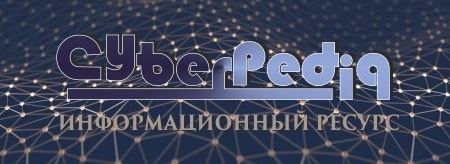
Эмиссия газов от очистных сооружений канализации: В последние годы внимание мирового сообщества сосредоточено на экологических проблемах...
Таксономические единицы (категории) растений: Каждая система классификации состоит из определённых соподчиненных друг другу...
Топ:
Оснащения врачебно-сестринской бригады.
Оценка эффективности инструментов коммуникационной политики: Внешние коммуникации - обмен информацией между организацией и её внешней средой...
Интересное:
Национальное богатство страны и его составляющие: для оценки элементов национального богатства используются...
Лечение прогрессирующих форм рака: Одним из наиболее важных достижений экспериментальной химиотерапии опухолей, начатой в 60-х и реализованной в 70-х годах, является...
Подходы к решению темы фильма: Существует три основных типа исторического фильма, имеющих между собой много общего...
Дисциплины:
![]() |
![]() |
5.00
из
|
Заказать работу |
|
|
Общая перспектива развития ходовых частей вагонов определяется перспективами развития всего железнодорожного транспорта и, в частности, подвижного состава. В настоящее время на магистральных железных дорогах СССР для грузовых вагонов допускаются нагрузки от колесной пары на рельсы до 22 тс. Выпускаемые промышленностью тележки грузовых вагонов рассчитаны на эту повышенную осевую нагрузку. В перспективе предполагается повысить допускаемую осевую нагрузку для грузовых вагонов до 25 тс, что потребует соответствующего усиления всех элементов ходовых частей. Металлурги отрасли вагоностроения изыскивают марки сталей с улучшенными прочностными и технологическими показателями. Эти стали должны обеспечить необходимую прочность узлов и деталей ходовых частей при минимальном увеличении их веса.
Одним из важнейших требований на перспективу развития ходовых частей вагонов является дальнейшая отработка конструкции и совершенствование технологии производства серийно выпускаемых тележек. Известно, например, что при существующей технологии производства в основных несущих деталях тележки еще полностью не исключены разностенность, рыхлоты и другие дефекты литья. Если эти дефекты останутся необнаруженными, то могут стать концентраторами напряжений, очагами нарушения целостности материала и причиной потери прочности детали. Важнейшим средством обеспечения качества отливки несущих деталей тележек является надежный неразрушающий контроль, который уже начали внедрять в вагоностроении.
При существующей конструкции опоры кузова на тележку через жесткий пятник возможна так называемая «перевалка» кузова, при которой контакт между пятником кузова и подпятником тележки происходит не по всей плоскости, а по кромке. Это приводит к ухудшению динамических качеств вагона, к повышенному износу элементов пятникового узла и даже к разрушению той части надрессорной балки, которая находится под пятником. Применение съемного подпятника, введение сферического узла опоры на тележку или упругих боковых скользунов может способствовать существенному улучшению условий работы этого узла.
|
Перспективны работы по совершенствованию рессорного подвешивания тележек грузовых вагонов. На существующих тележках с линейной жесткостью рессор статический прогиб подвешивания грузового вагона вынужденно ограничен сравнительно небольшой величиной, не превышающей 50 мм под нагрузкой брутто. При перевозке же легких грузов статический прогиб подвешивания вагонов составляет 8—12 мм. С целью улучшения ходовых качеств вагонов, в том числе при эксплуатации их в режиме малой нагрузки, в последние годы созданы тележки нескольких типов с нелинейным рессорным подвешиванием. Наиболее приемлемым вариантом нелинейного подвешивания является билинейное подвешивание.
Для улучшения динамических качеств ходовых частей в горизонтальном направлении, уменьшения интенсивности виляния и снижения боковых сил рекомендуется совершенствование параметров поперечного подрессоривання и узла опоры кузова на тележки. Рациональным является введение упругих скользунов в узел опоры.
