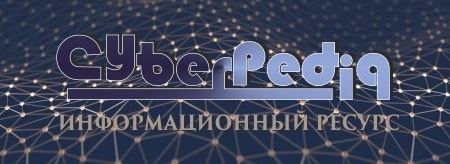
Таксономические единицы (категории) растений: Каждая система классификации состоит из определённых соподчиненных друг другу...
Семя – орган полового размножения и расселения растений: наружи у семян имеется плотный покров – кожура...
Топ:
Проблема типологии научных революций: Глобальные научные революции и типы научной рациональности...
Марксистская теория происхождения государства: По мнению Маркса и Энгельса, в основе развития общества, происходящих в нем изменений лежит...
Генеалогическое древо Султанов Османской империи: Османские правители, вначале, будучи еще бейлербеями Анатолии, женились на дочерях византийских императоров...
Интересное:
Средства для ингаляционного наркоза: Наркоз наступает в результате вдыхания (ингаляции) средств, которое осуществляют или с помощью маски...
Наиболее распространенные виды рака: Раковая опухоль — это самостоятельное новообразование, которое может возникнуть и от повышенного давления...
Аура как энергетическое поле: многослойную ауру человека можно представить себе подобным...
Дисциплины:
![]() |
![]() |
5.00
из
|
Заказать работу |
|
|
Основная цель замачивания зерна состоит в увеличении его влагосодержания до 43–47 % к общей массе. Кроме того, при рациональном ведении замачивания в чане осуществляются следующие операции:
1) мокрая очистка (мойка) зерна;
2) обработка зерна антисептиками;
3) активизация жизнедеятельности зерна.
При этом удаляются оставшиеся после очистки и сортирования легкие зерновые и незерновые примеси. Зерно при замачивании дезинфицируют и доводят до влажности, оптимальной для солодоращения.
Для осуществления указанных операций чан должен быть оборудован водяной и воздушной коммуникациями для подачи свежей воды и сжатого воздуха, устройствами для аэрации, перемешивания
и перекачивания зерна.
Если влажность зерна не более 14 %, то вся вода в нем находится в связанном состоянии и ее достаточно только для поддержания жизнеспособности зерна. При влажности, превышающей 15 %, в зерне появляется свободная вода, в которой начинают растворяться питательные вещества и перемещаться к зародышу. Таким образом, с появлением свободной воды ускоряются биохимические процессы, связанные с жизнедеятельностью зародыша, усиливается дыхание зерна, активируется деятельность ферментов.
При замачивании в воду переходят сахара, пентозаны, азотистые и минеральные вещества, всего теряется около 1 % сухих веществ зерна. Кроме того, со сплавом уносится от 1 % до 2 % сухих веществ зерна.
С увеличением содержания воды сильно возрастает энергия дыхания зерна. Например, при аэробном дыхании, когда реакция протекает при избытке кислорода, в процессе замачивания 1 кг зерна за 1 ч поглощает 63 мг кислорода. При таком дыхании имеющегося в воде кислорода достаточно только на 15 мин, поэтому для поддержания нормального дыхания в замочную воду подают сжатый воздух.
|
Если же кислорода в воде недостаточно, то может наступить анаэробное дыхание, при котором происходит более быстрое разрушение запасных веществ зерна с образованием этилового спирта и диоксида углерода. Даже в очень малых количествах спирт тормозит развитие зародыша зерна, а при концентрации спирта 0,8 % рост зародыша подавляется.
На скорость замачивания сильно влияет температура воды: чем она выше, тем быстрее проникает вода в зерно. Например, при температуре воды 15 °С продолжительность замачивания зерна на 1/3 короче, чем при 10 °С. Поэтому оптимальной температурой замачивания принято считать 10–12 °С, так как при более низкой температуре сильно тормозится развитие зародыша, а при более высокой – интенсивно развиваются микроорганизмы.
В процессе замачивания в зерне происходит глубокая перестройка всего ферментативного комплекса, активирование ферментов, особенно амилолитических и протеолитических. Изменяется также состояние белковых веществ, в зерне уменьшается содержание нерастворимых соединений, а растворимых – увеличивается. Замачивание зерна можно считать первой стадией его проращивания.
Моечный аппарат для зерна (рисунок 3.2) состоит из цилиндрического корпуса 4, вертикального привода со шнеком 3, сливной коробки 2 и выпускного устройства 1. Перемешивание зерна в целях его мойки и насыщения кислородом осуществляется с помощью моечного устройства 5.
