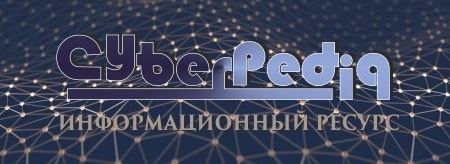
Двойное оплодотворение у цветковых растений: Оплодотворение - это процесс слияния мужской и женской половых клеток с образованием зиготы...
Эмиссия газов от очистных сооружений канализации: В последние годы внимание мирового сообщества сосредоточено на экологических проблемах...
Топ:
Проблема типологии научных революций: Глобальные научные революции и типы научной рациональности...
Особенности труда и отдыха в условиях низких температур: К работам при низких температурах на открытом воздухе и в не отапливаемых помещениях допускаются лица не моложе 18 лет, прошедшие...
Комплексной системы оценки состояния охраны труда на производственном объекте (КСОТ-П): Цели и задачи Комплексной системы оценки состояния охраны труда и определению факторов рисков по охране труда...
Интересное:
Уполаживание и террасирование склонов: Если глубина оврага более 5 м необходимо устройство берм. Варианты использования оврагов для градостроительных целей...
Распространение рака на другие отдаленные от желудка органы: Характерных симптомов рака желудка не существует. Выраженные симптомы появляются, когда опухоль...
Национальное богатство страны и его составляющие: для оценки элементов национального богатства используются...
Дисциплины:
![]() |
![]() |
5.00
из
|
Заказать работу |
|
|
При жестяницких работах применяют измерительный и разметочный, режущий, ударный, опорный и вспомогательный инструменты.
В группу измерительного и разметочного инструмента входят: линейка, складной метр, рулетка, угольники стальные, транспортир, угломеры, штангенциркуль, циркуль, очертка, чертилка, кернер и рейсмус.
В группу режущего инструмента входят ручные ножницы, ножовка ручная, напильники и кусачки.
Ручные ножницы предназначаются для резки листового материала: с прямыми лезвиями по прямой линии и с кривыми лезвиями по криволинейному контуру. Существуют правые и левые ножницы. У правых ножниц верхний нож расположен с правой стороны, а у левых — с левой.
Режущие лезвия ножниц при закрывании должны проходить одно около другого с небольшим трением, так как при наличии зазора между лезвиями разрезаемый материал сминается, а иногда и затягивается в этот зазор.
К группе ударного и опорного инструмента относят деревянный молоток, наводильник, гладильник, выколо-точные молотки, наковальни, оправки, стойки, скребки и шпераки.
Ударный инструмент.
К ударным инструментам предъявляются следующие требования: рабочие поверхности тщательно полируют, так как наличие неровностей на поверхности ударного инструмента служит причиной возникновения засечек и царапин на поверхности изготовляемого изделия; рабочую часть металлических молотков закаляют; молотки прочно насаживают на ручку; ручки должны иметь овальную форму и гладкую поверхность без сучков, выбоин и других дефектов.
Деревянный молоток (киянку) изготавливают из твердых пород дерева, пластмассы и резины и применяют для правки листов, посадки гофра, отбортовки кромок, образования фальца. Размеры молотка подбирают в зависимости от размера детали. Кроме молотков с плоскими рабочими поверхностями, имеются фасонные молотки со сферической и другими поверхностями.
|
Наводильник служит для посадки гофра, отбортовки кромок и разводки деталей, изготовляется из углеродистой инструментальной стали.
Гладильник необходим для правки сильно покоробленных мест и проковки листов.
Выколоточные молотки (шариковые) двусторонние и односторонние со сферическими бойками предназначаются для выколотки вручную изделия с шарообразной поверхностью.
Опорный инструмент
Опорный инструмент должен иметь отполированную рабочую поверхность. Рабочая часть его закалена и отпущена к хвостовой части.
