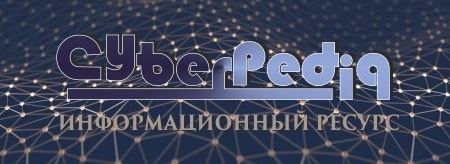
Организация стока поверхностных вод: Наибольшее количество влаги на земном шаре испаряется с поверхности морей и океанов (88‰)...
Автоматическое растормаживание колес: Тормозные устройства колес предназначены для уменьшения длины пробега и улучшения маневрирования ВС при...
Топ:
Отражение на счетах бухгалтерского учета процесса приобретения: Процесс заготовления представляет систему экономических событий, включающих приобретение организацией у поставщиков сырья...
Проблема типологии научных революций: Глобальные научные революции и типы научной рациональности...
Определение места расположения распределительного центра: Фирма реализует продукцию на рынках сбыта и имеет постоянных поставщиков в разных регионах. Увеличение объема продаж...
Интересное:
Наиболее распространенные виды рака: Раковая опухоль — это самостоятельное новообразование, которое может возникнуть и от повышенного давления...
Подходы к решению темы фильма: Существует три основных типа исторического фильма, имеющих между собой много общего...
Национальное богатство страны и его составляющие: для оценки элементов национального богатства используются...
Дисциплины:
![]() |
![]() |
5.00
из
|
Заказать работу |
|
|
1. Определение потребности в инструменте (оснастке)
Потребность предприятия по каждому виду инструментальной оснастки на плановый период определяется по формуле
|
где | По | – | потребность предприятия в инструментальной оснастке каждого вида на плановый период, шт.; |
Р | – | расход оснастки в плановом периоде, шт.; | |
Qоy | – | норматив оборотного фонда на конец планового периода, шт.; | |
Qоф | – | фактическая величина запаса на начало планового периода, шт. |
2. Определение расхода инструмента (оснастки)
2.1. В массовом и крупносерийном производстве расход оснастки может быть определен как
|
где | Р | – | расход оснастки в планируемом периоде, шт.; |
N | – | планируемый объем продукции, шт.; | |
tм | – | норма машинного времени, необходимого для выполнения одной операции данным инструментом, мин; | |
Тизн | – | стойкость инструмента до полного износа инструмента, ч; | |
ky | – | коэффициент преждевременной случайной убыли инструмента. |
|
где | Рнор | – | нормарасхода инструментана 1000 операций, шт.; |
η | – | число одновременно работающих инструментов данного типоразмера, шт. |
Стойкость инструмента до полного износа (норма износа)
|
где | Тизн | – | стойкость инструмента до полного износа, ч; |
mo | – | числопереточек данного инструмента по лимитирующему размеру; | |
tcm | – | стойкость инструмента между двумя переточками, ч; |
|
где | L | – | размер (величина) режущей части инструмента, мм; |
l | – | величина снимаемого слоя при одной переточке инструмента, мм. |
Общий расход инструмента данного типоразмера определяется по формуле
|
|
где | m | – | число наименований изделий, обрабатываемых данным инструментом; |
Σni | – | количество изделий i-гонаименования, подлежащих обработке в плановом периоде, шт. | |
Pi | – | норма расхода инструмента на 1000 операций при обработке i-го изделия, шт./1000 операций. |
2.2. В единичном и мелкосерийном производстве расход инструмента может быть определен по формуле
|
где | Fм | – | годовой машинный фонд времени работы оборудования, ч; |
βпр | – | процент (доля) применяемости данного инструмента в фонде машинного времени, %. |
3. Определение оборотного фонда оснастки (инструмента)
Оборотный фонд оснастки по предприятию (Qобщ) устанавливается на все виды и типоразмеры оснастки и состоит из оборотного фонда цеха (Qц), страхового (Qстр ) и переходящего запасов (Qперех) на центральном инструментальном складе (ЦИС). Оборотный фонд инструмента (оснастки) определяется по формуле
|
3.1. Состав оборотного фонда цеха (Qц) включает оснастку, находящуюся на рабочих местах, в заточке и в ремонте, а также годную оснастку в инструментально-раздаточной кладовой (ИРК).
