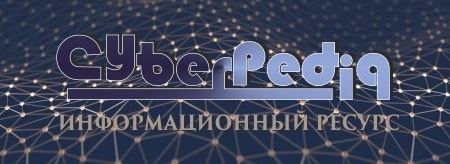
Состав сооружений: решетки и песколовки: Решетки – это первое устройство в схеме очистных сооружений. Они представляют...
Общие условия выбора системы дренажа: Система дренажа выбирается в зависимости от характера защищаемого...
Топ:
Оценка эффективности инструментов коммуникационной политики: Внешние коммуникации - обмен информацией между организацией и её внешней средой...
Методика измерений сопротивления растеканию тока анодного заземления: Анодный заземлитель (анод) – проводник, погруженный в электролитическую среду (грунт, раствор электролита) и подключенный к положительному...
Интересное:
Распространение рака на другие отдаленные от желудка органы: Характерных симптомов рака желудка не существует. Выраженные симптомы появляются, когда опухоль...
Средства для ингаляционного наркоза: Наркоз наступает в результате вдыхания (ингаляции) средств, которое осуществляют или с помощью маски...
Искусственное повышение поверхности территории: Варианты искусственного повышения поверхности территории необходимо выбирать на основе анализа следующих характеристик защищаемой территории...
Дисциплины:
![]() |
![]() |
5.00
из
|
Заказать работу |
|
|
Метод основан на последовательности операций:
1. Получения технического кремния,
SiС(гв) + Si02 (тв) -» Si(тв) + Si02(г) + СО(г) (3)
2. Перевода технического кремния в легколетучее соединение (трихлорсилан),
Si(тв) + ЗНСl(г) -» SiHCl3(г) + Н2 (г) (4)
3. Очистки трихлорсилана,
4. Восстановлении трихлорсилана,
SiHC13(г) + Н2 (г) = Si(тв) + ЗНСl(г) (7)
5. Проверка качества полученного поликристаллического кремния.
Последовательность операций представлена блок-схемой на рис.8.
Получение технического кремния. Исходным сырьем для большинства изделий микроэлектронной промышленности служит электронный кремний. Первым этапом его получения является изготовление сырья, называемого техническим (металлургическим) кремнием.
Рис.7. Схематическое изображение получения технического кремния в электродуговой печи.
Этот технологический этап реализуется с помощью дуговой печи с погруженным в нее электродом. Печь загружается кварцитом Si02 и углеродом в виде угля, щепок и кокса (рис.7) [3].
Температура реакции Т = 1800°С, энергоемкость W = 13 кВт/час. В печи происходит ряд промежуточных реакций. Результирующая реакция может быть представлена в виде реакции:
SiС(гв) + Si02 (тв) -» Si(тв) + Si02(г) + СО(г) (3)
Рис.8. Блок-схема 1: получение поликристаллического кремния восстановлением трихлорсилана.
Получаемый таким образом технический кремний содержит 98%
Si, 1-2 % Pb, Аu, В, Р, Са, Cr, Сu, Mg, Мn, Ni, Тi, V.
Получение трихлорсилана. Классическая технология поликристал-лического кремния основана на процессе водородного восстановления трихлорсилана, восстановления тетрахлорида кремния цинком и пиролиза моносилана, Большую часть кремния (около 80%) получают путем водородного восстановления трихлорсилана (ТХС).
|
Достоинства этого процесса - легкость и экономичность получения ТХС, эффективность очистки ТХС, высокое извлечение и большая скорость осаждения кремния (извлечение кремния при использовании тетрахлорида кремния составляет 15%, а при использовании ТХС - не менее 30%), меньшая себестоимость продукции.
Трихлорсилан обычно получают путем гидрохлорирования кремния: взаимодействием технического кремния с хлористым водородом или со смесью газов, содержащих хлористый водород, при температуре 260-400°С.
Процесс синтеза трихлорсилана сопровождается побочными реакциями образования тетрахлорида кремния и других хлорсиланов, а также галогенидов металлов, например А1С13, ВС13,FeC13 и т.д. Реакции получения хлорсиланов кремния являются обратимыми и экзотермическими (с выделением теплоты):
Si(тв) + ЗНСl(г) -» SiHCl3(г) + Н2(г) (4)
Si(тв) + 4НСl(г) -» SiCl4(г) + 2Н2(г) (5)
При температуре выше 300°С ТХС в продуктах реакций почти полностью отсутствует.
