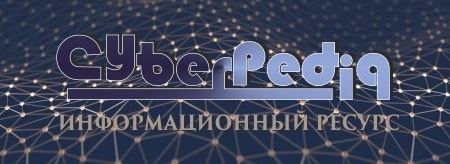
Таксономические единицы (категории) растений: Каждая система классификации состоит из определённых соподчиненных друг другу...
Папиллярные узоры пальцев рук - маркер спортивных способностей: дерматоглифические признаки формируются на 3-5 месяце беременности, не изменяются в течение жизни...
Топ:
Основы обеспечения единства измерений: Обеспечение единства измерений - деятельность метрологических служб, направленная на достижение...
Особенности труда и отдыха в условиях низких температур: К работам при низких температурах на открытом воздухе и в не отапливаемых помещениях допускаются лица не моложе 18 лет, прошедшие...
Теоретическая значимость работы: Описание теоретической значимости (ценности) результатов исследования должно присутствовать во введении...
Интересное:
Инженерная защита территорий, зданий и сооружений от опасных геологических процессов: Изучение оползневых явлений, оценка устойчивости склонов и проектирование противооползневых сооружений — актуальнейшие задачи, стоящие перед отечественными...
Искусственное повышение поверхности территории: Варианты искусственного повышения поверхности территории необходимо выбирать на основе анализа следующих характеристик защищаемой территории...
Берегоукрепление оползневых склонов: На прибрежных склонах основной причиной развития оползневых процессов является подмыв водами рек естественных склонов...
Дисциплины:
![]() |
![]() |
5.00
из
|
Заказать работу |
|
|
Содержание
Введение
1 Общая часть
1.1 Назначение и характеристики системы управления
1.2 Требования к системе управления
2 Конструкторская часть
2.1 Разработка структуры системы управления
2.2 Обоснование выбора контроллера
2.3 Выбор и обоснование выбора типа и количества модулей
2.4 Расчет процентного использования модулей
2.5 Выбор и расчёт блока питания
2.6 Конфигурирование системы
3 Технологическая часть
3.1 Последовательность и технология монтажа системы управления
3.2 Размещение системы управления. Планирование внутреннего пространства шкафа
3.3 Анализ методов диагностирования системы управления
Заключение
Список использованных источников
Введение
Торговая марка SIMATIC широко известна во всём мире, как синоним программируемых логических контроллеров. Сегодня под именем SIMATIC подразумеваются системы комплексной автоматизаций (Totally Integrated Automation – TIA), позволяющие создавать управляющие комплексы любой степени сложности на базе стандартных компонентов. TIA представляет качественно новый метод унификации систем автоматизаций мирового производства и технологий, в котором стандартные аппаратные и программные средства управления сливаются в единую систему: SIMATIC.
В основу построения таких систем положены следующие принципы:
1 Набор встроенных функций, всеобъемлющая диагностика, парольная защита, удобная система подключения внешних цепей, отсутствие ограничений на порядок размещения модулей позволяет создавать многообразные конфигураций систем управления.
2 Широкий спектр центральных процессоров, сигнальных, функциональных, коммуникационных и интерфейсных модулей позволяет в максимальной степени адаптировать контроллер к выполнению поставленных задач. Поддержка функций «горячей» замены модулей.
|
3 Возможность подключения к одному базовому блоку контроллера до 21 стойки расширения, возможность использования ТОР-соединений.
4 Возможность использования всего промышленного программного обеспечения SIMATIC.
Комплексная интегрируемая автоматизация включает в себя:
1 ПЛК - программируемые логические контроллеры;
2 системы управления процессом WinAC;
3 системы числового программного управления С7;
4 преобразователи частоты;
5 контрольно измерительная аппаратура;
6 программируемые сети NET;
7 распределения периферии;
8 низковольтные коммуникационная аппаратура (реле);
9 промышленные компьютеры (ПК).
