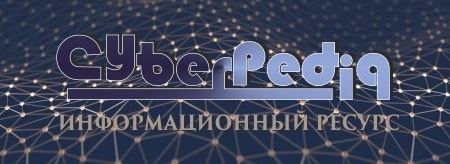
Таксономические единицы (категории) растений: Каждая система классификации состоит из определённых соподчиненных друг другу...
Археология об основании Рима: Новые раскопки проясняют и такой острый дискуссионный вопрос, как дата самого возникновения Рима...
Топ:
Техника безопасности при работе на пароконвектомате: К обслуживанию пароконвектомата допускаются лица, прошедшие технический минимум по эксплуатации оборудования...
История развития методов оптимизации: теорема Куна-Таккера, метод Лагранжа, роль выпуклости в оптимизации...
Устройство и оснащение процедурного кабинета: Решающая роль в обеспечении правильного лечения пациентов отводится процедурной медсестре...
Интересное:
Лечение прогрессирующих форм рака: Одним из наиболее важных достижений экспериментальной химиотерапии опухолей, начатой в 60-х и реализованной в 70-х годах, является...
Финансовый рынок и его значение в управлении денежными потоками на современном этапе: любому предприятию для расширения производства и увеличения прибыли нужны...
Влияние предпринимательской среды на эффективное функционирование предприятия: Предпринимательская среда – это совокупность внешних и внутренних факторов, оказывающих влияние на функционирование фирмы...
Дисциплины:
![]() |
![]() |
5.00
из
|
Заказать работу |
|
|
Решить вековую загадку булатного узора взялся Игорь Николаевич Голиков — начальник центральной лаборатории Златоустовского металлургического завода. Он создал творческую группу, в которую вошли П. В. Васильев, М. Ф. Лонгинов, Ю. И. Люндовский и автор этих строк. Выплавлять сталь было решено в тигле индукционной высокочастотной печи. Этот современный агрегат достаточно хорошо моделировал тигельный процесс, который П. П. Аносов использовал для получения булата. В первых опытах было решено воспользоваться рекомендациями изобретателя русского булата и как можно точнее повторить его эксперименты.
Нам было понятно, что свойства булата определяются содержанием углерода в стали и его распределением в железе. Поэтому шихта составлялась из содержащего мало вредных примесей мягкого железа (0,03% углерода) и серебристого графита.
Во время плавки поддерживался «большой жар» — расплав нагревали до 1600—1630°С. При таких температурах обеспечивалась высокая степень насыщения металла углеродом. Готовую сталь разливали в чугунные формы. Слиток охлаждали очень медленно. Многократно добиваясь крупной кристаллизации и прекрасно выраженной дендритной структуры слитка, мы ни разу не получали булатного узора. Чего-то в нашей технологии явно не хватало, но чего? Для ответа на этот вопрос было решено еще раз внимательно изучить всю имеющуюся литературу о булате. И вот что обнаружилось.
В 1919 году в Днепропетровском горном институте защищалась необычная диссертация: «Мягкий булат и происхождение булатного узора». Соискатель, уже немолодой человек, профессор А. П. Виноградов излагал свою теорию природы узорчатой стали. Материалы диссертации были опубликованы в 1928 году в «Научных записках кафедры металловедения и термической обработки металлов». В связи с тем, что к 50-м годам этот сборник стал библиографической редкостью, труд ученого остался малоизвестным.
|
А. П. Виноградову особыми приемами деформации стали удалось получить на основе дендритной ликвации углерода волокнистую неоднородность, проявляющуюся в виде узора. Однако узор этот оказался не сопоставимым с булатным, поскольку был выражен очень слабо.
«Следует признать,— писал А. П. Виноградов,— что хотя химическая и структурная неоднородность является неизбежной принадлежностью всякой литой стали, однако булаты резко отличаются особенно ярко выраженной химической и структурной неоднородностью». Отсюда вывод: при производстве булатной стали химическая неоднородность подчеркивалась и фиксировалась принципиально другими приемами. Талантливый ученый впервые замечает «эти приемы» в опубликованных трудах П. П. Аносова.
Внимательно изучая «Журнал опытов по приготовлению литой стали и булатов с краткими замечаниями», А. П. Виноградов обратил внимание на то обстоятельство, что при получении булатов металл часто недорасплавлялся. В примечаниях Аносов так и пишет: «не все расплавлялось» или — «несовершенно расплавилось».
