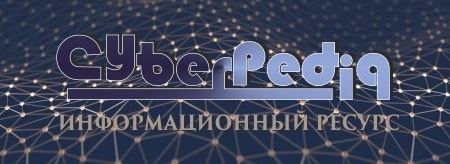
Наброски и зарисовки растений, плодов, цветов: Освоить конструктивное построение структуры дерева через зарисовки отдельных деревьев, группы деревьев...
Семя – орган полового размножения и расселения растений: наружи у семян имеется плотный покров – кожура...
Топ:
Марксистская теория происхождения государства: По мнению Маркса и Энгельса, в основе развития общества, происходящих в нем изменений лежит...
Эволюция кровеносной системы позвоночных животных: Биологическая эволюция – необратимый процесс исторического развития живой природы...
Интересное:
Средства для ингаляционного наркоза: Наркоз наступает в результате вдыхания (ингаляции) средств, которое осуществляют или с помощью маски...
Наиболее распространенные виды рака: Раковая опухоль — это самостоятельное новообразование, которое может возникнуть и от повышенного давления...
Подходы к решению темы фильма: Существует три основных типа исторического фильма, имеющих между собой много общего...
Дисциплины:
![]() |
![]() |
5.00
из
|
Заказать работу |
|
|
Основное назначение дефектации деталей при ремонте состоит в том, чтобы оценить фактическое техническое состояние этих деталей, выявить их износы и повреждения. Для этого все детали делят на группы:
детали остова – фундаментная рама, блок цилиндров, крышка цилиндров; детали цилиндро-поршневой группы (ЦПГ) – поршень, втулка, поршневой палец, шатун, поршневые кольца; детали валовой группы – коленчатый вал, рамовые и шатунные подшипники; детали механизма газораспределения – распределительный вал, клапаны, толкатели, коромысла, пружины; детали топливной аппаратуры и дистанционно-автоматического управления (ДАУ).
По результатам дефектации выделяют детали:
· пригодные для дальнейшей эксплуатации без ремонта;
· подлежащие ремонту;
· не подлежащие ремонту и направляемые в металлолом.
Различают визуальные и инструментально-приборные методы дефектации.
Визуальным осмотром выявляют макродефекты в виде трещин, задиров, царапин и т.п. Для повышения эффективности визуальных осмотров применяют оптические стекла (лупы). Такая дефектация дает общее представление о наличии дефекта без количественных показателей.
Инструментальные методы дефектации предполагают использование универсальных и специальных измерительных средств. К ним относятся линейки, штангенциркули, микрометры, индикаторные скобы и нутрометры, специальные зеркально-оптические приборы, калибры и т.п.
Эти методы позволяют определить количественную характеристику износа детали в виде изменения линейных размеров, искажений формы и взаимного расположения базовых поверхностей и т.д. Точность оценок при такой дефектации обычно составляет от 0,002 до 0,01 мм.
|
Физические методы дефектации с использованием специальных дефектоскопов применяются для выявления микроскопических поверхностных, подповерхностных и внутренних дефектов без разрушения деталей. По этому признаку их относят к методам неразрушающего контроля качества деталей.
В судоремонте используют следующие методы неразрушающего контроля: капиллярные, вихретоковые, магнитные, ультразвуковые, рентгеновские, гидравлические и воздушные.
Приведем перечень методов определения различных дефектов с краткой характеристикой и указанием области применения.
Косвенные методы оценки технического состояния машин и механизмов — контроль основных показателей работы: мощности, производительности, частоты вращения, давления, температуры, расхода топлива, электроэнергии, масла, утечки газа, что связано с коррозией, эрозией, изнашиванием, изменением упругих характеристик, ухудшением работы и балансировки движущихся частой, изменением параметров крепежных соединений, особенностями эксплуатации и пр.
Теплотехнические испытания — контроль мощности, удельного расхода топлива, утечек газа, давления, температуры отработавших газов.
Статистические методы — изучение износов, деформаций, нарушений сплошности, аварий, разрушений с целью разработки норм предельно допустимых значений и др.
Визуальный осмотр невооруженным глазом и с помощью оптических увеличителей — контроль состояния наружных и с применением специальных приспособлений, внутренних поверхностей деталей из любых металлов и неметаллов; обнаружение трещин, непроваров, подрезов, пор, свищей, коррозионных и эрозионных поражений.
Исследования структуры металлов и сплавов: макроскопические, микроскопические, рентгено-структурный анализ — контроль микрошлифов.
