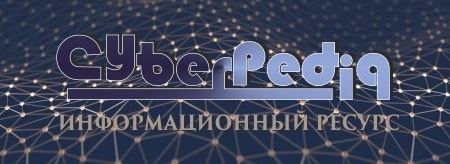
Своеобразие русской архитектуры: Основной материал – дерево – быстрота постройки, но недолговечность и необходимость деления...
Поперечные профили набережных и береговой полосы: На городских территориях берегоукрепление проектируют с учетом технических и экономических требований, но особое значение придают эстетическим...
Топ:
История развития методов оптимизации: теорема Куна-Таккера, метод Лагранжа, роль выпуклости в оптимизации...
Основы обеспечения единства измерений: Обеспечение единства измерений - деятельность метрологических служб, направленная на достижение...
Устройство и оснащение процедурного кабинета: Решающая роль в обеспечении правильного лечения пациентов отводится процедурной медсестре...
Интересное:
Отражение на счетах бухгалтерского учета процесса приобретения: Процесс заготовления представляет систему экономических событий, включающих приобретение организацией у поставщиков сырья...
Распространение рака на другие отдаленные от желудка органы: Характерных симптомов рака желудка не существует. Выраженные симптомы появляются, когда опухоль...
Аура как энергетическое поле: многослойную ауру человека можно представить себе подобным...
Дисциплины:
![]() |
![]() |
5.00
из
|
Заказать работу |
|
|
Классификация металлорежущих станков и условные обозначения
Металлорежущий станок — машина для размерной обработки заготовок в основном путем снятия стружки. В Советском Союзе выпускают большое количество металлорежущих станков, различных по назначению, технологическим возможностям и размерам. Совокупность всех признаков (типов и размеров) выпускаемых станков и станков, намечаемых к выпуску в течение определенного периода времени, например за пятилетие, называют типажом.
Обозначения станков. Модель станка обозначают тремя или четырьмя (иногда с добавлением букв) цифрами. Первая цифра указывает группу станка, вторая — тип, последние одна или две цифры указывают на один из характерных его размеров. Буква
внутри цифр указывает на модернизацию станка, а буква после всех цифр —модификацию (видоизменение) базовой модели станка или технологические особенности его (например, повышенной точности, причем при нормальной точности букву в шифре
не проставляют). Например, станок 2Н135: цифра 2 означает, что станок относится ко второй группе — сверлильный; Н — модернизированный; цифра 1 указывает на принадлежность станка к первому типу — вертикально-сверлильный; последние две
цифры означают максимальный диаметр сверления (35 мм).
Буква Ф в шифре говорит о том, что станок имеет числовое программное управление (ЧПУ), а цифра за ней указывает на то, какая система ЧПУ применена. Модель станка 16К20ФЗ расшифровывается так: станок токарно-винторезный с высотой центров над станиной 200 мм; ФЗ означает, что станок оснащен контурной системой числового программного управления.
Модели специализированных и специальных станков обозначают одной или двумя буквами, к которым добавляют также цифры, указывающие порядковый номер модели станка. Например, Московский станкостроительный завод «Красный пролетарий» имеет индекс МК, Горьковский завод фрезерных станков — ГФ и т. д.
|
По степени специализации различают следующие станки.
I. Универсальные, выполняющие различные переходы при обработке разнообразных деталей. Станки, используемые для очень большого диапазона работ, называют широкоуниверсальными. К универсальным станкам относят, например, токарно-винторезный станок 16К20.
2. Специализированные, обрабатывающие детали, сходные по конфигурации, но имеющие различные размеры, например ступенчатые валики, кольца подшипников качения и т. п. К таким станкам относят, в частности, многорезцовые токарные, токарные
для обработки коленчатых валов.
3. Специальные, предназначенные для обработки одной определенной детали или деталей только одного типоразмера, например лопаток газовых турбин.
