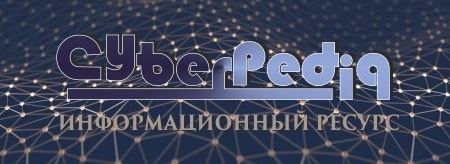
Типы оградительных сооружений в морском порту: По расположению оградительных сооружений в плане различают волноломы, обе оконечности...
Индивидуальные очистные сооружения: К классу индивидуальных очистных сооружений относят сооружения, пропускная способность которых...
Топ:
Когда производится ограждение поезда, остановившегося на перегоне: Во всех случаях немедленно должно быть ограждено место препятствия для движения поездов на смежном пути двухпутного...
Генеалогическое древо Султанов Османской империи: Османские правители, вначале, будучи еще бейлербеями Анатолии, женились на дочерях византийских императоров...
Проблема типологии научных революций: Глобальные научные революции и типы научной рациональности...
Интересное:
Искусственное повышение поверхности территории: Варианты искусственного повышения поверхности территории необходимо выбирать на основе анализа следующих характеристик защищаемой территории...
Что нужно делать при лейкемии: Прежде всего, необходимо выяснить, не страдаете ли вы каким-либо душевным недугом...
Инженерная защита территорий, зданий и сооружений от опасных геологических процессов: Изучение оползневых явлений, оценка устойчивости склонов и проектирование противооползневых сооружений — актуальнейшие задачи, стоящие перед отечественными...
Дисциплины:
![]() |
![]() |
5.00
из
|
Заказать работу |
|
|
Это один из наиболее распространенных способов восстановления изношенных деталей автотранспортных средств. Разнообразные методы наплавки различаются источниками тепловой энергии, способами защиты наплавляемого металла, уровнем автоматизации. Однако все виды наплавки имеют общие металлургические и физико-химические основы. К ним относятся расплавление наносимого металла с частичным расплавлением поверхностного слоя, перемешивание расплавов, кристаллизация.
Наибольшее распространение получила электродуговая наплавка, осуществляемая ручным и полуавтоматизированным способами. При механизированной наплавке вместо отдельных электродов применяется свернутая в бухту проволока либо электродная лента. Чаще всего используется наплавка под слоем флюса. Порошковый флюс, непрерывно подаваемый в зону дуги, образует над швом шлаковую оболочку, которая из-за низкой теплопроводности уменьшает скорость охлаждения наплавленного материала, что способствует нормализации структуры, а также защищает шов от окисления, предотвращает разбрызгивание металла, доля которого в шве колеблется от 30 до 65 %, что ухудшает свойства защитного слоя и делает их в значительной мере случайными величинами.
Напыление покрытий из порошковых материалов
Этот метод является одним из наиболее эффективных способов создания износостойких слоев. Если в высокотемпературную струю газа подать частицы порошка или капли расплава, то при столкновении с поверхностью они деформируются и прочно прикрепляются к детали. Существуют две разновидности такой технологии: газоплазменное напыление и электрическое напыление. При газоплазменном методе тепло выделяется в результате сжигания смеси горючего газа с кислородом, при электрическом методе источником тепла является электрическая дуга. Для газопламенного напыления в кустарных условиях производства используют обычные газовые горелки, обеспечивающие плавление и разбрызгивание материала проволоки, подаваемой в зону факела. В качестве источника высокотемпературной и скоростной струи удобно использовать плазмотрон (принцип действия которого описан выше). В этом случае напыляемый порошок подается в струю плазмы. Имеются и электродуговые устройства, в которых через зону плавления в дуговом разряде двух проволочных электродов вдувается сжатый воздух. Струя раскаленного воздуха вместе с каплями расплава направляется на поверхность детали.
|
Другим вариантом нагрева напыляемого материала является использование индукционных токов высокой частоты, которые возникают в проволоке, проходящей через охлаждаемый соленоид, генерирующий высокочастотное электромагнитное поле. Через катушку продувается струя воздуха, которая подхватывает капли расплавившейся проволоки и ударяет их о поверхность детали.
Главным достоинством метода напыления является его универсальность - независимость от природы материала детали. Можно наносить покрытия не только на металлы, но и на керамику, дерево, бетон, полимеры, ткани, бумагу. Это связано с тем, что напыление не оказывает заметного теплового воздействия на основу.
Ионно-плазменные методы
Данные методы весьма эффективны, но их применение требует высокого разрежения (они осуществляются в вакуумных камерах), поэтому они достаточно дорогостоящие и применяются лишь для весьма ответственных деталей, работающих при высоких температурах в условиях адгезионного и окислительного изнашивания. В условиях вакуума наносимый металл превращается в газ, пар, ионизированный пар и плазму, а затем в атмосфере реакционного или инертного газа оседает на поверхности детали. Покрытие может быть получено способами термического испарения, катодного или ионно-плазменного распыления или с помощью бомбардировки поверхности потоком из частиц осаждаемого вещества. В качестве реакционного газа применяют азот или углеводород, в результате формируется нитридное или карбидное покрытие.
|
Плакирование
Метод создания толстослойных покрытий применяется при изготовлении деталей или при восстановлении их формы после изнашивания. При этом толщина слоя может составлять несколько миллиметров. Плакирование также используется при изготовлении элементов скользящих электрических контактов в целях экономии дорогостоящих материалов с высокой электропроводностью, например, серебра.
Толстослойные покрытия часто наносятся методом прокатки. Сцепление слоев осуществляется за счет диффузии, стимулируемой высокой температурой. Применяются также диффузионная и электроконтактная сварка, наплавка, припаивание и другие способы. Таким методом получают биметаллические полосы, кольца.
|
|
Архитектура электронного правительства: Единая архитектура – это методологический подход при создании системы управления государства, который строится...
Опора деревянной одностоечной и способы укрепление угловых опор: Опоры ВЛ - конструкции, предназначенные для поддерживания проводов на необходимой высоте над землей, водой...
Двойное оплодотворение у цветковых растений: Оплодотворение - это процесс слияния мужской и женской половых клеток с образованием зиготы...
Своеобразие русской архитектуры: Основной материал – дерево – быстрота постройки, но недолговечность и необходимость деления...
© cyberpedia.su 2017-2024 - Не является автором материалов. Исключительное право сохранено за автором текста.
Если вы не хотите, чтобы данный материал был у нас на сайте, перейдите по ссылке: Нарушение авторских прав. Мы поможем в написании вашей работы!