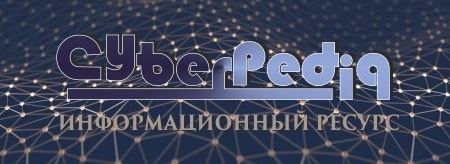
Своеобразие русской архитектуры: Основной материал – дерево – быстрота постройки, но недолговечность и необходимость деления...
Организация стока поверхностных вод: Наибольшее количество влаги на земном шаре испаряется с поверхности морей и океанов (88‰)...
Топ:
История развития методов оптимизации: теорема Куна-Таккера, метод Лагранжа, роль выпуклости в оптимизации...
Характеристика АТП и сварочно-жестяницкого участка: Транспорт в настоящее время является одной из важнейших отраслей народного хозяйства...
Организация стока поверхностных вод: Наибольшее количество влаги на земном шаре испаряется с поверхности морей и океанов...
Интересное:
Принципы управления денежными потоками: одним из методов контроля за состоянием денежной наличности является...
Берегоукрепление оползневых склонов: На прибрежных склонах основной причиной развития оползневых процессов является подмыв водами рек естественных склонов...
Национальное богатство страны и его составляющие: для оценки элементов национального богатства используются...
Дисциплины:
![]() |
![]() |
5.00
из
|
Заказать работу |
|
|
Этот способ наплавки является разновидностью наплавки под слоем флюса и защитных газов процесс осуществляется при вибрации электрода с подачей охлаждающей жидкостью на наплавленную поверхность выше дана схема вибродуговой установки с электромеханическим вибратором деталь «3» подлежащий наплавки устанавливаются в патроне или в центрах токарного станка, на суппорте станка монтируются наплавочная головка. Состоящая из механизма подачи проволоки «5» с кассетой для электродной проволоки «6» электромагнитного вибратора «7» с мундштуком «4» вибратор создает колебание конца электрода с частотой 110 Гц и амплитудой колебания от 1 до 4 мм обеспечивая размыкание и замыкание сварочной цепи
Вибрация электрода существенно влияет на качество наплавки.
В связи с разрывом происходит мелкокапельный переход металла с электрода на основную деталь, образуя минимально воздушную сварочную ванну, способствующую достаточно хорошему наплавлению электродного металла с основным, небольшому нагреву и созданию малой по глубине зоны термического влияния. Кроме того уменьшается выгорание легирующих элементов электродной проволоки.
Вибродуговой наплавкой можно получить сравнительно тонкие и весьма прочные покрытия толщиной от 0,8 до 2,5 мм на круглых деталях диаметром от15 мм и больше.
Электроснабжение установок осуществляется от источника тока величиной 24 V последовательно с ним включен дроссель «9» низкой частоты который стабилизирует силу сварочного тока. Реостат служит для легировки силы тока в цепи
в зону наплавки при помощи насоса «1» из фильтрующего отстойника. В бак
«2» подается охлаждающая жидкость 4-6 % водный раствор кальцинированной соды которая защищает месталл от окисления.
|
Преимущество небольшой нагрев поверхности детали небольшая зона техническая слияния:
Возможность получать
Качество наплавки зависит от полярности тока зависит от полярности тока шага наплавки угла подвода электрода к детали качество очистки и подготовка поверхности детали и толщины слоя наплавки.
Высокое качество наплавки получают при токе обратной полярности (+) на электроде (-) на детали, шаг наплавки 2,3-2,8 мм и углу подвода проволоки к детали 15-30градусов скорость подачи электродной проволоки не должна превышать 1,05 м/мин при однослойном наплавки 0,5 -0,65 м/мин при однослойной наплавке толщина слоя колеблется от 0,5 до 3 мм а при многослойной наплавки можно получать слой любой толщины.
14. Электроконтактная сварка и наплавка (приварка ленты, проволоки, порошка). Сущность процесса, область применения, достоинства и недостатки.
По форме выполняемых соединений различают три основных вида контактной сварки: стыковую, точечную и шовную или роликовую.
При стыковой сварке через стык соединяемых деталей пропускают электрический ток. После разогрева зоны сварки производится осадка.
