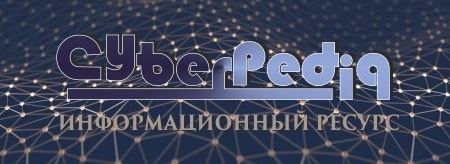
Эмиссия газов от очистных сооружений канализации: В последние годы внимание мирового сообщества сосредоточено на экологических проблемах...
Поперечные профили набережных и береговой полосы: На городских территориях берегоукрепление проектируют с учетом технических и экономических требований, но особое значение придают эстетическим...
Топ:
Процедура выполнения команд. Рабочий цикл процессора: Функционирование процессора в основном состоит из повторяющихся рабочих циклов, каждый из которых соответствует...
Отражение на счетах бухгалтерского учета процесса приобретения: Процесс заготовления представляет систему экономических событий, включающих приобретение организацией у поставщиков сырья...
Выпускная квалификационная работа: Основная часть ВКР, как правило, состоит из двух-трех глав, каждая из которых, в свою очередь...
Интересное:
Аура как энергетическое поле: многослойную ауру человека можно представить себе подобным...
Средства для ингаляционного наркоза: Наркоз наступает в результате вдыхания (ингаляции) средств, которое осуществляют или с помощью маски...
Наиболее распространенные виды рака: Раковая опухоль — это самостоятельное новообразование, которое может возникнуть и от повышенного давления...
Дисциплины:
![]() |
![]() |
5.00
из
|
Заказать работу |
|
|
Общие сведения. Электроэрозионная обработка металлов основана на воздействии электрических разрядов (импульсов) на отдельные участки обрабатываемой поверхности. Непосредственно в зоне обработки энергия разрядов между анодом (инструментом) и катодом (заготовкой) преобразуется в энергию тепловую. В зоне действия электрических разрядов температура достигает нескольких тысяч градусов, что приводит к оплавлению и даже испарению отдельных участков обрабатываемой поверхности, т. е. к так называемой эрозии металла. Так как электрические разряды возникают в последовательности, определяемой минимальными расстояниями между взаимодействующими поверхностями электродов, на электроде — заготовке отображается форма электрода — инструмента. Это позволяет эффективно обрабатывать изделия сложной формы.
Электроискровой метод разработан в 1943 г. советскими учеными Б. Р. и Н. И. Лазаренко. Он основан на явлении разрушения металла в цепи постоянного тока под действием искрового разряда.
При сближении металлических электродов в определенный момент происходит пробой межэлектродного пространства и он становится токопроводным. При этом возникает кратковременный мощный искровой разряд, с температурой 6000…11000 °С, что приводит к мгновенному расплавлению, испарению, взрывам и выбрасыванию частиц анода (детали). Процесс ведется в жидкой диэлектрической среде (масло, керосин), в которой оторвавшиеся от анода частицы охлаждаются и оседают. В связи с тем, что обработка ведется без соприкосновения заготовки и инструмента, представляется возможным обрабатывать токопроводящий металл любой твердости инструментом из мягкого металла (латуни, алюминия). Электроискровая обработка получила наибольшее распространение для прошивки отверстий любой формы в труднообрабатываемых материалах, включая твердые сплавы.
|
На рис. 7.1 приведена схема станка для прошивки отверстий. Па основании 8 установлена ванна 5 с диэлектрической жидкостью, и которой находится установленная на приспособлении 7 обрабатываемая заготовка 6. От зажима генератора импульсов 1 постоянный ток идет к катоду (инструменту) 4, через зазор δ — к аноду (заготовке) 6 и возвращается к другому зажиму генератора 1. Сопротивление R предназначено для регулирования силы тока и напряжения цепи, которые контролируются амперметром А и вольтметром V. Для образования одного за другим импульсных разрядов большой силы в электрическую цепь параллельно заготовке 6 и электроду — инструменту 4 включена конденсаторная батарея К.
Рис. 7.1. Схема электроискровой обработки
Как только инструмент — электрод приблизится к заготовке на величину пробивного зазора δ, возникает электрический разряд, на который затрачивается вся энергия, накопленная в батарее конденсаторов С. После разрядки конденсаторов, чтобы их зарядить, ток надо прервать. Таким образом, инструменту нужно сообщить колебательные перемещения (подачу S). Это осуществляют с помощью различных устройств, например, соленоидного регулятора 2, обеспечивающего замыкание и размыкание электрической цепи и автоматическое постепенное опускание инструмента. Форма инструмента должна соответствовать форме обработанной поверхности заготовки. Точность и шероховатость обработанной поверхности зависят от электрического режима обработки. При черновом режиме достигается шероховатость R z20, а при чистовом — 1,6…0,63.