Механические испытания: статические, динамические, усталостные, на ползучесть при высоких температурах; испытание металла на растяжение, ударный изгиб, твердость, сплющивание, срез, усталость и пр.
|
Химический анализ проб, травление поверхности растворами кислот — определение химического состава металла, контролв содержания вредных элементов (например, фосфора и серы), анализ металла на содержание газов (азота, кислорода, водорода), обнаружение поверхностных дефектов (трещин, рисок, царапин).
Обмер деталей: микрометраж, профилографирование, определение местного износа методом искусственных баз (метод отпечатков и вырезанных лунок); ультразвуковой метод — определение износа деталей, контроль прочных размеров, изменения формы, увеличения масляных зазоров, определение степени повреждения поверхности, утонения, отслаивания, выкрашивания и других дефектов.
Исследование продуктов изнашивания: весовой метод; химический анализ смазки; метод радиоактивных изотопов — контроль износа деталей.
Контроль на непроницаемость: гидравлические испытания (струей воды из шланга, наливом с частичным заполнением, наливом с полным заполнением и добавочным гидравлическим давлением); испытание керосином; пневматический метод; вакууммироваиие; цветной метод; звуковые испытания; испытание химической реакции — контроль плотности и прочности сварных швов; контроль корпусов судов, паровых котлов, баллонов, резервуаров, цистерн, работающих под давлением; контроль деталей главных и вспомогательных механизмов, трубопроводов, арматуры.
Испытания на коррозию: качественная оценка по внешнему виду; методы гравиметрический, объемный, электрохимический, профилографический, определение коррозионной стойкости по изменению механических свойств — контроль степени коррозионного поражения, коррозионной стойкости металла, химического состава продуктов коррозии, скорости коррозии, глубины коррозионного разъедания.
Капиллярные методы: пробы керосиновая, масляная, парафиновая, содовая, цветная, люминесцентная—определение только поверхностных или подповерхностных дефектов с выходом на поверхность у деталей из черных и цветных металлов, керамики, изделий порошковой металлургии, стекла, а также некоторых пластических и синтетических материалов; обнаружение трещин шириной раскрытия 0,01—0,03 мм и глубиной 0,03—0,04 мм и выше.
Ввиду меньшей чувствительности капиллярных методов по сравнению с магнитными их следует применять главным образом для контроля деталей, изготовленных из немагнитных материалов.
|
Испытания фильтрующимися частицами — метод используют главным образом для контроля пористых материалов (керамики, огнеупоров, абразивных кругов, бетонов). Процесс определения дефектов заключается в нанесении жидкой суспензии с частицами (цветными или люминесцентными) на пористый материал, в котором предполагаются дефекты, открытые с поверхности. В мосте нахождения дефекта поглощается жидкости больше, чем в зоне без дефекта. В промышленности используют преимущественно флуоресцентные частицы. Если трещина существует, то она отчетливо появляется сразу после нанесения жидкости. Жидкость, используемая для контроля, чаще всего представляет собой легкую фракцию нефти. Этот материал является наиболее подходящим с точки зрения стоимости, безопасности и скорости высыхания. Кроме того, применяют суспензии, приготовленные на воде, гликолях тяжелой фракции нефти и спирте.
Магнитные методы:
· магнитный порошковый контроль — позволяет обнаруживать поверхностные дефекты (усталостные, шлифовочные, закалочные, ковочные и штамповочные трещины, волосовины, флокены, надрывы, расслоения) деталей из ферромагнитных металлов и сплавов (железо, никель, кобальт, углеродистые, низколегированные и некоторые легированные стали). Обнаружение трещин шириной раскрытия от 0,005 мм и протяженностью в глубь металла 0,01 мм и выше. Глубина контроля — 5—6 мм; Способы намагничивания деталей изображены на рис 6.1.
Рисунок 6.1 - Способы намагничивания деталей:
а – продольный в соленоиде; б – продольный в полюсах электромагнита;
в – продольный пропусканием магнитного потока по стержню внутри детали;
г – циркулярный пропусканием тока через деталь; д – циркулярный пропусканием тока через стержень (тороидный); е – циркулярный пропусканием тока через проводник; ж – комбинированный
Магнитопорошковый метод контроля выполняется в шесть операций:
– подготовка к контролю, которая включает очистку поверхности от загрязнений;
|
– намагничивание;
– нанесение магнитного порошка;
– осмотр контролируемой поверхности и регистрация дефектов;
– оценка результатов контроля; – размагничивание.
