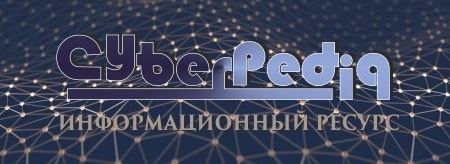
История развития хранилищ для нефти: Первые склады нефти появились в XVII веке. Они представляли собой землянные ямы-амбара глубиной 4…5 м...
История развития пистолетов-пулеметов: Предпосылкой для возникновения пистолетов-пулеметов послужила давняя тенденция тяготения винтовок...
Топ:
Оценка эффективности инструментов коммуникационной политики: Внешние коммуникации - обмен информацией между организацией и её внешней средой...
Генеалогическое древо Султанов Османской империи: Османские правители, вначале, будучи еще бейлербеями Анатолии, женились на дочерях византийских императоров...
Отражение на счетах бухгалтерского учета процесса приобретения: Процесс заготовления представляет систему экономических событий, включающих приобретение организацией у поставщиков сырья...
Интересное:
Мероприятия для защиты от морозного пучения грунтов: Инженерная защита от морозного (криогенного) пучения грунтов необходима для легких малоэтажных зданий и других сооружений...
Влияние предпринимательской среды на эффективное функционирование предприятия: Предпринимательская среда – это совокупность внешних и внутренних факторов, оказывающих влияние на функционирование фирмы...
Аура как энергетическое поле: многослойную ауру человека можно представить себе подобным...
Дисциплины:
![]() |
![]() |
5.00
из
|
Заказать работу |
Химико-термическая обработка. Цементация и азотирование. Термическая обработка после цементации.
ХТО - это процесс изменения химического состава, структуры и свойств поверхности стальных деталей за счет насыщения ее различными химическими элементами. При этом достигается значительное повышение твердости и износостойкости поверхности деталей при сохранении вязкой сердцевины.
Процесс ХТО складывается из 3–х составных:
1.диссоциация - распад молекул газа с образованием активных атомов насыщенного элемента;
2.абсорция - поглощение атомов насыщенного элемента поверхностью детали;
3.Диффузия атомов насыщенного элемента в глубь металла.
Цементация-процесс насыщения поверхности изделия углеродом. Цементация повышает тверость и износостойкость поверхности детали при сохранении вязкости сердцевины. Цементация производится путем нагрева стальных деталей при 880…950 °С в углеродосодержащей среде, называемой карбюризатором.
Цементация:
-твердая-проводится в стальных ящиках, куда укладываются детали вперемешку с карбюризатором. Карбюризатором служит порошок древесного угля с добавкой солей Na2СО3 или ВаСО3.
-газовая (более эффективная)проводится в газе, содержащем метан СН4 и оксид углеродаСО.
Маленькая твердость после ХТО легированных сталей обусловлена повышенным содержанием в структуре аустенита остаточного, для утранения которого после закалки, иногда проводят обработку холодом.
Для цементироания применяют стали с низким содержанием углерода 0.15–0.25%.
Азотирование – насыщение поверх азотом. При этом повышаются не только твердость и износостойкость, но и коррозионная стойкость. Проводится азотирование при температуре 500…600 °С в среде аммиака NН3 в течение длительного времени (до 60 ч.) Азотированию подвергают только легированные стали.
Химико-термическая обработка. Нитроцементация и цианирование. Диффузионная металлизация.
ХТО - это процесс изменения химического состава, структуры и свойств поверхности стальных деталей за счет насыщения ее различными химическими элементами. При этом достигается значительное повышение твердости и износостойкости поверхности деталей при сохранении вязкой сердцевины.
Процесс ХТО складывается из 3–х составных:
1.диссоциация - распад молекул газа с образованием активных атомов насыщенного элемента;
2.абсорция - поглощение атомов насыщенного элемента поверхностью детали;
3.Диффузия атомов насыщенного элемента в глубь металла.
Нитроцементация – процесс одновременного насыщения углеродом и азотом. Этот процесс проводиться при t 840-860. t-ра более низкая в газовой среде, состоящей из науглероживающего газа и аммиака. В этой среде процесс насыщения углерода идет более интенсивно. Продолжит процесса от 4 до 10 часов. Последующая закалка может осущ-ся прямо из печи с небольшим подстуживанием.