Общая часть
Требования к системе управления
Цель создания системы управления – построение единого информационно технологического и управляющего пространства, предоставляющего персоналу эффективное информационное окружение для принятия своевременных и качественных решений по управлению технологическим процессом.
Необходимо выяснить, какие устройства требуют аппаратно реализованных схем для удовлетворения требований безопасности. По определению, эти защитные схемы функционируют независимо от программируемого контроллера (хотя защитная схема в общем случае предоставляет интерфейс ввода/вывода для обеспечения координации с программой пользователя). Обычно проектируется матрица подключения каждого исполнительного устройства со своей собственной областью аварийного отключения. Эта матрица является основой для построения принципиальной схемы защитного устройства.
Для проектирования механизмов защиты следует действовать следующим образом:
а) определить логические и механические/электрические блокировки между отдельными задачами автоматизации;
б) спроектировать схемы, разрешающие ручное управление устройствами, относящимися к процессу, в случае аварии;
|
в) определить все остальные требования к защите для безопасного функционирования процесса.
Создание схемы защиты
В промышленном процессе независимо от программируемого контроллера (ПЛК) один аварийный выключатель отключает следующие устройства:
а) блок двигателей насосов;
б) двигатель компрессора;
в) клапаны.
Аварийный выключатель находится на станции оператора. Один вход в контроллер индицирует состояние аварийного выключателя.
К негативным факторам, определяющим промышленную среду, относятся: температура и влажность, удары и вибрация, коррозионно-активная газовая среда, минеральная и металлическая пыль, электромагнитные помехи. Эти факторы обусловливают жесткие требования, определяющие схемотехнические решения, элементную и конструктивную базу ПЛК. Физическое исполнение контроллера определяется требуемой степенью защиты, начиная от контроллеров в легких пластиковых корпусах, металлических корпусах, предназначенных для работы в особо жестких условиях. Правильно подобранный по условиям эксплуатации контроллер нельзя повредить извне без применения экстремальных методов.
Система управления должна удовлетворять жестким требованиям безопасности, не допускающим нанесения увечий и телесных повреждений, как самому оператору, так и другим лицам, находящимся в помещении. На случай аппаратной или программной ошибки, которые ведут к нарушению технологического процесса, обязательно должна присутствовать кнопка аварийной остановки.
Система управления должна быть многоуровневой и обеспечивать прозрачное взаимодействие различных уровней автоматизации, а именно:
1) уровень 1 - уровень агрегатов и установок (приборы и средства контроля, преобразователи, исполнительные устройства, ПЛК);
2) уровень 2 - уровень мониторинга и протоколирование процесса, настройки и управления технологическими процессами агрегатов и установок;
3) уровень 3 - система для планирования работы и управления агрегатами, оперативно диспетчерского управления, управление технологиями, учет производства, расходов ресурсов и интеграция между уровнем 2 и уровнем 4;
4) уровень 4 - уровень систем корпоративного управления.
Режим работы СУ должен быть непрерывным круглосуточным с перерывами на профилактические и ремонтные работы. Должно быть обеспечено совместное функционирование систем всех уровней в составе единого комплекса при полном или частичном отказе функций должны быть предусмотрены средства, направленные на минимизацию рисков и потерь.
|
При проектировании системы управления должны быть предусмотрены возможности расширения объемов входной информации, видов, количества и состава форм отображения информации, архивов истории процесса и подключения к другим системам автоматизации.
Защита данных должна осуществляться путем организации периодического резервного копирования данных на носитель информации и их хранение. При необходимости восстановления данных носители информации участвуют в их восстановлении применительно к той установке, где они были потеряны.
Среднее время наработки на отказ подсистем не менее 10000 часов и 5000 часов для системы управления в целом. Среднее время восстановления работоспособного состояния системы не более 4-х часов. Восстановление чаще всего обеспечивается оперативной заменой вышедших из строя модулей на заведомо исправные. При проектировании системы принимаются решения по организации архитектуры, режимов функционирования, внутрисистемных диагностических возможностей, решение по выбору программно-аппаратных средств системы, которые должны быть направлены на достижение требуемых показателей надежности функционирования.