· магнитографический метод — контроль трещин, непроваров, шлаковых и газовых включений сварных швов, изготовленных из ферромагнитных металлов при толщине металла 1 — 16 мм;
· контроль магнитными феррозондами — контроль ферромагнитных и неферромагнитных металлов и сплавов. Метод позволяет обнаруживать дефекты на глубине до 30 мм, измерять толщины при двустороннем доступе, контролировать степень размагничивания судов, выявлять ферромагнитные примеси;
· магнитная структуроскопия — контроль химического состава, структуры механических и физических свойств, структурной анизотропии изделий из ферромагнитных материалов;
· магнитная толщинометрия — контроль толщин изделий из ферромагнитных материалов, контроль покрытии из магнитных и немагнитных материалов при одностороннем доступе. Чувствительность метода примерно 4—6% измеряемой толщины;
· магнитно-люминесцетный метод — область применения та же, что и при магнитном порошковом методе, но возможен контроль изделий с темной поверхностью. Обнаружение трещин шириной раскрытия 0,0001 мм и протяженностью в глубь металла 0,005 мм.
Контроль вихревыми токами — контроль изделий из цветных и черных металлов, ферромагнитных и неферромагнитных. Кроме обнаружения дефектов, метод позволяет определять химический состав, твердость, прочность, проводимость, места с пониженной твердостью, толщину стенок и покрытий, степень декарбидизации и диффузии, несплошность покрытий, скорость коррозии. Обнаружение дефектов на глубине I—2 мм под поверхностью.
Метод электросопротивления - самая широкая область применения — определение наличия трещин, их глубины, а также толщины листов, стенок труб при одностороннем доступе, наличие расслоений. Чувствительность зависит от калибровки приборов, краевых эффектов материала изделия, его однородности, шероховатости поверхности.
Трибоэлектрический метод - контроль изделий из ферромагнитных и неферромагнитных материалов, а также неэлектропроводящнх неметаллов. Обнаружение трещин шириной до 0,1 мкм, определение химического состава материала, сортировка материала по маркам, контроль спаев стекла с металлом, контроль эмалированных изделий. Метод основан на возбуждении электрических зарядов при трении двух разнородных материалов. Трибоэлектрическая разность потенциалов, определяемая с помощью микровольтметра, зависит от пары используемых материалов. Приборы для сортировки, основанные на этом методе, имеют небольшие натирающие механизмы. Эталонный образец перемещают по гладкой и чистой поверхности контролируемого образца. Полученные таким образом напряжения сравнивают с напряжениями, возникающими при контроле уже известных материалов. Здесь также возможен нулевой метод, гак как трение двух одинаковых веществ не создает электризации.
|
Метод теплопроводности - контроль качества сварки, особенно точечной, обнаружение трещин и других дефектов с выходом на поверхность. Применяется для изделий из любых металлов и сплавов.
Электростатический порошковый контроль изделий из эмали, стекла, пластмасс, а также покрытий на металлах. Обнаружение трещин шириной раскрытия 2 мкм и выше.
Термоэлектрический метод - контроль изделий из ферримагнитных и неферромагнитных металлов. Обнаружение поверхностных дефектов (в основном трещин), определение химического состава материала, сортировка материала по маркам, определение толщины покрытий.
Контроль проникающим излучением: рентгеновскими лучами, гамма-лучами, бета-лучами, нейтронами — контроль изделий из любых металлов и сплавов. Определение дефектов поковок, отливок, сварных соединений самой сложной конфигурации (раковин, рыхлот, ликваций, неметаллических включений, трещин). Чувствительность контроля во многом зависит от расположения дефектов по отношению к направлению излучения. Диапазон контролируемых толщин — 3—250 мм, при использовании бетатронов — до 500 мм.
Акустические методы контроля:
· ультразвуком — для контроля изделий из любых металлов и сплавов, пластмасс, керамики, бетона. Диапазон контролируемых толщин 3—1000 мм. Метод дает возможность определять дефекты литья, поковок, сварных швов, готовых изделий и пр., измерять толщины при одностороннем доступе, определять скорость роста усталостных трещин и эксцентриситет высверленных отверстий; исследовать скорость коррозии, структурные превращения в металлах в зависимости от термообработки;
· метод собственных колебаний—для контроля изделий из любых материалов, обладающих упругими свойствами, а следовательно, собственной резонансной частотой. Метод позволяет контролировать длину, ширину, толщину, диаметр, модуль упругости, плотность, коэффициент Пуассона, трещины, модуль сдвига, температурную зависимость;
· акустическая дефектация механизмов—для упрощения и дополнения технического контроля, быстрого установления дефектных узлов и деталей механизмов, определения возможности их восстановления или необходимости замены. Возможем акустический подбор заменяемых деталей.
