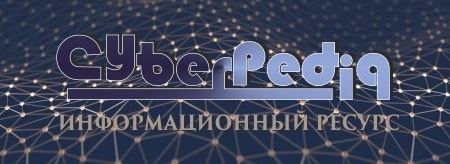
История развития пистолетов-пулеметов: Предпосылкой для возникновения пистолетов-пулеметов послужила давняя тенденция тяготения винтовок...
Типы оградительных сооружений в морском порту: По расположению оградительных сооружений в плане различают волноломы, обе оконечности...
Топ:
Генеалогическое древо Султанов Османской империи: Османские правители, вначале, будучи еще бейлербеями Анатолии, женились на дочерях византийских императоров...
Особенности труда и отдыха в условиях низких температур: К работам при низких температурах на открытом воздухе и в не отапливаемых помещениях допускаются лица не моложе 18 лет, прошедшие...
Проблема типологии научных революций: Глобальные научные революции и типы научной рациональности...
Интересное:
Средства для ингаляционного наркоза: Наркоз наступает в результате вдыхания (ингаляции) средств, которое осуществляют или с помощью маски...
Распространение рака на другие отдаленные от желудка органы: Характерных симптомов рака желудка не существует. Выраженные симптомы появляются, когда опухоль...
Финансовый рынок и его значение в управлении денежными потоками на современном этапе: любому предприятию для расширения производства и увеличения прибыли нужны...
Дисциплины:
![]() |
![]() |
5.00
из
|
Заказать работу |
|
|
Единичный тип производство
Единичное производство — представляет собой форму организации производства, при которой различные виды продукции изготавливаются в одном или нескольких экземплярах (штучный выпуск).
Основные особенности единичного производства заключаются в том, что программа завода состоит обычно из большой номенклатуры изделий различного назначения, выпуск каждого изделия запланирован в ограниченных количествах. Номенклатура продукции в программе завода неустойчива. Неустойчивость номенклатуры, ее разнотипность, ограниченность выпуска приводят к ограничению возможностей использования стандартизованных конструктивно-технологических решений. В этом случае велик удельный вес оригинальных и весьма маленький удельный вес унифицированных деталей.
Каждая единица конечной продукции уникальна по конструкции, выполняемым задачам и другим важным признакам.
Производственный процесс изготовления продукции носит прерывный характер. На выпуск каждой единицы продукции затрачивается относительно продолжительное время. На предприятиях применяется универсальное оборудование, сборочные процессы характеризуются значительной долей ручных работ, персонал обладает универсальными навыками.
Распространено в тяжелом машиностроении (производство крупных машин для черной металлургии и энергетики), химической промышленности, в сфере услуг.
Цехи заводов единичного производства обычно состоят из участков, организованных по технологическому принципу. Значительная трудоемкость продукции, высокая квалификация привлекаемых для выполнения операций рабочих, повышенные затраты материалов, связанные с большими допусками, обусловливают высокую себестоимость выпускаемых изделий. В себестоимости продукции значительный удельный вес имеет заработная плата, составляющая нередко 20 — 25% от полной себестоимости.
|
Серийный тип производство
Серийное производство — это форма организации производства, для которой характерен выпуск изделий большими партиями (сериями) с установленной регулярностью выпуска.
Серийное производство — наиболее распространенный тип производства.
Характеризуется постоянством выпуска довольно большой номенклатуры изделий. При этом годовая номенклатура выпускаемых изделий шире, чем номенклатура каждого месяца.
Это позволяет организовать выпуск продукции более или менее ритмично. Выпуск изделий в больших или относительно больших количествах позволяет проводить значительную унификацию выпускаемых изделий и технологических процессов, изготовлять стандартные или нормализованные детали, входящие в конструктивные ряды, большими партиями, что уменьшает их себестоимость.
Серийный тип производства характерен для станкостроения, производства проката черных металлов и т.п.
Организация труда в серийном производстве отличается высокой специализацией. За каждым рабочим местом закрепляется выполнение нескольких определенных деталеопераций. Это дает рабочему хорошо освоить инструмент, приспособления и весь процесс обработки, приобрести навыки и усовершенствовать приемы обработки. Особенности серийного производства обуславливают экономическую целесообразность выпуска продукции по циклически повторяющемуся графику.