Тщательно анализируя условия проводимых П. П. Аносовым плавок булатной стали, А. П. Виноградов убеждается, что основной их особенностью является науглероживание кусочков (обсечков) железа в тигле. Часть из них, взаимодействуя с графитом и печными газами, очень сильно науглероживалась и превращалась в малоуглеродистый чугун. Чугун, температура плавления которого 1200—1300°С, плавился и стекал каплями на дно тигля. Таким образом, в нижней части тигля скапливался жидкий чугун, а в его верхней части твердые обсечки мягкого низкоуглеродистого железа, температура плавления которых 1500—1535°С.
Нагрев металла в условиях тигельной плавки во времена П. П. Аносова осуществлялся до температур не выше 1460—1480°С, поэтому обсечки мягкого железа, погружаясь в конце концов в жидкий чугун, расплавиться не могли. Они могли лишь в твердом состоянии растворяться в чугуне. Плавка заканчивалась в тот момент, когда частички эти полностью в чугуне еще не растворились. Отсюда легко сделать вывод, что П. П. Аносов достигал большой физической неоднородности непосредственно при плавке стали за счет сохранения в основной массе высокоуглеродистого сплава частиц ненауглероженного и поэтому недорасплавившегося твердого железа.
|
Интересно, что П. П. Аносов понимал эти особенности технологии плавки булата. Он писал: «Искусство мастера в сем случае состоит в том, чтобы остановить работу в то мгновение, когда последний кусочек обсечков начинает расплавляться...» И далее: «При разбитии медленно охлажденных в печи тиглей сплавки казались как бы не совершенно расплавленными, ибо куски железа в некоторых местах сохранили первоначальную форму». В свете новой теории булатного узора эти замечания приобретают глубокий смысл.
Так как прекращение плавки у П. П. Аносова происходило в тот момент, когда в жидкость погружались твердые частицы железа, то последующее понижение температуры при охлаждении сплава в тигле приводило к кристаллизации высокоуглеродистой стали на имеющихся частицах железа, как на готовых центрах. Охлаждение стали в тигле, в котором она плавилась, как бы фиксировало полученную при плавке неоднородность. Недаром на основании своих опытов П. П. Аносов полагал, что переливание из тигля в изложницу порти г сталь.
Более того, по его наблюдению медленное охлаждение стали в тигле способствовало развитию кристаллизации и образованию узоров. Таким образом, процесс плавки и кристаллизации стали у П. П. Аносова неизбежно обусловливал крайнюю химическую, а следовательно, и структурную неоднородность слитка. Деформация при ковке этой неоднородной структуры и являлась причиной булатного узора.
К сожалению, на перечисленные особенности технологии производства булатной стали не обратил никакого внимания ни один из исследователей работ П. П. Аносова. Не указывал на них также никто из златоустовских мастеров, которые позже плавили булатную сталь. Естественно, что сам П. П. Аносов, не владея современными методами исследования металлов, не мог должным образом оценить степень влияния приведенных выше, на первый взгляд второстепенных, факторов на рисунок булата и его свойства.
|
После П. П. Аносова производство настоящих булатных клинков на Златоустовском заводе, как уже было отмечено, вскоре прекратилось. Д. К. Чернов объяснял это чрезвычайной сложностью процесса. «Производство узорчатой стали,— писал он,— требует усиленного постоянного наблюдения и преданности делу. В производстве булата очень ясно обнаружилось, какой капризный материал—сталь: малейшее несовершенство в процессе или нечистота материала — и уже сталь получается хуже, с мелким узором». А. П. Виноградов полагал, что причиной прекращения производства булата могло быть несоблюдение основного условия его получения: «прекращать процесс плавления, не дожидаясь полного растворения последних кусочков железа».
Действительно, П. П. Аносов, составив подробное описание приемов приготовления слитков булатной стали, не обратил должного внимания на момент прекращения плавки. Все последующие металлурги, плавившие булат после П. П. Аносова, не могли соблюсти это необходимое условие, обеспечивающее получение узорчатой стали. Поэтому они получали булат эпизодически и, как правило, с очень мелким узором.
Несмотря на то что А. П. Виноградов разработал оригинальную теорию, достаточно убедительно объясняющую природу химической и физической неоднородности булатной стали, его экспериментальные работы были посвящены главным образом вопросу формирования булатных узоров на основании так называемой «полосчатой структуры» низкоуглеродистой стали.
