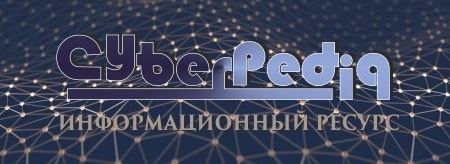
Эмиссия газов от очистных сооружений канализации: В последние годы внимание мирового сообщества сосредоточено на экологических проблемах...
Археология об основании Рима: Новые раскопки проясняют и такой острый дискуссионный вопрос, как дата самого возникновения Рима...
Топ:
История развития методов оптимизации: теорема Куна-Таккера, метод Лагранжа, роль выпуклости в оптимизации...
Устройство и оснащение процедурного кабинета: Решающая роль в обеспечении правильного лечения пациентов отводится процедурной медсестре...
Когда производится ограждение поезда, остановившегося на перегоне: Во всех случаях немедленно должно быть ограждено место препятствия для движения поездов на смежном пути двухпутного...
Интересное:
Влияние предпринимательской среды на эффективное функционирование предприятия: Предпринимательская среда – это совокупность внешних и внутренних факторов, оказывающих влияние на функционирование фирмы...
Берегоукрепление оползневых склонов: На прибрежных склонах основной причиной развития оползневых процессов является подмыв водами рек естественных склонов...
Что нужно делать при лейкемии: Прежде всего, необходимо выяснить, не страдаете ли вы каким-либо душевным недугом...
Дисциплины:
![]() |
![]() |
5.00
из
|
Заказать работу |
|
|
Основной задачей технологического процесса производства проката является получение прокатной продукции заданных форм, размеров и качества в необходимом количестве с минимальными затратами и наибольшей производительностью. Эта задача может быть решена только при точном соблюдении и выполнении всего технологического процесса производства проката и требований нормативно-технической документации.
Технологический процесс производства того или иного вида готового проката
включает в себя все необходимые последовательные операции обработки металла. Технологические операции в производстве проката весьма разнообразны. Однако существуют такие, которые являются основными и характерны для всех видов прокатного производства. К ним относятся: подготовка металла к прокатке, нагрев металла перед прокаткой, собственно прокатка, охлаждение проката, отделка готовой прокатной продукции. Каждая из этих операций является самостоятельной, но необходимой и взаимосвязанной с другими технологическими операциями производства проката. Совокупность технологических операций изготовления прокатной продукции, их необходимая последовательность представляют собой технологическую схему производства проката.
На металлургических предприятиях с полным металлургическим циклом технологической схемой производства проката является схема слиток – полупродукт (заготовка) – готовый прокат. В соответствии с этой схемой прокатное производство металлургического предприятия включает систему станов, обеспечивающих получение полупродукта в виде блюмов, слябов и заготовок из слитков и систему станов, выпускающих готовый прокат в виде сортового проката или горяче- и холоднокатаных листов и др., т.е. технологический процесс современного прокатного производства состоит из двух стадий: получение полупродукта (заготовки) и готовой продукции (готового проката).
|
В то же время технологическая схема производства того или иного вида готового проката предусматривает включение всех необходимых последовательных операций обработки, начиная с подготовки слитка или заготовки для нагрева и прокатки и кончая завершающей отделкой и определением качества готового проката (рисунок 26, а).
Следует отметить, прокатные цехи, имеющие в своем составе обжимные (блюминги, блюминги – слябинги, слябинги) и заготовочные станы, являются связующим звеном между сталеплавильными цехами и станами, выпускающими готовый прокат.
