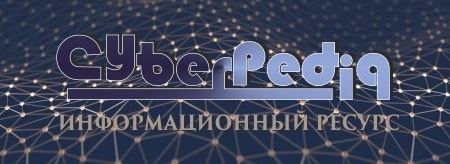
Типы оградительных сооружений в морском порту: По расположению оградительных сооружений в плане различают волноломы, обе оконечности...
Своеобразие русской архитектуры: Основной материал – дерево – быстрота постройки, но недолговечность и необходимость деления...
Топ:
Проблема типологии научных революций: Глобальные научные революции и типы научной рациональности...
История развития методов оптимизации: теорема Куна-Таккера, метод Лагранжа, роль выпуклости в оптимизации...
Интересное:
Влияние предпринимательской среды на эффективное функционирование предприятия: Предпринимательская среда – это совокупность внешних и внутренних факторов, оказывающих влияние на функционирование фирмы...
Уполаживание и террасирование склонов: Если глубина оврага более 5 м необходимо устройство берм. Варианты использования оврагов для градостроительных целей...
Лечение прогрессирующих форм рака: Одним из наиболее важных достижений экспериментальной химиотерапии опухолей, начатой в 60-х и реализованной в 70-х годах, является...
Дисциплины:
![]() |
![]() |
5.00
из
|
Заказать работу |
|
|
Методы исследования структуры металлов и сплавов
Внутреннее строение, или структуру, металлов и их дефекты изучают с помощью макроструктурного, микроструктурного, магнитного, люминесцентного, ультразвукового, рентгеновского и γ-дефектоскопического методов анализа.
Макроструктура — это строение металла, видимое невооруженным глазом или при небольшом увеличении с помощью лупы. Макроструктурный анализ используют для выявления формы и расположения зерен в литом металле, направления волокон в поковках и штамповках, местонахождения, размеров и форм нарушения сплошности, дефектов сварки, оценки толщины поверхностного слоя в изделиях, подвергнутых специальной поверхностной обработке, и др. Его осуществляют просмотром отшлифованной, отполированной и протравленной поверхности металлического изделия или макрошлифа (вырезанного из заготовки или металлоизделия темплета), поверхность которого шлифуют и протравливают.
Микроструктурный анализ — это исследование структуры металлов и сплавов с помощью микроскопов с увеличением от 1500 до 100000. Его осуществляют посредством изучения микрошлифов — вырезанных из металлоизделия или заготовки образцов, поверхность которых шлифуют, полируют и подвергают травлению специальными реактивами. При использовании электронных микроскопов рассматривают тонкий прозрачный слепок с микрошлифа — фольгу, или реплику.
В последнее время для исследования структуры и свойств металлов широко применяются методы фрактографии, позволяющие исследовать строение изломов, т. е. поверхностей, образующихся в результате разрушения металлоизделий или заготовок. Изломы изучают посредством макро- и микроструктурного анализа.
|
Магнитный метод (магнитная дефектоскопия) применяется для выявления трещин, волосовин, раковин и других дефектов, находящихся на поверхности (или близко около нее) изделий из ферромагнитных материалов. Сущность метода заключается в намагничивании изделия. Затем на поверхность наносится магнитный порошок окиси железа или его суспензия в керосине. Частицы порошка под действием магнитного потока, рассеивающегося в месте расположения дефекта, ориентируются по силовым линиям. В результате отчетливо выделяются даже самые мелкие дефекты.
Люминесцентный метод (люминесцентная дефектоскопия) используется для выявления поверхностных дефектов изделий (микротрещин). Он основывается на свойстве некоторых органических веществ светиться под действием ультрафиолетовых лучей. Сущность метода заключается в нанесении на поверхность изделия специального флуоресцирующего раствора и ее освещении ультрафиолетовым светом. Проникающий в микротрещины раствор под действием лучей светится, тем самым позволяя их выявить.
С помощью ультразвукового метода (ультразвуковая дефектоскопия) выявляют дефекты, расположенные глубоко в толще металла. Для этого используются ультразвуковые дефектоскопы, с помощью которых через толщу металла пропускают пучок ультразвуковых волн и контролируют их прохождение. Любая несплошность металла нарушает нормальное распространение волн, что можно увидеть на экране имеющегося в приборе осциллографа.
