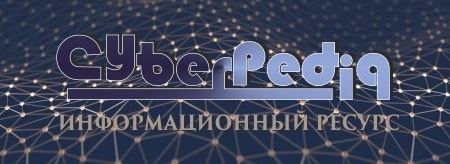
Биохимия спиртового брожения: Основу технологии получения пива составляет спиртовое брожение, - при котором сахар превращается...
Индивидуальные и групповые автопоилки: для животных. Схемы и конструкции...
Топ:
Характеристика АТП и сварочно-жестяницкого участка: Транспорт в настоящее время является одной из важнейших отраслей народного...
Проблема типологии научных революций: Глобальные научные революции и типы научной рациональности...
Когда производится ограждение поезда, остановившегося на перегоне: Во всех случаях немедленно должно быть ограждено место препятствия для движения поездов на смежном пути двухпутного...
Интересное:
Мероприятия для защиты от морозного пучения грунтов: Инженерная защита от морозного (криогенного) пучения грунтов необходима для легких малоэтажных зданий и других сооружений...
Инженерная защита территорий, зданий и сооружений от опасных геологических процессов: Изучение оползневых явлений, оценка устойчивости склонов и проектирование противооползневых сооружений — актуальнейшие задачи, стоящие перед отечественными...
Отражение на счетах бухгалтерского учета процесса приобретения: Процесс заготовления представляет систему экономических событий, включающих приобретение организацией у поставщиков сырья...
Дисциплины:
![]() |
![]() |
5.00
из
|
Заказать работу |
|
|
Рис. 1. График изменения Р при гидр. испытании газопроводов.
Рис. 2. График изменения Р при гидроиспытании нефтепроводов.
Рис. 3. Пневматические испытания (только для ГП).
При пневматическом испытании давление испытания равно 1,1 Рраб, а продолжительность испытания 12 часов. Заполнение ТП воздухом или природным газом осуществляется с осмотром трассы при давлении равным 0,3 Рисп, но не выше 2 МПа.
4. Способы испытаний трубопроводов на прочность и герметичность.
Трубопроводы должны испытываться в соответствии с проектом (рабочим проектом) гидравлическим (водой, незамерзающими жидкостями), пневматическим (природным газом, воздухом) или комбинированным (воздухом и водой или газом и водой) способами.
Все способы испытания равноценны и применимы для трубопроводов любого назначения.
Нефтепроводы следует испытывать, как правило, гидравлическим способом.
Трубопроводы, расположенные в пределах КС, ГРС, НПС испытываются только гидравлическим способом на давление P=1,25×Pраб в течение 24 часов.
Испытания газопроводов в горной и пересеченной местности разрешается проводить комбинированным способом (воздухом и водой или газом и водой).
Гидравлическое испытание трубопроводов водой при отрицательной температуре воздуха допускается только при условии предохранения трубопровода, линейной арматуры и приборов от замораживания.
Испытание трубопровода на прочность и проверку на герметичность следует производить после полной готовности участка или всего трубопровода:
- полной засыпки, обвалования или крепления на опорах;
- установки арматуры и приборов, катодных выводов;
- удаления персонала и вывозки техники из опасной зоны;
|
- обеспечения постоянной или временной связи.
До выполнения указанных работ в комиссию по испытанию трубопровода должна быть представлена исполнительная документация на испытываемый объект.
Способы, параметры и схемы проведения испытания, в которых указаны места забора и слива воды, согласованные с заинтересованными организациями, а также пункты подачи газа и обустройство временных коммуникаций устанавливаются рабочим проектом.
Протяженность испытываемых участков не ограничивается, за исключением случаев гидравлического и комбинированного испытания, когда протяженность участков назначается с учетом гидростатического давления.
Линейная часть и лупинги нефтепроводов, газопроводов и нефтепродуктопроводов должны подвергаться циклическому гидравлическому испытанию на прочность (в исключительных случаях проведение испытаний газопроводов на прочность допускается газом) и проверке на герметичность (газопроводы испытывают газом). При этом количество циклов должно быть не менее трех, а величины испытательного давления, в каждом цикле должны изменяться от давления, вызывающего в металле трубы напряжение 0,9 – 0,75 предела текучести.
Общее время выдержки участка трубопровода под испытательным давлением, без учета времени циклов снижения давления и восстановления должно быть не менее 24 ч.
