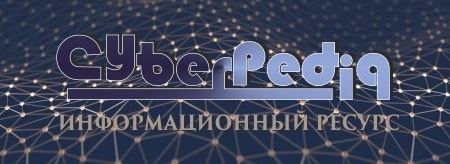
Механическое удерживание земляных масс: Механическое удерживание земляных масс на склоне обеспечивают контрфорсными сооружениями различных конструкций...
Типы оградительных сооружений в морском порту: По расположению оградительных сооружений в плане различают волноломы, обе оконечности...
Топ:
Определение места расположения распределительного центра: Фирма реализует продукцию на рынках сбыта и имеет постоянных поставщиков в разных регионах. Увеличение объема продаж...
Характеристика АТП и сварочно-жестяницкого участка: Транспорт в настоящее время является одной из важнейших отраслей народного хозяйства...
Эволюция кровеносной системы позвоночных животных: Биологическая эволюция – необратимый процесс исторического развития живой природы...
Интересное:
Наиболее распространенные виды рака: Раковая опухоль — это самостоятельное новообразование, которое может возникнуть и от повышенного давления...
Национальное богатство страны и его составляющие: для оценки элементов национального богатства используются...
Инженерная защита территорий, зданий и сооружений от опасных геологических процессов: Изучение оползневых явлений, оценка устойчивости склонов и проектирование противооползневых сооружений — актуальнейшие задачи, стоящие перед отечественными...
Дисциплины:
![]() |
![]() |
5.00
из
|
Заказать работу |
|
|
Комплексный экзамен по ПМ 01.
Билет № 15
Вопрос 2
Сварочными материалами называют расходные материалы, используемые при сварке.
Сварочные материалы могут выполнять следующие функции:
· обеспечение необходимых геометрических размеров сварного шва;
· получение металла сварного шва с требуемым химическим составом и свойствами;
· обеспечение защиты расплавленного металла от воздействия воздуха – газовой, шлаковой или газошлаковой;
· обеспечение стабильности процесса сварки;
· удаление вредных примесей из металла шва.
Виды сварочных материалов
Сварочные материалы | Разновидности |
Сварочные электроды и присадочные прутки | плавящиеся электроды с покрытием (с кислым, основным, рутиловым, целлюлозным, смешанным покрытием), неплавящиеся электроды |
Сварочная проволока | сплошная, порошковая, активированная |
Флюсы | защитные и электропроводные |
Газы | защитные (инертные и активные), горючие газы и газы, поддерживающие горение |
Керамические подкладки | для сварки стыковых швов, угловых и тавровых швов, всепозиционные, круглые и др. виды |
Сварочные электроды и проволока обеспечивают подачу электрического питания в зону сварки для нагрева. Плавящиеся покрытые электроды, порошковая и активированная проволока, защитный флюс для дуговой сварки содержат специальные компоненты, которые могут предназначаться для защиты металла от воздуха, поддержания стабильности процесса сварки, получения необходимого химического состава металла шва и т.п. Присадочный пруток вводится в сварной шов при сварке.
Основная роль защитных газов – обеспечение газовой защиты расплавленного металла от воздуха. К защитным газам относятся инертные (аргон, гелий и их смеси) и активные газы (углекислый газ и его смеси). Инертные газы не вступают в химические реакции с металлом и в нем практически не растворяются. Активные газы вступают в химические реакции с металлом или растворяются в нем.
|
Горючие газы и газы, поддерживающие горение применяются при газовой сварке и резке. К ним относятся ацетилен, пропан-бутановые смеси, метилацетилен-алленовая фракция (МАФ), водород, а также поддерживающий горение кислород.
Керамические подкладки используют для обеспечения высококачественного шва и формирования обратного валика.
Сварочные материалы (электроды, проволоку, присадочные прутки) также подразделяют по типу свариваемых сталей и металлов: для сварки углеродистых сталей, никзолегированных сталей, нержавеющих сталей, алюминия, меди, чугуна и т.п.
Билет 16
Вопрос 3
Сварочная проволока |
Основные виды сварочной проволоки – сплошного сечения, порошковая, активированная.
Сварочная проволока сплошного сечения
Сварочная проволока сплошного сечения применяется для полуавтоматической и автоматической сварки, а также для изготовления электродов и присадочных прутков.