Рентгеновский метод (рентгеновская дефектоскопия) применяется для контроля литых, кованых и штампованных деталей, а также сварных соединений. Он заключается в просвечивании деталей рентгеновским излучением и фиксировании выходящего излучения на специальной светочувствительной пленке. При этом темные места на пленке свидетельствуют о наличии дефектов в исследуемых деталях. Разновидностью рентгеновского метода является γ-дефектоскопия.
|
2. Методы испытаний
Деффекты кристаллического строения.Классификация.влияние плотности несовершенств кристаллов на механические свойства
Основными линейными дефектами являются дислокации. Априорное представление о дислокациях впервые использовано в 1934 году Орованом и Тейлером при исследовании пластической деформации кристаллических материалов, для объяснения большой разницы между практической и теоретической прочностью металла.
Закономерности курнакова
Если отрезок оси абсцисс разделить на сто частей, то точки этого отрезка будут соответствовать процентному составу двойных сплавов. Если по оси ординат отложить температуру, то получим координатную сетку диаграммы фазового состояния. Каждая точка диаграммы состояния соответствует определенному составу сплава при заданной температуре. Линии на диаграмме состояния отмечают температуры изменения фазового состава, а поля, ограниченные этими линиями, характеризуют области существования различных фазовых состояний.
Диаграммы состояния показывают изменения фазового состояния сплавов при изменении их состава и температуры, а также позволяют предсказывать свойства сплавов. Связь между составом сплава и его свойствами для различных типов диаграмм состояния впервые была установлена Н. С. Курнаковым и получила название закономерностей Курнакова. Рассмотрим некоторые типы диаграмм состояния и связь свойств сплавов с их составом.
Как отмечалось выше, при изоморфности кристаллических решеток, близости строения валентных электронных оболочек атомов и малой разнице в размерах атомов в твердом состоянии элементы образуют неограниченные твердые растворы. Диаграммы состояния таких сплавов выглядят, как показано на рис. 22 а.
Рис.22. Диаграммы состояния и зависимость свойств от состава для случаев: а), б) неограниченной растворимости компонентов в твердом состоянии; в), г) отсутствия растворимости компонентов в твердом состоянии; д), е) ограниченной растворимости компонентов в твердом состоянии. |
Верхняя линия на диаграмме состояния представляет собой геометрическое место точек начала кристаллизации или конца плавления - линию ликвидус. Выше этой линии все сплавы находятся в однофазном - жидком состоянии. Нижняя линия является геометрическим местом точек конца кристаллизации или начала плавления - линия солидус. Ниже этой линии все сплавы также в однофазном - твердом состоянии. Поскольку при изменении состава сплавов фазовое состояние при низких температурах не меняется, то зависимость свойств от состава имеет вид плавной линии с максимумом. Зависимость свойств от состава (прочности, удельного электрического сопротивления, твердости) показана на рис. 22 б). Самостоятельно объясните зависимость свойств от состава, опираясь на представления о влиянии точеных дефектов на механические и электрические свойства металлических материалов.
|
Диаграмма состояния системы для случая, когда компоненты полностью не растворяются друг в друге в твердом состоянии и растворимы в жидком состоянии, показана на рис. 22 в). В данном случае линия ликвидус выглядит в виде ломаной, причем при некотором составе, называемом эвтектическим (от греческого слова эвтектикос - легкоплавкий), линия ликвидус касается линии солидус. Линия солидус представляет собой горизонтальную линию. Ниже линии солидус в сплава имеется две твердые фазы, являющиеся чистыми компонентами сплава. Поскольку компоненты не растворимы друг в друге, то свойства линейно меняются при изменении состава в соответствии с тем, как меняется количество фаз. Однако вблизи эвтектического состава наблюдается отклонение от линейного закона. Это связано с тем, что при кристаллизации эвтектических сплавов из жидкости одновременно выпадают две твердые фазы, и формируется мелкозернистая структура. Измельчение зерен ведет за собой увеличение электрического сопротивления и прочности эвтектических сплавов.
Для систем сплавов с ограниченной растворимостью характерны диаграммы состояния, показанные на рис. 22 д). В таких системах имеются две области существования фаз, представляющих раствор одного компонента в другом, и область существования смеси двух фаз. При составах, соответствующих областям существования твердых растворов на основе какого-либо компонента, изменения свойств аналогично изменению свойств в системах с неограниченной растворимостью компонентов, а в областях составов, соответствующих двухфазным смесям, изменение состава ведет к изменению свойств, характерному для систем с нерастворимыми в твердом состоянии компонентами.
|
Химический состав.
