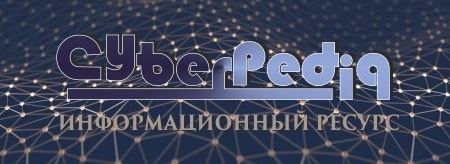
История создания датчика движения: Первый прибор для обнаружения движения был изобретен немецким физиком Генрихом Герцем...
Поперечные профили набережных и береговой полосы: На городских территориях берегоукрепление проектируют с учетом технических и экономических требований, но особое значение придают эстетическим...
Топ:
Организация стока поверхностных вод: Наибольшее количество влаги на земном шаре испаряется с поверхности морей и океанов...
Техника безопасности при работе на пароконвектомате: К обслуживанию пароконвектомата допускаются лица, прошедшие технический минимум по эксплуатации оборудования...
Интересное:
Средства для ингаляционного наркоза: Наркоз наступает в результате вдыхания (ингаляции) средств, которое осуществляют или с помощью маски...
Инженерная защита территорий, зданий и сооружений от опасных геологических процессов: Изучение оползневых явлений, оценка устойчивости склонов и проектирование противооползневых сооружений — актуальнейшие задачи, стоящие перед отечественными...
Наиболее распространенные виды рака: Раковая опухоль — это самостоятельное новообразование, которое может возникнуть и от повышенного давления...
Дисциплины:
![]() |
![]() |
5.00
из
|
Заказать работу |
|
|
ТЕОРИЯ РЕЗАНИЯ
Методические указаниЯ
к лабораторным работам №1…3
для студентов направления 6.09.02 "Инженерная механика"
всех форм обучения
Часть 1
Севастополь
УДК 621.001
Теория резания. Методические указания к лабораторным работам. Часть 1 /Разраб. С.М. Братан доктор техн. наук, Д.Е. Сидоров. – Севастополь: Изд-во СевНТУ, 2007. – 36с.
Целью методических указаний является оказание помощи студентам при выполнении лабораторных работ.
Методические указания предназначены для студентов направления “Инженерная механика” всех форм обучения.
Методические указания утверждены на заседании кафедры "Технологии машиностроения" протокол №2 от 10 октября 2006 г.
Допущено учебно-методическим центром и научно-методическим советом СевНТУ в качестве методических указаний.
Рецензент: А.В. Троценко, канд. техн. наук, доцент каф. “Технологии машиностроения”.
Ответственный за выпуск: Ю.К. Новоселов, зав. каф. “Технологии машиностроения”, доктор техн. наук.
Содержание
1. | Лабораторная работа №1. Исследование геометрии и конструкции резцов………….………….………….………….…………… | |
2. | Лабораторная работа №2. Кинематика резания………….………….…… | |
3. | Лабораторная работа №3. Рабочие углы резца………….………….……. | |
Библиографический список………….………….………….………….…… |
ЛАБОРАТОРНАЯ РАБОТА № 1
ИССЛЕДОВАНИЕ ГЕОМЕТРИИ И КОНСТРУКЦИИ РЕЗЦОВ
(Продолжительность выполнения – 4 часа)
Цель работы: изучить классификацию резцов, закрепить знание основных определений поверхностей и геометрических параметров резцов, ознакомиться с приборами, служащими для измерения геометрических параметров резцов и с правилами вычерчивания эскизов резцов.
|
Общие сведения
Главные элементы резцов
Резцы являются одним из простых и наиболее распространенных металлорежущих инструментов. Основные определения для обработки резцами даны в ГОСТ 25751-83.
Резец состоит из головки, т. е. рабочей части, и тела или стержня, служащего для закрепления резца (рисунок 1.1) в резцедержателе станка или в другом крепежном устройстве.
![]() |
Рисунок 1.1 – Конструкция резца |
Головка резца состоит из следующих элементов: 1) передней поверхности (грани); 2) задней поверхности (грани); 3) режущих кромок; 4) вершины.
Передней поверхностью называется поверхность резца, по которой сходит стружка.
Задними поверхностями называются поверхности, обращенные к обрабатываемой заготовке. Их две – главная и вспомогательная.