Металлургам давно известно, что после прокатки стали при низких температурах часто получают так называемую «полосчатую структуру», состоящую из участков перлита, чередующихся с видимыми простым глазом полосками чистого железа (феррита). А. П. Виноградов показал, что после низкотемпературной прокатки листовой стали, содержащей 0,30—0,35% углерода, и продолжительного отжига ее при температуре 800—900°С с последующим медленным охлаждением в печи полосчатая структура проявляется очень хорошо. Полосчатость в этом случае получается в виде параллельных слоев почти чистого феррита и углеродистой стали с 0,6—0,7%, углерода. Такая структура стали, по утверждению автора, имитирует «мягкие булаты» Аносова.
|
Даже при небольшой деформации слоев полосчатой структуры они могут стать волнообразными плоскостями с различной кривизной волн, а главное — могут значительно отклоняться от параллельности к поверхности образца. При достаточной толщине слоев отшлифованные образцы могут давать видимую простым глазом картину разнообразных узоров, характерных для булата. Если такой образец мысленно разрезать плоскостями, параллельными основанию, то они, подобно горизонталям при проектировании холмистой местности на карту, должны образовывать узор. Если слои приближаются к параллельным плоскостям, но не параллельны плоскости шлифа, то получается муаровый рисунок; если же они изгибаются в виде холма или углубления — ониксовидный. Применяя специальные приемы деформации стали — надрубы, разнообразную насечку и осадку,— А. П. Виноградов получал почти все известные рисунки булата.
Несмотря на то что А. П. Виноградов впервые экспериментально показал приемы получения булатного узора и выдвинул убедительно обоснованную теорию, объясняющую природу неоднородности булатной стали, ему не удалось приготовить настоящих булатов на основе высокоуглеродистых сплавов, у которых бы после закалки сохранились узоры. Последнее обстоятельство послужило поводом к критике взглядов А. П. Виноградова.
С целью подтверждения своих предположений А. П. Виноградов провел ряд плавок, в ходе которых путем присадки кусков железа в жидкую ванну пытался создать условия для получения физически неоднородного металла; но результаты этих опытов не были настолько выразительными, чтобы убедить в его правоте. Поэтому видные металлурги считали, что «нерасплавленные кристаллы, очевидно, не являются условием, необходимым для создания неоднородности жидкости», и что теория А. П. Виноградова применима скорее к сварочному булату, чем к литому.
Вутцы XX столетия
Итак, А. П. Виноградов впервые разглядел в булатном узоре физическую неоднородность стали. Не может быть сомнений в том, что П. П. Аносов добивался крайней неоднородности слитка за счет недорасплавившихся частиц низкоуглеродистого железа. С позиций современной науки такую структуру можно назвать неравновесной. А как же в древности получали неравновесную структуру вутца?
П. П. Аносов был прав, предполагая, что древние мастера изготовляли булат в специальных горнах, позволяющих совмещать процессы восстановления руды, науглероживания железа и его сплавления. Частицы восстановленной железной губки, по всей вероятности, науглероживались с поверхности окисью углерода и превращались в высокоуглеродистую сталь, а может быть, даже в чугун. Вместе с тем сердцевина частив сохранялась железной, ненауглероженной. Поскольку температура горна лежала между точками плавления железа и стали, то стальная оболочка частиц плавилась, и они соединялись в одно целое, образуя полусплавившийся слиток, макроструктура которого напоминала пирог с изюмом: зерна мягкого железа в окружении высокоуглеродистой стали.
|
Описанный выше способ получения неравновесной структуры слитка не единственный. Известно, что индийцы знали тигельный процесс задолго до европейцев. Они владели также сыродутным процессом приготовления железа, которое содержало не более одной-двух десятых процента углерода. Расплавить такое железо в тиглях они не могли. С другой стороны, они получали чугун, который легко плавился в тиглях, установленных в горн.
Железо — пластичный, упругий и вязкий металл, но недостаточно твердый. Чугун — твердый материал, но совсем не пластичный, хрупкий, его нельзя деформировать. Разве не напрашивается мысль: смешать кусочки чугуна и железа и расплавить их в тигле?
Теперь представим себе, что смесь кусочков чугуна и железа помещена в тигель и нагревается до температуры 1350—1380°С. В этом случае чугун в начале процесса плавился, а мягкое железо оставалось твердым. По мере нагревания сплава углерод из чугуна диффундировал (перемещался) в железо, чугун становился все более и более тугоплавким и в конце концов вся масса металла затвердевала. Естественно, что готовый сплав и в этом случае получался неоднородным, состоящим из двух фаз: высокоуглеродистой стали, в которую превратился чугун, отдавая углерод, и частиц железа, поверхность которых науглерожена.