Количество инструмента на рабочих местах при периодической его доставке по графику определяется как
|
где | ηрм | – | количество инструмента на рабочих местах; |
tп.и | – | периодичность доставки инструмента к рабочим местам, ч; | |
tc | – | периодичность съема инструмента со станка, ч; | |
ηт | – | количество одноименного инструмента, одновременноприменяемого на рабочем месте, шт.; | |
nр.м | – | число рабочих мест, на которых одновременно применяется данный инструмент; | |
kс | – | коэффициент страхового запаса инструмента на рабочем месте (величина kс обычно равна 1, на многорезцовых станках– 2-4. |
|
где | tшт | – | норма времени на операцию, мин; |
tм | – | машинное время, мин; | |
tст | – | стойкость инструмента между двумя переточками, ч. |
|
Периодичность доставки инструмента к рабочим местам выбирается в зависимости от периодичности съема инструмента со станка и принимается равной или кратной продолжительности смены. Число рабочих мест для выполнения производственной программы определяется по формуле
|
где | Nn | – | производственная программа в плановом периоде, шт.; |
Квн | – | коэффициент выполнения норм (1,1–1,2); | |
Fд | – | действительный годовой фонд времени работы оборудования, ч. |
Количество инструмента, находящегося в заточке и в ремонте,
определяется по формуле
|
где | tз | – | цикл заточки или ремонта инструмента, ч. |
3.2. Количество годного инструмента, находящегося в ИРК, определяется по формуле
|
где | рсрд | – | среднедневной расход инструмента, шт., шт./дн.; |
tn | – | периодичность поставки инструмента из ЦИС в ИРК, дн.; | |
Ксз | – | коэффициент страхового запаса инструмента в ИРК. |
Величину складских запасов регулируют по системе максимум-минимум. В соответствии с этой системой устанавливаются три уровня запасов:
максимальный:
|
где | Тпз | – | периодичность пополнения запаса, дн.; |
минимальный, соответствующий величине страхового запаса:
|
Qстр = рсрд × Тз,
где | Тз | – | возможное запаздывание очередной поставки, дн.; |
«точка заказа», соответствующая величине запаса, при котором необходимо сделать заказ на пополнение запаса:
|
где | Тизг | – | время, необходимое для срочного изготовления оснастки или получения ее со стороны, дн. |
4. Расход жесткого мерительного инструмента определяется по формуле
|
где | Nд | – | производственная программа, шт.; |
C | – | количество измерений на одну деталь; | |
i | – | выборочность контроля деталей (в десятичных долях); | |
Низн | – | норма износа мерителя, устанавливаемая по формуле |
|
где | а | – | величина допустимого износа, мк; |
b | – | количество промеров на 1 мк износа; | |
d | – | допустимое число ремонтов до полного износа мерителя. |
5. Расход штампов (Ршт) и сменных деталей штампов (Рдшт) определяется по следующим формулам:
|
|
|
где | Nшт | – | число штампуемых деталей по программе на планируемый период; |
Сшт | – | число ударов при штамповке одной детали; | |
Куд | – | количество ударов штампа до износа (смены) матрицы; | |
m | – | количество допустимых переточек или ремонтов матриц; | |
S | – | норматив стойкости матрицы (количество ударов между двумя переточками); | |
Се | – | число периодов стойкости матрицы; | |
ηшт | – | коэффициент, учитывающий снижение стойкости матрицы после переточки. |
|
где | L | – | величина допустимого стачивания матрицы, мм; |
l | – | слой металла, снимаемый с матрицы при переточке, мм. |
6. Расход приспособлений для станочных работ(укрупненный расчет) определяется по формуле
|
где | Тпр | – | период времени, для которого определяется расход приспособлений, мес.; |
tпр | – | срок службы приспособлений до полного износа, мес.; | |
n | – | число рабочих мест, на которых одновременно применяются данные приспособления. |
1.3. Организация и планирование ремонтного обслуживания
Ремонтный цикл – это повторяющаяся совокупность различных видов планового ремонта, выполняемых в предусмотренной последовательности через установленное равное количество часов оперативного времени работы оборудования, называемое межремонтным периодом.
