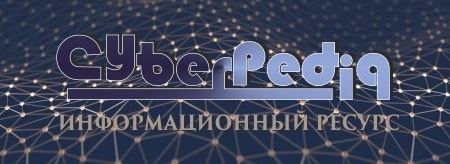
Механическое удерживание земляных масс: Механическое удерживание земляных масс на склоне обеспечивают контрфорсными сооружениями различных конструкций...
Археология об основании Рима: Новые раскопки проясняют и такой острый дискуссионный вопрос, как дата самого возникновения Рима...
Топ:
Организация стока поверхностных вод: Наибольшее количество влаги на земном шаре испаряется с поверхности морей и океанов...
Комплексной системы оценки состояния охраны труда на производственном объекте (КСОТ-П): Цели и задачи Комплексной системы оценки состояния охраны труда и определению факторов рисков по охране труда...
Особенности труда и отдыха в условиях низких температур: К работам при низких температурах на открытом воздухе и в не отапливаемых помещениях допускаются лица не моложе 18 лет, прошедшие...
Интересное:
Инженерная защита территорий, зданий и сооружений от опасных геологических процессов: Изучение оползневых явлений, оценка устойчивости склонов и проектирование противооползневых сооружений — актуальнейшие задачи, стоящие перед отечественными...
Аура как энергетическое поле: многослойную ауру человека можно представить себе подобным...
Что нужно делать при лейкемии: Прежде всего, необходимо выяснить, не страдаете ли вы каким-либо душевным недугом...
Дисциплины:
![]() |
![]() |
5.00
из
|
Заказать работу |
|
|
[ sH ]= …………..МПа.
(при НВ1 – НВ2 <70 минимальное из двух возможных [ sH ]1 и [ sH ]2,
при НВ1 – НВ2 ≥70 [ sH ]=([ sH ]1 + [ sH ]2 ) / 2, учитывая[ sH ]≤1,25[ sH ]min ).
Допускаемые напряжения изгиба при расчете на усталость.
4.1.8. Эквивалентное время работы, ч.
tFE= (Т1/Т1)6. t1 + (Т2/Т1)6. t2 + (Т3/Т1)6. t3 =
4.1.9. Эквивалентное число циклов нагружений
NFE1 = 60∙ n1∙ tFE∙ c =
NFE2 = 60 ∙ n2∙ tFE∙ c =
4.1.10. Коэффициент долговечности для материала шестерни и колеса.
Базовое число циклов нагружений NF01 = NFO2 = 4∙106
принимаем KFL1 =
принимаем KFL2 =
4.1.11. Базовый предел изгибной выносливости, МПа.
sFO1 =1.8∙ HB 1=
s FO2=1.8· HB2=
4.1.12. Допускаемые напряжения изгиба при расчете на изгибную выносливость, МПа.
[ sF ]1= (sFO1∙ KFL1∙ KFC)/ SF =
[ sF ]2= (sFO2∙ KFL2∙ KFC) /SF =
где: SF =1.75 - коэффициент безопасности,
K FC =1.0 - коэффициент, учитывающий реверсивность нагрузки.
4.1.13. Допускаемые контактные напряжения при расчете на контактную прочность при перегрузке моментом Т max, МПа.
[ σ H]max= [ σ H]max2= 2.8 σT =
4.1.14 Допускаемые напряжения изгиба при расчете на изгибную прочность при действии момента Т max, МПа.
[ s F]max1=2.74∙HB1 =
[ s F]max2=2.74∙HB2 =
4.2. Определение межосевого расстояния и размеров зубчатых колес.
Межосевое расстояние для косозубой цилиндрической передачи, мм.
где:
U = z2 /z1 = – передаточное число передачи
Yba=bw /aw= –относительная ширина зубчатого колеса
(принимается в интервале от 0.3÷0.5)
KHb – коэффициент неравномерности распределения нагрузки по линии контакта
Ybd = 0.5∙ Yba∙ (U+ 1) = тогда KHb=
Межосевое расстояние aw округляем в большую сторону до стандартного значения, или в меньшую, если процент расхождения не превышает 5%.
|
Принимаем aw= мм
.
4.3. Нормальный модуль зацепления
Выбор модуля зацепления выполняем в соответствии с рекомендациями:
mn =(0.01…0.02) ∙ aw =
Принимаем mn = мм, в соответствии со стандартным рядом чисел.
