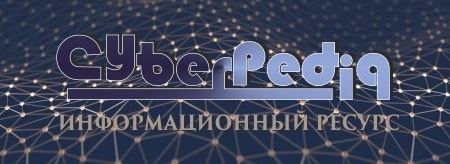
Своеобразие русской архитектуры: Основной материал – дерево – быстрота постройки, но недолговечность и необходимость деления...
Индивидуальные и групповые автопоилки: для животных. Схемы и конструкции...
Топ:
Выпускная квалификационная работа: Основная часть ВКР, как правило, состоит из двух-трех глав, каждая из которых, в свою очередь...
История развития методов оптимизации: теорема Куна-Таккера, метод Лагранжа, роль выпуклости в оптимизации...
Комплексной системы оценки состояния охраны труда на производственном объекте (КСОТ-П): Цели и задачи Комплексной системы оценки состояния охраны труда и определению факторов рисков по охране труда...
Интересное:
Инженерная защита территорий, зданий и сооружений от опасных геологических процессов: Изучение оползневых явлений, оценка устойчивости склонов и проектирование противооползневых сооружений — актуальнейшие задачи, стоящие перед отечественными...
Лечение прогрессирующих форм рака: Одним из наиболее важных достижений экспериментальной химиотерапии опухолей, начатой в 60-х и реализованной в 70-х годах, является...
Наиболее распространенные виды рака: Раковая опухоль — это самостоятельное новообразование, которое может возникнуть и от повышенного давления...
Дисциплины:
![]() |
![]() |
5.00
из
|
Заказать работу |
|
|
Производственный цикл является важным показателем технико-экономического развития, который определяет возможности предприятия по объему выпуска продукции и затраты на ее производство.При организации производственного процесса во времени главной задачей является достижение минимально возможной длительности производственного цикла.Сокращение производственного цикла дает возможность каждому производственному подразделению (цеху, участку) выполнить заданную программу с меньшим объемом незавершенного производства. Это значит, что организация получает возможность ускорить оборачиваемость оборотных средств, выполнить установленный план с меньшими затратами этих средств, высвободить часть оборотных средств на развитие других направлений деятельности. Важнейшими факторами сокращения производственного цикла является внедрение передовых технологий и автоматизация производственных процессов.
Длительность производственного цикла относится к нормативам организации производственного процесса. Без научно-обоснованного расчета длительности производственного цикла практически невозможно корректно составить производственную программу предприятия, определить основные технико-экономические и финансовые показатели деятельности компании.
Производственный цикл можно определить, как промежуток времени от начала до завершения производственного процесса. Кроме того, производственный цикл можно рассматривать как период пребывания различных видов ресурсов в производственном процессе с начала производства до выпуска готового продукта (услуги).
Производственный цикл, являясь частью времени производства, отличается от него на период, в течение которого предметы труда находятся в производственных запасах. (В телекоммуникациях, где процесс производства и потребления услуг совпадают по времени, производственный цикл совпадает по продолжительности со временем производства).
|
Производственный цикл охватывает рабочий период и длительность перерывов в производстве, обусловленных физическими, химическими, биологическими процессами (например, дубление кожи и т.п.) или природой предметов труда, технологией и организацией производства.
Рабочий период – это время, в течение которого производится непосредственное воздействие на предмет труда либо самим рабочим, либо машинами и механизмами под его управлением; время подготовительно заключительных работ; время естественных технологических процессов; время технологического обслуживания.
Время естественных технологических процессов – это время, в течение которого предмет труда изменяет свои характеристики без непосредственного воздействия человека или техники (сушка на воздухе древесины, рост и созревание рассады земляники и т.п.). Для ускорения производства многие естественные процессы осуществляются в искусственно созданных условиях – например, сушка древесины в специализированных сушильных камерах.
Время технологического обслуживания включает в себя: контроль качества обработки изделия; контроль режимов работы оборудования, его настройку, легкий ремонт; уборку рабочего места; подвоз заготовок, материалов, приемку и уборку обработанной продукции.
На длительность рабочего периода оказывает влияние разного рода факторы, например такие, как: качество проектно-конструкторских работ; уровень унификации и стандартизации изделий; степень точности изделий (высокая точность требует дополнительной обработки, что удлиняет производственный цикл); организационные факторы (организация рабочего места, размещение складских помещений и др.). Недостатки организационного характера увеличивают подготовительно-заключительное время (время технологического обслуживания).
|
Рабочий период состоит из времени выполнения технологических и нетехнологических операций; к числу последних относятся все контрольные и транспортные операции с момента выполнения первой производственной операции и до момента сдачи законченной продукции.
Операционным циклом называют время выполнения технологических операций и подготовительно-заключительных работ.
Структура производственного цикла в различных отраслях экономики РФ и на разных предприятиях неодинакова. Она определяется характером производимой продукции (услуг), технологическими процессами, уровнем техники и организации производства.
