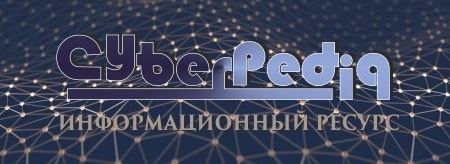
Наброски и зарисовки растений, плодов, цветов: Освоить конструктивное построение структуры дерева через зарисовки отдельных деревьев, группы деревьев...
Типы сооружений для обработки осадков: Септиками называются сооружения, в которых одновременно происходят осветление сточной жидкости...
Топ:
Характеристика АТП и сварочно-жестяницкого участка: Транспорт в настоящее время является одной из важнейших отраслей народного хозяйства...
Комплексной системы оценки состояния охраны труда на производственном объекте (КСОТ-П): Цели и задачи Комплексной системы оценки состояния охраны труда и определению факторов рисков по охране труда...
Техника безопасности при работе на пароконвектомате: К обслуживанию пароконвектомата допускаются лица, прошедшие технический минимум по эксплуатации оборудования...
Интересное:
Принципы управления денежными потоками: одним из методов контроля за состоянием денежной наличности является...
Отражение на счетах бухгалтерского учета процесса приобретения: Процесс заготовления представляет систему экономических событий, включающих приобретение организацией у поставщиков сырья...
Финансовый рынок и его значение в управлении денежными потоками на современном этапе: любому предприятию для расширения производства и увеличения прибыли нужны...
Дисциплины:
![]() |
![]() |
5.00
из
|
Заказать работу |
|
|
Изменение вылета стреловых кранов осуществляется наклоном стрелы или передвижением грузовой тележки по ее направляющим балкам. В первом случае общий расчет механизма изменения вылета состоит в определении усилия в канате полиспаста, выборе и расчете каната и барабана, выборе двигателя, редуктора, муфт и тормоза.
При изменении вылета передвижением грузовой тележки расчет аналогичен расчету механизма передвижения с учетом разности натяжений конечных ветвей грузового каната, сопротивления вследствие провисания хвостовой части тягового каната и центробежной силы инерции массы груза и тележки при повороте крана (для поворотных кранов).
При изменении вылета наклоном стрелы усилие в канате стрелового полиспаста у барабана
F ![]() ![]() | (2.68) |
где F — см. формулу (2.70); и
— кратность стрелового полиспаста; hо — КПД стрелового полиспаста и обводных блоков [см. (2.2)].
Момент статического сопротивления на валу двигателя при подъеме стрелы
Т с = F ![]() ![]() | (2.69) |
где — расчетный диаметр барабана лебедки изменения вылета [см. (2 33)]; и, hб, hпр — см. пояснения к формуле (1.30).
Статическая мощность двигателя определяется по формуле (133).
Усилие в стреловом полиспасте (Н) (рис. 2.13)
F ![]() ![]() | (2.70) |
где Q — масса груза при номинальной грузоподъемности (см. параграф 1.1), кг; т с — масса стрелы, кг; — масса стрелового полиспаста, кг;
— длина горизонтальной проекции стрелы, м;
— кратность грузоподъемного полиспаста;
— КПД грузоподъемного полиспаста;
— ветровая нагрузка на груз (см. параграф 1.3), Н;
— ветровая нагрузка на стрелу, Н;
— центробежная сила от груза и грузового полиспаста, Н;
— центробежная сила стрелы, Н;
— центробежная сила от стрелового полиспаста (учитывается половина его массы), Н; d —угол наклона полиспаста стрелы от горизонтали (рис. 2.13); Н,
, d — длина плеч сил (рис. 2.13).
|
Знак плюс перед вторым слагаемым знаменателя принимается, когда стреловой полиспаст наклонен от головки стрелы вверх, знак минус — при обратном наклоне.
Рис 2.13. Схема для определения усилия в стреловом полиспасте
Для стрел с вылетом до 25 м у кранов с частотой вращения до 1 мин-1 центробежные силы могут не учитываться.
