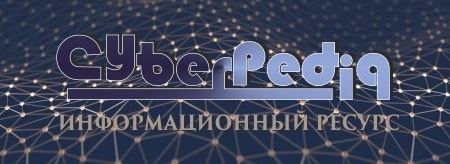
Биохимия спиртового брожения: Основу технологии получения пива составляет спиртовое брожение, - при котором сахар превращается...
Индивидуальные очистные сооружения: К классу индивидуальных очистных сооружений относят сооружения, пропускная способность которых...
Топ:
Особенности труда и отдыха в условиях низких температур: К работам при низких температурах на открытом воздухе и в не отапливаемых помещениях допускаются лица не моложе 18 лет, прошедшие...
Техника безопасности при работе на пароконвектомате: К обслуживанию пароконвектомата допускаются лица, прошедшие технический минимум по эксплуатации оборудования...
Основы обеспечения единства измерений: Обеспечение единства измерений - деятельность метрологических служб, направленная на достижение...
Интересное:
Средства для ингаляционного наркоза: Наркоз наступает в результате вдыхания (ингаляции) средств, которое осуществляют или с помощью маски...
Финансовый рынок и его значение в управлении денежными потоками на современном этапе: любому предприятию для расширения производства и увеличения прибыли нужны...
Искусственное повышение поверхности территории: Варианты искусственного повышения поверхности территории необходимо выбирать на основе анализа следующих характеристик защищаемой территории...
Дисциплины:
![]() |
![]() |
5.00
из
|
Заказать работу |
|
|
Контрольная работа
по дисциплине:
«Метрология, Стандартизация и Сертификация»
9Вариант
Выполнил студент группы РТбз3-5
Калугин ОлегВикторович
Проверил: Бутенко Виктор Иванович
Таганрог 2018
Часть
Задание:
- Изобразить и указать параметры кристаллической ячейки ГПУ.
- Расшифровать химический состав марок сталей: 16ГНМА, 9ХГС,45Х20Н25М.
- Описать технологию получения стали обыкновенного качества.
Решение:
1. Гексагональная плотноупакованная решетка, сокращенно ГПУ, отличается от простой гексагональной тем, что в центр объема каждой второй треугольной призмы помещен дополнительный узел. При этом весь кристалл оказывается составлен из правильных тетраэдров. Это накладывает строгое условие на соотношение между высотой призмы c и длиной ее основания a: c/a = {8/3}1/2. Хотя решетки с другим близким к этому значением c/a часто рассматривают как слабодеформированный вариант ГПУ.
2. 16ГНМА – Сталь жаропрочная низколегированная, содержащая углерод 0,16% - по одному проценту магния, никеля, молибдена. А-без посторонних примесей, шлак.
9ХГС - конструкционная легированная сталь с содержанием углерода 0,9%, хрома, магния и кремния до 1%.
45Х20Н25М –легированная сталь с содержанием углерода до 0,45%, до 0,2% хрома, до 0,25% никеля и до 1% молибдена.
3. Технология получения стали обыкновенного качества.
Передельный или литейный чугун в расплавленном или твердом виде и железосодержащие изделия, полученные прямым восстановлением (губчатое железо), составляют вместе с металлическими отходами и ломом исходные материалы для производства стали. К этим материалам добавляются некоторые шлакообразующие добавки, такие как известь, плавиковый шпат, раскислители (например, ферромарганец, ферросилиций, алюминий) и различные легирующие элементы. Процессы производства стали делятся на два основных способа, а именно: конвертерный процесс, в котором расплавленный передельный чугун в конвертере рафинируют от примесей, продувая его кислородом, и подовый процесс, для осуществления которого используются мартеновские или электрические печи. Конвертерные процессы не требуют внешнего источника тепла. Они применяются в том случае, когда загрузка состоит главным образом из расплавленного передельного чугуна. Окисление некоторых элементов, присутствующих в чугуне (например, углерода, фосфора, кремния и марганца), обеспечивает достаточно тепла, чтобы удерживать сталь в жидком состоянии и даже переплавить добавленный лом. Эти процессы включают в себя такие, при которых чистый кислород вдувается в расплавленный металл (процессы Линца-Донавица: ЛД или ЛДАС, ОБМ, ОЛП, Калдо и другие), и такие процессы, ныне уже устаревшие, при которых используется воздух, иногда обогащенный кислородом (томасовский и бессемеровский процессы). Подовые процессы, однако, требуют внешнего источника тепла. Они применяются, когда исходным материалом служит твердая шихта (например, отходы или лом, губчатое железо и твердый передельный чугун).