Структура ремонтного цикла – это перечень ремонтов, входящих в его состав, расположенных в последовательности их выполнения (табл. 2).
Продолжительность ремонтного цикла – это число часов оперативного времени работы оборудования, на протяжении которого производятся все работы, входящие в состав цикла. Простои, связанные с выполнением планового ремонта в цикл не входят.
Таблица 2
Структура ремонтного цикла (фрагмент)
Оборудование | Структура ремонтного цикла | Число ремонтов в цикле | Число плановых осмотров в межремонт-ном периоде | |||
Вид | Класс точности | Категория, т | сред-них | теку-щих | ||
Металлорежущее | Н | до 10т | КР-ТР-ТР-СР-ТР-ТР-КР | |||
П В А С | до 10т | КР-ТР-ТР-СР-ТР-ТР-СР-ТР-ТР-КР |
|
Структура межремонтного обслуживания:
Ое-Сп-Сп-Оч-Р-Сз-Сп-Сп-Оч-Р
Или
Ое + 4Сп + Сз + 2Оч + 2Р,
где | Ое | – | ежемесячный осмотр; |
Сп | – | пополнение смазки; | |
Сз | – | замена смазки; | |
Оч | – | частичный осмотр; | |
Р | – | профилактические регулировки. |
Ремонтный цикл измеряется оперативным временем работы оборудования, зависит от ряда факторов и определяется по формуле (для металлорежущего оборудования):
Тцр = 16800 × Ком × Кпи × Ккт × Кв × Кд × Ккм,
(34)
где | 16800 | – | нормативный ремонтный цикл, ч; |
Ком | – | коэффициент, учитывающий вид обрабатываемого материала; | |
Кпи | – | коэффициент, учитывающий вид применяемого инструмента; | |
Ккт | – | коэффициент, учитывающий класс точности станка; | |
Кв | – | коэффициент, учитывающий возраст станка; | |
Кд | – | коэффициент, учитывающий долговечность станка; | |
Ккм | – | коэффициент, учитывающий категорию массы станка. |
Значения коэффициентов приведены в табл. 3–5.
Межремонтный период Тмр и периодичность технического обслуживания Тто определяются по формулам:
|
|
где | Ктр, Кср, Ко | – | число (количество) соответственно текущих и средних плановых ремонтов и видов межремонтного обслуживания. |
Таблица 3
Значения коэффициентов, входящих в эмпирические формулы
для определения продолжительности ремонтных циклов
и межремонтных периодов (металлорежущие станки)
Коэффициент | Определяемый параметр | Значение коэффициента |
Ком | Обрабатываемый материал: сталь конструкционная прочие материалы | 1,0 0,75 |
Кпи | Материал применяемого инструмента: металл абразив | 1,0 0,8 |
Ккт | Класс точности: Н П В, А, С | 1,0 1,5 2,0 |
Ккм | Категория массы: до 10 т свыше 10 до 100 т свыше 100 т | 1,0 1,35 1,7 |
Таблица 4
Значение коэффициента Кв
Возраст | Класс точности | Порядковый номер планируемого ремонтного цикла | Значение коэффициента |
До 10 лет | Н, П. В, А, С. | 1-й и 2-й 1-й | 1,0 |
Свыше 10 лет | Н П, В, А, С | 2-й и 3-й 2-й | 0,9 |
Н П, В, А, С | 4-й 3-й | 0,8 | |
Н П, В, А, С | 5-й и более 4-й и более | 0,7 |
Таблица 5
Значение коэффициента Кд
Год выпуска оборудования | Значение коэффициента |
До 1975 г. | 0,8 |
С 1975 по 1980 г. | 0,9 |
С 1981 г. | 1,0 |
Трудоемкость и материалоемкость ремонтов и видов технического обслуживания оборудования зависят от его конструктивных особенностей. В основу расчета объема ремонтных работ и их материалоемкости положена трудоемкость (материалоемкость) единицы ремонтной сложности оборудования. Ремонтная сложность устанавливается раздельно для механической, электрической и электронной частей оборудования. В табл. 6 приведена трудоемкость ремонта механической части станка.
