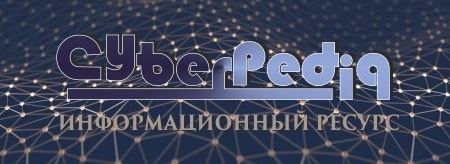
Общие условия выбора системы дренажа: Система дренажа выбирается в зависимости от характера защищаемого...
Археология об основании Рима: Новые раскопки проясняют и такой острый дискуссионный вопрос, как дата самого возникновения Рима...
Топ:
Комплексной системы оценки состояния охраны труда на производственном объекте (КСОТ-П): Цели и задачи Комплексной системы оценки состояния охраны труда и определению факторов рисков по охране труда...
Методика измерений сопротивления растеканию тока анодного заземления: Анодный заземлитель (анод) – проводник, погруженный в электролитическую среду (грунт, раствор электролита) и подключенный к положительному...
Генеалогическое древо Султанов Османской империи: Османские правители, вначале, будучи еще бейлербеями Анатолии, женились на дочерях византийских императоров...
Интересное:
Уполаживание и террасирование склонов: Если глубина оврага более 5 м необходимо устройство берм. Варианты использования оврагов для градостроительных целей...
Аура как энергетическое поле: многослойную ауру человека можно представить себе подобным...
Средства для ингаляционного наркоза: Наркоз наступает в результате вдыхания (ингаляции) средств, которое осуществляют или с помощью маски...
Дисциплины:
![]() |
![]() |
5.00
из
|
Заказать работу |
|
|
ОРГАНИЗАЦИОННАЯ ЧАСТЬ
ТЕХНИКО-ЭКОНОМИЧЕСКАЯ ХАРАКТЕРИСТИКА ТИПА ПРОИЗВОДСТВА
Одной из основных характеристик типа производства является коэффициент специализации, показывающий среднее число операций, закрепленных за одним рабочим местом. Различные типы производства характеризуются следующими коэффициентами специализации (серийности) Кс: массовое — Кс < 1; крупносерийное — Кс = 2-10; среднесерийное — Кс =10 - 20; мелкосерийное — Кс =20-40; единичное — Кс > 40.
В массовом производстве коэффициент специализации определяется:
К c = ,
где — такт выпуска деталей, мин:
=
;
F — действительный годовой фонд времени работы оборудования, ч (при двухсменной работе F д = 4 306 ч);
tшт.cр — среднее штучное время по операциям, мин:
tшт.ср =
где т — число операций (i = 1, 2,..., п).
Проведя расчет, определить тип производства.
РАСЧЕТ ПОТРЕБНОГО КОЛИЧЕСТВА ОБОРУДОВАНИЯ И ОПРЕДЕЛЕНИЕ ЕГО ЗАГРУЗКИ
В поточном производстве потребное количество оборудования определяется по каждой технологической операции, причем количество оборудования должно соответствовать числу рабочих мест. Расчетное число рабочих мест на i-й операции (n ) определяется:
npi =
При определении пpi - после запятой необходимо взять два знака.
По результатам пpi определяем принятое количество оборудования n npi. Коэффициент загрузки оборудования по i-й операции (K3i):
Kзi =
Результаты расчетов сведем в таблицу 1.1.
Таблица 1.1- Расчет количества оборудования (рабочих мест)
И коэффициента их загрузки по участку
№ операции | Тип станка | ![]() | t шт.,мин | n ![]() | n ![]() | Kзi |
7 | ||||||
Итого |
|
По полученным показателям проверить возможность применения многостаночного обслуживания, совмещения профессий и дозагрузки оборудования. Как правило, дозагрузка осуществляется при K3i < 1 с учетом данных о пропускной способности станков, их загрузки основной деталью в следующей последовательности. Результаты расчета сведем в таблицу 1.2.
