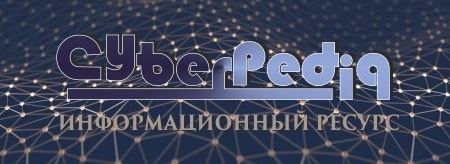
Наброски и зарисовки растений, плодов, цветов: Освоить конструктивное построение структуры дерева через зарисовки отдельных деревьев, группы деревьев...
Организация стока поверхностных вод: Наибольшее количество влаги на земном шаре испаряется с поверхности морей и океанов (88‰)...
Топ:
Отражение на счетах бухгалтерского учета процесса приобретения: Процесс заготовления представляет систему экономических событий, включающих приобретение организацией у поставщиков сырья...
Организация стока поверхностных вод: Наибольшее количество влаги на земном шаре испаряется с поверхности морей и океанов...
Характеристика АТП и сварочно-жестяницкого участка: Транспорт в настоящее время является одной из важнейших отраслей народного...
Интересное:
Наиболее распространенные виды рака: Раковая опухоль — это самостоятельное новообразование, которое может возникнуть и от повышенного давления...
Как мы говорим и как мы слушаем: общение можно сравнить с огромным зонтиком, под которым скрыто все...
Отражение на счетах бухгалтерского учета процесса приобретения: Процесс заготовления представляет систему экономических событий, включающих приобретение организацией у поставщиков сырья...
Дисциплины:
![]() |
![]() |
5.00
из
|
Заказать работу |
|
|
Производительность скипового подъемника в связи с неравномерностью загрузки во времени и в связи с возможным увеличением производительности доменной печи рассчитывают с запасом - так, чтобы коэффициент загруженности подъемника не превышал 60...75% [3,4]. Расчетный коэффициент загруженности Кр, подъемника выражают в виде отношения потребного для печи с заданной производительностью числа подачи (Zр) к теоретически возможному числу подач (Zt) при непрерывной работе подъемника:
Кр = 100 (Zр / Zt) (2.7)
Кр = 100 (146,84/419,4) = 35.
Теоретически возможную производительность скипового подъемника (возможное число подач) определяют из соотношения:
Z1 = 24 · 60 · 60/ t (2.8)
где t - время подъема одной подачи, выраженное в секундах.
Z1 = 24 · 60 · 60/206 = 419,4 подач в сутки,
t = пк (tп + tк) + пж (tп + tж) (2.9)
где tп - время подъема скипа на колошник, с;
tк и tж - время остановок скипа при загрузке соответственно кокса и железосодержащей части шихты в скип, с;
пк и пж - соответственно число скипов кокса и железосодержащих материалов в подаче.
t = 2 (38 + 12) + 2 (38+15) = 206 с
Время подъема скипа составляет 35…50с и в каждом конкретном случае определяется путем построения графика движения, учитывающего длину подъемника, скорость движения, время разгона в начале пути и торможения в конце; время стоянки скипа при загрузке кокса составляет 12...15 с, при загрузке железосодержащей части шихты 15...20 с.
Потребное или необходимое число подач (Zр) определяют по заданной суточной производительности доменной печи (Пс, т/сут). При этом с учетом величины удельного расхода кокса и железосодержащей шихты на 1т чугуна суточный расход кокса Qк составит (0,35...0,50) Пс5333,3т/сут, (0,35-0,5)5333,3=1866т/сут, а суточный расход железосодержащей шихты – Qж (1,75- 2,1) Пс 5333,3т/сут = 9333
|
Необходимое число подач по коксу составит:
Zр = Qк / (Рк пк) (2.10)
где Рк - масса кокса в скипе, т.
Zр = 1866/(5,05 · 2) = 185
Аналогичным образом определяют необходимое число подач по железосодержащей части шихты и для расчета коэффициента загруженности подъемника Кр берут большую величину. Масса материала в скипе:
Р = Vск qk, т (2.11)
где Vск - объем скипа, м3;
q- насыпная масса материала, т/м3;
k - коэффициент заполнения скипа (0,85).
Насыпная масса кокса составляет около 0,45; агломерата 1,9; окатышей 1,9т/м3. Требуемая производительность скипового подъемника обычно достигается при объеме скипа Vск, близком к 0,0065 Vп, где Vп - полезный объем печи.
Рк = 20,8 · 0,45 · 0,85 = 7,956 т.
