерации, стабильностью адсорбционных свойств в условиях длительной эксплуатации; быть нетоксичными, некоррозионно-активными.
При выборе адсорбента для промышленного использования приходится отдавать предпочтение тем или иным из перечисленных требований.
В газовой промышленности для осушки газов и жидкостей применяются активированная окись алюминия, алюмогели, силикагели и цеолиты (молекулярные сита); для очистки от кислых компонентов – цеолиты, для извлечения из газа углеводородных компонентов – активные угли и силикагели. Адсорбционные свойства адсорбентов существенно зависят от способа их приготовления и активации.
Примером применения процесса адсорбации может служить извлечение жидких углеводородов из потоков газа, содержащих мало тяжелых компонентов, активированным углем, удаление воды из газа – силикагелем или алюмогелем, удаление меркаптанов – молекулярными ситами и так далее.
|
|
Индивидуальные и групповые автопоилки: для животных. Схемы и конструкции...
История развития пистолетов-пулеметов: Предпосылкой для возникновения пистолетов-пулеметов послужила давняя тенденция тяготения винтовок...
Состав сооружений: решетки и песколовки: Решетки – это первое устройство в схеме очистных сооружений. Они представляют...
Семя – орган полового размножения и расселения растений: наружи у семян имеется плотный покров – кожура...
© cyberpedia.su 2017-2024 - Не является автором материалов. Исключительное право сохранено за автором текста.
Если вы не хотите, чтобы данный материал был у нас на сайте, перейдите по ссылке: Нарушение авторских прав. Мы поможем в написании вашей работы!