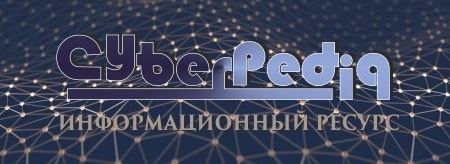
Архитектура электронного правительства: Единая архитектура – это методологический подход при создании системы управления государства, который строится...
История развития пистолетов-пулеметов: Предпосылкой для возникновения пистолетов-пулеметов послужила давняя тенденция тяготения винтовок...
Топ:
Отражение на счетах бухгалтерского учета процесса приобретения: Процесс заготовления представляет систему экономических событий, включающих приобретение организацией у поставщиков сырья...
Устройство и оснащение процедурного кабинета: Решающая роль в обеспечении правильного лечения пациентов отводится процедурной медсестре...
Марксистская теория происхождения государства: По мнению Маркса и Энгельса, в основе развития общества, происходящих в нем изменений лежит...
Интересное:
Средства для ингаляционного наркоза: Наркоз наступает в результате вдыхания (ингаляции) средств, которое осуществляют или с помощью маски...
Наиболее распространенные виды рака: Раковая опухоль — это самостоятельное новообразование, которое может возникнуть и от повышенного давления...
Что нужно делать при лейкемии: Прежде всего, необходимо выяснить, не страдаете ли вы каким-либо душевным недугом...
Дисциплины:
![]() |
![]() |
5.00
из
|
Заказать работу |
|
|
История развития мартеновского процесса.
Идея получения литой стали на поду отражательной печи высказывалась многими учеными (например, в 1722 г. Реомюром), но осуществить это долгое время не удавалось, так как температура факела обычного в то время топлива — генераторного газа — была недостаточной для нагрева металла выше 1500 °С (т.е. недостаточна для получения жидкой стали). В 1856 г. братья Сименс предложили использовать для подогрева воздуха тепло горячих отходящих газов, устанавливая для этого регенераторы. Принцип регенерации тепла был использован Пьером Мартеном для плавки стали. Началом существования мартеновского процесса можно считать 8 апреля 1864 г., когда П. Мартен на одном из заводов Франции выпустил первую плавку.
Уже в начале XX в в мартеновских печах выплавляли половину общего мирового производства стали. В России первая мартеновская печь была построена С. И. Мальцевым в 1866—1867 гг. на Ивано-Сергиевском железоделательном заводе (бывш. Калужской губернии) Мальцевского фабрично-заводского округа. В 1870 г. первые плавки проведены в печи вместимостью 2,5 т, построенной известными металлургами А. А. Износковым и Н. Н. Кузнецовым на Сормовском заводе. Эта печь хорошо работала и стала образцом для печей большой вместимости, построенных позже на других русских заводах. После Великой Октябрьской социалистической революции мартеновский процесс стал основным в отечественной металлургии. Огромную роль сыграли мартеновские печи в суровые годы Великой Отечественной войны. Советским металлургам впервые в мировой практике удалось удвоить садку мартеновских печей без существенной их перестройки (ММК, КМК), удалось наладить производство высококачественной стали (броневой, подшипниковой и т. п.) на действовавших в то время мартеновских печах.
|
Более чем столетний период развития мартеновского производства стали доказал высокое его совершенство и надежность.
В конце пятидесятых годов в СССР и в некоторых других странах появился и был реализован новый метод использования тепла отходящих из плавильного пространства продуктов сгорания топлива для нагрева скрапа. Так появился новый подовый сталеплавильный агрегат — двухванная печь. В некоторых странах, например в ЧССР, в Южно-Африканской республике, эти печи строят качающимися, они отапливаются относительно большим количеством топлива и их называют тандем-печами.
В СССР двухванные печи имеют емкость каждого плавильного пространства 250 или 300 т. Такие печи свободно размещаются в современных мартеновских цехах и имеют производительность в 2—2,5 раза выше, чем мартеновские печи, занимающие такую же площадь в цехе.