Максимальное усилие в стреловом полиспасте будет при наибольшем вылете стрелы. Расчетное усилие в стреловом полиспасте для определения необходимой мощности двигателя можно принимать равным полусумме усилий в полиспасте при крайних положениях стрелы.
Центробежная сила (Н) от массы груза
F ![]() ![]() | (2.71) |
где n пов — частота вращения поворотной части крана, мин-1; R — вылет стрелы, м.
Центробежная сила (Н) от массы стрелы
F ![]() ![]() | (2.72) |
где r, L, q — см/ рис. 2.13
Ордината центробежной силы F (рис. 2.13)
h ![]() ![]() | (2.73) |
Ход стрелового полиспаста (м)
DL = L max - L min, | (2.74) |
где L max, L min — длина стрелового полиспаста при наибольшем и наименьшем вылетах стрелы.
Длина каната, наматываемого на барабан стреловой лебедки,
l к = DL u ![]() | (2.75) |
Рис 2.14. Расчетная схема канатного механизма передвижения грузовой тележки
Средняя скорость навивки каната на барабан
u к = l к/ t, | (2.76) |
где t — заданное время наклона стрелы при переходе из одного крайнего положения в другое, с.
Момент статических сопротивлений на валу тормоза при торможении определяется по (2.37), в которой F б = F [см. (2.68)].
Далее расчет производится так же, как и для механизма подъема (см. параграф 2.1).
Коэффициент запаса торможения kT для механизма изменения вылета подъемом и опусканием стрелы принимают не менее 1,5.
При изменении вылета посредством перемещения грузовой тележки по направляющим балкам стрелы с помощью тягового каната (рис. 2.14) усилие в этом канате
F т = F пер + F ц + F н + F пр, | (2.77) |
где F пep — сопротивление передвижению тележки от трения, уклона пути и ветровой нагрузки [см. (2.39)], Н; F ц — центробежная сила инерции, создаваемая массой груза и тележки при повороте крана, Н:
|
F ц = ![]() | (2.78) |
Q — номинальная грузоподъемность (см. параграф 1.1), кг;
т т — масса тележки, кг; F н — разность натяжений ветвей грузового полиспаста, Н:
F н = F 1 – Fi = Qg ![]() | (2.79) |
F 1, Fi — натяжение первой и конечной ветвей каната грузового полиспаста (рис. 2.14); hбл —КПД канатного блока (см. табл. 2.1); z — количество ветвей каната в системе грузового полиспаста: z = и +2; и
— кратность грузового полиспаста; F пр — сопротивление от провисания хвостовой ветви тягового каната, Н:
F пр = q к g ![]() | (2.80) |
q к — погонная масса хвостового каната, кг/м; l — длина (наибольшая) хвостовой ветви тягового каната, м; h — провисание, допускаемое для хвостовой ветви тягового каната, м: h = (0,01...0,02) l.
Далее расчет привода лебедки механизма передвижения тележки производится так же, как и привода механизма передвижения мостового крана (см. параграф 2.2).