Конструкторская часть
Конфигурирование системы
Программируемый контроллер S7-300 позволяет включить в центральную монтажную стойку до 8 сигнальных модулей. Если такая однорядная конфигурация контроллера не является достаточной, то возможны два варианта расширения конфигурации при использовании CPU 314:
а) вариант двухрядной конфигурации, имеющей центральную стойку и одну стойку расширения (при использовании интерфейсных модулей IM 365 и с расстоянием до одного метра между стойками);
б) вариант конфигурации, состоящей максимально из 4 рядов, т.е. кроме центральной стойки, имеющей до 3 стоек расширения (при использовании интерфейсных модулей IM 360 и IM 361 и с расстоянием до десяти метров между стойками).
|
Воспользуемся вариантом двухрядной конфигурации, имеющей центральную стойку и одну стойку расширения.
Мы можем задействовать максимум восемь модулей в стойке. Число модулей может быть ограничено также максимально допустимым током потребления на одну стойку, который составляет 1.2 А. Модули связаны между собой внутренней шиной стойки.
С помощью программной утилиты Simatic Step 7 HW Config произведем конфигурирование нашей системы и приведем скриншот конфигурации на рисунке 8 – конфигурация центральной стойки, на рисунке 10 – конфигурация стойки расширения.
Рисунок 8 – Конфигурация центральной стойки
Рисунок 9 – Адресация модулей центральной стойки
Рисунок 10 – Конфигурирование стойки расширения
Рисунок 11 – Адресация модулей стойки расширения
Технологическая часть
Размещение системы управления. Планирование внутреннего пространства шкафа
Необходимо соблюдать размеры зазоров, чтобы обеспечить достаточное место для монтажа модулей и отвода выделяемого ими тепла. Для конструкций S7-300, размещенных на нескольких стойках, рисунок 12 показывает размеры зазоров между отдельными стойками, а также между соседними элементами оборудования, кабельными каналами, по отношению к стенкам шкафов и т.д. Ширина опорного элемента для экрана: а=80 мм
Рисунок 12 – Размер зазоров между отдельными стойками
S7-300 необходимо устанавливать в шкафах, если:
а) вы проектируете большую установку;
б) вы используете свои S7-300 в среде, подверженной действию помех или загрязнений;
в) для выполнения требований UL/CSA об установке в шкафах.
При выборе и расчете шкафов принимайте во внимание следующие критерии:
а) условия окружающей среды на месте установки шкафа;
б) требуемые монтажные зазоры для стоек (профильных шин);
в) общая мощность потерь содержащихся в шкафу компонентов.
Условия окружающей среды на месте установки шкафа (температура, влажность, пыль, химические вещества, опасность взрыва) определяют требуемый вид защиты (IP xx) шкафа.
Мощность потерь, которая может быть отведена из шкафа, зависит от его типа, температуры окружающей среды и размещения приборов в шкафу.
Чтобы определить размеры шкафа, пригодного для установки S7-300 необходимо принять во внимание следующие данные:
а) потребность в месте для стоек (профильных шин);
б) минимально допустимые зазоры между стойками и стенками шкафа;
в) минимально допустимые зазоры между стойками;
г) потребность в месте для кабельных каналов или вентиляторов;
д) положение продольных несущих ребер.
Рассчитаем рассеиваемую мощность компонентов для каждой корзины как сумму потребляемых мощностей.
|
P1 = 9,86+4+0,5+0,65+0,65+0,4+0,6+0,6+0,6+0,6+5,8 = 24,26 Вт
P2= 0,5+0,6+0,6+6,6+6,6+6+6=26,9 Вт
Таким образом, общая мощность потерь составляет 51,16 Вт.