|
Двумя основными процессами в этой категории являются мартеновский процесс, при котором нагрев осуществляется при сжигании мазута или газа, и сталеплавильные процессы в дуговых или индукционных печах, где нагрев осуществляется электричеством. Для производства некоторых видов стали могут быть последовательно использованы два различных процесса (дуплекс-процесс). Например, процесс плавки может начаться в мартеновской печи, а закончиться в электропечи; или же сталь, расплавленная в электропечи, может быть слита в специальный конвертер, где обезуглероживание завершается путём вдувания кислорода и аргона в жидкую ванну (процесс, используемый, например, для производства коррозионностойкой стали).
|
Возникло много новых процессов производства сталей специального состава или со специальными свойствами. Эти процессы включают дуговой переплав в вакууме, электронно-лучевую плавку и электрошлаковый переплав. Во всех этих процессах сталь получается из переплавляемого электрода, который при плавлении начинает капать в кристаллизатор. Кристаллизатор может быть изготовлен цельным или его днище может быть отъемным для того, чтобы затвердевшую отливку можно было вынуть снизу. Жидкая сталь, полученная вышеописанными процессами, с дальнейшим рафинированием или без него, сливается в ковш. На этом этапе в неё могут быть добавлены легирующие элементы или раскислители. Процесс также можно провести в вакууме, что обеспечивает снижение содержания газообразных примесей в стали. Стали, полученные этими процессами, подразделяются в соответствии с содержанием в них легирующих элементов на "нелегированные стали" и "легированные стали" (коррозионностойкие стали или другие виды). Далее они подразделяются в соответствии с их индивидуальными свойствами, например, на автоматную сталь, кремнистую электротехническую сталь, быстрорежущую сталь или кремнемарганцовистую сталь. [11]
Бессемеровский способ
Бессемеровским способом перерабатывают чугуны, содержащие мало фосфора и серы и богатые кремнием (не менее 2 %). При продувке кислорода сначала окисляется кремний с выделением значительного количества тепла. Вследствие этого начальная температура чугуна примерно с 1300 °C быстро поднимается до 1500—1600° С. Выгорания 1 % Si обусловливает повышение температуры на 200 °C. Около 1500 °C начинается интенсивное выгорание углерода. Вместе с ним интенсивно окисляется и железо, особенно к концу выгорания кремния и углерода:
· Si + O2 = SiO2
· 2C + O2 = 2CO ↑
· 2Fe + O2 = 2FeO
Образующийся монооксид железа FeO хорошо растворяется в расплавленном чугуне и частично переходит в сталь, а частично реагирует с SiO2 и в виде силиката железа FeSiO3 переходит в шлак:
· FeO + SiO2 = FeSiO3
Фосфор полностью переходит из чугуна в сталь, так P2O5 при избытке SiO2 не может реагировать с основными оксидами, поскольку SiO2 с последними реагирует более энергично. Поэтому фосфористые чугуны перерабатывать в сталь этим способом нельзя.