Для повышения выхода ТХС температуру у процесса снижают, что приводит к значительному замедлению скорости реакции (5). Для увеличения скорости реакции (4) используют катализаторы (медь, железо, алюминий и др.). Так, например,при введении в исходный кремний до 5 % меди содержание ТХС в смеси продуктов реакции при температуре 265 °С доходит до 95 %.
Синтез ТХС ведут в реакторе «кипящего» слоя, в который сверху непрерывно подают порошок технического кремния с размером частиц 0,01-1 мм.
Псевдоожиженный слой частиц толщиной 200-600мм создают встречным потоком хлористого водорода, который поступает в нижнюю часть реактора со скоростью 1-8 см/с. Этим самым обеспечивается перевод гетерогенного химико-технологического процесса из диффузионной в кинетическую область.
Так как процесс является экзотермическим, то для стабилизации режима в заданном интервале температур осуществляют интенсивный отвод теплоты и тщательный контроль температуры на разных уровнях псевдоожиженного слоя. Кроме температуры контролируют расход хлористого водорода и давление в реакторе.
|
Значительное влияние на выход ТХС оказывает присутствие примесей воды и кислорода в исходных компонентах. Эти примеси, окисляя порошок кремния, приводят к образованию на его поверхности плотных слоев Si02, препятствующих взаимодействию кремния с хлористым водородом и соответственно снижающих выход ТХС.
Так, например, при увеличении содержания Н20 в НС1 с 0,3 до 0,4 % выход ТХС уменьшается с 90 до 65 %.
В связи с этим хлористый водород, а также порошок кремния перед синтезом ТХС проходят тщательную осушку и очистку от кислорода.
Образующаяся в процессе синтеза ТХС парогазовая смесь поступает в зону охлаждения, где ее быстро охлаждают до 40 — 130 °С, в результате чего выделяются в виде пыли твердые частицы примеси (хлориды железа, алюминия и др.), которые вместе с частицами не прореагировавшего кремния и полихлоридов (SinC12n+2) затем отделяются с помощью фильтров.
После очистки от пыли (являющейся взрывоопасным продуктом) парогазовая смесь поступает на конденсацию при температуре — 70 °С. Происходит отделение SiHC13 и SiC14 (температуры кипения 31,8 и 57,2 °С соответственно) от водорода и НС1 (температура кипения 84 °С).
Полученная в результате конденсации смесь состоит в основном из ТХС (до 90-95 %), остальное — тетрахлорид кремния, который отделяют затем ректификацией. Выделяемый в результате разделения тетрахлорид кремния в дальнейшем используют для производства силиконов, кварцевого стекла, а также для получения трихлорсилана путем дополнительного гидрирования в присутствии катализатора.
На практике существуют и ситуации, когда ТХС получают как отходы производства на соседних химических производствах.
Очистка трихлорсилана. Получаемый ТХС содержит большое количество примесей, очистка от которых представляет сложную задачу. Наиболее эффективным методом очистки является ректификация, однако осуществить полную и глубокую очистку от примесей, имеющих различную физико-химическую природу, применяя только ректификацию, сложно. В связи с этим для увеличения глубины очистки по ряду примесей применяются дополнительные меры.
Так, например, для примесей, трудно очищаемых кристаллизационными методами (бор, фосфор, углерод), необходима наиболее глубокая очистка ТХС. Поэтому для повышения эффективности очистки эти микропримеси переводят в нелетучие или комплексные соединения. Для очистки от бора, например, пары ТХС пропускают через алюминиевую стружку при 120 °С. Поверхность стружки, поглощая бор, приводит к почти полной очистке от него ТХС. Побочно образующийся хлорид алюминия далее возгоняют при температуре 220 — 250 °С, а затем отделяют фракционной конденсацией
|
Кроме алюминия могут быть использованы серебро, медь или сурьма. Добавка меди к алюминию позволяет одновременно очищать ТХС от мышьяка и сурьмы. Повысить эффективность очистки от бора позволяет также введение в ТХС пента- или оксихлоридов фосфора. При этом образуются нелетучие комплексные соединения фосфора с бором, которые затем отделяют ректификацией.