4.4. Угол наклона зубьев и суммарное число зубьев передачи
Zå = 2aw· cosb / m =
Примечание: первоначально примем b=11о, тогда cosb = 0.98
Определение числа зубьев шестерни и колеса:
Z1= Zå / (U +1)=
принимаем Z1 = > 17 зубьев, Х =0 – коэффициент смещения,
Z2=Zå - Z1 =
4.5. Уточнение угла наклона зубьев
cosb= (mn∙ Zå) / (2 ∙ aw) = b =
Торцевой модуль, мм.
mt = mn / cosb =
4.6. Определение основных геометрических размеров зубчатых колес
Диаметр начальной (делительной) окружности, мм.
d1 = mt∙ Z1 =
d2 = mt∙ Z2 =
Диаметр окружности впадин, мм.
df1 = d1 2.5 m =
df2 = d2 2.5 m =
Диаметр окружности вершин, мм.
da1 = d1 + 2.0 m =
da2 = d2 + 2.0 m =
Ширина колеса bw= Yba∙ aw = принимаем bw = мм.
(Примечание: данный размер округляется по ряду Ra40)
Ширина шестерни b1 = bw + 5мм = принимаем b1 = мм.
4.7. Проверочный расчет зубьев на контактную выносливость
4.7.1. Определение окружной скорости в зацеплении (м/с) и степени точности передачи
V=p ∙ d1∙ n1 / (60·1000) =
Принимаем 8 степень точности.
(Эта степень соответствует точности редукторов общего назначения).
4.7.2. Определение расчетной нагрузки при расчете на контактную выносливость, н/м.
где:
KHb= – коэффициент неравномерности распределения нагрузки по линии контакта,при Ybd= bw / d1 =
KHV = – коэффициент динамической нагрузки, при V = …… м/с, HB < 350, передаче косозубой, степени точности 8)
KHa= – коэффициент, учитывающий перекрытие и неравномерную загрузку контактирующих пар зубьев, при V< …… м/с и 8-й степени точности.
4.7.3 Определение действующих контактных напряжений, МПа
|
где:
ZH = 1.76 ∙ cosb = – коэффициент, учитывающий геометрию передачи;
Z M = 275 МПа1/2 – коэффициент, учитывающий свойства материала;
Z ε = – коэффициент, учитывающий суммарную длину контактной линии
где:
Ke= 0,95 – коэффициент, учитывающий колебание длины контактной линии
ea - коэффициент торцевого перекрытия.
ea = [1.88 3.2 (1/ z1 + 1/ z2)] ∙ cosb =
Сравнение величин действительных sH и допускаемых напряжений:
sH = МПа < [ sH ] = МПа.
Вывод: работоспособность зубчатой передачи по контактной выносливости обеспечена.
4.8. Проверочный расчет на изгибную выносливость
4.8.1. Определение слабого элемента контактирующих колес
Имеем: z1 =
Эквивалентное число зубьев:
zv1 = z1 / cos³b =
Коэффициент формы зуба при X=0 YF1 =
При z2 =
Эквивалентное число зубьев:
zv2 =z2 / cos³b =
Коэффициент формы зуба при Х=0 YF2 =
Сравниваем [sF]1 / YF1 и [ sF]2 / YF2
Вывод: слабым элементом является зуб ----------------------------, поэтому расчет
изгибной выносливости ведем по зубу ---------------------------------
[sF]-- = МПа.
4.8.2. Определение расчетной нагрузки и проверка на изгибную выносливость.
Окружное усилие, Н Ft = 2T1*1000 / d1 =
Действующее изгибное напряжение в колесе σF2 составляет:
=
где:
YF =
Yε = 1 / (Kε ∙εα) =
Yβ = cosβ =
KFβ =
KFv =
KFα =
Сравнение величин действительных sF и допускаемых напряжений:
sF = МПа < [ sF ] = МПа
Вывод: работоспособность зубчатой передачи по изгибной выносливости обеспечена.
4.9. Проверочный расчет зубьев при перегрузках
Расчет ведём по Tmax в момент пуска,
Tmax/Tном = (из характеристики двигателя).
4.9.1 Контактные напряжения в момент пуска, МПа
sНmax = sН =
[ sН ]max2 =
sНmax = МПа < [ sН ]max2= МПа
Вывод: контактная прочность рабочей поверхности зуба при перегрузках обеспечена.
4.9.2 Напряжения изгиба в период пуска, МПа
sFmax = sF ∙ Tmax / Tном =
sFmax=
sFmax = МПа < sFmax -- = МПа.
Вывод: изгибная прочность зуба при перегрузках обеспечена.
Расчет редукторных валов
5.1. Расчет валов на чистое кручение (проектный расчет)
5.1.1. Определение диаметров валов
Ведущий вал
Диаметр входного участка вала I, мм:
Первая ступень вала под полумуфту.