Химический состав и диаметр проволоки для сварки сталей регламентирует ГОСТ 2246-70. Проволока для наплавки выпускается по ГОСТ 10543-75, проволока из меди и сплавов – по ГОСТ 16130-72, проволока из алюминия и сплавов – по ГОСТ 7871-75. Наиболее распространенной является стальная проволока. Она выпускается следующих диаметров (мм): 0,3; 0,5; 0,8; 1,0; 1,2; 1,4; 1,6; 2,0; 2,5; 3,0; 4,0; 5,0; 6,0; 8,0; 10,0; 12,0.
Пример обозначения: 3 Св08ХСМФА-ВИ-Э ГОСТ 2246-70.
Порошковая сварочная проволока
Порошковая сварочная проволока представляет собой трубчатую проволоку, заполненную порошкообразным наполнителем. Отношение массы порошка к массе металлической оболочки составляет от 15 до 40%. Конструкция порошковой проволоки может быть разной – простой трубчатой, с различными загибами оболочки, двухслойной (см. рисунок).
![]() |
ОБОЗНАЧЕНИЯ ЛЕГИРУЮЩИХ ЭЛЕМЕНТОВ
|
|
В ГОСТ приняты следующие буквенные обозначения легирующих элементов, входящих в марки стали.
А - азот
М - молибден
Ю - алюминий
Н - никель
Р - бор
Б - ниобий
Ф - ванадий
Е - селен
В - вольфрам
Т - титан
К - кобальт
У - углерод
С - кремний
П - фосфор
Г - марганец
Х - хром
Д - медь
Ц - цирконий
Влияние легирующих элементов:
Никель сообщает стали коррозионную стойкость, высокую прочность и пластичность, увеличивает прокаливаемость, повышает сопротивление удару.
Вольфрам образует в стали очень твердые соединения - карбиды, резко увеличивающие твердость и красностойкость стали. Вольфрам препятствует росту зерен при нагреве, способствует устранению хрупкости при отпуске.
Ванадий повышает твердость и прочность, измельчает зерно. Увеличивает плотность стали.
Кремний в количестве свыше 1% оказывает особое влияние на свойства стали: содержание 1-1.5% Si увеличивает прочность, причем вязкость сохраняется. При большем содержании кремния увеличиваются электросопротивление и магнитопроницаемость. Кремний увеличивает также упругость, окалийность.
Марганец при содержании свыше 1% увеличивает твердость, износоустойчивость, стойкость против ударных нагрузок, не уменьшая пластичности.
Кобальт повышает жаропрочность, магнитные свойства, увеличивает сопротивление удару.
Молибден увеличивает красностойкость, упругость, предел прочности на растяжение, антикоррозионные свойства и сопротивление окислению при высоких температурах.
Титан повышает прочность и плотность стали, способствует измельчению зерна, улучшает обрабатываемость и сопротивление коррозии.
Ниобий улучшает кислотостойкость и способствует уменьшению коррозии в сварных конструкциях.
Алюминий повышает жаростойкость и окалийность.
Медь увеличивает антикоррозионные свойства.
Церий повышает прочность и пластичность.
Цирконий позволяет получать сталь с заранее заданной зернистостью.
Лантан, церий, неодим уменьшают пористость, способствуют уменьшению содержания серы в стали, улучшают качество поверхности, измельчает зерно.
|
Билет № 17
Вопрос 2
Данная классификация приведена в официальном документе - ГОСТ 19521-74. Она подразумевает деление технологии на три типа:
· Термический. По названию понятно, что слияние двух заготовок происходит в результате точечного повышения их температуры, которое вызывает плавление и нарушение структуры металла. За счет этого частицы одной заготовки перемешиваются со второй. После окончания воздействия происходит практически мгновенное застывание. В данный вид включают дуговую, термитную, шлаковую, газовую, лучевую, лазерную и пр.
· Механический. В данном случае активно применяется воздействие высоким давлением на место спайки. Такая сварка обычно называется холодной, так как температура заготовок практически не меняется. Существуют различные технологии, подразумевающие воздействие трением, ультразвуковыми волнами, магнитными импульсами и пр.
· Термомеханический. Представляет собой промежуточный вариант между указанными выше. При его использовании на заготовки воздействуют как механическими, так и температурными методами. Т. е. происходит нагрев обрабатываемого участка с помощью тепловой энергии, а затем давлением объединяют ослабленные структуры заготовок. Хорошо знакомы с данным классом сварки кузнецы. Также его применяют при прокате металла, прессовании, выдавливании и т. д. Существуют различные подвиды: индукционный, газовый, диффузионный, дуговой.