По степени точности различают станки пяти классов. Класс Н — станки нормальной точности; к нему относят большинство универсальных станков. Класс П — станки повышенной точности, изготовляемые на базе станков нормальной точности, но при
повышенных требованиях к точности изготовления ответственных деталей станка и качеству сборки и регулированию. Класс В — станки высокой точности, достигаемой за счет специальной конструкции отдельных сборочных единиц, высоких требований к точности изготовления деталей, к качеству сборки и регулированию сборочных единиц и станка в целом. Класс А — станки особо высокой точности; при их изготовлении предъявляют еще более жесткие требования, чем при изготовлении станков класса В.
Класс С — станки особо точные или мастер-станки, предназначенные для изготовления деталей, определяющих точность станков классов А и В.
По массе различают станки легкие (до I т), средние (до 10 т) и тяжелые (свыше 10 т). Тяжелые, в свою очередь, делят на крупные (10—30 т). собственно тяжелые (30—100 т) и особо тяжелые, уникальные (более 100 т).
|
По виду обрабатываемой заготовки станки делятся на девять групп.
1 Токарные 2 Сверлильные и расточные 3 Шлифовальные, заточные, доводочные, полировальные, 4 Комбинированные 5 Зубо- и резьбообрабатывающие 6 Фрезерные 7 Строгальные, долбежные, протяжные 8 Разрезные (отрезные) 9 Разные.
Каждая группа делится на девять подгрупп (тип станков), которые указывают на степень автоматизации, компоновку, вид применяемого инструмента и т. д.
Базовые детали станков
Базовые детали металлорежущих станков служат для создания требуемого пространственного размещения узлов, несущих инструмент и обрабатываемую деталь, и обеспечивают точность, взаимного расположения под нагрузкой. Совокупность базовых деталей между инструментом и заготовкой образует несущую систему станка. К базовым деталям относят станины, основания, колонны, стойки, поперечины, ползуны, траверсы, столы, каретки, суппорты, планшайбы, корпуса шпиндельных бабок и т. п. (рис. 4.1).
Рис. 4.1 Базовые детали фрезерно-расточного станка
По форме они условно могут быть разделены на три группы: брусья – детали, у которых один габаритный размер больше двух других; пластины, у которых один размер значительно меньше двух других; коробки – габаритные размеры одного порядка.
Направляющие обеспечивают правильность траектории движения заготовки и (или) инструмента и точность перестановки узлов. Во многих случаях направляющие выполняют как одно целое с базовыми деталями. Базовые детали и направляющие должны иметь:
– первоначальную точность изготовления всех ответственных поверхностей для обеспечения требуемой геометрической точности высокую жесткость, определяемую контактными деформациями подвижных и неподвижных стыков, местными деформациями и деформациями самих базовых деталей;
– высокие демпфирующие свойства, т. е. способность гасить колебания между инструментом и заготовкой от действия различных источников вибраций;
– долговечность, которая выражается в стабильности формы базовых деталей и способности направляющих сохранять первоначальную точность в течение заданного срока эксплуатации.
Кроме того, базовые детали должны иметь малые температурные деформации, из-за которых могут произойти относительные смещения между инструментом и заготовкой, а направляющие должны обладать малой величиной и постоянством сил трения, так как от этого зависит точность позиционирования узлов станка. Перечисленные основные требования, предъявляемые к базовым деталям и направляющим станков, могут быть удовлетворены при правильном выборе материала и конструктивными принципами, которые являются общими, несмотря на многообразие форм.
|
Конструирование базовых деталей – это поиск компромиссного решения между противоречивыми требованиями: создание конструкций жестких, но имеющих малую массу; простых по конфигурации, но обеспечивающих высокую точность; дающих экономию металла, но учитывающих возможности литейной технологии при проектировании литых конструкций и возможности технологии сварных конструкций. Конструирование базовых деталей во многом опирается на богатый опыт, накопленный за долгие годы, как в нашей стране, так и за рубежом.
Направляющие станков
Направляющие — наиболее ответственная часть станины, служащая для перемещения сборочных единиц станка и находящихся на них инструментов и заготовок. В станках применяют направляющие скольжения и качения для прямолинейного и кругового перемещения.
Направляющие скольжения бывают закрытыми, когда подвижная сборочная единица станка имеет одну степень свободы, и открытыми. Основные формы направляющих скольжения показаны на рис.
