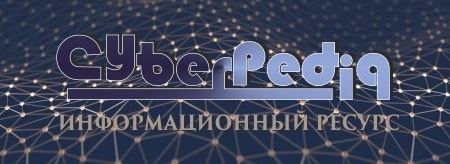
Таксономические единицы (категории) растений: Каждая система классификации состоит из определённых соподчиненных друг другу...
Археология об основании Рима: Новые раскопки проясняют и такой острый дискуссионный вопрос, как дата самого возникновения Рима...
Топ:
Характеристика АТП и сварочно-жестяницкого участка: Транспорт в настоящее время является одной из важнейших отраслей народного...
Определение места расположения распределительного центра: Фирма реализует продукцию на рынках сбыта и имеет постоянных поставщиков в разных регионах. Увеличение объема продаж...
Интересное:
Национальное богатство страны и его составляющие: для оценки элементов национального богатства используются...
Лечение прогрессирующих форм рака: Одним из наиболее важных достижений экспериментальной химиотерапии опухолей, начатой в 60-х и реализованной в 70-х годах, является...
Распространение рака на другие отдаленные от желудка органы: Характерных симптомов рака желудка не существует. Выраженные симптомы появляются, когда опухоль...
Дисциплины:
![]() |
![]() |
5.00
из
|
Заказать работу |
|
|
Пластмассы в твердом состоянии (без нагрева) подвергают в основном двум видам обработки: разделительной штамповке и обработке резанием.
Разделительная штамповка. Этим способом получают разнообразные изделия из листовых материалов для радиотехнических, электронных и других приборов.
Листовые пластмассы раскраивают ножницами различных конструкций или распиливают специальными пилами с применением особых фрез и карборундовых абразивных кругов. Фрезами и абразивными кругами режут толстолистовые материалы (S^2,5 мм). Листы толщиной до 2,5 мм раскраивают ножницами и разрезными штампами.
Технология вырубки, пробивки, зачистки и других разделительных операций отличается от технологии резки металлических материалов.
Как правило, при резке материалов повышенной и средней хрупкости (органическое стекло, текстолит и др.) для уменьшения дефектов и улучшения поверхности среза применяют специальную форму режущих кромок ножа и сильный прижим материала по контуру среза.
Специальная форма режущих кромок (заостренный передний угол) позволяет концентрировать давление на небольшой площади, уменьшая тем самым возможности появления трещин. Чтобы получить качественную поверхность, детали вырубают с припуском для зачистки поверхности среза в специальных зачистных штампах.
Мягкие и упругие волокнистые материалы разрезают на деревянных или фибровых подкладках с помощью контурных ножей (просечек), имеющих конфигурацию, соответствующую форме вырубаемой детали. При этом нож Должен входить в материал до соприкосновения с подкладкой.
Обработка пластмасс резанием. Применяют для проведения отделочных и доводочных операций после предварительного формования и для изготовления машино- и приборостроительных деталей из заготовок. В единичном и мелкосерийном производстве экономически нецелесообразно применять методы прессования, литья и другие ввиду высокой стоимости и сложности изготовления прессформ. В этом случае заготовкой для механической обработки является листовой или прутковый материал. Однако в тех случаях, когда это возможно, следует избегать или уменьшать механическую обработку, так как нарушается поверхностная смоляная пленка. Это приводит к уменьшению предела прочности, увеличению способности водо- и маслопогло- щения.
|
При прессовании, литье и других методах формования наблюдаются значительные колебания усадки материалов, что снижает получаемую точность размеров. Поэтому для получения высокого класса точности необходимо в ряде случаев применять механическую обработку. Кроме того, методами резания удаляют литниковую систему, зачищают заусенцы, получают отверстия малых диаметров, мелкие резьбы и т. д.
Особенности физико-механических свойств пластмасс и специфика их строения существенно влияют на технологию обработки, конструкцию режущего инструмента и приспособлений.