Производительность вагон - весов зависит от их грузоподъемности и организации совместной работы по скиповым подъемникам. Средняя часовая производительность вагона:
Пч = 3600Рk/t, (т/ч) (2.12)
где Р - грузоподъемность вагон весов, т
k - коэффициент заполнения карманов (0,9);
t - длительность цикла работы вагон-весов (с), включающая время набора материалов из бункеров их разгрузки в скип, передвижения от скиповой ямы к соответствующим бункерам и обратно и время простоя в ожидании скипов.
Величину t определяют путем построения графика совместной работы вагон-весов и скипового подъемника. Длительность определяемого таким образом цикла достигает 250 с, хотя длительность собственно доставки очередной порции материалов вагоном не превышает 1 мин.
|
Пч = 3600 · 40 · 0,9/250 =518,4 ч.
Емкость бункеров для руды из расчета 2,5 м3 на 1 м3 объема печи - 6750м3; для кокса из расчёта 0,7 м3 на 1м3 объема печи – 1890 м3.
Производительность вагоноопрокидывателя (П, вагонов в сутки):
П = (1440 - tп)/ tр, (2.13)
где tр - задолженность вагоноопрокидывателя на разгрузку одного вагона, мин;
tп - время простоев в сутки, мин.
Задолженность башенного или роторного вагоноопракидывателя на разгрузку одного вагона (подача вагона на люльку или ротор, опрокидывание вагона и его выдача) составляет 2...3 мин. Обычно вагоноопракидыватель занят разгрузкой 35...40% рабочего времени и разгружает около 70 вагонов за смену; в отдельных случаях занятость разгрузкой достигает 80% рабочего времени и количество разгружаемых вагонов достигает 170.
П = (1440 - 1152)/ 2 = 144 вагона
Число чугуновозных ковшей. Необходимое в доменном цехе количество (п) открытых грушевидных чугуновозных ковшей (парк ковшей) определяют по формуле:
п = поб + прем, + През, (2.14)
где поб, прем, през - число ковшей, находящихся в обороте, ремонте и резерве соответственно.
Число ковшей, находящихся в обороте, равно
nоб = П · пП · tоб · k /(24 · Р · 0,8) (2.15)
где П - суточная производительность печи, т/сут;
пП - число печей в цехе, шт;
tоб - длительность цикла оборота ковша (5...7 ч);
k - коэффициент неравномерности выпусков чугуна (1,25);
Р- номинальная емкость ковша, 300 т;
0,8 - коэффициент заполнения ковша чугуном.
поб = 5333,3 · 2 · 6 ·1,25/(24 · 300 · 0,8) = 14 ковшей.
Число ковшей, одновременно находящихся в ремонте:
прем = поб (tх.р. + п’ tг.р)/ т tоб, (2.16)
где tх.р. и tг.р - продолжительность холодного и горячего ремонтов соответственно, ч;
т - стойкость футеровки (число наливов) между холодными ремонтами, шт;
п’ - число горячих ремонтов, проводимых за одну кампанию между холодными ремонтами, шт.
Стойкость футеровки между холодными (капитальными) и горячими ремонтами составляет соответственно 350 и 115- 120 наливов.
|
Продолжительность ремонтов - около 100 и 8 ч.
прем = 14· (100 + 2 · 8) /120 · 6 = 2 ковша.
Число резервных ковшей:
през = (2.17)
где Пmах - максимальная производительность печи, т/сут;
к - число выпусков чугуна в сутки на печи с максимальной производительностью.
Примерное число выпусков чугуна (т) в сутки на печах с одной леткой составляет 8...10, при двух летках 10...14; при трех-четырех летках 15...20.
през = = 2 ковша
п = 13 + 2 + 2= 18 ковшей.
Число разливочных машин рассчитывают исходя из необходимости обеспечить разливку чугуна при его минимальном потреблении сталеплавильными цехами, то есть при остановках на ремонт конвертеров. Если разницу между суточной выплавкой чугуна и его потреблением сталеплавильным цехом обозначить Qс (т/сут), а суточную производительность одной машины Пс (т/сут), то потребное число машин составит п = Qс / Пс.
Суточная производительность одной машины при условии бесперебойной подачи ковшей равна:
Пс = 0,995(Р · tС / tЦ), т/сут (2.18)
где Р - масса чугуна в ковше, т;
tЦ - продолжительность цикла разливки одного ковша, ч;
0,995 - коэффициент учета потерь чугуна при разливке;
tС - время работы машины в сутки (его принимают равным 20ч, остальное время затрачивается на ремонт желоба и эксплуатационные нужды самой машины).