В станках очень часто используют комбинированные направляющие, одна из которых плоская, а вторая — призматическая, V-образная или в виде половины ласточкина хвоста. Направляющие, выполненные в виде планок, прикрепляемых винтами к литой чугунной станине или привариваемых к стальной сварной станине, называют накладными.
Направляющие, предусматривающие подвод масла к сопряженным поверхностям под давлением и обеспечивающие создание масляной подушки по всей площади контакта, носят название гидростатических. Иногда в станках применяют аэростатические
направляющие, предусматривающие создание воздушной подушки в зазоре между сопряженными поверхностями направляющих.
|
В станках все шире применяют направляющие качения, которые подобно направляющим скольжения могут быть открытыми и закрытыми. Схемы наиболее распространенных форм направляющих качения приведены в табл.
Фрикционная передача
При фрикционной передаче вращение от одного колеса к другому передается при помощи силы трения. Оба колеса прижимаются друг к другу с некоторой силой и вследствие возникающего между ними трения вращают одно другое. Недостаток фрикционной передачи: большая сила, давящая на колеса, вызывающая дополнительное трение, а следовательно, требующая и дополнительную силу для вращения. Кроме того, колеса при вращении, как бы они ни были прижаты друг к другу дают проскальзывание. Поэтому там, где требуется точное соотношение чисел оборотов колес, фрикционная передача себя не оправдывает.
Достоинства фрикционной передачи:
Недостатки фрикционной передачи:
Применение фрикционной передачи:
В машиностроении чаще всего применяют бесступенчатые фрикционные передачи для бесступенчатого регулирования скорости.
а - лобовая передача, б - угловая передача, в - цилиндрическая передача
В самодельных устройствах фрикционная передача может быть широко использована. Особенно приемлемы передачи цилиндрическая и лобовая. Колеса для передач можно делать деревянные. Для лучшего сцепления, рабочие поверхности колес следует "обшить" слоем мягкой резины толщиной в 2-3 мм. Резину можно или прибить мелкими гвоздиками, или приклеить клеем.
Зубчатая передача
В зубчатых передачах вращение от одного колеса к другому передается при помощи зубьев. Зубчатые колеса вращаются намного легче фрикционных. Объясняется это тем, что здесь нажима колеса на колесо совсем не требуется. Для правильного зацепления и легкой работы колес профиль зубца делают по определенной кривой, называемой эвольвентой.
Диаметр начальной окружности является основным расчетным диаметром зубчатых колес. Расстояние, взятое по начальной окружности между осями соседних зубцов, между осями впадин или от начала одного зубца до начала другого, называется шагом зацепления. Разумеется, что шаги у зацепляющихся шестерен должны быть равны.
Передаточное число в зубчатых колесах может выражаться и через число зубцов:
|
i = z2/z1
где z2 - число зубцов ведомого колеса, z1 - число зубцов ведущего колеса.
Есть в шестернях еще одна очень важная величина, которую именуют модулем. Модулем называют отношение шага к величине π (3,14) или отношение диаметра начальной окружности к числу зубцов на колесе. Модуль, шаг и другие величины шестерен измеряются в миллиметрах. Колеса с одинаковым модулем, с любым количеством зубцов дают нормальное зацепление. Модули зубчатых колес берутся не произвольно. Величины их стандартизированы.
Передаточное число шестеренчатой передачи берется обычно в определенных пределах. Оно колеблется до 1:10. При увеличении передаточного числа одна из шестерен делается очень большой, механизм получается громоздким. Но иногда бывает нужно получить очень большое передаточное число, которое одной парой шестерен создать трудно. В этом случае ставится несколько пар и передаточное число распределяется между ними.
Иногда в передачах малую шестерню требуется сделать особенно уменьшенной, например в часах, в приборах. В этих случаях шестерню с валом делают из одного куска. Такую цельную шестерню принято называть трибком (трибок).
Часто в машинах применяют цилиндрические шестерни, у которых зубец идет не по оси вращения, а под некоторым углом (г). Такие шестерни работают на больших скоростях очень плавно, и зубцы их выносят большую нагрузку. Колеса с косыми зубцами носят название косозубых цилиндрических колес. Еще более плавный ход при большой прочности зубцов дают так называемые шевронные колеса (д). Зубцы у этих колес скошены в обе стороны, расположены "в елочку".