Время выдержки участка под испытательным давлением должно быть не менее ч:
- до первого цикла снижения давления - 6;
- между циклами снижения давления - 3;
- после ликвидации последнего дефекта или последнего цикла снижения давления - 3.
Проверку на герметичность участка или трубопровода в целом производят после испытания на прочность и снижения испытательного давления до проектного рабочего в течение времени, необходимого для осмотра трассы (но не менее 12 ч).
Трубопровод считается выдержавшим испытание на прочность и проверку на герметичность, если за время испытания трубопровода на прочность труба не разрушилась, а при проверке на герметичность давление остаётся неизменным, и не будут обнаружены утечки.
|
При разрыве, обнаружении утечек визуально, по звуку, запаху или с помощью приборов участок трубопровода подлежит ремонту и повторному испытанию на прочность и проверке на герметичность.
При многониточной прокладке промысловых трубопроводов допускается одновременное их испытание гидравлическим или пневматическим способом.
Правила охраны МТ.
Для обеспечения нормальных условий эксплуатации МТ и исключения их повреждений на земельных участках прилегающих к землям, предоставленным в пользование предприятиям, устанавливается охранная зона, в которой вводятся особые условия землепользования. Земли охранных зон остаются в пользовании землепользователей и используются ими с соблюдением установленных ограничений.
Размеры охранной зоны устанавливаются правилами охраны МТ, утв. Госгортехнадзором:
- вдоль трасс ТП транспортирующих нефть, природный газ, нефтепродукты, нефтяной и искусственные углеводородные газы в виде участка земли ограниченного условными линиями, проходящими в 25 м от оси ТП с каждой стороны;
- вдоль трасс ТП, транспортирующих сжиженные углеводородные газы, нестабильные бензин и конденсат в виде участка земли, огранич. условными линями, проходящими в 100 м с каждой стороны от оси ТП
- вдоль трасс многониточных ТП в виде участка земли, ограниченного условными линями, проходящими на указанных выше расстояниях от оси и крайних трубопроводов
- вокруг емкостей для хранения и разгазирования конденсата земляных амбаров для аварийного выпуска продукции в виде участка земли, ограниченного замкнутой линией отстоящей от границ территории на 50 м во все стороны
- вокруг НС, резервуарных парков, КС, ГРС на 100 м во все стороны.
В охранной зоне без письменного разрешения соответствующих органов запрещается сооружать здания, автодороги, садить лес и т. д.
9. Условия образования гидратов в ГП
При эксплуатации газовых и газоконденсатных месторождений в скважинах, газосборных сетях, трубопроводах и оборудовании установок подготовки газа, КС и МГ при определенных термодинамических условиях образуются гидраты - твёрдые кристаллические соединения переменного состава, которые при высоком давлении могут существовать при положительных (до 20-25ºС) температурах.
|
По внешнему виду гидраты напоминают спрессованный снег или лёд и имеют близкую им плотность и прочность.
Образование гидратов в ГП снижают его пропускную способность, увеличивают потерю давления, что приводит к увеличению энергозатрат на транспорт газа и в конечном итоге может привести к закупорке трубопровода.
Гидратообразующими компонентами природного газа являются углеводороды (метан, этан, пропан, изобутан), а также неуглеводородные газы (сероводород, азот).
Газовые гидраты – это соединения, которые образуются при внедрении молекул газа в пустоты кристаллических структур, составленных из молекул воды.
Для образования гидратов необходимо наличие капельной воды и определенный термодинамический режим в ГП (давление, температура). Наличие воды в жидкой фазе, хотя и является обязательным условием, но недостаточным для образования гидратов.
Условия гидратообразования можно рассчитать по следующим уравнениям:
1) при положительных температурах гидратообразования: tг=18,47*lgP – B + 18,65
2) при отрицательных температурах: tг=58,5*lgP + B1 - 59,32;
где tг-равновесная температура гидратообразований, оС; Р-равновесное давление гидратообразований (ГО), МПа; В, В 1-эмпирические коэффициенты, значения которых зависят от приведенной плотности газа.
Равновесная температура - температура, ниже которой при определенном давлении образуются гидраты.
Для приближенных расчетов условия образования гидратов для газов с различной плотностью определяются по графику «Зависимость давлений от температуры гидратообразований газа при относительной плотности». На графике слева от линий - зона существования гидратов, а справа – зона без гидратов.