Подтипы серийного производства:
§ мелкосерийное;
§ серийное;
§ крупносерийное.
Мелкосерийное тяготеет к единичному, а крупносерийное — к массовому. Это деление носит условный характер. Например, в соответствии с классификацией, предложенной Вудворд выделяются единичное и мелкосерийное производство (Unit Production), массовое (Mass Production) и непрерывное (Process Production).
|
Производство мелкосерийное является переходным от единичного к серийному. Выпуск изделий может осуществляться малыми партиями.
В настоящее время в машиностроении одним из конкурентных факторов стала способность фирмы изготовлять уникальное, зачастую повышенной сложности оборудование малой партией по спецзаказу покупателей.
Внедрение компьютеризации позволяет повысить гибкость производства и внести в мелкосерийное производство черты поточного производства. Например, появилась возможность изготовлять несколько типов изделий на одной поточной линии с затратой минимального количества времени для переналадки оборудования.
Крупносерийное производство является переходной формой к массовому производству.
В крупносерийном производстве выпуск изделий осуществляется крупными партиями в течение длительного периода. Обычно предприятия этого типа специализируются на выпуске отдельных изделий или комплектов по предметному типу.
Массовый тип производства
Массовое производство — представляет собой форму организации производства, характеризующуюся постоянным выпуском строго ограниченной номенклатуры изделий, однородных по назначению, конструкции, технологическому типу, изготовляемых одновременно и параллельно.
Особенностью массового производства является изготовление однотипной продукции в больших объемах в течение длительного времени.
Важнейшей особенностью массового производства является ограничение номенклатуры выпускаемых изделий. Завод или цех выпускают одно-два наименования изделий. Это создает экономическую целесообразность широкого применения в конструкциях изделий унифицированных и взаимозаменяемых элементов.
Отдельные единицы выпускаемой продукции не отличаются друг от друга (могут быть только незначительные отличия в характеристиках и комплектации).
Время прохождения единицы продукции через систему относительно мало: оно измеряется в минутах или часах. Число наименований изделий в месячной и годовой программах совпадают.
Для изделий характерна высокая стандартизация и унификация их узлов и деталей. Массовое производство характеризуется высокой степенью комплексной механизации и автоматизации технологических процессов. Массовый тип производства типичен для автомобильных заводов, заводов сельскохозяйственных машин, предприятий обувной промышленности и др.
|
Значительные объемы выпуска позволяют использовать высокопроизводительное оборудование (автоматы, агрегатные станки, автоматические линии). Вместо универсальной оснастки используется специальная. Дифференцированный технологический процесс позволяет узко специализировать рабочие места посредством закрепления за каждым из них ограниченного числа деталеопераций.
Тщательная разработка технологического процесса, применение специальных станков и оснастки позволяют использовать труд узкоспециализированных рабочих-операторов. Вместе с тем широко используется труд высококвалифицированных рабочих-наладчиков.
Основы производства стали
⇐ Предыдущая12 3 45678910Следующая ⇒
Стали – железоуглеродистые сплавы, содержащие практически до 1,5% С.
Осн. исх. материалами для произ-ва стали явл-ся передельный чугун и стальной лом (скрап).
Сущность любого металлургического передела чугуна в сталь – снижение содержания С и примесей путем их избирательного окисления и перевода в шлак и газы в процессе плавки.
Fe окис-ся при взаим-вии чугуна с O2 в сталеплавильных печах:
.
Одновременно с Fe окисляются Si, P, Mn и C. Образующийся оксид Fe при высоких температурах отдаёт свой кислород более активным примесям в чугуне, окисляя их.
Процессы выплавки стали осуществляют в четыре этапа.
1 Расплавление шихты и нагрев ванны жидкого металла.
Темпер-ра Ме сравнительно невысокая, интенсивно происходит окисление Fe, образование оксида Fe и окисление примесей: Si, Mn и P.
Наиболее важная задача этапа – удаление P. Для этого желательно проведение плавки в основной печи, где шлак содержит . Фосфорный ангидрид
образует с оксидом Fe нестойкое соединение
.
– более сильное основание, чем оксид Fe, поэтому при невысоких темпер-рах связывает
и переводит его в шлак:
.