|
Все процессы в конверторе идут быстро — в течение 10—20 минут, так как кислород воздуха, продуваемый через чугун, реагирует с соответствующими веществами сразу по всему объёму металла. При продувке воздухом, обогащенным кислородом, процессы ускоряются. Монооксид углерода CO, образующийся при выгорании углерода, пробулькивает вверх, сгорает там, образуя над горловиной конвертора факел светлого пламени, который по мере выгорания углерода уменьшается, а затем совсем исчезает, что и служит признаком окончания процесса. Получаемая при этом сталь содержит значительные количества растворенного монооксида железа FeO, который сильно снижает качество стали. Поэтому перед разливкой сталь надо обязательно раскислить с помощью различных раскислителей — ферросилиция, ферромарганца или алюминия:
· 2FeO + Si = 2Fe + SiO2
· FeO + Mn = Fe + MnO
· 3FeO + 2Al = 3Fe + Al2O3
Монооксид марганца MnO как основной оксид реагирует с SiO2 и образует силикат марганца MnSiO3, который переходит в шлак. Оксид алюминия как нерастворимое при этих условиях вещество тоже всплывает наверх и переходит в шлак. Несмотря на простоту и высокую продуктивность, бессемеровский способ теперь не слишком распространен, поскольку он имеет ряд существенных недостатков. Так, чугун для бессемеровского способа должен быть с наименьшим содержанием фосфора и серы, что далеко не всегда возможно. При этом способе происходит очень большое выгорание металла, и выход стали составляет лишь 90 % от массы чугуна, а также расходуется много раскислителей. Серьёзным недостатком является невозможность регулирования химического состава стали.
Бессемеровская сталь содержит обычно менее 0,2 % углерода и используется как техническое железо для производства проволоки, болтов, кровельного железа и т. п.
В настоящее время этот процесс является устаревшим.
Томасовский способ
Томасовским способом перерабатывают чугун с большим содержанием фосфора (до 2 % и более). Основное отличие этого способа от бессемеровского заключается в том, что футеровку конвертера делают из оксидов магния и кальция. Кроме того, к чугуну добавляют ещё до 15 % CaO. Вследствие этого шлакообразующие вещества содержат значительный избыток оксидов с основными свойствами.
|
В этих условиях фосфатный ангидрид P2O5, который возникает при сгорании фосфора, взаимодействует с избытком CaO с образованием фосфата кальция, переходит в шлак:
· 4P + 5O2 = 2P2O5
· P2O5 + 3CaO = Ca3(PO4)2
Реакция горения фосфора является одним из главных источников тепла при этом способе. При сгорании 1 % фосфора температура конвертора поднимается на 150 °C. Сера выделяется в шлак в виде нерастворимого в расплавленной стали сульфида кальция CaS, который образуется в результате взаимодействия растворимого FeS с CaO по реакции:
· FeS + CaO = FeO + CaS
Все последние процессы происходят так же, как и при бессемеровском способе. Недостатки Томасовского способа такие же, как и бессемеровского. Томасовская сталь также малоуглеродная и используется как техническое железо для производства проволоки, кровельного железа и т. п.
В СССР Томасовский способ применяли для переработки фосфористого чугуна с керченского бурого железняка. Получаемый при этом шлак содержит до 20 % P2O5. Его размалывают и применяют как фосфорное удобрение на кислых почвах.
Метод является устаревшим и в настоящее время практически вытеснен из производства.
Мартеновская печь
Мартеновский способ отличается от конверторного тем, что выжигание избытка углерода в чугуне происходит не только за счет кислорода воздуха, но и кислорода оксидов железа, которые добавляются в виде железной руды и ржавого железного лома.
Мартеновская печь состоит из плавильной ванны, перекрытой сводом из огнеупорного кирпича, и особых камер регенераторов для предварительного подогрева воздуха и горючего газа. Регенераторы заполнены насадкой из огнеупорного кирпича. Когда первые два регенератора нагреваются печными газами, горючий газ и воздух вдуваются в печь через раскаленные третий и четвёртый регенераторы. Через некоторое время, когда первые два регенератора нагреваются, поток газов направляют в противоположном направлении и т. д.
