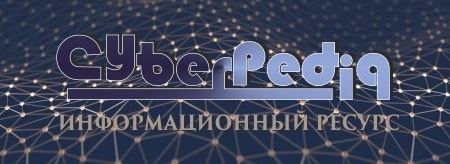
Наброски и зарисовки растений, плодов, цветов: Освоить конструктивное построение структуры дерева через зарисовки отдельных деревьев, группы деревьев...
Кормораздатчик мобильный электрифицированный: схема и процесс работы устройства...
Топ:
Характеристика АТП и сварочно-жестяницкого участка: Транспорт в настоящее время является одной из важнейших отраслей народного хозяйства...
Характеристика АТП и сварочно-жестяницкого участка: Транспорт в настоящее время является одной из важнейших отраслей народного...
Основы обеспечения единства измерений: Обеспечение единства измерений - деятельность метрологических служб, направленная на достижение...
Интересное:
Подходы к решению темы фильма: Существует три основных типа исторического фильма, имеющих между собой много общего...
Распространение рака на другие отдаленные от желудка органы: Характерных симптомов рака желудка не существует. Выраженные симптомы появляются, когда опухоль...
Влияние предпринимательской среды на эффективное функционирование предприятия: Предпринимательская среда – это совокупность внешних и внутренних факторов, оказывающих влияние на функционирование фирмы...
Дисциплины:
![]() |
![]() |
5.00
из
|
Заказать работу |
|
|
Кокс – это почти чистый углерод. В угле же содержится много водорода и кислорода. Коксование – процесс переработки смеси углей (угольной шихты) различных марок (коксующихся, жирных, газовых, отощенных, слабоспекающихся) путем нагревания без доступа воздуха до температур 900-11000С. Получение кокса осуществляется в коксовых печах. Процесс спекания продолжается 14-17 часов. Дальнейшая обработка кокса заключается в его тушении водой (мокрый способ) или газом-охладителем (сухой способ), с последующей сортировкой на разные по крупности фракции.
В составе Коксохимического производства ОАО «НЛМК» 2 коксовых цеха. Коксовый цех №1(батареи №1-2) производит кокс мокрого тушения. Коксовый цех №2(батареи №5-6) производит кокс сухого тушения.
Суммарная производственная мощность Коксохимического производства – 2,7 млн.тонн в год.
Общая схема переработки летучих продуктов коксования приведена на рис.5
Фасонолитейный цех
Назначение ФЛЦ – производство ремонтного, стального, чугунного и цветного литья для нужд комбината и сторонних родственных предприятий. Характер производства единичное и мелкосерийное производство. Развес отливок от 1 кг до 50 т. Кроме этого в цехе изготавливается художественное литье. Так, большинство памятников, установленных в Липецке и области, отливалось в этом цехе, конкретно, памятник Петру I, установленный на одноименной площади у кинотеатра «Октябрь».
Цех состоит из нескольких отделений, описание некоторых из них последует ниже.
Смесеприготовительное отделение. В смесеприготовительном отделении установлены трое смешивающих бегунов модели 15107 производительностью 12 т/ час каждые и пара смешивающих бегунов модели 1А12 производительностью 3,5 т/час. На данном участке происходит приготовление формовочных и стержневых смесей, которые затем по ленточным транспортерам передаются в бункеры – накопители формовочного отделения. Формовочная смесь состоит из наполнителя – формовочный песок и связующего – жидкое стекло, формовочная глина или синтетические смолы. В соответствии с тем, какое применяется связующее, формовочные смеси подразделяются на жидкостекольные, песчано-глинистые и смоляные.
|
Плавильное отделение. На данном участке производится широкий ассортимент марок сталей и сплавов. Это низко- и среднеуглеродистые, низко- и высоколегированные марки сталей, предназначенных для изготовления отливок, а также конструкционные и инструментальные марки сталей, предназначенных для изготовления поковок. Кроме этого в незначительных объемах производится бронзовое литье.