Цианирование – это процесс насыщения углеродом и азотом в следствии окисления расплавленных цианистых солей. t-ра 820-960, в расплавлен солях содержащих цианистый натрий. Для получения слоя небольшой толщины от 0,15-0,3 мм цианирование производят при t 820-860 в течении 30-90 мин. Поледующ закалку и низкий отпуск проводят сразу после цианирования. Для получения большего слоя от 0,5-2мм, t цианирования составляет 930-960. время выдержки от 1,5-6 часов. При этих T сталь в больших степенях насыщается углеродом до 0,8-2%. После такого режима деталь охлаждается на воздухе а затем под закалку нагревают в соленых ваннах, после чего подвергаются низкому отпуску.
Диффузионная металлизация. Целью д м является насыщение поверхностных слоев стали различными элементами с целью повышения коррозионной стойкости, повышения твердости, усталостной прочности. Насыщение производят хромом. Процесс наз-ся хромированием, кремнием – сицилированием, Al – алиторованием, бором – борированием, при борировании резко повышается твердость поверх-х слоев, их износостойкость.
Термическая обработка.
Термической обработкой называется совокупность операций нагрева, выдержки и охлаждения твердых металлических сплавов с целью получения заданных свойств за счет изменения внутреннего строения и структуры. Различают следующие виды термической обработки: отжиг, закалка и отпуск.
ОТЖИГ I РОДА Отжиг I рода в зависимости or исходного состояния стали и температуры ею выполнения может включать процессы: гомогенизации, рекристаллизации, снижения твердости, нятия остаточных напряжений.
Особенность: отжиг 1 рода можно проводить при температурах выше или ниже температур фазовых превращений. Этот вид обработки в зависимости от температурных условий его выполнения устраняет химическую или физическую неоднородность, созданную предшествующими обработками.
ОТЖИГ II РОДА (ФАЗОВАЯ ПЕРЕКРИСТАЛЛИЗАЦИЯ) Отжиг II рода заключается в нагреве стали до температур выше точек Ас1 или Ac3, выдержке и, как правило, последующем медленном охлаждении. В процессе нагрева и охлаждения в этом случае протекают фазовые превращения (? - а-превращение), определяющие структуру и свойства стали. Понижая прочность и твердость, отжиг облегчает обработку, резание средне- и высокоуглеродистой стали. Измельчая зерно снимая внутренние напряжения Различают следующие виды отжига: - полный, -изотермический - неполный.
3. ЗАКАЛКА Закалка — термическая обработка — заключается в нагреве стали до температуры выше критической (А3 для доэвтектоидной и а1—для заэвтектоидной сталей) или температуры растворения избыточных фаз, в выдержке и последующем охлаждении со скоростью, превышающей критическую. Закалка не является окончательной операцией термической обработки. Чтобы уменьшить хрупкость и напряжения, вызванные закалкой, и получить требуемые механические свойства, сталь после закалки обязательно подвергают отпуску. Инструментальную сталь в основном подвергают закалке и отпуску для повышения твердости, износостойкости и прочности, а конструкционную сталь — для повышения прочности, твердости, получения достаточно высокой пластичности и вязкости, а для ряда деталей также высокой износостойкости. Бывает:
- Непрерывная,
- Прерывистая,
- Закалка с самоотпуском,
- Ступенчатая закалка,
-Изотермическая,
-обработка стали холодом.
Углеродистые стали.
Сплавы железа с углеродом с содержанием углерода до 2,14% называют сталями. Помимо углерода в углеродистые стали при выплавке попадают посторонние примеси: обусловленные тезнологическими процессами (Mn, Si), невозможностью их удаления при плавке (P, S), случайными обстоятельствами (Ni, Cu). Если перечисленные элементы входят в больших количествах, чем предусмотренные ГОСТом на углеродистые стали, эти стали считают легирующими.
Углеродистые конструкционные стали подразделяются на стали:
- обыкновенного качества
Буквы «Ст» в марке стали обозначают «сталь»,
цифры — условный номер марки (с увеличением номера возрастает в стали содержание углерода.
В зависимости от условий и степени раскисления различают стали:
1) спокойные «сп» Ст1сп)
2) полуспокойные «ПС» (Стпc);
3) кипящие «кп» (Сткп).
В их составе разное массовое содержание кремния и кислорода:
в спокойных 0,15—0,3 % Si и —0,002 % О2;
в полуспокойных 0,05—0,15 % Si и —0,01 % 02 и
в кипящих — не более 0,05 % Si и ~0,02 % О2.