Шестеренчатая передача применяется не только с параллельными валами, когда используются так называемые цилиндрические шестерни, но и тогда, когда валы идут под любым углом. Такая передача под углом называется конической зубчатой передачей, а шестерни - коническими (ж).
Конические шестерни, так же как и цилиндрические, бывают со спиральным косым зубцом (з). Такие шестерни обычно применяются в автомобилях (для плавности работы). В зубчатых передачах можно применить шестерни с рейкой. Для периодического вращения может применяться шестеренчатая пара, у которой ведущая шестерня имеет неполное число зубцов.
Ведущие шестерни встречаются и с одним зубцом. Такие передачи очень часто применялись в счетных механизмах. Ведущая шестерня имеет один зубец, а ведомая - десять, и, таким образом, за один оборот ведущей шестерни ведомая повернется всего на одну десятую оборота. Чтобы повернуть ведомую шестерню на один оборот, ведущая должна сделать десять оборотов.
а - шестерня с одним зубом, б - мальтийский крест
Достоинства зубчатой передачи:
Недостатки зубчатой передачи:
Применение зубчатой передачи:
Наиболее распространённый вид механических передач. Их применяют для передачи мощностей - от ничтожно малых до десятков тысяч кВт.
К разобранному типу передач можно отнести и так называемое мальтийское зацепление, или мальтийский крест (б). Механизм мальтийского креста применяется для периодического вращения.
Ременная передача
Ременная передача, как и шестеренчатая, встречается очень часто. Ремень, натянутый на шкивы, охватывает какую-то их часть. Эта облегающая часть (дуга) носит, название угла обхвата. Чем больше будет угол обхвата, тем лучше образуется сцепление, лучше и надежнее будет вращение шкивов. При малом угле обхвата может получиться так, что ремень на малом шкиве станет проскальзывать, вращение будет передаваться плохо или его совсем не будет. Угол обхвата зависит от соотношения размеров шкивов и их расстояния друг от друга. На рисунках (а, б) показано, как меняются углы обхвата. Когда требуется увеличить угол обхвата, у передачи ставят нажимной шкив-ролик (в).
В зависимости от расположения валов и ремня ременная передача бывает разных видов.
Открытая передача (г). Оба шкива при такой передаче вращаются в одну сторону.
Перекрестная передача (д). Такую передачу применяют, когда требуется изменить вращение ведомого шкива. Шкивы вращаются навстречу друг другу.
Полуперекрестная передача (е) применяется, когда валы лежат не параллельно, а под углом.
Угловая передача (ж) образуется, когда валы идут под углом, но лежат как бы в одной плоскости. При этой передаче для получения надлежащего направления ремня обязательно устанавливают ролики.
Спаренная передача (з). При этой передаче с одного ведущего шкива могут идти ремни на несколько ведомых шкивов.
Кроме перечисленных передач, бывает еще и ступенчатая передача (и). Она применяется тогда, когда требуется изменять число оборотов ведомого вала. Оба шкива в этой передаче делаются ступенчатыми. Переставляя ремень на ту или иную пару ступеней, меняют число оборотов ведомого вала. При этом длина ремня остается неизменной.
По своему профилю ремни бывают плоские, круглые и трапецеидальные (к, л, м).
Передаточное число ременных передач берется в пределах 1:4, 1:5 и только в исключительном случае - до 1:8.
При расчете ременной передачи учитывается скольжение ремня по шкивам. Это проскальзывание выражается в пределах 2-3%. Чтобы получить нужные обороты, диаметр ведомого шкива уменьшают в этих же пределах.
Шкивы можно cделать из фанеры или легких металлов.
Достоинства ременной передачи:
Недостатки ременной передачи:
Применение ременной передачи:
Используется очень часто, от бытовой электроники до промышленных механизмов мощностью до 50 кВт.