На каждый из классов существует своя технология обработки, которую изучают в колледжах на соответствующих направлениях. Их выпускники обычно занимаются и ремонтом сварочного оборудования.
Билет № 17
Вопрос 3
Сварка балок составного двутаврового сечения.
Составные двутавровые балки отличаются наличием швов значительной протяженности и большого сечения. Поэтому для выполнения поясных швов рекомендуется автоматическая сварка под флюсом с расположением швов «в лодочку».
Для того, чтобы избежать больших остаточных деформаций двутавровых сечений — кривизны и винтообразности, рекомендуется вести сварку всех поясных швов в одном направлении и соблюдать порядок их наложения, показанный на рис.9.
Рис.9 Последовательность сварки поясных швов двутавровых балок:
а - балки симметричного сечения большой высоты; б - балки симметричного сечения небольшой высоты из тонколистового металла; в - балки симметричного сечения небольшой высоты из толстолистового металла; г - балки с развитым верхним поясом; д - балки несимметричного сечения; е - балки с одним составным или утолщенным поясом; 1-4 - очередность наложения швов.
При автоматической сварке «в лодочку» за один проход накладывают угловые швы катетом до 16 мм включительно, при ручной — до 10 мм, при полуавтоматической — до 12 мм.
|
В подкрановых балках, предназначенных для кранов с тяжелым режимом работы, требуется сплошное сплавление стенки с верхним поясом. Сплошное проплавление стенки без разделки фасок при толщине металла до 14 мм включительно обеспечивается автоматической сваркой, при 8-14 мм - полуавтоматической.
Для увеличения глубины провара поясные швы со сплошным проплавлением стенки следует выполнять в «несимметричную лодочку» (рис.10). В этом случае балка устанавливается с наклоном 30° к горизонтальной оси.
Рис.10 Сварка поясных швов балок в «несимметричную лодочку»: а - установка балки под сварку; б - вид сварного соединения и швов; 1 - наклонный козелок; 2 - свариваемая балка; 3 - электрод.
Билет № 18
Вопрос 2
Сваркой называется процесс получения неразъемного соединения твердых материалов путем их местного сплавления или совместного деформирования, в результате чего возникают прочные связи между атомами свариваемых материалов. Схема классификации основных способов сварки приведена на рис. 1.
Сварка плавлением
Электродуговая сварка. Необходимое для местного расплавления деталей и присадочного материала тепло образуется при горении электрической дуги между свариваемым металлом и электродом. По способу механизации сварка может быть ручная, полуавтоматическая и автоматическая. Механизированная (полуавтоматическая и автоматическая) сварка может быть под флюсом и в защитных газах.
Электрошлаковая сварка. Плавление основного металла и присадочного материала происходит за счет тепла, выделяющегося при прохождении электрического тока через расплавленный шлак (в период установившегося процесса).
Электроннолучевая сварка. Сварка выполняется в камерах с разряжением до 10-4 — 10-6 мм рт. ст. Тепло выделяется за счет бомбардировки зоны сварки электронным потоком, приобретающим высокие скорости в высоковольтной установке, имеющей мощность до 50 квт. Анодом является свариваемая деталь, а катодом — вольфрамовая нить или спираль, нагретая до температуры 2300° С.
Газовая сварка. Основной и присадочный металлы расплавляются высокотемпературным газокислородным пламенем (температура до 3200° С).
Импульсно-дуговая сварка. Сущность способа состоит в том, что сварочный ток не сохраняет постоянную величину, а поступает в дежурную сварочную дугу определенными кратковременными импульсами.
Плазменная сварка. Плавление металлов осуществляется плазменно-дуговой струей, имеющей температуру выше 10 000° С.
Лазерная сварка. Сварка основана на использовании фотоэлектронной энергии. При большом усилении световой луч способен плавить металл. Для получения такого луча применяют специальные устройства — лазеры.
Сварка давлением
Контактная сварка. Место сварки разогревается или расплавляется теплом, образованным при прохождении электрического тока через контактируемые места изделий.
Ультразвуковая сварка. Сварка осуществляется за счет превращения при помощи специального преобразователя ультразвуковых колебаний в механические высокой частоты и применения небольшого сдавливающего усилия.