Кроме основных условий гидратообразования (влага, температура) существуют побочные условия образования гидратов:
- турбулентность движения газа,
- повороты трубопровода,
- сужение (факторы приводят к перемешиванию потока).
Для безаварийной эксплуатации МГ необходимо заранее выявить места возможного гидратообразования.
Для обнаружения зон гидратообразования и своевременного предотвращения образования гидратов необходимо знать состав транспортируемого газа, его плотность, изменение температуры и давления по длине ГП и влагосодержания, подаваемого в ГП газа. График определения возможной зоны гидратообразования МГ. Зону возможного гидратообразования в МГ определяют: для данного участка г/п строят кривые изменения давления - линия 1, кривые изменения температуры – линия 2, линия равновесных температур – линия 3.
|
Т.к. газ поступает в ГП с температурой выше точки росы, то он будет не насыщенным влагой. Следовательно, в самом начале ГП влага выпадать не будет. В точке М tгазаравна точке росы и начиная с этого сечения ГП в нем будет выпадать влага. При падении температуры от т. М до В - гидраты не образуются, т.к. tгаза> tгидратообр.; в т. В tгаза = tгидратообр → появились условия образования гидратов. После т. С tгаза> tгидратообр→ гидраты не образуются. Гидраты самопроизвольно разрушаются при отсутствии необходимых условий (давления, теспературы).
Требования к ГП для пропуска очистного устройства.
· Диаметр г/п д.б. по всей длине одинаков
· Запорная арматура д.б. равнопроходной
· Отводы, компенсаторы д.б. с радиусом изгиба не менее 5 диаметров очищаемого г/п
· В тройниках, на отводах, на перемычках если их диаметр более 30% диаметра основного г/п предусматривается установка направляющих планок для предотвращения заклинивания очистных устройств.
· Внутренняя поверхность не должна иметь выступающих деталей, кроме сигнализаторов прохождения поршня, рычаг которых утопает при прохождении очистного устройства.
· Перходы через естественные и искуственные препятствия должны выполнятся с учётом дополнительных нагрузок от веса поршня и любой газоконденсатной смеси.
19. Классификация потерь газа при ТП транспорте
В целом потери газа можно условно разделить на явные и неявные (скрытые).
На линейной части МГ явными потерями следует считать:
- утечки газа, выходящего через свищи, микротрещины, неплотности ЗА;
- потери при стравливании и продувки газа ремонтируемых участков ГП;
- потери при стравливании и продувки в процессе подключения отводов, перемычек и других технологических линий;
- потери при периодической очистке внутренней полости ГП;
- утечки при продувке конденсатосборников, импульсных трубок, КИПиА.
На КС явными потерями можно считать:
- потери при стравливании и продувки обвязки нагнетателей в процессе пусков и остановок ГПА;
- потери при продувке ПУ;
- потери в системе уплотнений нагнетателей ГПА;
- затраты топливного газа ГПА на КС при транспортировке газа с гидравлической эффективностью равной проектной;
|
- затраты пускового газа на пуске ГПА с запуском от ТД;
- затраты импульсного газа на перестановки кранов обвязки КС.
Неявные (скрытые) потери и затраты газа трудно обнаружить и замерить, а определить их можно только косвенным путем.
Неявными потерями следует считать:
- потери газа в результате фазовых превращений в ГП (образование из паров жидкой фазы и гидратов);
- затраты топливного газа на КС при снижении гидравлической эффективности линейных участков ГП от проектной величины;
- потери при эксплуатации на КС безрегенеративных ГТУ;
- потери при отклонении работы ГПА от оптимальных режимов;
- затраты топливного газа при наличии перетоков компремированного газа в обвязках нагнетательных и входных коммуникаций ГПА на КС.
20. Сокращение потерь газа при ТП транспорте
Основные причины отказов в работе МГ:
- наружная коррозия металлов - 53%;
- неудовлетворительное качество сварочных и строительно-монтажных работ - 18%;
- дефекты труб и заводского оборудования - 13%;
- внутренняя коррозия и эрозия - 6%;
- пробивка механизмами тела труб - 3%;
- нарушение правил технической эксплуатации - 2%;
- другие причины - 5%.
Вцелом потери газа можно условно разделить на явные и неявные (скрытые).