Режущие кромки образуются пересечением передней и задних поверхностей. Их две – главная режущая кромка и вспомогательная.
Главная режущая кромка выполняет главную работу резания. Она образуется от пересечения передней и главной задней поверхностей. Вспомогательная режущая кромка образуется от пересечения передней и вспомогательной задней поверхностей. Вспомогательных режущих кромок может быть две (например, у отрезного резца).
Вершиной резца является место сопряжения главной режущей кромки со вспомогательной.
Форма режущей части резца определяется конфигурацией и расположением передней и задней поверхностей. Расположение указанных поверхностей и режущих кромок в пространстве характеризуется рядом углов, называемых углами резца.
Исходной базой для измерения углов являются две плоскости: основная плоскость 5 и плоскость резания 4, указанные на рисунке 1.2.
![]() |
Рисунок 1.2 – Поверхности детали при точении |
На рисунке 1.2 обозначены также три поверхности детали: обрабатываемая поверхность 1, поверхность резания 2 и обработанная поверхность 3.
|
Плоскость резания 4 – плоскость, касательная к поверхности резания и проходящая через главную режущую кромку.
Основная плоскость 5 – плоскость, параллельная направлениям продольной и поперечной подач резца.
Главная секущая плоскость – плоскость, перпендикулярная к проекции главной режущей кромки на основную плоскость.
Резцы классифицируют по ряду признаков.
Классификация резцов приведена в таблице 1.1.
Таблица 1.1
1.По применяемости на станках | ||||||
Токарные, строгальные, долбежные, автоматные | ||||||
2.По видам обработки | ||||||
Проходные | Подрезные | Прорезные | ||||
![]() | ![]() | ![]() | ||||
Отрезные | Расточные | Фасочные | ||||
![]() | ![]() | ![]() | ||||
Резьбовые | Галтельные | Фасонные | ||||
![]() | ![]() | ![]() | ||||
3. По характеру обработки | ||||||
Черновые, чистовые, для тонкого точения | ||||||
4. По направлению подачи | ||||||
Правые | Левые | |||||
![]() ![]() | ![]() ![]() | |||||
5. По форме головки | ||||||
Прямые (левый, правый) | Изогнутые (вверх вперед, вниз назад) | |||||
![]() | ![]() | |||||
С отогнутой головкой (левый, правый) | С оттянутой головкой (влево, симметрично, вправо) | |||||
![]() |
![]() | |||||
6. По способу изготовления и крепления режущей части | ||||||
Цельные | С приваренной или припаянной пластинкой | С механическим креплением пластинки | ||||
![]() |
![]() | ![]() | ||||
7. По конструктивным особенностям | ||||||
Державочные | Стержневые | |||||
![]() | ![]() | |||||
Призматические | Круглые | |||||
![]() | ![]() | |||||
8. По материалу режущей части | ||||||
Быстрорежущие, твердосплавные, минералокерамические, алмазные | ||||||
По виду обработки токарные резцы делятся на проходные, подрезные, расточные, отрезные, прорезные, галтельные, ф асочные резьбовые и фасонные ( см. таблицу 1.1).
Проходные резцы применяются как для обработки вдоль оси заготовки, так и для подрезки торца (рисунок 1.3).
![]() |
Рисунок 1.3 – Обработка заготовки проходным резцом |
Подрезные резцы применяют для обработки заготовок в направлении, перпендикулярном или наклонном к оси вращения (рисунок 1.4). Подрезной упорный резец может быть использован и для продольной обточки с одновременной обработкой торцевой поверхности, составляющей с цилиндрической поверхностью прямой угол.
![]() |
Рисунок 1.4 – Обработка заготовки подрезным резцом |
Прорезные резцы (рисунок 1.5) аналогичны отрезным (рисунок 1.6), но имеют длину режущей кромки, соответствующую ширине прорезаемой канавки.
![]() |
Рисунок 1.5 – Обработка заготовки прорезнымрезцом |
![]() |
Рисунок 1.6 – Обработка заготовки отрезнымрезцом |
Галтельные резцы применяют для протачивания закругленных канавок.
|
Резьбовые резцы применяют для нарезания наружной и внутренней резьбы (рисунок 1.7).