Основное плавильное оборудование – это две дуговые сталеплавильные печи ДСП- 25 емкостью 25 т каждая, одна дуговая сталеплавильная печь с выкатным подом 5Мт емкостью 5 т и две индукционные печи ИСТ 025 емкостью 250 кг каждая. Тип футеровки на всех печах – основной.
Термообрубное отделение. В термообрубном отделении происходит окончательная очистка литья, его обрубка, обрезка, термообработка и сдача ОТК готовой продукции. Выбитые отливки с выбивных решеток поступают в дробеметные камеры, для удаления остатков формовочной смеси и пригара. Для этих целей в цехе установлены две дробеметные камеры, одна проходного типа, другая с поворотным выкатным столом, предназначенных для очистки литься среднего развеса. Для очистки мелкого литья в цехе установлен дробеметный галтовочный барабан с объемом рабочей камеры 1,7 м3. Кроме этого, для удаления у отливок пригара в труднодоступных местах в цехе установлен галтовочный барабан объемом 10 м3. Принцип очистки литья в дробькамерах заключается в следующем: в рабочем пространстве камеры – в нижней, средней и верхней частях установлены три вала, на которых крепятся лопатки из износостойкого материала. При вращении валов, на лопатки, по специальным каналам подается чугунная дробь, которая затем, получая ускорение, попадает на поверхность отливки и удаляет с нее формовочную смесь и пригар. Заливы и просечки металла удаляются с поверхности отливки и удаляет с помощью огневой резки и пневматических отбойных молотков. Далее обрубленные и очищенные отливки подвергаются термической обработке. Целью термообработки является снятие литейных напряжений в отливке, улучшение микроструктуры металла и придание ему специальных механических свойств. Для этих целей в цехе установлены четыре закалочные печи с выкатным подом, и закалочный бак с водой емкостью 46 м3, в которых в основной производятся закалка марганцовистого литья. На участке также установлена термическая печь №5 с площадью пода 72 м2, предназначенная для высоко- и низкотемпературного отпуска отливок и крупногабаритных сварных стальных конструкций. Цех имеет возможность производить все виды термической обработки деталей и конструкций.
|
Конверторный цех № 2
Сталь, по сравнению с чугуном, содержит значительно меньше углерода (до 2%). Она мягче, податливее, её легче обрабатывать. Металлурги научились легировать сталь, то есть «сдабривать» её различными добавками и придавать ей разнообразные свойства, изменяя в каждом конкретном случае условия ведения технологического процесса. Если, например, в сталь добавить немного титана (Тi), легкого и прочного металла, а затем хром (Сг) и никель (Ni), то получим сталь твердую, пластичную и коррозионностойкую (нержавеющая сталь). Легирующими добавками также служат - вольфрам (W), кобальт (Со), молибден (МЬ),ванадий (V), цирконий (Zг) др. Большинство этих добавок вводят в сталь в виде готовых сплавов с железом, которые называются ферросплавами. Некоторые из них выплавляются в ферросплавном цехе комбината (ФСЦ)
Принципиальная схема кислородного конвертера
Для выплавки стали, на комбинате используются кислородные конвертеры, представляющие собой емкости грушевидной формы, футерованные внутри стойким огнеупорным кирпичом. В Кц №1 установлено 3 конвертера емкостью по 160 т каждый, в Кц №2 - 2 конвертера емкостью по 300 т.
|
В общем виде процесс производства стали можно представить как ряд операций, задачей которых является удаление примесей из чугуна. Если производство чугуна с точки зрения химиков процесс восстановительный, то передел чугуна и металлического лома в сталь - окислительный.
Технология кислородно-конвертерного процесса выплавки стали основана на удалении (окислении) примесей (углерода, кремния, марганца, фосфора и серы) за счет вдувания в жидкий чугун через вертикальную водоохлаждаемую фурму технически чистого кислорода и перевода этих примесей в шлак или газовую фазу.
В качестве шлакообразующих материалов используется металлургическая известь, доломит и плавиковый шпат. Эти материалы, реагируя с примесями, связывают их в прочные соединения, которые не растворяются в стали, а всплывают в шлак.
Заливка жидкого чугуна.