На линейной части МГ явными потерями следует считать:
- утечки газа, выходящего через свищи, микротрещины, неплотности ЗА;
- потери при стравливании и продувки газа ремонтируемых участков ГП;
- потери при стравливании и продувки в процессе подключения отводов, перемычек и других технологических линий;
- потери при периодической очистке внутренней полости ГП;
- утечки при продувке конденсатосборников, импульсных трубок, КИПиА.
На КС явными потерями можно считать:
- потери при стравливании и продувки обвязки нагнетателей в процессе пусков и остановок ГПА;
- потери при продувке ПУ;
- потери в системе уплотнений нагнетателей ГПА;
- затраты топливного газа ГПА на КС при транспортировке газа с гидравлической эффективностью равной проектной;
- затраты пускового газа на пуске ГПА с запуском от ТД;
- затраты импульсного газа на перестановки кранов обвязки КС.
Неявные (скрытые) потери и затраты газа трудно обнаружить и замерить, а определить их можно только косвенным путем.
Неявными потерями следует считать:
- потери газа в результате фазовых превращений в ГП (образование из паров жидкой фазы и гидратов);
- затраты топливного газа на КС при снижении гидравлической эффективности линейных участков ГП от проектной величины;
- потери при эксплуатации на КС безрегенеративных ГТУ;
- потери при отклонении работы ГПА от оптимальных режимов;
- затраты топливного газа при наличии перетоков компремированного газа в обвязках нагнетательных и входных коммуникаций ГПА на КС.
Основными мероприятиями, направленными на снижение потерь газа являются:
- сокращение потерь газа в атмосферу при ремонтах участков ГП благодаря совершенствованию технологий и применение устройств для утилизации газа;
- сокращение потерь газа при продувках и испытаниях вновь вводимых, неотремонтированных ГП благодаря применению высоконапорных и высокопроизводительных передвижных воздушных компрессорных установок;
- внедрение прогрессивных методов ремонта ГП - ремонт ГП без остановки перекачки газа, врезка отводов в действующий ГП под давлением;
- внедрение безогневых методов ремонта ГП;
- повышение эксплуатационной надежности ГП и их сооружений путем качественного и современного проведения ППР (планово-предупредительных ремонтов);
- исключение повреждения ГП сторонними организациями благодаря соблюдению порядка (правил) ведения работ в охранной зоне ГП.
Утилизацию газа при опорожнении участка ГП можно осуществить следующими
способами:
- перепуском газа из подлежащего ремонту с повышенным давлением через существующие или временно проложенные перемычки с более низким давлением газа;
- подключением к ремонтируемому участку потребителей газа через ГП-отвод;
- перекачкой газа из ремонтируемого участка ГП в соседний прилегающий участок данного ГП или в параллельный ГП передвижными компрессорными установками.
Схема МГПА (мобильного ГПА)
Установка состоит из ГПА, включающего в себя:
- приводной двигатель 3;
- нагнетатель 4 на входе которого установлен регулятор давления 5;
- на выходе из нагнетателя установлен холодильник газа 2 и эжектор 1, всасывающая камера которого через обратный клапан 6 соединена с входным ТП нагнетателя;
- 7 - турбодетандер;
- 8 - генератор для выработки эл. энергии;
- 13 - фланцевые соединения;
- 10 - ремонтируемый участок;
- 12 - остальной участок;
- 9,11 - линейные краны.
Газ, сжимаемый нагнетателем охлаждается в холодильнике 2 и направляется к высоконапорной камере эжектора 1. Вторая часть газа через обратный клапан 6 подается к низконапорной камере эжектора и эжектируется. Приток газа после эжектора направляется в ТП 12.Эжектор отключается автоматически после того, как давление газа в опорожняемом участке упадет ниже допустимого, определяемого коэффициентом эжекции. Постоянство параметров газа на входе в нагнетатель, обеспечивается регулирующим клапаном 5.
Учет природного газа. Требования к узлам учета газа.
Для измерения объемного (мгновенного и суммарного) расхода жидкости, пара или газа очень часто используют вихревые расходомеры. Принцип действия вихревого расходомера основан на широко известном природном явлении: если на пути движущегося потока встречается препятствие, то за ним образуются завихрения. Критерием любого гидродинамического потока служит число Рейнольдса, при числе Рейнольдса выше 100 количество завихрений увеличивается, они отрываются от препятствия и образуют цепочку чередующихся, закрученных по или против часовой стрелки вихрей, получившую название дорожки Кармана.