Благодаря своим качествам и невысокой стоимости мартеновская сталь нашла широкое применение.
Периоды плавки.
Процесс выплавки стали в март.печи при любой его разнов-ти вкл-т след-ие периоды: заправка печи, завалка, прогрев тв шихтовых матер-в, завалка тв чугуна или заливка жидкого, плавление, доводка (полировка и чистый кип плавки), раскисление и легир-е металла, выпуск Ме и шлака из печи в ковш и окончат-е раскисление и легир-е.
Заправка печи произв-ся для восстан-я изношенных за время плавки уч-в наварки передней и задней стенок и откосов. Заправку след-т произв-ть быстро и кач-но, не допуская заметного охлаж-я раб.пространства печи и насадок регенер-в, так как этим обесп-ся «горячий» ход печи, т.е. норм усл-я ее работы без уменьш-я стойк-ти фут-ки. Поэт заправку откоса задней стенки выше уровня шлака произв-т еще в период раскис-я предыдущ плавки, а заправку откосов на уровне шлака и ниже – в проц ее выпуска. Заправка должна нач-ся с мом-та, когда Ме пошел по желобу, и провод-ся максимально быстро. В период заправки значит-е сниж подачи топлива и охлажд-е печи не допуск-ся. В кач-ве заправ-х матер-в должны использ-ся периклаз-й и хромитопериклаз-й порошки, обожженный доломит. После выпуска металла оценивают состояние подины путем осмотра. При наличии остатков Ме и шлака на подине, следует произвести удаление их сжатым воздухом и подсыпку углублений мелкозернистыми заправ-ми матер-ми. После чего закрывается выпускное отверстие и нач-ся завалка шихты.
|
Завалка твердых шихтовых материалов и их прогрев практически опред-т горячий ход их плавл-я, его продолж-ть увелич-ся практ-ки пропорц-но величине отклонения завалки от оптим-го времени. Задачей завалки яв-ся оптимиз-я и уменьш-е длит-ти процесса, так как оптимальное время завалки позволяет произвести качественный прогрев материала в печи и не охладить насадки регенераторов ниже 1000 °С. Скорость завалки зависит от наличия в цехе ж/д составов с шихтовыми матер-ми, загружаемыми в мульды и поданными на площадку в том же порядке как будут загружаться в печь.
При выплавки стали скрап-рудным процессом завалку осущ-т в следующем порядке: на подину равномерным слоем загружают часть жел руды (агломераты или окатыши), затем слой известняка 5-7% (извести 3-5%) и оставш руду. В процессе завалки руду и известняк необходимо прогревать до полного удал-я влаги. При эт их нужно подвергать перемеш-ю. После завалки и прогрева руды и известняка необх-мо загружать стальной лом, сначала мелкий затем крупный. В проц завалки каждый слой металлошихты нужно тщательно прогревать.
При выплавке стали скрап-процессом, падину прикрывают метал-й стружкой или мелким железо-стальным ломом в кол-ве 15-25% от массы садки. Затем равномерно загружают известняк или известь в кол-ве 5-7% и 3-5% от массы садки соот-но. После прогрева заваливают остальной лом.
Заливка жидкого чугуна осущ-ся после прогрева шихт-х матер-в при помощи съемного или стацион-го желоба. Продолж-ть заливки чуг должна сост-ть 15-30мин. Чугун необх-мо заливать медленно иначе возможно бурное окис-е С и выброс шлака и Ме из печи.
Период плавления. Началом периода плавки след-т считать заливку жидк чугуна.Созд-е в период плавления оптим-х шлакового режима и баланса О2 позв-т в этот период провести основн часть рафинир-я Ме (обесп-ть требуемую степень дефосфорации Ме).
|
Продолж-ть плавления кроме емкости и тепловой мощности печи зависит от шлакового режима периода. Количество чугуна в шихте, темп-ра жидкого чугуна. Важным фактором при этом яв-ся степень нагрева тв шихты, особенно стального лома. При недостаточном их прогреве период плавления может значительно увеличиться.