Перевод бора в нелетучие соединения может быть также осуществлен путем добавления в ТХС трифенилхлорметана (или триметиламина, ацетонитрила, аминокислоты, кетона и т. д.), приводящего к образованию с бором комплексов, которые затем удаляют ректификацией. Очистку от борсодержащих примесей осуществляют также адсорбцией в реакторах, заполненных алюмогелем или другими гелями (Fe203, Mg(OH)2) с последующей ректификацией ТХС.
Для очистки от фосфора ТХС насыщают хлором с переводом трихлорида фосфора в пентахлорид.
Контроль чистоты получаемого после очистки ТХС осуществляют методами ИК-спектроскопии, хроматографии, а также измерением типа и величины проводимости тестовых образцов кремния, получаемых из проб ТХС.
Тестовый метод существует в двух модификациях. В соответствии с первой на лабораторной установке осаждением из газовой фазы получают поликристаллический стержень кремния диаметром 10-20 мм. Далее из него бестигельной зонной плавкой выращивают контрольный монокристалл, по типу проводимости и удельному сопротивлению которого судят о чистоте ТХС.
Для определения концентрации доноров проводят один проход зоны в аргоне или вакууме и получают монокристалл n-типа, по удельному сопротивлению которого судят о чистоте по донорам (удельное сопротивление по донорам); для определения концентрации бора приводят 5 — 15 проходов зоны в вакууме, в результате чего получают монокристалл р-типа, по удельному сопротивлению которого судят о чистоте по бору (удельное сопротивление по бору).
|
По второй модификации тестового метода монокристалл кремния выращивают непосредственно из газовой фазы на монокристаллический стержень в миниатюрном кварцевом реакторе и далее измеряют его удельное сопротивление.
Остаточное содержание микропримесей в ТХС после очистки не должно превышать, %: бора — 3*10-8, фосфора —10-7, мышьяка 5*10-10, углерода (в виде углеводородов) — 5*10-7.
По электрическим измерениям тестовых образцов остаточное содержание доноров должно обеспечивать удельное сопротивление кремния п-типа не менее 5000 Ом*см, а по акцепторам у кристаллов р-типа — не менее 8000 Ом*см.
Восстановление очищенного трихлорсилана и в результате этого получение поликристаллического кремния проводят в атмосфере водорода на поверхности разогретых кремниевых стержней-основах диаметром 4-8 мм (до 30 мм), получаемых методом выращивания с пьедестала(рис.9) [15].
Уравнение происходящей реакции выглядит так:
SiHC13(г) + Н2(г) = Si(тв) + 3НСl(г) (6)
В некоторых технологиях вместо цилиндрических стержней используются пластинчатые (толщиной 1-5 мм и шириной 30-100 мм) с большей площадью осаждения. Материалом для выращивания стержней служит высококачественный полукристаллический кремний.
В некоторых технологиях вместо цилиндрических стержней используются пластинчатые (толщиной 1-5 мм и шириной 30-100 мм) с большей площадью осаждения. Материалом для выращивания стержней служит высококачественный поликристаллический кремний.
Рис.9. Схема установки восстановления трихлорсилана.
Поверхность стержней-основ подвергают ультразвуковой очистке, травлению в смеси кислот (например, HF+HN03), отмывке и сушке. К стержням-основам для получения высококачественного поликристаллического кремния предъявляются высокие требования по чистоте: они должны иметь удельное сопротивление по донорам >700 Ом*см и по бору >5000 Ом*см.
Из стержней изготовляют электронагреватели (например, П-образной формы) и их нагрев осуществляют пропусканием электрического тока. По мере роста диаметра стержней силу тока постепенно увеличивают.
Выбор условий водородного восстановления ТХС осуществляют на основе оптимальной взаимосвязи следующих параметров процесса:
-равновесной степени превращения SiHCl3 в Si, кристаллической структуры получаемых стержней,
-температуры процесса, энергозатрат,
-мольного отношения H2: SiHCl3,
-скорости осаждения кремния.
Оптимальными условиями процесса восстановления считают температуру 1100 — 1150 °С, мольное отношение Н2: SiHCl3 в пределах 5-15 [22]. При температуре стержней ниже оптимальной повышается степень превращения ТХС в тетрахлорид кремния и уменьшается выход кремния. Увеличение температуры приводит к существенному возрастанию энергозатрат. При оптимальном мольном отношении Н2: SiHCl3 = 5-15 стержни имеют плотную мелкокристаллическую структуру и относительно ровную поверхность.
|
За пределами этих отношений образуется неровная поверхность, структура стержней становится крупнокристаллической с включениями газовых пор, которые при последующем плавлении поликремния в процессе выращивания кристаллов приводят к бурлению и разбрызгиванию расплава.