Электроискровой метод обработки используется при изготовлении штампов, пресс-форм, кокилей, твердосплавных фильер, при извлечении поломанного инструмента и в некоторых иных случаях. Применение его ограничивается малой производительностью довольно быстрым износом инструмента вследствие высокой температуры при разряде.
|
Электро импульсный метод обработки, принципиальная схема которого показана на рис. 7.2, заключается в последовательном возбуждении разрядов между инструментом 5 и заготовкой 8, которая на специальном приспособлении 7 размещена в ванне с диэлектрическом жидкостью 6. От приводного электродвигателя 1 движение передается генератору импульсов 2, который дает импульсы только одного направления (униполярные). Между электродом — инструментом 5 и заготовкой 8 возникают электрические разряды. Колебательное
движение инструменту в направлении подачи S сообщает регулятор подачи 4. Для регулирования силы тока в цепь включено сопротивление 3. При предварительной обработке используются машинные генераторы, дающие импульсы большой длительности и энергии, а при чистовой—ламповые или транзисторные генераторы, дающие импульсы малой энергии, но высокой частоты. В отличие от электроискровой обработки при электроимпульсной заготовка является катодом, а инструмент — анодом. Температура в рабочей зоне (до 4000—5000 °С) значительно ниже, чем при электроискровой обработке, поэтому и инструмент срабатывается меньше. Электроды-инструменты изготавливают из меди, алюминия и его сплавов, чугуна, но наилучшими являются углеграфитовые электроды. Низкочастотная электроимпульсная обработка с питанием от машинных генераторов дает грубую поверхность с шероховатостью до Rz40 √ а высокочастотная (с частотой 7—25 кГц)—Rz20√:1.25√. Применяется электроимпульсная обработка преимущественно при трехкоординатной обработке штампов, пресс-форм, турбинных лопаток, ручьев в валках периодического проката и др.
Анодно-механическая обработка (предложена в 1943 г. В. Н. Гусевым). Она основана на одновременном действии электромеханического и электроискрового процессов, протекающих в среде электролита, которым является водный раствор жидкого стекла. При пропускании через ванну постоянного тока на поверхности заготовки — анода образуются пленки продуктов растворения металла, которые механически удаляются инструментом (катодом). Так как вершины шероховатостей на обрабатываемой поверхности анода отделены от катода небольшим промежутком, через него проходит кратковременный дуговой разряд. При этом микроскопический участок поверхности детали оплавляется и расплавленные частицы также удаляются движущимся анодом, т. е. происходят электроэрозионные процессы. Заготовке или инструменту сообщается движение подачи. При мягком режиме, когда плотность тока меньше 15 А/см2, обработка осуществляется в основном за счет электрохимического растворения и механического удаления пленки. Таким способом осуществляют так называемое анодно-механическое шлифование и достигают шероховатости поверхности 0.32…О.04. При более жестком режиме (при больших токах) удаление металла из зоны обработки осуществляется за счет электроэрозии и шероховатость обработанной поверхности отвечает Rz 160… Rz 20.
|
Этот метод эффективно используется при отрезании заготовки из труднообрабатываемых высокопрочных сплавов.
Рис. 7. 3 показана схема анодно-механического отрезания.
Инструмент — катод 2, которым служит тонкий диск из мягкой стали (рис. 7.3), вращающийся с большой скоростью, соприкасается с заготовкой — анодом 1. В зону контакта по трубе 3 подается жидкое стекло. Диск и заготовка подключаются к генератору постоянного тока. Процесс ведут на жестких электрических режимах, поэтому наряду с анодным растворением и механическим воздействием существенную роль играют электротермические процессы.
Электроконтактная обработка основана на электромеханическом разрушении металла под воздействием электродуговых разрядов быстро перемещающимся инструментом. Съем металла с заготовки 1 (рис. 7.4) осуществляется в воздушной среде вращающимся диском — электродом 2, который служит рабочим инструментом. Диск и заготовка соединены с источником питания — понижающим трансформатором 3. При вращении диска, к которому заготовка прижимается под давлением 2 • 104 Па —5 • 104 Па, происходит периодический разрыв контактов, возникают электродуговые разряды, под воздействием которых и разрушается металл заготовки. Соприкосновение под небольшим давлением двух металлических электродов (инструмента и заготовки) приводит к образованию в месте контакта повышенного переходного сопротивления.