Низкая теплопроводность пластмасс приводит к концентрации тепла, выделяющегося при резании. В результате этого происходит интенсивный нагрев инструмента, размягчение и оплавление деталей из термопластов, обугливание и прижоги реактопластов.
Процесс стружкообразования при обработке пластмасс зависит от природы и физико-механических свойств пластмасс, геометрии инструмента и режимов резания,
Смолы, входящие в состав пластмасс, при нагреве размягчаются и обволакивают рабочую поверхность инструмента, что затрудняет отвод стружки и ухудшает качество получаемой поверхности.
При обработке пластмасс, имеющих в составе наполнителя кварцевый порошок и стекловолокно, в стружке образуются высокоабразивные частицы, что приводит к быстрому износу режущего инструмента. При обработке стеклопластиков образуется тонкая пыль, загрязняющая и изнашивающая станки, а также загрязняющая атмосферу цеха.
|
Пластмассы при обработке с малыми скоростями и большими глубинами резания ведут себя как хрупкое тело: появляются трещины, сколы.
Большое разнообразие полимерных материалов обусловливает значительное колебание оптимальных режимов резания и геометрии инструмента.
Наибольшую производительность и наибольшую стойкость обеспечивает инструмент из твердых сплавов, несколько меньшую — инструмент из быстрорежущей стали и еще более низкую — инструмент из углеродистых инструментальных сталей.
Задний угол а выбирают равным 12—20°, т. е. несколько больший, чем при обработке металлов. Это улучшает условия резания и повышает стойкость инструмента.
Вследствие низкого сопротивления срезу передний угол выбирают значительно большим (15—20°), чем при резании металлов.
Канавки для отвода стружки делают более емкими и полируют во избежание прилипания стружки.
При обработке отверстий и получении резьб следует применять инструмент несколько большего диаметра (на 0,04—0,1 мм) для компенсации усадки.
Обработку пластмасс можно проводить на обычном металлорежущем и деревообрабатывающем оборудовании.
Точение. Точением хорошо обрабатывают винипласт, органическое стекло, полиэтилен, фторопласты, слоистые пластики. Для точения используют универсальные быстроходные металлорежущие станки, токарные и револьверные. Режущий инструмент изготавливают из твердых сплавов (ВК6, ВК8), быстрорежущих сталей (Р9, Р18) и реже из углеродистых (У10А, У12А). Геометрия заточки резцов для обработки термопластов (Л) и реактопластов пластмасс (В) следующая:
а в
................................ 15—20° 10—20°
а................................................................ <20° 10—20°
Для всех случаев А = 0°; <р — 45°.
Глубину резания и подачу выбирают в зависимости от припусков на обработку и требуемой чистоты поверхности. Точение проводят на больших скоростях, но с небольшой подачей. Припуск снимают за один-два прохода. На второй проход рекомендуется оставлять припуск не более 0,5—1,0 мм.
Твердосплавной инструмент допускает скорости резания в два-три раза выше, чем инструмент из быстрорежущей стали.
|
Возможное образование сколов предупреждается фаской со стороны входа инструмента или обработкой деталей, собранных в пакет.
При обработке термопластов охлаждение проводят эмульсией или водой, а при обработке термореактивных пластмасс — сжатым воздухом.
Фрезерование. Применяют для изготовления деталей из блочных термопластов и слоистых пластмасс, удаления литников, получения сложных контуров детали после прессования или литья, получения пазов различной конфигурации, зубонарезания и т. д.
Для фрезерования используют быстроходные ме- талло- и деревообрабатывающие станки, а при массовом производстве экономически целесообразно применять специальные фрезерные станки.