![]() |
Рисунок 1.7 – Обработка заготовки резьбовымрезцом |
Фасочные резцы применяют для обработки фасок.
Фасонные резцы применяют для обработки фасонных поверхностей (рисунок 1.8).
![]() |
Рисунок 1.8 – Обработка заготовки фасоннымрезцом |
Расточные резцы применяют для обработки глухих и сквозных отверстий (рисунок 1.9).
![]() |
Рисунок 1.9 – Обработка заготовки расточнымрезцом |
По направлению подачи токарные резцы делятся на праве и левые.
Правыми резцами называются такие, у которых при наложении на них сверху ладони правой руки так, чтобы пальцы были направлены к вершине, главная режущая кромка оказывается расположенной на стороне большого пальца. При работе на токарном станке эти резцы перемещаются справа налево (от задней бабки к передней).
Левыми резцами называются такие резцы, у которых при указанном выше наложении левой руки главная режущая кромка оказывается расположенной на стороне большого пальца.
По форме головки и по ее расположению относительно стержня резцы разделяются на прямые, отогнутые, изогнутые и с оттянутой головкой.
У прямых резцов ось прямая. У отогнутых резцов головка резца в плане отогнута в сторону. У изогнутых резцов ось резца изогнута в боковой проекции.
У резцов с оттянутой головкой головка уже тела резца. Она может быть расположена как симметрично к оси тела резца, так и быть смещенной по отношению к ней, причем головка может быть прямой, отогнутой и изогнутой.
Высотой головки h резца называется расстояние вершины резца от опорной поверхности, измеренное перпендикулярно к ней. Высота головки может быть положительной когда вершина резца выше поверхности, или отрицательной, когда вершина резца ниже опорной поверхности (рисунок 1.10).
Длиной головки резца называется наибольшее расстояние от вершины резца до линии выхода поверхности заточки, измеренное параллельно продольным граням тела резца.
|
![]() |
Рисунок 1.10 – Высота головки резца |
На обрабатываемой заготовке при снятии с нее стружки различают следующие поверхности: обрабатываемую; обработанную; поверхность резания.
Обрабатываемой поверхностью называется та поверхность заготовки, которая будет срезана.
Обработанной поверхностью называется поверхность, полученная после снятия стружки.
Поверхностью резания называется поверхность, образуемая на обрабатываемой заготовке непосредственно режущей кромкой. Поверхность резания является переходной между обрабатываемой и обработанной поверхностями.
Углы резца
Режущая часть резца имеет форму клина, заточенного под определенными углами.
Углы резца делятся на главные и вспомогательные.
Главные углы измеряются в главной секущей плоскости. К главным углам резца относятся задний угол , угол заострения
, передний угол
и угол резания
.
На рисунке 1.11 дана рабочая часть резца с необходимыми сечениями, где показаны главные и вспомогательные углы:
![]() |
Рисунок 1.11 – Основные углы резца |
а ) – главный передним углом называется угол между передней поверхностью резца и плоскостью, перпендикулярной к плоскости резания, проведенной через главную режущую кромку. Он может быть положительным, когда передняя поверхность направлена вниз от плоскости, перпендикулярной к плоскости резания равным нулю, когда передняя поверхность перпендикулярна плоскости резания (рисунок 1.11);
б) – главным задним углом называется угол между главной задней поверхностью резца и плоскостью резания;
в) – углом резания называется угол между передней поверхностью резца и плоскостью резания.
г) – главный угол заострения называется угол между передней и главной задней поверхностью резца.
При положительном значении между углами существует зависимость
При положительном значении
.
Кроме рассмотренных главных углов, резец характеризуется вспомогательными: передним углам, углами в плане и углом наклона главной режущей кромки.
Вспомогательные углы измеряются во вспомогательной секущей плоскости.
Вспомогательная секущая плоскость – это плоскость, перпендикулярная к проекции вспомогательной режущей кромки на основную плоскость.
– вспомогательный задний угол называется угол между вспомогательной задней поверхностью и плоскостью, проходящей через вспомогательную режущую кромку, перпендикулярную основной плоскости.