|
Таблица 6
Трудоемкость ремонта и полного планового осмотра оборудования
(механическая часть на 1 ремонтную единицу)
Вид работ | Назначение работ | Ремонт | Плановый осмотр | |||
капитальный | средний | текущий | внутри Тцр | перед КР | ||
Станочные | 1. Изготовление заменяемых деталей 2. Восстановление деталей 3. Пригонка при сборке Всего | 14,0 | 3,0 | 2,0 | 0,1 | 0,1 |
Слесарные и прочие работы | 1. 2. 3. Всего | 36,0 | 6,0 | 4,0 | 0,75 | 1,0 |
Итого | 50,0 | 9,0 | 6,0 | 0,85 | 1,1 |
Единица ремонтной сложности механической части – это сложность условного оборудования, трудоемкость капитального ремонта которого в условиях среднего ремонтно-механического цеха составляет 50 нормо-ч.
Единица ремонтной сложности электрической части – 12,5 нормо-ч.
1.4.Организация и планирование транспортного обслуживания
Основой для определения маршрутов межцеховых и внутризаводских перевозок, количества транспортных средств и организации работы транспортного цеха являются грузооборот и грузопотоки предприятия и отдельных цехов.
Грузопоток – объем грузов, перемещаемых в единицу времени между двумя пунктами.
Грузооборот – сумма отдельных грузопотоков, т.е. общее количество грузов, перемещаемое в единицу времени.
Число транспортных средств прерывного (циклического) действия определяется по формуле
|
где | Qc | – | суточный грузооборот, т; |
qтр.с | – | суточная производительность единицы транспортного средства, т. |
Суточный грузооборот определяется по формуле
|
где | Q | – | грузооборот в плановом периоде, т; |
k | – | коэффициент, учитывающий неравномерность грузооборота; | |
Fp | – | число рабочих дней в плановом периоде, дн. |
Суточная производительность транспортного средства определяется по формуле
|
где | q | – | грузоподъемность транспортного средства, т; |
K1 | – | коэффициент использования грузоподъемности транспортного средства; | |
Fд.с | – | суточный фонд времени работы транспорта, мин; | |
К2 | – | коэффициент использования транспортного средства во времени; | |
Тц.т | – | транспортный цикл, мин. |
|
где | Тпр | – | время пробега (в оба конца), мин; |
Тп | – | время погрузки, мин; | |
Тр | – | время разгрузки, мин. |
Число средств непрерывного транспорта определяется по формуле
|
где | Qч | – | часовой грузооборот, т; |
qч | – | часовая производительность транспорта, т/ч. |
|
где | М | – | масса одной грузовой единицы, т; |
V | – | скорость движения транспорта, м/мин; | |
а | – | расстояние между двумя смежными грузами на транспорте, м. |
Для комплексной механизации и автоматизации транспортных и складских операций необходимо широко применять контейнеры и средства пакетирования. Парк контейнеров и средств пакетирования определяется по формуле
|
где | Q | – | грузооборот в плановом периоде, т; |
Кк.н | – | коэффициент, учитывающий потребность в контейнерах в связи с неравномерностью перевозок; | |
Кк.р | – | коэффициент, учитывающий потребность в контейнерах в связи с нахождением транспортных средств в ремонте; | |
qк | – | выработка на один контейнер за расчетный период, т. |
|
где | qк.с | – | статическая нагрузка контейнера, т; |
Fк | – | число календарных дней в расчетном периоде, дн.; | |
Fн | – | время нахождения контейнеров в нерабочем состоянии, дн.; | |
То | – | среднее время оборота контейнера, дн. |
1.5. Организация складского хозяйства
