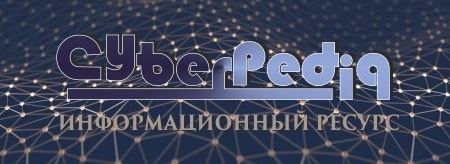
История создания датчика движения: Первый прибор для обнаружения движения был изобретен немецким физиком Генрихом Герцем...
Типы сооружений для обработки осадков: Септиками называются сооружения, в которых одновременно происходят осветление сточной жидкости...
Топ:
Устройство и оснащение процедурного кабинета: Решающая роль в обеспечении правильного лечения пациентов отводится процедурной медсестре...
Организация стока поверхностных вод: Наибольшее количество влаги на земном шаре испаряется с поверхности морей и океанов...
Интересное:
Национальное богатство страны и его составляющие: для оценки элементов национального богатства используются...
Наиболее распространенные виды рака: Раковая опухоль — это самостоятельное новообразование, которое может возникнуть и от повышенного давления...
Средства для ингаляционного наркоза: Наркоз наступает в результате вдыхания (ингаляции) средств, которое осуществляют или с помощью маски...
Дисциплины:
![]() |
![]() |
5.00
из
|
Заказать работу |
|
|
Фирма «Ipsco Inc.» эксплуатирует стан Стеккеля в Регине с 1960 г. и производит полосы шириной до 1956 мм и толщиной 1,9-19,0 мм. Технологическая линия была усовершенствована и модернизирована в 1979 и 1991 гг. В США фирмы «Tuscaloosa Steel» первой использовала стан Стеккеля для производства широких толстых полос в рулонах.
Три других производителя листовой стали - «Lukens», «Oregon Steel» и «Ipsco Inc.» -используют новые станы Стеккеля, чтобы получить аналогичные преимущества с точки зрения качества и себестоимости продукции.
В 1995 г. «Lukens» на заводе в Коншонхокене (Пенсильвания) начала использовать для чистовой прокатки при производстве полос в мерных длинах новый стан Стеккеля. На этом стане прокатали первые рулоны шириной 2794 мм. В 1996 г. «Oregon Steel» приступил к прокатке более широких полос на стане Стеккеля в Портланде.
«Tuscaloosa Steel» и «Lukens» могут прокатывать полосы в мерных длинах шириной до 2590 мм и полосы в рулонах шириной до 2440 мм. На стане фирмы «Ipsco Inc.» в Монпельере, построенном фирмой «Mannesmann Demag», прокатывают листы шириной до 3050 мм и полосы в рулонах шириной до 2440 мм. «Oregon Steel» на новом стане в Типпинсе намерена увеличить ширину полос до 3560 мм для листов и 3050 мм для полос в рулонах.
Металлургические фирмы выбирают стан Стеккеля, главным образом, по трем причинам:
- низкие капитальные затраты на строительство и более низкие издержки производства для прокатки широких полос в рулонах или в мерных длинах;
- возможность производства полос более широкого сортамента по толщине и ширине;
- высокое качество поверхности полос по сравнению с традиционными реверсивными листопрокатными станами.
Стан Стеккеля фирмы «Ipsco Inc.» имеет производительность 1,25 млн. т/год. Фирма «Lukens» удваивает производительность по прокату на своем заводе в Коншохокене до 700 тыс. т/год посредством выполнения чистовой прокатки на новом стане Стеккеля вместо прежнего двухклетевого. Новый одноклетьевой стан Стеккеля заменит четырехклетевой реверсивный стан в Портланде, а также двухклетевой стан в Фонтане (Калифорния).
|
Важным и существенным в случае прокатки на станах Стеккеля является получение тонколистового проката. Поскольку в течение прокатки на стане Стеккеля температура раската остается на уровне 982-1090 °С, качество поверхности заметно лучше, чем в случае традиционных реверсивных станов.
Новые станы Стеккеля для регулирования толщины и плоскостности проката используют устройства изгиба и смещения рабочих валков, а также автоматическое регулирование толщины.
Фирмы «Tuscaloosa Steel», «Oregon Steel» и «Lukens» для улучшения металлургических свойств и повышения пределах текучести проката используют регулируемое охлаждение.
На фирме «Lukens» прокатываемый рулон проходит через секцию охлаждения ламинарным потоком, что позволит охлаждать полосы с предварительно заданной скоростью в зависимости от толщины проката и химического состава. В настоящее время «Lukens» может производить листовой прокат, обладающий пределом текучести до 492 МПа. Секция охлаждения позволит повысить эту величину до 703 МПа. Варианты планировок с использованием стана Стеккеля поканы на рис.3.
Возможности использование стана Стеккеля
Использование более тонких слябов позволяет уменьшить число проходов, требуемых для достижения заданной толщины. Это сокращает продолжительность прокатки, уменьшает износ валков и позволяет фирме «Tuscaloosa Steel» повысить годовую производительность по готовому прокату с 500 до 800 тыс. т. Кроме того, меньшее число проходов приводит к улучшению качества поверхности.