![]() | Мойка зерна в этом чане достигается посредством интенсивной перекачки его с водой пропеллером, быстро вращающимся в широкой центральной трубе. Пропеллер при нормальном заполнении аппарата зерном находится выше уровня зерна в водяном слое. Поэтому при пуске ротора вначале перекачивается только вода, которая затем увлекает за собой и зерно. Вследствие ускоренного движения воды относительно зерна и трения частиц зерна между собой мойка происходит весьма энергично. Аппарат предварительного замачи-вания предназначается только для мойки и |
поэтому он устанавливается совместно с замочными чанами.
|
Замочный чан (рисунок 3.3) представляет собой стальной цилиндрический сосуд с коническим днищем.
В центре чана установлена вертикальная труба 1 для перекачивания зерна. Снизу в расширенный конец трубы трубка 2 подводит сжатый воздух под давлением до 0,3 МПа. На верхнем конце трубы укреплено сегнерово колесо 3. На поверхности конического днища расположены кольцевые барботерные трубки 4. Сжатый воздух подводят к ним по трубкам 5. В нижней части конического днища находится стальная решетка 6 для задержки зерна при спуске в трубу 7.
Чан наполняют водой снизу через решетку 6. Грязную воду со всплывшими легковесными зернами удаляют через вырез 8 в верхней
кромке чана. Сплавное зерно улавливают в общей для всех чанов ловушке с решетчатым днищем или в небольших сливных коробках
с сетчатыми корзинами при каждом чане. Замоченное зерно спускают из чана через отверстие 9, закрываемое конусом 10.
Мойка зерна в чане происходит следующим образом. В чан, наполовину заполненный водой, насыпают зерно, затем снизу через решетку 6 подают свежую воду. Загрязненную воду удаляют через вырез в верхней части чана. Одновременно с пропусканием воды через барботерные трубки 4 поступает сжатый воздух для перемешивания зерна. Для перекачивания зерна снизу вверх подают сжатый воздух по трубке 2 в центральную трубу 1. В этой трубе образуется смесь воды, зерна и пузырьков воздуха. Эта смесь, имея меньшую плотность, чем смесь воды и зерна, окружающая трубу, вытесняется вверх. Сегнерово колесо, вращаясь равномерно, распределяет перекачиваемое зерно по периферии чана. Углекислоту, накапливающуюся во время воздушного замачивания зерна в нижней части чана, спускают по трубе 7 или отсасывают вентилятором.
В таком аппарате перед замачиванием можно проводить и мойку зерна. При любом способе замачивания зерно должно быть предварительно промыто. Для этого чистый замочный аппарат на 1/3 объема заполняют водой и тонкой струей засыпают туда зерно, доливая аппарат водой с таким расчетом, чтобы уровень ее был выше зерна. Первая вода предназначена для промывания зерна, в ней оно находится
1–1,5 ч. За это время всплывает легкое зерно и примеси, которые тут же удаляются. После этого зерно моют вторично, вытесняя первую грязную воду чистой, подаваемой снизу. Затем в воду в аппарате добавляют концентрированные растворы дезинфицирующих веществ
и оставляют зерно на 2–3 ч.
|
Способы замачивания
Замачивание промытого и продезинфицированного зерна проводят воздушно-водяным способом в непрерывном потоке воды и воздуха оросительным и воздушно-оросительным способами при температуре не ниже 12 °С и не выше 17 °С.
При воздушно-водяном замачивании зерно попеременно находится то под водой (водяное замачивание), то без нее (воздушное замачивание). Такое чередование повторяется через каждые 3–6 ч. Для поддержания аэробного дыхания через зерно каждый час в течение 10 мин продувают воздух независимо от того, находится ли оно под водой или на воздухе. Через 8 ч зерно вместе с замочной водой перемешивают
сжатым воздухом в течение 40 мин, перекачивая смесь через центральную трубу замочного аппарата.
Замачивание зерна в непрерывном потоке воды и воздуха. Для замачивания зерна в непрерывном потоке воды и воздуха в трубопроводе для воды монтируют смеситель воды и воздуха, куда подводят сжатый воздух. Воду, насыщенную воздухом, подают в аппарат снизу в таком количестве, чтобы на поверхности воды непрерывно проскакивали пузырьки воздуха. В этом случае зерно снабжается кислородом непрерывно. При работе по этому способу замачивание зерна происходит быстрее, чем при воздушно-водяном.
При оросительном замачивании после мойки и удаления сплава поверхность зерна в замочном аппарате непрерывно орошается распыляемой водой, подаваемой через медленно вращающееся сегнерово колесо. Вода при распылении насыщается воздухом, проходит через слой зерна, увлекая с собой накопившийся диоксид углерода, выводится снизу. Зерно находится под водой первые 6–8 ч, остальное время вода поступает через оросительное устройство.
При оросительном замачивании в высоких аппаратах зерно замачивается и прорастает неравномерно: в верхних слоях быстро, в нижних остается недомоченным.