В диапазоне чисел Рейнольдса 2×104¸7×106 вихри образуются непрерывно и стабильно, а частота их образования приобретает линейную зависимость от скорости потока. Этот диапазон и используется для работы вихревых расходомеров.
Нормальный рабочий диапазон вихревых расходомеров соответствует диапазону чисел Рейнольдса от 2×104 и выше до 10 м/с для жидкостей и до скорости потока 80 м/с для газа и пара.
Требования предъявляемые к вихревым расходомерам:
·широкий диапазон измерения;
·малая потеря давления;
·простота и надежность эксплуатации;
Виды ремонтов ЛЧ ГНП.
В общем случае ремонт ЛЧ ГНП подразделяется на плановой и внеплановый или аварийный.
В зависимости от особенностью эксплуатирования Тр-да, степени повреждения и износа оборудования, а также от трудоёмкости ремонтных работ различают следующие виды плановых ремонтов ГНП:
- текущий
- капитальный
Текущий ремонт – комплекс ремонтных работ по поддержанию МГНП работоспособном состоянии и представляет собой замену или восстановление отдельных частей оборудования.
Капитальный ремонт – это комплекс технических мероприятий направленный на полное или близкое к полному восстановлению МГНП до проектных характеристик.
Специфика работ при капитальном ремонте выражается в следующем:
1) Технике и технологии
1.1. наличие демонтажных работ, предусматривающих выполнение последовательных ремонтно-восстановительных операциях.
1.2. наличие специальных операций, заключающихся в устранении дефектов трубы
1.3. сложность проведения вскрышных работ и значительная доля ручного труда
1.4. сложность и трудоёмкость работ по очистке наружной поверхности Тр-дов от старой изоляции и продуктов коррозии
1.5. конструктивно-технологические отличия применяемых спец-х машин (экскаваторы и очистные машины)
2) В организации проведения работ – операции по вскрытию, подъему, очистке от старой изоляции сварочно-восстановительной, изоляционно-укладочной работами и работами по засыпке Тр-да не могут быть совмещены специализированном потоке при min сближениях потоках.
К аварийному ремонту относится работы связаны:
1. с ликвидаций аварий, возникающие в разрыве Тр-да;
2. закупор Тр-да, приводящий к полной или частичной его остановке.
Специфика аварийного ремонта МГНП заключается в том, что его выполняют не только в любое время года, но и в любое время суток, в любых погодных условиях с min затратой времени. Аварийные работы выполняют специальные восстановительные службы, подразделения, которые укомплектованы работниками соот-щих профессий и квалификаций, общестроительными спецмашинами и механизмами, оборудованием и материалами.
Способы кап. ремонта.
Кап ремонт с заменой труб производят следующими способами:
· Путем укладки в совмещенную траншею вновь прокладываемого ТП или его участка рядом с заменяемым с последующим демонтажем последнего.
· Путем укладки в отдаленную траншею в пределах существующего технологического коридора вновь прокладываемого участка ТП с промежуточным вскрытием и демонтажем заменяемого ТП.
· Путем демонтажа заменяемого ТП и укладки вновь прокладываемого во вновь разработанную траншею или в существующую.
Капремонт НП с заменой изоляции и при необходимости с восстановлением несущей способности стенки трубы может производиться без остановки НП:
· С подъемом ТП в траншее d=219-720 мм.
· С подъемом и укладкой ТП на лежки в траншее d=219-720 мм.
· Без подъема с сохранением положения в транше d=820-1220 мм.
Кап ремонт ГП с заменой изоляции и при необходимости с восстановлением несущей способности стенки трубы после полного освобождения от газа до давления 100-500 Па:
· С подъемом и укладкой ТП на лежки в траншее.
· С подъемом трубы в траншее.
· С подъемом и укладкой ТП на лежки на бровке траншеи.
· Ремонт ТП в траншее с подкопкой под трубу.
· С прокладкой новой нитки параллельно действующей (применяется, когда остановка трубы невозможна).
При ремонте вскрытие ТП производится по двум схемам: а) при ремонте с подъемом он вскрывается до нижней образующей; б) при ремонте без подъема (с подкопом) ТП должен быть вскрыт ниже нижней образующей на глубину не менее 1 м.
Рис. 1. График изменения Р при гидр. испытании газопроводов.