Спокойные стали получают полным раскислением стали ферромарганцем, ферросилициумом, алюминием в печи, а затем в ковше. Они застывают спокойно без газовыделения.
Кипящие стали раскисляют только ферромарганцем и до затвердевания в них содержится повышенное количество FeO. При застывании в изложнице FeO взаимодействует с углеродом стали, образуя СО, который выделяется в виде пузырьков, создавая впечатление, что металл кипит.
Стали обыкновенного качества, особенно кипящие, наиболее дешевые. В процессе выплавки они меньше очищаются от вредных примесей. Массовая доля серы должна быть не более 0,05 %, фосфора — не более 0,04 % и азота — не более 0,008 %. Стали отливают в крупные слитки, вследствие чего в них раз-вита ликвация и они содержат сравнительно большое количество неметаллических включений.
С повышением условного номера марки стали возрастает пре дел прочности и текучести и снижается пластичность. Из сталей обыкновенного качества изготовляют горячекатаный рядовой прокат: балки, швеллеры, уголки, прутки, а также листы, трубы и поковки. Стали в состоянии поставки широко применяют в строительстве для сварных, клепаных и болтовых конструкций, реже для изготовления малонагруженных деталей машин (валы, оси, зубчатые колеса и т. д.).
Кипящие стали (Ст1кп), содержащие повышенное количество кислорода, имеют порог хладноломкости на 30— 40 °С выше, чем стали спокойные (Ст1сп). Поэтому для ответственных сварных конструкций, а также работающих при низких климатических температурах применяют спокойные, стали (Ст1сп, Ст2сп, СтЗсп). С повышением содержания в стали углерода свариваемость ухудшается. Поэтому стали Ст5 и Ст6 с более высоким содержанием углерода применяют для элементов строительных конструкций, не подвергаемых сварке. Стали, предназначенные для сварных конструкций, должны обладать малой чувствительностью к термическому старению, а стали, подвергаемые холодной правке и гибке, — малой склонностью к деформационному старению. Стали обыкновенного качества нередко имеют специализированное назначение (моего- и судостроение, сельскохозяйственное машиностроение и т. д.) и поступают по особым техническим условиям. Низкоуглеродистые стали СтЗ, Ст4 и другие обладают малой устойчивостью переохлажденного аустенита ' (высокой критической скоростью закалки)» поэтому после закалки мартенсит не образуется. Качественные углеродистые стали. Эти стали (ГОСТ 1050—74). Качественные углеродистые стали маркируют цифрами 08, 10, 15, 20,..., 85, которые указывают среднее содержание углерода в сотых долях процента.
Низкоуглеродистые стали (содержание углерода <0,25 %) 05кп, 08, 07кп, 10, 10кп обладают невысокой прочностью и высокой пластичностью. sв = 330-340 МПа, s0,2= 200-210 МПа и? = ЗЗ-31 %. Эти стали без термической обработки применяют для малонагруженных деталей. Тонколистовую холоднокатаную низкоуглеродистую сталь используют для холодной штамповки изделий. Стали 15, 15кп, 20, 25 чаще применяют без термической обработки или в нормализованном состоянии. Низкоуглеродистые качественные стали используют и для ответственных сварных конструкций, а также для деталей машин, упрочняемых цементацией. Среднеуглеродистые стали (0,3—0,5 % С) 30, 35, 40, 45, 50, 55 применяют после нормализации, улучшения и поверхностной закалки для самых разнообразных деталей во всех отраслях машиностроения. Эти стали в нормализованном состоянии по сравнению с низкоуглеродистыми имеют более высокую прочность при более низкой пластичности (sв = 500-5-610 МПа, s0,2= 300-360 МПа,? = 21 -16 %). Стали в отожженном состоянии хорошо обрабатываются резанием. Наиболее легко обрабатываются доэвтектоидные стали со структурой пластинчатого перлита. Прокаливаемость сталей невелика; критический диаметр после закалки в воде не превышает 10—12 мм (95 % мартенсита). В связи с этим их следует применять для изготовления небольших деталей или более крупных, но не требующих сквозной прокаливаемости. Для повышения прокаливаемости стали добавочно легируют марганцем (40Г, 50Г).
Стали с высоким содержанием углерода (0,6—0,85 % С) 60, 65, 70, 80 и 85 обладают повышенной прочностью, износостойкостью и упругими свойствами; применяют их после закалки и отпуска, нормализации и отпуска и поверхностной закалки для-j деталей, работающих в условиях трения при наличии высоких! статических вибрационных нагрузок. Из этих сталей изготовляют пружины и рессоры, шпиндели, замковые шайбы, прокатные, валки и т. д.