Положение режущих кромок определяется углами в плане (рисунок 1.11):
а) – главный угол в плане – угол между проекцией главной режущей кромки на основную плоскость и направлением подачи (угол между плоскостью резания и рабочей плоскостью);
|
б) – вспомогательный угол в плане – угол между проекцией вспомогательной режущей кромки на основную плоскость и направлением подачи (угол между рабочей плоскостью и проекцией вспомогательной режущей кромки на основную плоскость);
в) – угол при вершине – угол между проекциями главной и вспомогательной режущих кромок на основную плоскость;
Очевидно, что j + e + j1 = 180°.
г) – угол наклона главной режущей кромки – угол, заключенный между главной режущей кромкой и линией, проведенной через вершину резца параллельно основной плоскости (угол между главной режущей кромкой и основной плоскостью).
На рисунке 1.12 показан угол со стороны главной задней поверхности.
![]() |
Рисунок 1.12 – Угол ![]() |
Угол наклона главной режущей кромки может быть положительным (рисунок 1.12, а), равным нулю (рисунок 1.12, б), отрицательным (рисунок 1.12, в).
При положительном угле - вершина резца занимает низшее положение на главной режущей кромке, при отрицательном угле
- вершина резца занимает высшее положение на главной режущей кромке.
1.1.3. Геометрические элементы режущей части резцов
Геометрические элементы режущей части инструмента, под которыми понимают форму передней поверхности, его углы, форму режущих кромок, оказывают большое влияние на его износ (стойкость). Оптимальное значение геометрических элементов зависит от материала обрабатываемой заготовки, материала режущей части инструмента, типа инструмента и условий обработки.
Передняя поверхность резцов делается нескольких форм. Наиболее простой является плоская положительная (рисунок 1.13 форма I). Она рекомендуется: 1) для резцов всех типов (как с пластинками из быстрорежущих сталей, так и с пластинками из твердых сплавов) при обработке чугуна; 2) для резцов из быстрорежущей стали при обработке ими сталей с подачами до 0,2 мм; 3) для фасонных резцов со сложным контуром режущей кромки. Для облегчения заточки и доводки резца по передней поверхности угол делается не на всей передней поверхности пластинки, а на некоторой ширине
мм.Угол же врезания пластинки
.
Для упрочнения режущего лезвия на некоторой ширине делается фаска под углом
(форма II).Такая форма называется плоской с фаской. Применяется она:
1) для быстрорежущих резцов при обработке ими сталей с подачей мм за один оборот заготовки, (при точении) или двойной ход
2) для резцов, оснащенных пластинками из твердых сплавов, при недостаточной жесткости системы для облегчения отвода стружки необходимо применять стружкозавиватели (форма II- а).
Для облегчения стружкоотвода (стружкозавивания) передняя поверхность делается с выкружкой радиусом R. Такая форма называется радиусной с фаской, и она применяется:
– для быстрорежущих резцов всех типов (за исключением фасонных со сложным контуром режущей кромки) при обработке ими сталей;
– для твердосплавных резцов при получистовой обработке
При обработке твердосплавными резцами сталей применяются плоская отрицательная двойная (форма III) и плоская отрицательная одинарнаяформы. Первая (форма III- а) при достаточной жесткости системы станок – заготовка – резец – приспособление.
Передний угол делается для облегчения процесса стружкообразования, уменьшения трения и износа по передней поверхности резца. Наиболее благоприятным значением угла
был бы угол 45°, но такая величина переднего угла уменьшает угол заострения, и делает режущее лезвие резца недостаточно прочным. Поэтому при обработке твердых металлов, когда в процессе резания на резец будут действовать значительные силы, при обработке прерывистых поверхностей, когда имеет место удар, а также при обработке хрупких металлов (серые чугуны), когда вследствие „сыпучей" стружки надлома нагрузка на резец сосредоточена на участке, близко расположенном к режущей кромке, в целях упрочнения режущей кромки передний угол приходится уменьшать. Чем мягче обрабатываемый металл, тем меньшие силы будут действовать на резец, тем, следовательно, большим может быть взят передний угол
.
