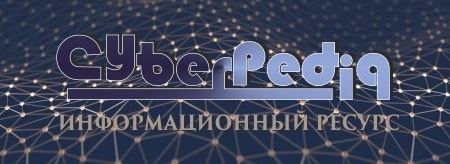
Биохимия спиртового брожения: Основу технологии получения пива составляет спиртовое брожение, - при котором сахар превращается...
Типы оградительных сооружений в морском порту: По расположению оградительных сооружений в плане различают волноломы, обе оконечности...
Топ:
История развития методов оптимизации: теорема Куна-Таккера, метод Лагранжа, роль выпуклости в оптимизации...
Эволюция кровеносной системы позвоночных животных: Биологическая эволюция – необратимый процесс исторического развития живой природы...
Оценка эффективности инструментов коммуникационной политики: Внешние коммуникации - обмен информацией между организацией и её внешней средой...
Интересное:
Отражение на счетах бухгалтерского учета процесса приобретения: Процесс заготовления представляет систему экономических событий, включающих приобретение организацией у поставщиков сырья...
Национальное богатство страны и его составляющие: для оценки элементов национального богатства используются...
Что нужно делать при лейкемии: Прежде всего, необходимо выяснить, не страдаете ли вы каким-либо душевным недугом...
Дисциплины:
![]() |
![]() |
5.00
из
|
Заказать работу |
|
|
Высокая стоимость и дефицит электроэнергии вызывают необходимость изменения технологического процесса производства электростали и применения альтернативных источников тепловой энергии в рабочем пространстве на основе экзотермических реакций окисления. Однако из всех химических элементов шихтовых материалов, используемых при электроплавке, в качестве альтернативного источника тепловой энергии следует рассматривать только углерод, который вводят:
в рабочее пространство при завалке – материалы-науглеро-живатели (карбюризаторы) различной стоимости: кокс, электродный бой, измельченный уголь или кокс соответствующего гранулометрического состава, твердый или жидкий чугун, карбид железа и др. Экзотермическая реакция окисления избыточного углерода, растворенного в металле, обеспечивает увеличение энтальпии металла, так как является теплотехнически совершенным источником тепловой энергии. Например, окисление 0,1 % углерода газообразным кислородом повышает температуру на 10…15 К при тепловом эффекте реакции 9,43 МДж/кг;
в ванну жидкого металла – порошок кокса в потоке кислорода (донная продувка) для барботажа ванны за счет образования монооксида углерода и дополнительной теплогенерации (7, 55 МДж/кг);
в шлак – угольный порошок или порошок кокса в сверхзвуковом потоке кислорода для дополнительного образования монооксида углерода при формировании вспененного («пенистого») шлака;
в «свободное» пространство – угольный порошок в потоке кислорода для дополнительной теплогенерации при образовании диоксида углерода (28,44 МДж/кг) для компенсации тепловых потерь в водоохлаждаемых элементах рабочего пространства.
|
В «свободном» пространстве дополнительную теплогенерацию создают за счет дожигания выделяющегося из ванны монооксида углерода (25,3 МДж/м3 кислорода). Эффективность систем дожигания характеризуют степенью дожигания в виде соотношения содержания СО2/(СО + СО2) в отходящих газах, которая может составлять 60…100 %, и эффективностью теплопередачи, которая может составить:
на ванну жидкого металла 30…40 %,
на холодную металлошихту 50…60 %,
в шахтной печи 80…90 %.
Результирующая эффективность достигает 35…65 %, обеспечивая экономию электроэнергии при дожигании технологических газов в дуговых печах до 60 кВт×ч/т (см. табл. 14).
Для дожигания технологических газов в рабочем пространстве дуговых печей требуется, как уже указывалось, дополнительный расход кислорода порядка 10…15 м3/т, который подводят через так называемые струйные (вихревые) инжекторы разной конструкции:
– система из трех пар горизонтальных стальных труб (из коррозионно-стойкой стали), направляющих струи кислорода попарно навстречу друг другу тангенциально к поверхности стены, которая образует в пространстве за электродами вихревой треугольник (система дожигания ALARC-PC французской фирмы L¢Air Liquide);
– многоцелевая кислородная фурма в эркерной зоне печи;
– кислородная фурма со сверхзвуковой струей, обеспечивающая дожигание прямо в шлаке, но при этом вырастает окисленность шлака и уменьшается выход годного;
– вихревой радиационный инжектор кислорода (ВРИК) с керамическим криволинейным диффузором диаметром 1,0…1,5 м, устанавливаемый в водоохлаждаемых элементах комбинированного свода. ВРИК, работающий по принципу плоскопламенной горелки, создает плоский настильный факел, а нагретая поверхность диффузора – сплошной спектр излучения (в отличие от селективного спектра излучения факела дожигания, состоящего в основном из трехатомного газа – диоксида углерода), обеспечивая эффективную теплопередачу в рабочее пространство печи (ВРИК конструкции МИСиС и АО «НЛМК»).
|
При плавлении твердого металлолома эффективно применение ТКГ. Сжигание природного газа* (теплота сгорания 32…43 МДж/м3) экономически выгоднее по сравнению с теплогенерацией электроэнергии в дуговых печах (в воздухе в 4–5 раз, в кислороде в 3–4 раза). В ТКГ газ сжигают в чистом кислороде с коэффициентом расхода n 2 для получения высокотемпературного факела (до 2000 К), но при достижении температуры металлолома 800…1000 К начинается интенсивное окисление железа продуктами горения топлива, которые при этом восстанавливаются до СО и Н2, и происходит «недожог» топлива, что делает работу ТКГ малоэффективной (коэффициент использования топлива падает с 70 до 20 %) и ограничивают время их работы до 15…20 мин.