2 Осн. этап. Кипение метал. ванны – начинается по мере прогрева до более высоких температур.
При повышении темпер-ры более интенсивно протекает реакция окисления С, происходящая с поглощением теплоты:
|
.
Для окисления С в Ме вводят незначительное кол-во руды, окалины или вдувают О2.
При реакции оксида Fe с C, пузырьки выделяются из жидкого Ме, вызывая «кипение ванны». При «кипении» уменьшается содержание С в Ме до требуемого, выравнивается темпер-ра по объему ванны, частично удаляются неметал. включения, прилипающие к всплывающим пузырькам
, а также газы, проникающие в пузырьки
. Все это способствует повышению качества Ме.
Также создаются условия для удаления S. S в стали находится в виде сульфида (), к-рый растворяется также в осн. шлаке. Чем выше темпер-ра, тем большее кол-во
растворяется в шлаке и взаим-вует с
:
Образующееся соединение растворяется в шлаке, но не растворяется в железе, поэтому S удаляется в шлак.
3 Раскисление стали заключается в восст-нии оксида Fe, растворённого в жидком Ме.
При плавке повышение содержания O2 в Ме необходимо для окисления примесей, но в готовой стали О2 – вредная примесь, так как понижает механич. св-ва стали, особенно при высоких темпер-рах.
Сталь раскисляют двумя способами: осаждающим и диффузионным.
Осаждающее раскисление осущ-ся введением в жидкую сталь растворимых раскислителей (ферромарганца, ферросилиция, алюминия), содержащих элементы, к-рые обладают большим сродством к O2, чем Fe. В рез-те раскисления восст-ся Fe и образуются оксиды: , к-рые имеют меньшую плотность, чем сталь, и удаляются в шлак.
Диффузионное раскисление осуществляется раскислением шлака. Ферромарганец, ферросилиций и алюминий в измельчённом виде загружают на поверхность шлака. Раскислители, восстанавливая оксид Fe, уменьшают его содержание в шлаке. След-но, оксид Fe, растворённый в стали переходит в шлак. Образующиеся при этом процессе оксиды остаются в шлаке, а восстановленное Fe переходит в сталь, при этом в стали снижается содержание неметалл. включений и повышается ее кач-во.
В зависимости от степени раскисления выплавляют стали: а) спокойные, б) кипящие, в) полуспокойные.
Спокойная сталь получается при полном раскислении в печи и ковше.
Кипящая сталь раскислена в печи неполностью. Ее раскисление продолжается в изложнице при затвердевании слитка, благодаря взаим-вию оксида Fe и C: , Образующийся
выделяется из стали, способствуя удалению из стали N2 и H2, газы выделяются в виде пузырьков, вызывая её кипение. Кипящая сталь не содержит неметалл. включений, поэтому обладает хорошей пластичностью.
Полуспокойная сталь имеет промежуточную раскисленность м/у спокойной и кипящей. Частично она раскисляется в печи и в ковше, а частично – в изложнице, благодаря взаим-вию оксида Fe и C, содержащихся в стали.
4 Легирование стали осуществляется введением ферросплавов или чистых Ме в необх. кол-ве в расплав. Легирующие элементы, у к-рых сродство к О2 меньше, чем у Fe (), при плавке и разливке не окисляются, поэтому их вводят в любое время плавки. Легирующие элементы, у к-рых сродство к O2 больше, чем у Fe (
), вводят в Ме после раскисления или одновременно с ним в конце плавки, а иногда в ковш.
|
Раскисление стали
⇐ Предыдущая1234 5 678910Следующая ⇒
Раскисление стали заключается в восстановлении оксида Fe, растворённого в жидком Ме.
При плавке повышение содержания кислорода в Ме необходимо для окисления примесей, но в готовой стали кислород – вредная примесь, так как понижает механ-е св-ва стали, особенно при высоких темпер-рах.
Сталь раскисляют двумя способами: осаждающим и диффузионным.
Осаждающее раскисление осуществляется введением в жидкую сталь растворимых раскислителей (ферромарганца, ферросилиция, алюминия), содержащих элементы, которые обладают большим сродством к кислороду, чем Fe. В результате раскисления восст-ся Fe и образуются оксиды:
, к-рые имеют меньшую плотность, чем сталь, и удаляются в шлак.