Так как основность первичного шлака спускаемого в плавление невелика – 0,5-1. Густые шлаки необходимо исправлять бокситом, железорудными окатышами или окалиной, жидкий - присадкой извести.
Обычно продолж-ть периода плавл-я при выплавке стали на жидк чугуне должна сост-ть 2-3 часа. На тв чугуне–3-4 ч, т.к. для плавл-я чугуна требуется дополн-й расход тепла.
Если сод-е С в Ме по расплавл-ю металлошихты менее устан-го предела, то до начала доводки расплав нужно науглерож-ть путем вдувания порошков графита, кокса или электродн стружки. Их вводят в струе сжат.воздуха или азота через специальную трубу.
Период доводки плавки. Доводка обычно сост-т из 2х стадий: полировки (рудн кипения) и чистого (свободн) кипения.
Полировка -это по существу период наводки шлака для обеспечения требуемой степени десульфурации и завершения дефосфорации металла (к началу «чистого кипа» содержание фосфора в металле должно быть не более 0,010%).
Задачей этого периода является окончательное рафинированиие металла.
Началом «полировки» следует считать момент введения в Ме тв окислителя массой не менее 0,5 % от массы садки или начало продувки Ме сжатым воздухом. Наведение высокоосновного шлака следует производить присадкой шлакообразующих материалов (извести, боксита, плавикового шпата, загружаемыми порциями массой не более 1,5-2,5% от массы садки). Чтобы ускорить шлакообраз-е одновр-но присаж-т и жел руду (агломерат, окатыши). Продолж-ть периода полировки должна быть 30-60 мин.
Период чистого кипения необходим для окончательной подготовки металла к раскислению, легированию и выпуску. Началом «чистого кипа» следует считать энергичное кипение металла «ровными» пузырями не менее чем на 2/3 площади его открытой поверхности в ванне печи под основным жидкоподвижным шлаком. В это период С окисляется только кислородом газовой фазы печи. Продолж-ть чистого кипения необходимая для дегазации Ме должна составлять 40-60 мин.
|
Раскисление и легирование металла в печи
Раскисление и легирование проводят в печи. Для уменьшения угара раскисляющих и легирующих элементов металл предварительно раскисляют 25-45% ферросилицием. При этом продолжительность периода раскисления не должна превышать 25 минут, т.к. длительная выдержка металла в печи после раскисления способствует насыщению металла водородом с газовой фазой в печи. В период раскисления и легирования металла в печи допускается корректировка содержания в нем углерода присадками предельного чугуна, графита, молотого кокса, из расчета внесения углерода не более чем на 0,05% без учета угара.
Легирование и раскисление металла при выпуске плавки в ковш
Скорость выпуска плавки из март. печи должна находится в пределах 10-40 т/мин.
В ковше металл раскисляют 45% ферросилицием марки ФС45, силикомарганцем марки МнС17 присаживают на струю при выпуске плавки. Окончат-е раскисление производят чушковым алюминием вторичной марки АВ87 с содержанием алюминия не менее 87%, присаживаемым в кусках на струю металла в начале выпуска плавки. Ферросплав с легко окисляемыми Ме – Ti, Ca, B, V присаживают после Al.
Разливка стали произв-ся в изложницы, установл-е на поддоны, располож-е на ж/д тележках, сифонным способом, на слитки массой до 5 тонн.
Шихтовые материалы.
Разл-т метал-е и неМе составл-ие шихтовых материалов.
1.Металлическая группа шихтовых материалов.