Кованые и сварные наковальни различных форм применяют для правки листов, загибания кромки в углах, отбортовки. Изготовляют их из инструментальной стали У7. У сварных наковален хвостовик делают из обычной конструкционной стали, а рабочую часть — из инструментальной, так как в дальнейшем она подвергается закалке и отпуску. Во время работы наковальни закрепляют в тисках или деревянных подставках.
Оправки (рельсовая оправка, брус и верстачный угольник) необходимы в тех же случаях, что и наковальни. Изготовляют их из углеродистой стали.
Стойки разнообразных форм и размеров предназначены для выколотки шаровых поверхностей, правки днищ, бортиков и круглых деталей. Изготовляют стойки из инструментальной стали.
Скребки используют при гибке, закатывании проволоки. Изготовляют их из инструментальной стали. Во время работы закрепляют в тисках или деревянных подставках.
Шпераки применяют для правки, гибки и развальцовки труб, правки конусов, загибания кромок. Их изготовляют из инструментальной стали цельными и сварными. Для работы закрепляют в тисках.
В группу вспомогательного инструмента входят круглогубцы, ручные гофрилки, фальцмейсель, тиски ручные, струбцины, плита для правки плоскостей и дрели.
|
Круглогубцы с закаленными и отполированными губками употребляют для гофрирования металла при его посадке. Для этих же целей применяют ручные гофрилки (рис. 1а), изготовляемые из конструкционной стали, рабочая поверхность которых должна быть чисто отполирована.
Фальцмейсель (рис. 1б) предназначен для уплотнения фальцевых швов.
Тиски ручные применяют для закрепления деталей небольших размеров при опиливании и правке, параллельные тиски — для закрепления деталей большого размера.
Струбцины служат для прижимания деталей к макетам при выколотке и шаблонов к листу при разметке.
Плиту для правки плоскостей изготовляют из чугуна или конструкционной стали. Она должна быть с гладкой поверхностью.
Дрели для сверления отверстий бывают ручные, электрические и пневматические. Подробное описание дрелей приводится в пособиях по слесарным работам.
Оборудование
Рабочий верстак представляет собой прочный и устойчивый стол, верхняя крышка которого обита мягким войлоком или резиной и окантована уголковым железом. На верстаке установлены тиски, плита для правки плоскостей, стальной брус или рельсовая оправка с полированной рабочей частью. Верстак имеет выдвижные ящики для хранения инструмента и мелких приспособлений и полки для заготовок и материала.
Рычажные ножницы предназначены для разрезания листового материала любой длины по прямой линии. Для отрезания полос одинаковой ширины ножницы имеют упор. Параллельность сторон полосы обеспечивается установленной на столе неподвижной упорной линейкой.
Режущая кромка верхнего ножа изогнутой формы, благодаря чему во время работы угол между лезвием ножа и материалом не изменяется. Противовес на конце держателя ножа предназначен для предупреждения самоопускания верхнего ножа и обеспечивает равномерный нажим на разрезаемый материал. Прижимная планка (прижим) прижимает листовой материал к столу при его резке.
Ножницами можно резать материал толщиной до 1,5 мм с пределом прочности на разрыв, равным 45—50 кг/мм2. Наибольшая ширина отрезаемой полосы при работе с упором 460 мм.
Прямолинейное и криволинейное разрезание листового материала проводится вибрационными электрическими ножницами, у которых нижний нож неподвижен, а верхний быстро вибрирует в вертикальном направлении. Положение нижнего ножа по высоте изменяют с помощью регулировочного винта.
|
Угол заточки лезвий ножей зависит от твердости разрезаемого материала: для стали он равен 6—7°, а для алюминиевых сплавов — 10—12°.
Тупые ножи затачивают только с тыльной стороны, так как при заточке передних граней ножей увеличивается зазор между ними, что приводит к сминанию разрезаемого материала.
Зигмашина — несложный универсальный станок, состоящий из станины, профилировочного механизма, имеющего верхний и нижний ролики, упора, механизма привода и регулировочного механизма.
С помощью регулировочного механизма верхний ролик перемещается в вертикальном направлении и нижний в осевом.