Плавильные ванны мощных мартеновских печей имеют длину до 16 м, ширину до 6 м и высоту более 1 м. Вместимость таких ванн достигает 500 т стали. В плавильную ванну загружают железный лом и железную руду. К шихте добавляют также известняк как флюс. Температура печи поддерживается при 1600—1700 °C и выше. Выгорания углерода и примесей чугуна в первый период плавки происходит главным образом за счет избытка кислорода в горючей смеси с теми же реакциями, что и в конверторе, а когда над расплавленным чугуном образуется слой шлака — за счет оксидов железа
· 4Fe2O3 + 6Si = 8Fe + 6SiO2
· 2Fe2O3 + 6Mn = 4Fe + 6MnO
· Fe2O3 + 3C = 2Fe + 3CO ↑
· 5Fe2O3 + 2P = 10FeO + P2O5
|
· FeO + С = Fe + CO ↑
Вследствие взаимодействия основных и кислотных оксидов образуются силикаты и фосфаты, которые переходят в шлак. Сера тоже переходит в шлак в виде сульфида кальция:
· MnO + SiO2 = MnSiO3
· 3CaO + P2O5 = Ca3(PO4)2
· FeS + CaO = FeO + CaS
Мартеновские печи, как и конверторы, работают периодически. После разливки стали печь снова загружают шихтой и т. д. Процесс переработки чугуна в сталь в мартенах происходит относительно медленно в течение 6–7 часов. В отличие от конвертора, в мартенах можно легко регулировать химический состав стали, добавляя к чугуну железный лом и руду в той или иной пропорции. Перед окончанием плавки нагрева печи прекращают, сливают шлак, а затем добавляют раскислители. В мартенах можно получать и легированную сталь. Для этого в конце плавки добавляют к стали соответствующие металлы или сплавы.
В настоящее время работающие мартеновские печи сохранились только в России, Украине и Индии.
Электротермический способ
Электротермический способ имеет перед мартеновским и особенно конверторным целый ряд преимуществ. Этот способ позволяет получать сталь очень высокого качества и точно регулировать её химический состав. Доступ воздуха в электропечь незначительный, поэтому значительно меньше образуется монооксида железа FeO, загрязняющего сталь и снижающего её свойства. Температура в электропечи — не ниже 1650 °C. Это позволяет проводить плавку стали на сильно основных шлаках (которые трудно плавятся), при которой полнее удаляется фосфор и сера. Кроме того, благодаря очень высокой температуре в электропечах можно легировать сталь тугоплавкими металлами — молибденом и вольфрамом. Но в электропечах расходуется очень много электроэнергии — до 800 кВт·ч на 1 т стали. Поэтому этот способ применяют только для получения высококачественной спецстали.
Электропечи бывают разной ёмкости — от 0,5 до 180 т. Футеровку печи выполняют обычно из периклазо-углеродистого огнеупора, а свод печи из магнезито-хромитового огнеупора. Состав шихты может быть разный. Иногда она состоит на 90 % из железного лома и на 10 % из чугуна, иногда в ней преобладает чугун с добавками в определенной пропорции железной руды и железного лома. К шихте добавляют также известняк или известь как флюс. Химические процессы при выплавке стали в электропечах те же, что и в мартенах.
Часть 2.
Задание:
Деталь №4
Исходные данные: d=24 мм, D1=1,5d, D2=2d, L=4d
Материал: Чугун СЧ15. Вид обработки Токарная.
Технология важнейшего производства: технология литейного производства.
Решение:
1. Рекомендуемые значения режимов резания на токарную операцию механической обработки детали V=1,2-2,5 м/с; S=0,2-0,4мм/об, припуск на обработку Z=2-5 мм.
2. Глубина резания
Для D1 =
=1мм
Для D2 =
=1мм
3. Частота вращения шпинделя металлорежущего станка
Для D1n1= =
= 63,7об/мин
Для D2n2= =
=47,8 об/мин
Полученное значение частоты вращения n сравнивается с паспортными данными станка и принимается nф≤n. В работе nф принимают путем округления расчетного значения n в меньшую сторону до нуля в последней цифре, т.е. в нашем случае если n1=63,7об/мин, то nф1=60 об/мин
n2=47,8 об/мин, то nф2=40 об/мин
4. Фактическая скорость резания
Vф1= =
=1,13 м/с
Vф2= =
=1 м/с
5. Основное время обработки
t0= t01+ t02+ t03t04=7+9=16мин
t01= =
=7мин
t02= =
=9мин
Рис. 5. Отлитая втулка послеизвлеченияиз формы: 1 — литниковая чаша, 2 — лнтннковый стояк, 3 — шлакоулоинтель. 4 — питатели,5 — выпор,6 — изделие
Список использованных источников информации:
1. markmet.ru
2. victorborisov.livejournal.com
Bibliofond.ru
Контрольная работа
по дисциплине:
«Метрология, Стандартизация и Сертификация»
9Вариант
Выполнил студент группы РТбз3-5
Калугин ОлегВикторович
Проверил: Бутенко Виктор Иванович
Таганрог 2018
Часть
Задание:
- Изобразить и указать параметры кристаллической ячейки ГПУ.