Между тем такой способ получения стали имел существенный недостаток: чугун затвердевал быстрее, чем происходила сварка между науглероженными кусочками железа и чугуна, поскольку между ними трудно было обеспечить хороший контакт. В результате сплошность металла после ковки могла нарушаться трещинами. Можно ли этого избежать? Да, можно, если плавить в тигле сначала один чугун, и только после его расплавления добавлять в жидкий сплав мелкие кусочки железа. В этом случае контакт достигается идеальный, и диффузия углерода из чугуна в железо будет идти гораздо быстрее. Возможно, что в древние времена в Индии и других странах Востока таким путем получали знаменитые вутцы.
В Европе значительно позднее пришли фактически к такому же способу получения стали. Так, например, Реомюр еще в 1722 году высказывал идею о возможности превращения мягкого железа в сталь путем погружения его в жидкий чугун. В это время Европа еще не знала ни тигельного процесса, ни отражательных печей. Поэтому эта идея была осуществлена на Западе только в 1840—1860 годах братьями Эмилем и Пьером Мартенами, которые путем сплавления чугуна и лома впервые получили сталь на поду большегрузной отражательной печи. Известно, что температуры, которые достигались в мартеновских печах, позволяли полностью расплавить чугун и железо и получить жидкую сталь. Поэтому Европа перешагнула «булатный период» производства стали, и булат с его высокими свойствами и неповторимыми узорами навсегда остался для нее тайной.
«Неравновесная» теория булатного узора объясняет также, почему после П. П. Аносова практически никто не мог получить лучшие сорта булата. «Сильный» жар во время плавки, им рекомендуемый, стал своего рода психологическим барьером, который не смогли перешагнуть его последователи. Все дело в том, что «сильный жар» в отражательной печи Сименса, в которой впоследствии плавили тигельную сталь, соответствовал температуре 1500—1530°С; у Аносова же он не достигал этих температур. Таким образом, исследователи, повторявшие опыты Аносова, расплавляли шихту при таких температурах, которые не могли обеспечить неоднородность: чугун и железо полностью расплавлялись, и это приводило к получению обычной (гомогенной) углеродистой стали.
Что касается медленного охлаждения слитка, то здесь было заложено рациональное зерно. Этот фактор, с одной стороны, благоприятствовал достижению нужной неоднородности, а с другой — создавал условия для дальнейшей диффузии углерода, что, в свою очередь, способствовало формированию зоны постепенного изменения концентрации этого элемента при переходе слоев высокоуглеродистого металла в слои низкоуглеродистого. Такое строение обеспечивало уменьшение напряжений при деформации и нагреве стали и исключало появление в металле разрывов и трещин.
Кстати, теперь ясно, что сущность структуры настоящего булата ц сварочного булата фактически одна и та же. И все-таки свойства литого булата со сварочным несравнимы. У литого булата они должны были быть значительно выше. Это легко объяснить прежде всего тем, что содержание углерода в литом булате (1,3—2,0%) больше, чем в сварочном (0,6—0,8%). Кроме того, в литом булате, как мы теперь знаем, наблюдается более постепенный переход от высокоуглеродистых слоев к низкоуглеродистым. Очевидно, чем менее резок этот переход, тем выше механические свойства булатного клинка.
Почему же А. П. Виноградов, блестяще разгадавший секрет получения литой узорчатой стали, не сумел экспериментально воспроизвести аносовские плавки и получить высокоуглеродистый булат? По всей вероятности, он не имел тигельной печи. А в другом агрегате создать условия для науглероживания железа до чугуна и остановить плавку в нужный момент не так-то просто. Для этого требуется искусство мастера. Недаром даже соратник изобретателя русского булата Н. П. Швецов не мог повторить полностью результаты Аносова.
В свете «неравновесной» теории булата выбранная нами для эксперимента тигельная индукционная сталеплавильная печь оказалась самым удачным агрегатом для получения булатной стали. В такой печи можно поддержать температуру сплава на любом необходимом уровне и плавить нужную массу металла.
Было решено приготовить на техническом железе и графите синтетический чугун, содержащий как можно менее вредных примесей. Предполагалось чугун расплавлять в тигле индукционной печи и погружать в него кусочки малоуглеродистого железа. Температура в печи должна была поддерживаться на уровне 1460°С, чтобы железо не плавилось, а лишь растворялось в жидком чугуне. Наши первые эксперименты полностью подтвердили теорию А. П. Виноградова и окончательно установили, что при искусственно созданной неоднородности в жидкой или полужидкой стали можно получить слиток высокоуглеродистого сплава с включениями частиц малоуглеродистого железа. Появление булатного узора после деформации такого слитка и получение отличительных свойств, приписываемых булатам, теперь сомнений не вызывало. Надо было только хорошо отработать все детали технологии плавки. Пришлось провести немало опытов, отлить десятки слитков, чтобы научиться управлять процессом, задавать и выдерживать требуемый химический состав стали.
