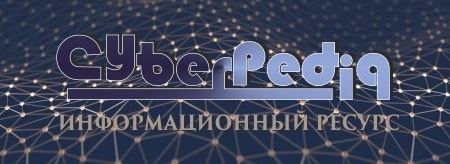
Эмиссия газов от очистных сооружений канализации: В последние годы внимание мирового сообщества сосредоточено на экологических проблемах...
Наброски и зарисовки растений, плодов, цветов: Освоить конструктивное построение структуры дерева через зарисовки отдельных деревьев, группы деревьев...
Топ:
Установка замедленного коксования: Чем выше температура и ниже давление, тем место разрыва углеродной цепи всё больше смещается к её концу и значительно возрастает...
Марксистская теория происхождения государства: По мнению Маркса и Энгельса, в основе развития общества, происходящих в нем изменений лежит...
Интересное:
Наиболее распространенные виды рака: Раковая опухоль — это самостоятельное новообразование, которое может возникнуть и от повышенного давления...
Средства для ингаляционного наркоза: Наркоз наступает в результате вдыхания (ингаляции) средств, которое осуществляют или с помощью маски...
Финансовый рынок и его значение в управлении денежными потоками на современном этапе: любому предприятию для расширения производства и увеличения прибыли нужны...
Дисциплины:
![]() |
![]() |
5.00
из
|
Заказать работу |
|
|
В корпусно-сварочных цехах (КСЦ) производятся работы по изготовлению деталей, плоских и объемных секций корпусов судов (для судостроения), а также работы по ремонту металлических корпусов судов, котлов, судовой вентиляции, люковых закрытий, элементов рулевых устройств (насадка, баллер, перья рулей).
Корпусно-сварочный цех состоит из участков: первичной обработки металла (УПО), корпусно-заготовительного (КЗУ) и сборочно-сварочного (ССУ). В цехе может быть склад металла.
На УПО производится правка металла, его очистка и грунтовка. Оборудование – листогибочные (листоправильные) вальцы, правильно-растяжные машины, щеточные машины, пескоструйные аппараты, дробеструйные и дробеметные аппараты, специальные химические ванны, грунтовочные камеры, сушильные камеры (отделения: предварительной правки и очистки). В настоящее время многие предприятия получают металл, поступающий с металлургических предприятий уже прошедший первичную обработку (правку, очистку, грунтовку). В этом случае отпадает необходимость в участке первичной обработки.
На КЗУ осуществляется изготовление деталей корпуса и элементов набора. В процессе заготовки деталей производятся операции: разметка, резка, гибка и правка заготовок, маркировка. Оборудование: шаблоны, фотопроекционные установки, гильотинные ножницы, газорезательные машины, газовые резаки, гибочные вальцы, кромкогибочные станки, гидравлические прессы.
На ССУ производится изготовление плоских и объемных секций корпусов судов для судостроения и судоремонта, установка листов и секций непосредственно на стапеле. Поэтому корпусная сталь из КЗУ поступает как на ССУ, так и непосредственно на стапель. Оборудование: сварочные трансформаторы, полуавтоматы сварки, электроды, кондукторы, кантователи блоков, гидроталрепы и гидрораспоры, передвижные телескопические подмости.
|
Производственный процесс в КСЦ организуют по следующей схеме. Со склада стали металл подают на правку, затем очистку и грунтовку. Далее его размечают, маркируют и передают на резку, обработку кромок и гибку, после чего собирают плоскостные и объемные секции, прихватывают и сваривают. При строительстве новых судов секции отправляют на сборку корпусов в цех или на стапель. Для ремонта судов, находящихся на стапеле или плаву, используют как сборные секции, так и отдельные листы или профильная сталь.
Плановые задания КСЦ определяют исходя из его производственной мощности, под которой понимают максимально возможный выпуск продукции в единицу времени (квартал, год) при полном использовании оборудования и производственных площадей.
Выпуск продукции КСЦ измеряется стоимостью или трудоемкостью ее изготовления, а также в натуральных единицах – тоннах перерабатываемой стали. Производственная мощность КСЦ обычно измеряется в тоннах перерабатываемой стали либо в нормированных человеко-часах трудоемкости работ.