Диффузионное раскисление осуществляется раскислением шлака. Ферромарганец, ферросилиций и алюминий в измельчённом виде загружают на поверхность шлака. Раскислители, восстанавливая оксид Fe, уменьшают его содержание в шлаке. Следовательно, оксид Fe, растворённый в стали переходит в шлак. Образующиеся при этом процессе оксиды остаются в шлаке, а восстановленное Feо переходит в сталь, при этом в стали снижается содержание неметалл-х включений и повышается ее кач-во.
Производство меди
⇐ Предыдущая45678 9 10111213Следующая ⇒
Медь – тяжелый цв. Ме, обладает высокой пластичностью, коррозионной стойкостью, малым уд. электросопротивлением, высокой теплопровод-тью, поэтому ее широко используют для изгот-я электропроводов, деталей эл. машин и приборов, в хим. машиностроении. Медные сплавы разделяют на бронзы (сплавы Cu с Pb, Al, Si, Sb и P) и латуни (сплавы Cu и Zn).
Cu в природе находится в виде сернистых соединений, оксидов, гидрокарбонатов, углекислых соединений в составе сульфидных руд и самородной металлической меди.
Гидрометаллургический способ – получение меди путём её выщелачивания слабым р-ром серной кислоты и последующего выделения металл. меди из р-ра.
Получение меди пирометаллургическимспособом состоит из обогащения, обжига, плавки на штейн, продувки в конвертере, рафинирования.
Обогащение медных руд производится методом флотации и окислительного обжига. Метод флотации основан на использовании различной смачиваемости медьсодержащих частиц и пустой породы. Позволяет получать медный концентрат, содержащий 10…35 % меди.
Медные руды и концентраты, содержащие большие количества S, подвергаются окислительному обжигу. В процессе нагрева концентрата или руды до 700…800 0C в присутствии кислорода воздуха сульфиды окисляются и содержание S снижается почти вдвое против исходного.
После обжига руда и медный концентрат подвергаются плавке на штейн, представляющий собой сплав, содержащий сульфиды Cu и Fe. Чаще всего плавка производится в пламенных отражательных печах. Темпер-ра в зоне плавки 1450 0C.
Полученный медный штейн, с целью окисления сульфидов и железа, подвергают продувке сжатым воздухом в горизонтальных конвертерах с боковым дутьём. Образующиеся окислы переводят в шлак, а серу – в . Тепло в конвертере выделяется за счёт протекания хим. реакций без подачи топлива. Темпер-ра в конвертере составляет 1200…1300°C. Так в конвертере получают черновую медь, содержащую 98,4…99,4 % меди, 0,01…0,04 % железа, 0,02…0,1 % серы и небольшое кол-во никеля, олова, сурьмы, серебра, золота. Эту медь сливают в ковш и разливают в стальные изложницы или на разливочной машине.
Черновую медь рафинируют для удаления вредных примесей, проводят огневое, а затем электролитическое рафинирование.
Сущность огневого рафинирования черновой меди заключается в окислении примесей, имеющих большее сродство к кислороду, чем медь, удалении их с газами и переводе в шлак. После огневого рафинирования получают медь чистотой 99…99,5%.
Электролитическое рафинирование проводят для получения чистой от примесей меди (99,95% Cu). Электролиз проводят в ваннах, где анод изготавливают из меди огневого рафинирования, а катод – из тонких листов чистой меди. Электролитом служит водный р-р CuSO4(10…16%) и H2SO4 (10…16%). При пропускании пост. тока анод растворяется, медь переходит в раствор, а на катодах разряжаются ионы меди, осаждаясь на них слоем чистой меди. Примеси осаждаются на дно ванны в виде шлака, к-рый идёт на переработку с целью извлечения Ме.
Медь по чистоте подразделяется на марки: М0 (99,95% Cu), М1 (99,9%), М2(99,7%), М3 (99,5%), М4 (99%).
Производство титана
⇐ Предыдущая56789 10 11121314Следующая ⇒
Титан – тугоплавкий Ме., обладает высокой коррозионной стойкостью. Титан и его сплавы используют для изгот-я деталей самолетов, в хим. машиностроении, судостроении и др.