Рис. 2. График изменения Р при гидроиспытании нефтепроводов.
Рис. 3. Пневматические испытания (только для ГП).
При пневматическом испытании давление испытания равно 1,1 Рраб, а продолжительность испытания 12 часов. Заполнение ТП воздухом или природным газом осуществляется с осмотром трассы при давлении равным 0,3 Рисп, но не выше 2 МПа.
4. Способы испытаний трубопроводов на прочность и герметичность.
Трубопроводы должны испытываться в соответствии с проектом (рабочим проектом) гидравлическим (водой, незамерзающими жидкостями), пневматическим (природным газом, воздухом) или комбинированным (воздухом и водой или газом и водой) способами.
Все способы испытания равноценны и применимы для трубопроводов любого назначения.
Нефтепроводы следует испытывать, как правило, гидравлическим способом.
Трубопроводы, расположенные в пределах КС, ГРС, НПС испытываются только гидравлическим способом на давление P=1,25×Pраб в течение 24 часов.
Испытания газопроводов в горной и пересеченной местности разрешается проводить комбинированным способом (воздухом и водой или газом и водой).
Гидравлическое испытание трубопроводов водой при отрицательной температуре воздуха допускается только при условии предохранения трубопровода, линейной арматуры и приборов от замораживания.
Испытание трубопровода на прочность и проверку на герметичность следует производить после полной готовности участка или всего трубопровода:
- полной засыпки, обвалования или крепления на опорах;
- установки арматуры и приборов, катодных выводов;
- удаления персонала и вывозки техники из опасной зоны;
- обеспечения постоянной или временной связи.
До выполнения указанных работ в комиссию по испытанию трубопровода должна быть представлена исполнительная документация на испытываемый объект.
Способы, параметры и схемы проведения испытания, в которых указаны места забора и слива воды, согласованные с заинтересованными организациями, а также пункты подачи газа и обустройство временных коммуникаций устанавливаются рабочим проектом.
Протяженность испытываемых участков не ограничивается, за исключением случаев гидравлического и комбинированного испытания, когда протяженность участков назначается с учетом гидростатического давления.
Линейная часть и лупинги нефтепроводов, газопроводов и нефтепродуктопроводов должны подвергаться циклическому гидравлическому испытанию на прочность (в исключительных случаях проведение испытаний газопроводов на прочность допускается газом) и проверке на герметичность (газопроводы испытывают газом). При этом количество циклов должно быть не менее трех, а величины испытательного давления, в каждом цикле должны изменяться от давления, вызывающего в металле трубы напряжение 0,9 – 0,75 предела текучести.
Общее время выдержки участка трубопровода под испытательным давлением, без учета времени циклов снижения давления и восстановления должно быть не менее 24 ч.
Время выдержки участка под испытательным давлением должно быть не менее ч:
- до первого цикла снижения давления - 6;
- между циклами снижения давления - 3;
- после ликвидации последнего дефекта или последнего цикла снижения давления - 3.
Проверку на герметичность участка или трубопровода в целом производят после испытания на прочность и снижения испытательного давления до проектного рабочего в течение времени, необходимого для осмотра трассы (но не менее 12 ч).
Трубопровод считается выдержавшим испытание на прочность и проверку на герметичность, если за время испытания трубопровода на прочность труба не разрушилась, а при проверке на герметичность давление остаётся неизменным, и не будут обнаружены утечки.
При разрыве, обнаружении утечек визуально, по звуку, запаху или с помощью приборов участок трубопровода подлежит ремонту и повторному испытанию на прочность и проверке на герметичность.
При многониточной прокладке промысловых трубопроводов допускается одновременное их испытание гидравлическим или пневматическим способом.
Гидравлический способ испытания.
Для проведения гидравлического испытания давление внутри трубопроводов создают водой или жидкостями с пониженной температурой замерзания, предусмотренными проектом.
В качестве источников воды для гидравлического испытания следует использовать естественные или искусственные водоемы (реки, озера, водохранилища, каналы и т.п.), пересекаемые строящимся трубопроводом или расположенные вблизи него.
В состав основных работ по гидравлическому испытанию трубопровода входят:
-подготовка к испытанию;
-наполнение трубопровода водой;
-подъем давления до испытательного;
-испытание на прочность;
-сброс давления до проектного рабочего;
-проверка на герметичность;
-сброс давления до 0,1-0,2 МПа (1-2 кгс/см2).