Воздушно-оросительное замачивание. Зерно периодически орошается водой, а путем отсоса воздуха из межзернового пространства создаются стабильные условия аэробного дыхания зерна. Этот способ замачивания осуществляется в следующем порядке: чисто вымытое зерно вначале оставляют под водой на 4 ч, спускают воду, в течение 18–20 ч орошают водой с периодическим аэрированием. Затем попеременно оставляют то под водой на 2–4 ч, то без воды на 12–20 ч с орошением. Зерно орошают в аппарате водой через форсунки или через сегнерово колесо в течение 15 мин, затем из нижней части аппарата вакуум-насосом отсасывают воздух в течение 15 мин и после этого создают продолжительную (1 ч) воздушную паузу, когда зерно находится в покое.
|
Расчет замочного чана
Для мойки и замачивания зерна используются специальные аппараты разных конструкций. Как моечные, так и замочные аппараты изготовляют из листовой стали толщиной 4–6 мм и обрабатывают специальным покрытием, исключающим коррозию металла.
Объем замочного аппарата рассчитывается с учетом объема замачиваемого зерна, увеличения объема материала на 40 % при росте
его влагосодержания до 45 % и дополнительного объема для нормального ведения замачивания (10–15%). Общая вместимость всех замочных аппаратов рассчитывается с учетом общей продолжительности замачивания, включающей время на заполнение аппаратов, выгрузку
и мойку.
В крупных чанах при большой глубине выделяется значительное количество углекислоты, которая тормозит развитие зерна. Однако интенсивным перемешиванием и аэрацией зерна отрицательное влияние углекислоты и высокого слоя зерна на качество замочки можно исключить. Поэтому на крупных солодовенных заводах имеются чаны емкостью до 65 т.
Объем замочного чана
, (3.1)
где – масса замоченного зерна, кг;
– насыпная плотность зерна, кг/м3, (650–750).
Масса замоченного зерна
, (3.2)
где – масса сухих веществ замоченного зерна, кг;
– потери сухих веществ со сплавом и на выщелачивание при замачивании, %;
– влажность замоченного зерна, %.
Масса сухих веществ замоченного зерна
, (3.3)
здесь – масса сортированного зерна, кг;
– влажность сортированного зерна, %.
При проектировании замочного отделения вместимость одного замочного аппарата можно рассчитать по формуле
, (3.4)
где – диаметр аппарата, м;
– высота цилиндрической части, м (
);
– высота конической части, м.
Диаметр аппарата находится из уравнения (3.4) при условии, что угол, образующий конус с горизонтом, равен 450. При этом угле высота конической части
.
Для определения количества аппаратов, которое необходимо для данного производства, следует разделить общую продолжительность замачивания, выраженную в часах, на период времени от одной замочки до другой. К расчетному числу чанов желательно добавить еще один чан – запасный, который позволит производить дезинфекцию чанов, их осмотр и ремонт без снижения производительности замочного отделения.
|
Число замочных аппаратов в зависимости от продолжительности замачивания
, (3.5)
где – продолжительность мойки и замачивания, ч.
При получении солода продолжительность мойки и дезинфекция зерна 64 ч, а продолжительность замачивания в непрерывном токе воды и воздухе 48–72 ч.
Расход воды на замачивание зерна зависит от способа замачивания, температуры воды, загрязненности зерна и др. Вследствие многообразия режимов работы расход воды для замачивания непостоянен. Его можно определить приближенно. Чем меньше производится смен воды, чем теплее вода, и чем менее загрязнено зерно, тем меньше расходуется воды. При мойке зерна обычно требуется воды больше, чем при каждой последующей смене, так как грязную воду приходится спускать из аппарата, пока она не станет совершенно чистой.
Для ориентировочного расчета количества воды, расходуемого на замачивание зерна, можно применить опытные данные (таблица 3.1).
Таблица 3.1 – Расход воды на замачивание
Наименование операции | Расход воды (м3/т) |
Первая смена воды (мойка зерна) | 1,2–2,0 |
Каждая последующая смена воды (замачивание зерна) | 0,8–1,2 |
Общий расход воды (м3/ч) складывается из расхода на промывку зерна (первое замачивание) и расходов воды при ее сменах во время замачивания
:
, (3.6)
где – число смен воды при замачивании.
В зависимости от технологии замачивания воду меняют от 4 до
10 раз.
Для замачивания зерна расход сжатого воздуха принимают в соответствии с таблицей 3.2 при условии, что он охлажден в оросительных камерах кондиционеров.