Для металлургических предприятий с неполным металлургическим циклом технологической схемой производства проката является либо слиток – готовый прокат, либо полупродукт – готовый прокат. В этих схемах отсутствуют операции, связанные с производством полупродукта непосредственно на данном предприятии, а процесс производства осуществляется или из заготовки, получаемой со стороны, или из слитка небольшой массы, из которого готовый прокат получают за один нагрев. Эти технологические схемы являются наиболее распространенными на металлургических предприятиях. Успешное развитие непрерывной разливки стали на металлургических предприятиях значительно изменило технологическую схему производства проката и преобразовало ее в схему непрерывнолитая заготовк – готовый прокат (рисунок 26, б). Использование непрерывнолитой заготовки в прокатных цехах при производстве готового проката является эффективным процессом, позволяющим исключать целый ряд технологических операций и дорогостоящие обжимные и заготовочные станы из технологического процесса производства проката.
Дальнейшее развитие процессов непрерывной разливки и прокатки, выражающееся в их совмещении, значительно изменяет технологическую схему производства проката непрерывная разливка – готовый прокат и сокращает цикл металлургического производства, исключая такие технологические операции, как нагрев, транспортировку и складирование металла.
|
Как уже было отмечено, основными технологическими операциями в прокатных цехах являются подготовка металла к прокатке, нагрев металла перед прокаткой, собственно прокатка, охлаждение проката, отделка готовой продукции.
Подготовка исходных материалов (слитков и заготовок) к прокатке состоит в удалении с них различных поверхностных дефектов: плен, волосовин, трещин, закатов, царапин и некоторых других. Эта операция особенно важна при прокатке качественной углеродистой и легированной стали, идущей на изготовление ответственных деталей машин в различных отраслях промышленности. В этом случае затраты на подготовку материалов окупаются увеличением выхода годного и получением надлежащего качества готовой продукции.
Необходимость удаления поверхностных дефектов на металле вызывается тем обстоятельством, что они, как правило, не устраняются в процессе прокатки, а переходят на
а б
а – производство проката из слитка;
б – производство проката из непрерывнолитой заготовки
Рисунок 26 – Последовательность операций в технологических схемах
производства проката
готовый прокат. Большую часть поверхностных дефектов металла удаляют путем зачистки. Наиболее экономичным способом удаления поверхностных дефектов является огневая зачистка. Ее применяют для снятия как местных дефектов, так и всего поверхностного слоя. В процессе такой зачистки слой металла сжигается и удаляется с поверхности кислородной струей. Большое значение для улучшения качества зачистки имеет степень чистоты кислорода.
Огневую зачистку осуществляют вручную и специальными машинами. Как правило, при ручной огневой зачистке удаляются определенные дефекты поверхности слитков и заготовок. В этом случае резак подводят к дефекту и в течение нескольких секунд подогревают металл до 950–1000 °С. Резак устанавливают под углом 75–80° к поверхности заготовки. После достижения температуры воспламенения металла увеличивают количество впускаемого в резак кислорода, который сжигает и удаляет слой металла, при этом наклон резака к поверхности заготовки уменьшают до 25–30°.
|
В настоящее время огневой зачистке подвергают стали почти всех видов. Легко
поддаются огневой зачистке все углеродистые и низколегированные стали. При огневой зачистке нержавеющих, жаропрочных и других сталей с большим содержанием хрома применяют специальные флюсы и обмазки, облегчающие зажигание и получение легкоплавкого шлака.
Широкое распространение получили машины огневой зачистки, устанавливаемые в технологическом потоке на линии рольганга между блюмингом или слябингом и ножницами.
При машинной огневой зачистке удаление поверхностных дефектов осуществляется сплошным сжиганием поверхностного слоя с двух или четырех сторон раската.
Сплошную механизированную огневую зачистку применяют также на складе заготовок. При этом металл зачищают в холодном или подогретом состоянии комбинированными агрегатами, которые совмещают осмотр и зачистку заготовок.
К другим способам удаления поверхностных дефектов с заготовок и слитков относят вырубку (зачистку) пневматическими молотками и абразивную зачистку.
Вырубка поверхностных дефектов пневматическими молотками – операция малопроизводительная (особенно при обработке легированной стали) и вредная для здоровья рабочих. Этот способ является наиболее трудоемким в прокатном производстве и не соответствует современным масштабам производства. Его применяют преимущественно в качестве дополнительной отделочной операции при зачистке другими способами.