Таблица 1.2 - Расчет дозагрузки оборудования
№ операции | Наименование оборудования | Количество станков | Штучное время | Пропускная способность станков, ст-час (4306 • гр.З) | Загрузка станков основной деталью, ч | Объем возможной дозагрузки станков, ст-час (гр.5 — гр.6) | Вид догружаемой детали | Штучное время догружаемой детали, мин | Принятое количество догружаемых деталей, шт. | Фактический объем дозагрузки станков, ст-час | Неиспользуемое время, ст-час, (гр.7 — гр.11) | Коэффициент загрузки оборудования и рабочих мест |
Итого |
1. Определяем пропускную способность оборудования (Рi) по каждой операции исходя из годового фонда времени их работы, ст-час (графа 5):
Рi = n F
=4306 n
2. Определяем загрузку оборудования основной деталью по каждой операции (Qoi), ст-час (графа 6):
Qoi =
3. Рассчитаем объем возможной дозагрузки станков по каждой операции (Q в.дi) (графа 7):
Q =P
-Q
4. Выбираем деталь для дозагрузки оборудования. Исходные данные технологического процесса обработки догружаемой детали даны в таблице 1. При заполнении графы 9 определяющим фактором выступает вид оборудования, на котором должна выполняться технологическая операция. График движения изделия по рабочим местам по догружаемой детали может отличаться от основной.
5. Определяем загрузку операций догружаемой деталью (N' ), ед.:
N' =
Для обеспечения равной пропускной способности между операциями принимаем количество догружаемых деталей по минимальному значению N'д, полученному в расчете, т.е. Nд =minN'д. Результаты заносим в графу 10.
|
6. Определяем фактический объем дозагрузки по каждой операции (Q ), ст-час (графа 11):
Q =
7. Определяем неиспользуемое время по операциям ст-час (∆Qi), (графа 12):
.
8. Определяем коэффициент загрузки оборудования и рабочих мест с учетом принятой дозагрузки по каждой операции K3i:
K3i = .
Таким образом, дозагрузка технологического процесса другой деталью позволила повысить загрузку оборудования на участке до уровня, соответствующего массовому производству.
Таблица 1.3 - Расчет количества оборудования на потоке
№ операции | Наименование операции | Основная деталь
![]() | Догружаемая де-
таль ![]() ![]() | Устанавливается в потоке единиц оборудования,
n ![]() | |||||
t ![]() | n ![]() | n ![]() | t ![]() | n ![]() | n ![]() | ||||
Итого | |||||||||
В графе 9 устанавливаемое количество оборудования принимается по каждой группе оборудования по максимальному значению n основной или догружаемой детали.
7. Расчет коэффициента загрузки линии проводится по следующей зависимости:
а) при выпуске отдельных видов деталей:
— основная деталь:
K
— догружаемая деталь:
K
где т — число операций;
б) средний коэффициент загрузки линии в целом (К ):
K
где k — число разновидностей изделий.
Сравнивая итоговый показатель загрузки поточной линии К с итоговыми показателями, полученными в таблицах 1.1 и 1.2, следует сделать вывод о целесообразности производства догружаемой детали в данном потоке.
Дозагрузка считается целесообразной, если отклонение К от итоговых показателей K
(табл. 1.1 и 1.2 приложения) не превышает 10-15%.
На основании табл. 1.3 составляем сводную ведомость потребного оборудования на участке, технико-экономическая характеристика которого представлена в табл. 2.4 приложения.
Таблица 1.4 - Технико-экономическая характеристика оборудования
Тип станка | Габаритные размеры, мм | Количество оборудования, ед ед. на участке | Мощность М, кВт | Категория ремонтной сложности | Сумма единиц ремонтной сложности | Стоимость оборудования
Ц ![]() | Балансовая стоимость оборудования с учётом установке Соб, тыс.у.е. | ||||
Одного станка | Всех станков гр.3*гр.4 | Механической части,Rм | Электрической части, Rэ | Механической части, гр.3 * гр.6 | Электрической части, гр.3 * гр.7 | Одного станка | Всех станков гр.3 * гр.10 | ||||
Вертикально-сверлильный | 3200x1250 | 18,5 | 410,0 | ||||||||
Протяжной | 3250x2250 | 18,0 | 330,0 | ||||||||
Токарный | 2800x1480 | 22,4 | 630,0 | ||||||||
Фрезерный | 2665x4700 | 14,0 | 370,0 | ||||||||
Итого |
Примечание. Балансовая стоимость оборудования с учетом доставки и монтажа выше его прейскурантной стоимости на 10—17%.