В современных ДСП применяют оконные (дверные), стеновые, эркерные и сводовые, стационарные, выдвижные и поворотные, коротко- и длиннофакельные ТКГ тепловой мощностью 3…10 МВт в количестве 6–9 (в шахтных печах до 16) и суммарной мощностью до 50 МВт. Расположение ТКГ должно создавать циркуляцию продуктов горения в объеме металлолома, дополняя теплотехнически несовершенную радиационную теплопередачу от высокотемпературной зоны горения газообразного топлива (из-за радиационных характеристик факела) интенсивной конвективной теплопередачей.
Применение ТКГ в зависимости от их конструкции и режима работы, удельного расхода природного газа 5…10 м3/т (при средним коэффициенте использования топлива, по данным Ю.Н. Тулуевского, 40 %) может снизать удельный расход электроэнергии на малых печах на 90…120 кВт·ч/т (см. табл. 14) и на 30…60 кВт·ч/т на крупных высокомощных печах, а также сократить длительность энергетического периода плавки на 5…15 мин и ускорить расплавление твердой металлошихты на 10…15 % (при недостаточной мощности электропечного трансформатора).
Нежелательным, но неизбежным источником тепловой энергии является процесс окисления графитированных электродов (1,0…1,5 кг/т в ДСП ПТ; 1,5…3,0 кг/т в ДСП), который создает теплогенерацию в рабочем пространстве печи порядка 50…150 МДж/т или составляет 3…5 % приходной части энергетического баланса.
Вспененные шлаки
Вспененные («пенистые») шлаки обеспечивают режим работы современных ДСП с длинными дугами, т.е. на более высоких ступенях вторичного напряжения согласно (34) и меньших токах с соответствующими более высокими электротехническими показателями, способствуя повышению производительности, экономии электроэнергии (см. табл. 14) и снижению расхода дорогостоящих высококачественных графитированных электродов. При этом экранирование столба дуги повышает теплотехническую эффективность использования тепловой энергии дуги на 30…60 %. При достаточной электропроводности «пенистого» шлака происходит шунтирование дуги и дуговая печь превращается в печь сопротивления с теплотехнически совершенной внутренней теплогенерацией и прямым нагревом шлаковой ванны по закону Джоуля – Ленца; при этом в электрической цепи протекает синусоидальный ток и ДСП также имеет более высокие электротехнические показатели l и hэ.
|
Вспенивание окислительного печного шлака происходит при вдувании в зону ниже уровня раздела «шлак – металл» углерода в виде порошкообразного угля или коксовой мелочи (0,5…3,0 мм) в количестве 4…8 кг/т в потоке сжатого воздуха или кислорода.
Дуговые сталеплавильные печи постоянного тока
(ДСП ПТ)
Экономически выгодное благодаря вышеописанным технологическим, теплотехническим и конструктивным решениям увеличение электрической мощности S ном ДСП (см. главу 1, § 3, решение задачи № 1) создает целый ряд проблем эксплуатации таких печей: высокий уровень шума (свыше 120 дБ), помехи в питающей электросети («фликкер»), низкий естественный коэффициент мощности (), большой расход графитированных электродов и др. Альтернативой высокомощным ДСП являются ДСП ПТ, самыми крупными из которых являются печи вместимостью 160 (Япония) и 220 (Малайзия) т и мощностью 120 и 160 МВт соответственно.
ДСП ПТ имеют меньший расход 1,1…1,3 кг/т графитированного электрода-катода диаметром до 800 мм при силе тока до 140 кА, более нижний уровень шума (на 10…15 дБ), снижение уровня фликкер-эффекта в 2–3 раза (по оценке Международного союза по электротермии), более равномерную тепловою нагрузку на стену и свод (см. § 4), интенсивное ЭМП ванны жидкого металла-анода, меньшие пылегазовые выбросы, что позволяет считать ДСП ПТ более экономичными, электротехнически совершенными и экологически безопасными агрегатами.
|
|
Двойное оплодотворение у цветковых растений: Оплодотворение - это процесс слияния мужской и женской половых клеток с образованием зиготы...
Наброски и зарисовки растений, плодов, цветов: Освоить конструктивное построение структуры дерева через зарисовки отдельных деревьев, группы деревьев...
Таксономические единицы (категории) растений: Каждая система классификации состоит из определённых соподчиненных друг другу...
Индивидуальные и групповые автопоилки: для животных. Схемы и конструкции...
© cyberpedia.su 2017-2024 - Не является автором материалов. Исключительное право сохранено за автором текста.
Если вы не хотите, чтобы данный материал был у нас на сайте, перейдите по ссылке: Нарушение авторских прав. Мы поможем в написании вашей работы!