Чугун используется в шихте мартеновских печей в твердом или жидком состоянии. Прим-ние чугуна в жидком состоянии возможно на заводах с доменным производством. Сод-е С в передельных чугунах сост-т 3,5–4,5%. ГОСТом предусмотрено также опред-е содерж-е Si. Окисление Si полож-но влияет на тепловой баланс мартеновского процесса. Однако его избыт сод-е нежелательно, так как это прив-т к увеличению расхода руды и известняка, получению большого количества шлака, увеличению износа футеровки печи и расхода заправочных матер-в. Чугуны с max содерж-м Si (до 1,25 %)могут исп-ся при скрап-процессе, поск-ку в шихту чугун входит в сравнительно небольшом кол-ве. Содерж-е Mn в чугуне нах-ся в широких пределах (0,2—1,75%). Предусмотренное в чугунах предельное сод-е Р (>0,3%) объясняется экономическими и технолог-ми требов-ми. С повыш-м содерж-я Р в чугуне (≤0,3 %) увелич-ся расход известняка, руды, извести для успешного осуществления проц-са дефосфорации, кот сопровождается длительным спуском большого кол-ва шлака из печи. Большое содерж-е S в чугуне (>0,07 %) приводит к увелич-ю продолж-ти плавки и пониж-ю производ-ти печи.
|
Стальной скрап подразд-т на внутренний оборотный (отходы сталеплав-х, прокатных, кузнечно-прессовых и др обрабатыв-х цехов своего завода) и привозной (покупной). Скрап подвергают предварит-й подготовке с получением оптим-х размеров и массы.
К металлической части шихты относятся также ферросплавы.
2.Неметаллическая группа шихтовых материалов.
· Флюсы. Флюсы применяют для образования и регулирования состава шлака в соответствии с требуемыми его физ и хим свойствами. В качестве флюса используют известняк, боксит, плавиковый шпат, бой шамотного кирпича.
Известняк сост-т преимущ-но из минерала кальцита и поэтому сод-т ~98 % СаСО3 (не менее 50 % СаО). Известняк вводят в состав шихты для удаления S и Р из Ме в шлак.
Известь прим-т для наводки шлака после расплав-я шихты. Состав извести опред-ся составом известняка, получ-ся в рез-те обжига. СаО в извести долж быть не менее 80%.
Боксит прим-т для разжижения шлака. Его вводят не то-ко в шихту, но и в ванну по ходу плавки. Основн составляющей боксита яв-ся глинозем, который и разжижает шлак.
Сод-т значит кол-во оксидов Fe, поэт яв-ся не то-ко флюсом, но и окислителем, т. е. при использ-ии боксита достиг-ся не то-ко разжижение шлака, но и ускор-ся шлакообраз-е.
Иногда для разжижения оч густых (содерж-х высокие конц-ции СаО) шлаков прим-ся плавиковый шпат. Основн составляющая плавик-го шпата – минерал флюорит CaF2.
· Тв окислители прим-т для ускорения окисления примесей метал-й ванны, в особенности при высоком содержании чугуна в шихте. К тв окислителям относятся: жел руда, окалина, марганцевые руды, мартеновский агломерат и офлюсованный агломерат.
Железная руда. К железной руде предъявляют след-ие треб-ия: 1) высокое сод-е оксидов железа (≥84 % Fe2О3) и небольшое количество пустой породы и вредных примесей.
Окалина, растворяющ-ся в шлаке, повыш-т содерж-е оксидов Fe и окислительную спос-ть, одноврем-но улучш-ся растворение извести в шлаке. Составл-й окалины яв-ся Fe3О4.
Агломерат, при его использ-ии в шихте вместо жел руды неск-ко раньше происх-т шлакообр-е, что до некоторой степени способствует удалению Р из Ме. К недост-м агломерата необх-мо отнести; пониж окислительный потенциал, малую плотность по сравнению с жел рудой и недостат-ю его прочность. Для ускорения усвоения агломерата шлаком иногда прим-т офлюсованный известью аглом-т или известково-рудные брикеты.
Завалка шихты и ее прогрев.
В состав шихты входят материалы, резко различающиеся по физическим свойствам. Наряду с обладающей относительно высокой теплопроводностью металлической частью шихты в ее состав входят менее теплопроводные неметаллические составляющие: известняк, руда, агломерат и т.д. Приведенный коэффициент теплопроводности этих кусковых материалов, учитывающий их большую неплотность, по крайней мере на порядок ниже, чем даже у неплотного скрапа. Кроме того, все компоненты неметаллической части шихты при их нагреве требуют огромное количество тепла на протекание таких процессов, как разложение карбоната кальция, разложение гидратов оксидов железа и глинозема и т. п., поэтому завалка шихты и распределение ее составляющих в объеме ванны представляют собой довольно сложную задачу, в особенности когда неметаллическая часть шихты составляет значительную долю ее массы и объема.