В зависимости от химического состава различают стали углеродистые (ГОСТ 380-71, ГОСТ 1050-75) и легированные (ГОСТ 4543-71, ГОСТ 5632-72, ГОСТ 14959-79). В свою очередь углеродистые стали могут быть:
· малоуглеродистыми, т. е. содержащими углерода менее 0,25%;
· среднеуглеродистыми, содержание углерода составляет 0,25-0,60%
· высокоуглеродистыми, в которых концентрация углерода превышает 0,60% Легированные стали подразделяют на:
1. низколегированные содержание легирующих элементов до 2,5%
2. среднелегированные, в их состав входят от 2,5 до 10% легирующих элементов;
3. высоколегированные, которые содержат свыше 10% легирующих элементов.
Назначение .
По назначению стали бывают:
· Конструкционные, предназначенные для изготовления строительных и машиностроительных изделий.
· Инструментальные, из которых изготовляют режущий, мерительный, штамповый и прочие инструменты. Эти стали содержат более 0,65% углерода.
· С особыми физическими свойствами, например, с определенными магнитными характеристиками или малым коэффициентом линейного расширения: электротехническая сталь, суперинвар.
· С особыми химическими свойствами, например, нержавеющие, жаростойкие или жаропрочные стали.
Качество.
В зависимости от содержания вредных примесей: серы и фосфора-стали подразделяют на:
1. Стали обыкновенного качества, содержание до 0.06% серы и до 0,07% фосфора.
2. Качественные - до 0,035% серы и фосфора каждого отдельно.
3. Высококачественные - до 0.025% серы и фосфора.
4. Особовысококачественные, до 0,025% фосфора и до 0,015% серы.
Степень раскисления.
По степени удаления кислорода из стали, т. е. По степени её раскисления, существуют:
· спокойные стали, т. е., полностью раскисленные; такие стали обозначаются буквами “сп” в конце марки (иногда буквы опускаются);
· кипящие стали - слабо раскисленные; маркируются буквами "кп";
· полу спокойные стали, занимающие промежуточное положение между двумя предыдущими; обозначаются буквами "пс".
Сталь обыкновенного качества подразделяется еще и по поставкам на 3 группы:
1. сталь группы А поставляется потребителям по механическим свойствам (такая сталь может иметь повышенное содержание серы или фосфора);
2. сталь группы Б - по химическому составу;
3. сталь группы В - с гарантированными механическими свойствами и химическим составом.
В зависимости от нормируемых показателей (предел прочности σ, относительное удлинение δ%, предел текучести δт, изгиб в холодном состоянии) сталь каждой группы делится на категории, которые обозначаются арабскими цифрами.
|
Стали обыкновенного качества обозначают буквами "Ст" и условным номером марки (от 0 до 6) в зависимости от химического состава и механических свойств. Чем выше содержание углерода и прочностные свойства стали, тем больше её номер. Буква "Г" после номера марки указывает на повышенное содержание марганца в стали. Перед маркой указывают группу стали, причем группа "А" в обозначении марки стали не ставится. Для указания категории стали к обозначению марки добавляют номер в конце соответствующий категории, первую категорию обычно не указывают.
Например:
Ст1кп2 - углеродистая сталь обыкновенного качества, кипящая, № марки 1, второй категории, поставляется потребителям по механическим свойствам (группа А);
ВСт5Г - углеродистая сталь обыкновенного качества с повышенным содержанием марганца, спокойная, № марки 5, первой категории с гарантированными механическими свойствами и химическим составом (группа В);
Вст0 - углеродистая сталь обыкновенного качества, номер марки 0, группы Б, первой категории (стали марок Ст0 и Бст0 по степени раскисления не разделяют).
Качественные стали маркируют следующим образом:
1 в начале марки указывают содержание углерода цифрой, соответствующей его средней концентрации;
а) в сотых долях процента для сталей, содержащих до 0,65% углерода;
05кп – сталь углеродистая качественная, кипящая, содержит 0,05% С;
60 – сталь углеродистая качественная, спокойная, содержит 0,60% С;
б) в десятых долях процента для индустриальных сталей, которые дополнительно снабжаются буквой "У":
У7 – углеродистая инструментальная, качественная сталь, содержащая 0,7% С, спокойная (все инструментальные стали хорошо раскислены);
У12 - углеродистая инструментальная, качественная сталь, спокойная содержит 1,2% С;
2 легирующие элементы, входящие в состав стали, обозначают русскими буквами:
А – азот К – кобальт Т – титан Б – ниобий М – молибден Ф- ванадий
В – вольфрам Н – никель Х – хром Г – марганец
П – фосфор Ц – цирконий Д – медь Р – бор Ю – алюминий
Е – селен С – кремний Ч – редкоземельные металлы
Если после буквы, обозначающей легирующий элемент, стоит цифра, то она указывает содержание этого элемента в процентах. Если цифры нет, то сталь содержит 0,8-1,5% легирующего элемента, за исключением молибдена и ванадия (содержание которых в солях обычно до 0,2-0,3%), а также бора (в стали с буквой Р его должно быть не менее 0,0010%).