Сварка трением. Сварка заключается в том, что вследствие трения одного из свариваемых стержней о другой место соединения разогревается; при приложении осевого усилия соединяемые металлы свариваются.
Холодная сварка. Сварка основана на способности металла образовывать общие кристаллы при значительном давлении.
Газопрессовая сварка. Сварка осуществляется нагреванием концов стержней или труб по всему периметру окружности многопламенными горелками до пластического состояния или плавления с их последующим сжатием.
Термитная сварка. Процесс сварки заключается в том, что свариваемые детали закладываются в огнеупорную форму, а в установленный сверху тигель засыпается термит — порошок из алюминия и окиси железа. При горении термита окись железа восстанавливается, а образующийся при этом жидкий металл при заполнении формы оплавляет и соединяет кромки свариваемых изделий.
Сварка токами высокой частоты. Этот способ сварки основан на разогреве токами высокой частоты концов стыкуемых стержней или труб до пластического состояния с последующим приложением осевых усилий для получения неразъемного соединения.
Билет 20
Вопрос 2
ПОКРЫТЫЕ ЭЛЕКТРОДЫ
Покрытый электрод – плавящийся электрод, на поверхности которого есть покрытие, неразрывно связанное с металлом электродного стержня.
Назначение электродов
Для ручной дуговой сварки металлоконструкций
широкой номенклатуры из различных сталей,
металлов и сплавов, для наплавки слоев с особыми
свойствами на поверхности деталей и узлов, а
также для дуговой резки и строжки металлов.
Функции:
- подводят электрический ток к дуговому промежутку;
- зажигают дугу и перемещают ее в пространстве;
- регулируют токовый режим в процессе сварки;
- расплавляют основной и присадочный металл;
- формируют сварочную ванну;
- формируют сварной шов необходимых формы и качества.
Электродное покрытие - это смесь измельченныхкомпонентов и связующего вещества, нанесенная наметаллический стержень методом опрессовки или (реже)окунания. При плавлении покрытия формируетсягазошлаковая защита плавящегося металла. В однихвидах покрытий доминирует шлаковая защита сварочнойванны, а в других - газовая.
Б. 20, в 3
Билет 21
Вопрос 2
Автоматическая сварка под флюсом – дуговая сварка проволокой (проволочным электродом) под слоем флюса с механизированными операциями подачи проволоки и перемещения дуги вдоль линии шва.
Общепринятые обозначения
SAW – Submerged Arc Welding – сварка погруженной дугой
Билет 21
Вопрос 3
Методы контроля качества сварных соединений могут быть разделены на две основные группы:
- методы контроля без разрушения образцов или изделий – неразрушающий контроль;
- методы контроля с разрушением образцов или производственных стыков – разрушающий контроль.
Обе группы методов контроля регламентируются соответствующими стандартами. Группа методов контроля, объединенная общими физическими характеристиками, составляет вид контроля.
Наиболее распространенными методами неразрушающего контроля являются: акустический, капиллярный, магнитный, радиационный, испытания с помощью течеискателей, гидравлические испытания, внешний осмотр и обмер сварных швов.
Неразрушающий контроль – это контроль свойств и параметров объекта, при котором не должна быть нарушена пригодность объекта к использованию и эксплуатации.
Внешний осмотр и обмер сварных швов
Внешний осмотр и обмеры сварных швов являются первыми контрольными операциями по приемке готового сварного узла или изделия. Этим видам контроля подвергают все сварные швы независимо от того, как они будут испытаны в дальнейшем. Внешним осмотром сварных швов выявляют наружные дефекты: непровары, наплывы, подрезы, наружные трещины и поры, смещение свариваемых кромок деталей и т.д. Визуальный осмотр производят как невооруженным глазом, так и с применением лупы с увеличением до 10 раз. Перед осмотром сварной шов и прилегающую к нему поверхность металла шириной 20 мм очищают от шлака, брызг и загрязнений. Размеры сварных швов контролируют обычно измерительными инструментами или специальными шаблонами. Внешний осмотр и обмеры сварных швов не дают возможности окончательно судить о качестве сварки. Они устанавливают только внешние дефекты шва и позволяют определить их сомнительные участки, которые могут быть проверены более точными способами.