Общая площадь склада определяется по формуле
|
где | Sпол | – | полезная площадь склада, непосредственно занятая хранимыми материалами, м2; |
Кисп | – | коэффициент использования площади склада, учитывающий вспомогательную площадь, площадь проездов, проходов, приема и выдачи материалов, весов, шкафов, стола кладовщика и т.д. |
Полезная площадь рассчитывается в зависимости от способа хранения материалов по следующим формулам:
при напольном хранении в штабелях:
|
где | Zmax | – | величина максимального складского запаса материалов; |
qg | – | допустимая масса груза на 1 м2 площади пола (согласно справочным данным), т, кг; |
|
где | Zmin | – | минимальная норма запаса материала; |
Тц | – | время между двумя поступлениями партий материалов (длительность цикла), дн.; | |
Qр | – | среднедневной расход материала за период исполнения заказа; |
при хранении в стеллажах:
|
где | Sст | – | площадь, занимаемая одним стеллажом, м2; |
nст | – | расчетное количество стеллажей. |
|
где | Vо | – | объем стеллажа, м3 (см3); |
kзп | – | коэффициент заполнения объема стеллажа; | |
qу | – | плотность хранимого материала, т/м3 (г/см3); |
|
где a, b и h – соответственно длина, ширина и высота стеллажа, м.
Принятое количество стеллажей устанавливается после проверки соответствия их числа допустимой нагрузке по формуле
|
ВАРИАНТЫ КОНТРОЛЬНЫХ ЗАДАНИЙ
Задание № 1
1. Раскройте цели и функции службы материально-технического обеспечения на предприятии.
2. В механическом цехе мощность установленного оборудования составляет 448,2 кВт. Средний коэффициент полезного действия электромоторов – 0,9. Средний коэффициент загрузки оборудования – 0,8. Средний коэффициент одновременной работы оборудования – 0,7. Коэффициент полезного действия питающей электрической сети – 0,96. Плановый коэффициент спроса потребителей электроэнергии по цеху 0,6. Режим работы цеха – двухсменный по 8 ч. Потери времени на плановые ремонты составляет 5%. Определите экономию (перерасход) силовой электроэнергии по цеху за год.
3. Определите для станка длительность ремонтного цикла, межремонтного и межосмотрового периода (периодичность технического обслуживания), а также объем ремонтных работ за ремонтный цикл.
Станок металлорежущий повышенной точности, категория по массе средняя, используется для обточки заготовок из конструкционной стали металлическим инструментом. Станок установлен в феврале прошлого года. Ремонтная сложность станка составляет 40 единиц.
В структуре ремонтного цикла для этой категории оборудования пять текущих (плановых) ремонтов и шесть технических (межремонтных) обслуживаний. Режим работы двухсменный, действительный годовой фонд времени станка – 3980 ч, удельный вес оперативного времени в действительном фонде составляет 70%.
Задание № 2
1. Раскройте цели и функции энергетического хозяйства предприятия.
2. Структура ремонтного цикла легкого токарно-револьверного станка следующая: Кр – Тр – Тр – Ср – Тр – Тр – Ср – Тр – Тр – Кр.
Рассчитайте длительность ремонтного цикла и межремонтных периодов станка, выпущенного в 1998 г. и работающего в условиях механического цеха крупносерийного производства на операции обточки алюминиевых втулок.
Станок 7-й категории ремонтной сложности работает в две смены. удельный вес оперативного времени в действительном фонде составляет 75 %. Определите трудоемкость ремонтных работ за ремонтный цикл.