Червячная передача
Червячная передача служит для получения вращения между валами, пересекающимися в одной плоскости. Передача состоит из винта (червяка) и винтового колеса, которые находятся в зацеплении. При вращении червяка витки ведут зубцы колеса и заставляют его вращаться. Обычно вращение от червяка передается колесу. Обратная передача почти не встречается из-за самоторможения.
Червячная передача применяется чаще всего при больших передаточных числах в пределах от 5 до 300. Благодаря большому передаточному числу червячная передача широко применяется в качестве механизма для снижения числа оборотов - редуктора.
Обычно червяк соединяется при помощи муфты с электромотором, а вал червячного колеса соединяется с машинами (станком, лебедкой, транспортером и пр.), которым он и передает необходимое вращение. Конструктивно червячный редуктор оформляют в самостоятельный механизм, помещенный в закрытый корпус.
Передаточное число червячной передачи (i), зависит от числа заходов червяка и количества зубцов на колесе. Его можно легко вычислить по формуле:
i = Z/K
где Z - число зубцов винтового колеса, а K - число заходов червяка. Решим пример: мотор совершает n1 = 1500 об/мин, на валу червячной шестерни нужно получить n2 = 50 об/мин. Червяк двухзаходный, то есть K = 2. Необходимо определить передаточное число и количество зубцов на винтовой шестерне. Передаточное число определится из формулы:
i = n1/n2 = 1500/50 = 30
Число зубцов на шестерне Z = i·K = 30·2 = 60 зубцов.
Редукторы можно сделать по-разному. У одних червяк делается из обыкновенного крепежного винта, у других он изготовляется навивкой на стержень в виде пружины проволоки или узкой медной полоски (на ребро). Для прочности витки к стержню следует припаивать. Червячные шестерни подбирают от ненужного часового механизма. Но их можно сделать и самим: нарезать напильником из латунного или дюралевого диска.
При изготовлении редукторов нужно следить за тем, чтобы винт и шестерня при вращении не имели бы осевого смещения. В быстроходных редукторах его валы следует устанавливать на подшипниках.
Достоинства червячной передачи:
Недостатки червячной передачи:
Применение червячной передачи:
Преимущественно используется, когда требуется большое передаточное число.
Цепная передача
Цепная передача по сравнению с ременной удобна тем, что не дает проскальзывания и позволяет соблюдать правильность передаточного числа. Цепная передача осуществляется только при параллельных валах.
а - пластинчатая роликовая цепь, б - бесшумная цепь
Основной величиной цепной передачи является шаг. Шагом считается расстояние между осями роликов у цепи или расстояние между зубцами звездочки.
Кроме роликовых цепей, в машинах широко применяются еще зубчатые, так называемые бесшумные цепи. Каждое звено их соединено из нескольких зубчатых пластин в ряд. Ширина этой цепи намного больше, чем роликовая. Звездочка такой передачи похожа на шестерню. Зубчатые цепи могут работать на больших скоростях.
Допустимое передаточное число цепных передач может быть до 1:15. Самое малое число зубцов у звездочек берут: у роликовых цепей - 9, а у зубчатых - 13-15. Расстояние между осями звездочек принимают не менее полуторного диаметра большой звездочки.
Цепь надевается на звездочки не туго, как ремни, а с некоторым провисанием. Для регулирования натяжения применяется натяжной ролик. Число оборотов ведомой звездочки зависит от соотношения зубцов на обеих звездочках.
Достоинства цепной передачи:
Недостатки цепной передачи:
Применение цепной передачи:
При межосевых расстояниях, при которых зубчатые передачи требуют промежуточных ступеней или паразитных зубчатых колес, не вызываемых необходимостью получения нужного передаточного отношения; при необходимости работы без проскальзывания (препятствующего применению клиноременных передач).