Гидравлические испытания
Гидравлическим испытаниям подвергают трубопроводы, резервуары, технологические аппараты и другие объекты с целью проверки плотности и прочности сварных швов. Перед испытанием сварное изделие полностью герметизируют водонепроницаемыми заглушками. Сварные швы с наружной стороны тщательно обтирают ветошью или обдувают сжатым воздухом до получения сухой поверхности. После полного заполнения изделия водой с помощью насоса или гидравлического пресса создают испытательное давление (обычно в 1,5 – 2 раза больше рабочего). Дефектные места определяют по появлению течи, просачиванию воды в виде капель, запотеванию на поверхности шва или вблизи него.
Акустический метод контроля
Из акустических методов контроля наибольшее распространение получила ультразвуковая дефектоскопия. Хорошо обнаруживаются дефекты с малым раскрытием, типа трещин, газовых пор и шлаковых включений, в том числе и те, которые невозможно определить радиационной дефектоскопией.
Испытания с помощью течеискателей
Контроль течеискателями применяют для испытания ответственных сварных конструкций, течеискатели достаточно сложны и дорогостоящи. В качестве газа-индикатора в них используется гелий. Обладая высокой проникающей способностью, он способен проходить через мельчайшие несплошности в металле и регистрируется течеискателем. В процессе контроля сварной шов обдувают или внутренний объем изделия заполняют смесью газа-индикатора с воздухом. Проникающий через неплотности газ улавливается щупом и анализируется в течеискателе.
Капиллярный метод контроля
В производстве применяют два способа контроля:
- люминесцентный – основан на свойстве некоторых веществ (люминофоров) светиться при действии ультрафиолетовых лучей;
- цветная дефектоскопия – когда применяются красители, видимые в зоне дефекта при дневном свете.
В капиллярном виде контроля используют движение индикаторного вещества, т.е. проникновение индикатора по микропорам и микротрещинам вглубь дефектов как бы по капиллярам. После нанесения индикаторов на поверхность шва и выдержки излишний индикатор удаляют. Оставшийся в дефектах индикатор под воздействием облучения начинает высвечиваться, и тем самым обнаруживаются дефекты сварного шва.
Радиационный метод контроля
Контроль рентгеновским излучением в технике известен как контроль радиационным методом и основан на способности рентгеновских лучей проникать через сварное соединение и воздействовать на регистрирующее устройство (фотопленку). В зависимости от способа регистрации результатов различают три метода радиационного контроля: радиографический, радиоскопический и радиометрический. Наибольшее распространение получил радиографический метод контроля сварных соединений, поскольку снимок является документом, подтверждающим качество сварного шва. Рентгеновский снимок на фотопленке хранится столько времени, сколько по техническим условиям должно работать изделие.
Магнитный метод контроля
Среди магнитных методов контроля следует отметить магнитографический и магнитопорошковый. Суть магнитографического метода заключается в намагничивании контролируемого участка сварного шва и околошовной зоны с одновременной записью магнитного поля на магнитную пленку и последующем считывании полученной информации с помощью специальных устройств магнитографических дефектоскопов. Контроль, осуществляемый магнитопорошковым методом, состоит в том, что на поверхность намагниченного сварного соединения наносят ферромагнитный порошок. Под действием втягивающей силы магнитных полей рассеяния частицы порошка перемещаются по поверхности соединения и скапливаются в виде валиков над дефектами. Форма этих скоплений соответствует очертаниям выявляемых дефектов. Наибольшее распространение имеет магнитопорошковый метод, так как он позволяет визуально наблюдать расположение ферромагнитного порошка вокруг дефекта. Однако этот метод применим только для контроля ферромагнитных материалов (углеродистые стали).
Билет 22
Вопрос 2
Полуавтоматическая сварка – дуговая сварка автоматически подающимся проволочным электродом (проволокой) в среде защитного газа.
Комплексный экзамен по ПМ 01.
Билет № 15
Вопрос 2
Сварочными материалами называют расходные материалы, используемые при сварке.
Сварочные материалы могут выполнять следующие функции:
· обеспечение необходимых геометрических размеров сварного шва;
· получение металла сварного шва с требуемым химическим составом и свойствами;
· обеспечение защиты расплавленного металла от воздействия воздуха – газовой, шлаковой или газошлаковой;
· обеспечение стабильности процесса сварки;
· удаление вредных примесей из металла шва.