Оборудование компании «Danieli» включает одноручьевую МНЛЗ, камеру для закалки слябов, нагревательную печь с шагающим балочным подом, стан Стеккеля с высокой степенью автоматизации, систему ламинарного охлаждения и подпольную многороликовую моталку, а также установленное в линию оборудование для отделки проката (холодильник, ножницы, машины для правки в горячем и холодном состоянии). Использование МНЛЗ тонких слябов позволяет производить как лист в рулонах, так и отдельные листы, и имеет несомненные преимущества по сравнению с традиционной технологией:
|
- получаемые слябы имеют мелкозернистую структуру, которую при обычном процессе прокатки на толстолистовом стане можно получить только после нескольких черновых пропусков;
- в нагревательную печь заготовка поступает с более высокой температурой, обеспечивая тем самым «непрерывный процесс», вдвое-втрое уменьшая длину печи, время нагрева и расход топлива;
- число черновых пропусков уменьшается в два раза, исключается необходимость в установке черновой клети, что позволяет на 30 % и более сократить удельный расход энергии при прокатке;
- заправка подката в первую печь стана Стеккеля производится при температуре на 50-75 °С выше, чем при прокатке на обычном толстолистовом стане, что позволяет получать более тонкий лист, а также улучшает механические и геометрические характеристики готового проката.
Процесс «динамического слабого обжатия» позволяет уменьшить размеры зерна при любом режиме литья благодаря большему объему кристаллизатора. Площадь, занимаемая толстолистовым станом, уменьшается вследствие размещения печей для нагрева рулонов впереди и сзади клети с горизонтальными валками.
Стан Стеккеля показан на рис. 4.
Стан Стеккеля
Рис. 4.: 1 - печь; 2 - протяжные ролики; 3 - рентгеновский толщиномер;
4 - эджер; 5 - реверсивная клеть кварто; 6 - измеритель ширины полосы;
7 – протяжные ролики; 8 – печь.
В качестве исходной заготовки используются слябы толщиной 101-152 мм и шириной 1524-3200 мм, а также рулоны толщиной 2,3-19,0 мм и шириной 1524-2515 мм. Готовые листы имеют толщину 4,8-51 мм и ширину 1524-3124 мм.
Двухклетевые реверсивные станы наиболее приемлемы для средних объемов производства проката широкого сортамента. По качеству продукции они соответствуют требованиям, предъявляемым к современным станам холодной прокатки (табл. 7).
|
Размещение коллекторов и контрольно-измерительной аппаратуры (КИП) на двухклетевой реверсивном стане холодной прокатки показано на рис. 5. На рис. 7 показана конструкция клети кварто с установкой устройств для регулирования положения валков.
Прокатные станы типа RS (Redes-Sendzimir) предназначены для производства тонкой высокоточной полосы из различных сталей, меди, латуни, бериллиевых сплавов, фосфористой бронзы, алюминия, полудрагоценных сплавов, применяемых в электронике и электротехнике. Они могут быть использованы как реверсивные или как клети непрерывных станов.
Таблица 7
Основные характеристики двухклетевых реверсивных станов
Продукция | Белая жесть | Черная жесть |
Годовая производительность, тыс. т | ||
Капиталовложения по сравнению с непрерывным станом,% | ||
Тип клетей | Кварто, в т.ч. со смещением рабочего валка в горизонтальной плоскости; шестивалковые | |
Типы приводов валков | Индивидуальный, групповой. Приводные опорные или рабочие валки | |
Система подачи смазочно-охлаждающей жидкости | Многокамерные коллекторы для выборочного охлаждения валков | |
Сушка полосы | Регулируемое устройство для обтирки и обдувки полосы | |
Перевалка валков | Тележки с боковым перемещением и системой вталкивания комплекта валков |
Размещение коллекторов и контрольно-измерительной аппаратуры
Рис.5.
На рис. 6 показан прокатный стан типа B400-ZR64/18 предназначенный для холодной прокатки листов в рулонах.
Линия стана B400-ZR64/8
Рис. 6
Рабочая клеть кварто
![]() |
Рис. 7.1 - цилиндры смещения рабочего валка в горизонтальной плоскости; 2 - зажимный цилиндр; 3 - Е-блоки для смещения рабочего валка в горизонтальной плоскости; 4 - подушки рабочего валка; 5 - станина; 6 - опорный валок; 7 - рабочий валок; 8 - гидравлическая система автоматического контроля толщины; 9 - подушка верхнего опорного валка; 10 - подушка верхнего рабочего валка; 11 - цилиндр уравновешивания опорного валка; 12 - подушка нижнего рабочего валка; 13 - цилиндр прогиба рабочего валка; 14 - подушка нижнего опорного валка; 15 - электромеханические клинья.
Техническая характеристика:
Диаметр рабочих валков, мм 50
Диаметр промежуточных валков, мм 110
Диаметр опорных валков, мм 400
Мощность двигателя, кВт 380
Скорость прокатки, м/мин 0/150/400
Минимальная толщина полосы, мм 0,03
Максимальная ширина полосы, мм 450
Вес рулонов, кгс 5000
Мощность двигателя, кВт 380
|
|
Состав сооружений: решетки и песколовки: Решетки – это первое устройство в схеме очистных сооружений. Они представляют...
Общие условия выбора системы дренажа: Система дренажа выбирается в зависимости от характера защищаемого...
История развития пистолетов-пулеметов: Предпосылкой для возникновения пистолетов-пулеметов послужила давняя тенденция тяготения винтовок...
Опора деревянной одностоечной и способы укрепление угловых опор: Опоры ВЛ - конструкции, предназначенные для поддерживания проводов на необходимой высоте над землей, водой...
© cyberpedia.su 2017-2024 - Не является автором материалов. Исключительное право сохранено за автором текста.
Если вы не хотите, чтобы данный материал был у нас на сайте, перейдите по ссылке: Нарушение авторских прав. Мы поможем в написании вашей работы!