Рисунок 13 - Отводимая мощность потерь
Исходя из незначительной мощности потерь и с учётом рисунка 13 выбираем шкаф с собственной конвекцией. Отвод тепла производится только через стенки шкафа, тепло скапливается в основном в верхней части.
На следующем рисунке показана диаграмма с ориентировочными значениями для допустимых температур окружающей среды шкафа с размерами 600 x 600 x 2000 мм в зависимости от мощности потерь. Эти значения соответствуют действительности только при соблюдении предписанных зазоров и монтажных размеров для стоек (профильных шин).
Заключение
Разработка системы управления промышленным объектом на базе микропроцессорного контроллера достаточно трудоемкий процесс и включает в себя множество стадий.
Так как любой технологический процесс представляет собой совокупность определенных операций, то перед началом проектирования системы автоматизации для требуемого технологического процесса мы разбили его на составляющие операции. После того, как все операции были определены, мы изучили оборудование, которое будет участвовать в технологическом процессе. Первой стадией проектирования системы автоматизации являлось определение назначения и характеристик системы управления технологическим процессом, а также изучение требований, предъявляемых к системе управления в процессе её разработки и функционирования.
После проработки начальной стадии проектирования мы приступили к разработке структуры системы управления, а именно была разработана упрощенная структура (рисунок 1), а затем, на её основе, полная структурная схема системы управления (рисунок 2). В связи с относительно низкой степенью сложности решаемых задач было принято решение об использовании контроллера S7-300. Затем из общего количества входных и выходных сигналов мы определили, какие из сигналов являются аналоговыми, а какими дискретными для последующего выбора количества и типа сигнальных модулей. Типы и количество модулей выбирались исходя из количества и типа сигналов, а также требований к диагностическим способностям модулей. Далее, мы рассчитали процентное использование каждого из модулей. После определения необходимого количества, а также типов модулей была рассчитана общая потребляемая мощность, исходя из которой выбирался блок питания. Заключительным этапом конструкторской части было конфигурирование системы с помощью программы Simatic STEP 7.
Внутреннее пространство шкафа, а также его тип выбирался исходя из мощности потерь, которая в среднем составила 10% от потребляемой мощности. После проведения расчетов был выбран шкаф с собственной конвекцией.
В завершении разработки системы управления промышленным объектом на базе микропроцессорного контроллера был проведен анализ методов диагностирования системы управления.
Содержание
Введение
1 Общая часть
1.1 Назначение и характеристики системы управления
1.2 Требования к системе управления
2 Конструкторская часть
2.1 Разработка структуры системы управления
2.2 Обоснование выбора контроллера
2.3 Выбор и обоснование выбора типа и количества модулей
2.4 Расчет процентного использования модулей
2.5 Выбор и расчёт блока питания
2.6 Конфигурирование системы
3 Технологическая часть
3.1 Последовательность и технология монтажа системы управления
3.2 Размещение системы управления. Планирование внутреннего пространства шкафа
3.3 Анализ методов диагностирования системы управления
Заключение
Список использованных источников
Введение
Торговая марка SIMATIC широко известна во всём мире, как синоним программируемых логических контроллеров. Сегодня под именем SIMATIC подразумеваются системы комплексной автоматизаций (Totally Integrated Automation – TIA), позволяющие создавать управляющие комплексы любой степени сложности на базе стандартных компонентов. TIA представляет качественно новый метод унификации систем автоматизаций мирового производства и технологий, в котором стандартные аппаратные и программные средства управления сливаются в единую систему: SIMATIC.
В основу построения таких систем положены следующие принципы:
1 Набор встроенных функций, всеобъемлющая диагностика, парольная защита, удобная система подключения внешних цепей, отсутствие ограничений на порядок размещения модулей позволяет создавать многообразные конфигураций систем управления.
2 Широкий спектр центральных процессоров, сигнальных, функциональных, коммуникационных и интерфейсных модулей позволяет в максимальной степени адаптировать контроллер к выполнению поставленных задач. Поддержка функций «горячей» замены модулей.