Технология производства стали включает последовательное выполнение следующих операций:
1. Загрузка металлического лома в конвертер в количестве 18-22 % от всей металлической шихты плавки.
2. Заливка жидкого чугуна в конвертер.
3. Продувка металла в конвертере техническим кислородом.
4. Измерение температуры и отбор проб металла и шлака после окончания продувки.
5. Выпуск плавки из конвертера в сталеразливочный ковш с присадкой науглероживателя и раскислителей (ферросплавов, обеспечивающих получение расплава с химическим составом, близким к среднему составу для данной марки стали).
6. Обработка расплава аргоном в сталеразливочном ковше (внепечная обработка) производится для усреднения и корректировки химического состава и температуры.
Весь цикл получения одной плавки жидкой стали таким способом составляет от 40 до 60 минут.
Производство слябов осуществляется путем разливки жидкой стали на установках непрерывной разливки стали (УНРС).
Установка непрерывной разливки стали агрегат, который позволяет разливать жидкий металл в твердые заготовки заданного сечения - прямоугольного (слябы), квадратного (блюмы), круглого или профилированного (круг, тавр, двутавр и тд.). Кц №1 оснащен 6 установками вертикального типа, высотой 42 м (16 м над землей, 27 м под землей). В Кц №2 такими установками уже не пользуются. Но большее значение имеют установки непрерывной разливки стали криволинейного типа. Схема данной установки приведена ниже.
|
Резка слябов.
Когда слиток полностью затвердел и выпрямлен в горизонтальное положение, он попадает на установку газовой резки, где специальные резаки смесью природного газа и кислорода разрезают его на куски заданных размеров. Отрезанные слябы при помощи роликового конвейера (рольганга) подаются на склад, где проходят контроль качества, и обработку, обеспечивающую удаление выявленных дефектов. Затем слябы отгружают в листопрокатный цех №3 или в полувагоны для отправки сторонним потребителям.
В состав оборудования Кц №2 входят четыре УНРС криволинейного типа и одна - радиального типа. Для разливки металла применяют сталеразливочные ковши емкостью 180 и 350 т и промежуточные ковши емкостью 10, 23, 30 и 50 т.
Сталеплавильное производство ОАО «НЛМК» состоит из двух кислородно-конвертерных цехов - Кц №1 и Кц №2 производительностью порядка 3,8 и 5,5 млн. т литых слябов в год соответственно.
Копровый цех
Вторичные черные металлы являются важнейшим сырьем для металлургии. Основными источниками вторичных черных металлов являются, как известно, отходы собственного металлургического производства, отходы металлообработки и амортизационный лом. Количество собственных (оборотных) металлоотходов на металлургических предприятиях зависит от объема выплавки и уровня использования непрерывной разливки стали. Это количество непрерывно снижается.
В условиях роста загрязненности оборотного лома и возможного дефицита особое значение приобретает разработка и совершенствование промышленных способов очистки и подготовки металлолома на всех отечественных ломоперерабатывающих предприятиях.
С увеличением доли качественных сталей (электротехнических, трубной, автолистовой, особонизкоуглеродистой и др.) с повышенными требованиями по содержанию примесей в общем объеме производства ОАО “Ново-Липецкий металлургический комбинат” возрастают требования к качеству шихтовых материалов, в том числе лома.
Качество лома характеризуется тремя основными параметрами:
• содержанием железа металлического;
• содержанием серы, легирующих и цветных металлов (в первую очередь таких, как хром, никель, медь, олово, молибден) и неметаллических примесей;
• насыпной плотностью и максимальными размерами куска.
• Качество товарного лома, поступающего в копровый цех ОАО “НЛМК”, регламентируется требованиями ГОСТа 2787-75 “Металлы черные вторичные” и договорами на поставку металлолома.