Краткие особенности технологии производства булата в индукционной сталеплавильной печи оказались следующими. В печь загружается железо или малоуглеродистая сталь в количестве 12—24 кг, плавится и подогревается до температуры 1650°С. После подогрева расплав раскисляется кремнием и алюминием. Затем металл науглероживается графитом, в результате чего получается синтетический чугун с содержанием углерода 3,0—4,0%. Когда чугун готов, в расплав вводится мелкодробленая обезжиренная стружка малоуглеродистой стали или мягкого железа в кусочках размером не более 10—15 мм. Каждый кусочек должен быть сухим, чистым, без ржавчины, цветов побежалости, каких-либо следов окисления. Количество стружки составляет 50—70% от массы чугуна — в зависимости от требуемого состава стали.
Стружка вводится постепенно, порциями. Перед присадкой каждой порции стружки в жидкую ванну температура металла не должна превышать 1480—1500°С. Необходимая степень оплавления стружки определяется с помощью стального прутка диаметром 15—20 мм. Таким прутком, после дачи каждой порции стружки, металл перемешивается до тех пор, пока можно ощущать удары твердых кусочков стружки, движущихся в ванне под действием электромагнитных потоков, о пруток. Таким образом, при приобретении навыка можно определять примерные размеры твердых включений малоуглеродистой стали в жидкой ванне.
По мере оплавления каждой порции стружки металл приобретает полужидкое или кашицеобразное состояние. В связи с этим перед присадкой следующей порции стружки он должен быстро подогреваться до необходимой температуры. После присадки последней порции стружки расплав, если это необходимо, нагревается до получения достаточной для разливки жидкоподвижности и раскисляется алюминием. Степень подогрева должна быть такой, чтобы в расплаве фиксировалась неоднородность — наличие недорасплавленных мелких стальных частиц. Благодаря тому, что эти частицы под действием электромагнитного поля взвешены во всем объеме жидкой ванны, готовую сталь можно выливать из тигля индукционной печи в форму.
Приготовленные нами булаты либо выливались в графитовые формы, либо оставлялись остывать в печи. В том и другом случае слиток медленно остывал в течение нескольких часов. Если полученный сплав выливался в графитовую форму, то необходимо было применять повышенный расход стружки. В этом случае получались булатные слитки с высокоуглеродистой матрицей, в которую вкраплены частицы мягкого железа (фото 5). Оплавившиеся частицы мягкого железа успевали науглероживаться в период плавки только с поверхности. Поэтому они сохраняли небольшое содержание углерода в сердцевине (0,03—0,05%), в то время как среднее содержание углерода в матрице составляло 1.4—1,6%.
Если же сплав до конца плавки поддерживался в кашицеобразном состоянии и застывал непосредственно в печи, применялся низкий расход стружки. Науглероживание частиц железа в этом случае происходило в большей степени. Концентрация углерода в преобладающем большинстве включений достигала 0,8—1,0%, а содержание углерода в матрице оставалось на прежнем уровне (1,5%). Интересно, что поверхность включений также науглероживалась более сильно (фото 6).
Слиткам, полученным по первому способу, дали название булатов с ферритными прослойками, а по второму — булатов с углеродистыми прослойками. Струйчатые узоры на изделиях можно получать только из слитков булата с ферритными прослойками.
Позднее мы научились изготовлять легированные булаты. В частности, для подчеркивания узора в сталь иногда вводили кремний и фосфора которые повышают устойчивость феррита при ее термической обработке. Вводя в сплав никель и хром, можно получить нержавеющие булаты.
После того как мы убедились, что найденный способ получения слитков булатной стали повторим как в части технологического процесса, так и в части макроструктуры слитка, была сделана заявка на изобретение. Вскоре Государственный комитет по делам изобретений и открытий при Совете Министров СССР выдал нам авторское свидетельство на «Способ изготовления слитков булатной стали».
Булатный слиток получен, но можно ли утверждать, что он похож на тот самый вутц, который изготовляли наши далекие предки? По-видимому, можно, и вот почему.
Не так давно в Хайдарабаде (Индия) было издано сочинение Аль-Бируни «Книга собрания (очерков) о познании драгоценных камней». В главе «О железе» автор сообщает несколько способов получения тигельной стали в Средней Азии, Иране и Индии, относящихся к IX—XI векам. «Сталь по своему составу,— пишет Аль-Бируни,— бывает двух сортов: первый, когда в тигле плавится нармохан (кричное железо) и «вода» (чугун) его одинаковым плавлением, и они оба в нем соединяются так, что не отличимы один от другого. И такая сталь пригодна для напильников и им подобных... Второй сорт получается, когда в тигле указанные вещества плавятся неодинаково и между ними не происходит совершенного смешения. Отдельные частицы их располагаются вперемешку, но при этом каждая из них видна по особому оттенку. Называется это фаранд. В мечах, которые их (два оттенка) соединяют, он высоко ценится».