- Расшифровать химический состав марок сталей: 16ГНМА, 9ХГС,45Х20Н25М.
- Описать технологию получения стали обыкновенного качества.
Решение:
1. Гексагональная плотноупакованная решетка, сокращенно ГПУ, отличается от простой гексагональной тем, что в центр объема каждой второй треугольной призмы помещен дополнительный узел. При этом весь кристалл оказывается составлен из правильных тетраэдров. Это накладывает строгое условие на соотношение между высотой призмы c и длиной ее основания a: c/a = {8/3}1/2. Хотя решетки с другим близким к этому значением c/a часто рассматривают как слабодеформированный вариант ГПУ.
2. 16ГНМА – Сталь жаропрочная низколегированная, содержащая углерод 0,16% - по одному проценту магния, никеля, молибдена. А-без посторонних примесей, шлак.
9ХГС - конструкционная легированная сталь с содержанием углерода 0,9%, хрома, магния и кремния до 1%.
45Х20Н25М –легированная сталь с содержанием углерода до 0,45%, до 0,2% хрома, до 0,25% никеля и до 1% молибдена.
3. Технология получения стали обыкновенного качества.
Передельный или литейный чугун в расплавленном или твердом виде и железосодержащие изделия, полученные прямым восстановлением (губчатое железо), составляют вместе с металлическими отходами и ломом исходные материалы для производства стали. К этим материалам добавляются некоторые шлакообразующие добавки, такие как известь, плавиковый шпат, раскислители (например, ферромарганец, ферросилиций, алюминий) и различные легирующие элементы. Процессы производства стали делятся на два основных способа, а именно: конвертерный процесс, в котором расплавленный передельный чугун в конвертере рафинируют от примесей, продувая его кислородом, и подовый процесс, для осуществления которого используются мартеновские или электрические печи. Конвертерные процессы не требуют внешнего источника тепла. Они применяются в том случае, когда загрузка состоит главным образом из расплавленного передельного чугуна. Окисление некоторых элементов, присутствующих в чугуне (например, углерода, фосфора, кремния и марганца), обеспечивает достаточно тепла, чтобы удерживать сталь в жидком состоянии и даже переплавить добавленный лом. Эти процессы включают в себя такие, при которых чистый кислород вдувается в расплавленный металл (процессы Линца-Донавица: ЛД или ЛДАС, ОБМ, ОЛП, Калдо и другие), и такие процессы, ныне уже устаревшие, при которых используется воздух, иногда обогащенный кислородом (томасовский и бессемеровский процессы). Подовые процессы, однако, требуют внешнего источника тепла. Они применяются, когда исходным материалом служит твердая шихта (например, отходы или лом, губчатое железо и твердый передельный чугун).
Двумя основными процессами в этой категории являются мартеновский процесс, при котором нагрев осуществляется при сжигании мазута или газа, и сталеплавильные процессы в дуговых или индукционных печах, где нагрев осуществляется электричеством. Для производства некоторых видов стали могут быть последовательно использованы два различных процесса (дуплекс-процесс). Например, процесс плавки может начаться в мартеновской печи, а закончиться в электропечи; или же сталь, расплавленная в электропечи, может быть слита в специальный конвертер, где обезуглероживание завершается путём вдувания кислорода и аргона в жидкую ванну (процесс, используемый, например, для производства коррозионностойкой стали).