Поляризационный метод исследования напряжений с применением фотоупругих покрытий — измерение величины деформаций, их направления; распределение деформаций в конструкциях и деталях, находящихся под воздействием статических и динамических нагрузок; выбор оптимальной конструкции с точки зрения прочности; определение места концентрации напряжений, надежность конструкции, исследование образования малых трещин, измерение деформации вблизи заклепок и сварных швов.
Измерение деформаций датчиками электрического- сопротивления-исследование изделий из любых материалов (металлов, бетона, клеящих составов, кирпича, резины, пластмасс). Измеряемые значения деформации — от стотысячных долей миллиметра и выше.
Метод хрупких покрытий - определение направления и величины упругих деформаций в металле, по которым вычисляют напряжения.
Радиотехнический метод - при контроле толщин и определении качества металлов и других материалов. При наличии дефекта электромагнитные поля отражаются, изменяя интерференционную картину.
Вопросы для самоконтроля
1. Основное назначение дефектации.
2. Какие дефекты выявляют при визуальном методе дефектации? При инструментально-приборном?
3. Какие методы неразрушающего контроля Вам известны?
4. Опишите магнитные методы контроля. Какие дефекты они позволяют обнаружить?
5. Что такое трибоэлектрический метод контроля?
6. Опишите акустические методы контроля.
Упрочнение деталей
Применение процессов упрочняющей технологии позволяет повысить ресурс и надёжность продукции машиностроения, обеспечить работоспособность деталей в самых жестких условиях эксплуатации, при высоких температурах, в агрессивных средах (в морской среде), при действии динамических и контактных нагрузок
Разработаны новые способы и технологии нанесения покрытий в частности, многослойных и многокомпонентных; получили развитие методы поверхностного легирования и упрочнения лазером, электронным лучом, электрическим искровым разрядом, совершенствуются способы и процессы поверхностного и пластичного деформирования, плазменного напыления, нанесения покрытия с помощью плазмотрона – пламенного генератора (высокочастотного N<=1 МВт или дугового N=100 ВТ – 10МВт); в высококачественных плазматронах плазмообразующее вещество нагревается в разрядной камере вихревыми токами (токами Фуко), т.е. замкнутыми индукционными токами в массивных проводниках, которые возникают под действием вихревого электрического поля, порожденного переменным магнитным полем; для уменьшения потерь электроэнергии магнитопроводы машин и аппаратов переменного тока изготавливают из изолированных стальных пластин; в дуговых плазматронах (N=100 ВТ – 10МВт), проходя через сжатую электрическую дугу, с высокой концентрацией энергии, нагревается плазмообразующее вещество.
Использование многих процессов упрочнения ограничено, к примеру, из-за увеличения шероховатости или снижения сопротивления усталости, или из-за высокой пористости металла и пр. В таких случаях сочетанием разных способов упрочнения обеспечивают высокий уровень эксплуатационных свойств, расширяя технологические возможности. Комбинированным способом обработки, к примеру, можно увеличить прочность сцепления покрытий путём упрочнения подложки (грунтовки перед нанесением покрытия). Но при этом возможна несовместимость отдельных процессов обработки металлов. Поэтому существуют базовые способы упрочнения, в частности, поверхностное пластическое деформирование (ППД), которое применяют в комбинациях с нанесением гальванических химических покрытий, покрытий напылением.
Комбинированное упрочнение – самое эффективное, но трудоёмкое средство, поэтому его используют для ответственных деталей, когда традиционные технологии не обеспечивают требуемых свойств деталей.
Особенности поверхностного упрочнения:
1. При обеспечении жаростойкости и сопротивлении коррозии, твёрдость и прочность не являются критериями определяющими работоспособность поверхностного слоя
2. Критерии прочности определяются условиями нагружения детали и оцениваются твёрдостью (контактные напряжения сопротивление абразивному износу), либо пределом усталости (динамическое нагружение), либо временным сопротивлением sв, либо ударной вязкостью (хрупкое разрушение).
3. Увеличение прочности наряду с другими факторами обусловлено формируемой дислокационной структурой: линейными дефектами кристаллической решётки, определяющими прочность, пластичность и др.