Итак, нелегкие многолетние поиски, металлургов успешно завершены. Древняя технология получения булата была воспроизведена на новой основе в современном сталеплавильном агрегате...
Булатные узоры
Для получения булатного слитка нужны были опыт и терпение; но еще больше времени и сил требовалось для того, чтобы правильно его проковать и получить изделия высокого качества. Если ограничиться лишь тем, что из куска стали вырезать клинок, то свойства его будут чрезвычайно низкими. Если же проковать вутц на полосу путем его деформации только в одном направлении, то ферритные включения вытянутся и на изделии получится полосчатый прямолинейный узор, характерный для низших сортов булата. В этом случае мягкие ферритные полоски могут оказаться на лезвии клинка и он потеряет свои режущие свойства.
Встречались ли в древности с таким явлением? Да, встречались! Вот что об этом пишет Аль-Бируни: «К мечам, известным под названием ал-кубурийские, относятся как будто те, которые находят в могилах знатных покойников. И слышал я, что если мечи (изготовлены) из металла, который при плавке получил неодинаковое (количество) примесей («зелья»), то на них остаются тонкие нежные канальца (жилки), не впитывающие воду (углерод). Если они попадаются на лезвиях, то (мечи) не способны резать из-за отсутствия твердости. И если их стесать с лезвия, то вреда нет». Недаром турецкие и египетские клинки с «полосатым» узором даже в древности считались булатами самого низкого качества.
А как же следует проковать вутц, чтобы получить из него клинок с высокими свойствами? Люди давно заметили, что дерево вдоль волокон колется легко, а поперек — с трудом. Значит, надо проковать слиток так, чтобы волокна структуры булата «обтекали» контуры изделия. Если это клинок, то волокна должны быть направлены вдоль лезвия. Но и расположение волокон в виде прямых линий не обеспечивает высоких свойств, поэтому необходимо ориентировать волокна в разных направлениях, «перепутать» их, тогда высокие свойства обеспечены.
Сегодня металлурги хорошо знают, что чем больше «сплетать» волокно при ковке, тем более стойкие и прочные изделия можно получить. Достигается это многократной ковкой в разных направлениях, а контролируется современными методами металлографического анализа. В древние же времена только появление на поверхности клинка коленчатого или сетчатого узора указывало мастеру на совершенство приемов ковки. Постичь их было не легко. Опыт и умение приобретались годами, передавались из рода в род и хранились в глубокой тайне.
Из глубины столетий до нас дошел единственный способ ковки, которым в древности получали йеменские мечи с волокнистыми узорами, называемые «фарандом» или «мухаввас» (ткань с переливчатым оттенком). Вутц ковали не в длину, а начиная с одного конца, пока не расплющивали на блюдо. Блюдо разрезали по спирали, и полученные округлые полосы выравнивали. Из них ив" вали мечи.
Возможно, что П. П. Аносов скрывал способы проковки своих клинков. Во всяком случае в работе «О булатах» много внимания уделяется режимам нагрева стали перед горячей деформацией, а ковка описывается предельно кратко: слиток рассекают зубилами на три части, разрубленные части «проковывают в правильные бруски, а потом в полосы». И это все. *
П. П. Аносов, безусловно, знал работы Бреана в Мериме, опубликованные в первой четверти XIX века, в которых своеобразие булатных узоров объяснялось только приемами ковки. «Я на опыте убедился,— сообщая Бреан в 1823 году, что волнистые жилки, которые кузнецы называют коленами, являются результатами приема ковки. Если ограничиваться вытяжкой в длину, то жилки будут продольные, если же тянуть одинаково не всех направлениях, то рисунок имеет кристаллический вид; если же видоизменить вытяжку в двух направлениях, то получатся переходы, как в восточных булатах. Не нужно долгих опытов, чтобы достигнуть получения какого угодно узора».
Последнее утверждение неверно, и Мериме в более поздней работе совершенно правильно уточняет: «Что касается причудливости узора, то он является результатом работы молота при вытяжке, требующей много времени и искусства, чем и объясняется высокая цена клинков».
О своем искусстве получения различных видов булатных узоров П. П. Аносов не рассказывает...