Вся поступившая со склада корпусная сталь (листовая и профильная) проходит через УПО (100% по черной массе), где подвергается первичной обработке, а затем поступает на КЗУ для изготовления деталей. На КЗУ корпусная сталь подвергается разметке и резке, поэтому она поступает на стапель или ССУ в чистой массе (за вычетом отходов).
В расчетах чистая масса Qчис корпусной стали определяется по выражению:
Qчис=Qчер*kч, (6.1)
где Qчер – объем перерабатываемой стали по черной массе;
kч – коэффициент пересчета черной массы в чистую.
На ССУ поступает лишь часть корпусной стали: около 90% для программы судостроения и 25% для программы судоремонта. Остальная сталь (корпусные детали) поступает непосредственно на стапель.
Мощность КСЦ определяется по выражению:
|
(6.2)
где FПР – производственная площадь цеха;
– средний по цеху норматив съема стали с 1 м2 производственной площади.
Норматив съема стали принимается средним, так как нормативы съема дифференцированы по участкам (стадиям обработки) и по структуре программы (судостроение и судоремонт).
К производственным площадям, включаемым в расчет производственной мощности цеха (участка), относятся площади, занятые оборудованием, рабочими местами, транспортным оборудованием (рольгангами, транспортерами и т.п.), проходами и проездами между оборудованием и рабочими местами (кроме пожарных и магистральных).
Общая площадь цеха кроме производственной включает еще и вспомогательную. К вспомогательной относят площади инструментальных, кладовых, цеховых материальных и межоперационных кладовых и складов, помещения ОТК, пожарные и магистральные проезды.
Производственная площадь цеха FПР определяется как сумма площадей участков:
FПР = Fупо+ Fкзу + Fссу. (6.3)
где Fупо , Fкзу, Fссу – производственные площади участков, соответственно, первичной обработки, корпусно-заготовительного, сборочно-сварочного.
Производственная площадь УПО определяется по формуле:
, (6.4)
где Нупс – норматив съема стали с 1 м2 производственной площади УПО.
Производственная площадь КЗУ:
(6.5)
где QС и QР – объемы переработанной стали по черной массе по объектам судостроения и судоремонта;
НКЗС , НКЗР – нормативы съема стали с 1 м2 производственной площади по судостроению и судоремонту.
Производственная площадь ССУ:
(6.6)
где ,
– объемы переработанной стали по чистой массе на ССУ для объектов судостроения и судоремонта;
НСС, НСР – нормативы съема стали с 1м2 производственной площади по судостроению и судоремонту.
Общая расчетная площадь цеха:
FО= kвсп*(FУПО+FКЗУ+FССУ), (6.7)
где kвсп – коэффициент, учитывающий вспомогательную площадь;
Фактическая площадь цеха определяется с учетом принятой стандартной ширины пролетов bп и расстояний между несущими колоннами lк:
Fф=nп*bп*(mк-lr)=Вц*Lц, (6.8)
где nп – число принятых пролетов в общей ширине здания цеха Вц ;
mк – число колонн в общей длине здания Lц.
В расчетах принимается bп =12,18,24,36 м; lк =6 м.
Для расчета мощности цеха определяется средневзвешенный норматив съема стали с 1 м2 производственной площади:
|
(6.9)
где – средние нормативы съема стали с УПО, КЗУ, ССУ.
ηПР – коэффициент приведения участковых норм к цеховым.
QУПО=Qчер; QКЗУ=QС+QР; QССУ= (6.10)
Значение нормативов и
определяется из выражений:
=
(6.11)
=
(6.12)
Фактическая мощность КСЦ находится по формуле:
(6.13)
Схема организации технологического процесса и производственная структура КСЦ приведена на рис. 16
|
|
Особенности сооружения опор в сложных условиях: Сооружение ВЛ в районах с суровыми климатическими и тяжелыми геологическими условиями...
Своеобразие русской архитектуры: Основной материал – дерево – быстрота постройки, но недолговечность и необходимость деления...
Историки об Елизавете Петровне: Елизавета попала между двумя встречными культурными течениями, воспитывалась среди новых европейских веяний и преданий...
Индивидуальные очистные сооружения: К классу индивидуальных очистных сооружений относят сооружения, пропускная способность которых...
© cyberpedia.su 2017-2024 - Не является автором материалов. Исключительное право сохранено за автором текста.
Если вы не хотите, чтобы данный материал был у нас на сайте, перейдите по ссылке: Нарушение авторских прав. Мы поможем в написании вашей работы!