Произв-во Ti включает обогащение титановых руд, выплавку из них титанового шлака с последующим получением из него четыреххлористого Ti и восст-е из последнего металл. Ti магнием.
Сырьем явл-ся титаномагнетитовые руды, из к-рых выделяют ильменитовый концентрат (ильменит FeO*TiO2).
Титановый шлак, полученый плавлением ильменитового концентрата с дрвесным углем и антрацитом, подвергают хлорированию в спец. печи: TiO2+2C+2Cl2=TiCl4+2CO
Ti из TiCl4 восст-ют в реакторах при темпер-ре 950…1000°С. В реактор загружаю чушковый Mg; после откачки воздуха и заполнения полости реактора аргоном внутрь подают газообразный TiCl4:
2Mg+ TiCl4=Ti+2MgCl2
Тв. частицы Ti спекаются в пористую массу – губку, а жидкий MgCl2 выпускают ч/з летку реактора. Для удаления из титановой губки примесей ее нагревают до 900..950°С в вакууме. Полученные слитки титана имеют дефекты, поэтому их вторично переплавляют, используя как расходуемые электроды. Чистота титана 99,6…99,7%.
Специальные способы литья
⇐ Предыдущая1011121314 15 16171819Следующая ⇒
В современном литейном производстве все более широкое применение получают специальные способы литья: в оболочковые формы, по выплавляемым моделям, кокильное, под давлением, центробежное и другие.
Эти способы позволяют получать отливки повышенной точности, с малой шероховатостью поверхности, минимальными припусками на механическую обработку, а иногда полностью исключают ее, что обеспечивает высокую производительность труда. Каждый специальный способ литья имеет свои особенности, определяющие области применения.
Литье в оболочковые формы - процесс получения отливок из расплавленного металла в формах, изготовленных по горячей модельной оснастке из специальных песчано-смоляных смесей.
Литье по выплавляемым моделям – процесс получения отливок из расплавленного металла в формах, рабочая полость которых образуется благодаря удалению (вытеканию) легкоплавкого материала модели при ее предварительном нагревании.
Литье в металлические формы (кокили) получило большое распространение. Этим способом получают более 40% всех отливок из алюминиевых и магниевых сплавов, отливки из чугуна и стали. Литье в кокиль – изготовление отливок из расплавленного металла в металлических формах-кокилях.
При центробежном литье сплав заливается во вращающиеся формы. Формирование отливки осуществляется под действием центробежных сил, что обеспечивает высокую плотность и механические свойства отливок.
Литьем под давлением получают отливки в металлических формах (пресс-формах), при этом заливку металла в форму и формирование отливки осуществляют под давлением.
Сущность процесса электрошлакового литья заключается в переплаве расходуемого электрода в водоохлаждаемой металлической форме (кристаллизаторе).
Тип и материал опок
Настоящий стандарт распространяется на литейные опоки, предназначенные для изготовления песчаных форм машинной и ручной формовкой.
Опоки должны изготовляться следующих типов:
-- цельнолитые из стали, чугуна и легких цветных сплавов;
-- сварные из стандартного и специального профильного проката, а также из литых стальных элементов;
-- сборные из стальных и чугунных элементов.
Опоки типов 1 и 2 -- предпочтительного применения.
По контуру в свету (конфигурации) опоки каждого типа разделяются на виды:
прямоугольные или квадратные (черт. 1);
круглые (черт. 2);
фасонные (черт. 3).
Рис. 8 Классификация опок по конфигурации
По массе опоки разделяются на категории, приведенные в табл. 1.
Таблица 1
Категория опок | Наименование опок | Масса, кг | |
Опоки | Полуформы | ||
1 | Ручные | до 30 | до 60 |
2 | Комбинированные (с ручным и крановым подъемом) | Свыше 30 до 60 | Свыше 60 |
3 | Крановые | Свыше 60 |
Примечание. Масса полуформы включает массу опоки и уплотненной формовочной смеси.
По способу формовки и положению при заливки опоки разделяются на группы, указанные в табл. 2.