В механизм привода ручной зигмашины входят рукоятка и несколько зубчатых колес. От него движение передается на два параллельных вала, вращающихся в противоположные стороны. На выступающих концах валов гайками крепят сменные ролики 2 различной формы и ширины. При вращении ролики захватывают материал и протаскивают его, образуя углубления различной глубины и формы.
В зависимости от формы роликов на зигмашине проводят отбортовку, рифтовку материала и закатывание проволоки. Если вместо роликов на зигмашину установить дисковые ножи, то можно резать материал на прямолинейные и криволинейные полосы.
Упор перемещается в горизонтальном направлении и фиксируется в определенном положении зажимом.
Клепка.
В слесарном деле клепка различается по степени механизации работ. Основные виды клепки — ручная, выполняемая с помощью слесарного молотка, и механизированная, осуществляемая при помощи ручных пневматических молотков, подвесных и стационарных прессов, клепальных машин и др.
Инструмент для ручной клепки. Основным инструментом для выполнения клепальных работ служит слесарный молоток с квадратным бойком, а вспомогательным— поддержка, натяжка и обжимка.
Для получения доброкачественной клепки вес молотка должен соответствовать диаметру стержня заклепки. Так, для заклепок диаметром 2—2,5 мм выбирают молоток весом примерно 150—200 г; для заклепок диаметром 3—3,5 мм — соответственно 200—350 г; для заклепок диаметром 4—5 мм — молоток весом 350— 450 г; диаметром 6—8 мм —молоток весом 450—500 г, а для заклепок диаметром 8—10 мм — молоток весом 800—1000 г.
|
Поддержки являются опорой для закладной головки заклепки во время осадки и отделки замыкающей головки. По конструкции поддержки могут быть самыми разнообразными, они выбираются не только по форме заклепки, но и по весу. Вес поддержки должен быть в 4—5 раз больше веса молотка.
Натяжка служит для уплотнения соединяемых частей перед расклепкой образующей головки. Отверстие на рабочем конце натяжки делают на 0,2 мм большим, чем диаметр стержня заклепки.
Обжимки применяют для придания замыкающей головке заклепки окончательной формы.
Поддержки изготовляют из стали марки 45, а натяжки и обжимки — из инструментальной стали марки У8 с последующей закалкой рабочих концов на длине 13—15 мм.
Ручной механизированный инструмент для клепки.
Механизация клепальных работ сводится в первую очередь к массовому применению пневматических молотков.
В зависимости от назначения пневматические клепальные молотки имеют различные размеры, конструкцию, вес, силу и число ударов. Они предназначены главным образом для заклепок диаметром до 32 мм.
По конструкции клепальные молотки принципиально ничем не отличаются от описанных выше рубильных мо-лоткОв. Однако при клепке требуется большая работа единичного удара при меньшем числе ударов. Рубильные молотки имеют меньшую мощность.
Многоударный пневматический молоток позволяет расклепывать заклепку за 10—30 ударов (в зависимости от мощности применяемого молотка). Непрерывные удары продолжаются до тех пор, пока палец работающего нажимает на пусковой курок рукоятки.
Следует помнить, что клепка пневматическим молотком осуществляется двумя рабочими: один из них производит клепку, а второй является подручным. При применении переносных (подвесных) бугельных молотков Одноударного действия оказывается возможным отказаться от подручного.
Специальные прессы и машины для клепки. Прессовая клепка по сравнению с ударной имеет ряд преимуществ: качество клепки на прессах более высокое; отсутствует шум при работе; производительность труда выше, чем при ручной клепке.
Прессы для клепки подразделяются на ручные, подвесные и стационарные. В массовом производстве применяется автоматизированная клепка, выполняемая машинами-автоматами.
Ручные и подвесные прессы предназначены для склепывания заклепок диаметром до 6—7 мм.