В более поздних исследованиях неоднократно подчеркивалось, что получение булатов с коленчатыми и сетчатыми узорами связано с применением сложных, не известных нам приемов ковки. Так, например, Г. А. Кащенко в 30-х годах нашего столетия писал: «Внешним признаком булатной стали является красивый, видимый простым глазом узор. Этот узор представляет собой макроструктуру стали, называемую коленчатой или булатной. Она получалась, по-видимому, путем энергичной и многосторонней ковки, проводимой в особых условиях. При этом металл претерпевал глубокое обжатие в разных направлениях, в силу чего в металле уничтожается слабость, связанная с односторонней волокнистостью... Попытки воспроизвести булатную сталь, делавшиеся еще 100 лет назад и в более позднее время, приводили к успеху, хотя и неполному, так что процесс ковки булата является до сих пор не вполне выясненным...»
Интересно, что на нерешенность этого вопроса даже в 1978 году указывал немецкий металлург М. Захсе.
Между тем советскому металлургу Р. А. Лиждвою удалось раскрыть механизм одного из способов формирования булатного узора. Он изобрел и разработал приемы кузнечной вытяжки с направлением подачи слитка (заготовки) под острым или прямым углом к фронту бойков молота. Этот способ, известный под названием «косая ковка», позволяет сочетать вытяжку металла в двух направлениях с его протяжкой вдоль оси заготовки. Р. А. Лиждвой экспериментально показал, что при протяжке металла вначале под прямым, а затем под острым углом к фронту бойков или с произвольным изменением угла подачи заготовки в пределах 45—90° формируется текстура, соответствующая узору волнистого булата.
Старший реставратор Владимиро-Суздальского музея-заповедника В. И. Басов выплавил тигельным способом высокоуглеродистую сталь с содержанием углерода 1,3—1,9%. В результате замедленной кристаллизации слитка этой стали была получена высокая степень дендритной ликвации углерода. Проковкой стали путем нанесения крестообразных ударов под углом 45° к оси проковываемой заготовки был получен клинок с узором, очень похожим на сетчатый булат. Правда, в связи с тем что резкой физической неоднородностью сталь, по-видимому, не обладала, узор на клинке проявился не совсем четко.
Макроструктура полученных нами булатных слитков (см. фото 5, 6) гарантировала хорошее проявление узора после ковки. Для получения различных узоров (фото 7) мы использовали круглые бойки и фасонные штампы, а также оригинальный метод горячей деформации, о котором будет рассказано позже.
Применяли ли древние кузнецы фасонные штампы? Да, применяли. Археологические находки свидетельствуют, что при изготовлении сложных поковок в IX—Х веках должны были обязательно участвовать два инструмента: фигурные подкладки и фасонные штампы.
Наши исследования показали, что наиболее удобными для ковки являются круглые слитки диаметром 100—140 мм и длиной 150—240 мм. Перед деформацией их поверхность счищалась абразивами. Если после удаления верхней корки на поверхности слитка обнаруживали дефекты, они также удалялись. Перед ковкой для повышения пластичности металла при деформации слитки отжигали. Нагрев слитков под ковку осуществлял ли очень медленно. Так же, как это делал П. П. Аносов, слитки сажали в камерную печь при температуре 200°С и в течение 2—3 часов нагревали до 600°С. Последующий прогрев слитков с 600 до 900—1080°С осуществляли в течение 2 часов. Промежуточный нагрев металла во время ковки производили так, чтобы слитки в продолжение 20—30 минут нагревались до необходимой температуры.
Ковку нагретых слитков производили легкими ударами на молоте 750 кг. Слиток первый раз проковывали на полосу сечением 50Х50 или круг диаметром 50—60 мм. После расковки подприбыльную часть, длиной до 1/3 длины полученной штанги, удаляли. После вторичного нагрева штангу проковывали на полосу сечением 70Х20 или круг диаметром — 20 мм.
С целью более четкого выявления макроструктуры поковки отжигали по следующему режиму: медленный нагрев до 780—800°С, выдержка при этой температуре 5—6 часов, охлаждение в печи до 600°С и последующее охлаждение на воздухе.
В первых экспериментах мы обычными методами ковки вытягивали слиток в полосу. На поковках после шлифовки и травления поверхности слабым раствором соляной кислоты появлялся полосатый узор, характерный для низших сортов булата. На фото 8 показан нож, сделанный из нашего булата типа шам. Светлые полосы на темном фоне — участки малоуглеродистой стали (железа) в объеме высокоуглеродистой основы. Рисунок на этом ноже очень напоминает узор на аносовском кинжале (см. фото 3).