При точечной сварке соединяемые детали, чаще всего листы, собирают внахлёстку и зажимают между двумя медными, охлаждаемыми изнутри проточной водой электродами, подводящими ток к месту сварки и имеющими вид усечённого конуса. Ток проходит от одного электрода к другому через толщу соединяемых металлов и контакт между ними и производит местный нагрев их(вплоть до температуры расплавления). Давлением Р, приложеныым к электрода, производят осадку. Полученное сваренное соединение в плане имеет форму пятна диаметром в несколько миллиметров. Это пятно называют точкой.
При шовной сварке электроды, подводящие ток к изделию и осуществляющие сварку, имеют форму роликов, катящихся по изделию, в связи с чем эту разновидность контактной сварки называют также роликовой. При шовной сварке листы соединяются непрерывным плотным швом.
|
Энергия, выделяемая на контактах между электродами и основным металлом, расходуется на подогрев поверхности свариваемых деталей и ускоряет износ электродов, в связи с чем является вредной. Для уменьшения износа электродов обычно предусматривается водяное охлаждение их.
Все разновидности электрической контактной сварки широко используют в промышленности, а в ряде отраслей (например в автомобилестроении и др.) находят наибольшее по сравнению с другими способами сварки применение.
Сущность способа ЭКН заключается в нагреве присадочного материала и приконтактного объема металла восстанавливаемой детали импульсами электрического тока и их совместной пластической деформации, обеспечивающей образование физического контакта, активацию контактных поверхностей и объемное взаимодействие покрытия и материала основы.
В качестве присадки при ЭКН применяются как порошковые материалы, так и компактные материалы (сплошные металлические ленты и проволоки, порошковые ленты и проволоки). В случае использования в качестве присадки порошковых материалов процесс называется электроконтактное припекание (ЭКП). Припекание – технологический процесс, заключающийся в нанесении на поверхность восстанавливаемой детали порошковой формовки или слоя порошка с целью получения двухслойного материала путем нагрева до температуры, обеспечивающей спекание порошкового материала и образования прочной диффузионной связи с деталью.
Наварка стальной ленты. Металлическая лента используется для восстановления деталей типа тел вращения (валы, оси, ролики). Для этого используют отожженные СЛ. В этом случае теплота выделяется в основном на переходном сопротивлении лента – деталь. Наплавленный слой (определение «наплавленный слой» в принципе некорректно.) формируется в результате соединения СЛ с поверхностью детали. Его толщина практически равна толщине СЛ. Ленты почти всех марок стали при наварке значительно упрочняются (наблюдали даже упрочнение слоя, наплавленного лентой стали 08). Получаемая твердость пропорциональна содержанию углерода в стали.
Упрочнение происходит неравномерно. Наиболее интенсивно упрочнение происходит в зонах наплавленного слоя, не подвергающихся термическому воздействию последующих импульсов тока. Площадь этих зон составляет 50–90% от общей площади наплавленной поверхности. Остальная часть наплавленного слоя разупрочняется при наварке смежных участков в результате повторного термического воздействия. Степень разупрочнения повышается при увеличении содержания углерода в стали и снижении содержания легирующих элементов.
|
При правильном выборе режима наплавленные слои являются практически беспористыми. Однако с повышением содержания углерода возрастает вероятность образования в наплавленном слое сетки трещин. Поэтому электроконтактную наварку СЛ наиболее целесообразно применять для восстановления и упрочнения деталей, имеющих большой запас усталостной прочности.
Недостатками наплавки металлической лентой являются сравнительно низкая прочность сцепления покрытия с основой, тонкий слой наплавленного металла. Увеличить толщину наплавки в данном случае не представляется возможным. Более толстое покрытие позволяет получить ЭКН сварочной проволокой.
Наплавка сварочной проволокой. Электроконтактную наплавку осуществляют на специальной установке совместным деформированием наплавляемого металла и поверхностного слоя металла основы, нагретых в очаге деформации до пластического состояния короткими (0,02–0,04 с) импульсами тока 10–20 кА. В результате каждого из последовательных электромеханических циклов процесса на поверхности металла основы образуется единичная площадка наплавленного металла, перекрывающая соседние. Деформация наплавляемого металла за цикл составляет 40 – 60%. Наличие пластической деформации присадочного материала дает возможность повысить прочность сцепления покрытия с основой.