Детали и узлы небольших размеров с небольшим числом заклепок при незначительной длине прямолинейных участков клепают обычно на прессах одиночной клепки. Деталь и.узлы больших размеров с большой протяженностью прямолинейных швов целесообразно клепать на прессах для групповой клепки.
|
Мелкие детали при клепке держат в руках; при клепке больших деталей и узлов применяют различные поддерживающие устройства, например рольганги, монорельсы и др.
Место соединения двух листов или деталей с помощью заклепок называют заклепочным швом.
Заклепки можно располагать вдоль шва в один, два, три и более рядов. В зависимости от этого швы называют однорядными, двухрядными, многорядными. В двухрядных и многорядных швах заклепки могут располагаться параллельными рядами или в шахматном порядке.
По способу соединения листов или деталей между собой различают швы внахлестку и встык.
Шов внахлестку образуется тогда, когда край одного листа накладывается на край другого листа.
Шов встык с одной накладкой получают так. Соединяемые листы своими торцами плотно прижимают друг к другу. На них с одной стороны вдоль стыка накладывают полосу — накладку — и к ней приклепывают каждый из листов. Шов встык с двумя накладками образуется, как и в первом случае, только накладки помещают с обеих сторон склепываемых листов.
Чтобы отверстия заклепочного шва в обеих соединяемых деталях совпадали, необходимо соблюдать следующее правило. Небольшие детали сверлят в собранном виде. При этом их сжимают болтами или струбцинами.
Сравнительно длинные листы при склепывании предварительно соединяют болтами, а заклепки ставят через два-три отверстия. Если требуется склепать детали всего в трех-четырех местах, сначала заклепки ставят в крайние отверстия, а затем в средние.
Пайка.
Пайка - процесс соединения металлов или неметаллических материалов посредством расплавленного присадочного металла, называемого припоем и имеющего температуру плавления ниже температуры плавления основного металла (или неметаллического материала). Процесс пайки применяется либо для получения отдельных деталей, либо для сборки узлов или окончательной сборки приборов. В процессе пайки происходят взаимное растворение и диффузия припоя и основного металла, чем и обеспечиваются прочность, герметичность, электропроводность и теплопроводность паяного соединения. При пайке не происходит расплавления металла спаиваемых деталей, благодаря чему резко снижается степень коробления и окисления металла.
Для получения качественного соединения температура нагрева спаиваемых деталей в зоне шва должна быть на 50-100° С выше температуры плавления припоя. Спаиваемые детали нагревают в печах, в пламени газовой горелки, токами высокой частоты, паяльниками. Прочное соединение припоя (сплавление припоя) с основным металлом можно образовать лишь в том случае, если поверхности спаиваемых деталей свободны от окислов и загрязнений. Для запиты поверхностей спаиваемых деталей от интенсивного окисления в результате нагрева место пайки покрывают флюсом, который образует жидкую и газообразную преграды между поверхностями спаиваемых деталей и окружающим воздухом.
Процесс пайки заключается в следующем: при нагревании припой расплавляется и, соприкасаясь с нагретым, но свободным от окисной пленки основным металлом, смачивает его, и растекается по его поверхности. Способность припоя заполнять швы зависит от степени смачивания припоем основного металла, его капиллярных свойств и шероховатости поверхности спаиваемых деталей.
Пайка мягкими припоями.
При пайке мягкими припоями используют припои с температурами плавления ниже 400˚ С, обеспечивающие получение паяных швов с пределами прочности до 10 кГ/мм2.
Применяют следующие мягкие припои: оловянно-свинцовые, малооловянистые, легкоплавкие и специальные.
Припои оловянно-свинцовые (ПОС), имеющие температуру плавления = 183 ÷ 265˚С, представляют собой сплавы олова и свинца с добавкой 1,5-2,5% сурьмы и обозначаются (ГОСТ 1499-54) ПОС-18, ПОС-30, ПОС-40, ПОС-50, ПОС-61, ПОС-90 (цифра показывает процент содержания олова).
Малооловянистые и безоловянистые мягкие припои: свинцовые (t пл = 327° С), свинцово-серебряные (2,5% серебра, t пл = 304° С) и др.