3. Годовая программа выпуска изделия «А» составляет 50 тыс. шт. На изготовление единицы изделия требуется 800 г меди, которая поступает на завод ежеквартально. Страховой (минимальный) запас меди установлен на 20 дней. Склад работает в течение года 255 дней. Хранение меди на складе напольное (в штабелях). Допустимая масса груза на 1 м3 площади пола – 2 т.
Определите общую площадь склада, если коэффициент ее использования составляет 0,65.
Задание № 3
1. Раскройте организационную структуру и задачи отдела материально-технического обеспечения предприятия.
2. Определите затраты на силовою электроэнергию для участка механического цеха за год на основе данных, приведенных в таблице.
Состав оборудования цеха
Станки | Установленная мощность моторов, кВт | сos φ электро- моторов | Коэффициент машинного времени работы станков (Км) |
1. Токарно-винторезные 2. Токарно-револьверные 3. Вертикально-фрезерные 4. Горизонтально- фрезерные 5. Вертикально-сверлильные 6. Радиально-сверлильные 7. Кругло-шлифовальные 8. Плоскошлифовальные 9. Шлифовально-полировальные 10. Зуборезные | 0,8 0,7 0,8 0,8 0,6 0,6 0,7 0,8 0,6 0,7 | 0,7 0,8 0,8 0,8 0,7 0,4 0,7 0,7 0,6 0,6 |
Режим работы участка – двухсменный. Продолжительность рабочей смены – 8 ч. Число рабочих дней в году – 250, потери времени на плановые ремонты составляют 5%.
3. Токарные резцы хранятся на инструментальном складе в клеточных стеллажах. Размеры двустороннего стеллажа 1,2×4 м, высота – 2 м. Годовой расход резцов достигает 100 тыс. шт. Средние размеры токарного резца 30×30 мм, длина 250 мм при плотности стали 8 г/см3. Инструмент поступает ежеквартально партиями со специализированного завода. Страховой запас установлен 20 дней. Коэффициент заполнения стеллажей по объему – 0,3. Вспомогательная площадь составляет 50% общей площади склада. Склад работает 250 дней в году. Допустимая масса груза на 1 м2 площади пола составляет 2 т.
Определите необходимую складскую площадь для хранения токарных резцов.
Задание № 4
1. Поясните методику планирования потребности предприятия (или цеха) в энергоресурсах.
2. Рассчитайте годовой объем ремонтных слесарных работ в механическом цехе (без учета текущего обслуживания), если согласно графикам ремонта в данном году производятся следующие виды ремонтов.
Категория сложности ремонта | |||||
Число ремонтов |
Определите численность ремонтных слесарей в цехе при условии их работы в две смены. Действительный годовой фонд работы рабочего равен 1740 ч.
3. Завод потребляет в год 60 т листового свинца (плотность
11,4 кг/дм3), который поступает через каждые 2 месяца. Гарантийный запас свинца – 20 дней. Склад работает 255 дней в году. Листы свинца хранятся на полочных стеллажах размером 1,8×1,5 м и высотой 2 м. Коэффициент заполнения стеллажей по объему – 0,5. Допустимая масса груза на 1 м2 площади пола – 2 т. Определите необходимую общую площадь склада, если коэффициент ее использования равен 0,7.
Задание № 5
1. Раскройте основные направления экономии энергоресурсов на предприятии.
2. Определите годовой объем ремонтных работ в ремонтно-механическом цехе (РМЦ) предприятия, если согласно графикам ремонта в данном году производятся следующие капитальные ремонты.
Категория сложности ремонта | ||||||
Число ремонтов |
Определите численность ремонтных слесарей и ремонтных слесарей-электриков при условии их работы в одну смену, если действительный годовой фонд работы рабочего равен 1740 ч.