С учетом диаметра выходного конца вала двигателя и подобрав муфту, которая может соединять валы разных диаметров (пределах одного номинального момента) принимаем диаметр входного участка ведущего вала
|
d1 = мм.
Вторая ступень вала под уплотнение и подшипник.
d 1м = мм.
Манжеты резиновые армированные по ГОСТ 8752-79: d= мм, D = мм, h1= мм.
Под подшипник I вала принимаем диаметр
d2= мм.
Третья ступень вала под шестерню.
Шестерню выполним за одно целое с валом.Предусматриваем в конструкции возможность выхода фрезы (если необходимо).
d3 = мм.
Четвертая ступень вала под подшипник.
d4= мм
Ведомый вал
Диаметр выходного участка вала II, мм:
Первая ступень вала под открытую передачу
Принимаем диаметр участка тихоходного вала
d1 = мм.
Вторая ступень вала под уплотнение и подшипник.
d 2м = мм.
Манжеты резиновые армированные по ГОСТ 8752-79: d= мм, D = мм, h1= мм.
Под подшипник II вала принимаем диаметр
d2= мм
Третья ступень вала под колесо
d3 = мм.
Четвертая ступень вала под подшипник.
d4= мм.
Пятая упорная ступень
d5 =
5.1.2. Конструктивные размеры колеса.
В качестве заготовки для колеса принимаем поковку.
Диаметр ступицы колеса (внутренний), мм dвн =d3=
Диаметр ступицы колеса (наружный), мм dст=
Длина ступицы: l ст=
Толщина обода: S=
Толщина диска: С=
Толщина ступицы: δ=
5.1.3. Подбор подшипников
Принимаем подшипники шариковые радиальные однорядные легкой серии. ГОСТ 8338-75
ВалI - № D = мм, d = мм, B = мм, С = кН, Сo = кН
ВалII - № D = мм, d = мм, B = мм, С = кН, Co = кН.
Схема установки подшипников враспор.
5.1.4. Подбор и расчет муфты.
Для соединения выходного конца двигателя и быстроходного вала редуктора, применяем упругую втулочно- пальцевую муфту – МУВП… ГОСТ 21424-93. Размер муфты взят по диаметру вала двигателя.
Муфта обеспечит надежную работу привода с минимальными дополнительными нагрузками.
Радиальная сила, действующая на вал: Fм = 50 Б =
Стандарт допускает сочетание полумуфт с различными диаметрами посадочных отверстий в пределах одного номинального вращающего момента.
Т.к. диаметр входного вала редуктора меньше (d =…. мм), сочетаем полумуфты разных диаметров.
Для муфты с диаметром вала одной из полумуфт …… мм имеем:
диаметр пальца dп = ….мм,
число пальцев Z =…,
|
диаметр расположения пальцев D =
длина резиновой втулки L =
коэффициент перегрузки К =1,3.
Полумуфты изготовляют из чугуна марки СЧ20 (ГОСТ 1412-85);
Материал пальцев- сталь 45 (ГОСТ 1050- 88);
Материал упругих втулок – резина.
Слабым элементом муфты является резиновая втулка.
Для проверки прочности муфты рассчитаем резину – по напряжениям смятия,
считая, что напряжения распределены равномерно по длине втулки:
σсм = ≤ [σcм]
σсм = =
рекомендуют принимать [σcм] =1,8…2 (3) МПа.
Вывод: муфта выдержит заданную нагрузку.
5.1.5. Расчет шпоночных соединений.
На ведущем и ведомом валах применяем шпонки призматические со скругленными торцами по ГОСТ 23360-78
Материал шпонок – сталь 45 нормализованная.
Диаметр вала d | Сечение шпонки, b x h | Глубина паза вала, t1 | Глубина паза втулки, t2 | Длина шпонки l |
Напряжения смятия и условие прочности: см =
Допускаемое напряжение смятия
при стальной ступице при чугунной
Ведущий вал
Расчет шпоночного соединения для передачи вращающего момента с полумуфты на входной вал редуктора:
см =
Вывод: условие см
выполняется.
Ведомый вал
Расчет шпоночного соединения для передачи вращающего момента на звездочку:
см =
Расчет шпоночного соединения для передачи вращающего момента на
зубчатое колесо.
см =
Вывод: условие см
выполняется.
5.2Выполнение компоновочного чертежа редуктора.
Толщина стенки редуктора …мм;
Зазор между вращающимися колесам и внутренними стенками корпуса…мм;
Ширина фланца от внутренней поверхности корпуса до крышки подшипникового узла … мм;
Ширина фланца вне мест установки крышек подшипниковых узлов …мм.