Задний угол делается для уменьшения трения задних поверхностей резца об обработанную поверхность и поверхность резания, которые в процессе резания подвергаются как упругим, так и пластическим деформациям.
Наличие этих деформаций вызывает некоторое выпучивание поверхностей, приводящее к возникновению давления на заднюю поверхность резца вблизи его режущей кромки. Чем больше будет задний угол , тем дальше будет отстоять задняя поверхность от мест вспучивания, тем меньше будет трение при относительном перемещении резца и заготовки. Однако большое значение заднего угла уменьшает угол заострения
, что приводит к снижению прочности режущего лезвия (кромки) резца.
Среднее значение величины заднего угла для резцов 6° – 12°.
Форма I | Форма II |
![]() | ![]() |
Форма II-a | Форма III |
![]() | ![]() |
Форма III-a | |
![]() | |
Рисунок 1.13 – Форма передней поверхности резца |
Чем меньше толщина срезаемого слоя, тем большим должен быть угол ,.а так как толщина срезаемого слоя пропорциональна величине подачи, то значения заднего угла и выбираются обычно в зависимости от подачи: чем меньше подача, тем больше задний угол.
В таблице 1.2 приведены средние значения задних и передних углов, рекомендуемых для резцов, оснащенных пластинками из твердых сплавов.
Таблица 1.2
Обрабатываемый материал | ![]() | ![]() | |||
Величина подачи ![]() | Форма передней поверхности | ||||
![]() | ![]() | I, II, II- a | III, III- a | ||
Стали конструкционные, углеродистые и легированые | ![]() | -5 | |||
![]() | - | - | -10 | ||
Чугун серый | ![]() | - | |||
![]() | - | ||||
Чугун ковкий | ![]() | - |
Задний вспомогательный угол берется равным главному заднему углу у всех резцов, кроме отрезных и прорезных. У последних угол
.
Главный угол в плане и вспомогательный –
оказывают большое влияние на стойкость резца. Чем меньше главный и вспомогательный углы в плане, тем более массивной будет головка резца, тем тоньше стружка и длиннее активная часть режущей кромки, тем меньшую термодинамическую нагрузку будет испытывать единица длины режущего лезвия, тем менее интенсивно будет изнашиваться резец и выше будет его стойкость. Кроме того, малые углы
и
способствуют получению более чистой обработанной поверхности. Но с уменьшением
и
увеличивается отжим резца от заготовки и при недостаточной жесткости системы станок – заготовка – резец – приспособление могут возникнуть вибрации, при которых резко ухудшается качество обработки. Для нормальных условий работы, принимают значения
.
Угол наклона главной режущей кромки влияет на направление схода стружки, на массивность головки резца и на место начального соприкосновения срезаемого слоя с режущей кромкой при прерывистом резании.
Радиус закругления при вершине резца в плане повышает прочность режущей кромки у вершины, стойкость резца и улучшает чистоту обработанной поверхности. Однако увеличение радиуса приводит к резкому возрастанию силы отжима резца от заготовки и к возникновению вибраций.
ПОРЯДОК ВЫПОЛНЕНИЯ РАБОТЫ
2.1. Нарисовать эскизы трех резцов с необходимыми сечениями.
2.2. Произвести измерение трех резцов. Результаты измерения занести в протокол, образец которого показан в таблице 1.3.
2.3. Составить отчет о проделанной работе.
Таблица 1.3
Наименование резца | Углы резца в градусах | Материал режущей части | ||||||||
Главные | В плане | Вспомогательные | ||||||||
![]() | ![]() | ![]() | ![]() | ![]() | ![]() | ![]() | ![]() | ![]() | ||
СОДЕРЖАНИЕ ОТЧЕТА
Отчет содержит:
а) основные теоретические положения, изложенные в разделе 1.1 настоящих методических указаний;
б) эскизы резцов с указанием главных и вспомогательных углов, углов в плане и габаритных размеров;
в) заполненный протокол измерений (таблица 1.3);
г) выводы по работе.