3. Годовой расход черных металлов на предприятии составляет 300 т. Металл поступает периодически в течение года шесть раз. Страховой запас – 20 дней. Склад работает 250 дней в году. Хранение металла на складе – напольное. Допустимая масса груза на 1 м2 площади пола – 2 т.
Определите необходимую общую площадь склада, если коэффициент ее использования равен 0,7.
Задание № 6
1. Раскройте содержание технико-экономических показателей деятельности энергохозяйства предприятия.
2. Длительность ремонтного цикла составляет 9 лет. Структура ремонтного цикла включает, кроме одного капитального ремонта, два средних, а также ряд текущих ремонтов и периодических осмотров. Длительность межремонтного периода – 1 год, время между осмотрами оборудования – 6 мес.
Определите число текущих ремонтов и осмотров и объем ремонтных работ за ремонтный цикл.
3. Годовой расход черных металлов на предприятии составляет 500 т. Металл поступает периодически в течение года шесть раз. Страховой запас – 15 дней. Склад работает 260 дней в году. Хранение металла на складе –
напольное. Допустимая масса груза на 1 м2 площади пола – 2 т.
Определите необходимую общую площадь склада, если коэффициент ее использования равен 0,7.
Задание № 7
1. Раскройте основные направления совершенствования организации энергетического хозяйства на предприятии.
2. Суточный грузооборот двух цехов составляет 14 т. Маршрут пробега автокара двусторонний. Средняя скорость движения автокара по маршруту – 60 м/мин. Грузоподъемность автокара – 1 т. Расстояние между цехами – 300 м. Время погрузки-разгрузки автокара в первом цехе 16 мин, во втором – 18 мин. Коэффициент использования грузоподъемности автокара – 0,8. Коэффициент использования времени работы автокара – 0,85. Режим работы автокара – двухсменный.
Определите необходимое число автокаров и производительность автокара за один рейс.
3. На центральном инструментальном складе строгальные резцы хранятся на клеточных двухсторонних стеллажах размером 1,2×4 и высотой 1,8 м. Средние размеры резца – 35×35 мм, длина 300 мм. Плотность материала резца – 7,8 г/см3. Годовой расход резцов принят 50 тыс. шт. Инструментальный склад снабжается резцами ежеквартально. Гарантийный запас инструмента составляет 15 дней. Коэффициент заполнения стеллажей по объему – 0,4. Склад работает 260 дней в году. Допустимая масса груза
на 1 м2 площади пола 1,8 т.
Определите необходимую площадь для хранения строгальных резцов, если вспомогательные площади составляют 40% общей площади.
Задание № 8
1. Раскройте цели и функции инструментального обслуживания на предприятия.
2. Согласно шахматной ведомости (см. таблицу) на завод со станции железной дороги необходимо перевезти 10000 т груза. Расстояние от железнодорожной станции до завода – 5,6 км. Для перевозки груза будут использованы пятитонные машины. Скорость движения автомашины – 42 км/ч. Время погрузки – 40 мин, время разгрузки – 25 мин. Число рабочих дней в году 255. Режим работы – двухсменный. Продолжительность рабочей смены – 8 ч. Потери времени на плановые ремонты автомашин составляют 4%. Коэффициент использования грузоподъемности автомашины – 0,8.
|
|
История развития хранилищ для нефти: Первые склады нефти появились в XVII веке. Они представляли собой землянные ямы-амбара глубиной 4…5 м...
Индивидуальные очистные сооружения: К классу индивидуальных очистных сооружений относят сооружения, пропускная способность которых...
История создания датчика движения: Первый прибор для обнаружения движения был изобретен немецким физиком Генрихом Герцем...
Семя – орган полового размножения и расселения растений: наружи у семян имеется плотный покров – кожура...
© cyberpedia.su 2017-2024 - Не является автором материалов. Исключительное право сохранено за автором текста.
Если вы не хотите, чтобы данный материал был у нас на сайте, перейдите по ссылке: Нарушение авторских прав. Мы поможем в написании вашей работы!