• За девять месяцев прошлого года в копровый цех поступило 809,2 тыс. тонн товарного лома, средняя насыпная плотность которого составила 0,53 t/m3. Доля габаритного лома видов (1А-3А) составила 59,8%, доля лома, требующего переработки с помощью газовой резки (3А2, 5А и железнодорожного лома), – 27,9%, пакетов и брикетов – 2,9%, лома для пакетирования – около 1%. Кроме того, в копровый цех поступило 49,99 тыс. тонн (6,2%) горячебрикетированного железа (ГБЖ) производства АО “Лебединский ГОК”, качество которого регламентируется ТУ 0726-003-000186803-98.
|
От цехов комбината в копровый цех поступило 432,7 тыс. тонн оборотного металлолома, основную часть которого составили обрезь углеродистая – 44,8%, обрезь электротехнических сталей – 14,2%, скрап – 28,5%. Большая часть обрези представляла собой легковесный лом и требовала переработки методом пакетирования.
Поступивший в копровый цех металлолом, в зависимости от вида, подвергался переработке с помощью пакетирования, газовой резки, копрового и взрывного дробления и сортировки. Всего за девять месяцев 2011 года переработано 995,2 тыс. тонн лома, из них с помощью сортировки – 45,6%, с помощью газовой резки – 34,2%, с помощью пакетирования – 12,7%.
Переработанный металлический лом, предназначенный для использования в качестве металлошихты в сталеплавильных цехах, подразделяется на 1-й, 2-й и 3-й сорта:
– 1-й сорт – обрезь слябов, металлические отходы прокатных цехов, листовые стальные отходы с автозаводов, а также стальной скрап конвертерных цехов;
– 2-й сорт – рельсы, металлоконструкции, лом сельскохозяйственных машин, автомобилей, железнодорожных вагонов без силовых агрегатов и деталей привода, пакеты собственного производства и пакеты из чистых легковесных стальных отходов (Вид 8А);
– 3-й сорт – брикеты из стальной стружки (Вид 6А и 7А), пакеты из легковесных стальных отходов и лома, (Вид 9А и 10А), стальные канаты и проволока, чугунный скрап после копрового и взрывного дробления.
Первый сорт лома или смесь первого и второго сортов используется в сталеплавильных цехах в качестве металлошихты для выплавки качественных сталей, второй сорт – для выплавки сталей рядового сортамента. Третий сорт лома как самостоятельный вид металлошихты не используется и служит для подшихтовки при выплавке сталей рядового сортамента.
Таким образом, основными видами товарного лома, поступившего в копровый цех являются габаритный и негабаритный металлолом для газовой резки, основными видами оборотного лома – обрезь углеродистая, скрап и обрезь электротехнических марок стали. Исходя из этого основные виды переработки, в ходе которых можно повышать насыпную плотность лома и удалять примеси цветных металлов и неметаллических материалов, – сортировка, газовая резка, пакетирование и копровое дробление. Использование металлического лома 1-го сорта обеспечивает получение качественной стали с заведомо низкими массовыми долями цветных элементов.
Важной проблемой для копрового цеха ОАО “НЛМК” является переработка непрерывно растущего количества амортизационного легковесного лома. Одним из реальных путей решения этой проблемы представляется приобретение и установка современных гидравлических ножниц с предварительным уплотнением (подпрессовкой) перерабатываемого лома. Очистка порезанного на ножницах металлического лома от неметаллических примесей может производиться с помощью установленных за ножницами виброплощадки или вращающегося барабана.
Переработка легковесного амортизационного лома с помощью ножничной резки позволит снизить долю применения ручного труда и повысить качество металлошихты за счет увеличения насыпного веса лотков.
Ферросплавный цех
Производит ферросилиций (65%). Примеси – алюминий и титан.
3 сорта ферросилиция: 1 – й (алюминия 0,5%, титана 0,5%),
2 – й (алюминия 0,7%, титана 0,5%),
3 – й (алюминия 1,2%, титана 0,5%),
есть ещё 4 – й сорт с содержанием алюминия до 2,5%.
Данный продукт применяется в электросталеплавильном цехе и кислородно-конвертерном цехе №2.
Это производство очень энергоёмкое. Для него необходим рудо восстанавливающий способ в открытых печах (3 печи).