|
Рис. 7.4. Схема электроконтактной обработки
Проходящий через место контакта электрический ток вследствие выделения джоулевого тепла нагревает, размягчает и плавит металл заготовки, облегчая его удаление. Во избежание сильного разогрева и плавления инструмента—электрода его вращают со скоростью, превышающей 30 м/с, при которой длительность соприкосновения контактирующего участка диска с заготовкой ничтожно мала. Вращающийся диск выбрасывает частицы раскаленного металла в виде снопа искр. Так как к инструменту и заготовке можно подвести ток большой мощности, интенсивность процесса достаточно велика и в ряде случаев может превзойти по производительности обычную обработку резанием. В то же время он не обеспечивает высокой точности и шероховатость поверхности не превосходит
Rz 80… Rz 20. Кроме того, при большом съеме металла в поверхностном слое происходят значительные фазовые изменения, могут возникнуть трещины и другие пороки. Поэтому электроконтактная обработка используется главным образом для выполнения грубых и неответственных операций, например зачистка отливок и штамповок из труднообрабатываемых сплавов.
Электрохимическая обработка
Общие сведения. При протекании постоянного электрического тока
между электродами анодом и катодом, которые находятся в ванне с раствором электролита, происходят определенные физико-химические процессы. На одном из них — явлении анодного растворения — основана электрохимическая обработка металлов. Анодное растворение заключается в том, что при прохождении постоянного тока через электролит электрод, соединенный с положительным полюсом источника тока (анод), растворяется. При этом металл анода (заготовки) на поверхности переходит в ионное состояние и выносится электролитом из рабочей зоны.
Электролитическое полирование. Этот метод получил широкое распространение при тонкой обработке. На поверхности детали, установленной в электролитической ванне на аноде, при прохождении тока образуется защитная пленка, предохраняющая впадины микронеровностей от его воздействия. Эта пленка не препятствует растворению микровыступов вследствие того, что на них действует более плотный поток электронов и поверхность детали сглаживается. Шероховатость обработанной поверхности зависит от тщательности предварительной обработки. Обычно в производственных условиях достигают R а = 0,63—0,08, но при обработке предварительно шлифованных поверхностей может быть достигнута шероховатость R а 0,04…0,01. Электролитическое полирование успешно используется для окончательной обработки сложных по конфигурации деталей (лопатки турбин, клапаны для подачи горючего, режущие и измерительные инструменты и др.). Помимо уменьшения шероховатости поверхности эта обработка благоприятно сказывается на коррозионной стойкости, усталостной прочности и пределе выносливости металла. Это объясняется тем, что при обработке в поверхностном слое не только не нарушается исходная структура, как это бывает при большинстве других методов обработки, но и удаляется ослабленный при предварительной обработке слой.
|
Электрохимическая размерная обработка. На рис. 7. 5 показано электрохимическое прошивание отверстия. Анодом при ЭХОК является заготовка 4, а катодом – инструмент (трубка) 5. К заготовке подается электролит через трубку. Зазор между торцом трубки и обрабатываемой поверхностью, исключающийся межэлектродный контакт, создается давлением вытекающего электролита. При прохождении через электролит электрического тока происходит анодное растворение металла заготовки в рабочей зоне и продукты растворения уносятся протекающим электролитом через отверстие в ванночке 7. В процессе обработки трубка 5 под действием пружины 6 совершает движение подачи, сохраняя постоянным межэлектродный зазор. Процесс может идти таким образом, что движение подачи и сохранение необходимого зазора осуществляется станком, на котором ведется обработка.
Рис. 7.5. Схема электрохимической размерной обработки
В струе электролита происходит растворение анода. Растворяет соли на заготовке и удаляет их из зоны обработки. При этом способе одновременно обрабатывается вся поверхность заготовки, которая находится под активным действием катода (инструмента). Это обеспечивает высокую производительность инструменту придает форму обработанную форме обрабатываемой поверхности происходит по методу отражения или копирования износа инструмента отсутствуют, так как по существу основную работу выполняют электролит. Способ используют для обработки заготовки из высокопрочных сплавов и других труднообрабатываемых материалов.
|
|
Папиллярные узоры пальцев рук - маркер спортивных способностей: дерматоглифические признаки формируются на 3-5 месяце беременности, не изменяются в течение жизни...
Адаптации растений и животных к жизни в горах: Большое значение для жизни организмов в горах имеют степень расчленения, крутизна и экспозиционные различия склонов...
Поперечные профили набережных и береговой полосы: На городских территориях берегоукрепление проектируют с учетом технических и экономических требований, но особое значение придают эстетическим...
Кормораздатчик мобильный электрифицированный: схема и процесс работы устройства...
© cyberpedia.su 2017-2024 - Не является автором материалов. Исключительное право сохранено за автором текста.
Если вы не хотите, чтобы данный материал был у нас на сайте, перейдите по ссылке: Нарушение авторских прав. Мы поможем в написании вашей работы!