|
ПОСТРОЕНИЕ ПЛАНА-ГРАФИКА РАБОТЫ ЛИНИИ
Построим план-график работы поточной линии только по основной детали.
а) Определение периода обслуживания.
Под периодом обслуживания понимаем промежуток времени, в течение которого достигается равенство выпуска деталей по всем операциям и рабочий-оператор завершает полный цикл обслуживания закрепленных за ним станков.
Период обслуживания (Тпо) зависит от величины детали и ее веса (таблица 1.5).
Таблица 1.5 - Рекомендуемые значения периода обслуживания
Величина детали | Примерный вес детали, кг | Продолжительность периода обслуживания Tпобс |
Крупная | свыше 15 | 1— 2ч |
Средняя | 3—15 | 1/2 — 1 смена |
Мелкая | менее 3 | 1 — 2 смены |
Исходя из конкретных условий принимаем Тп обс =...
б) Расчет выработки за период обслуживания.
Выработка за период обслуживания по основной детали определяется:
Bп.обс= ,
Определим загрузку оборудования основной деталью по каждой группе оборудования. Для этого рассчитаем трудоемкость работы по производству основной детали в течение периода обслуживания по каждой операции (Tстi):
Тстi= Bп.обс * tштi,
Результаты расчетов представить в табл. 2.6 приложения (графа 5).
Таблица 1.6 - Расчет графика работы оборудования за период обслуживания
№ операции | Наименование операции | n ![]() | t ![]() | T ![]() | Время работы недогруженного станка Т недогрi | Номер рабочего | График работы оборудования
T ![]() | Примечание |
Итого |
|
Определяем время работы недогруженного станка по каждой операции (Тнедогрi.):
Тнедогрi = Тстi – Тп.обс n
где n — количество единиц оборудования, полностью загруженных в течение периода обслуживания.
Время работы недогруженного станка (графа 6) T ; определяется следующим образом. Например, на операции имеется 2 станка, время работы которых за период обслуживания (Тобс = 1 смене = 8,2 ч = 492 мин) составляет 692 мин. Следовательно, один станок будет полностью загружен, т.е. 492 ч, а второй недогружен. Время работы недогруженного станка составит 692 - 492 = 200 ч. В случае если Тстi< Тп.обс., то время работы недогруженного станка T
= Тстi
в) Проверим соответствие количества оборудования ппрi (или рабочих мест) и численности основных производственных рабочих Чо.п.рi Если n > Чо.п.рi, то надо расставить рабочих по рабочим местам таким образом, чтобы время, необходимое для выполнения планового задания (выработки за период обслуживания), не превышало Тп обс. При этом допускается совмещение работ, многостаночность обслуживания.
В графе 7 — «номер рабочего» — проставляется фактический номер рабочего по каждой единице оборудования в соответствии с его закреплением по операциям и рабочим.
Пример заполнения графы 8 — «график работы оборудования» — показан ниже в таблице:
№ операции | Наименование операции | n ![]() | tштi | Тстi | Т недогр | Номер рабочего | График работы оборудования Т ![]() | Примечание |
Сверлильная | 1,7 | / 492 / / 200 / | ||||||
Протяжка | 0,86 | / 350 / | 1 станок простаивает | |||||
Протяжка | 0,7 | / 285 / | ||||||
Итого |
г) Рассчитать межоперационные оборотные заделы (Zo6) и построить график их изменения.