Широкое распространение в прокатных цехах получила абразивная зачистка круга-
ми для сплошного и выборочного удаления поверхностных дефектов. Для абразивной зачистки применяют подвесные стационарные и переносные специальные станки. Используемые для зачистки металла абразивные круги различаются по шлифующему материалу (карборундовые, электрокорундовые), связке (керамическая, бакелитовая), размеру зерна, твердости, профилю. Применение того или иного абразивного круга определяется свойствами зачищаемого металла. Абразивную зачистку применяют в основном при производстве легированных сталей, ибо только в этом случае становится экономически целесообразным применение данного способа.
|
Нагрев исходных материалов перед прокаткой осуществляется с целью повышения его пластичности и уменьшения сопротивления деформации. Нагрев является одной из важных и основных операций в процессе прокатки. Он должен обеспечить равномерное распределение температуры по сечению прокатываемого металла, его минимальное окисление и обезуглероживание, повышение механических свойств, уменьшение чувствительности стали к флокенам и т.д.
Продолжительность нагрева определяется физико-химическими свойствами нагреваемой стали, температурными условиями, зависящими от конструкции печи, расположения металла в печи, формы и размеров нагреваемых заготовок.
Правильно выбранный режим и температурные интервалы нагрева позволяют получить однофазную структуру. Благодаря диффузии происходит перераспределение примесей и выравнивание состава металла (гомогенизация).
При нагреве исходных материалов в нагревательных устройствах всегда происходит окисление металла – процесс химического взаимодействия окислительных печных газов с железом, примесями и легирующими компонентами с образованием на поверхности слитка или заготовки окалины. Наружный, самый тонкий слой окалины состоит из Fe2O3 (гематита), средний – из Fe3O4, (магнетита) и внутренний – самый толстый слой – из FeO (вюстита).
Образование окалины при нагреве является источником потерь годного металла. Угар металла при нормальной работе нагревательных устройств составляет 1–2 % от массы нагреваемого металла. Если учесть, что металл при прокатке от слитка до готового продукта нагревают несколько раз, то можно принять угар в среднем 3–4 % от массы нагреваемого металла. Кроме того, окалина при прокатке вдавливается в металл, что ухудшает качество поверхности, ускоряет износ валков, а также способствует образованию брака в результате вскрытия подкорковых пузырей. В связи с этим возникает необходимость удаления окалины с поверхности прокатываемой полосы. При горячей прокатке листовой стали на станах устанавливают специальные клети – окалиноломатели – для дробления окалины, которая затем сбивается водой высокого давления (гидросбив). Окалину с поверхности горячекатаных рулонов перед холодной прокаткой удаляют травлением их в растворе кислоты, чтобы окалина не вдавливалась при холодной прокатке и для уменьшения износа валков и обеспечения чистой поверхности листовой стали.
На образование окалины влияет температура нагрева, продолжительность пребывания металла при высоких температурах, скорость нагрева и печная атмосфера.
|
Наряду с окислением металла происходит обезуглероживание поверхностного слоя, представляющее процесс взаимодействия печных газов с углеродом стали, приводящее к уменьшению содержания углерода в поверхностном слое металла. Обезуглероживание зависит от тех же факторов, что и окали-нообразование.
Повышение температуры металла при его нагреве, как правило, благоприятно влияет на процесс прокатки. Однако при нагреве выше определенной для данной стали температуры происходит рост зерна, который ведет к ослаблению связи между ними и тем самым к ухуддшению механических свойств стали. Такое явление называетмся перегревом. В ряде случаев свойства перегретой стали можно улучшить, подвергнув ее термической обработке. Сильный перегрев исправить нельзя, так как зерна сильно перегретой стали теряют способность к рекристаллизации и при нагреве остаются неизменными.