Толщина крышки подшипникового узла для обоих валов …мм.
Для проектируемого редуктора осевые размеры валов:
ВалI l1=
l2 =
l Б = 2l2 = (пролет быстроходного вала).
Вал II l4 =
l3 =
l т = 2l3 = (пролет тихоходного вала).
5.3.Определение опорных реакций и построение эпюр внутренних
усилий в валах
Схемы для расчета быстроходного и тихоходного валов.
Усилия в зубчатом зацеплении, Н:
Окружное усилие Ft = 2· TII ·1000 / d2 =
Радиальное усилие Fr =Ft ·tga /cosb =
Осевое усилие Fа = Ft·tgb =
углы: α = 200 , β = 0 .
Консольная нагрузка со стороны муфты: Fм =
Консольная нагрузкасо стороны цепной передачи: F Ц= F t +2 Ff =
Разложим её на составляющиев соответствии с углом 450 наклона линии центров звездочек к горизонту:
F ЦВ= F Ц cos 45 =
F ЦГ = F Ц =
Уравнения равновесия на валах и определение реакций в опорах:
Входной вал.
∑М = 0 Реакции от сил в зацеплении:
|
- в плоскости YOZ
RБВ = Ft l2/ l Б =
RАВ = Ft(l Б – l2)/ l Б =
- в плоскости XOZ
RБГ = (Frl2+ Fad1/2)/ l Б =
RАГ =[ Fr(l Б – l2) - Fad1/2 ]/ l Б =
Суммарные реакции опор от сил в зацеплении:
RА = =
RБ = =
Реакции от силы Fм:
RБМ = Fмl1/ l Б =
RАМ = Fм(l Б + l1)/ l Б =
Полные реакции опор для расчета подшипников, Н:
FrA = RА + RАМ =
FrБ = RБ + RБМ =
Выходной вал.
Реакции в плоскости YOZ:
RГВ =[Ftl3 + FцВ(l т + l4)]/ l т =
RВВ = [-Ft(l т – l3) + FцВl4 ]/ l т =
Реакции в плоскости XOZ:
RГГ = [- Fr l3+ Fad2/2 + FцГ(l т + l4)]/ l т =
RВГ = [Fr(l т – l3)+ Fad2/2 + FцГl4]/ l т =
Суммарные реакции опор для расчета подшипников, Н:
FrВ= =
FrГ = =
5.4.Расчет подшипников валов на долговечность.
Выполняем проверку выбранных подшипников быстроходного вала.
.
Подшипник__________, С = __________ Н; С0 = ___________ Н:
Частота вращения вала n = _________ мин -1, d = _______ мм.
Вал нагружен осевой силой Fа =_______ Н.
Для радиальных подшипников осевые составляющие RосеваяА = RосеваяБ = 0.
Из условия равновесия вала осевые реакции опор: R аА = 0; R аБ = Fа =______Н.
Т.к. R аА = 0, то для опоры А имеем: X = 1; Y = 0.
Для опоры Б отношение Fа / С0 = ______________________ e = ____
Отношение Fа / (V FrБ) = _______________________, < или > е.
Тогда для опоры Б: X =___________ Y = __________.
Эквивалентная нагрузка
Р А =
Р Б =
Для более нагруженной опоры ________
__________________________________________
Выполняем проверку выбранных подшипников тихоходного вала.
Подшипник__________, С = ____________ Н; С0 = ____________Н:
Частота вращения вала n = __________ мин -1, d = __________ мм.
Вал нагружен осевой силой Fа =_______ Н.
Для радиальных подшипников осевые составляющие RосеваяВ= RосеваяГ = 0.
Из условия равновесия вала осевые реакции опор: R аГ = 0; R аВ = Fа =______Н.
Т.к. R аГ = 0, то для опоры Г имеем: X = 1; Y = 0.
Для опоры В отношение Fа / С0 = ______________________ e = ______
Отношение Fа / (V FrВ) = _______________________,< или > e.
Тогда для опоры В: X =_________ Y = __________.
Эквивалентная нагрузка
Р В =
Р Г =
Для более нагруженной опоры ________
__________________________________________
Для зубчатых редукторов ресурс работы подшипников может превышать 36000ч (таков ресурс самого редуктора), но не должен быть менее 10000ч (минимально допустимая долговечность подшипника).
Поэтому для входного вала принимаем подшипник ______
для выходного вала принимаем подшипник ______
Смазывание подшипников в редукторе осуществляется разбрызгиванием, т.к. подшипники установлены в корпус без изоляции от общей картерной системы смазки.
Окружная скорость зубчатого колеса, м/с V = ____________ и
Контактные напряжения, Н/мм2 σН =_____________.