Храповые механизмы
Кроме непрерывного вращательного движения, в машинах очень часто применяется прерывистое вращательное движение. Такое движение осуществляется при помощи так называемого храпового механизма. Основными частями храпового механизма являются: храповик (диск с зубцами), рычаг и собачка. Зубцы храповика имеют особую форму. Одна сторона у них сделана пологой, а другая отвесной или несколько поднутренной. Храповик насажен на вал неподвижно. Рычаг же, сидящий рядом с храповиком, может свободно качаться. На рычаге имеется собачка, которая одним концом лежит на храповике. С помощью шатуна или тяги от того или иного ведущего механизма рычаг приходит в качательное движение. При отклонении рычага влево собачка скользит свободно по пологому склону зубцов, не поворачивая храповик. При отходе вправо собачка упирается в уступ зубца и поворачивает храповик на некоторый угол. Так, непрерывно качаясь в ту и другую сторону, рычаг с собачкой приводит храповик с валом в периодическое вращательное движение. Для надежного прилегания собачки к храповику собачка снабжается нажимной пружиной.
Но чаще бывает другое назначение храпового механизма - предохранения вала с храповиком от проворачивания. Так, у лебедки при подъеме груза храповик с собачкой не дают барабану провертываться обратно.
Иногда нужно получить вращение храповика не только в одну сторону, но и в другую. В этом случае зубцы у храповика делают прямоугольными, а собачку - перекидной (б). Перекинув собачку вправо или влево, можно изменить и вращение храповика.
Число зубцов на храповике зависит от требуемого угла поворота. На какую часть окружности поворачивается храповик, столько делают и зубцов. Например, если на 60° - одну шестую долю окружности, то берут 6 зубцов; на 30° - одну двенадцатую долю - делают 12 зубцов и т.д. Меньше шести зубцов на храповике обычно не бывает.
Храповик должен быть небольшим. Большой храповик потребует увеличения размаха рычага и большого хода кривошипа, качающего рычаг. Высоту зубца храповика следует брать в пределах 0,35-0,4 от шага. Профиль зубца делают остроугольным, пологую сторону зубца - прямой, но ее можно и очерчивать по радиусу. Рычагов лучше брать два, помещая их по обеим сторонам храповика. При двух рычагах собачка и поводок от кривошипа встанут между ними и уменьшат перекос при работе. Нажим собачки можно осуществлять не только пружиной, но и резинкой. Конец собачки следует хорошо скашивать, чтобы она надежнее упиралась в зубец.
Подшипники качения.
Для шпинделей станков практически применяются все основные типы подшипников качения: шариковые радиальные и радиально-упорные, роликовые с коническими и цилиндрическими роликами, а также специальные конструкции. Последние отличаются от обычных не только повышенной точностью, грузоподъемностью и быстроходностью, но и конструктивными особенностями. К таким подшипникам относятся двухрядный подшипник с цилиндрическими роликами. Двойной ряд точных роликов и их шахматное расположение повышает грузоподъемность подшипника. Точность вращения шпинделей в таких подшипниках может быть обеспечена в пределах нескольких микрометров.
При проектировании подшипниковых узлов необходимо обращать внимание на уплотнения подшипников, защищающие их от загрязнения и предотвращающие вытекание смазки.
Подшипники качения теряют свою работоспособность в основном в результате усталости поверхностных слоев дорожек и тел качения.
Шарикоподшипники применяют для быстроходных малонагруженных опор (шпиндели внутришлифовальных станков, небольших токарных станков и автоматов, сверлильных).
При повышенных нагрузках и прецизионности целесообразно применять подшипники с цилиндрическими роликами (шпиндели токарных и револьверных станков и автоматов, быстроходных фрезерных станков, тяжелых шлифовальных и резьбошлифовальных).
При повышенных нагрузках на шпиндель и средних частотах вращения применяют конические роликовые подшипники (шпиндели многорезцовых, фрезерных и других станков).
Подшипники скольжения применяют в шпиндельных узлах тех станков, где подшипники качения не могут обеспечить требуемой точности и долговечности работы. В качестве таких опор используют гидродинамические, гидростатические подшипники, а также подшипники с газовой смазкой.
В гидростатических подшипниках под давлением подается жидкость, образующая между сопрягаемыми поверхностями равномерную масляную подушку. В аэростатических подшипниках подается сжатый воздух, образующий воздушную подушку.
Гидродинамические подшипники применяют в станках с высокими постоянствами или мало изменяющимися скоростями вращения шпинделей при незначительных нагрузках (станки шлифовальной группы).