Примерная последовательность расчета механизма изменения вылета наклоном стрелы:
1) определяется усилие в стреловом полиспасте для крайних положений стрелы [см. (2.70)];
2) определяется максимальное и минимальное усилие в канате стрелового каната у барабана [см. (2 68)];
3) определяется среднее усилие в канате Fl cp, равное полусумме максимального и минимального усилий;
4) определяется средняя скорость навивки каната на барабан по (2.76);
5) определяется необходимая мощность двигателя согласно (2.42) при F пер u пер = F u к и h = hбhпр, где hб — КПД барабана (cм. табл. 1.18); hпр — КПД привода механизма. По табл. III.3 выбирается двигатель;
6) производится расчет каната на прочность по (2.6) и выбирается канат по табл. III.1.1...III.1.7;
7) пределяются диаметры барабана по (2.9) и (2.33);
8) определяется частота вращения барабана согласно (2.35) при u г u п = u к, где u к — см. (2.76);
9) определяется общее передаточное число привода по (2.36) и составляется кинематическая схема механизма;
10) определяется расчетная мощность редуктора по (1.101) или (1.102) и выбирается редуктор (см. параграф Ш.4);
11) определяются расчетные моменты соединительных муфт при максимальных нагрузках стрелового полиспаста согласно (1.30) при F = F
;
12) проверяется двигатель на время пуска по (1.71) при максимальном и минимальном усилии в канате. Полученное время должно соответствовать данным табл. 1.20;
|
13) определяется момент статического сопротивления на валу тормоза при торможении Т по (2.37), принимая F
= F
;
14) определяется тормозной момент, необходимый по правилам Госгортехнадзора, по (2.38) при Т = Т
и выбирается тормоз по табл. Ш.5.П... Ш.5.14;
15) определяется время торможения по (1.72) при максимальном силии в канате и проверяется его соответствие данным табл. 1.20;
16) проверяется правильность выбора двигателя по пусковому моменту при наибольшей нагрузке F (т.е. при крайнем нижнем положении стрелы) из условия Т max£ Т ср.п, где Т max — максимальный момент на валу двигателя согласно (2.69) при F
= F
, Т ср.п — среднепусковой момент двигателя [см. (1.89)]. Проверка двигателя на нагрев может не производиться, так как его мощность определена по средней нагрузке, которая при приближенных асчетах принимается как среднеквадратичная. Более подробно см. [12].
17) производится расчет на прочность отдельных элементов механизма (барабана, крепления концов каната и др.).
При изменении вылета посредством передвижения грузовой тележки последовательность расчета механизма передвижения тележки аналогична такому же расчету механизма передвижения крана (см. параграф 2.2). При этом усилие в канате лебедки определяется по (2.77).
РАСЧЕТ МЕХАНИЗМА ПОВОРОТА
Общий расчет механизма поворота. Он заключается в определении нагрузок на опоры поворотной части крана, в определении сопротивлений вращению, выборе двигателя, редуктора, муфт, тормоза и расчете конечного звена передачи — зубчатой, цевочной или канатной.
Момент сопротивления вращению поворотной части крана на валу двигателя в период пуска (разгона)
Т пуск = Т ин + Т с = Т ин + (Т укл+ Т в+ Т тр) ![]() | (2.81) |
где Т ин — момент сопротивления от сил инерции при пуске [см. (1.65)]; Т укл — момент статического сопротивления от веса крана и груза относительно оси вращения крана при нахождении крана на уклоне; Т в — момент статического сопротивления от ветравой нагрузки относительно оси вращения крана; Т тр — момент статического сопротивления от сил трения относительно оси вращения крана; Т с, и, h — [см. формулу (1.32)].
|
Наибольший момент сопротивления (Н·м) вращению от веса поворотной части крана и груза при нахождении крана на уклоне
Т укл = (т пов l пов+ QR) g sin a, | (2.82) |
где т пов — масса поворотной части крана, кг: т пов = т пл + т пв + т б+ т с (соответственно масса поворотной платформы, противовеса с противовесной стрелой, башни, стрелы); l пов — расстояние от оси вращения крана до центра тяжести поворотной части крана, м;
l пов = ![]() |
L пл, l пв, l б и l с — соответственно расстояния от оси вращения крана до центра тяжести соответственно платформы, противовеса, башни и стрелы, м; Q — масса груза при номинальной грузоподъемности (см. параграф 1.1), кг; R — вылет крана, м; a—угол наклона пути крана.
Наибольший момент сопротивления (Н·м) вращению поворотной части крана от ветровой нагрузки относительно оси вращения крана
Т в = ![]() | (2.83) |
где F , F
— ветровые нагрузки на кран и груз (1.3), Н;
— расстояние от оси вращения до центра тяжести площади наветренной поверхности крана, м.
Момент сопротивления (Н·м) вращению поворотной части крана от сил трения относительно оси вращения крана
Т тр = ![]() | (2.84) |
где Fi, fi, ri — опорные нагрузки (см. ниже), Н, коэффициенты трения [см. пояснения к формулам (1.81) и (1.82)], радиусы действия сил трения опор поворотной части крана, м.