Таблица 3.2 – Расход сжатого воздуха на замачивание 1 кг зерна
Операция | Расход сжатого воздуха на 1 кг зерна, м3/(кг.ч) (при 20 0С и давлении 0,1 МПа) | Рабочее давление сжатого воздуха, МПа |
Мойка зерна | 0,033 | 0,15 |
Сухая продувка | 0,037 | 0,10 |
Влажная продувка | 0,052 | 0,15 |
Перемешивание зерна | 0,039 | 0,15 |
Перекачивание зерна | 0,031 | 0,30 |
Замачивание зерна: при непрерывном токе воды и воздуха оросительное | 0,043 | 0,15 |
0,033 | 0,15 |
Расход сжатого воздуха на 1 кг зерна при мойке и замачивании ориентировочно можно принимать в пределах Р =0,04¸0,06 м3/(кг.ч). Расчет общего часового расхода сжатого воздуха при рабочем давлении ведут в пересчете на нормальное давление по формуле
, (3.7)
где – расход сжатого воздуха на 1 кг зерна соответственно при мойке и замачивании, м3/(кг.ч);
– плотность воздуха при рабочем и нормальном давлениях, кг/м3.
Расход энергии на аэрирование. В ходе процесса замачивания для достижения заданного технологического эффекта необходимо обеспечивать интенсивное перемешивание среды в объеме аппарата. Поэтому на аэрационную систему помимо функции подвода заданного количества кислорода также возлагается функция по пневматическому перемешиванию среды, в результате чего достигается равномерное распределение зерновой массы по объему аппарата, увеличение скорости сорбции кислорода и т.д.
Осуществление процесса перемешивания требует подвода энергии. При этом достигается определенный эффект – увеличение производительности или при той же производительности повышение качества
готового продукта. Расчет мощности (кВт), необходимой для привода воздуходувки при пневматическом перемешивании, ведут по формуле
, (3.8)
где – количество подаваемого воздуха, определяемое из условия необходимого его количества в процессе замачивания, м3/с;
– гидравлическое сопротивление системы, Па;
– КПД воздуходувки.
Воздух, поступающий в аппарат, должен обладать давлением, достаточным для преодоления гидростатического давления столба жидкости в аппарате, создания скоростного напора и преодоления сопротивлений трения [6]. Давление воздуха должно удовлетворить уравнению
, (3.9)
где – давление столба перемешиваемой жидкости, Па;
– гидравлическое сопротивление барботера, Па;
– перепад давлений, обусловленный поверхностным натяжением в отверстиях барботера, Па.
Давление столба перемешиваемой жидкости
, (3.10)
где – плотность перемешиваемой жидкости, кг/м3;
– высота столба перемешиваемой жидкости, м.
Гидравлическое сопротивление барботера
, (3.11)
где – плотность газа (воздуха), кг/м3;
– скорость воздуха в отверстиях барботера, м/с;
– сумма коэффициентов сопротивления трубопроводной системы.
Перепад давлений, обусловленный поверхностным натяжением в отверстиях барботера
, (3.12)
где – поверхностное натяжение жидкости, Н/м;
– диаметр отверстий, м.
Расчет аэрационной системы. При расчетах воздухораспределительной системы исходят из следующих предпосылок [7, 8]: скорость движения воздуха в воздуховоде принимается в пределах от 20 до 25 м/с, площадь выходных отверстий воздухораспределительных трубок должна превышать площадь сечения стояка на 25 %. Воздух при этом подается в объем, где происходит перемешивание, через специальные устройства – барботеры.
Диаметр нагнетательного трубопровода
. (3.13)
Суммарная площадь отверстий в воздухораспределительных трубках при условии, что площадь воздухопропускных отверстий должна быть в сумме более площади стояка (коллектора) на 25 %:
, (3.14)
где – диаметр коллектора, м.
Геометрические параметры воздухораспределительных трубок определяются следующим образом. Воздухораспределительные трубки барботера имеют отверстия размером . Тогда количество отверстий для выпуска воздуха
. (3.15)
Число отверстий на 1 м длины трубки
, (3.16)
где – число рядов отверстий в поперечном сечении трубки;
– количество рядов отверстий на 1 м длины трубок.
Общая длина трубок барботера
. (3.17)
В зависимости от типа барботера определяются его геометрические размеры.
Диаметр аэрационной системы
, (3.18)
где – диаметр аппарата, м;
– расстояние между наружным диаметром барботера и обечайкой аппарата, м.
|
|
Адаптации растений и животных к жизни в горах: Большое значение для жизни организмов в горах имеют степень расчленения, крутизна и экспозиционные различия склонов...
Автоматическое растормаживание колес: Тормозные устройства колес предназначены для уменьшения длины пробега и улучшения маневрирования ВС при...
Своеобразие русской архитектуры: Основной материал – дерево – быстрота постройки, но недолговечность и необходимость деления...
Наброски и зарисовки растений, плодов, цветов: Освоить конструктивное построение структуры дерева через зарисовки отдельных деревьев, группы деревьев...
© cyberpedia.su 2017-2024 - Не является автором материалов. Исключительное право сохранено за автором текста.
Если вы не хотите, чтобы данный материал был у нас на сайте, перейдите по ссылке: Нарушение авторских прав. Мы поможем в написании вашей работы!