Легкоплавкие припои (t пл = 60,5 ÷ 145° С) - сплавы олова, свинца, висмута и кадмия. Их применяют в случаях, когда требуется понижение температуры пайки из-за опасности перегрева деталей, а также для «ступенчатых» (вторых) паек. Механическая прочность припоев незначительна, причем висмутовые припои обладают большой хрупкостью.
Специальные припои используют для пайки материалов, не поддающихся качественной пайке стандартными припоями, причем чаще всего их используют Для пайки алюминия. Для пайки алюминия и его сплавов применяют специальные припои на оловянной основе, которые содержат цинк, кадмий и иногда алюминий, а также чистое олово (содержание олова 99,92%), причем лучшими являются оловянно-цинковые, оловянно-кадмиевые и кадмиево-цинковые сплавы (t пл = 197 ÷ 310° С), так как цинк и кадмий (особенно цинк) хорошо диффундируют в алюминии. Мягкие припои поставляются в виде чушек, прутков, проволоки, ленты, а также трубок из оловянно-свинцового сплава, заполненных канифолевым флюсом. Применение трубчатых припоев значительно упрощает процесс паяльных работ и способствует его механизации. При пайке мягкими припоями флюсы, как правило, необходимы.
Пайка твердыми припоями.
При пайке твердыми припоями применяют припои с температурами плавлениявыше 400° С: медные (t пл= 1083° С), медно-цинковые (t пл, = 845 ÷ 900° С), меднофосфористые (t пл = 700 ÷ 830° С), серебряные (t пл = 635 ÷ 870° С) и др.
Твердые припои подразделяются на тугоплавкие с температурой плавления выше 875° С и легкоплавкие с температурой плавления ниже 875° С.
Чистая электролитическая медь (марки М1 и М2) применяется в основном при пайке сталей в печах с защитной средой.
Медноцинковые припои мало распространены вследствие низких механических свойств. В качестве медноцинковых припоев используются также латуни марок Л62 и Л68.
Меднофосфористые припои применяются как заменители серебряных припоев и мягких припоев. Их можно использовать только для пайки медных и латунных деталей, не работающих на изгиб, вибрацию и удар. Пайка меди меднофосфористыми припоями осуществляется без флюса; при пайке сплавов на основе меди флюс необходим.
Меднофосфористые припои нельзя применять для пайки черных металлов, так как они плохо смачивают эти металлы и в пограничных диффузионных слоях образуются хрупкие фосфиды железа.
Наиболее высокое качество получается при твердой пайке с серебряными припоями, которые можно применять для пайки черных и цветных металлов при условии, если температура плавления припоя ниже температуры плавления паяемого металла. При твердой пайке алюминия и его сплавов применяют припои на основе алюминия (t пл = 525 ÷ 580° С).
Припой.
Припой должен хорошо растворять основной металл, обладать смачивающей способностью, быть дешевым и недефицитным. Припои представляют собой сплавы цветных металлов сложного состава. По температуре плавления припои подразделяют на особо легкоплавкие (температура плавления ниже 145 0С), легкоплавкие (145…450 0С), среднеплавкие (450…1100 0С) и тугоплавкие (выше 1050 0С). К особо легкоплавким и легкоплавким припоям относятся оловянно-свинцовые, на основе висмута, индия, олова, цинка, свинца. К среднеплавким и тугоплавким относятся припои медные, медно-цинковые, медно-никелевые, с благородными металлами (серебром, золотом, платиной). Припои изготавливают в виде прутков, листов, проволок, полос, спиралей, дисков, колец, зерен, которые укладывают в место соединения.
Область применения пайки
Применение пайки и склеивания в машиностроении возрастает в связи с широким внедрением новых конструкционных материалов (например, пластмасс) и высокопрочных легированных сталей, многие из которых плохо свариваются. Примерами применения пайки в машиностроении могут служить радиаторы автомобилей и тракторов, камеры сгорания жидкостных реактивных двигателей, лопатки турбин, топливные и масляные трубопроводы и др. В самолетостроении наблюдается тенденция перехода от клепаной алюминиевой.