Принимаем марку масла для зубчатых передач _________________
Расчет цепной передачи.
В проектируемом приводе ленточного конвейера открытая цепная передача устанавливается после цилиндрического редуктора и применяется для понижения частоты вращения барабана.
Выбираем приводную роликовую однорядную цепь ПР ГОСТ 13568-75.
крутящий момент на валу ведущей звездочки (тихоходном валу редуктора), Нм.
T 1 = T II =
передаваемая мощность, кВт.
N 1 = N II =
частота вращения ведущей звездочки, об/мин.
n1 = nII =
частота вращения ведомой звездочки, об/мин.
n2 = n1/Uц =
передаточное отношение цепной передачи Uц =
угол наклона цепи 450, работа передачи в одну смену, спокойная нагрузка, периодическое смазывание цепи, периодическое регулирование натяжения цепи.
m = 1
z 1 = 31 – 2Uц =
z 2 = z 1 ∙ U ц =
коэффициент K Э = k Д∙ k a∙ k н∙ k p∙ k см∙ k п = 1∙1∙1∙1.25∙1.5∙1 = 1.875
Пусть допускаемое давление в шарнирах [ р ] = МПа, межосевое расстояние, по соображениям долговечности цепи, а = 40 t.
Находим шаг цепи:
t =
Примем ближайший больший шаг по стандарту t = мм;
Тогда проекция опорной поверхности шарнира А ОП = мм2,
Разрушающая нагрузка Q = кН,
Масса одного метра цепи q = кг/м;
Выполним проверку цепи по двум показателям: по частоте вращения и по давлению в шарнирах.
Допускаемая для цепи с выбранным шагом t частота вращения
[ n ] = об/мин. Следовательно условие n1 ≤ [ n1 ] выполняется.
При n1 = об/мин, значение [ р ]табл. = МПа.
[ р ]= [ р ]табл. · кz=
кz =1+0,01(z1 – 17) =
расчетное давление в шарнирах, МПа.
p = Ft∙KЭ / А ОП =
здесь F t = N 1 ∙ 103/ v =
Средняя скорость цепи, м/с. v = z 1∙ t ∙ n 1 / (60 ∙103) =
Следовательно условие p ≤ [ p ] выполняется.
Число звеньев цепи:
L t = 2 a t + 0,5z∑ + ∆2/ a t =
где z∑ = z 1 + z 2 =
поправка ∆ = (z2 – z1)/2π =
а t = a / t = 40 ∙ t/ t = 40.
округляем значение L t до четного целого значения: L t =
Уточняем межосевое расстояние а, мм
Для свободного провисания цепи уменьшаем межосевое расстояние на 0,4%, т.е принимаем а = арасч. – арасч · 0,004 ≈ мм.
Диаметры делительных окружностей звездочек, мм:
ведущей dд1 = t / sin(1800 / z1) =
ведомой dд2 = t / sin(1800 / z2) =
Диаметры наружных окружностей звездочек:
ведущей D e1 = t [ctg (180/ z 1) + 0.7] – 0.31 d 1 =
ведомой D e2 = t [ctg (180/ z 2) + 0.7] – 0.31 d 1 =
где d 1 = мм – диаметр ролика цепи.
Силы, действующие на цепь:
окружная сила, Н F t =
центробежная сила, Н Fv = q∙ v 2 =
сила от провисания цепи, Н Ff = 9.81∙ kf ∙ ∙ q∙ a =
kf – коэффициент провисания При угле наклона 450 kf =1,5.
Расчетная нагрузка на валы
F Ц= F t +2 Ff =
Проверяем коэффициент запаса s:
s = Q ∙ 103/ (k д ∙ F t + Fv + Ff ) =
нормативный коэффициент запаса прочности [s]=
Условие s ≥ [s] выполнено.
|
|
Индивидуальные и групповые автопоилки: для животных. Схемы и конструкции...
История развития хранилищ для нефти: Первые склады нефти появились в XVII веке. Они представляли собой землянные ямы-амбара глубиной 4…5 м...
Поперечные профили набережных и береговой полосы: На городских территориях берегоукрепление проектируют с учетом технических и экономических требований, но особое значение придают эстетическим...
Историки об Елизавете Петровне: Елизавета попала между двумя встречными культурными течениями, воспитывалась среди новых европейских веяний и преданий...
© cyberpedia.su 2017-2024 - Не является автором материалов. Исключительное право сохранено за автором текста.
Если вы не хотите, чтобы данный материал был у нас на сайте, перейдите по ссылке: Нарушение авторских прав. Мы поможем в написании вашей работы!