Статическая мощность (кВт) двигателя привода механизма поворота крана
P c = ![]() | (2.85) |
где Т с — момент статических сопротивлений вращению поворотной части крана относительно оси вращения крана, Н·м: Т с = Т укл + Т в + Т тр [см. (2.81)]; п пов — частота вращения поворотной части крана, мин-1; h — КПД привода механизма поворота (см. табл. 1.18).
Двигатель предварительно выбирают по статической мощности Р с, принимая при этом из каталога ближайший больший по мощности. После определения необходимого пускового момента механизма поворота Т пуск [см. (2.81)] согласно формуле (2.85) определяют по этому моменту необходимую мощность двигателя при пуске Р пуск. Необходимая номинальная мощность двигателя может быть определена из условия Р дв³ k Р пуск, где k — коэффициент, учитывающий допустимую перегрузку двигателя в период пуска (k = 0,35...0,5). Затем двигатель проверяется согласно указаниям параграфа 1.7.
Момент сопротивления (Н·м) при торможении (тормозной момент) механизма поворота крана на валу тормоза при неблагоприятном сочетании нагрузок
Т т = Т ![]() ![]() ![]() | (2.86) |
где Т — см. формулу (1.66) и пояснения к формулам (1.60), (1.62), (1.64), (1.66); Т
— момент статических сопротивлений повороту вращающейся части крана на валу тормоза при торможении, Н·м:
Т ![]() ![]() | (2.86) |
![]() | ![]() |
Рис. 2.15. Расчетные схемы кранов: а — с поворотной колонной, б — с неподвижной колонной |
|
Предохранительная фрикционная муфта привода механизма поворота крана рассчитывается на момент
Т пр= (1,1…1,2) Т ![]() | (2.87) |
где Т — момент, передаваемый двигателем предохранительной фрикционной муфте в период пуска механизма поворота.
Опорно-поворотное устройство кранов с расположением опор в вертикальной плоскости (рис. 2.15). Нагрузки:
на опоры А и С:
F А = F С = ![]() | (2.88) |
на опору В:
F В = (Q + m c + m пв) g; | (2.89) |
где Q — масса груза, кг; m c — масса стрелы (поворотной части крана без противовеса и противовесной стрелы), кг; m пв — масса противовеса и противовесной стрелы, кг; l с и l пв — расстояния от оси вращения крана до центра тяжести соответственно стрелы и противовеса, м.
Массу противовеса для крана с постоянным вылетом стрелы можно принять
m пв = ![]() | (2.90) |
где j = k г/(k г + l); k г — коэффициент использования крана по грузоподъемности (см. табл. 1.7).
Момент сопротивления (Н·м) вращению от сил трения в этих опорах относительно оси вращения крана
Т тр =0,5 (FAfAdA + FBfBdB + FCfCdC), | (2.91) |
где dA, dB, dC — диаметры цапф опор; fA, fB, fC — коэффициенты трения в соответствующих опорах.
Если в опоре применяются опорные колеса (опора A, рис. 2.15 и 2.16), момент сопротивления вращению (Н·м) относительно оси колонны в такой опоре при двух опорных колесах
Т тр А = ![]() | (2.92) |
где FA — опорная нагрузка, Н [см. (2.88)]; b — угол между опорными колесами; DA — диаметр круга катания в опоре, м; D к — диаметр колеса, м; m — коэффициент трения качения ролика по кругу катания (по колонне): m = 0,0003...0,0007 м; d к, f — см. пояснения к формуле (1.82).
В этой формуле знак плюс перед цифрой 1 при неподвижной колонне (внешняя опора), знак минус — при вращающейся колонне (внутренняя опора).
Опорные колеса рассчитываются на контактную прочность.