Возникло много новых процессов производства сталей специального состава или со специальными свойствами. Эти процессы включают дуговой переплав в вакууме, электронно-лучевую плавку и электрошлаковый переплав. Во всех этих процессах сталь получается из переплавляемого электрода, который при плавлении начинает капать в кристаллизатор. Кристаллизатор может быть изготовлен цельным или его днище может быть отъемным для того, чтобы затвердевшую отливку можно было вынуть снизу. Жидкая сталь, полученная вышеописанными процессами, с дальнейшим рафинированием или без него, сливается в ковш. На этом этапе в неё могут быть добавлены легирующие элементы или раскислители. Процесс также можно провести в вакууме, что обеспечивает снижение содержания газообразных примесей в стали. Стали, полученные этими процессами, подразделяются в соответствии с содержанием в них легирующих элементов на "нелегированные стали" и "легированные стали" (коррозионностойкие стали или другие виды). Далее они подразделяются в соответствии с их индивидуальными свойствами, например, на автоматную сталь, кремнистую электротехническую сталь, быстрорежущую сталь или кремнемарганцовистую сталь. [11]
Кислородно-конверторный способ получения стали
По этому способу окисления избыток углерода и других примесей чугуна окисляют кислородом, который продувают сквозь расплавленный чугун под давлением в специальных печах — конверторах. Конвертер представляет собой грушевидную стальную печь, футерованную внутри огнеупорным кирпичом. Он может поворачиваться вокруг своей оси. Ёмкость конвертора 50-60 т. Материалом его футеровки служит либо динас (в состав которого входят главным образом SiO2; имеющий кислотные свойства), или доломитная масса (смесь CaO и MgO), которые получают из доломита MgCO3 • CaCO3. Эта масса имеет основные свойства. В зависимости от материала футеровки печи конверторный способ разделяют на два вида: бессемеровский и томасовский.
Бессемеровский способ
Бессемеровским способом перерабатывают чугуны, содержащие мало фосфора и серы и богатые кремнием (не менее 2 %). При продувке кислорода сначала окисляется кремний с выделением значительного количества тепла. Вследствие этого начальная температура чугуна примерно с 1300 °C быстро поднимается до 1500—1600° С. Выгорания 1 % Si обусловливает повышение температуры на 200 °C. Около 1500 °C начинается интенсивное выгорание углерода. Вместе с ним интенсивно окисляется и железо, особенно к концу выгорания кремния и углерода:
· Si + O2 = SiO2
· 2C + O2 = 2CO ↑
· 2Fe + O2 = 2FeO
Образующийся монооксид железа FeO хорошо растворяется в расплавленном чугуне и частично переходит в сталь, а частично реагирует с SiO2 и в виде силиката железа FeSiO3 переходит в шлак:
· FeO + SiO2 = FeSiO3
Фосфор полностью переходит из чугуна в сталь, так P2O5 при избытке SiO2 не может реагировать с основными оксидами, поскольку SiO2 с последними реагирует более энергично. Поэтому фосфористые чугуны перерабатывать в сталь этим способом нельзя.
Все процессы в конверторе идут быстро — в течение 10—20 минут, так как кислород воздуха, продуваемый через чугун, реагирует с соответствующими веществами сразу по всему объёму металла. При продувке воздухом, обогащенным кислородом, процессы ускоряются. Монооксид углерода CO, образующийся при выгорании углерода, пробулькивает вверх, сгорает там, образуя над горловиной конвертора факел светлого пламени, который по мере выгорания углерода уменьшается, а затем совсем исчезает, что и служит признаком окончания процесса. Получаемая при этом сталь содержит значительные количества растворенного монооксида железа FeO, который сильно снижает качество стали. Поэтому перед разливкой сталь надо обязательно раскислить с помощью различных раскислителей — ферросилиция, ферромарганца или алюминия:
· 2FeO + Si = 2Fe + SiO2
· FeO + Mn = Fe + MnO
· 3FeO + 2Al = 3Fe + Al2O3
Монооксид марганца MnO как основной оксид реагирует с SiO2 и образует силикат марганца MnSiO3, который переходит в шлак. Оксид алюминия как нерастворимое при этих условиях вещество тоже всплывает наверх и переходит в шлак. Несмотря на простоту и высокую продуктивность, бессемеровский способ теперь не слишком распространен, поскольку он имеет ряд существенных недостатков. Так, чугун для бессемеровского способа должен быть с наименьшим содержанием фосфора и серы, что далеко не всегда возможно. При этом способе происходит очень большое выгорание металла, и выход стали составляет лишь 90 % от массы чугуна, а также расходуется много раскислителей. Серьёзным недостатком является невозможность регулирования химического состава стали.