При необходимости выполняются работы, связанные с выявлением и ликвидацией дефектов.
Для гидравлического испытания трубопровод при необходимости следует разделить на участки, протяженность которых ограничивают с учетом разности высотных отметок по трассе и испытательных давлений, установленных проектом.
Гидравлическое испытание на прочность необходимо производить для:
1) трубопроводов (кроме магистральных нефте- и нефтепродуктопроводов) - на давление 1,1 Рраб в верхней точке и не более гарантированного заводом испытательного давления (Рзав) в нижней точке (рис.1);
Рис.1. График изменения давления при гидравлическом испытании трубопроводов (кроме магистральных нефтепроводов и нефтепродуктопроводов):1 - заполнение трубопровода водой; 2 - подъем давления до Рисп (а - в нижней точке трубопровода Рисп≤ Рдав; б - в верхней точке трубопровода Рисп = 1,1 Рраб); 3 - испытание на прочность; 4 - снижение давления; 5 - проверка на герметичность.
2) нефтепроводов, нефтепродуктопроводов – на гарантированное заводом испытательное давление в нижней точке и не менее 1,1 Рраб в верхней точке (рис.2).
Рис.2. График изменения давления при гидравлическом испытании магистральных нефтепроводов и нефтепродуктопроводов:1 - заполнение трубопровода водой; 2 - подъем давления до Рисп (а - в нижней точке трубопровода Рисп= Рзав; б - в верхней точке трубопровода Рисп ≥1,1 Рраб); 3 - испытание на прочность; 4 - снижение давления; 5 - проверка на прочность.
Время выдержки под испытательным давлением должно составлять 24 ч.
При подготовке к испытанию каждого участка необходимо в соответствии с принятой схемой испытания выполнить следующие операции:
- отключить испытываемый участок от смежных участков сферическими заглушками или линейной арматурой (если перепад давления на арматуре не превысит паспортной характеристики);
- смонтировать и испытать обвязочные трубопроводы наполнительных и опрессовочных агрегатов и шлейф подсоединения к трубопроводу;
- смонтировать (при необходимости) узлы пуска и приема поршней;
- установить контрольно-измерительные приборы;
- смонтировать (при необходимости) воздухоспускные и сливные краны.
При заполнении трубопровода водой для гидравлического испытания из него необходимо удалить воздух.
Удаление воздуха из трубопровода следует осуществлять с помощью поршней-разделителей или через воздухоспускные краны, предназначенные для целей эксплуатации или установленные на концах участка трубопровода.
Диаметр воздухоспускных кранов следует выбирать в зависимости от суммарной производительности наполнительных агрегатов и диаметра испытываемого трубопровода.
Для трубопроводов диаметром до 500 мм и суммарной производительности агрегатов 300 м3/ч устанавливают воздухоспускные краны диаметром 25-32 мм, при диаметрах трубопроводов более 500 мм и большей суммарной производительности агрегатов - воздухоспускные краны диаметром 50-100 мм.
На концах испытываемых участков следует устанавливать воздухоспускные краны диаметром не менее 50 мм.
Наполнение трубопровода без пропуска поршня-разделителя необходимо осуществлять при открытых воздухоспускных кранах, которые закрывают, как только через них перестанет выходить воздух и потечет плотная струя воды.
Наполнение трубопровода с пропуском поршня-разделителя производится при полностью закрытых воздухоспускных кранах и открытой линейной запорной арматуре.
Затем давление в трубопроводе поднимается наполнительными агрегатами до давления, максимально возможного по их техническим характеристикам, а далее - опрессовочными агрегатами - до давления испытания.
Трубопровод считается выдержавшим испытание на прочность и проверку на герметичность, если за время испытания трубопровода на прочность давление остается неизменным, а при проверке на герметичность не будут обнаружены утечки.
После испытания трубопровода на прочность и проверки на герметичность гидравлическим способом из него должна быть полностью удалена вода.
6. Пневматический способ испытания.
Для проведения пневматического испытания давление внутри газопроводов, нефте- и нефтепродуктопроводов создают воздухом или природным газом.
В качестве источников сжатого воздуха используют передвижные компрессорные установки, которые в зависимости от объема полости испытываемого участка и величины испытательного давления применяют по одной или объединяют в группы.