График движения оборотного задела в прерывно-поточной линии строится на основе графика работы оборудования. Образуются оборотные заделы из-за различной производительности смежных рабочих мест. Их величина определяется между двумя смежными операциями с учетом выделенных фаз, на которые расчленен период работы в каждой паре смежных операций в соответствии с графиком. Размер максимального оборотного задела между парой смежных операций с различной производительностью определяется по формуле:
Z =
-
,
где Zоб — величина изменения межоперационного оборотного задела между двумя смежными операциями за время фазы; Fc — продолжительность фазы, мин, т.е. отрезка времени, в течение которого не происходит никаких изменений в распорядке выполнения операций; n , n
— количество параллельно работающих станков соответственно на предшествующей и последующей операциях; t шт n-1, t шт n штучное время соответственно на предшествующей и последующей операциях, мин.
|
Общая величина Zоб на линии определяется как сумма задела на начало смены на всех операциях.
д) Рассчитать величину технологического задела (Zтехн) на начало периода обслуживания. Его величина определяется:
Z =
где т — количество операций; с — количество рабочих мест на операции; n' — количество одновременно обрабатываемых на каждом рабочем месте деталей. В нашем примере п' = 1 шт.
е) Рассчитать величину транспортного задела (Z).
Величина Z зависит от принятого порядка передачи деталей с операции на операцию и характера транспортного средства (табл. 1.7)
Таблица 1.7 - Рекомендуемые размеры транспортных партий, шт.
Вес детали, кг | Размеры транспортной партии при средней трудоемкости операций по данной детали | |||
До 1 мин | 1,0 — 2,5 мин | 2,5 — 5,0 мин | 5,0 — 11,0 мин | |
До 0,1 | ||||
0,1-0,2 | ||||
0,2 — 0,5 | ||||
0,5 — 1,0 | ||||
1,0 — 2,0 | ||||
2,0 — 5,0 |
При периодической транспортировке
Z =p (m-1),
где р — размер передаточной транспортной партии.
В остальных случаях рекомендуется поштучная передача.
ж) Рассчитать общую величину цикловых заделов (Z ) прямоточной линии:
Z =Z
+Z
+Z
Расчет провести по основной или догружаемой детали.
Таким образом, в массовом производстве одна и та же продукция выпускается через одинаковый промежуток времени — такт. Каждое рабочее место выполняет свою операцию. Если, например, ежесуточно выпускается 200 единиц продукции, то это значит, что на каждом рабочем месте закрепленная операция выполняется 200 раз.
ОРГАНИЗАЦИЯ И ПЛАНИРОВАНИЕ ОБЕСПЕЧЕНИЯ ИНСТРУМЕНТОМ
В условиях массового производства комплектация и доставка нужного инструмента осуществляется согласно сменному заданию или на основании карты подготовки выполнения сменного задания. Снабжение рабочих мест инструментом централизованное. Заточка инструмента осуществляется централизованно.
Таблица 1.8 - Время работы инструмента до полного износа
Наименование инструмента | L, мм | 1, мм | t ![]() | Расчет T ![]() |
Резец подрезной | 2,5 | 3,0 | ||
Резец проходной | 4,0 | 2,0 | ||
Сверла | 0,7 | 2,5 | ||
Фреза | 7,3 | 0,6 | 4,0 |
2. Определяем расход режущего инструмента на программу (табл. 1.9).
Таблица 1.9 - Расчет потребности режущего инструмента
Наименование инструмента | Деталь | N, шт. | t ![]() | d ![]() | T ![]() | И ![]() |
Резец подрезной | основная догружаемая | 0,65 0,75 | ||||
Всего | ||||||
Резец проходной | основная догружаемая | 0,60 0,65 | ||||
Всего | ||||||
Сверла | основная догружаемая | 0,7 0,8 | ||||
Всего | ||||||
Фреза | основная догружаемая | 0,7 0,8 | ||||
Всего |
Примечание: условно принимаем, что резец подрезной устанавливается на одной токарной операции, а резец проходной — на другой.