Количество стержней, устанавливаемых в различных промышленных реакторах, колеблется от 2 до 16, длина каждого стержня составляет до 2 м, конечный диаметр 150- 250 мм. За счет взаимного нагрева стержней скорость осаждения кремния в многостержневых аппаратах выше, чем в двухстержневых; скорость роста диаметра стержней достигает 0,5 мм/ч, энергозатраты составляют 3000 кВт *ч/кг.
Для повышения чистоты получаемого кремния производят тщательную очистку водорода, реакторы делают из специальных сталей, а также защищают их поверхность от взаимодействия с газовой средой путем введения дополнительных кварцевых (кремниевых) колпаков, отделяющих реакционный объем от стенок реактора. Хорошей защитой стенок реактора является покрытие их защитными пленками, например, полихлорсиланом.
Получение кремния из моносилана SiH4 путем термического разложения производится по аналогичной методике при температурах около 1000°С. Образующийся в реакции 7 водород обладает высокой степенью чистоты и используется в сопутствующем производстве.
SiH4(т)=Si(т) + 2H2(г) (7)
Также и получаемый по этой технологии поликремний обладает более высокой степенью чистоты, чем кремний, получаемый восстановлением ТХС, но получается более дорогим.
Извлечение кремния из SiCl4 и SiI4 осуществляют восстановлением тетрахлорида кремния цинком, либо термической диссоциацией тетрахлорида.
Получаемые полукристаллические стержни перед использованием в процессах выращивания монокристаллов методом Чохральского разламывают на удобные для загрузки в тигель куски или разрезают на мерные заготовки. Для процесса бестигельной зонной плавки стержни обрабатывают под нужный диаметр шлифовкой.
Удаление поверхностных слоев, обогащенных примесями и газами, кроме того, предотвращает разбрызгивание кремния из расплавленной зоны.
Современные технологические схемы получения поликристаллического кремния включают в себя регенерацию и повторное использование всех компонентов и продуктов реакций восстановления (пиролиза), что улучшает технико-экономические показатели процесса, снижает себестоимость получаемого кремния, делает процесс экологически более чистым.
Рассмотренный процесс осаждения поликристаллического кремния используется также для получения на его основе полукристаллических труб на углеродных оправках. Вследствие высокой чистоты и прочности эти трубы применяются вместо кварцевых в печах высокотемпературных процессов (свыше 1200°С) в технологии полупроводниковых и микроэлектронных приборов.
Кремниевые трубы не подвержены просаживанию или другой деформации в течение нескольких лет эксплуатации, несмотря на постоянное температурное циклирование между 900 и 1250°С, тогда как кварцевые трубы имеют ограниченный срок службы при тех же процессах.
Потребление поликристаллического кремния электронной промышленностью составляет несколько тысяч тонн в год.
Для получения кремния высокой чистоты полукристаллические стержни подвергают кристаллизационной очистке методом зонной плавки в вакууме. При этом помимо кристаллизационной очистки кремния от нелетучих примесей (преимущественно акцепторов) происходит существенная очистка его от летучих доноров за счет испарения их из расплавленной зоны. Так, после 15 проходов расплавленной зоны со скоростью 3 мм/мин, получают монокристаллы кремния р-типа электропроводности с остаточной концентрацией примеси менее 10-13 см-3 и удельным сопротивлением (по бору) более 104 Ом*см.
|
|
История создания датчика движения: Первый прибор для обнаружения движения был изобретен немецким физиком Генрихом Герцем...
Автоматическое растормаживание колес: Тормозные устройства колес предназначены для уменьшения длины пробега и улучшения маневрирования ВС при...
Кормораздатчик мобильный электрифицированный: схема и процесс работы устройства...
Типы сооружений для обработки осадков: Септиками называются сооружения, в которых одновременно происходят осветление сточной жидкости...
© cyberpedia.su 2017-2024 - Не является автором материалов. Исключительное право сохранено за автором текста.
Если вы не хотите, чтобы данный материал был у нас на сайте, перейдите по ссылке: Нарушение авторских прав. Мы поможем в написании вашей работы!