При фрезеровании на обрабатываемой поверхности могут появляться задиры, трещины и прижоги, возможно отслаивание материала, скалывание кромок и обламывание краев листа. Учитывая это, во избежание появления брака необходимо соблюдать ряд правил:
1) для предотвращения выкрашивания и обламывания толщина кромки изделия должна быть не менее 0,1 мм;
2) при фрезеровании слоистых пластмасс следует применять попутное фрезерование; 3) фрезеруемую деталь необходимо плотно прижимать к опорной базе и жестко закреплять на станке и в приспособлении; 4) обрабатываемый участок должен иметь плотный контакт по всей поверхности с опорной поверхностью приспособления; 5) фрезерование пластмасс лучше всего проводить фрезами со спиральным зубом. Угол наклона зуба 20—55° к оси фрезы.
Конструкцию фрезы и геометрию, заточки режущих лезвий выбирают в зависимости от обрабатываемого материала, конструкции детали и режима резания. Для фрезерования термопластов фрезы изготавливают из углеродистой стали, а для термореактивных пластмасс— из быстрорежущей стали или с пластинками твердого сплава. Углы заточки: Y=10-i-25o; а=15-т-30°. При фрезеровании пазов необходимо затачивать режущие лезвия и торец инструмента для предотвращения подгорания или сплавления обрабатываемых слоев материала детали.
Фрезерование проводят в два прохода с глубиной резания менее 3 мм, оставляя на чистовой проход 0,5 мм.
|
При. фрезеровании для охлаждения инструмента применяют сжатый воздух, а для некоторых видов термопластов допускается применение эмульсии.
Сверление. При сверлении отверстий в пластмассовых деталях большое значение имеет правильный выбор конструкции и геометрии сверл, режимов резания, способов охлаждения инструмента и зоны обработки.
Для сверления пластмасс применяют спиральные специальные и перовые сверла.
При получении отверстий в термопластах стандартными сверлами (рис. 434, а) возможно их заедание..Во избежание этого необходимо применять следующую геометрию сверл: угол при вершине 2Ф около 70°, задний угол а==4ч-8°, угол наклона канавки со — 15— 17°. Кроме того, такой угол наклона канавки снижает нагрев детали и обеспечивает хороший отвод стружки.
При получении отверстий в термореактивных пластмассах и листовых слоистых пластиках желательно применять сверла из быстрорежущей стали (рис.434,б). Геометрия сверл в этом случае должна быть: 2<р = =50—60°, а = 14-М 6°, (о = 10°. Стружечная канавка должна быть широкой и глубокой.
Наилучшее качество обработки получается при применении перовых сверл, и спиральных сверл с широкой, хорошо полированной канавкой.
При сверлении глубоких отверстий (рис. 434, в) во избежание прожога следует периодически вынимать
инструмент, охлаждать его й очищать от стружки. Охлаждение проводят сжатым воздухом, а для стеклотек- столитов и фенопластов возможно применение 5%-ного раствора эмульсола в воде.
Отверстия с диаметром больше 6—9 мм получают за два прохода: предварительное сверление проводят на диаметр не менее 0,5 от окончательного размера.
Нарезание резьбы. Наружные и внутренние резьбы нарезают в пластмассовых заготовках (стержневых, листовых, блочных) и в готовых деталях, полученных формованием. Наружные резьбы нарезают резцами, плашками, фрезами, внутренние — азотированными или хромированными метчиками.
Резьбы большого и среднего диаметра нарезают на токарно-винторезных станках со смазывающе-охлажда- ющей жидкостью из смеси парафинового масла (60%) и керосина (40%). Режимы резания аналогичны режимам для латуни и стали, но глубина резания должна быть меньше 0,1—0,2 мм. С увеличением глубины резания возможно выкрашивание или появление трещин на деталях малой толщины.
Для нарезания внутренней резьбы применяют стандартные метчики из быстрорежущей стали с отрицательным передним углом у——(5-4-10°). Такой угол уменьшает заедание метчика при вывертывании. Рекомендуется применять комплект из двух-трех метчиков и метчики с резьбой через шаг. Чтобы получить чистую и гладкую поверхность, следует чаще очищать метчик от стружки и смазывать маслом или пчелиным воском.
|
При нарезании резьбы в деталях из наполненных термопластов и слоистых пластмасс наблюдается усадка на 0,05—0,15 мм. В соответствии с этим диаметр метчика должен быть больше номинального диаметра резьбы на величину усадки.