При температурах, близких к точке плавления стали, внутрь ее проникает кислород, который окисляет зерна. В результате связь между зернами стали настолько ослабляется, что металл при прокатке разрушается. Это явление называется пережогом.
Явления перегрева и пережога чаще всего возможны при вынужденной задержке металла в печи. В этом случае понижают температуру в печи и уменьшают количество подаваемого воздуха.
Для нагрева применяют нагревательные устройства различных конструкций: нагревательные колодцы, методические, камерные, туннельные, колпаковые печи.
Важно, чтобы при нагреве исходного металла до заданной температуры был обеспечен равномерный нагрев его по всему сечению. Неравномерный нагрев способствует образованию внутренних разрывов, увеличению износа прокатных валков и вызывает опасность поломки их и т.д. Нагретый металл, если он равномерно нагрет по всему сечению и длине, значительно легче деформируется.
После прокатки на соответствующем типе стана до заданного профиля одним из основных заключительных процессов является охлаждение проката.
Необходимость охлаждения проката вызвана предохранением его от образования поверхностных и внутренних трещин, остаточных напряжений и получением нужной структуры и физико-механических свойств металла.
Из-за неравномерной потери тепла по поперечному сечению проката при его ох-
лаждении и происходящих в нем структурных превращений в нем возникают напряжения. В начальный период охлаждения поверхностные слои испытывают напряжения растяжения, а внутренние – напряжения сжатия. В последующие периоды охлаждения, наоборот, поверхностные слои – напряжения сжатия, внутренние – растяжения. Эти тепловые напряжения накладываются на напряжения, возникающие по другим причинам, и в результате величина их может достичь значений, превышающих прочность металла. В металле образуются внешние или внутренние микро- или макротрещины, которые служат причиной появления более глубоких трещин или даже полного разрушения.
В зависимости от состава, скорости падения температуры металла при его охлаждении, склонности к образованию пороков, связанных с охлаждением, применяются различные способы охлаждения: обычное, замедленное, ускоренное и быстрое.
Обычное охлаждение металла осуществляется на воздухе, на стеллажах, на холодильниках. Такому охлаждению подвергают стали, не склонные к образованию трещин и флокенов. При обычном охлаждении металл должен терять температуру как можно быстрее.
Замедленное охлаждение применяется для уменьшения температурного перепада по сечению готового проката и обеспечения более полного протекания процесса рекристаллизации с целью снижения величины остаточных термических и структурных напряжений и предотвращения образования флокенов и трещин. Охлаждение осуществляют в проходных отапливаемых печах, отапливаемых и неотапливаемых колодцах.
Ускоренное охлаждение характеризуется очень высокими скоростями охлаждения, достигающими 300–400 °С/с, и может применяться только к сталям, не чувствительным к образованию дефектов при любых скоростях охлаждения. По своей сути этот способ является закалкой стали с прокатного нагрева. Полнота закалки регулируется продолжительностью выдержки в воде или ее давлением и температурой воды. Целью ускоренного охлаждения является получение мелкозернистого строения стали; предотвращение образования карбидной сетки при прокатке высокоуглеродистой и подшипниковой стали; повышение физико-механических характеристик прокатанного металла; получение чистой от окалины поверхности проката; сокращение производственных площадей и снижение себестоимости проката. Ускоренное охлаждение используется для листового проката и катанки перед сматыванием в рулоны и бунты.
Быстрый (термоупрочняющий) режим охлаждения обеспечивает закалку с последующим режимом самоотпуска с прокатного нагрева. С этой целью применяют регулируемые системы быстрого охлаждения водой. При охлаждении металла могут образовываться наружные и внутренние трещины (флокены). Наружные трещины образуются в результате возникновения остаточных напряжений при прокатке и охлаждении.
Отделка проката является заключительной технологической операцией процесса прокатки, позволяющей получить прокат с требуемыми ГОСТом и ТУ механическими и другими служебными свойствами и придать ему товарный вид. К отделочным операциям относятся термическая обработка, очистка поверхности от окалины, порезка и правка, сплошная и выборочная зачистка поверхностных дефектов, контроль качества металла, маркировка, упаковка и т.д.