Конкретные параметры перспективных тележек грузовых вагонов обоснованы многочисленными работами ВНИИВ, ЦНИИ МПС, ЛИИЖТ и МИИТ. В этих работах рекомендовано использовать одноступенчатое (центральное или буксовое) подвешивание, воспринимающее как вертикальные, так и горизонтальные (боковые) динамические воздействия. Разность высот рессорного подвешивания под нагрузкой брутто и нагрузкой тары может достигать 45 мм. При этом желательно иметь статический прогиб подвешивания под тарой около 20—25 мм. Для реализации таких параметров по прогибу целесообразно иметь билинейное подвешивание с перегибом кривой жесткости в точке, расположенной несколько выше точки статического прогиба в порожнем состоянии.
|
Горизонтальную жесткость подвешивания рекомендовано выбирать равной 700—1200 кгс/мм на тележку. При использовании центрального подвешивания между колесными парами и боковыми рамами необходима упругая связь в продольном и поперечном направлениях. Опору боковых рам на корпус буксы при этом целесообразно осуществлять через резинометаллический упругий элемент с жесткостью 1000—1600 кгс/мм на один буксовый узел.
Дальнейшему совершенствованию подлежат колесные пары и буксовые узлы тележек. Продолжаются работы по изысканию новых марок колесной и осевой сталей и улучшению технологии производства колес и осевых заготовок. Одной из важных задач в совершенствовании колесных пар тележек как грузовых, так и пассажирских вагонов является создание и внедрение в производство буксовых узлов с открытыми осевыми центрами.
Дальнейшее совершенствование тележек пассажирских вагонов связано со значительным повышением в перспективе скоростей пассажирских поездов (до 200—250 км/ч). На перспективу прототипом тележки пассажирского вагона может служить тележка ТСК-1 (рис. 31), спроектированная для вагонов скоростного поезда РТ-200. Эта тележка рассчитана на скорость движения 200 км/ч. Она имеет двойное подвешивание: буксовое из витых пружин и центральное безлюлечное из упругих пневматических элементов. В центральном подвешивании тележки ТСК-1 применены пневматические упругие элементы диафрагменного типа с резинокордной оболочкой модели 580x170. Опора кузова на тележки осуществлена через скользуны. Надрессорный брус связан с рамой тележки продольными поводками с резинометаллическими упругими элементами по концам. В буксовых узлах тележки использовано по три подшипника: два роликовых для восприятия радиальных сил и один шариковый — для восприятия осевых сил. Тележки оборудованы дисковым и магнитно-рельсовым тормозами. Для предотвращения заклинивания колес при торможении тормоз снабжен электронным противоюзным устройством.
![]() | Р |
При отработке конструкции тележки ТСК-1 совершенствуют узел упругой связи колесной пары с рамой тележки в продольном и поперечном направлениях. Жесткость этой связи в продольном направлении будет составлять 7500—8500 кгс/см, а в поперечном 2300—2700 кгс/см на одну колесную пару. Статический прогиб буксового подвешивания увеличится до 50—60 мм при номинальной нагрузке. Центральное подвешивание будет иметь статический эквивалентный прогиб 200—220 мм, а жесткость поперечного подрессоривания составит не более 700 кгс/см.
|
№30
Характеристики вагонов |
Одной из важных характеристик грузового вагона является его грузоподъемность, под которой понимают максимально допускаемую конструкцией нагрузку вагона, устанавливаемую МПС с учетом полного обеспечения безопасности движения поездов.
Удельная грузоподъемность вагона — это количество тонн грузоподъемности, приходящееся на 1 м' геометрического объема кузова (т/м').
Грузоподъемность и вместимость вагона могут быть полностью использованы при удельной грузоподъемности, равной плотности груза, т. е. массе 1 м' груза в том виде и состоянии, в которых его перевозят по железным дорогам. Если плотность груза меньше удельной грузоподъемности вагона, вместимость вагона используется полностью, а грузоподъемность — не полностью, при большой плотности — наоборот.
При разработке планов перевозок грузов по железным дорогам используют показатели техническая норма загрузки и статическая нагрузка вагона.