Характер дислокационной структуры металла зависит от типа кристаллической решётки, степени деформации (пластической) температуры деформирования, последующего теплового воздействия.
Дислокационной структурой можно управлять, сочетая деформирование с термообработкой. Термообработка после пластической деформации «рассасывает» дислокационные скопления, способствует релаксации (установлению термодинамического равновесия)
Варьируя температуру и время термообработки можно активно изменить структуру материала. Деформирование при температуре 0,3-0,6 Тплавления позволяет увеличить прочность и плотность металла.
Основные направления повышения прочности металлов:
1) Деформационные упрочнения (наклёп)
2) Легирование – за счёт «связанных» дислокаций (линейных дефектов кристаллической решётки, правильное расположение и чередование атомных плоскостей, определяющих прочность и пластичность и др.) легирующими добавками.
3) Термическое или деформационное воздействие, вызывающее фазовое превращение т.е. переходы вещества из одной фазы в другую. Фаза – определённый момент в ходе развития любого процесса.
4) Механическое введение в сплав или выделение в нём дисперсных частиц с целью получения композиционных материалов.
5) Скоростная закалка из жидкой фазы с формированием мегастабильных структур в том числе аморфных (устойчивое состояние, из которого система может перейти в более устойчивое под действием внешних факторов сомопроизводства). Например, жидкость в состоянии перегрева или переохлаждения.
Нанесение покрытий является наиболее распространённым способом защиты металлов от коррозии, увеличения износостойкости, антифрикционных средств, жаростойкости. Покрытия обычно имеют ярко выраженную границу с подложкой, обеспечивающей адгезию покрытия. Для увеличения адгезии покрытия наносят на шероховатую поверхность. Многие процессы нанесения покрытия проходят при динамическом воздействии частиц на поверхность подложки, причём частицы могут находиться в жидкой фазе и иметь высокую температуру.
В итоге на границе покрытия с подложкой происходят сложные физико-химические процессы, в частности сплавление частиц покрытия с металлом основы, диффузия компонентов в основной материал, рост кристаллов покрытия на базе кристаллов подложки, – эпитаксия – ориентировочный рост одного микрокристалла на поверхность другого (подложки); при одинаковых веществах гомоэпитаксия, при различных веществах – гетероэпитаксия.
Определяется эпитаксия условием сопряжения кристаллических решёток кристалла и подложки.
Даже при плотном контакте покрытия и основы, их сваривания и эпитаксии в переходном слое имеются участки с ослабленными связями: места загрязнения и окисления, поры. Такие участки по сути являются микротрещинами, находящимися в одной плоскости и способными к распространению при приложении внешних нагрузок и действия остаточных напряжений по механизмам хрупкого и усталостного разрушения. В последнее время разработаны композиционные покрытия, содержащие частицы различных материалов:
1) Карбиды (химические соединения углерода с металлом и некоторыми неметаллами. Например, карбид кальция, карборунд, карбид вольфрама, титана, тантала (Та – серый блестящий металл, хорошо обрабатывается, не растворим в кислотах, обладает высокой твёрдостью и химической устойчивостью, применяется для ответственных деталей химической и электроламповой аппаратуры). Ниобия – Niobium (Nb) химический элемент, свойства близки к танталу – светло-серый, тугоплавкий металл, плотность 8,57 г/см3, температура плавления 2500 0С; минералы – пирохлор, колумбит, лопарит. Применяют при растворении, при изготовлении деталей реактивных двигателей, химической и нефтеперегонной аппаратуры, в радиоэлектроники для проведения сверхпроводящих соленоидов из сплавов Ni, Su, Ti, Zr (циркония — минерал в виде силиката – солей кремниевых и алюминиевых кислот, например топаз, керамика, кирпич, цемент, бетон, огнеупоры, стекло).
2) Нитриды — химические соедтнения азота с металлами: Al, Br (бор), Si, W (вольфрам), Ti(титан). Например: AlN, BN, Si3N4, W2N, TiN и др. используют в жаропрочных сплавах, в полупроводниковых приборах, как абразивы. Действием азота или аммиака на металлы при 500-600 0С получают нитридные покрытия, высокотвёрдые, износо- и кислотостойкие.
3) Бориды — химические соединения бора (В); бор в природе встречается в виде буры, соли тетраборной кислоты – осадок усыхающих бороносящих солёных озёр, бесцветное кристаллическое вещество, tип=741 0С; расплавленный бор растворяет окислы металлов, что используют при очистке поверхности при сварке, пайке, резке.