Важную отделочную операцию сортовой стали представляет собой термическая обработка. Наиболее распространенными способами термической обработки являются различные виды отжига – полный, неполный, изотермический, рекристаллизационный, сфероидизирующий, диффузионный, а также нормализация, закалка и отпуск.
Очистка поверхности проката осуществляется травлением его в растворах серной и соляной кислот. В процессе травления часть окалины растворяется, а часть отслаивает-
ся. Прокат после травления промывают в чистой воде и нейтрализуют в щелочной ван-
не. Окалину удаляют также путем дробеметной очистки и иглофрезерованием.
Резку осуществляютдля порезки металла на заданные длины. Разрезка пилами применяется для относительно крупных заготовок. Заготовка характеризуется высокой точностью по длине, хорошим качеством среза, перпендикулярностью торца к оси. Основными недостатками являются низкая производительность и значительные потери металла на рез.
Разрезка на эксцентриковых пресс-ножницах применяется для стального проката круглого или квадратного сечения до 300 мм. Является наиболее производительным и дешевым процессом разделки проката на заготовки. Основными недостатками являются косой рез и смятие концов заготовки.
Листовой прокат разрезают на гильотинных ножницах.
Правку металла используют как с целью придания прокату товарного вида, так и с целью осуществления необходимых отделочных операций (светление, абразивная зачистка, снятие заусенцев).
Иногда правку выполняют в горячем состоянии, например, при производстве толстых листов. Но обычно – в холодном состоянии, так как последующее охлаждение после горячей правки может вызвать дополнительное изменение формы.
Процесс правки заключается в однократном или многократном пластическом изгибе искривленных участков полосы, каждый раз в обратном направлении.
Правку можно выполнять и растяжением полосы, если напряжения растяжения будут превышать предел текучести материала.
Роликоправильные машины с параллельно расположенными роликами предназначены для правки листа и сортового проката (рисунок 27).
Процесс правки заключается в прохождении полосы между двумя рядами последовательно расположенных роликов, установленных в шахматном порядке таким образом, что при движении полосы, ее искривление устраняется.
Рисунок 27 – Схема правки проката на роликоправильных машинах с
параллельно расположенными роликами
Правильные машины с косорасположенными гиперболоидальными роликами предназначены для правки труб и круглых прутков (рисунок 28).
Рисунок 28 – Схема правки проката на машинах с косорасположенными
гиперболоидальными роликами
Ролики выполняют в виде однополостного гиперболоида и располагают под неко-
торым углом друг к другу. Выправляемый металл, кроме поступательного движения, совершает вращательное, что вызывает многократные перегибы полосы роликами и обеспечивает осесимметричную правку.
Растяжные правильные машины используют для правки тонких листов (менее 0,3 мм), трудно поддающихся правке на роликоправильных машинах.
Различают сплошную и выборочную зачистку поверхности проката. Сплошную зачистку применяют в случае значительной пораженности дефектами проката; выборочную – при наличии на поверхности проката или единичных дефектов, или небольших дефектных участков. Зачистка поверхности проката осуществляется методами, которые рассматривались выше.
Пакетирование и увязка проката являются окончательной операцией прокатного производства. Их качество определяет товарный вид пакетов и их сохранность при транспортировке. В зависимости от профиля и размеров прокат собирают в круглые или прямоугольные пакеты.
Производство полупродукта
Полупродукт – это промежуточный продукт технологического процесса, предназначенный для дальнейшей переработки. В производстве проката полупродуктом являются блюмы, слябы, заготовка. В настоящее время полупродукт получают двумя способами: прокаткой слитков на обжимных и заготовочных станах и непрерывной разливкой на машинах непрерывного литья заготовок.
Обжимные и заготовочные станы являются промежуточным звеном между сталеплавильными и прокатными цехами, производящими готовый прокат.