При скрап-процессе неметаллическую часть шихты заваливают на слой металлического мелкого лома, располагая известняк, боксит и т. д. не сплошным слоем, а отдельными участками. Сверху заваливают остальной лом (скрап) и, наконец, твердый чугун. При скрап-рудном процессе на подину заваливают железную руду, поверх нее известняк (руда в этом случае защищает подину от приваривания к ней известняка), затем прикрывают известняк оставшейся рудой и уже после этого заваливают весь скрап.
Слой скрапа имеет относительно большое тепловое сопротивление, так как ложится неплотно и многочисленные замкнутые пустоты значительно затрудняют теплопередачу к нижним слоям шихты.
При скрап-процессе прогрев шихты непосредственно переходит в ее плавление, причем первоначально шихта постепенно уплотняется и оседает, затем покрывается слоем первичного шлака и частично расплавившегося чугуна. После того как сравнивается поверхность ванны, протекает обычный процесс плавления.
При скрап-рудном процессе прогрев шихты имеет целью предотвращение намораживания жидкого чугуна на поверхности кусков скрапа и ускорение растворения хорошо прогретого скрапа в углеродистом расплаве.
Удаление S и Р.
Фосфор окисляется одновременно с кремнием и марганцем в начале плавки. Практически фосфор стремятся удалить из металла в период плавления и первой половине периода кипения, т. е. тогда, когда металл еще сильно не нагрелся. Для создания железисто-известкового шлака осуществляют присадку железной руды (или окалины, или агломерата) и извести или известняка.
Обычно для удаления фосфора до 0,010—0,015 % достаточно однократного скачивания шлака, но если фосфора в шихте много, то однократного скачивания шлака оказывается недостаточно. Скачивание шлака — операция сложная, поэтому высокофосфористую шихту предпочитают перерабатывать в качающихся мартеновских печах. В отличие от обычных стационарных печей рабочее пространство качающихся печей можно поворачивать относительно продольной оси. Печь может наклоняться в сторону выпускного отверстия примерно на 30—35° и в сторону передней стенки на 25°, что значительно облегчает скачивание шлака. Головки печи неподвижны; между неподвижными головками и качающимся рабочим пространством имеется зазор, размеры которого должны быть очень малыми. Шихта этих печей на 65—75 % состоит из фосфористого чугуна, содержащего 1,5—1,6% Р. Скачиваемый при переработке высокофосфористого чугуна шлак так же, как и шлак томасовского процесса, используют в качестве удобрения.
Десульфурация вследствие высокого содержания в мартеновских шлаках оксидов железа имеет ограниченное развитие. При обычной шихте получение в готовой стали <0,04 % S (требования ГОСТа для большинства марок) особых трудностей не представляет, однако получение более низких (<0,015—0,020 %) концентраций серы затруднительно. В связи с этим при выплавке металла с особо низким содержанием серы операцию удаления серы частично переносят в ковш. Особое внимание обращают на содержание серы в топливе. Применяемый для отопления коксовый газ обязательно подвергают операции сероочистки. Допустимое содержание серы в нем не должно превышать 2 г/м3. Для отопления мартеновских печей применяют низкосернистый мазут. Наиболее чистым (по содержанию серы) топливом является природный газ.
Рафинирование металла.
После полного расплавления шихты нач-ся сл-щий технологический период плавки — рафинирование Ме от примесей и получ-е стали заданного состава (марки).
В заводской практике этот период обычно наз-ют доводкой или полировкой. Доводку подразд-ют на периоды рудного (интенсивная продувка ванны кислородом) и безрудного (или чистого) кипения. Безрудное кипение должно обеспечить нагрев металла до темп-ры, необходимой д/нормальной разливки, выравнивание хим. состава и темп-ры Ме во всем его объеме. В теч-е периода выполняют экспресс-анализ металла.