Подготовка к пайке.
Правильный и рациональный выбор припоя и основного металла, предназначенного для изготовления паяных изделий, возможен в том случае, если известны их основные механические, коррозийные и другие свойства. К припою, кроме всего прочего. иногда предъявляется требование согласования цвета с основным металлом и возможности работы паяного соединения при определенных температурах. При повышенных температурах прочность паяных соединений значительно снижается. При низких температурах (ниже нуля) большинство легкоплавких припоев снижают свою пластичность и ударную вязкость. При температурах ниже -185 град.С лучшими припоями по прочности и пластичности являются свинцовые сплавы с 2,5% серебра и 5% олова и оловянно-свинцовый припой с 25% индия. При пайке разнородных металлов следует учитывать различие в коэффициентах линейного расширения: неправильно выполненная конструкция может привести к разрушению основного металла или паяного соединения во время нагрева или после пайки
Качественное паяное соединение может быть получено только в том случае, если место соединения предварительно очищено от грязи, жира, продуктов коррозии и окисных пленок, которые препятствуют проникновению припоя в шов.
Механическую очистку поверхности изделий от окислов, ржавчины и окалины производят наждачной бумагой, напильниками, металлическими щетками, шлифовальными кругами, стальной и чугунной дробью и др.
Простейшим и весьма эффективным способом обезжиривания в единичном и мелкосерийном производствах паяных изделий является обработка обработка этих изделий венской известью. Тонко размолотую венскую известь разводят водой до кашицеобразного состояния, кистью наносят ее на изделие, затем тщательно протирают изделие и раствор смывают водой.
В условиях массового производства чаще применяют щелочные растворы различного состава. В зависимости от загрязнения температуру растворов поддерживают в пределах 60-90 град.С с продолжительностью обезжиривания 5-30 минут.
Толстые слои смазочных масел с изделия со сложными поверхностями, с внутренними полостями и глубокими отверстиями удаляют при помощи органических растворителей. Органические растворители не могут быть применены для обезжиривания деталей, поверхность которых покрыта влагой, шлифовальной пастой, пылью и неорганическими веществами. В качестве органических растворителей применяют бензин, керосин, ацетон, дихлорэтан, трихлорэтан и другие углеводороды.
В единичном и малосерийном производствах применяют обезжиривание в бензине, керосине и ацетоне. В крупносерийном производстве детали очищают от жира дихлорэтаном и трихлорэтиленом.
Детали обезжиривают несколькими способами: погружением изделия в растворитель, парами растворителя и комбинированным способом. Методом погружения обычно обрабатывают детали тонкого сечения, сильно загрязненные маслом и полированными пастами. В парах растворителя обрабатывают крупногабаритные и малозагрязненные изделия. Еще более совершенным является способ комбинированного обезжиривания в парах, погружением и обрызгиванием.
Окончательное чистовое удаление масел производят методом электрохимического обезжиривания в холодных или горячих щелочных растворах с подключением изделия к источнику постоянного электрического тока.
Имеющиеся на поверхности изделий пленки окислов и других соединений при обезжиривании не удаляются. Наличие этих пленок препятствует образованию прочного соединения припоя с паяемым металлом, поэтому изделия перед пайкой после обезжиривания подвергают травлению. Окалину и окислы с поверхности стали снимают погружением в растворы серной, соляной, фосфорной и других кислот.
Изделия из черных металлов, травленные во фтористоводородной и фосфорной кислотах. имеют более чистую поверхность, чем после травления в серной и соляной кислотах. Для сокращения времени травления и получения чистой поверхности применяют смеси кислот. Травление производят при температурах 20-90 град.С.
Для ускорения процесса очистки применяют электрохимический способ травления, при котором изделие помещают в качестве анода (анодное травление) или катода (катодное травление) в электролитическую ванну.