Гидростатические опоры обеспечивают высокую точность вращения, обладают высокой демпфирующей способностью, что значительно повышает виброустойчивость шпиндельного узла, имеют практически неограниченную долговечность, высокую нагрузочную способность при любой частоте вращения шпинделя.
Недостаток: Эти опоры требуют сложной системы питания и сбора масла.
В станкостроении применяют аэростатические подшипники, по принципу действия подобные гидростатическим. Только в зазор между сопрягаемыми поверхностями подается сжатый воздух. Вследствие этого нагрузочная способность их невелика. Однако малая вязкость воздуха позволяет существенно снизить потери на трение. Поэтому их и применяют в небольших прецизионных станках при больших окружных скоростях вращения шпинделя.
Смазывание во многом определяет надежность работы шпиндельного узла. Для подшипников качения применяют жидкий либо твердый смазочный материал.
Отличие ШУ с гидростатическими опорами — высокая точность вращения; они могут быть выполнены быстроходными при сравнительно высокой жесткости. Кроме этого, гидростатические опоры характеризуются отсутствием износа, способностью выдерживать высокие нагрузки, демпфирующей способностью и отсутствием металлического контакта при пуске шпинделя. Поэтому такие ШУ нашли применение прежде всего в тяжелых станках.
Гидростатические опоры обеспечивают высокую точность вращения, обладают высокой демпфирующей способностью, что значительно повышает виброустойчивость шпиндельного узла, имеют практически неограниченную долговечность, высокую нагрузочную способность при любой частоте вращения шпинделя. Гидростатические опоры могут быть использованы в качестве датчиков силы в системах адаптивного управления, в качестве приводов микроперемещений.
Принцип действия гидростатического подшипника основан на том, что при прокачивании масла под давлением от внешнего источника через зазоры (щели) между сопряженными поверхностями в зазоре, образуется несущий масляный слой, исключающий непосредственный контакт поверхностей даже при невращающемся шпинделе.
Рис. 4.24 Гидростатические осевые а) и радиальные б) опоры.
В радиальных подшипниках равномерно по окружности делают полости-карманы, куда через дроссели подается под давлением масло от источника питания (насоса). При приложении внешней нагрузки вал занимает эксцентричное положение, зазоры h в подшипнике перераспределяются, что приводит к увеличению давления р масла в одних карманах и уменьшению в противоположных. Уравнивания давлений в карманах не происходит вследствие наличия дросселей на входе в каждый карман. Разность давлений создает результирующую силу Fc,воспринимающую внешнюю нагрузку. Отвод смазочного материала производится через торцы подшипника, иногда и через дренажные канавки, выполненные на перемычках между карманами.
Недостатки гидростатических опор: необходимость применения циркуляционной смазки, тщательная фильтрация масла, периодический контроль состояния ШУ, охлаждение рабочей жидкости вследствие значительного тепловыделения (особенно в быстроходных ШУ), значительные потери мощности при вращении шпинделя на холостом ходу.
Классификация муфт.
В зависимости от конструкции мyфты различаются по функциональному назначению и принципу действу. Различают следующие виды мyфт: механические, гидравлические, электрические и др. Широко применяемые мyфты стандартизованы.
Основная паспортная характеристика мyфты - значение вращающего момента, на передачу которого она рассчитана.
Кулачковые муфты
Кулачковые муфты состоят из двух частей — подвижной и неподвижной. Подвижная часть может перемещаться вдоль одного вала, неподвижная — жестко закреплена на другом валу. На их торцах имеются кулачки или зубья, посредством которых осуществляется сцепление муфты. На фиг. 88, а показана схема кулачковой муфты и приведены наиболее распространенные профили зубьев (кулачков).
Системы управления станками
Под управлением станком понимают совокупность воздействий на его механизмы, обеспечивающих выполнение технологического цикла обработки, а под системой управления — устройство или совокупность устройств, реализующих эти воздействия.
Цикл работы станка — это совокупность всех движений, необходимых для обработки заготовок и выполняемых в определенной последовательности. Циклы, осуществляемые при работе станочного оборудования, делят на две группы. Первую группу образуют циклы, которые остаются неизменными и повторяются многократно в процессе эксплуатации оборудования, например циклы работы автоматических линий и агрегатных станков.