При линейном контакте колеса с плоской опорной поверхностью катания (рельс с плоской головкой) контактные напряжения (Па)
sН = 0,167 kf ![]() | (2.93) |
при точечном контакте колеса с выпуклой опорной поверхностью катания (рельс с выпуклой головкой)
sН = kkf ![]() | (2.94) |
где kf — коэффициент, учитывающий влияние трения на работу опорных колес. При режимах работы: легком kf = 1,0, среднем — kf = 1,04... 1,06, тяжелом kf = 1,06...1,1; F p — расчетная нагрузка на колесо, Н:
F p = kН kДF; | (2.95) |
kН — коэффициент неравномерности распределения нагрузки по ширине рельса: для рельсов с плоской головкой kН = 2, с выпуклой головкой — kН = 1,1; kД —коэффициент динамичности, зависящий от скорости передвижения колеса u. При u (м/с) менее 1; 1…1,5; 1,5...3; более 3 kД соответственно равен 1,0; 1,1; 1,2; 1,3. F — максимальная нагрузка на колесо при номинальных нагрузках на кран в рабочем состоянии, Н; Е - приведенный модуль упругости материала колеса и рельса, Па:
Е = ![]() | (2.96) |
Е 1 и Е 2 — модуль упругости материала соответственно колеса и рельса, Па; b — рабочая ширина головки рельса без учета закруглений, м; R – радиус колеса, м; k — коэффициент, зависящий от отношения R 2/ R < 1; R 1— больший из радиусов колеса и скругления (выпуклости головки рельса, м; R 2 — меньший из радиусов колеса и скругления головки рельса, м:
k» 0,09 ![]() | (2.97) |
![]() | ![]() ![]() |
Рис. 2.16. Расчетная схема опорных нагрузок на катки крана с неподвижной колонной | Рис. 2.17. Расчетные схемы опорно-поворотного устройства: а — нагружения; б — опорного участка; в — для установления расчетного пролета, определяющего опорные реакции |
Допускаемые контактные напряжения [ан] составляют 0,7...0,9 предела текучести материала колеса 25·107...32·107 Па. Подробнее см. [1].
Опорно-поворотные устройства кранов с расположением опор в горизонтальной плоскости (рис. 2.17). Все действующие на опорно-поворотные устройства силы можно свести к вертикальной силе F B, приложенной по оси опорно-поворотного устройства, горизонтальной силе F г, приложенной к опорным элементам по центру тяжести тел качения и к моменту М, определяемому из условия
M = F в L + F г h, | (2.98) |
где L и h — см. рис. 2.17.
Средняя нагрузка (Н) на один опорный элемент в секторе с углом b опорно-поворотного устройства:
а) каткового (опорная реакция вертикальна)
F = ![]() | (2.99) |
б) шарикового или роликового (опорная реакция наклонена под углом g к вертикали)
F = ![]() | (2.100) |
где — число опорных элементов в секторе с углом b; D ср — диаметр опорного круга по средней линии качения (диаметр беговой дорожки тел качения), м; b — центральный угол между точками пересечения окружности диаметром D ср с осями продольных (хребтовых) балок рамы неповоротной части крана (см. рис. 2.17); g — угол наклона опорной реакции к вертикали.
Для опорно-поворотного устройства шарикового, роликового и многокаткового
![]() | (2.101) |
где z — общее количество опорных элементов в опорно-поворотном устройстве (шариков, роликов, катков).
Для опорно-поворотного устройства с опорными колесами равно 2 или 4 (по два колеса на балансире).
Для опорно-поворотных устройств с кольцами из хромистой или марганцовистой стали, при твердости рабочей поверхности 47...55 HRC, со стандартными шариками или роликами (диаметр ролика равен его длине) предельная допустимая нагрузка (МН):
на шарик
F ш = 45 d ![]() | (2.102) |
на ролик
F p = 45 d ![]() | (2.103) |
где d ш, d p — диаметр соответственно шарика и ролика, м.
Момент сил трения (Н·м) в шариковых и роликовых опорно-поворотных устройствах относительно оси вращения может быть принят равным
Т тр = ![]() | (2.104) |
Момент сил трения (Н·м) в опорно-поворотных устройствах многокатковых и с опорными колесами может быть принят равным
Т тр = F в ![]() | (2.105) |
где D к, d к, m, f — см. пояснения к формулам (1.81) и (1.82).