Пс = 0,995(300 · 20/0,26) = 22916,5 т/сутки.
Продолжительность цикла разливки одного ковша складывается из времени t1 разливки и времени t2 между двумя разливками, затрачиваемого на захват и подъем ковша, обратный поворот порожнего ковша, замену ковша; величину t2 принимают равной 10...15 мин, или 0,17...0,25 ч.
Продолжительность разливки одного ковша равна:
t1 = 60 · Р · 1/ (· q · v), ч (2.19)
где пл - число лент;
l - расстояние между изложницами (~ 0,3 м);
q - масса чушки, т;
v - скорость движения ленты, м/мин.
Изложницы выполняют одноместными для получения чушек массой 45 кг или двухместными для получения двух чушек массой по 23 или 18 кг. Скорость движение ленты разливочных машин составляет 9,1...13,8 м/мин.
|
t1 = 60 · 300 · 0,3 / (2 · 45 · 13) = 4,6I5 мин.
tц = t1 + t2 = 0,07 + 0,19 = 0,26 ч.
Qс = 4570 т/сут. п = 4570/22916,5 = 0,2
Число шлаковозов при ковшевой уборке шлака в доменном цехе определяют по формуле:
п = поб + прем+ през, шт (2.20)
где - поб, прем, през - число шлаковозов, находящихся соответственно в обороте, в ремонте и резервных.
Число шлаковозов, находящихся в обороте равно:
поб = , шт (2.21)
где Q – суточный выход шлака с одной печи, т/сут;
пП – число печей в цехе, шт.;
κ – коэффициент неравномерности выпусков шлака (1,25);
tОБ – продолжительность цикла оборота ковша, ч;
V – объем шлакового ковша (11 или 16,5м3);
d – плотность жидкого шлака (около 1,6 т/м3 );
0,8 – коэффициент заполнения ковша;
βВ и βН – доля верхнего и нижнего шлака соответственно.
Из общего количества шлака доля верхнего составляет 0,5…0,45, доля нижнего 0,5…0,55; время оборота ковшей с верхним и нижним шлаком в расчетах принимают близким к 5 ч.
поб = = 50/10 = 5 ковшей
Число шлаковозов, одновременно находящихся в ремонте:
прем = поб (tр / t), шт (2.22)
где tр - продолжительность капитальных, средних и текущих ремонтов шлаковозов за кампанию, сут;
t - продолжительность кампании ковша между капитальными ремонтами, сут.
Продолжительность компании между капитальными ремонтами принимают равной шести годам. За это время проводят два средних и шесть текущих ремонтов. Продолжительность капитального, среднего и текущего ремонтов составляет соответственно 3; 2,5 и 1 сут.
t = 365 · 6 = 2190 сут.
tр = 3 + 5 + 6 = 14 сут.
прем = 4,4 · (14/2190) = 0,028 ковша.
Число резервных шлаковозов в соответствии с существующими нормами рассчитывают следующим образом:
през = , шт (2.23)
где тВ и тн - число выпусков верхнего и нижнего шлака соответственно.
Расчетное число выпусков верхнего шлака на печах с одной чугунной леткой составляет 16...20, на печах с двумя чугунными летками 20...24. Число выпусков нижнего шлака равно числу выпусков чугуна, данные о которых приведены при расчете количества чугуновозов [3,4].
през = = 6 ковшей.
п = 5 + 1 + 6 = 12 ковшей.
2.2 Технологическая часть
|
|
Архитектура электронного правительства: Единая архитектура – это методологический подход при создании системы управления государства, который строится...
Эмиссия газов от очистных сооружений канализации: В последние годы внимание мирового сообщества сосредоточено на экологических проблемах...
Опора деревянной одностоечной и способы укрепление угловых опор: Опоры ВЛ - конструкции, предназначенные для поддерживания проводов на необходимой высоте над землей, водой...
Поперечные профили набережных и береговой полосы: На городских территориях берегоукрепление проектируют с учетом технических и экономических требований, но особое значение придают эстетическим...
© cyberpedia.su 2017-2024 - Не является автором материалов. Исключительное право сохранено за автором текста.
Если вы не хотите, чтобы данный материал был у нас на сайте, перейдите по ссылке: Нарушение авторских прав. Мы поможем в написании вашей работы!