Таблица 2
Группа опок | Способ формовки | Комплектность опок | Положение при заливке опок |
1 | Машинный | Парные (нижние, верхние) | Горизонтальное и вертикальное |
2 | Пескометный и ручной | Парные (нижние, верхние) тройные и более (нижние, средние, верхние) | |
3 | В почве | Одиночные (верхние) | Горизонтальное |
За основную расчетную величину для конструктивных элементов опок всех типов следует принимать средний размер в свету, где L -- длина опоки в свету, В -- ширина опоки в свету.
Для круглых опок средним размером в свету является диаметр.
Основные размеры опок должны соответствовать указанным на черт. 1,2, 3 и в табл. 3, 4, 5.
Средние размеры опок в свету для определенного их типа и материала указаны в табл. 6.
Таблица 6
Тип опок | Материал опок | Средний размер опок в свету, мм | ||||||
До 500 | Св. 500 до 755 | Св. 755 до1050 | Св. 1050 до 1500 | Св. 1500 до 2500 | Св. 2500 до 3500 | Св. 8500 до 5000 | ||
1 | Сталь | X | X | X | X | X | X | X |
Чугун | X | X | X | X | X | X | -- | |
Легкие цветные сплавы | X | X | X | X | X | -- | -- | |
2 | Стандартный прокат | X | X | X | X | X | --- | |
Специальный профильный прокат | X | X | X | X | -- | -- | -- | |
Литые стальные элементы | X | X | X | -- | -- | -- | -- | |
3 | Сталь | -- | -- | -- | X | X | X | X |
Чугун | -- | -- | -- | X | X | X | -- |
При габаритном размере отливки 390 мм выбираем опоку литую цельнолитую стальную прямоугольную с размерами в свету 500х600.
Плавильные печи для стали
Плавка стали происходит при температуре 1500-1600 градусов Цельсия. В процессе плавки необходимо снизить содержание веществ, ухудшающих качество стали, таких как сера, фосфор и кислород. Выбор футеровки зависит от состава желаемого расплава. Индукционные печи идеально подходят для производства легированных сталей. Время плавки стали в среднем занимает около 1 часа.
Эти печи работают, преимущественно, на промышленных частотах в 50 Гц и оснащаются высокоточной автоматикой, позволяющей контролировать как температуру, так и интенсивность ликвации. Величина угара в них едва достигает 2%, кроме того, они не требовательны к качеству подготовки шихтовых материалов.
Плавильные печи для меди
Плавка меди в индукционной печи занимает не более 40 минут. Процесс получения расплава происходит при температуре 1000-1300 градусов Цельсия. Плавить можно в вакууме, в среде защитных газов или в открытой среде. Благодаря высокой тепло- и электропроводности и гибкости медь широко используется в различных отраслях промышленности.
При производстве медного расплава очень важно обеспечить химическую чистоту, поэтому, печи, в ряде случаев, имеют герметичную рабочую камеру, а индукционный нагрев осуществляется в мягком режиме. Существенных конструктивных отличий от индукционных печей для цветных металлов здесь нет, основное же требование - отсутствие непосредственной реакции между материалом тигля и расплавом.
Производство стали
Сталью называют сплавы железа с углеродом и другими элементами. Такие сплавы обладают пластическими свойствами как в нагретом, так и в холодном состоянии и могут подвергаться прокатке, волочению, ковке и штамповке. Сталь содержит до 2% углерода и некоторое количество марганца, кремния, а также вредные примеси фосфора и серы. Кроме этого, в стали могут содержаться и легирующие элементы хром, никель, ванадий, титан и др.
В настоящее время сталь производят преимущественно путем передела чугуна, при котором из него удаляется избыток углерода, кремния, марганца, а также вредных примесей для придания стали необходимых свойств. Углерод и другие примеси при высокой температуре соединяются с кислородом гораздо энергичнее, чем железо, и их можно удалить при незначительных потерях железа. Углерод чугуна, соединяясь с кислородом, превращается в газ СО и улетучивается. Другие примеси превращаются в оксиды SiO2, МnО и Р2О, которые вследствие меньшего по сравнению с металлом удельного веса всплывают и образуют шлак. В настоящее время в промышленности в основном применяют конвертерный и мартеновский методы получения стали, кроме того, сталь получают в электрических дуговых и индукционных печах.