На блюмингах и слябингах осуществляется прокатка слитков, различных по размерам и массе, что определяется марочным составом стали, изготовляемым на заводе.
Перед прокаткой осуществляется нагрев слитков в нагревательных колодцах с целью придания металлу высокой пластичности и наименьшего сопротивления его деформации.
Продолжительность нагрева слитков определяется их химическим составом, температурой посада металла в нагревательные устройства и отношением поверхности к их массе.
В настоящее время свыше 90 % слитков в нагревательные колодцы блюмингов и слябингов поступает с температурой 800–900 0С. Такой метод нагрева называется горячим посадом слитков. Применение горячего посада значительно экономит топливо и резко увеличивает пропускную способность нагревательных колодцев.
Посадку слитков производят специальным клещевым краном, а в колодцах их уста-
навливают прибыльной частью вверх. Нагретые слитки при помощи тележки с опрокидывателем (слитковоза) подают к рабочей клети блюминга или слябинга.
Число проходов, за которые прокатывают слитки, предусматривают технологиче-
скими инструкциями. На отечественных обжимных станах стремятся к увеличению обжатий за проход, что приводит к сокращению их числа, а значит, и повышению производительности станов.
Эффективным путем повышения производительности обжимных станов является технология многослитковой прокатки. Многослитковая прокатка заключается в последовательной прокатке двух или более слитков, лежащих на рольганге последовательно один за другим. В каждом пропуске второй слиток подается в валки стана непосредственно за первым без паузы или с минимальной паузой. Многослитковая прокатка ведется опреде-
ленное число пропусков. При достижении раскатами значительной длины каждым в пос-
ледних пропусках их кантуют порознь, а прокатывают парами или по одному.
Технология многослитковой прокатки обеспечивает уменьшение почти в два раза суммарного времени пауз и некоторое уменьшение машинного времени.
После выхода из клети полупродукт в технологическом потоке проходит сплошную зачистку поверхности в машинах огневой зачистки. Эта операция полностью
механизирована и частично автоматизирована.
Иногда на блюмингах и заготовочных станах вместо машин огневой зачистки устанавливают фрезерные многорезцовые станки – термофрезерные машины – для механической зачистки снятием стружки с горячих слитков, блюмов, слябов и заготовки. Этот способ является весьма эффективным.
За машиной огневой зачистки осуществляется обрезка переднего и заднего концов раскатов и порезка их на мерные длины на ножницах. Величина обрези в зависимости от марки стали и условий кристаллизации со стороны усадочной раковины обычно составляет 12–14 % от массы раската, с донной части 2–3 %.
После разрезки на ножницах блюмы или слябы клеймят с торца в горячем состоянии при помощи специального клеймовочного устройства. В клеймо обычно входят следующие знаки и цифры: условный знак завода, марка стали, номер плавки, литера головного блюма или сляба от данного слитка и др.
Полученный полупродукт больших сечений может сразу в потоке прокатываться на заготовочных станах или передаваться к печам сортовых станов.
Готовые блюмы и слябы в пролете остывания укладывают в штабеля.
Остывший полупродукт, в случае необходимости, зачищают и после приемки контроллерами передают на склад заготовки.
|
|
Индивидуальные и групповые автопоилки: для животных. Схемы и конструкции...
Археология об основании Рима: Новые раскопки проясняют и такой острый дискуссионный вопрос, как дата самого возникновения Рима...
Автоматическое растормаживание колес: Тормозные устройства колес предназначены для уменьшения длины пробега и улучшения маневрирования ВС при...
Типы сооружений для обработки осадков: Септиками называются сооружения, в которых одновременно происходят осветление сточной жидкости...
© cyberpedia.su 2017-2024 - Не является автором материалов. Исключительное право сохранено за автором текста.
Если вы не хотите, чтобы данный материал был у нас на сайте, перейдите по ссылке: Нарушение авторских прав. Мы поможем в написании вашей работы!