В данном цехе также производят ферротитан, сварочные флюсы, борсодержащие сплавы (данное предприятие единственное производит этот продукт). 1 см3 бора поглощает количество радиации, испускаемое 10 – 15 см3 радия, эти сплавы самые дорогие. Наш комбинат поставлял эти сплавы на место ликвидации аварии Чернобыльской АЭС. Здесь же производят ацетилен, в виде баллонов, внутри которых находится пористая масса и ацетон, куда потом закачивают ацетилен.
Компоненты шихты приходят в вагонах и выгружаются на шихтовый двор. Здесь кокс дробят дробилками, а потом просевают. Все компоненты разделены между собой, чтобы было удобнее производить дозировку для получения шихты необходимого состава. Одним из компонентов шихты является стальная стружка. Также применяется древесная стружка, необходимая для того, чтобы разрыхлять колошник печи. На территории цеха есть газоочистка, в которой вода уносит в отстойники отходы производства, но она эффективна только на 65%. Вскоре здесь хотят построить сухую газоочистку. Вообще цех стандартизирует немецкая фирма «Зергюф», что приводит к постоянному улучшению качества работы цеха.
Далее шихта поступает в машинный зал. Здесь есть 4 дымоотсоса. По тракту шихтоподачи компоненты проходят в бункер, а затем развозятся по дозировочным площадкам. Дозируют, начиная с самого лёгкого компонента, чтобы легче было перемешивать шихту. На этом участке расположены печи мощностью по 10,5 МВт. В печь опускается 3 электрода при температуре 150 0С, и шихта начинает плавиться. В смену цех потребляет приблизительно 75 кВТ часов электроэнергии, поэтому в цехе есть электрический режим. Все элементы печи водоохлаждаемые. Печь в основном обслуживает 3 человека.
Через лётку готовый продукт по желобу попадает в изложницу, где он остывает, а после его подают на разбивочную машину. Далее в измельченном виде продукт попадает в бункера хранения. Этот цех единственный получает ферросилиций такого высокого качества с первого передела.
В алюминотермическом отделении производят дорогостоящие плавки с получением борсодержащих сплавов.
Заключение
Новолипецкий металлургический комбинат – это визитная карточка города Липецка, который по праву называют Городом Металлургов.
ОАО «НЛМК», сегодня занимает позицию быстрорастущей компании со сбалансированной стратегией развития. Основной стратегией НЛМК является стремление к увеличению акционерной стоимости и последовательному снижению влияния отраслевых рисков. Реализация поставленных целей осуществляется за счет модернизации производства, увеличения выпуска сталепрокатной продукции, приобретения и развития новых активов, улучшения качества и расширение ассортимента продукции, повышения энергетической и экологической эффективности, освоения новых рынков, оптимизации структуры управления.
Стабильно развивающийся, постоянно обновляющий свое производство, комбинат вносит наибольший вклад в промышленность страны, и по праву входит в тройку лидирующих металлургических производителей, известные по всему миру, такие как ОАО «ММК» и ОАО «Северсталь». Такие позиции ОАО «НЛМК» достигло, благодаря своей четкой управленческой деятельности, рациональному использованию ресурсов, которое является самым низкозатратным, и как следствие, имеет высокий уровень капиталоотдачи.
Все эти конкурентоспособные преимущества позволяют предприятию играть активные роли не только на Российском рынке, но и на мировой арене.
В ОАО «НЛМК» для оптимизации ресурсов в настоящее время действует полтикика в области ресурсосбережения. В соотвествии с данной политикой ОАО «НЛМК» стремится к обеспечению производства продукции заданного качества и объема с минимальными затратами, в том числе путем внедрения ресурсосберегающих мероприятий, оборудования и технологий.
Несмотря на планируемое увеличение производтва на период до 2015 год, ожидается дальнейшее снижение негативного воздействия комбината на окружающую среду.
Решения природоохранных задач обеспечиваются за счет:
· Вывода из эксплуатации устаревших и физически изношенных производств;
· Модернизации действующего оборудования с учетом экологических требований;
· Строительства современных агрегатов с совершенной природоохранной составляющей по системам очистки.
В 2009 году ОАО «НЛМК» первым среди крупных российских предприятий перешло на полностью закрытый цикл водоснабжения и прекратило сбросы сточных промышленных вод.