Такие покрытия обеспечивают высокую износостойкость и сопротивление эрозии, характерные для твёрдых материалов, при устранении хрупкости. В одном направлении повышения качественных характеристик покрытия является многослойное нанесение, связанные с необходимостью повышения адгезии к подложке. При этом в качестве подслоя наносится покрытие из металла имеющее хорошую адгезию с материалами адгезии и покрытия. Например, нанесение медного подслоя при никелировании стальных деталей. Многослойные покрытия дают комплекс свойств поверхности: износостойкость, антифрикционные свойства и т.д.
Нижний слой даёт высокую сопротивляемость изнашиванию, а верхний слой выполняется из антифрикционного материала. Известны многослойные покрытия, имеющие слой из металлокерамики или твёрдого сплава (ВК6-М, Т15К6, TiN, Al2O3,TiC и др.) многослойные покрытия могут быть применены для повышения прочностных свойств покрытий, снижения пористости, для снижения релаксации внутренних напряжений, увеличения вязкости и сопротивления растягиванию. Такие покрытия имеют, как правило, более высокую плотность и прочность. Нанесение толстых покрытий сопровождается формированием значительных напряжений, крупнозернистой структуры, увеличенной пористости.
Многослойные покрытия позволяют избежать этих недостатков. Нанесение твёрдых слоёв (крупных материалов) с вязкими прослойками обеспечивает комплекс полезных свойств (износостойкость, антифрикционные свойства, сопротивление усталости и коррозии). Нанесение многослойных покрытий позволяет получить мелкозернистую структуру покрытия, локализовать и залечивать микротрещины, снижать тепловые напряжения. При наличия твёрдого покрытия на мягкой подложке в условиях трения под прикрытием могут протекать деформационные процессы отслаивания и разрушения — покрытие должно иметь толщину, превышающую глубину распространения остаточных напряжений.
Существует оптимальный для каждого вида покрытия диапазон толщин. Основными направлениями повышения эксплуатационных свойств деталей с покрытиями являются: повышения прочности сцепления с основой, улучшения структуры покрытия, финишная обработка поверхностей для обеспечения точности и микрогеометрии.
Плазменное напыление покрытий порошковыми материалами:
a) Керамическими — TiO, Cr2O3, B4C2WB, TiN, Al2O3, Cr3C2, и др;
b) Сплавы соединения: Ni-Al, Ti-Ni, WC-Co, WC-Ni, W-ZO2.
Обобщённая характеристика: прочность сцепления с основой 20-25 МПа, толщина покрытия 20-1500 мкм, пористость 10-15%, шероховатость Rмах = 40-500 мкм.
Подготовка поверхности под покрытие:
Точение с большими подачами и резцами с малыми углами при вершине, электромеханическая обработка для создания микрогеометрии специального профиля, электроэрозионная обработка, пескоструйная или дробеструйная очистка поверхности от загрязнения и получения шероховатости с Rмах = 500-750 мкм, что обеспечивает хорошую сцепляемость покрытия с подложкой.
Технологические факторы и условия нанесения покрытий:
1. Нагревание деталей до 150-200 0С
2. Плазмотрон
3. Расход газа и порошка
4. Характеристики источника питания плазмотрона
5. Расстояние от среза сопла до поверхности
6. Дисперсность порошка и условия его подачи в плазменную струю
7. Скорость относительного перемещения плазмотрона и поверхности изделия
8. Производительность по расходу порошка — 3-20 кг/час
9. Обработка поверхности после покрытия: термическая с целью спекания, оплавления, снятия напряжений; пропитка эпоксидными кремнийорганическими смолами, жидким стеклом, химическими растворами на основе Cr2O3 и AlNO3, шлифование или точение резцами из алмаза. Достоинства: высокая производительность, широкая гамма наносимых материалов, возможность комплексных и многослойных покрытий, возможность восстановления деталей с большим износом.
Недостатки: низкая прочность сцепления с основой, пористость, дорогое оборудование.
Детонационное напыление
Подготовка поверхности: точение и шлифовка, полирование, дробеструйная обработка, обкатка роликами и шариками, химическое травление, очистка растворителями. Накатка углублений, оптимальная шероховатость поверхности после подготовки Rа=0,08-1,25 мкм материалом 20-150 МПа, толщины покрытия 2-500 мкм, пористость 1-40%, шероховатость Rа=0,05-2,5 мкм.