Наварка порошковых материалов. Использование свободных порошков позволяет готовить широкую гамму композиций различных технологических и эксплуатационных свойств, имея в наличии небольшую номенклатуру порошков матричных, технологических и упрочняющих материалов. Наварку производят сухими порошками со свободной их подачей под сварочные ролики.
Для уменьшения износа электрода, а также для устранения налипания порошковых материалов на контактную поверхность роликового электрода между последними и порошковым слоем целесообразно вводить технологическую медную или латунную ленту толщиной 0,1–0,2 мм (рис. 10, в). При нанесении твердосплавных металлических порошков, когда требуется приложение к слою значительных давлений (DР>О,7 МН/м), возможен токоподвод непосредственно через технологическую прокладку. Верхний ролик выполняется из жаропрочной стали.
|
В настоящее время широко применяется ЭКПП предварительно сформированных покрытий. Порошок с помощью плазмы или газопламенного устройства напыляют на поверхность заготовки, после чего она подвергается воздействию давления с одновременным пропусканием электрического тока. Указанный способ позволяет эффективно упрочнять крупногабаритные детали, оплавление которых после напыления практически невозможно. Электроконтактное припекание предварительно напыленных покрытий дает возможность получать слои с высокими физико-механическими свойствами, которые существенно превосходят характеристики оплавленных покрытий.
Применяющиеся в настоящее время дозирующие устройства для электроконтактной наплавки металлических порошков не позволяют решить поставленную задачу. Это связано с тем, что требуемый расход порошкового материала определяется сечением крана бункера и давлением порошка, масса которого изменяется в процессе упрочнения. Вследствие значительного удельного веса металлических порошков давление на слои, прилегающие к отверстию крана, в процессе наплавки существенно изменяется. Кроме того, требуемая величина толщины слоя порошка регулируется вручную, что приводит к ошибкам, снижающим качество металлопокрытия.
НАПЕКАНИЕ И НАПЛАВКА
Электроконтактное напекание металлических порошков применяют для восстановления деталей типа валов и осей. Технология этого процесса разработана в Челябинском институте механизации и электрификации сельского хозяйства. Сущность его заключается в следующем:
Между вращающейся деталью 4 (рис. 4), установленной в шпиндель токарного станка, и медным роликом-электродом 2, подают присадочный порошок 3. Ролик 2, при помощи
пневмо- или гидро - цилиндра 1 прижимается к детали с усилием 0,75...1,2 кН. При прокатывании детали и ролика и в результате большлого электрического сопротивления в месте их контакта порошок нагревается до температуры 1000...1300'С. Раскаленные частицы порошка спекаются межд собой и с поверхностью детали. Для напеканияпорошка применяют большуюсилу тока 2500...3500 А напряжение 0,7...1,2 В от трансформатора 6.
Качество слоя во многом зависит от размеров детали и ролика, от давления, создаваемого роликом, химического состава порошка и окружной скорости детали. При диаметрах восстанавливаемых деталей от 0 до 100 мм электроконтактным напеканием можно получить слой толщиной от 0 до 1,5 мм. С увеличением диаметра детали толщина наносимого слоя возрастает. Скорость напекания составляет 0,11...0,25 м мин. Преимущества процесса — высокая производительность, малая глубина теплового воздействия и высокая износостойкость напеченного слоя. К недостаткам можно отнести ограниченность толщины напекаемого слоя и сложность оборудования.
|
Рис. 40. Схема электроконтактного напекания металлических порошков:
1 – силовой цилиндр; 2 – ролик; 3 – металлический порошок; 4 – деталь;
5 – напекаемый слой; 6 – трансформатор; Р – прижимное усилие.
Основные виды сварки. Подготовка поверхностей перед сваркой.
Сваркой называют технологический процесс получения механически неразъемных соединений, характеризующихся непрерывностью структур – непрерывной структурной связью.
Механическая сварка.
Она же сварка взрывом. Выделение тепла происходит за счет трения между соединяемыми материалами. Трение происходит за счет взрыва, который сжимает соприкасающиеся поверхности деталей. Данный метод применяется для плакирования металлов инородным материалом. Например, сталь плакируется алюминием.
Термическая сварка.
Данный тип сварки включает в себя несколько разновидностей, которые мы сейчас и рассмотрим.
Электродуговая сварка.