Примерная последовательность расчета механизма поворота:
1) определяются опорные нагрузки по (2.88), (2.89), (2.99), (2.100);
2) определяются моменты сопротивления вращению от уклона пути, ветровой нагрузки и сил трения по (2.82), (2.83), (2.91), (2.105);
3) определяется статическая мощность двигателя по (2.85) и выбирается двигатель (см. параграф III.3);
4) определяется общее передаточное число привода согласно (2.36) при п б = п пов и составляется кинематическая схема механизма;
5) определяется расчетная мощность редуктора по (1.101) или (1.102);
6) определяются расчетные моменты соединительных муфт [см: (1.33) и (1.103)] и выбираются муфты (табл. III.5.1...III.5.9);
7) определяется время пуска (торможения) по (1.76) и проверяется соответствие его данным табл. 1.21;
8) определяется момент сопротивления вращению поворотной части крана на валу двигателя при пуске по (2.81);
9) определяется необходимая мощность двигателя при пуске согласно (2.85) при Т с = Т пуск и производится его проверка согласно пояснениям к формуле (2.85);
10) проверяется двигатель на нагрев (см. параграф 1.7);
11) определяется момент сопротивления на валу тормоза при торможении по (2.86) и выбирается тормоз по табл. III.5.11... Ш.5.14;
12) производится расчет на прочность отдельных элементов механизма (опорных колес, предохранительной фрикционной муфты и др.).
Глава 3. ПРИМЕРЫ РАСЧЕТОВ МЕХАНИЗМОВ ГРУЗОПОДЪЕМНЫХ МАШИН
ПРИМЕР РАСЧЕТА МЕХАНИЗМА ПОДЪЕМА ГРУЗА
Рассчитать механизм подъема груза электрического мостового крана грузоподъемностью Q = 5 т для перегрузки массовых грузов. Скорость подъема груза uг = 0,25 м/с. Высота подъема Н = 15 м. Режим работы — средний, ПВ = 25% (группа 4 режима работы по табл. 1.8).
Принимаем механизм подъема со сдвоенным двукратным полиспастом (см. табл. 2.2).
Усилие в канате, набегающем на барабан [см. (2.1)],
F б = ![]() |
Поскольку обводные блоки отсутствуют, по формуле (2.3)
hо = hп = ![]() |
где hбл = 0,98 (см. табл. 2.1).
Расчетное разрывное усилие в канате [см. (2.6)] при максимальной нагрузке на канат F к= F б = 12 386 Н и k = 5,5
F = 12 386 · 5,5 = 68 123 Н. |
С учетом данных табл. 2.5 из табл. III.1.1 выбираем по ГОСТ 2688—80 канат двойной свивки типа ЛК-Р конструкции 6´19(1 + 6 + 6/6+1 о.с.) диаметром d = 11мм, имеющий при маркировочной группе проволок 1764 МПа разрывное усилие F = 68 800 Н.
Канат грузовой (Г), первой марки (1), из проволоки без покрытия (-), правой крестовой свивки (-), нераскручивающийся (Н) согласно (2.1) обозначается:
Канат—11—Г—I—H—1764 ГОСТ 2688—80.
Фактический коэффициент запаса прочности каната
k j = ![]() |
Требуемый диаметр барабана по средней линии навитото стального каната [см. (2.9)] D = 11·25 = 275 мм. Принимаем диаметр барабана D = 300 мм.
По табл. III.2.5 выбираем подвеску крюковую типа 1 грузоподъемностью 5 т, имеющую блоки диаметром 320 мм с расстоянием между блоками b = 200 мм.
Длина каната, навиваемого на барабан с одного полиспаста [см. (2.10)] при z 1 = 2, z 2 = 3,
L к= 15·2 + 3,14·0,3(2 + 3) = 34,7 м. |
Рабочая длина барабана для навивки каната с одного полиспаста при t = 12,5 мм, т = 1и j = 1 [см. (2.11)]
L б= ![]() |
Приняв расстояние между правой и левой нарезками на барабане (длина ненарезной части) равным расстоянию между ручьями блоков в крюковой обойме, т.е. l = b = 0,2 м, найдем полную длину барабана
L = 2 L б + l = 2·0,444+0.2 = 1,088 м. |
Минимальная толщина стенки литого чугунного барабана [см. (2.18)] dmin = 0,02·0,289+0,006…0,01 = 0,012...0,016 м = 12...16 мм, где D б = D - d = 0,3-0,011 = 0,289 м. Принимаем d = 14 мм.