Техническая норма загрузки вагона — это обязательное количество груза, которое должно быть погружено в данный тип вагона при полном использовании вместимости или грузоподъемности. Эта норма устанавливается для каждого конкретного типа вагона при загрузке его конкретным грузом (для вагонов — в тоннах, для контейнеров в килограммах). Сетевые технические нормы загрузки вагонов разрабатываются и устанавливаются МПС, местные- дорогами погрузки.
Статическая нагрузка вагона — это количество тонн погруженного груза, приходящееся в среднем на один вагон.
Система нумерации подвижного состава позволила в восьмизначном номере объединить неповторяющийся инвентарный номер, присвоенный данной единице подвижного состава, основную характеристику его и кодовую защиту достоверности считывания номера.
|
Первая цифра характеризует род подвижного состава: 2 — крытые грузовые вагоны, 4 — платформы, 6 — полувагоны, 7 — цистерны, 8 — изотермические вагоны, 3 и 9 — прочие вагоны (специализированные и др.).
Общим для всех грузовых вагонов (помимо номеров прочих вагонов, начинающихся с цифры 3) является кодирование осности. Второй знак номера характеризует осность и основные характеристики вагона.
Цифры 0-8 обозначают четырехосные, цифра 9 — восьмиосные вагоны. Все шестиосные вагоны и транспортеры отнесены к прочим вагонам, номера которых начинаются с цифры 3 (у шестиосных вторая цифра номера — 6, у транспортеров — 9). Помимо осности, вторая цифра определяет: для крытых вагонов — объем кузова (0 — до 120 м', 1 — намного более 120 м', 4 — намного более 120 м' с уширенными дверными проемами), для платформ — длину рамы (0 — до 13,4 м, 2 — 13,4 м и больше), для четырехосных полувагонов- наличие люков в полу и торцовых дверей (0- с люками и торцовыми дверями, 4 — с люками без торцовых дверей, 8- с глухим кузовом), для цистерн — специализацию, для рефрижераторных вагонов и ледников — особенности конструкции.
Четвертый, пятый и шестой знаки в номере вагона определяют их порядковый номер и характеристик не содержат. В седьмом знаке цифра 9 свидетельствует о наличии у вагона (помимо рефрижераторных) переходной площадки. Восьмая цифра — контрольная. С ее помощью проверяется правильность считывания (передачи) номера. Она наносится слитно с остальными цифрами номера.
Техническая характеристика универсальных платформ | |||
Показатели |
Модели | ||
13-401 | 13-4012 | 13-491 | |
Грузоподъёмность, т | 70 | 71 | 66,5 |
Масса валька (тара), т | 20,92 | 21,4 | 26,5 |
Площадь пола, кв. м | 36,8 | 36,8 | 52 |
База, мм: | |||
валька | 9720 | 9720 | 144400 |
тележки | 1850 | 1850 | нет |
Длина, мм: | |||
по осям сцепления автосцепок | 14620 | 14620 | 19620 |
по концевым балкам рамы | 13400 | 13400 | 18400 |
кузова внутри | 13300 | 13300 | 18300 |
Ширина, мм: | |||
максимальная | 3150 | 3150 | 3062 |
кузова внутри | 2770 | 2770 | 2760 |
Высота бортов, мм: | |||
продольных | 500 | 500 | 500 |
торцевых | 400 | 400 | 400 |
Высота от уровня головок рельсов, мм: | |||
максимальная | 1820 | 1820 | 1820 |
до уровня пола | 1310 | 1320 | 1320 |
до оси автосцепок | 1040-1080 | 1040-1080 | 1040-1080 |
№31
|
|
Общие условия выбора системы дренажа: Система дренажа выбирается в зависимости от характера защищаемого...
Семя – орган полового размножения и расселения растений: наружи у семян имеется плотный покров – кожура...
Организация стока поверхностных вод: Наибольшее количество влаги на земном шаре испаряется с поверхности морей и океанов (88‰)...
Архитектура электронного правительства: Единая архитектура – это методологический подход при создании системы управления государства, который строится...
© cyberpedia.su 2017-2024 - Не является автором материалов. Исключительное право сохранено за автором текста.
Если вы не хотите, чтобы данный материал был у нас на сайте, перейдите по ссылке: Нарушение авторских прав. Мы поможем в написании вашей работы!