Несмотря на различия в структуре, возможности сокращения длительности производственного цикла заложены как в сокращении рабочего времени, так и в сокращении времени перерывов на каждой стадии производства и на каждом производственном участке. Это достигается путем проведения различных мероприятий как технического (конструкторского, технологического), так и организационного порядка.
Различают производственные циклы изделия в целом, циклы сборных единиц и отдельных деталей, циклы выполнения однородных операций, циклы выполнения отдельных операций.
Вследствие того, что производственный процесс протекает во времени и пространстве, производственный цикл, можно измерить длиной пути движения изделия и его комплектующих элементов, а так же временем, в течение которого продукт или услуга проходит весь путь от производства до реализации.
Длина производственного цикла– это не линия, а площадь, на которой размещается специализированное оборудование, инвентарь, поэтому на практике для измерения производственного цикла в большинстве случаев определяется не длина пути, а площадь и объем помещения, в котором размещается производство.
Измерение производственного цикла с помощью длины пути ведется от первого рабочего места, где началось производство продукта и его компонентов, до последнего. Отсюда необходима такая планировка рабочих мест, которая максимально сокращает и облегчает коммуникационные и транспортные связи между ними. Чем короче путь движения продукта или услуги в производственном процессе, тем меньше расходы на его межоперационную транспортировку, меньше требуется производственной площади и, как правило, меньше времени на обработку.
|
Продолжительность производственного цикла во времени– это интервал календарного времени от начала первой производственной операции до окончания последней; измеряется в днях, часах, минутах, секундах в зависимости от вида изделия и стадии обработки.
Структура производственного цикла во времени может рассматриваться с трех позиций: рабочего, механизмов и предметов труда (прохождения заготовок и деталей). Часть элементов цикла может совмещаться (перекрываться), например, основное время – с техническим и организационным обслуживанием, обслуживание деталей - с подготовкой рабочего места.
Время перерывов в работе– это время, в течение которого не производится никакого воздействия на предмет труда и не происходит изменение его качественной характеристики, но продукция еще не является готовой и процесс производства не закончен.
Различают регламентированные и нерегламентированные перерывы.
Регламентированные перерывы делятся на внутрисменные (межоперационные) и междусменные (связанные с режимом работы).
Межоперационные перерывы делятся на:
· перерывы, связанные с партиями изделий– имеют место при обработке деталей партиями. Каждая деталь или узел, поступая к рабочему месту в составе партии, пролеживают до начала и по окончании обработки, пока вся партия не пройдет через данную операцию;
· перерывы комплектования– возникают в тех случаях, когда детали и узлы пролеживают в связи с незаконченностью изготовления других изделий, входящих в один комплект;
· перерывы ожидания– обусловлены несогласованностью (несинхронностью) длительности смежных операций технологического процесса, возникают, когда предыдущая операция заканчивается раньше, чем освобождается рабочее место для выполнения следующей операции.
Междусменные перерывы включают в себя перерывы между рабочими сменами, обеденные перерывы, перерывы для отдыха рабочих, выходные и праздничные дни.
Нерегламентированные перерывы связаны с организационно-техническими неполадками (несвоевременное обеспечение рабочего места материалом, инструментом, поломка оборудования, нарушение трудовой дисциплины и т.д.). Они включаются в производственный цикл в виде поправочного коэффициента.
|
Рассмотрим несколько моделей для определения времени производственного цикла. Для этого охарактеризуем три основных вида организации производственных процессов во времени [4]:
1. последовательный, характерный для единичной или партионной обработки или сборки изделий;
2. параллельный, применяемый в условиях поточной обработки или сборки;
3. параллельно-последовательный, используемый в условиях прямоточной обработки или сборки изделий.
При последовательном виде движения производственный заказ – одна деталь (партия деталей) – в процессе их производства переходит на каждую последующую операцию процесса только после окончания обработки всех деталей этой партии на предыдущей операции. В таком случае с операции на операцию транспортируется вся партия деталей одновременно. При этом каждая деталь партии пролеживает на каждой операции сначала в ожидании своей очереди обработки, а затем в ожидании окончания обработки всех деталей партии по этой операции. При этом партией деталей называется количество одноименных деталей, одновременно запускаемых в производство (обрабатываемых с одной наладки оборудования).
На рисунке 2.5 представлен график последовательного движения предметов труда по операциям.
Время обработки при последовательном виде движения предметов труда tпос прямо пропорционально числу деталей в партии и времени обработки одной детали по всем операциям, т. е.
,где (1)
– время обработки партии деталей при последовательном виде движения;
– время обработки одной детали по всем операциям в мин;
n – число деталей в партии.
Операции | nt1 | nt2 | nt3 | nt4 | |||||
tпос |
Рисунок 2.5–График последовательного движения предметов труда
При параллельном виде движения обработка каждой детали в партии на каждой последующей операции начинается немедленно после окончания предыдущей операции, независимо от того что обработка других деталей в партии на данной операции еще не окончена.