Ко второй группе относятся циклы, совершаемые однократно в определенные моменты. Эти циклы инициируются специальной командой. Примерами таких циклов являются циклы движений вспомогательных механизмов в станках: поиск и смена инструмента, зажим и освобождение подвижных узлов, загрузка и зажим заготовок, выгрузка обработанных деталей и т.д.
Управление станком может быть ручным или автоматическим. Примером системы ручного управления является много-рукояточное устройство, в котором для перемещения каждого блока зубчатых колес предусмотрена рукоятка. Ручное управление может быть селективным (избирательным), преселективным (с предварительным набором скоростей) и дистанционным (кнопочным).
Автоматическое управление подразделяется на кулачковое; с помощью регулируемых упоров; программное и адаптивное. По виду различают цикловое и числовое программное управление. Цикловым программным управлением (ЦПУ) называют управление, при котором полностью или частично программируется цикл работы станка, режимы обработки и смена инструмента, а размерная информация (перемещения рабочих органов станка) задается с помощью путевых упоров, устанавливаемых на специальных линейках или барабанах.
Общие сведения о конусах
Коническая поверхность характеризуется следующими параметрами (рис. 4.31): меньшим d и большим D диаметрами и расстоянием l между плоскостями, в которых расположены окружности диаметрами D и d. Угол а называется углом наклона конуса, а угол 2α — углом конуса.
Отношение K= (D - d)/l называется конусностью и обычно обозначается со знаком деления (например, 1:20 или 1:50), а в некоторых случаях — десятичной дробью (например, 0,05 или 0,02).
Отношение Y= (D - d)/(2l) = tgα называется уклоном.
классификация металлорежущих станков и условные обозначения
Металлорежущий станок — машина для размерной обработки заготовок в основном путем снятия стружки. В Советском Союзе выпускают большое количество металлорежущих станков, различных по назначению, технологическим возможностям и размерам. Совокупность всех признаков (типов и размеров) выпускаемых станков и станков, намечаемых к выпуску в течение определенного периода времени, например за пятилетие, называют типажом.
Обозначения станков. Модель станка обозначают тремя или четырьмя (иногда с добавлением букв) цифрами. Первая цифра указывает группу станка, вторая — тип, последние одна или две цифры указывают на один из характерных его размеров. Буква
внутри цифр указывает на модернизацию станка, а буква после всех цифр —модификацию (видоизменение) базовой модели станка или технологические особенности его (например, повышенной точности, причем при нормальной точности букву в шифре
не проставляют). Например, станок 2Н135: цифра 2 означает, что станок относится ко второй группе — сверлильный; Н — модернизированный; цифра 1 указывает на принадлежность станка к первому типу — вертикально-сверлильный; последние две
цифры означают максимальный диаметр сверления (35 мм).
Буква Ф в шифре говорит о том, что станок имеет числовое программное управление (ЧПУ), а цифра за ней указывает на то, какая система ЧПУ применена. Модель станка 16К20ФЗ расшифровывается так: станок токарно-винторезный с высотой центров над станиной 200 мм; ФЗ означает, что станок оснащен контурной системой числового программного управления.
Модели специализированных и специальных станков обозначают одной или двумя буквами, к которым добавляют также цифры, указывающие порядковый номер модели станка. Например, Москов
Адаптации растений и животных к жизни в горах: Большое значение для жизни организмов в горах имеют степень расчленения, крутизна и экспозиционные различия склонов...
Архитектура электронного правительства: Единая архитектура – это методологический подход при создании системы управления государства, который строится...
Таксономические единицы (категории) растений: Каждая система классификации состоит из определённых соподчиненных друг другу...
Папиллярные узоры пальцев рук - маркер спортивных способностей: дерматоглифические признаки формируются на 3-5 месяце беременности, не изменяются в течение жизни...
© cyberpedia.su 2017-2024 - Не является автором материалов. Исключительное право сохранено за автором текста.
Если вы не хотите, чтобы данный материал был у нас на сайте, перейдите по ссылке: Нарушение авторских прав. Мы поможем в написании вашей работы!