3 Возможность подключения к одному базовому блоку контроллера до 21 стойки расширения, возможность использования ТОР-соединений.
4 Возможность использования всего промышленного программного обеспечения SIMATIC.
Комплексная интегрируемая автоматизация включает в себя:
1 ПЛК - программируемые логические контроллеры;
2 системы управления процессом WinAC;
3 системы числового программного управления С7;
4 преобразователи частоты;
5 контрольно измерительная аппаратура;
6 программируемые сети NET;
7 распределения периферии;
8 низковольтные коммуникационная аппаратура (реле);
9 промышленные компьютеры (ПК).
Общая часть
Назначение и характеристики системы управления
Программируемый логическийконтроллер(ПЛК) – это устройство на основе микропроцессора, основная задача которого сбор информации с датчиков, последовательная обработка по заданному алгоритму, а также выдача сигналов на исполнительное устройство. Современные ПЛК помимо простых логических операций способны выполнять цифровую обработку сигналов, управление приводами, регулирование, функции операторского управления. для управления исполнительными механизмами — электродвигателями, клапанами, лампочками и т. п., которые являются неотъемлемой частью систем автоматизации во всех отраслях промышленности.
Программируемый логический контроллер играет очень важную роль в технологическом процессе установки выпаривания. Установка выпаривания является достаточно сложным технологическим объектом с множеством датчиков различного назначения, а именно: датчик давления вакуумной камеры, датчик уровня выпарной камеры, датчик давления пара, датчик давления продукта, датчик температуры пара, датчик расхода продукта, датчик температуры выпарной камеры, датчик давления выпарной камеры, датчик давления дистиллята, датчик температуры дистиллята, 2 датчика температуры концентрата, 2 датчики давления концентрата, 2 датчика температуры продукта, 2 датчика давления концентрата в емкости, датчик расхода концентрата.
Система управления осуществляет контроль за клапанами: вакуумный клапан, клапан подачи эмульсии, клапан подачи пара, клапан подачи продукта, клапан концентрата выпарной камеры, клапан откачки дистиллята выпарной камеры, клапан концентрата, клапан эмульсии. А также целым блоком двигателей насосов: насос дистиллята, дозировочный насос, вакуумный насос, насос концентрата. Датчики позволяют ПЛК следить за необходимыми физическими величинами, исходя из значений которых, ПЛК подает управляющие сигналы на блок двигателей, клапаны.
Так, например, получив информацию о высоком давлении в одной из камер от датчика давления пара, ПЛК подает управляющий сигнал на клапан, тем самым открывая его.
Система управления контролирует технологический процесс выпаривания. Получая сигналы с датчиков, она обрабатывает их, после чего выдает управляющие сигналы на исполнительные устройства с целью изменения необходимой величины до значения, соответствующего технологическому процессу.
Требования к системе управления
Цель создания системы управления – построение единого информационно технологического и управляющего пространства, предоставляющего персоналу эффективное информационное окружение для принятия своевременных и качественных решений по управлению технологическим процессом.
Необходимо выяснить, какие устройства требуют аппаратно реализованных схем для удовлетворения требований безопасности. По определению, эти защитные схемы функционируют независимо от программируемого контроллера (хотя защитная схема в общем случае предоставляет интерфейс ввода/вывода для обеспечения координации с программой пользователя). Обычно проектируется матрица подключения каждого исполнительного устройства со своей собственной областью аварийного отключения. Эта матрица является основой для построения принципиальной схемы защитного устройства.
Для проектирования механизмов защиты следует действовать следующим образом:
а) определить логические и механические/электрические блокировки между отдельными задачами автоматизации;
б) спроектировать схемы, разрешающие ручное управление устройствами, относящимися к процессу, в случае аварии;
в) определить все остальные требования к защите для безопасного функционирования процесса.