Единичный тип производство
Единичное производство — представляет собой форму организации производства, при которой различные виды продукции изготавливаются в одном или нескольких экземплярах (штучный выпуск).
Основные особенности единичного производства заключаются в том, что программа завода состоит обычно из большой номенклатуры изделий различного назначения, выпуск каждого изделия запланирован в ограниченных количествах. Номенклатура продукции в программе завода неустойчива. Неустойчивость номенклатуры, ее разнотипность, ограниченность выпуска приводят к ограничению возможностей использования стандартизованных конструктивно-технологических решений. В этом случае велик удельный вес оригинальных и весьма маленький удельный вес унифицированных деталей.
Каждая единица конечной продукции уникальна по конструкции, выполняемым задачам и другим важным признакам.
Производственный процесс изготовления продукции носит прерывный характер. На выпуск каждой единицы продукции затрачивается относительно продолжительное время. На предприятиях применяется универсальное оборудование, сборочные процессы характеризуются значительной долей ручных работ, персонал обладает универсальными навыками.
Распространено в тяжелом машиностроении (производство крупных машин для черной металлургии и энергетики), химической промышленности, в сфере услуг.
Цехи заводов единичного производства обычно состоят из участков, организованных по технологическому принципу. Значительная трудоемкость продукции, высокая квалификация привлекаемых для выполнения операций рабочих, повышенные затраты материалов, связанные с большими допусками, обусловливают высокую себестоимость выпускаемых изделий. В себестоимости продукции значительный удельный вес имеет заработная плата, составляющая нередко 20 — 25% от полной себестоимости.
Серийный тип производство
Серийное производство — это форма организации производства, для которой характерен выпуск изделий большими партиями (сериями) с установленной регулярностью выпуска.
Серийное производство — наиболее распространенный тип производства.
Характеризуется постоянством выпуска довольно большой номенклатуры изделий. При этом годовая номенклатура выпускаемых изделий шире, чем номенклатура каждого месяца.
Это позволяет организовать выпуск продукции более или менее ритмично. Выпуск изделий в больших или относительно больших количествах позволяет проводить значительную унификацию выпускаемых изделий и технологических процессов, изготовлять стандартные или нормализованные детали, входящие в конструктивные ряды, большими партиями, что уменьшает их себестоимость.
Серийный тип производства характерен для станкостроения, производства проката черных металлов и т.п.
Организация труда в серийном производстве отличается высокой специализацией. За каждым рабочим местом закрепляется выполнение нескольких определенных деталеопераций. Это дает рабочему хорошо освоить инструмент, приспособления и весь процесс обработки, приобрести навыки и усовершенствовать приемы обработки. Особенности серийного производства обуславливают экономическую целесообразность выпуска продукции по циклически повторяющемуся графику.
Подтипы серийного производства:
§ мелкосерийное;
§ серийное;
§ крупносерийное.
Мелкосерийное тяготеет к единичному, а крупносерийное — к массовому. Это деление носит условный характер. Например, в соответствии с классификацией, предложенной Вудворд выделяются единичное и мелкосерийное производство (Unit Production), массовое (Mass Production) и непрерывное (Process Production).
Производство мелкосерийное является переходным от единичного к серийному. Выпуск изделий может осуществляться малыми партиями.
В настоящее время в машиностроении одним из конкурентных факторов стала способность фирмы изготовлять уникальное, зачастую повышенной сложности оборудование малой партией по спецзаказу покупателей.
Внедрение компьютеризации позволяет повысить гибкость производства и внести в мелкосерийное производство черты поточного производства. Например, появилась возможность изготовлять несколько типов изделий на одной поточной линии с затратой минимального количества времени для переналадки оборудования.
Крупносерийное производство является переходной формой к массовому производству.
В крупносерийном производстве выпуск изделий осуществляется крупными партиями в течение длительного периода. Обычно предприятия этого типа специализируются на выпуске отдельных изделий или комплектов по предметному типу.
Массовый тип производства
Массовое производство — представляет собой форму организации производства, характеризующуюся постоянным выпуском строго ограниченной номенклатуры изделий, однородных по назначению, конструкции, технологическому типу, изготовляемых одновременно и параллельно.