Технологические факторы и условия нанесения покрытий:
Состав электролита, плотность тока, вид тока (постоянный, переменный, импульсный, асимметричный), наложение ультразвука, поддержание и регулирование состава электролита и температуры, ток и дисперсность порошка, вводимого в электролит для покрытия, его концентрация в электролите, условия циркуляции или перемешивания электролита.
Достоинства: высокая производительность, недорогое оборудование, возможность получения многослойных и композиционных покрытий, отсутствие нагрева и коробления деталей.
Недостатки: снижение сопротивления усталости деталей на 15-20%, токсичность электролита и загрязнение окружающей среды.
Вакуумное напыление
1. Термическое напыление – испарение материала в вакуум и его конденсация на упрочняемом изделии.
2. Ионное распыление – распыление мишени из наносимого материала ионной бомбардировкой и осаждение образовавшихся частиц на поверхности деталей
Во всех случаях используется реактивный газ: азот, кислород, метан ацетилен и др.; газ взаимодействует с испаренным или распылённым материалом с образованием химических соединений конденсирующихся на деталях (реактивное распыление).
Материалы покрытий: Ti, Zr, Ta, Nb, W, Mo, Cr, Al и другие химические соединения этих металлов и сплавы Ni, Cr, Al, Y (иттрий).
Обобщающая характеристика покрытия:
· Прочность сцепления 50-500 МПа
· Толщина покрытия 0,2-200 мкм
· Пористость 0,5-5%
· Параметр шероховатости Ra = 0,08-2,5 мкм
· Производительность зависит от размеров изделий, необходимой толщины покрытия, на установках типа «Булат» скорость осаждения покрытия 3-15 мкм/час.
Поверхностное регулирование – изменение химического состава поверхностных объёмов металла диффузионным насыщением материала химико-термической обработкой, методами поверхностного плавления с введением необходимых компонентов (лазерные легирования, электроэрозионные упрочнения, плазменное и электронно-лучевое легирование, ионная имплантация). Поверхностное легирование имеет ряд преимуществ в сравнении с нанесением покрытия. Главное из них – высокая прочность сцепления с основой, поскольку граница материала с легированным слоем имеет диффузионный характер.
Увеличение содержания хрома в упрочняющем материале повышает твёрдость, износостойкость, антифрикционность основных конструкционных материалов, повышает коррозийную стойкость стали. Вольфрам и молибден увеличивает теплостойкость инструментальных сталей. Ванадий способствует образованию мелкодисперсных износостойких карбидов. Добавки алюминия увеличивают жаростойкость. Поверхностное упрочнение направлено на защиту от внешнего воздействия больше, чем на обеспечивание прочности.
Наиболее исследованным способом поверхностного легирования является химико-термическая обработка:
· Цементация (насыщение углеродами) – повышение износостойкости, эрозионной стойкости, выносливости, сопротивления усталости и износостойкости.
· Азотирование — предотвращение схватывания, сопротивления изнашиванию, увеличение коррозионной стойкости и сопротивления усталости, кавитационному разрушению.
· Силицирование – повышение коррозионной стойкости и жаростойкости
· Алитирование – обеспечение жаростойкости, коррозионной стойкости, сопротивления эрозии.
· Цинкование и кадмирование– защита от коррозии.
· Хромирование – повышение изностойкости, термической усталости, увеличение жаростойкости.
· Вольфрамирование, ванадирование, молибденирование – повышение коррозионной стойкости, жаростойкости, медных и алюминиевых сплавов.
· Такталирование – увеличение износостойкости и сопротивления коррозии в химически активных средах.
· Бериллизация – защита от высокотемпературной коррозии
· Меднение – повышение электропроводности и антифрикционных свойств, защита от коррозии.
· Фосфатирование – увеличение коррозионной стойкости кислотостойкости, улучшение антифрикционных свойств.
· Сурьмирование – улучшение антифрикционных свойств.
· Молибденсилицирование и вольфрамсилицирование – повышение износостойкости и жаростойкости.
· Хромотитаносилицирование – защита ниобиевых сплавов от окисления при высоких температурах.
· Хромотитаноалитирование– повышение жаростойкости и эрозионной стойкости сталей.