Анодное травление основано на растворении металла и механическом отрыве окислов выделяющимся кислородом. Катодом при травлении служит обычно свинец, или железо, анодом - изделие. При катодном травлении в качестве анодов применяют свинцовые листы, графит, уголь и олово.
Для предварительной очистки деталей от продуктов коррозии и, окислов и жировых загрязнений применяют комбинированное обезжиривание и травление. С целью антикоррозийной защиты при хранении изделий после химической обработки применяют пассивирование и сушку.
Ультразвуковая обработка резко сокращает процесс очистки деталей от жировых загрязнений. Ее применяют в тех случаях, когда другие способы не обеспечивают нужную чистоту поверхности. В качестве очищающей среды используют органические растворители, щелочные растворы, горячую воду, мыльный раствор и др.
После обработки ультразвуком изделия необходимо промывать в чистой воде, а раствор очищать от примесей.
Термическая, или пламенная очистка состоит в нагреве очищаемой поверхности металла горелкой. Для очистки горелку быстро перемещают по поверхности металла, посторонние вещества при этом сгорают. Мундштуку горелки придают серповидную, угловую и другие формы в зависимости от формы очищаемой поверхности. Скорость перемещения должна быть достаточной, чтобы не допустить коробления поверхности металла; в среднем она равна 3-10 м/ч.
Растворы, применяемые для травления и обезжиривания, не должны загрязняться посторонними веществами, особенно недопустимо перенесение химических реактивов из обезжиривающих ванн в травильные и наоборот. Поэтому после каждой проделанной операции по подготовке поверхности необходима тщательная промывка изделия в воде.
Рабочие приемы пайки.
Классификация пайки носит довольно сложный характер из-за большого числа классифицируемых параметров. Согласно технологической классификации по ГОСТ 17349-79 пайка металлов подразделяется: по способу получения припоя, по характеру заполнения припоем зазора, по типу кристаллизации шва, по способу удаления оксидной пленки, по источнику нагрева, по наличию или отсутствию давления в стыке, по одновременности выполнения соединений.
Одной из основных является классификация пайки по температуре плавления используемого припоя. В зависимости от этого параметра пайку подразделяют на низкотемпературную (используются припои с температурой плавления до 450°C) и высокотемпературную (температура плавления припоев выше 450°C).
Низкотемпературная пайка более экономична и проста в исполнении, чем высокотемпературная. Ее преимуществом является возможность применения на миниатюрных деталях и тонких пленках. Хорошая тепло- и электропроводность припоев, простота выполнения процесса пайки, возможность соединения разнородных материалов обеспечивают низкотемпературной пайке ведущую роль при создании изделий в электронике и микроэлектронике.
К преимуществам высокотемпературной пайки относится возможность изготовления соединений, выдерживающих большую нагрузку, в том числе и ударную, а также получение вакуумно-плотных и герметичных соединений, работающих в условиях высоких давлений. Основными способами нагрева при высокотемпературной пайке, в единичном и мелкосерийном производстве, является нагрев газовыми горелками, индукционными токами средней и высокой частоты.
Композиционная пайка применяется при пайке изделий, имеющих некапиллярные или неравномерные зазоры. Она осуществляется с использованием композиционных припоев, состоящих из наполнителя и легкоплавкой составляющей. Наполнитель имеет температуру плавления выше температуры пайки, поэтому он не расплавляется, а лишь заполняет собой зазоры между паяемыми изделиями, служа средой распространения легкоплавкой составляющей.
По характеру получения припоя различают следующие виды пайки.
Пайка готовым припоем - самый распространенный вид пайки. Готовый припой расплавляется нагревом, заполняет зазор между соединяемыми деталями и удерживается в нем благодаря капиллярным силам. Последние играют очень важную роль в технологии пайки. Они заставляют расплавленный припой проникать в самые узкие щели соединения, обеспечивая его прочность.
Реакционно-флюсовая пайка, характеризующаяся протеканием реакции вытеснения между основным металлом и флюсом, в результате которой образуется припой. Наиболее известная реакция при реакционно-флюсовой пайке: 3ZnCl2 (флюс) + 2Al (соединяемый металл) = 2AlCl3 + Zn (припой).