Бессемеровская сталь содержит обычно менее 0,2 % углерода и используется как техническое железо для производства проволоки, болтов, кровельного железа и т. п.
В настоящее время этот процесс является устаревшим.
Томасовский способ
Томасовским способом перерабатывают чугун с большим содержанием фосфора (до 2 % и более). Основное отличие этого способа от бессемеровского заключается в том, что футеровку конвертера делают из оксидов магния и кальция. Кроме того, к чугуну добавляют ещё до 15 % CaO. Вследствие этого шлакообразующие вещества содержат значительный избыток оксидов с основными свойствами.
В этих условиях фосфатный ангидрид P2O5, который возникает при сгорании фосфора, взаимодействует с избытком CaO с образованием фосфата кальция, переходит в шлак:
· 4P + 5O2 = 2P2O5
· P2O5 + 3CaO = Ca3(PO4)2
Реакция горения фосфора является одним из главных источников тепла при этом способе. При сгорании 1 % фосфора температура конвертора поднимается на 150 °C. Сера выделяется в шлак в виде нерастворимого в расплавленной стали сульфида кальция CaS, который образуется в результате взаимодействия растворимого FeS с CaO по реакции:
· FeS + CaO = FeO + CaS
Все последние процессы происходят так же, как и при бессемеровском способе. Недостатки Томасовского способа такие же, как и бессемеровского. Томасовская сталь также малоуглеродная и используется как техническое железо для производства проволоки, кровельного железа и т. п.
В СССР Томасовский способ применяли для переработки фосфористого чугуна с керченского бурого железняка. Получаемый при этом шлак содержит до 20 % P2O5. Его размалывают и применяют как фосфорное удобрение на кислых почвах.
Метод является устаревшим и в настоящее время практически вытеснен из производства.
Мартеновская печь
Мартеновский способ отличается от конверторного тем, что выжигание избытка углерода в чугуне происходит не только за счет кислорода воздуха, но и кислорода оксидов железа, которые добавляются в виде железной руды и ржавого железного лома.
Мартеновская печь состоит из плавильной ванны, перекрытой сводом из огнеупорного кирпича, и особых камер регенераторов для предварительного подогрева воздуха и горючего газа. Регенераторы заполнены насадкой из огнеупорного кирпича. Когда первые два регенератора нагреваются печными газами, горючий газ и воздух вдуваются в печь через раскаленные третий и четвёртый регенераторы. Через некоторое время, когда первые два регенератора нагреваются, поток газов направляют в противоположном направлении и т. д.
Плавильные ванны мощных мартеновских печей имеют длину до 16 м, ширину до 6 м и высоту более 1 м. Вместимость таких ванн достигает 500 т стали. В плавильную ванну загружают железный лом и железную руду. К шихте добавляют также известняк как флюс. Температура печи поддерживается при 1600—1700 °C и выше. Выгорания углерода и примесей чугуна в первый период плавки происходит главным образом за счет избытка кислорода в горючей смеси с теми же реакциями, что и в конверторе, а когда над расплавленным чугуном образуется слой шлака — за счет оксидов железа
· 4Fe2O3 + 6Si = 8Fe + 6SiO2
· 2Fe2O3 + 6Mn = 4Fe + 6MnO
· Fe2O3 + 3C = 2Fe + 3CO ↑
· 5Fe2O3 + 2P = 10FeO + P2O5
· FeO + С = Fe + CO ↑
Вследствие взаимодействия основных и кислотных оксидов образуются силикаты и фосфаты, которые переходят в шлак. Сера тоже переходит в шлак в виде сульфида кальция:
· MnO + SiO2 = MnSiO3
· 3CaO + P2O5 = Ca3(PO4)2
· FeS + CaO = FeO + CaS
Мартеновские печи, как и конверторы, работают периодически. После разливки стали печь снова загружают шихтой и т. д. Процесс переработки чугуна в сталь в мартенах происходит относительно медленно в течение 6–7 часов. В отличие от конвертора, в мартенах можно легко регулировать химический состав стали, добавляя к чугуну железный лом и руду в той или иной пропорции. Перед окончанием плавки нагрева печи прекращают, сливают шлак, а затем добавляют раскислители. В мартенах можно получать и легированную сталь. Для этого в конце плавки добавляют к стали соответствующие металлы или сплавы.