НЛМК является основным налогоплательщиком в регионе и развивает корпоративную культуру, осуществляя социальную поддержку сотрудников. Ежегодно НЛМК строит около 30 000 кв. м жилья для своих работников в Липецке. В последние 4 года заработная плата работников НЛМК повышалась на 25-30% ежегодно. Медицинский комплекс НЛМК на сегодняшний день является одним из самых крупных и хорошо оснащенных в регионе, Новолипецкий комбинат поддерживает спортивные организации, созданный Компанией фонд пенсионного обеспечения НПФ «Социальное Развитие» является 25-ым по величине активов в России. НЛМК также поддерживает образовательные инициативы, предоставляя стипендии студентам ВУЗов.
Приложения
Приложение 1
Стратегия в действии
План действий | Ожидаемые результаты |
· Увеличение объемов выплавки стали более чем на 40%; · Модернизация сталеплавильных мощностей; · Улучшение качества и технических характеристик стали и, как следствие, увеличение объемов производства стали, используемой в отраслях, предъявляющих высокие требования к качеству стальной продукции; | · Рост прибыли за счет использования низкозатратной производственной платформы в России; · Статус одного из наиболее низкозатратных производителей стали в мире и, как следствие, высокий уровень отдачи на капитал; |
· Расширение присутствия дивизиона на ключевых рынках сбыта; · Увеличение производства стали и сортового проката более чем на 60%; | · Увеличение прибыли за счет реализации перспективного проекта в центральном регионе России; · Увеличение доли на рынке сортового проката в России; |
· Вертикальная интеграция с высокоэффективными сырьевыми активами; · Поддержание 100% самообеспеченности железорудным концентратом и коксом; · Сокращение расхода основных видов сырья за счет постоянного освоения новых технологий; · Развитие сети площадок по сбору металлолома; · Поиск возможностей эффективной вертикальной интеграции с активами по добыче коксующегося угля; · Увеличение самообеспеченности электроэнергией на основной площадке; · Освоение энергосберегающих технологий; | · 100% самообеспеченность железорудным концентратом, коксом; · Свыше 40% электроэнергии, потребляемой основной производственной площадкой, вырабатывается на собственных мощностях; · Самый низкий показатель себестоимости 1 тонны железорудного концентрата в России; · Укрепление позиций как на внутреннем, так и на экспортном рынках оцинкованного проката оцинкованного проката и проката с полимерными покрытиями; · Сохранение высокой доли прибыльности продаж трансформаторной стали. |
Список используемой литературы
1. Белянский А.Д. Тонколистовая прокатка. Технология и оборудование / А. Д. Белянский, Л. А. Кузнецов, И. В. Франценюк. М., 1994.
2. Воскобойников В.Г. Общая металлургия: учебник для ВУЗов – 4 издание, переработанное и дополненное / В. Г. Воскобойников, В. А. Кудрин, А. М. Якушев. М., 2008.
3. Коршиков Г.В. Энциклопедический словарь-справочник по металлургии. Липецк, 1998.
4. Компания НЛМК. Корпоративный журнал группы предприятий НЛМК. Липецк, 2011. № 2.
5. Официальный сайт ОАО «НЛМК»: www.nlmk.ru.
|
|
Наброски и зарисовки растений, плодов, цветов: Освоить конструктивное построение структуры дерева через зарисовки отдельных деревьев, группы деревьев...
Кормораздатчик мобильный электрифицированный: схема и процесс работы устройства...
Особенности сооружения опор в сложных условиях: Сооружение ВЛ в районах с суровыми климатическими и тяжелыми геологическими условиями...
Поперечные профили набережных и береговой полосы: На городских территориях берегоукрепление проектируют с учетом технических и экономических требований, но особое значение придают эстетическим...
© cyberpedia.su 2017-2024 - Не является автором материалов. Исключительное право сохранено за автором текста.
Если вы не хотите, чтобы данный материал был у нас на сайте, перейдите по ссылке: Нарушение авторских прав. Мы поможем в написании вашей работы!