3. Определяем запас инструмента на рабочих местах. Количество инструмента, находящегося на рабочих местах при периодической его подноске (Z ), определяется:
Z =
где t — периодичность подноски инструмента к рабочим местам, ч. Обычно t
выбирается в зависимости от периодичности съема и принимается равной или кратной длительности смены; t
— периодичность съема инструмента со станка, ч. Устанавливается в соответствии с величиной стойкости инструмента:
t =
n — число рабочих мест, на которых применяется данный инструмент; m
— количество одноименного инструмента, применяемого на рабочем месте (в приводимом примере(m
=1); Кс.з— коэффициент страхового запаса инструмента на рабочих местах. Обычно К
= 1; на многорезцовых станках К
= 2 ~ 4.
Расчет проводится в следующей последовательности.
а) Определим периодичность съема t и подачи инструмента t
со станка (табл. 1.10).
Таблица 1.10 - Периодичность съема инструмента со станков
Наименование инструмента | t ст, ч ![]() | t ![]() | d ![]() | t ![]() | t ![]() |
Резец подрезной | 3,0 | 0,65 | |||
Резец проходной | 2,0 | 0,60 | |||
Сверла | 2,5 | 0,7 | |||
Фреза | 4,0 | 0,7 |
Если резец или сверло применяется на нескольких операциях технологического процесса изготовления детали, расчет надо вести по каждой операции ввиду различия tштi.
б) Определяем запас инструмента на рабочих местах по ранее приведенной формуле.
Таблица 1.11 - Норма износа измерительных инструментов по видам
Наименование инструмента | а ![]() | b, шт. | ![]() | ![]() | Тм, шт. |
Скоба | 0,7 | ||||
Калибр | 0,7 |
Таблица 1.12 - Расход измерительного инструмента по видам для основной и догружаемой детали
Наименование инструмента | ![]() | К ![]() | Т ![]() | К ![]() |
Для основной детали | ||||
Скоба | 0,75 | |||
Калибр | 0,8 | |||
Для догружаемой детали | ||||
Скоба | 0,75 | |||
Калибр | 0,8 |
РАСЧЕТ ПЛОЩАДИ УЧАСТКА
Площадь участка (S ) состоит из основной производственной площади (S
) и вспомогательной (S
):
S =S
+S
.
Основная производственная площадь (табл. 1.13) составляет (S ):
S =
(S
S
где S1 и S2 — площадь, занимаемая соответственно станками и проходами, м2; п — принятое количество станков.
Таблица 1.13 - Расчет производственной площади участка
№ операции, i | Наименование оборудования | Габаритные размеры | Принятое количество станков П ![]() | Площадь, м2 |
одного станка, S ![]() | проходов, S ![]() | общая, S ![]() | ||
Всего |
Площадь проходов принимается на 1 станок в среднем 12 м2.
Вспомогательная площадь (S ):
S
где S — складская площадь под заготовки и готовые детали (примем 15% от производственной); S
— площадь инструментально-раздаточных кладовых (ИРК) для массового производства примем 0,35 м2 на станок; S
— площадь одного контрольного пункта (6 м2); Sбыт — площадь бытовых и конторских помещений (примем 1,22 м2 на 1 рабочего в наибольшую смену).
Произведем расчет вспомогательной площади участка. Определим общую площадь участка S .
Определим объем здания (V):
V = S *h,
где h — высота здания (9,25 м).
Стоимость здания определим по формуле:
С = V*Ц
,
где Ц —цена 1 м3 здания (600 у.е.).
Таблица 1.14 - Сроки ввода оборудования в эксплуатацию по основному производству
Наименование станков | Количество единиц | Категория сложности ремонта | Месяцы установки или капитального ремонта станков по годам (предлагаемые) | |||
Вертикально-сверлильные | II, V | VI, VIII | 1,Х | И, IV | ||
Протяжные | I.VI | II, III, V | VII, IX | I | ||
Токарные | XI, III | V, IX, X | III, IX | |||
Фрезерные | I, IV | V, IX |
Структура ремонтного цикла имеет следующий вид:
К-0- M - О - М2 – О - С
- О - М3 – О - М4 – О - С2 – О - М5 – О - М6 – О - К.