Приняв в качестве материала барабана чугун марки СЧ 15 (sв=650 МПа, [sсж]=130 МПа), по формуле (2.16) найдем напряжение сжатия в стенке барабана:
sсж= = 70,78·106 Па = 70,78 МПа<130 МПа.
Статическая мощность двигателя [см. (2.31)] при h = 0,85
Р с= ![]() |
С учетом указаний к формуле (2.31) из табл. III.3.5 выбираем крановый электродвигатель с фазным ротором MTF 211-6, имеющим при ПВ = 25% номинальную мощность Р ном = 9 кВт и частоту вращения п = 915 мин-1. Момент инерции ротора I р = 0,115 кг·м2, максимальный пусковой момент двигателя Т mах = 195 Н·м.
Частота вращения барабана [см. (2.35)] при D расч = D = 0,3 м
п б= ![]() |
Передаточное число привода
и = п / п б = 915/31,8 = 28,8. |
Расчетная мощность редуктора [см. (1.101)] при k p=l и Р = Р с
Р р= 1,0·13,46 = 13,46 кВт. |
Из табл. Ш.4.2 по передаточному числу и мощности выбираем редуктор цилиндрический, двухступенчатый, горизонтальный, крановый типоразмера Ц2-300 с передаточным числом и р = 32,42 и мощностью на быстроходном валу при среднем режиме работы Р р = 14,6 кВт.
Момент статического сопротивления на валу двигателя в период пуска [см. (1.27)] с учетом того, что на барабан навиваются две ветви каната, при hб = 0,94 и hпр = 0,9 (ориентировочно)
Т с= ![]() |
Номинальный момент, передаваемый муфтой, принимается равным моменту статических сопротивлений Т = Т с = 135 Н·м.
Номинальный момент на валу двигателя по формуле (1.33)
Т ном= 9550 ![]() ![]() |
Расчетный момент для выбора соединительной муфты [см. (1.103)]
Т м= 135·1,3·1,2 = 211 Н·м. |
Из табл. III.5.9 выберем ближайшую по требуемому крутящему моменту упругую втулочно-пальцевую муфту № 1 с тормозным шкивом диаметром D T = 200 мм и наибольшим передаваемым крутящим моментом 500 Н·м.
Момент инерции муфты I м = 0,125 кг·м2. Момент инерции ротора двигателя и муфты I = I p + I м = 0,225 + 0,125 = 0,35 кг·м2.
Средний пусковой момент двигателя [см. (1.89)] при ymin=1,4.
Т пуск= Т ср.п = ![]() |
где ymах = = 2,08.
Время пуска при подъеме груза [см. (1.67)]
t п= ![]() |
Фактическая частота вращения барабана по формуле (2.36)
п =
= 28,2 мин-1.
Фактическая скорость подъема груза по формуле (2.35)
u ![]() ![]() |
Эта скорость отличается от ближайшего значения 0,2 м/с из стандартного ряда на 10%, что допустимо. Ускорение при пуске, согласно (1.80),
а = ![]() |
Полученные значения t и а соответствуют рекомендациям табл. 1.19 и 1.25.
Поскольку график действительной загрузки механизма подъема не задан, воспользуемся усредненным графиком использования механизма по грузоподъемности (см. рис. 1.1, а), построенным на основе опыта эксплуатации кранов. Определим моменты, развиваемые двигателем, и время его пуска при подъеме и опускании груза в различные периоды работы мехаттнзма. Согласно графику, за время цикла (подъем и опускание груза) механизм будет работать с номинальным грузом Q = 5000 кг — 1 раз, с грузом 0,5 Q = 2500 кг — 5 раз, с грузом 0,2 Q = 1000 кг — 1 раз, с грузом 0,05 Q = 250 кг — Зраза.