Виды сварочных материалов
Сварочные материалы | Разновидности |
Сварочные электроды и присадочные прутки | плавящиеся электроды с покрытием (с кислым, основным, рутиловым, целлюлозным, смешанным покрытием), неплавящиеся электроды |
Сварочная проволока | сплошная, порошковая, активированная |
Флюсы | защитные и электропроводные |
Газы | защитные (инертные и активные), горючие газы и газы, поддерживающие горение |
Керамические подкладки | для сварки стыковых швов, угловых и тавровых швов, всепозиционные, круглые и др. виды |
Сварочные электроды и проволока обеспечивают подачу электрического питания в зону сварки для нагрева. Плавящиеся покрытые электроды, порошковая и активированная проволока, защитный флюс для дуговой сварки содержат специальные компоненты, которые могут предназначаться для защиты металла от воздуха, поддержания стабильности процесса сварки, получения необходимого химического состава металла шва и т.п. Присадочный пруток вводится в сварной шов при сварке.
Основная роль защитных газов – обеспечение газовой защиты расплавленного металла от воздуха. К защитным газам относятся инертные (аргон, гелий и их смеси) и активные газы (углекислый газ и его смеси). Инертные газы не вступают в химические реакции с металлом и в нем практически не растворяются. Активные газы вступают в химические реакции с металлом или растворяются в нем.
Горючие газы и газы, поддерживающие горение применяются при газовой сварке и резке. К ним относятся ацетилен, пропан-бутановые смеси, метилацетилен-алленовая фракция (МАФ), водород, а также поддерживающий горение кислород.
Керамические подкладки используют для обеспечения высококачественного шва и формирования обратного валика.
Сварочные материалы (электроды, проволоку, присадочные прутки) также подразделяют по типу свариваемых сталей и металлов: для сварки углеродистых сталей, никзолегированных сталей, нержавеющих сталей, алюминия, меди, чугуна и т.п.
Билет 16
Вопрос 3
Сварочная проволока |
Основные виды сварочной проволоки – сплошного сечения, порошковая, активированная.
Сварочная проволока сплошного сечения
Сварочная проволока сплошного сечения применяется для полуавтоматической и автоматической сварки, а также для изготовления электродов и присадочных прутков.
Химический состав и диаметр проволоки для сварки сталей регламентирует ГОСТ 2246-70. Проволока для наплавки выпускается по ГОСТ 10543-75, проволока из меди и сплавов – по ГОСТ 16130-72, проволока из алюминия и сплавов – по ГОСТ 7871-75. Наиболее распространенной является стальная проволока. Она выпускается следующих диаметров (мм): 0,3; 0,5; 0,8; 1,0; 1,2; 1,4; 1,6; 2,0; 2,5; 3,0; 4,0; 5,0; 6,0; 8,0; 10,0; 12,0.
Пример обозначения: 3 Св08ХСМФА-ВИ-Э ГОСТ 2246-70.
Порошковая сварочная проволока
Порошковая сварочная проволока представляет собой трубчатую проволоку, заполненную порошкообразным наполнителем. Отношение массы порошка к массе металлической оболочки составляет от 15 до 40%. Конструкция порошковой проволоки может быть разной – простой трубчатой, с различными загибами оболочки, двухслойной (см. рисунок).
![]() |
ОБОЗНАЧЕНИЯ ЛЕГИРУЮЩИХ ЭЛЕМЕНТОВ
В ГОСТ приняты следующие буквенные обозначения легирующих элементов, входящих в марки стали.
А - азот
М - молибден
Ю - алюминий
Н - никель
Р - бор
Б - ниобий
Ф - ванадий
Е - селен
В - вольфрам
Т - титан
К - кобальт
У - углерод
С - кремний
П - фосфор
Г - марганец
Х - хром
Д - медь
Ц - цирконий
Влияние легирующих элементов:
Никель сообщает стали коррозионную стойкость, высокую прочность и пластичность, увеличивает прокаливаемость, повышает сопротивление удару.
Вольфрам образует в стали очень твердые соединения - карбиды, резко увеличивающие твердость и красностойкость стали. Вольфрам препятствует росту зерен при нагреве, способствует устранению хрупкости при отпуске.
Ванадий повышает твердость и прочность, измельчает зерно. Увеличивает плотность стали.