Распространённым способом комбинированного упрочнения является сочетание химико-термической обработки (ХТО) с термической обработкой. Например, для высоколегированных сталей 14Х17Н2, 20Х1, 13Х11, Н2В2НФ после цементации рекомендуется закалка при 1000 0С, охлаждение в масле, обработка холодом при 60-70 0С, отпуск при 150-170 0С. После такой обработки твёрдость поверхности HRC 62-66.
Обработка деталей после ХТО пластическим деформированием также является освоенным методом комбинированного упрочнения.
Установлено, что дробеструйный наклёп цементированной стали 20Х2Н4А, выполненный по оптимальным режимам, позволил увеличить предел выносливости на базе испытаний 10 циклов с 540 до 1000 МПа, причем это произошло несмотря на то, что параметр шероховатости Ra поверхности после дробеструйной обработки увеличился с 0,16 до 2,5 мкм.
При обработке обкатыванием азотированных деталей достигается повышение предела выносливости на 53%.
Обработка поверхностным пластическим деформированием деталей (ППД) цементированных сталей является эффективным средством увеличения контактной выносливости. Сравнение различных способов ППД показало увеличение контактного сопротивления усталости, характеризуемое числом циклов нагружения до разрушения, при обработке стальными микропорошками в1,6 раза, стеклянной дробью в 1,8 раза, алмазным выглаживанием в8,4 раза. Основными причинами увеличения контактной усталостной прочности при использовании ППД являются:
· Наличие в рабочем слое остаточных напряжений сжатия
· Увеличение твёрдости
· Уменьшение шероховатости поверхности
· Эффект «тренировки», когда деформационное упрочнение препятствует развитию пластических деформаций, ответственных за образование и развитие микротрещин, возникающих при контактном усталостном напряжении.
При значительной шероховатости упрочнённые ХТО поверхности обладают повышенной изнашивающей способностью по сравнению с сопряжённым элементом пары трения. Это особенно важно учитывать для деталей, не допускающих финишную механическую обработку. Например, при термическом оксидировании или ионном азотировании сплавов упрочнённый слой, обеспечивающий их износостойкость, и не допускает механической обработки. В то же время в результате ХТО формируется микрогеометрия с характерными пористыми структурами, вызывающими при скольжении повышенный износ контроля.
Поверхностный слой легирует в процессе плавления при нагреве концентрированными потоками энергии. Формирование легированного слоя в этом случае сопровождается сложными металлургическими явлениями (процессами), достигаются большие скорости нагрева, плавления, кристаллизации и охлаждения. Это даёт возможность увеличить взаимную растворимость взаимодействующих компонентов, проверить закалку из жидкой фазы с образованием метастабильных структур, обладающих высокой прочностью. Образование метастабильных фаз — одно из основных научных достижений при поверхностном легировании.
В последнее время широко применяется лазерное легирование с использованием намазывания поверхностей пастами определённых составов, предварительного нанесения покрытий из легируемого материала, накатывания фольги или проволоки. Лазерное легирование выполняют импульсным или непрерывным излучением лазера с изменением глубины проплавления от 0,05 до 5 мм. Для поверхностного легирования сталей используют C, Cr, Mo, W, порошки твёрдых сплавов (ВК8 и др.).
Лазерное легирование может проводится из газовой среды. Например, азотирование стали 38ХМЮА в среде NA3 (аммиака) при оплавлении поверхности лучами лазера.
Насыщение титановых сплавов кислородом и азотом, являющимися сильными упрочнителями, выполнялось при плавлении лазером. Эффект от такой обработки значителен, однако наблюдается резкое увеличение шероховатости поверхности.
Существует способ лазерного легирования никелевых сплавов алюминием для повышения их окалиностойкости и сопротивления коррозии. На подложку укладывают лист алюминия поверх него – лист никеля. При сканировании луча лазера слой никеля расплав
|
|
Семя – орган полового размножения и расселения растений: наружи у семян имеется плотный покров – кожура...
Организация стока поверхностных вод: Наибольшее количество влаги на земном шаре испаряется с поверхности морей и океанов (88‰)...
Адаптации растений и животных к жизни в горах: Большое значение для жизни организмов в горах имеют степень расчленения, крутизна и экспозиционные различия склонов...
Своеобразие русской архитектуры: Основной материал – дерево – быстрота постройки, но недолговечность и необходимость деления...
© cyberpedia.su 2017-2024 - Не является автором материалов. Исключительное право сохранено за автором текста.
Если вы не хотите, чтобы данный материал был у нас на сайте, перейдите по ссылке: Нарушение авторских прав. Мы поможем в написании вашей работы!