Данный вид сварки наиболее часто используемый. Расплавление свариваемых материалов и/или деталей происходит за счет выделяемой электрической дугой теплоты. После застывания свариваемые поверхности образуют единое сварное соединение. Для данного типа сварки необходим сильноточный источник питания низкого напряжения. К его зажиму присоединяется сварочный электрод, к которому, в свою очередь, прикасается свариваемая деталь.
Основными «подвидами» электродуговой сварки являются: ручная дуговая сварка, сварка неплавящимся электродом, сварка плавящимся электродом, сварка под флюсом, электрошлаковая сварка.
Ручная дуговая сварка.
Является универсальным технологическим процессом. С её помощью можно производить сварочные работы в любом пространственном положении, из различных марок сталей, даже при отсутствии необходимого оборудования. Используется специальный покрытый флюсом электрод. Покрытие используется для защиты шва металла от внешних воздействий. Сварка проводится на постоянном токе прямой или обратной полярности и на переменном токе. Данный вид сварки применяется для выполнения коротких и криволинейных швов в труднодоступных местах, а также при монтажных работах.
Сварка неплавящимся электродом.
В качестве электрода используется стержень из графита или вольфрама. Температура плавления данных материалов выше температуры, при которой протекает сварочный процесс. Сварка чаще всего проводится в среде защитного газа (аргон, гелий, азот и их смесях) для защиты шва и электрода от влияния атмосферы. Сварку может проводить как без присадочного материала, так и с ним. В качестве присадочного материала используются металлические прутки, проволока, полосы.
Сварка плавящимся электродом.
В качестве электрода используется проволока (стальная, медная или алюминиевая), к которой через токопроводящий наконечник подводится ток. Электрическая дуга расплавляет проволоку, и для обеспечения её постоянной длины проволока подаётся автоматически механизмом подачи. Для защиты от атмосферы применяются защитные газы (аргон, гелий, углекислый газ и их смеси), подающиеся из сварочной головки вместе с электродной проволокой.
Сварка под флюсом.
В этом виде сварки конец электрода также представлен в виде металлической проволоки или стержня, на конец которой (-го) подается слой флюса. В качестве флюсов применяют прокаленную буру, борную кислоту, кремниевую кислоту и др. Флюсы используются в виде порошков, паст, водных растворов. Горение дуги происходит в газовом пузыре, находящемся между металлом и слоем флюса. Сама дуга при этом не видна. Благодаря этой технологии усиливается защита металла от вредного воздействия атмосферы и улучшается глубина проплавления металла.
Электрошлаковая сварка.
При электрошлаковой сварке в качестве электродов служат: электродная проволока, стержни, пластины. Источником теплоты является расплавленный шлак, через который протекает электрический ток. При этом теплота, выделяемая флюсом, расплавляет кромки свариваемых деталей и присадочную проволоку. Способ находит своё применение при сварке вертикальных швов толстостенных изделий. Электрошлаковую сварку используют в машиностроении для изготовления ковано-сварных и лито-сварных конструкций.
Плазменная сварка.
Источником теплоты является плазменная струя, получаемая при нагреве электрическим током электрода. Струя плазмы сжимается и ускоряется под действием электромагнитных сил, оказывая на свариваемое изделие как тепловое, так и газодинамическое воздействие. Теплом струи расплавляется основной металл около дуги, а также присадочный металл. Помимо сварки этот способ часто используется для наплавки, напыления и резки.
Электронно-лучевая сварка.
Источником теплоты является электронный луч. Луч получается за счёт термоэлектронной эмиссии с катода электронно-лучевой пушки. Данный вид сварки применяется в промышленных условиях в вакуумных камерах. Известна также технология сварки электронным лучом в атмосфере нормального давления, когда электронный луч покидает область вакуума непосредственно перед свариваемыми деталями.
Лазерная сварка.
Источником теплоты служит сфокусированный лазерный луч. Применяют твердотельные, газовые, жидкостные и полупроводниковые лазерные установки. Лазерный луч также используется для резки различных материалов. Основными достоинствами лазерной сварки являются: возможность вести процесс на больших скоростях, практически отсутствие деформаций изделия и узкий шов.
Газопламенная сварка.
Источником теплоты является газовый факел, образующийся при сгорании смеси кислорода и горючего газа. В качестве горючего газа могут быть использованы ацетилен, водород, пропан, бутан и их смеси. Тепло, выделяющееся при горении смеси кислорода и горючего газа, оплавляет свариваемые поверхности и присадочный материал с образованием сварочной ванны. Пламя может быть «окислительным» или «восстановительным», это регулируется количеством кислорода.