Создание схемы защиты
В промышленном процессе независимо от программируемого контроллера (ПЛК) один аварийный выключатель отключает следующие устройства:
а) блок двигателей насосов;
б) двигатель компрессора;
в) клапаны.
Аварийный выключатель находится на станции оператора. Один вход в контроллер индицирует состояние аварийного выключателя.
К негативным факторам, определяющим промышленную среду, относятся: температура и влажность, удары и вибрация, коррозионно-активная газовая среда, минеральная и металлическая пыль, электромагнитные помехи. Эти факторы обусловливают жесткие требования, определяющие схемотехнические решения, элементную и конструктивную базу ПЛК. Физическое исполнение контроллера определяется требуемой степенью защиты, начиная от контроллеров в легких пластиковых корпусах, металлических корпусах, предназначенных для работы в особо жестких условиях. Правильно подобранный по условиям эксплуатации контроллер нельзя повредить извне без применения экстремальных методов.
Система управления должна удовлетворять жестким требованиям безопасности, не допускающим нанесения увечий и телесных повреждений, как самому оператору, так и другим лицам, находящимся в помещении. На случай аппаратной или программной ошибки, которые ведут к нарушению технологического процесса, обязательно должна присутствовать кнопка аварийной остановки.
Система управления должна быть многоуровневой и обеспечивать прозрачное взаимодействие различных уровней автоматизации, а именно:
1) уровень 1 - уровень агрегатов и установок (приборы и средства контроля, преобразователи, исполнительные устройства, ПЛК);
2) уровень 2 - уровень мониторинга и протоколирование процесса, настройки и управления технологическими процессами агрегатов и установок;
3) уровень 3 - система для планирования работы и управления агрегатами, оперативно диспетчерского управления, управление технологиями, учет производства, расходов ресурсов и интеграция между уровнем 2 и уровнем 4;
4) уровень 4 - уровень систем корпоративного управления.
Режим работы СУ должен быть непрерывным круглосуточным с перерывами на профилактические и ремонтные работы. Должно быть обеспечено совместное функционирование систем всех уровней в составе единого комплекса при полном или частичном отказе функций должны быть предусмотрены средства, направленные на минимизацию рисков и потерь.
При проектировании системы управления должны быть предусмотрены возможности расширения объемов входной информации, видов, количества и состава форм отображения информации, архивов истории процесса и подключения к другим системам автоматизации.
Защита данных должна осуществляться путем организации периодического резервного копирования данных на носитель информации и их хранение. При необходимости восстановления данных носители информации участвуют в их восстановлении применительно к той установке, где они были потеряны.
Среднее время наработки на отказ подсистем не менее 10000 часов и 5000 часов для системы управления в целом. Среднее время восстановления работоспособного состояния системы не более 4-х часов. Восстановление чаще всего обеспечивается оперативной заменой вышедших из строя модулей на заведомо исправные. При проектировании системы принимаются решения по организации архитектуры, режимов функционирования, внутрисистемных диагностических возможностей, решение по выбору программно-аппаратных средств системы, которые должны быть направлены на достижение требуемых показателей надежности функционирования.
Конструкторская часть
|
|
Поперечные профили набережных и береговой полосы: На городских территориях берегоукрепление проектируют с учетом технических и экономических требований, но особое значение придают эстетическим...
Типы оградительных сооружений в морском порту: По расположению оградительных сооружений в плане различают волноломы, обе оконечности...
Эмиссия газов от очистных сооружений канализации: В последние годы внимание мирового сообщества сосредоточено на экологических проблемах...
Своеобразие русской архитектуры: Основной материал – дерево – быстрота постройки, но недолговечность и необходимость деления...
© cyberpedia.su 2017-2024 - Не является автором материалов. Исключительное право сохранено за автором текста.
Если вы не хотите, чтобы данный материал был у нас на сайте, перейдите по ссылке: Нарушение авторских прав. Мы поможем в написании вашей работы!