Кремний в количестве свыше 1% оказывает особое влияние на свойства стали: содержание 1-1.5% Si увеличивает прочность, причем вязкость сохраняется. При большем содержании кремния увеличиваются электросопротивление и магнитопроницаемость. Кремний увеличивает также упругость, окалийность.
Марганец при содержании свыше 1% увеличивает твердость, износоустойчивость, стойкость против ударных нагрузок, не уменьшая пластичности.
Кобальт повышает жаропрочность, магнитные свойства, увеличивает сопротивление удару.
Молибден увеличивает красностойкость, упругость, предел прочности на растяжение, антикоррозионные свойства и сопротивление окислению при высоких температурах.
Титан повышает прочность и плотность стали, способствует измельчению зерна, улучшает обрабатываемость и сопротивление коррозии.
Ниобий улучшает кислотостойкость и способствует уменьшению коррозии в сварных конструкциях.
Алюминий повышает жаростойкость и окалийность.
Медь увеличивает антикоррозионные свойства.
Церий повышает прочность и пластичность.
Цирконий позволяет получать сталь с заранее заданной зернистостью.
Лантан, церий, неодим уменьшают пористость, способствуют уменьшению содержания серы в стали, улучшают качество поверхности, измельчает зерно.
Билет № 17
Вопрос 2
Данная классификация приведена в официальном документе - ГОСТ 19521-74. Она подразумевает деление технологии на три типа:
· Термический. По названию понятно, что слияние двух заготовок происходит в результате точечного повышения их температуры, которое вызывает плавление и нарушение структуры металла. За счет этого частицы одной заготовки перемешиваются со второй. После окончания воздействия происходит практически мгновенное застывание. В данный вид включают дуговую, термитную, шлаковую, газовую, лучевую, лазерную и пр.
· Механический. В данном случае активно применяется воздействие высоким давлением на место спайки. Такая сварка обычно называется холодной, так как температура заготовок практически не меняется. Существуют различные технологии, подразумевающие воздействие трением, ультразвуковыми волнами, магнитными импульсами и пр.
· Термомеханический. Представляет собой промежуточный вариант между указанными выше. При его использовании на заготовки воздействуют как механическими, так и температурными методами. Т. е. происходит нагрев обрабатываемого участка с помощью тепловой энергии, а затем давлением объединяют ослабленные структуры заготовок. Хорошо знакомы с данным классом сварки кузнецы. Также его применяют при прокате металла, прессовании, выдавливании и т. д. Существуют различные подвиды: индукционный, газовый, диффузионный, дуговой.
На каждый из классов существует своя технология обработки, которую изучают в колледжах на соответствующих направлениях. Их выпускники обычно занимаются и ремонтом сварочного оборудования.
Билет № 17
Вопрос 3
Сварка балок составного двутаврового сечения.
Составные двутавровые балки отличаются наличием швов значительной протяженности и большого сечения. Поэтому для выполнения поясных швов рекомендуется автоматическая сварка под флюсом с расположением швов «в лодочку».
Для того, чтобы избежать больших остаточных деформаций двутавровых сечений — кривизны и винтообразности, рекомендуется вести сварку всех поясных швов в одном направлении и соблюдать порядок их наложения, показанный на рис.9.
Рис.9 Последовательность сварки поясных швов двутавровых балок:
а - балки симметричного сечения большой высоты; б - балки симметричного сечения небольшой высоты из тонколистового металла; в - балки симметричного сечения небольшой высоты из толстолистового металла; г - балки с развитым верхним поясом; д - балки несимметричного сечения; е - балки с одни
|
|
Двойное оплодотворение у цветковых растений: Оплодотворение - это процесс слияния мужской и женской половых клеток с образованием зиготы...
Своеобразие русской архитектуры: Основной материал – дерево – быстрота постройки, но недолговечность и необходимость деления...
Опора деревянной одностоечной и способы укрепление угловых опор: Опоры ВЛ - конструкции, предназначенные для поддерживания проводов на необходимой высоте над землей, водой...
История создания датчика движения: Первый прибор для обнаружения движения был изобретен немецким физиком Генрихом Герцем...
© cyberpedia.su 2017-2024 - Не является автором материалов. Исключительное право сохранено за автором текста.
Если вы не хотите, чтобы данный материал был у нас на сайте, перейдите по ссылке: Нарушение авторских прав. Мы поможем в написании вашей работы!