Особенностью массового производства является изготовление однотипной продукции в больших объемах в течение длительного времени.
Важнейшей особенностью массового производства является ограничение номенклатуры выпускаемых изделий. Завод или цех выпускают одно-два наименования изделий. Это создает экономическую целесообразность широкого применения в конструкциях изделий унифицированных и взаимозаменяемых элементов.
Отдельные единицы выпускаемой продукции не отличаются друг от друга (могут быть только незначительные отличия в характеристиках и комплектации).
Время прохождения единицы продукции через систему относительно мало: оно измеряется в минутах или часах. Число наименований изделий в месячной и годовой программах совпадают.
Для изделий характерна высокая стандартизация и унификация их узлов и деталей. Массовое производство характеризуется высокой степенью комплексной механизации и автоматизации технологических процессов. Массовый тип производства типичен для автомобильных заводов, заводов сельскохозяйственных машин, предприятий обувной промышленности и др.
Значительные объемы выпуска позволяют использовать высокопроизводительное оборудование (автоматы, агрегатные станки, автоматические линии). Вместо универсальной оснастки используется специальная. Дифференцированный технологический процесс позволяет узко специализировать рабочие места посредством закрепления за каждым из них ограниченного числа деталеопераций.
Тщательная разработка технологического процесса, применение специальных станков и оснастки позволяют использовать труд узкоспециализированных рабочих-операторов. Вместе с тем широко используется труд высококвалифицированных рабочих-наладчиков.
Ручная и машинная формовки. Формовочные и стержневые смеси
⇐ Предыдущая678910 11 12131415Следующая ⇒
Формы изготавливаются вручную, на формовочных машинах и на автоматических линиях.
Ручная формовка применяется для получения одной или нескольких отливок в условиях опытного производства, в ремонтном производстве, для крупных отливок массой 200…300 тонн.
Приемы ручной формовки: в парных опоках по разъемной модели; формовка шаблонами; формовка в кессонах.
Формовка шаблонами применяется для получения отливок, имеющих конфигурацию тел вращения в единичном производстве
Шаблон – профильная доска. В уплотненной формовочной смеси вращением шаблона 1, закрепленного на шпинделе 2 при помощи серьги 3, оформляют наружную поверхность отливки и используют ее как модель для формовки в опоке верхней полуформы. Снимают шаблон 1, плоскость разъема покрывают разделительным слоем сухого кварцевого песка, устанавливают модели литниковой системы, опоку, засыпают формовочную смесь и уплотняют ее. Затем снимают верхнюю полуформу. Далее устанавливают шаблон 4, к-рым оформляют нижнюю полуформу, снимая слой смеси, равный толщине стенки отливки. Снимают шаблон и устанавливают верхнюю полуформу
Формовка в кессонах. Формовкой в кессонах получают крупные отливки массой до 200 тонн.
Кессон – железобетонная яма, расположенная ниже уровня пола цеха, водонепроницаемая для грунтовых вод.
Механизированный кессон имеет две подвижные и две неподвижные стенки из чугунных плит. Дно из полых плит, которые можно продувать (для ускорения охлаждения отливок) и кессона. Кессон имеет механизм для передвижения стенок и приспособлен для установки и закрепления верхней полуформы.
Машинная формовка используется в массовом и серийном производстве, а также для мелких серий и отдельных отливок.
Повышается производительность труда,
|
|
Поперечные профили набережных и береговой полосы: На городских территориях берегоукрепление проектируют с учетом технических и экономических требований, но особое значение придают эстетическим...
Типы оградительных сооружений в морском порту: По расположению оградительных сооружений в плане различают волноломы, обе оконечности...
Организация стока поверхностных вод: Наибольшее количество влаги на земном шаре испаряется с поверхности морей и океанов (88‰)...
Историки об Елизавете Петровне: Елизавета попала между двумя встречными культурными течениями, воспитывалась среди новых европейских веяний и преданий...
© cyberpedia.su 2017-2024 - Не является автором материалов. Исключительное право сохранено за автором текста.
Если вы не хотите, чтобы данный материал был у нас на сайте, перейдите по ссылке: Нарушение авторских прав. Мы поможем в написании вашей работы!