31. Основы легирования стали. Взаимодействие легирующих элементов с железом и углеродом. Влияние легирующих элементов на устойчивость аустенита и феррита.
Легирующие элементы вводятся в сталь для получения требуемой структуры и свойств. Почти все элементы растворяются в железе и влияют на положение точек А3 и А4.По влиянию делятся на 2 группы:
Сплавы наз аустенитными, если при всех температурах твердый раствор легирующего элемента в?-железе и не испытывают фазовых превращений. Частично претерпевающие превращение – полуастенитные. 2)понижают А4 и повышают А3. Интервалы точек А1 и А3 сливаются, область?-фазы полностью замыкается. Сплавы, сост из твердово легирующего элемента в?-железе, наз ферритными. Все легир. эл-ты упрочняют сталь. Часто наряду с повыш. прочности, повыш. пластичность, наприм. легир. Ni. Легир. эл-ты измен. кинетику распада А, сниж. скорость диффузии при всех тем-рах стали, поэтому увелич. устойчивость А. С-образные кривые смещаются вправо, тем самым сниж. критич. скорость закалки. Это улучш. закаливаемость и прокаливаемость стали, так действуют все легир. эл-ты, кроме кобальта.
В сталях в кот. содерж. легир. эл-тов
<2,5% наз. низколегир.;
2,5-10% - легир.;
>10% - высоколегир.
Особенности поведения металлов и сплавов при высоких температурах. Жаростойкость и жаропрочность. Критерии жаропрочности. Состав, назначение, термическая обработка жаропрочных сплавов на никелевой основе.
Жаропрочность – способность противостоять агрессивной среде при высоких температурах. Если среда действительно газовая, то проблема сводится к окалености. Газы в зависимости от температуры ведут ся по разному. Азот нейтрален при комнатной температуре, а при 1100град очень агрессивен. Fe окисляется и образуется плотная пленка, которая предохраняет от дальнейшего окисления. Она устойчива до 500град. При 570град окись железа Fe3O4 превращается в FeO (дюстит), который растворяет в себе и O и Fe. При повышении температуры вся сталь может превратится в окаленную и ее нужно защищать легированием Al,Ti,Si,Cr. При длительной работе при нагрузке меньше предела текучести и температуре 0,4-0,5 от температуры плавления металл испытывает медленную пластическую деформацию, которая называется ползучестью. Напряжение, которое вызывается разрушением металла при высоких температурах, сильно зависит от продолжительности приложения нагрузки. Оно может быть большим при кратковременном приложении нагрузки и значительно меньшим при длительном приложении нагрузки. При работе металла при высоких температурах возникает жаропрочность. Основной критерий – предел прочности (который приводит к разрушению металла при заданной температуре за время) и предел ползучести (вызываемый деформацией за опред время при опред температуре). Ползучесть вызывает ослабляет напряжение в предварительно нагруженных деталях. Большенство жаропрочных металлов поликристаллические. Крупнозернистые металлы легируют таким образом, что по границам зерен выделяются упрочнительные фазы. Монокристаллические металлы очень дорогие. В зависимости от температуры применяются различные сплавы.
Жаропрочные сплавы на основе никеля, как правило, обладают сложным химсоставом. Термическая обработка. Деформируемые никелевые жаропрочные сплавы содержат в матрице дисперсные выделения карбидов типа MC. Гомогенизационный отжиг даёт возможность подготовить матрицу к получению равномерного распределения частиц упрочняющей фазы ' в процессе последующего старения После гомогенизационного отжига важно выдержать скорость охлаждения, чтобы препятствовать выделению нежелательных фаз. Охлаждение между этапами старения проводится плавно в течение 2 часов.
Титан и его сплавы.
Титан – металл серого цвета. Температура плавления 1668град.
Технический титан изготовляют 2х марок ВТ1-00 (99,53%), ВТ1-0 (99,46%). На поверхности легко образуется оксидная пленка, повышающая сопротивление коррозии в некоторых агрессивных средах. Его обрабатывают давлением. Сплавы имеют большее применение, чем титан. Легирование титана Fe,Al, Mn, Cr, V, Si повышает его прочность, но снижает пластичность и вязкость. Жаропрочность повышают Al Mo Zr. Титановые сплавы имеют высокую удельную прочность. Al N O повышают температуру полиморфного превращения и расширяют область?-фазы. Mo V Mn Fe Cr понижают эту температуру и расширяют область?-фазы:?>?+ТхМу. При охлаждении?-фаза претерпевает эфтектоидное превращение. Как правило все промышленные сплавы титана содержат алюминий. Могут иметь нейтральные элементы (Sn Zr).