Поскольку светлые полосы обычно вытягивались по волокну вдоль лезвия клинка, на лезвие древние мастера старались выводить высокоуглеродистый участок металла. Такое лезвие после закалки на мартенсит приобретало значительную твердость, но самозатачивающим свойством не обладало. Возможно, что прожилки железа в таком булате обеспечивали клинку только повышенную вязкость.
Для превращения полосатого рисунка в волнистый мы обжимали ребра заготовки круглым прутком, после чего края вырезали. Коленчатый узор получали путем горячего скручивания заготовки и последующего ее обжатия.
По предложению Ю. И. Люндовского, часть заготовок перед горячей деформацией подвергали местному нагреву токами высокой частоты. Пруток диаметром 1.5—20 мм устанавливали в одновитковый кольцевой индуктор диаметром до 50 мм. Концы бруска фиксировали в зажимах. На расстоянии 20 мм от конца заготовку нагревали токами высокой частоты. Нагреву подвергался участок шириной 15—20 мм. После достижения температуры 1000 —1050°С пруток скручивали в направлении по часовой стрелке на угол 90°. Затем заготовку перемещали вдоль ее оси на 20 мм, нагревали соседний участок и скручивали в направлении против часовой стрелки на такой же угол. Таким же образом производили нагрев и деформацию скручиванием во взаимно противоположных направлениях отдельных участков всей заготовки. После этого заготовку либо обжимали фасонными штампами, либо просто проковывали на толщину 5—8 мм и вырезали пластины, из которых изготовляли клинки и другие изделия.
Клинок, изготовленный этим способом, имел ярко выраженный узор с гроздевидными фигурами, принимающий форму мотков и прядей, выступающих прозрачной сеткой на более темном фоне рисунка. Это был узор типичного кара-табана (черный блестящий)—лучшего индийского булата.
Усвоив найденные приемы ковки булатных слитков и добившись многократной повторяемости булатных узоров на основе ферритных прослоек, мы приступили к изучению узоров, получающихся на булатах с углеродистыми прослойками. Узор на таких булатах выявлялся более глубоким травлением, получался более выпуклым и тонким, но менее выразительным, так как цвет углеродистых прожилок не сильно отличался от цвета высокоуглеродистой матрицы. Кроме того, эти булаты обладали значительно худшей пластичностью, их было тяжелее деформировать, и это затрудняло получение сетчатых и коленчатых узоров.
Волнистый рисунок на клинках, приготовленных П. Н. Швецовым, очень похож на полученный нами рисунок булата с углеродистыми прослойками (фото 9). Аналогичные рисунки нами были получены на топорике и кортиках (фото 10, 11). Металлографическим анализом было подтверждено и сходство их микроструктур. Таким образом, скорее всего П. Н. Швецов высших сортов булата типа табан и хорасан получать не умел.
Сохранились сведения, что П. Н. Швецов при приготовлении булатов «железо предпочитал в виде гвоздей, листов, но при непременном условии — без ржавчины». Это дает основание предполагать, что при приготовлении булатов он пользовался приемами, описанными П. П. Аносовым. Однако температура в печи Сименса, куда ставились тигли во времена П. Н. Швецова, была достаточно высокой, и поэтому кусочки железа могли почти полностью расплавляться и науглероживаться. Все же в этих условиях, по-видимому, можно было добиться некоторой неоднородности стали по углероду; но слитков с включениями из железа (феррита), изготовить уже было невозможно. С другой стороны, если мастер не вынимал тигель со сталью из печи вовремя, у него выходила обычная углеродистая сталь. Вот почему булат у П. Н. Швецова получался не всегда.
В свете вышеизложенного легко объяснить замечание П. П. Аносова о том, что «твердый булат переходит от перегревки прямо в чугун, а мягкий в сталь». Перегрев булатов перед ковкой обеспечивает высокую скорость диффузии углерода, которая может полностью устранить неоднородность булата и «стереть» его узоры.
Когда П. П. Аносов
|
|
История развития хранилищ для нефти: Первые склады нефти появились в XVII веке. Они представляли собой землянные ямы-амбара глубиной 4…5 м...
Общие условия выбора системы дренажа: Система дренажа выбирается в зависимости от характера защищаемого...
Папиллярные узоры пальцев рук - маркер спортивных способностей: дерматоглифические признаки формируются на 3-5 месяце беременности, не изменяются в течение жизни...
Таксономические единицы (категории) растений: Каждая система классификации состоит из определённых соподчиненных друг другу...
© cyberpedia.su 2017-2024 - Не является автором материалов. Исключительное право сохранено за автором текста.
Если вы не хотите, чтобы данный материал был у нас на сайте, перейдите по ссылке: Нарушение авторских прав. Мы поможем в написании вашей работы!