Чтобы паять металл, кроме подготовленных соответствующим образом паяемых изделий необходимо иметь источник тепла, припой и флюс.
Станочная лаборатория
План лаборатории
Спецификация оборудования станочной лаборатории
1. Токарно-винторезный станок 16К25;
2. Токарно-винторезный станок 1В62Г;
3. Токарно-винторезный станок 16К20;
4. Токарно-винторезный станок 16К20;
5. Токарно-винторезный станок 16К20;
6. Токарно-винторезный станок 1В62Г;
7. Токарно-винторезный станок 1Д95;
8. Токарно-винторезный станок 1М95;
9. Калорифер;
10. Вертикально-сверлильный станок 2Н135;
11. Универсально-фрезерный станок 6Р80Г;
12. Строгальный станок 7Б35;
13. Отрезной ножовочный станок 872М;
14. Горизонтально-фрезерный станок 6Н81Г;
15. Горизонтально-фрезерный станок 6М82;
16. Горизонтально-фрезерный станок 6Н83;
17. Вертикально-фрезерный станок с кнопочной станцией 6А62П;
18. Вертикально-фрезерный станок 6В11;
19. Круглошлифовальный станок 312М;
20. Плоскошлифовальный станок 3Г71;
21. Заточной станок;
22. Силовой щит для питания станков 1…9 (рубильник № 4);
23. Силовой щит для питания станков 10,11,12, и 21, и слесарной лаборатории (рубильник № 5);
24. Силовой щит для питания станков 13…20 (рубильник № 6);
Работа на токарных станках.
Глубиной резания называется толщина слоя металла, снимаемого за один проход резца. Она обозначается буквой t и колеблется от 0,5 до 3 и больше миллиметров при черновой обработке до десятых долей миллиметра при чистовой обточке.
Подача —это движение резца вдоль обрабатываемой поверхности. Численно она выражается в миллиметрах, обозначается буквой S и указывает на величину смещения резца за один оборот детали. В зависимости от прочности обрабатываемого материала, жесткости узлов станка и резца, величина подачи может меняться от 0,1—0,15 мм/об до 2—3 мм/об при скоростных режимах резания. Чем тверже металл, тем меньше должна быть подача.
Скорость резания зависит от числа оборотов шпинделя и диаметра детали и подсчитывается по формуле.
Выбирая ту или иную скорость резания, нужно учитывать твердость обрабатываемого материала и стойкость резца, которая измеряется временем непрерывной работы его до затупления в минутах. Она зависит от формы резца, его размеров, материала, из которого изготовлен резец, от точения с охлаждающей эмульсией или без нее.
Наибольшую стойкость имеют резцы с пластинками из твердых сплавов, наименьшую — резцы из углеродистой стали.
Вот, например, какие скорости резания можно рекомендовать при точении различных материалов резцом из быстрорежущей стали. Стойкость его без охлаждения равна 60 минутам.
Примерные данные о скорости резания металлов:
Материал | Скорость резания в м/мин. |
Серый чугун | 25 |
Твердая сталь | 25 |
Мягкая сталь | 50 |
Бронза | 75 |
Латунь | 100 |
Алюминий | 250 |
|
|
Двойное оплодотворение у цветковых растений: Оплодотворение - это процесс слияния мужской и женской половых клеток с образованием зиготы...
Семя – орган полового размножения и расселения растений: наружи у семян имеется плотный покров – кожура...
Типы оградительных сооружений в морском порту: По расположению оградительных сооружений в плане различают волноломы, обе оконечности...
Архитектура электронного правительства: Единая архитектура – это методологический подход при создании системы управления государства, который строится...
© cyberpedia.su 2017-2024 - Не является автором материалов. Исключительное право сохранено за автором текста.
Если вы не хотите, чтобы данный материал был у нас на сайте, перейдите по ссылке: Нарушение авторских прав. Мы поможем в написании вашей работы!