Титановые сплавы применяются в авиации, ракетной технике, в химическом машиностроении и др. ВТ5 хорошо обрабатывается давлением и сваривается. ВТ6 обладает хорошими механическими и технологическими свойствами и упрочняется термической обработкой. Термическая обработка титановых сплавов.
В зависимости от состава и назначения можно подвергать отжигу, закалке, старению и химико-термической обработке.
Чаще подвергают отжигу. Нагрев до 870-980град и далее выдержка при 530-660град. Широко применяется вакуумный отжиг, который позволяет уменьшить содержание водорода в титановых сплавах, что приводит к уменьшению склонности к замедленному разрушению и коррозийному растрескиванию. Для снятия небольших внутренних напряжений применяют неполный отжиг при 550-650 град. Титановые сплавы имеют низкое сопротивление износу и при использовании в узлах трения подвергаются химико-термической обработке. Для повышения износостойкости титан азотируют при 850-950 град в течение 30-60 часов в атмосфере азота (слой 0,05-0,15 мм).. ВТ5 хорошо обрабатывается давлением и сваривается. ВТ6 обладает хорошими механическими и технологическими свойствами и упрочняется термической обработкой. ВТ14 применяют для изготовления тяжелонагруженых деталей. Сплав упрочняется закалкой при 850-880град в воде с последующим старением при 480-500град 12-16 часов. ВТ8 применяют после изотермического отжига. Для фасонного литья применяют сплавы ВТ5Л, ВТ6Л, ВТ14Л, которые обладают достаточно хорошими литейными и механическими свойствами.
Химико-термическая обработка. Цементация и азотирование. Термическая обработка после цементации.
ХТО - это процесс изменения химического состава, структуры и свойств поверхности стальных деталей за счет насыщения ее различными химическими элементами. При этом достигается значительное повышение твердости и износостойкости поверхности деталей при сохранении вязкой сердцевины.
Процесс ХТО складывается из 3–х составных:
1.диссоциация - распад молекул газа с образованием активных атомов насыщенного элемента;
2.абсорция - поглощение атомов насыщенного элемента поверхностью детали;
3.Диффузия атомов насыщенного элемента в глубь металла.
Цементация-процесс насыщения поверхности изделия углеродом. Цементация повышает тверость и износостойкость поверхности детали при сохранении вязкости сердцевины. Цементация производится путем нагрева стальных деталей при 880…950 °С в углеродосодержащей среде, называемой карбюризатором.
Цементация:
-твердая-проводится в стальных ящиках, куда укладываются детали вперемешку с карбюризатором. Карбюризатором служит порошок древесного угля с добавкой солей Na2СО3 или ВаСО3.
-газовая (более эффективная)проводится в газе, содержащем метан СН4 и оксид углеродаСО.
Маленькая твердость после ХТО легированных сталей обусловлена повышенным содержанием в структуре аустенита остаточного, для утранения которого после закалки, иногда проводят обработку холодом.
Для цементироания применяют стали с низким содержанием углерода 0.15–0.25%.
Азотирование – насыщение поверх азотом. При этом повышаются не только твердость и износостойкость, но и коррозионная стойкость. Проводится азотирование при температуре 500…600 °С в среде аммиака NН3 в течение длительного времени (до 60 ч.) Азотированию подвергают только легированные стали.
Индивидуальные и групповые автопоилки: для животных. Схемы и конструкции...
Автоматическое растормаживание колес: Тормозные устройства колес предназначены для уменьшения длины пробега и улучшения маневрирования ВС при...
Архитектура электронного правительства: Единая архитектура – это методологический подход при создании системы управления государства, который строится...
История развития пистолетов-пулеметов: Предпосылкой для возникновения пистолетов-пулеметов послужила давняя тенденция тяготения винтовок...
© cyberpedia.su 2017-2024 - Не является автором материалов. Исключительное право сохранено за автором текста.
Если вы не хотите, чтобы данный материал был у нас на сайте, перейдите по ссылке: Нарушение авторских прав. Мы поможем в написании вашей работы!