В слоистых пластиках резьбу следует нарезать перпендикулярно слоям, иначе возможно расслаивание.
![]() |
![]() |
Шлифование. Шлифование изделий из термореак»
тивных пластмасс осуществляют абразивными кругами с мягкой связкой зернистостью 30—40. Для удаления грата и заусенцев, для получения более чистой поверхности после шлифования абразивными кругами применяют обработку наждачными полотнами или наждачной бумагой.
Шлифование изделий из термопластичных пластмасс проводят фланелевыми или суконными кругами с пастой из отмученной пемзы с водой. Органическое стекло шлифуют специальными пастами или наждачной бумагой с зернистостью абразива 150—250.
Чистота обработанной поверхности зависит от толщины снимаемой стружки, материала инструмента, режима обработки и т. д. Глубину резания (поперечную подачу) выбирают для чернового шлифования в пределах t=0,07-1-0,2 мм, а для чистового шлифования t=0,01-г-0,05 мм. Зернистость абразива для черновой и чистовой обработки должна составлять соответственно 16—40 и 80—140. Шлифование, проводят с высокими Скоростями, равными 20—40 м/с, так как при меньших скоростях шкурки быстро замасливаются. Во избежание прижогов материала продолжительность контакта детали с кругом должна быть минимальной (не более 1,0—1,5 с).
Полирование. Пластмассовые детали подвергают полированию для удаления следов зачистки или механической обработки (рисок, царапин), выведения матовых пятен, придания поверхностям гладкого блестящего вида. При полировании снимают очень тонкий слой пластмассы. В промышленности наибольшее распространение получило полирование в галтовочных барабанах и на полировальных станках специальными кругами.
Для мелких деталей применяют полирование в галтовочных барабанах. В галтовочный барабан загружают хорошо очищенные от загрязнений пластмассовые детали и полировальный состав. При сухом способе полировальным составом является пемза тонкого помола или опилки с мелом, пропитанные машинным и вазелиновым маслами. Процесс полирования продолжается 2—3 ч при скорости вращения барабана 20—80 об/мин. Детали отделяют от полировального состава на ситах, промывают и сушат. При мокром способе полировальный состав состоит из пемзы тонкого помола с водой (100 г пемзы на 10 л воды). Процесс протекает более интенсивно, продолжается 1—2 ч, при этом снимается больший припуск.
Полирование проводят на полировальных станках хлопчатобумажными, байковыми и суконными кругами, а окончательное полирование — кругами из бязи, байки или муслина. На предварительных операциях применяют пасту ГОИ для термореактивных пластмасс и ВИАМ-2 для термопластичных. Матерчатые круги имеют диаметр 200—400 мм и толщину 60—100 мм. При полировании реактопластов скорость вращения полировального круга составляет 1500—2000 об/мин, а для термопластов 1000—1500 об/мин (для предупреждения сильного нагрева деталей).
При полировании на станках во избежание перегрева, прижога и изменения цвета поверхности детали нельзя, допускать сильного прижима детали к кругу,
|
|
Типы сооружений для обработки осадков: Септиками называются сооружения, в которых одновременно происходят осветление сточной жидкости...
Типы оградительных сооружений в морском порту: По расположению оградительных сооружений в плане различают волноломы, обе оконечности...
Биохимия спиртового брожения: Основу технологии получения пива составляет спиртовое брожение, - при котором сахар превращается...
Индивидуальные очистные сооружения: К классу индивидуальных очистных сооружений относят сооружения, пропускная способность которых...
© cyberpedia.su 2017-2024 - Не является автором материалов. Исключительное право сохранено за автором текста.
Если вы не хотите, чтобы данный материал был у нас на сайте, перейдите по ссылке: Нарушение авторских прав. Мы поможем в написании вашей работы!