При всех вариантах основного мартеновского процесса (и плавке в двухванной печи) кремний, содержащийся в чугуне или скрапе (особенно в легированных кремнием сталях; динамной, трансформаторной, рессорной и др.), успевает полностью окислиться и перейти в шлак еще до окончания плавления шихты. В период плавления удаляется также большая часть углерода, марганца и фосфора.
Таким образом, в период рафинирования из металла удаляются и переходят в газовую фазу или в шлак оставшиеся в металле следующие элементы: С, Mn, Р и S, иногда Сг.
История развития мартеновского процесса.
Идея получения литой стали на поду отражательной печи высказывалась многими учеными (например, в 1722 г. Реомюром), но осуществить это долгое время не удавалось, так как температура факела обычного в то время топлива — генераторного газа — была недостаточной для нагрева металла выше 1500 °С (т.е. недостаточна для получения жидкой стали). В 1856 г. братья Сименс предложили использовать для подогрева воздуха тепло горячих отходящих газов, устанавливая для этого регенераторы. Принцип регенерации тепла был использован Пьером Мартеном для плавки стали. Началом существования мартеновского процесса можно считать 8 апреля 1864 г., когда П. Мартен на одном из заводов Франции выпустил первую плавку.
Уже в начале XX в в мартеновских печах выплавляли половину общего мирового производства стали. В России первая мартеновская печь была построена С. И. Мальцевым в 1866—1867 гг. на Ивано-Сергиевском железоделательном заводе (бывш. Калужской губернии) Мальцевского фабрично-заводского округа. В 1870 г. первые плавки проведены в печи вместимостью 2,5 т, построенной известными металлургами А. А. Износковым и Н. Н. Кузнецовым на Сормовском заводе. Эта печь хорошо работала и стала образцом для печей большой вместимости, построенных позже на других русских заводах. После Великой Октябрьской социалистической революции мартеновский процесс стал основным в отечественной металлургии. Огромную роль сыграли мартеновские печи в суровые годы Великой Отечественной войны. Советским металлургам впервые в мировой практике удалось удвоить садку мартеновских печей без существенной их перестройки (ММК, КМК), удалось наладить производство высококачественной стали (броневой, подшипниковой и т. п.) на действовавших в то время мартеновских печах.
Более чем столетний период развития мартеновского производства стали доказал высокое его совершенство и надежность.
В конце пятидесятых годов в СССР и в некоторых других странах появился и был реализован новый метод использования тепла отходящих из плавильного пространства продуктов сгорания топлива для нагрева скрапа. Так появился новый подовый сталеплавильный агрегат — двухванная печь. В некоторых странах, например в ЧССР, в Южно-Африканской республике, эти печи строят качающимися, они отапливаются относительно большим количеством топлива и их называют тандем-печами.
В СССР двухванные печи имеют емкость каждого плавильного пространства 250 или 300 т. Такие печи свободно размещаются в современных мартеновских цехах и имеют производительность в 2—2,5 раза выше, чем мартеновские печи, занимающие такую же площадь в цехе.
Благодаря своим качествам и невысокой стоимости мартеновская сталь нашла широкое применение.
|
|
Поперечные профили набережных и береговой полосы: На городских территориях берегоукрепление проектируют с учетом технических и экономических требований, но особое значение придают эстетическим...
Кормораздатчик мобильный электрифицированный: схема и процесс работы устройства...
Биохимия спиртового брожения: Основу технологии получения пива составляет спиртовое брожение, - при котором сахар превращается...
Историки об Елизавете Петровне: Елизавета попала между двумя встречными культурными течениями, воспитывалась среди новых европейских веяний и преданий...
© cyberpedia.su 2017-2024 - Не является автором материалов. Исключительное право сохранено за автором текста.
Если вы не хотите, чтобы данный материал был у нас на сайте, перейдите по ссылке: Нарушение авторских прав. Мы поможем в написании вашей работы!