Примеры:
14Г2 – низко легированная качественная сталь, спокойная, содержит приблизительно 14% углерода и до 2,0% марганца.
03Х16Н15М3Б - высоко легированная качественная сталь, спокойная содержит 0,03% C, 16,0% Cr, 15,0% Ni, до З,0% Мо, до 1,0% Nb.
Методы исследования структуры металлов и сплавов
Внутреннее строение, или структуру, металлов и их дефекты изучают с помощью макроструктурного, микроструктурного, магнитного, люминесцентного, ультразвукового, рентгеновского и γ-дефектоскопического методов анализа.
Макроструктура — это строение металла, видимое невооруженным глазом или при небольшом увеличении с помощью лупы. Макроструктурный анализ используют для выявления формы и расположения зерен в литом металле, направления волокон в поковках и штамповках, местонахождения, размеров и форм нарушения сплошности, дефектов сварки, оценки толщины поверхностного слоя в изделиях, подвергнутых специальной поверхностной обработке, и др. Его осуществляют просмотром отшлифованной, отполированной и протравленной поверхности металлического изделия или макрошлифа (вырезанного из заготовки или металлоизделия темплета), поверхность которого шлифуют и протравливают.
Микроструктурный анализ — это исследование структуры металлов и сплавов с помощью микроскопов с увеличением от 1500 до 100000. Его осуществляют посредством изучения микрошлифов — вырезанных из металлоизделия или заготовки образцов, поверхность которых шлифуют, полируют и подвергают травлению специальными реактивами. При использовании электронных микроскопов рассматривают тонкий прозрачный слепок с микрошлифа — фольгу, или реплику.
В последнее время для исследования структуры и свойств металлов широко применяются методы фрактографии, позволяющие исследовать строение изломов, т. е. поверхностей, образующихся в результате разрушения металлоизделий или заготовок. Изломы изучают посредством макро- и микроструктурного анализа.
Магнитный метод (магнитная дефектоскопия) применяется для выявления трещин, волосовин, раковин и других дефектов, находящихся на поверхности (или близко около нее) изделий из ферромагнитных материалов. Сущность метода заключается в намагничивании изделия. Затем на поверхность наносится магнитный порошок окиси железа или его суспензия в керосине. Частицы порошка под действием магнитного потока, рассеивающегося в месте расположения дефекта, ориентируются по силовым линиям. В результате отчетливо выделяются даже самые мелкие дефекты.
Люминесцентный метод (люминесцентная дефектоскопия) используется для выявления поверхностных дефектов изделий (микротрещин). Он основывается на свойстве некоторых органических веществ светиться под действием ультрафиолетовых лучей. Сущность метода заключается в нанесении на поверхность изделия специального флуоресцирующего раствора и ее освещении ультрафиолетовым светом. Проникающий в микротрещины раствор под действием лучей светится, тем самым позволяя их выявить.
С помощью ультразвукового метода (ультразвуковая дефектоскопия) выявляют дефекты, расположенные глубоко в толще металла. Для этого используются ультразвуковые дефектоскопы, с помощью которых через толщу металла пропускают пучок ультразвуковых волн и контролируют их прохождение. Любая несплошность металла нарушает нормальное распространение волн, что можно увидеть на экране имеющегося в приборе осциллографа.
Рентгеновский метод (рентгеновская дефектоскопия) применяется для контроля литых, кованых и штампованных деталей, а также сварных соединений. Он заключается в просвечивании деталей рентгеновским излучением и фиксировании выходящего излучения на специальной светочувствительной пленке. При этом темные места на пленке свидетельствуют о наличии дефектов в исследуемых деталях. Разновидностью рентгеновского метода является γ-дефектоскопия.
2. Методы испытаний
|
|
Особенности сооружения опор в сложных условиях: Сооружение ВЛ в районах с суровыми климатическими и тяжелыми геологическими условиями...
Своеобразие русской архитектуры: Основной материал – дерево – быстрота постройки, но недолговечность и необходимость деления...
Кормораздатчик мобильный электрифицированный: схема и процесс работы устройства...
Историки об Елизавете Петровне: Елизавета попала между двумя встречными культурными течениями, воспитывалась среди новых европейских веяний и преданий...
© cyberpedia.su 2017-2024 - Не является автором материалов. Исключительное право сохранено за автором текста.
Если вы не хотите, чтобы данный материал был у нас на сайте, перейдите по ссылке: Нарушение авторских прав. Мы поможем в написании вашей работы!