Природный газ для испытания трубопроводов следует подавать от скважины (только для промысловых трубопроводов) или от действующих газопроводов, пересекающих строящийся объект или проходящих непосредственно около него.
Давление при пневматическом испытании на прочность трубопровода в целом на последнем этапе должно быть равно 1,1 Рраб, а продолжительность выдержки под этим давлением - 12 ч.
График изменения давления в трубопроводе при пневматическом испытании приведен на рис.1.
Рис.1. График изменения давления в трубопроводе при пневматическом испытании:1 - подъем давления; 2 - осмотр трубопровода; 3 - испытание на прочность; 4 - сброс давления; 5 - проверка на герметичность.
При пневматическом испытании заполнение трубопровода и подъем давления в нем до испытательного (Рисп) должны вестись через полностью открытые краны байпасных линий при закрытых линейных кранах.
Заполнение трубопровода воздухом или природным газом производится плавно [не более 0,3 МПа (3 кгс/см2) в час], с осмотром трассы при величине давления, равного 0,3 от испытательного на прочность, но не выше 2 МПа (20 кгс/см2). На время осмотра подъем давления должен быть прекращен. Дальнейший подъем давления до испытательного следует производить без остановок. Под испытательным давлением трубопровод должен быть выдержан для стабилизации давления и температуры в течение 12 ч при открытых кранах байпасных линий и закрытых линейных кранах. Затем следует снизить давление до рабочего, после чего закрыть краны байпасных линий и провести осмотр трассы, наблюдения и замеры величины давления в течение не менее 12 ч.
При пневматическом испытании трубопровода на прочность допускается снижение давления на 1 % за 12 ч.
При подъеме давления от 0,3 Рисп. до Рисп. в течение 12 ч при стабилизации давления, температуры и испытаниях на прочность осмотр трассы запрещается.
Осмотр трассы следует производить только после снижения испытательного давления до рабочего с целью проверки трубопровода на герметичность.
В процессе закачки в природный газ или воздух следует добавлять одорант, что облегчает последующий поиск утечек в трубопроводе. Для этого на узлах подключения к источникам газа или воздуха необходимо монтировать установки для дозирования одоранта. Рекомендуемая норма одоризации этилмеркаптаном 50-80 г на 1000 м3 газа или воздуха.
Если при осмотре трассы или в процессе подъема давления будет обнаружена утечка, то подачу воздуха или газа в трубопровод следует немедленно прекратить, после чего должна быть установлена возможность и целесообразность дальнейшего проведения испытаний или необходимость перепуска воздуха или газа в соседний участок.
После окончания испытания трубопровода на прочность давление необходимо снизить до проектного рабочего и только после этого выполнить контрольный осмотр трассы для проверки на герметичность.
Воздух или газ при сбросе давления следует по возможности перепустить в соседние участки.
Учитывая, что при пневматическом испытании процессы наполнения трубопровода природным газом и воздухом до испытательного давления занимают значительное время, необходимо особое внимание обращать на рациональное использование накопленной в трубопроводе энергии путем многократного перепуска и перекачивания природного газа или воздуха из испытанных участков в участки, подлежащие испытанию. Для предотвращения потерь газа или воздуха при разрывах заполнение трубопровода напорной средой и подъем давления до испытательного необходимо производить по байпасным линиям при закрытых линейных кранах.
7.Содержание и оформление трассы МТ
Для сооружения, эксплуатации и ремонта объектов МТ выделяются земельные участки, размером которых регламентируются, утвержденные нормами отводов или проектно-технической документацией. Земельные участки могут предоставляться предприятиям во временное или постоянное пользование. Предоставленные земельные участки во временное пользование, по миновании надобности д. б. приведены в сос
|
|
Кормораздатчик мобильный электрифицированный: схема и процесс работы устройства...
История создания датчика движения: Первый прибор для обнаружения движения был изобретен немецким физиком Генрихом Герцем...
Индивидуальные очистные сооружения: К классу индивидуальных очистных сооружений относят сооружения, пропускная способность которых...
Семя – орган полового размножения и расселения растений: наружи у семян имеется плотный покров – кожура...
© cyberpedia.su 2017-2024 - Не является автором материалов. Исключительное право сохранено за автором текста.
Если вы не хотите, чтобы данный материал был у нас на сайте, перейдите по ссылке: Нарушение авторских прав. Мы поможем в написании вашей работы!