Табл. 3.1. Моменты, развиваемые двигателем, и время его пуска
Наименование показателя | Обозначение | Единица | Результаты расчета при массе поднимаемого груза, кг | |||
КПД (см. рис. 1.2) | h | - | 0,85 | 0,8 | 0,65 | 0,5 |
Натяжение каната у барабана при подъеме груза по (2.1) | F б | H | 12 386 | |||
Момент при подъеме груза по (1.27) | Т с | Н·м | 71,7 | 35,3 | 11,5 | |
Время пуска при подъеме по (1.67) | t п | с | 1,4 | 0,42 | 0,29 | 0,24 |
Натяжение каната у барабана при опускании груза [в формуле (2.1) коэффициент h0 должен быть в числителе] | F ![]() | Н | 12 195 | |||
Момент при опускании груза по (1.28) | Т ![]() | Н·м | 97,4 | 51,7 | 25,5 | 8,28 |
Время пуска при опускании по (1.67) | t оп | с | 0,15 | 0,18 | 0,20 | 0,22 |
В табл. 3.1 избыточный момент при опускании груза — сумма среднего пускового момента двигателя и момента статических сопротивлений механизма при опускании груза.
Результаты расчетов приводятся в табл. 3.1.
Средняя высота подъема груза составляет 0,5...0,8 номинальной высоты Н = 15 м. Примем Н ср = 0,8 Н = 0,8·15= 12 м.
Тогда время установившегося движения
t y = ![]() ![]() |
Сумма времени пуска при подъеме и опускании груза за цикл работы механизма å t п =1,4 + 5·0,42+1,029 + 3·0,24 + 0,15 + 5·0,18+1·0,2 + 3·0,22 = 6,42 с.
Общее время включений двигателя за цикл å t = 2 (1 + 5 + 1 + 3) t y + å t п = = 2 · 10 · 54,5 + 6,42 = 1096,42 с.
Среднеквадратичный момент [см. (1.93)]
Т ср = ![]() |
Среднеквадратичная мощность двигателя по (1.92)
Р ср = ![]() |
Следовательно, условие (1.91) соблюдается (5,76<9).
Момент статического сопротивления на валу двигателя при торможении механизма по (2.27)
Т ![]() ![]() |
Необходимый по нормам Госгортехнадзора момент, развиваемый тормозом [см. (2.38)], при k т = 1,75 Т т = 95,47·1,75= 167 Н·м.
Из табл. III.5.11 выбираем тормоз ТКТ-300/200 с тормозным моментом 240 Н·м, диаметром тормозного шкива D т = 300 мм. Регулировкой можно получить требуемый тормозной момент Т т = 167 Н·м.
По формуле (1.68) определим время торможения при опускании груза (при подъеме груза это время будет меньше, так как в этом случае момент от веса груза и тормозной момент действуют в одном направлении):
t т = ![]() |
Из табл. 1.22 для среднего режима работы находим путь торможения механизма подъема груза
s = ![]() |
Время торможения в предположении, что скорости подъема и опускания груза одинаковы, согласно (1.75),
t ![]() ![]() |
|
|
Эмиссия газов от очистных сооружений канализации: В последние годы внимание мирового сообщества сосредоточено на экологических проблемах...
Механическое удерживание земляных масс: Механическое удерживание земляных масс на склоне обеспечивают контрфорсными сооружениями различных конструкций...
Двойное оплодотворение у цветковых растений: Оплодотворение - это процесс слияния мужской и женской половых клеток с образованием зиготы...
Состав сооружений: решетки и песколовки: Решетки – это первое устройство в схеме очистных сооружений. Они представляют...
© cyberpedia.su 2017-2024 - Не является автором материалов. Исключительное право сохранено за автором текста.
Если вы не хотите, чтобы данный материал был у нас на сайте, перейдите по ссылке: Нарушение авторских прав. Мы поможем в написании вашей работы!