Термомеханическая сварка
Сварка происходит за счет нагревания свариваемых поверхностей. У этого вида сварки тоже имеются свои разновидности.
Контактная сварка.
При данном типе сварки изделия нагреваются, и происходит их деформация, что обеспечивает их взаимное проникновение. Свариваемые детали зажимаются в сварочных клещах, и по электродам пускают ток высокого напряжения, который плавит детали. Затем ток отключают и сильно сжимают клещи, из-за чего металл кристаллизируется, образуя, сварной шов.
Диффузионная сварка.
При диффузионной сварке соединяемые поверхности сдавливают и нагревают. Обычно этот процесс происходит в вакууме. В результате этого действия образуется сварочный шов. Данная технология весьма дорогостоящая и поэтому находит свое применение в основном в авиакосмической, электронной и инструментальной промышленности.
Кузнечная сварка.
Сваривание поверхностей происходит за счет ударов кованым молотом по раскаленным деталям. Данный тип сварки не надежен, малопроизводителен и пригоден для ограниченного числа сплавов. Кузнечная сварка на сегодняшний день практически нигде не используется.
Сварка высокочастотными токами.
Свариваемые изделия располагают вплотную друг к другу и разогревают за счет пропускания тока высокой частоты, затем детали сжимают. После этого полученному изделию необходимо остыть, и оно готово. Метод применяется в основном для изготовления труб и фасонных изделий из сортовой стали.
Разнообразие способов сварки, отраслей промышленности, в которых её используют, свариваемых материалов, видов конструкций и огромные объёмы применения позволяют охарактеризовать технологический процесс сварки, как один из важнейших в металлообработке
Подготовка к сварке предусматривает разметку, правку, резку, гибку, обработку кромок.
Правка. Цель этой операции — устранение деформаций. Сортовой и листовой металл небольшой толщины правится в холодном состоянии, а толстый (как и значительно деформированный) предварительно надо подогреть до 250—300°С.
Разметка выполняется с целью нанесения размеров Детали на металл. Разметка может быть выполнена индивидуально, по шаблонам, а также оптическим и машинным методами. Индивидуальная разметка — очень трудоемкий процесс. Шаблоны обычно изготовляют из алюминиевого листа. Для разметки используют инструменты: линейку, угольник, рулетку и чертилку.
Резка как этап подготовки к сварке может быть термической или механической. По производительности термическая резка уступает механической, но она более универсальна и позволяет точно выкроить заготовки разной геометрической формы (в том числе криволинейной). Механическая резка не может дать такой результат, так как возможности ножниц и прессов ограничены.
Кромки подготавливаются также двумя способами — термическим и механическим. Но чаще используется механический способ.
Кромки с односторонним или двусторонним скосом можно получить, используя одновременно два или три резака, расположенных под соответствующими углами. Механическая обработка кромок на станках выполняется для обеспечения требуемой точности сборки, для образования фасок, имеющих заданное очертание, в случаях, если технические условия требуют удаления металла с поверхности кромок после резки.
Гибка может осуществляться разным инструментом и разными способами, но классическим является гибка на листогибочных вальцах. Кроме этого используется и штамповка (в промышленных условиях).
Кроме этих операций обязательно надо хорошо очистить поверхности свариваемых деталей от грязи, ржавчины, окалины, масел.
|
|
Двойное оплодотворение у цветковых растений: Оплодотворение - это процесс слияния мужской и женской половых клеток с образованием зиготы...
Общие условия выбора системы дренажа: Система дренажа выбирается в зависимости от характера защищаемого...
История развития пистолетов-пулеметов: Предпосылкой для возникновения пистолетов-пулеметов послужила давняя тенденция тяготения винтовок...
Организация стока поверхностных вод: Наибольшее количество влаги на земном шаре испаряется с поверхности морей и океанов (88‰)...
© cyberpedia.su 2017-2024 - Не является автором материалов. Исключительное право сохранено за автором текста.
Если вы не хотите, чтобы данный материал был у нас на сайте, перейдите по ссылке: Нарушение авторских прав. Мы поможем в написании вашей работы!