В настоящее время работающие мартеновские печи сохранились только в России, Украине и Индии.
Электротермический способ
Электротермический способ имеет перед мартеновским и особенно конверторным целый ряд преимуществ. Этот способ позволяет получать сталь очень высокого качества и точно регулировать её химический состав. Доступ воздуха в электропечь незначительный, поэтому значительно меньше образуется монооксида железа FeO, загрязняющего сталь и снижающего её свойства. Температура в электропечи — не ниже 1650 °C. Это позволяет проводить плавку стали на сильно основных шлаках (которые трудно плавятся), при которой полнее удаляется фосфор и сера. Кроме того, благодаря очень высокой температуре в электропечах можно легировать сталь тугоплавкими металлами — молибденом и вольфрамом. Но в электропечах расходуется очень много электроэнергии — до 800 кВт·ч на 1 т стали. Поэтому этот способ применяют только для получения высококачественной спецстали.
Электропечи бывают разной ёмкости — от 0,5 до 180 т. Футеровку печи выполняют обычно из периклазо-углеродистого огнеупора, а свод печи из магнезито-хромитового огнеупора. Состав шихты может быть разный. Иногда она состоит на 90 % из железного лома и на 10 % из чугуна, иногда в ней преобладает чугун с добавками в определенной пропорции железной руды и железного лома. К шихте добавляют также известняк или известь как флюс. Химические процессы при выплавке стали в электропечах те же, что и в мартенах.
Часть 2.
Задание:
Деталь №4
Исходные данные: d=24 мм, D1=1,5d, D2=2d, L=4d
Материал: Чугун СЧ15. Вид обработки Токарная.
Технология важнейшего производства: технология литейного производства.
Решение:
1. Рекомендуемые значения режимов резания на токарную операцию механической обработки детали V=1,2-2,5 м/с; S=0,2-0,4мм/об, припуск на обработку Z=2-5 мм.
2. Глубина резания
Для D1 =
=1мм
Для D2 =
=1мм
3. Частота вращения шпинделя металлорежущего станка
Для D1n1= =
= 63,7об/мин
Для D2n2= =
=47,8 об/мин
Полученное значение частоты вращения n сравнивается с паспортными данными станка и принимается nф≤n. В работе nф принимают путем округления расчетного значения n в меньшую сторону до нуля в последней цифре, т.е. в нашем случае если n1=63,7об/мин, то nф1=60 об/мин
n2=47,8 об/мин, то nф2=40 об/мин
4. Фактическая скорость резания
Vф1= =
=1,13 м/с
Vф2= =
=1 м/с
5. Основное время обработки
t0= t01+ t02+ t03t04=7+9=16мин
t01= =
=7мин
t02= =
=9мин
|
|
Археология об основании Рима: Новые раскопки проясняют и такой острый дискуссионный вопрос, как дата самого возникновения Рима...
Автоматическое растормаживание колес: Тормозные устройства колес предназначены для уменьшения длины пробега и улучшения маневрирования ВС при...
Особенности сооружения опор в сложных условиях: Сооружение ВЛ в районах с суровыми климатическими и тяжелыми геологическими условиями...
Адаптации растений и животных к жизни в горах: Большое значение для жизни организмов в горах имеют степень расчленения, крутизна и экспозиционные различия склонов...
© cyberpedia.su 2017-2024 - Не является автором материалов. Исключительное право сохранено за автором текста.
Если вы не хотите, чтобы данный материал был у нас на сайте, перейдите по ссылке: Нарушение авторских прав. Мы поможем в написании вашей работы!