КОНТРОЛЬНЫЕ ВОПРОСЫ
4.1. Назовите отличительные признаки токарных, строгальных, долбежных, и автоматных резцов.
4.2. Сколько режущих кромок у проходного токарного резца?
4.3. Какие углы измеряются в главной секущей плоскости?
4.4. Какими углами определяется положение режущих кромок?
4.5. На что влияет вспомогательный задний угол?
3.6. На что влияет угол наклона главной режущей кромки?
3.7. Какие приборы применяются для измерения углов резцов?
ЛАБОРАТОРНАЯ РАБОТА № 2
КИНЕМАТИКА РЕЗАНИЯ
(Продолжительность выполнения – 4 часа)
Цель работы:
1. Ознакомление с кинематическими схемами резания;
2. Изучить движения резания, движение подачи и вспомогательные движения при строгании и продольном точении;
3. Получить навыки в построении схем резания и обозначении элементов режима резания и срезаемого слоя на примере строгания и точения.
ОБЩИЕ СВЕДЕНИЯ
Для того чтобы инструмент мог удалить с детали стружку (припуск) инструменту и детали сообщают движения с определенными направлениями и скоростями. Все движения могут быть определены принципиальными кинематическими схемами, которые выражают абсолютные движения, сообщаемые в процессе резания инструмента и обрабатываемой детали механизмами станка.
В зависимости от числа и характера сочетаемых движений принципиальные кинематические схемы могут быть разделены на восемь групп:
1 – Одно прямолинейное движение;
2 – Два прямолинейных движения;
3 – Одно вращательное;
4 – Два вращательных;
5 – Одно вращательное и одно прямолинейное;
6 – Два вращательных и одно прямолинейное;
7 – Два прямолинейных и одно вращательное;
8 – Три вращательных.
В зависимости от соотношения угловых и линейных скоростей, движения, сообщаемых инструменту или детали, называют движением резания, а другое – движением подачи. Движение резания – это движение, которое необходимо для осуществления непрерывного процесса резания или периодического его повторения. Скорость движения резания во много раз превышает движение подачи. Скорость движения резания называют скоростью резания, скорость движения подачи – просто подачей.
На рисунках 2.1. а и 2.2. а приведены фотографии двух распространенных видов обработки: строгания и продольного точения.
При строгании движением резания является прямолинейное движение детали (рисунок 2.1. б и 2.1. в) совершаемое после каждого двойного хода резца. При продольном точении движением резания является вращательное движение детали, а движением подачи – прямолинейное движение резца вдоль оси детали одновременно с движением резания (рисунок 2.2. б и 2.2. в).
Сущность того или иного метода обработки определяется только соотношением скоростей, осуществляемых при движении, и не зависит от того, сообщается ли движение резания и подачи инструменту или детали.
В зависимости от того совершаются движения резания и подачи одновременно или в разное время, все инструменты делят на инструменты с простым и сложным рабочим движением. Если движение подачи отсутствует на время движения резания – это простое рабочее движение. Если движение резания и подачи совершаются одновременно – сложное рабочее движение. Исходя из этого строгальный резец (рисунок 2.1) совершает простое, а токарный резец (рисунок 2.2) – сложное движение.
Большинство режущих инструментов (токарные резцы, сверла, зенкеры, развертки, фрезы и др.) имеет сложное рабочее движение.
Инструментов с простым рабочим движением значительно меньше. К ним можно отнести строгальные и долбежные резцы, протяжки и некоторые другие инструменты.
Если при сложном рабочем движении инструмента векторы скорости резания и подачи
сложить, то результирующий вектор будет вектором истинной скорости резания. Так как вектор подачи
весьма мал по сравнению с вектором
, то истинная скорость резания по величине мало отличается от вектора скорости резания
. При простом рабочем движении, если отсутствует движение подачи понятия истинной скорости резания и скорости резания совпадает. Вектор истинной скорости резания всегда направлен по касательной к траектории рабочего движения инструмента. При строгании траекторией рабочего движения является прямая линия, при продольном точении – винтовая линия с винтовой осью, совпадающей с осью детали.