Время обработки партии деталей при параллельном виде движения Тпар может быть определено по следующей формуле (2):
,где (2)
– время обработки партии деталей при параллельном виде движения;
– время обработки одной детали по всем операциям в мин;
– число деталей в партии;
– такт выпуска, соответствующий в данном случае наиболее продолжительной операции, мин.
|
Однако при параллельном виде движения, в процессе обработки партии деталей на некоторых рабочих местах могут возникать простои людей и оборудования (рисунок 2.6), продолжительность которых определяется разностью между тактом и длительностями отдельных операций процесса. Такие простои неизбежны в том случае, если операции, следующие одна за другой, не синхронизированы (не выровнены по их длительности), как это обычно делается на поточных линиях. Поэтому практическое применение параллельного вида движения предметов труда оказывается, безусловно, целесообразным и экономически выгодным при поточной организации производственного процесса.
Операции | t1 | t2 t | t3 | t4 | (n-1)r | r | r | ||
![]() |
Рисунок 2.6 – График параллельного движения предметов труда
Необходимость выравнивания (синхронизации) длительности отдельных операций существенно ограничивает возможность широкого применения параллельного вида движения, что способствует применению третьего – параллельно-последовательного вида движения предметов труда.
Параллельно-последовательный вид движения предметов труда характеризуется тем, что процесс обработки деталей данной партии на каждой последующей операции начинается раньше, чем полностью заканчивается обработка всей партии деталей на каждой предыдущей операции. Детали передаются с одной операции на другую частями, транспортными (передаточными) партиями. Накопление некоторого количества деталей на предыдущих операциях перед началом обработки партии на последующих операциях (производственный задел) позволяет избежать возникновения простоев.
Параллельно-последовательный вид движения предметов труда позволяет значительно уменьшить продолжительность производственного процесса обработки (сборки) по сравнению с последовательным видом движения.
Применение параллельно-последовательного вида движения экономически целесообразно в случаях изготовления трудоемких деталей, когда длительности операций процесса значительно колеблются, а также в случаях изготовления малотрудоемких деталей крупными партиями (например, мелких унифицированных деталей и т. д.).
При параллельно-последовательном виде движения предметов труда могут быть три случая сочетания длительности операций:
1. Предыдущая и последующая операции имеют одинаковую длительность,
();
2. Длительность предыдущей операции больше длительности последующей,
т. е.
>
;
3. Длительность предыдущей операции меньше длительности последующей
, т. е.
<
.
В первом случае передача деталей с операции на операцию может быть организована поштучно; из соображения удобства транспортировки может быть применена одновременная передача нескольких деталей (передаточной партией).
Во втором случае последующая, менее продолжительная операция может быть начата только после окончания обработки всех деталей на предыдущей операции, входящих в первую передаточную партию. На рисунке 2.7 это имеет место при переходе от первой операции ко второй.
В третьем случае (на рисунке 2.4 – переход от 3 к 4-й операции) нет необходимости накапливать детали на предыдущей операции. Достаточно передать одну деталь на последующую операцию и начать ее обработку без всякого опасения возможности возникновения простоя. В этом, как и в первом случае, передаточная партия устанавливается только из транспортных соображений.
Момент начала работы на каждой следующей операции (рабочем месте) определяется по графику или путем расчета минимальных смещений с.
Минимальное смещение с определяется как разность между длительностями предыдущей большей t
и последующей меньшей операциями t
, см. (3):
,где (3)
– минимальное смещение;
,
– длительность соответствующих операции;
– число деталей в партии;
– величина передаточной (транспортной) партии, которая для второго случая сочетания длительности операций определяется из соотношения ñ1/t1
( – минимальное смещение первой операции), во всех остальных случаях – из условий удобства транспортировки.
Минимальное расчетное смещение включается в общую продолжительность производственного процесса Т при сочетании длительности операции, относящемся ко второму случаю. В первом и третьем случаях минимальное смещение устанавливается равным времени, необходимому для формирования передаточной партии.
Операции | nt1 с1 | n т рt1 с2 с3 |
![]() |
![]() |
Рисунок 2.7–График параллельного движения предметов труда
Определяя общую продолжительность производственного процесса при параллельно-последовательном виде движения предметов труда, следует учитывать расчетную величину смещения Ес (формула 4):
, где (4)
– время обработки партии деталей при параллельно-последовательном виде движения;
– длительность последней (конечной) операции в данном производственном
процессе;
- расчетная величина смещения;
– число деталей в партии.
|
|
Своеобразие русской архитектуры: Основной материал – дерево – быстрота постройки, но недолговечность и необходимость деления...
Семя – орган полового размножения и расселения растений: наружи у семян имеется плотный покров – кожура...
Типы сооружений для обработки осадков: Септиками называются сооружения, в которых одновременно происходят осветление сточной жидкости...
Археология об основании Рима: Новые раскопки проясняют и такой острый дискуссионный вопрос, как дата самого возникновения Рима...
© cyberpedia.su 2017-2024 - Не является автором материалов. Исключительное право сохранено за автором текста.
Если вы не хотите, чтобы данный материал был у нас на сайте, перейдите по ссылке: Нарушение авторских прав. Мы поможем в написании вашей работы!