Продолжительность ремонтного цикла Т = 24 000 ч, или 6 лет, при двухсменной работе оборудования.
а) Рассчитать продолжительность в месяцах межремонтного (Т и межосмотрового (Т
) периодов по формулам:
Т
Т
где n n
n
— соответственно количество малых, средних ремонтов и осмотров в структуре ремонтного цикла.
б) Составить график ремонта оборудования, установленного в первом году (табл. 1.15 приложения), во втором году (табл. 1.16), в третьем году (табл. 1.17) и в четвертом году (табл. 1.18).
Порядок выполнения графика ремонта оборудования следующий.
Пусть Т мес., Т
= 4 мес. Оборудование введено в эксплуатацию в феврале первого года. Тогда структуру ремонтного цикла можно представить таблицей:
Оборудование | К | О | m ![]() | О | М ![]() | О | С ![]() | О | М3 | О | М4 | О | С2 | … |
Сверлильное | II | VI 01 | X | II | VI 02 | X | II | VI 03 | X | II | VI 04 | X | II |
в) Составить график ремонта оборудования на планируемый год (табл. 2.19 приложения). Номер планируемого года определяется учащимся самостоятельно.
Таблица 1.15 - График ремонта оборудования, установленного в 2001 г.
Наименование оборудования | Nст | К | К | О | M1 | О | М2 | O | C ![]() | O | М3 | O | М4 | O | С2 | О | М5 | О | М6 | O |
Сверлильное | II V | |||||||||||||||||||
Протяжное | I VI | |||||||||||||||||||
Токарное | XI III |
Таблица 1.16 - График ремонта оборудования, установленного в 2002 г.
Наименование оборудования | Nст | К | О | M1 | О | М2 | O | C ![]() | O | М3 | O | М4 | O | С2 | О | М5 | О | М6 | O | K |
Сверлильное | VI VIII | |||||||||||||||||||
Протяжное | II III V | |||||||||||||||||||
Токарное | V IX X | |||||||||||||||||||
Фрезерное | I IV |
Таблица 1.17 - График ремонта оборудования, установленного в 2003 г.
Наименование оборудования | Nст | К | О | m ![]() | О | М2 | O | C ![]() | O | М3 | O | М4 | O | С2 | М5 | О | M6 | O | K | |
Сверлильное | I X | |||||||||||||||||||
Протяжное | VII IX | |||||||||||||||||||
Токарное | III IX | |||||||||||||||||||
Фрезерное | V IX |
Таблица 1.18 - График ремонта оборудования, установленного в 2004 г.
Наименование оборудования | Nст | К | О | m ![]() | О | М2 | O | C ![]() | O | М3 | O | М4 | O | С2 | М5 | О | M6 | O | K | |
Сверлильное | II IV | |||||||||||||||||||
Протяжное | I |
|
|
Археология об основании Рима: Новые раскопки проясняют и такой острый дискуссионный вопрос, как дата самого возникновения Рима...
Биохимия спиртового брожения: Основу технологии получения пива составляет спиртовое брожение, - при котором сахар превращается...
Механическое удерживание земляных масс: Механическое удерживание земляных масс на склоне обеспечивают контрфорсными сооружениями различных конструкций...
Папиллярные узоры пальцев рук - маркер спортивных способностей: дерматоглифические признаки формируются на 3-5 месяце беременности, не изменяются в течение жизни...
© cyberpedia.su 2017-2024 - Не является автором материалов. Исключительное право сохранено за автором текста.
Если вы не хотите, чтобы данный материал был у нас на сайте, перейдите по ссылке: Нарушение авторских прав. Мы поможем в написании вашей работы!