В процессе срезания припуска на детали различают характерные поверхности: обрабатываемую 1, обработанную 2 и поверхность резания 3 (рисунки 2.1 и 2.2).
Порядок выполнения работы
1. Ознакомиться с основными кинематическими схемами резания;
2. Ознакомиться с движением резания, движением подачи установочными и вспомогательными движениями при строгании и точении;
3. Измерить после обработки на строгальном и токарно-винторезном станках поверхности детали. Занести в таблицу измерений данные измерений и режимы резания;
4. Рассчитать скорость резания , скорость минутной подачи
и истинную скорость резания
, а также построить схему резания при строгании и точении с указанием всех элементов, в том числе толщину
и ширину
среза;
5. Оформить отчет.
СОДЕРЖАНИЕ ОТЧЕТА
Отчет по лабораторным работам должен включать:
1. Схемы резания строгания и продольного точения (рисунки 2.3 и 2.4);
2. Таблицу необходимых данных;
3. Расчеты величины элементов резания и срезаемого слоя;
4. Выводы о форме сечения срезанных слоев.
Для зачета по лабораторной работе следует иметь оформленный отчет и ответить на контрольные вопросы.
КОНТРОЛЬНЫЕ ВОПРОСЫ
1. Дайте определение элементов резания и срезаемого слоя.
2. Чем отличается простое рабочее движение от сложного?
3. Назовите процессы обработки заготовок резанием имеющие сложное рабочее движение инструмента.
4. Как влияет угол наклона главной режущей кромки на скорость съема припуска?
5. Изменится ли толщина среза при увеличении переднего угла? Ели да то как?
6. Какое влияние оказывает главный угол в плане на ширину срезаемого слоя.
ЛАБОРАТОРНАЯ РАБОТА № 3
РАБОЧИЕ УГЛЫ РЕЗЦА
(Продолжительность выполнения – 2 часа)
Цель работы:
1. Ознакомиться с факторами, влияющими на изменение рабочих углов резца;
2. Получить навыки в проведении расчетов рабочих углов резцов на примере продольного точения.
ОБЩИЕ СВЕДЕНИЯ
В процессе резания под влиянием ряда факторов происходит изменение углов заточки (статических) резца. К таким факторам можно отнести:
– изменение положения вершин и оси резца по отношению к оси изделия;
– конструктивные особенности обрабатываемой детали, состояния поверхностного слоя после предыдущей обработки;
– скорость резания и подача.
Во всех случаях трансформация углов связана с изменением положения плоскости резания, а в ряде случаев и основной плоскости [2].
В этом случае следует помнить, что плоскость резания – это координатная плоскость, проходящая через касательную к режущей кромке в рассматриваемой ее точке в направлении скорости резания. Основная плоскость – координатная плоскость, проходящая через касательную к режущей кромке в рассматриваемой точке режущей кромки.
На рисунке 3.1 показан случай, когда ось резца неперпендикулярна к оси изделия и отклоняется от перпендикуляра к ней на угол . Тогда действительные (рабочие) углы в плане равны:
;
.
![]() |
Рисунок 3.1 – Схема процесса продольного точения со смещенными осями |
На рисунке 3.2 показан частный случай изменения углов в связи с отклонением вершины резца от линии центров, при (например, при обточке бурта или проточке канавки).
| ||||
| ||||
Рисунок 3.2 – Частные случаи изменения углов в связи с отклонениями вершины резца от линии центров |
|
|
Индивидуальные очистные сооружения: К классу индивидуальных очистных сооружений относят сооружения, пропускная способность которых...
Биохимия спиртового брожения: Основу технологии получения пива составляет спиртовое брожение, - при котором сахар превращается...
Архитектура электронного правительства: Единая архитектура – это методологический подход при создании системы управления государства, который строится...
История развития пистолетов-пулеметов: Предпосылкой для возникновения пистолетов-пулеметов послужила давняя тенденция тяготения винтовок...
© cyberpedia.su 2017-2024 - Не является автором материалов. Исключительное право сохранено за автором текста.
Если вы не хотите, чтобы данный материал был у нас на сайте, перейдите по ссылке: Нарушение авторских прав. Мы поможем в написании вашей работы!